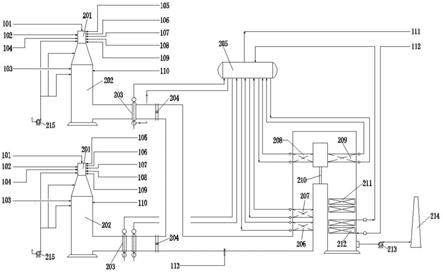
1.本发明涉及煤化工、焦化等领域,具体涉及一种乙二醇装置废气废液焚烧处理的工艺系统及方法。
背景技术:
2.乙二醇是一种重要的化工原料,在纺织、树脂、纤维、表面活性剂等行业有着广泛的应用。近几年,煤制乙二醇技术越来越成熟,装置越来越趋向于大型化。随着大量煤基乙二醇装置的投产,国内乙二醇装置的自给率也在逐渐提高。与此同时,在乙二醇装置的生产有多个工艺路线,部分工艺路线中会产生一些含有亚硝酸甲酯的酯化尾气,不产生废液,也有一些工艺路线会产生大量的mf废液、dmc重组分、dmc轻馏分、dmo重组分等,废液中含亚硝酸甲酯、草酸二甲酯、甲酸甲酯等,这些物质存在易燃、易爆、易腐蚀、易分解等特点,存在一定的危险性,处理难度较大。随着环保形势的日益严格,亟需对这些废气、废液进行合理的处置。
3.目前,在一些规模较小的乙二醇生产装置上,由于产生的废气或废液的总量较小,一些企业直接将该废气废液送至厂区的动力锅炉单元进行焚烧处理。对于不产生废液的乙二醇生产装置来说,直接通过焚烧装置将含亚硝酸甲酯的酯化尾气的进行焚烧处理是最为简便的方法。专利cn109745859a就介绍了一种对乙二醇酯化尾气处理装置及方法,但是未涉及到对废液的处理。
4.对于一些同时副产多股废气、废液且生产规模较大的乙二醇装置来说,采用动力锅炉处理难度较大,不易兼容且存在一定风险,而新建单独的焚烧装置是处理这些废气、废液的最好方式。但对于大型乙二醇装置同时副产出的大量废气、废液来说,由于各组分来源不同且分散、成分复杂、热值不同,如何利用低氮燃烧技术最大限度降低氮氧化物的产生,如何解决废液热值波动大、废液枪易烧坏、易腐蚀,以及scr反应易超温、催化剂失效、以及实现焚烧处理系统的安全稳定运行和烟气达标无害化排放等问题,是目前亟需解决的问题。
技术实现要素:
5.有鉴于此,本发明旨在提出一种乙二醇装置废气废液焚烧处理系统及方法,以解决现有技术在对大型乙二醇装置副产出的大量废气、废液同时进行处理时,所存在的如何确保焚烧处理系统的安全稳定运行和烟气达标无害化排放的问题。
6.为达到上述目的,本发明的技术方案是这样实现的:
7.一种乙二醇装置废气废液焚烧处理系统,包括依次连通的废气废液储存装置、介质输送单元、焚烧单元、一体化尾气处理单元、排放单元;所述焚烧单元的烟气出口与一体化尾气处理单元的烟气入口连接,所述焚烧单元的烟气出口设置水保护段,用于对高温烟气降温;在沿着烟气的流动方向,所述一体化尾气处理单元包括依次连接的scnr脱硝段、余热锅炉,所述余热锅炉的气道内依次设置蒸发段、scr脱硝反应器、省煤器,用于对烟气依次
进行scnr脱硝、换热降温、scr脱硝、余热回收;从而通过焚烧装置对大型乙二醇装置副产出的废气废液进行分级进料、分级配风、焚烧,同时配合设置一体化尾气处理单元,将焚烧单元产出的烟气,依次经过水保护段降温、sncr脱硝、多级蒸发段换热、scr脱硝、余热回收等工艺处理,从而在对大型乙二醇装置副产出的废气废液进行同时处理时,不仅确保了废气废液的充分燃烧,使得炉膛温度场分布均匀,避免局部超温,保证了焚烧处理系统的安全稳定运行,而且实现了烟气达标无害化排放。
8.进一步的,所述焚烧单元包括燃烧器、燃烧室,所述燃烧室包括竖直段和水平段,所述竖直段的底部与水平段连通;所述燃烧器设置在燃烧室竖直段的顶部,所述水保护段设置在燃烧室水平段的烟气出口;从而利用外部冷却水对高温烟气进行降温,使烟气温度降至约900℃后,烟气进入一体化尾气处理单元进行尾气处理,通过水保护段对高温烟气进行换热,使烟气降温,以满足scnr脱硝工艺对烟气温度的要求,有利于提高脱硝效果。
9.进一步的,所述燃烧器包括还原区、氧化区,所述氧化区的一侧与燃烧室连通,氧化区的另一侧与还原区连通;与所述还原区对应的燃烧器的壳体设置第一级燃烧单元、第二级燃烧单元和长明灯,所述第一级燃烧单元、第二级燃烧单元、长明灯均贯穿燃烧器的壳体,并延伸至还原区中,与所述氧化区对应的燃烧器的壳体设置第三级燃烧单元,所述第三级燃烧单元贯穿燃烧器的壳体,并延伸至氧化区中。从而通过在还原区设置两级燃烧单元,并使还原区的过量空气系数小于1,为还原区的燃烧过程提供欠氧氛围,利用欠氧还原反应原理,抑制高热值废料的热力型氮氧化物的生成,一方面有利于确保焚烧效果,另一方面能有效降低尾气中氮氧化物的含量,以减轻下游尾气处理单元的运行压力;在氧化区的助燃空气处于过氧状态,一方面有利于可燃物的充分分解燃烧,另一方面通过提供过量空气,以确保炉温在1100℃以上,有利于炉膛温度的控制,使其处于安全可控的范围之内。
