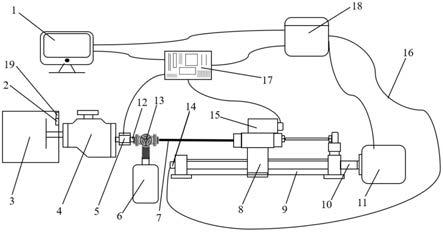
1.本实用新型涉及故障模拟装置,尤其是涉及一种航空发动机可调静子叶片压力故障模拟装置。
背景技术:
2.在航空发动机正常运行过程中,当燃油泵故障、油滤堵塞、管道泄漏等发生时,可调静子叶片电液伺服阀的压力将减少或者增大,导致作动筒位移速度变慢、无法到达指定位置、作动筒抖动。极端情况下,作动筒无法响应位移控制指令。在航空发动机非线性容错控制算法研究中,假设了执行器系统故障的理论数学模型。为了保证执行器系统故障的理论数学模型与真实物理过程一致,需要通过实验研究执行器系统发生故障后,执行器系统的数学模型的变化规律,校正发动机容错控制模型,为容错控制算法建立基础。由于直接模拟航空发动机燃油泵故障、油滤堵塞、管道泄漏等故障的难度大、成本高、操作难,所以本实用新型直接模拟可调静子叶片电液伺服阀的压力变化,间接模拟以上故障对可调静子叶片控制造成的影响。
技术实现要素:
3.本实用新