10.进一步的,所述第一级燃烧单元包括第一级供料装置、与第一级供料装置配合的第一级配风管路;所述长明灯与第一级供料装置配合;所述第一级供料装置包括由内至外依次套设的高热值废液管路、雾化介质管路、主燃料气管路;所述第二级燃烧单元包括第二级供料装置、与第二级供料装置配合的第二级配风管路;所述第二级供料装置包括由内至外依次套设的废液管路、雾化介质管路、高热值废气管路;所述第三级燃烧单元包括第三级供料装置、与第三级供料装置配合的第三级配风管路;所述第三级供料装置具有低热值废料入口,用于向氧化区提供低热值废料。从而通过在燃烧器上设置分级进料、分级配风,使得燃烧器能够对多种组分的废料同时进行燃烧,并通过多个燃烧单元对不同热值的废气、废液、雾化汽等废料进行合理分配,使其在合适的燃烧区域进行燃烧,有利于提高燃烧效率,同时由于多个燃烧单元分散设置,使得燃烧热量分散,再通过多个高强旋流器的扰流混合作用,能控制炉膛温度分布均匀,一方面有利于控制燃烧过程中氮氧化物的产生量,能够有效降低尾气中氮氧化物的含量,另一方面避免了常规燃烧器中存在的热量过于集中的问题,能够有效地控制炉膛的温度,防止燃烧器的相关部件发生烧坏腐蚀等情况。
11.进一步的,所述第一级燃烧单元设置在燃烧器的中心轴上,所述第二级燃烧单元、第三级燃烧单元均设置多个,并以相互独立的圆周阵列方式设置在燃烧器的壳体上,这种设置方式一方面通过交错布置能提高主火焰的稳定性,保证中心火焰区的温度高于1300℃,有利于中高热值废液的完全、充分燃烧;另一方面也可以将高热值废料的燃烧单元与低热值废料的燃烧单元在燃烧器的环周上交替布置,通过合理配置喷枪数量和位置,对炉膛
热负荷进行分散布置,避免火焰集中,降低氮氧化物生成的同时,保证了废气废液的整体燃尽率。
12.进一步的,所述scnr脱硝段设置脱硝剂喷嘴,用于对烟气喷洒脱硝剂;优选的,所述脱硝剂沿着scnr脱硝段的烟气管路的切向喷入,所述脱硝剂为质量浓度10%-20%的氨水或尿素的水溶液;从而对焚烧单元中产出的烟气,进行scnr脱硝工艺的处理,脱除一部分氮氧化物后再进入余热锅炉,减小了下游设备的脱硝难度,有利于提高整套系统的脱硝效率。
13.进一步的,所述蒸发段包括第一蒸发段、第二蒸发段、第三蒸发段、第四蒸发段,所述余热锅炉内部设置烟道旁路,所述烟道旁路的烟气入口与第二蒸发段的烟气出口连通,所述烟道旁路的烟气出口与scr脱硝反应器的烟气入口连通,所述烟道旁路中设置调节阀;从而通过多级蒸发段以及烟道旁路的结合,能够调节不同负荷下进入scr脱硝反应器的烟气温度,使得进入scr脱硝反应器的烟气温度始终维持在380-420℃这一最佳温度区间,以提高脱硝效率。
14.进一步的,所述系统还包括中央处理单元,所述scr脱硝反应器的烟气入口设置温度检测装置,所述中央处理单元与温度检测装置连接,用于实时获取scr脱硝反应器入口的烟气温度;所述中央处理单元与调节阀连接,用于控制调节阀的开度;从而能够实时对烟气温度进行智能化监控,实现了在不同负荷或物料波动情况下,根据烟气温度情况对系统的运行进行调控,以便于系统中控室对整个烟气处理过程进行智能化管控,不仅整体系统的平稳运行,有利于提高脱硝效率,而且提高了系统的自动化程度。
15.一种乙二醇装置废气废液焚烧处理方法,应用于所述的一种乙二醇装置废气废液焚烧处理系统,所述方法包括:s1、向焚烧单元中分级进料、分级配风,并焚烧废气、废液;s2、焚烧单元生成的烟气进入水保护段,对烟气进行降温;s3、降温后的烟气进入一体化尾气处理单元,依次进行sncr脱硝、蒸发段换热、scr脱硝、余热回收;s4、处理后的烟气经排放单元外排。从而所述方法通过焚烧装置对大型乙二醇装置副产出的废气废液进行分级进料、分级配风、焚烧,同时配合设置一体化尾气处理单元,将焚烧单元产出的烟气,依次经过水保护段降温、sncr脱硝、多级蒸发段换热、scr脱硝、余热回收等工艺处理,从而在对大型乙二醇装置副产出的废气废液进行同时处理时,不仅确保了废气废液的充分燃烧,使得炉膛温度场分布均匀,避免局部超温,保证了焚烧处理系统的安全稳定运行,而且实现了烟气达标无害化排放。
16.相对于现有技术,本发明所述的一种乙二醇装置废气废液焚烧处理系统及方法具有以下优势:
17.本发明所述的一种乙二醇装置废气废液焚烧处理系统及方法,通过焚烧装置对大型乙二醇装置副产出的废气废液进行分级进料、分级配风、焚烧,同时配合设置一体化尾气处理单元,将焚烧单元产出的烟气,依次经过水保护段降温、sncr脱硝、多级蒸发段换热、scr脱硝、余热回收等工艺处理,从而在对大型乙二醇装置副产出的废气废液进行同时处理时,不仅确保了废气废液的充分燃烧,使得炉膛温度场分布均匀,避免局部超温,保证了焚烧处理系统的安全稳定运行,而且实现了烟气达标无害化排放,使得焚烧单元产出的1100℃左右、氮氧化物浓度在1000mg/nm3以上的烟气,进行尾气处理后,转换为温度在170-180℃左右、氮氧化物排放浓度≤50mg/nm3的达标尾气,其它指标满足gb31571-2017排放限值
要求,不仅满足尾气外排的环保要求,而且烟囱排放尾气时不带水汽、不冒白烟、不拖尾。
附图说明
18.构成本发明的一部分的附图用来提供对本发明的进一步理解,本发明的示意性实施例及其说明用于解释本发明,并不构成对本发明的不当限定。在附图中:
19.图1为本发明实施例所述的一种乙二醇装置废气废液焚烧处理系统的模块示意图;
20.图2为本发明实施例所述的一种乙二醇装置废气废液焚烧处理系统中焚烧单元及一体化尾气处理单元的结构示意图;
21.图3为本发明实施例所述的一种乙二醇装置废气废液焚烧处理系统中焚烧单元及一体化尾气处理单元的另一种结构示意图;
22.图4为本发明实施例所述的一种乙二醇装置废气废液焚烧处理系统中焚烧炉的燃烧器结构示意图。
23.附图标记说明:
24.一次风入口1,二次风入口2,三次风入口3,主燃料气入口4,雾化介质入口5,高热值废液入口6,长明灯7,废液入口8,雾化介质入口9,高热值废气入口10,低热值废料入口11,一次风旋流器12,二次风旋流器13,三次风旋流器14,还原区15,氧化区16。
具体实施方式
25.下文将使用本领域技术人员向本领域的其它技术人员传达他们工作的实质所通常使用的术语来描述本公开的发明概念。然而,这些发明概念可体现为许多不同的形式,因而不应视为限于本文中所述的实施例。此外,术语“第一”、“第二”仅用于描述目的,而不能理解为指示或暗示相对重要性或者隐含指明所指示的技术特征的数量。由此,限定有“第一”、“第二”的特征可以明示或者隐含地包括至少一个该特征。在本发明的描述中,“多个”的含义是至少两个,例如两个,三个等,除非另有明确具体的限定。
26.需要说明的是,在不冲突的情况下,本发明中的实施例及实施例中的特征可以相互组合。
27.下面将参考附图并结合实施例来详细说明本发明。
28.在现有的乙二醇生产过程而言,一些规模较小的乙二醇生产装置,由于产生的废气或废液的总量较小,可以直接将该废气废液送至厂区的动力锅炉单元进行焚烧处理;然而对于同时副产多股废气、废液且生产规模较大的乙二醇装置来说,副产出的废气有1-4种,如乙二醇驰放气氢回收系统解析气、mn废气、液相加氢废气等;副产出的废液有3-7种,废液中含有亚硝酸甲酯、草酸二甲酯、甲酸甲酯、乙醇及其它醇类等物质;这些废液存在易燃、易爆、易腐蚀、易分解等特点,其成分复杂,来源复杂,热值差别大,总量大,尤其重组分废液等废料的焚烧难度大,采用动力锅炉处理难度较大,不易兼容且存在一定风险;从而在对大型乙二醇装置废气同时进行处理时,其中需要面临如何利用低氮燃烧技术最大限度降低氮氧化物的产生,如何解决废液热值波动大、废液枪易烧坏、易腐蚀,以及scr反应易超温、催化剂失效等多个问题,尤其是如何确保焚烧处理系统的安全稳定运行和烟气达标无害化排放的问题。
29.因此,为了解决现有技术在对大型乙二醇装置副产出的大量废气、废液同时进行处理时,所存在的如何确保焚烧处理系统的安全稳定运行和烟气达标无害化排放的问题,本实施例提出一种乙二醇装置废气废液焚烧处理系统及方法,如附图1-4所示,所述系统包括依次连通的废气废液储存装置、介质输送单元、焚烧单元、一体化尾气处理单元、排放单元;
30.所述废气废液储存输送装置包括多个废气储存单元和多个废液储存单元,所述废气储存单元的入口与上游的乙二醇生产系统的废气排放口连接,所述废液储存单元的入口与上游的乙二醇生产系统的废液排放口连接,所述废气储存单元的出口通过介质输送单元与焚烧单元连接,用于将废气输送至焚烧单元进行燃烧,所述废液储存单元的出口通过介质输送单元与焚烧单元连接,用于将废液输送至焚烧单元进行燃烧;所述介质输送单元均包括常规的泵结构,用于输送气体、液体等介质;
31.除此之外,部分废液储存单元与焚烧单元的连接处设置雾化器,用于对废液进行雾化处理,使废液变为雾化汽进入焚烧单元进行燃烧;需要说明的是,“雾化汽”这一用词是指废液被雾化成极细的液滴,形成的一种近似于雾气的流体。
32.作为一种雾化器的实施方案,废液储存单元包括废液缓冲罐,雾化器为雾化喷枪,从而废液进入缓冲罐,然后通过废液泵增压至喷枪雾化所需压力,废液经压缩空气和蒸汽雾化成极细的液滴后进入焚烧单元;此外,每股废液单独配置缓冲罐,缓存时间按不低于2小时,满足上游波动时有一定的的缓冲时间,保证进入雾化喷枪的流量和压力稳定。
33.所述焚烧单元为立式焚烧炉,包括燃烧器、燃烧室,所述燃烧室包括竖直段和水平段,所述竖直段的底部与水平段连通,即所述燃烧室呈“l”型;所述燃烧器设置在燃烧室竖直段的顶部,使得废气废液的焚烧主要在燃烧室的竖直段完成。此外,焚烧炉为负压操作,炉子上设置温度、压力等检测仪表,设置防爆设施,防止废物外泄,确保安全可靠运行。
34.根据配风情况的不同,如附图4所示,所述燃烧器包括还原区15、氧化区16,其中,还原区15位于燃烧器的火道附近,氧化区16位于燃烧器壳体内部,所述氧化区16的一侧与燃烧室连通,氧化区16的另一侧与还原区15连通;与所述还原区15对应的燃烧器的壳体设置第一级燃烧单元、第二级燃烧单元和长明灯7,所述第一级燃烧单元、第二级燃烧单元、长明灯7均贯穿燃烧器的壳体,并延伸至还原区15中,所述第一级燃烧单元包括第一级供料装置、与第一级供料装置配合的第一级配风管路;所述第二级燃烧单元包括第二级供料装置、与第二级供料装置配合的第二级配风管路;所述长明灯7与第一级供料装置配合;与所述氧化区16对应的燃烧器壳体设置第三级燃烧单元,所述第三级燃烧单元贯穿燃烧器的壳体,并延伸至氧化区16中,所述第三级燃烧单元包括第三级供料装置、与第三级供料装置配合的第三级配风管路;从而通过长明灯7对第一级供料装置的物料进行点火引燃,然后点燃后的火焰继续引燃第二级供料装置的物料、第三级供料装置的物料;
35.其中,还原区15具有两级供料以及两级配风,所述第一级供料装置包括由内至外依次套设的高热值废液管路、雾化介质管路、主燃料气管路,用于向还原区15中提供高热值废液、雾化汽等高热值废料以及主燃料气,如附图4所示,高热值废液管路设置高热值废液入口6,雾化介质管路设置雾化介质入口5,主燃料气管路设置主燃料气入口4;所述第一级配风管路经由一次风入口1并通过一次风旋流器12,向还原区15中提供第一级助燃空气,为主燃料气、高热值废液、雾化汽提供次当量风;优选的,第一级供料装置用于供给并燃烧热
值最高的废料。
36.所述第二级供料装置包括由内至外依次套设的废液管路、雾化介质管路、高热值废气管路,用于向还原区15中提供高热值废液、雾化汽、高热值废气等高热值废料,如附图4所示,废液管路设置废液入口8,雾化介质管路设置雾化介质入口9,高热值废气管路设置高热值废气入口10;所述第二级配风管路经由二次风入口2并通过二次风旋流器13,向还原区15中提供第二级助燃空气,为高热值废液、雾化汽、高热值废气、以及第一级供料装置的出料提供次当量风;优选的,第二级供料装置用于供给并燃烧热值次高的废料。
37.其中,在还原区15的供料中均为高热值废料,在还原区15的两级供料、两级配风以及燃烧过程中,还原区15的过量空气系数小于1,为还原区15的燃烧过程提供欠氧氛围,利用欠氧还原反应原理,抑制高热值废料的热力型氮氧化物的生成,一方面有利于确保焚烧效果,另一方面能有效降低尾气中氮氧化物的含量,以减轻下游尾气处理单元的运行压力。
38.对于氧化区16而言,具有一级供料以及一级配风,所述第三级供料装置具有低热值废料入口11,用于向氧化区16提供低热值废气、低热值废液、低热值雾化汽等低热值废料;所述第三级配风管路经由三次风入口3并通过三次风旋流器14,向氧化区16提供第三级助燃空气;优选的,第三级供料装置用于供给并燃烧热值较低的废料。
39.其中,氧化区16的助燃空气处于过氧状态,一方面有利于可燃物的充分分解燃烧,另一方面通过第三级配风管路在燃烧室前段,提供一定量的过量空气,以确保炉温在1100℃以上,有利于炉膛温度的控制,使其处于安全可控的范围之内。
40.在第一级配风、第二级配风、第三级配风的过程中,外部的助燃空气均由旋流器旋入燃烧器中,一方面使物料与空气形成强制外混形式,保证每股废料都能与助燃空气充分混合,实现完全热解,有利于提高燃烧效率,另一方面使整个炉膛处于湍流状态,炉膛温度场分布均匀,避免局部超温。
41.此外,对于燃烧器而言,第一级供料装置、第一级配风管路设置在燃烧器的中心轴上,作为中心枪,用于供给并燃烧热值最高的废料;第二级供料装置、第二级配风管路,第三级供料装置、第三级配风管路均可以设置多个,并以相互独立的圆周阵列方式设置在燃烧器的壳体上;一方面通过交错布置能提高主火焰的稳定性,保证中心火焰区的温度高于1300℃,有利于中高热值废液的完全、充分燃烧;另一方面也可以将高热值废料的燃烧单元与低热值废料的燃烧单元在燃烧器的环周上交替布置,通过合理配置喷枪数量和位置,对炉膛热负荷进行分散布置,避免火焰集中,降低氮氧化物生成的同时,保证了废气废液的整体燃尽率。
42.此外,对于不能自持燃烧的废气、废液,从炉体锥段环形均布、通过多个小孔分散喷入高温炉膛,避免对主火焰稳定性的影响,同时实现与炉膛内部高温烟气的充分混合、燃烧,降低高热值燃料燃烧温度,抑制热力型氮氧化物的生成。
43.对于每一组相互配合的供料装置、配风管路而言,配风管路的出口设置有套设在供料装置外的旋流器,且旋流器与供料装置同心设置,构成一组独立的燃烧单元,每组燃烧单元可以单独燃烧废气、废液、雾化汽中的一个或多个组分。从而使得燃烧器能够对多种组分的废料同时进行燃烧,并通过多个燃烧单元对不同热值的废气、废液、雾化汽等废料进行合理分配,使其在合适的燃烧区域进行燃烧,有利于提高燃烧效率,同时由于多个燃烧单元分散设置,使得燃烧热量分散,再通过多个高强旋流器的扰流混合作用,能控制炉膛温度分
布均匀,一方面有利于控制燃烧过程中氮氧化物的产生量,能够有效降低尾气中氮氧化物的含量,另一方面避免了常规燃烧器中存在的热量过于集中的问题,能够有效地控制炉膛的温度,防止燃烧器的相关部件发生烧坏腐蚀等情况。
44.对于不同的废液而言,由于其密度、粘度、腐蚀性不同,在供料装置向燃烧器内输送物料时需要对相应的供料装置进行单独设置,例如:一般废液的供料装置采用310s喷头,具有较好的耐高温性能;含有亚硝酸甲酯和草酸二甲酯的废液的供料装置采用哈氏合金喷头,同时具有较好的耐腐蚀和耐高温性能;另外,对于废液的雾化过程,含有亚硝酸甲酯、草酸二甲酯、甲酸甲酯等危险等级高的废液,雾化介质优先采用压缩空气;含乙醇及其它醇类物质的常规废液,可采用低压蒸汽雾化。
45.经过燃烧器的供料、配风、引燃后,废料在燃烧室的竖直段内充分燃烧,产生1100℃以上的高温烟气,然后高温烟气从竖直段的底部流入水平段;所述燃烧室通过水平段与一体化尾气处理单元连通,所述水平段的烟气出口端设置水保护段203/403,利用外部冷却水对高温烟气进行降温,使烟气温度降至约900℃后,烟气进入一体化尾气处理单元进行尾气处理。
46.对于一体化尾气处理单元而言,在沿着烟气的流动方向,包括依次连通的scnr脱硝段、余热锅炉;其中,蒸发段、scr脱硝反应器211/411、省煤器212/412依次设置在余热锅炉的气道中,所述余热锅炉的出口与烟囱214/414连通,即烟气经过scnr脱硝后,进入余热锅炉进行换热降温、scr脱硝、余热回收后,经由烟囱214/414排放。
47.所述水保护段203/403的出口与scnr脱硝段连通,从而温度降至约900℃的烟气进入scnr脱硝段,进行scnr脱硝,从而通过水保护段203/403对高温烟气进行换热,使烟气降温,以满足scnr脱硝工艺对烟气温度的要求,有利于提高脱硝效果。所述scnr脱硝段设置脱硝剂喷嘴113/313,用于对烟气喷洒脱硝剂;所述脱硝剂优选为质量浓度10%-20%的氨水或尿素的水溶液。
48.通过scnr脱硝段对烟气进行处理后,脱除一部分氮氧化物,然后烟气进入余热锅炉;其中,所述余热锅炉为π型余热锅炉,采用模块化设计,在沿着烟气的流动方向,所述余热锅炉的气道内部依次设置多级蒸发段和省煤器212/412,所述余热锅炉在最后一级蒸发段与省煤器212/412之间的气道中设置scr脱硝反应器211/411;蒸发受热面采用上、下集箱加对流管束构成管组的结构方式,方便了现场组装,汽水系统采用自然循环形式,在变负荷工况时,能保证水位稳定,使得烟气经过蒸发段换热,烟气降温至380℃左右,进入scr脱硝反应器211/411,脱除剩余的氮氧化物,最后进入省煤器212/412与除氧水换热后降温至180℃,然后经引风机213/413输送至烟囱214/414排放。对于汽水系统中的除氧水而言,用于对烟气进行换热,经过省煤器212/412升温至200℃后进入蒸发段和水保护段203/403,同时副产3.5mpag饱和蒸汽。
49.作为本技术优选的方案,所述余热锅炉内部设置四级蒸发段,分别为第一蒸发段206/406、第二蒸发段207/407、第三蒸发段208/408、第四蒸发段209/409,所述余热锅炉内部设置烟道旁路210/410,所述烟道旁路210/410的烟气入口与第二蒸发段207/407的烟气出口连通,所述烟道旁路210/410的烟气出口与scr脱硝反应器211/411的烟气入口连通,所述烟道旁路210/410中设置调节阀;在调节阀完全关闭状态时,烟道旁路210/410关闭,烟气依次流经四级蒸发段、scr脱硝反应器211/411;在调节阀开启时,烟道旁路210/410开启,至
少部分烟气依次流经第一蒸发段206/406、第二蒸发段207/407、烟道旁路210/410、scr脱硝反应器211/411;从而通过设置烟道旁路210/410,用于调节不同负荷下进入scr脱硝反应器的烟气温度,使得进入scr脱硝反应器211/411的烟气温度始终维持在380-420℃这一最佳温度区间,以提高脱硝效率。
50.具体的,为了保证进入scr脱硝反应器211/411的烟气温度相对稳定,所述scr脱硝反应器211/411的烟气入口设置温度检测装置,系统中控室根据温度检测装置实时获取的烟气温度反馈,来调节调节阀的开度,使第二蒸发段207/407流出的部分高温烟气,经过烟道旁路210/410,直接与第四蒸发段209/409流出的烟气混合,从而使得调节阀可调整不同负荷下进入scr脱硝反应器的烟气温度,保证scr脱硝效果的稳定,实现烟气的达标排放。
51.从而对于所述系统而言,通过设置一体化尾气处理单元,将焚烧单元产出的烟气,依次经过水保护段203/403降温、sncr脱硝、多级蒸发段换热、scr脱硝、余热回收,使得焚烧单元产出的1100℃左右、氮氧化物浓度在1000mg/nm3以上的烟气,进行尾气处理后,转换为温度在170-180℃左右、氮氧化物排放浓度≤50mg/nm3的达标尾气,其它指标满足gb31571-2017排放限值要求,不仅满足尾气外排的环保要求,而且烟囱排放尾气时不带水汽、不冒白烟、不拖尾。
52.除此之外,所述余热锅炉、scr脱硝反应器211/411内均设置吹灰装置,来防止废液焚烧可能产生的少量飞灰进入下游系统所造成的堵塞等不良影响。所述系统还包括中央处理单元,水保护段203/403的出口,scr脱硝反应器211/411的进出口烟道、省煤器212/412出口烟道分别设置温度检测装置,所述中央处理单元与各个温度检测装置连接,用于实时监测各反应段的烟气温度等参数,并根据烟气温度情况对系统的运行进行调控,以便于系统中控室对整个烟气处理过程进行智能化管控。同时,中央处理单元与烟道旁路210/410的调节阀连接,用于控制调节阀的开度,以便于对进入scr脱硝反应器的烟气温度进行调节。中央处理单元具有计数模块,用于在系统调控过程中进行计数动作。
53.结合以上对乙二醇装置废气废液焚烧处理系统的介绍,本技术还提出一种乙二醇装置废气废液焚烧处理方法,包括:
54.s1、向焚烧单元中分级进料、分级配风,并焚烧废料;
55.优选的,在燃烧器的中心轴上向还原区15中进行第一级进料、第一级配风,用于供给并燃烧热值最高的废料;在燃烧器的中心轴的外围向还原区15中进行第二级进料、第二级配风,用于供给并燃烧热值次高的废料;在燃烧器壳体的外围向氧化区16进行第三级进料、第三级配风,用于供给并燃烧热值较低的废料。
56.s2、焚烧单元生成的烟气进入水保护段203/403,对烟气进行降温,将烟气降温至900℃;
57.s3、降温后的烟气进入一体化尾气处理单元,依次进行sncr脱硝、蒸发段换热、scr脱硝、余热回收;
58.s4、处理后的烟气经排放单元外排,其中,所述排放单元为烟囱。
59.在烟气进行蒸发段换热过程中,步骤s3还包括:
60.s31、中央处理单元实时获取scr脱硝反应器入口温度t;
61.s32、判断是否t大于第一额定温度;是,则进行步骤s33,否,则进行步骤s35;
62.s33、控制烟道旁路的调节阀减小开度,并判断调节阀是否完全关闭;是,则第一计
数值k加1,进行步骤s34;否,则返回步骤s31;
63.s34、判断k是否大于第一预设值;是,则发送报警信息;否,则返回步骤s31;
64.s35、判断是否t小于第二额定温度;是,则进行步骤s36;否,则返回步骤s31;
65.s36、控制烟道旁路的调节阀增大开度,并判断调节阀是否完全开启;是,则第二计数值m加1,进行步骤s37;否,则返回步骤s31;
66.s37、判断m是否大于第二预设值,是,则发送报警信息;否,则返回步骤s31。
67.其中,第一额定温度为420℃,第二额定温度为380℃,第一预设值为2-5,第二预设值为2-5;发送报警信息的过程,可以是中央处理单元直接向系统中控室发送报警信息,也可以是中央处理单元直接控制警报器启动,进行报警;
68.从而在烟气进行蒸发段换热过程中,通过对烟气温度进行智能化监控,实现了在不同负荷或物料波动情况下,对进入scr脱硝反应器的烟气温度的自动化调控,确保进入scr脱硝反应器211/411的烟气温度始终维持在380-420℃这一最佳温度区间,不仅有利于提高脱硝效率,而且提高了系统的自动化程度,极大地降低了人工操控的难度;同时,在某些特殊情况或设备故障的情况下,若烟气温度不在380-420℃这一温度范围内,则系统可以自动报警,以提醒工程师及时进行检查维修,有利于对系统的非正常运行状态或设备故障等情况进行及时的智能化排查,有利于保障系统的正常稳定运行。
69.实施例1
70.上游乙二醇装置来的需焚烧处理的废液有6种,分别为dmc轻馏分105、dmo重组分106、dmc重组分107、mf废液108、火炬凝液109、乙醇产品塔废液110等,废液总量约13t/h。废液含亚硝酸甲酯、草酸二甲酯、甲酸甲酯、乙醇及其它醇类等,这些物质存在易燃、易爆、易腐蚀、易分解等特点。所需焚烧处理的废气有3种,分别为:乙二醇驰放气氢回收系统解析气102、mn废气103、液相加氢废气104等,废气总量15561nm3/h。所需处理的废气、废液成分复杂,热值差别大,总量大,尤其重组分等废液焚烧难度大。
71.根据上述废液,废气的特点,本实施例提出的乙二醇装置废气废液焚烧处理系统,包括多个并列的焚烧单元和一个一体化尾气处理单元;为了便于描述,以两个并列的焚烧单元为例,如附图2所示,对于任意一个焚烧单元而言,单套焚烧炉各按50%负荷设计,单套焚烧系统操作弹性:60~110%。
72.进入焚烧装置的废液105/106/107/108/109/110分别进入缓冲罐,然后通过废液泵增压至喷枪雾化所需压力,废液经压缩空气和蒸汽雾化成极细的液滴后进入燃烧器201。废气、废液与一定量的助燃风机215来空气在焚烧炉202内充分燃烧,产生1100℃以上的高温烟气。焚烧后烟气中no
x
浓度在1000mg/nm3以上。焚烧炉202设计立式顶烧,烟气从竖直炉体底部出,后接水平布置水保护段,烟气温度降至约900℃,两套焚烧炉出来的烟气汇合后在烟道内喷入20%的氨水溶液,通过sncr脱硝反应脱除一部分氮氧化物。然后烟气进入π型余热锅炉,经一级蒸发段206、二级蒸发段207、三级蒸发段208、四级蒸发段209降温至380℃进入scr脱硝反应器211脱除剩余的氮氧化物,最后进入省煤器212与除氧水换热后降温至180℃经过引风机213排入烟囱214。132℃的除氧水112先经过省煤器升温至200℃后进入蒸发段206-209和水保护段203,汽包205副产3.5mpag饱和蒸汽111。
73.任一个焚烧单元均具有独立的燃烧器201,燃烧器201的中心枪设置为热值最高的废液枪和主燃料枪夹套结构:夹套上设置主燃料气入口4,主燃料气入口4在开工升温阶段
通入天然气,在系统升温完成后切换为高热值的液相加氢废气104,中心废液枪上设置高热值的mf废液入口,该废液通过雾化介质雾化后进入中心火焰区。热值较高的废气通过燃烧器201上环周均布的多只废液喷枪进入燃烧器,该废液喷枪同样为夹套结构:中心枪上通入剩余的几股较高热值废液,夹套走乙二醇驰放气氢回收系统解析气102。不能自持燃烧的mn废气103、乙醇产品塔废液110从焚烧炉202上的入口进入,该入口在焚烧炉上的锥段环形均布、通过多个小孔分散喷入高温炉膛,避免对主火焰稳定性的影响,同时实现与炉膛内部高温烟气的充分混合、燃烧。上述废气、废液喷枪交错布置的设计能提高主火焰的稳定性,保证中心火焰区的温度高于1300℃,有利于中高热值废液的完全、充分燃烧。
74.除此之外,任一个焚烧单元为立式焚烧炉,包括燃烧器、燃烧室,所述燃烧室包括竖直段和水平段,所述竖直段的底部与水平段连通,即所述燃烧室呈“l”型;所述燃烧器设置在燃烧室竖直段的顶部,使得废气废液的焚烧主要在燃烧室的竖直段完成,所述水平段的出口设置烟道阀204,所述烟道阀204为大口径自动切断阀,正常情况下烟道阀204均处于开启状态,即两组焚烧单元均处于运行状态,两组焚烧单元出来的高温烟气经过水保护段203的换热降温后,汇合进入一体化尾气处理单元,进行sncr脱硝、多级蒸发段换热、scr脱硝、余热回收,直至排放。
75.以两组焚烧单元为例,当某一焚烧炉处于50%以下低负荷运行时,关闭其出口的烟道阀204,只维持一台焚烧炉运行,确保单台焚烧炉操作负荷大于50%,提高焚烧系统的稳定性,避免低负荷下的能量损耗。同时,两套焚烧炉可以互为备用,通过对烟道阀204进行切换。当一台焚烧炉故障检修时,关闭其出口的烟道阀204,将运行的焚烧炉与故障的焚烧炉进行安全隔离,不影响同系列焚烧炉的稳定运行,降低对上游乙二醇生产装置的影响。
76.最终,本实施例中排放的烟气温度在172~179℃之间,烟囱214排放的烟气不带水汽、不冒白烟、不拖尾,排放烟气中no
x
排放浓度为37mg/nm3,满足no
x
排放浓度≤50mg/nm3的环保指标,其它指标也均满足gb31571-2017排放限值要求。
77.实施例2
78.乙二醇装置来的需焚烧处理的废液有6种,分别为dmc轻馏分305、dmo重组分306、dmc重组分307、mf废液308、火炬凝液309、乙醇产品塔废液310等,废液总量约13t/h。废液中含有亚硝酸甲酯、草酸二甲酯、甲酸甲酯、乙醇及其它醇类等,这些物质存在易燃、易爆、易腐蚀、易分解等特点。所需焚烧处理的废气有3种,分别为:乙二醇驰放气氢回收系统解析气302、mn废气303、液相加氢废气304等,废气总量15561nm3/h。
79.本实施例提出的乙二醇装置废气废液焚烧处理系统,包括一个焚烧单元和一个一体化尾气处理单元;如附图3所示,所述系统为单套系统,按废气、废液加和量的70%设计,正常运行时按废气、废液加和量的50%同时运行,即处理废液6.5t/h,废气7780.5nm3/h,一套故障时满负荷运行一套,处理不完的废液先作缓存,下面对单套系统进行说明。
80.进入焚烧装置的废液305/306/307/308/309/310分别进入缓冲罐,然后通过废液泵增压至喷枪雾化所需压力,废液经压缩空气或蒸汽雾化成极细的液滴后分别进入两套焚烧装置的燃烧器401及焚烧炉402。废气、废液与助燃风机404来的助燃空气在焚烧炉402内充分燃烧,产生1100℃以上的高温烟气。焚烧后烟气中no
x
浓度在1000mg/nm3以上。焚烧炉402设计立式顶烧,烟气从竖直炉体底部出,后接水平布置水保护段403,烟气温度降至约900℃,此时喷入氨水溶液,通过sncr脱硝反应脱除一部分氮氧化物。出焚烧炉402的高温烟
气进入π型余热锅炉,经蒸发段406/407/408/409降温至380℃进入scr脱硝反应器411脱除剩余的氮氧化物,最后进入省煤器412与除氧水312换热后降温至180℃经过引风机413排入烟囱414。132℃的除氧水312先经过省煤器412升温至200℃后进入蒸发段406/407/408/409和水保护段403,汽包405副产3.5mpag饱和蒸汽311。
81.对于焚烧单元的结构及设置,与实施例1基本相同,在此不进行赘述。最终,本实施例中排放的烟气温度在170~176℃之间,烟囱214排放的烟气不带水汽、不冒白烟、不拖尾,排放烟气中no
x
排放浓度为43mg/nm3,满足no
x
排放浓度≤50mg/nm3的环保指标,其它指标也均满足gb31571-2017排放限值要求。
82.需要说明的是,为了便于对附图进行查阅、避免引起歧义,附图2中的附图标号“1xx”与附图3中的附图标号“3xx”对应,附图2中的附图标号“2xx”与附图3中的附图标号“4xx”对应,均是指同一类部件;例如:水保护段在附图2中的附图标号为203,在附图3中的附图标号为403。
83.以上所述仅为本发明的较佳实施例而已,并不用以限制本发明,凡在本发明的精神和原则之内,所作的任何修改、等同替换、改进等,均应包含在本发明的保护范围之内。
再多了解一些
本文用于企业家、创业者技术爱好者查询,结果仅供参考。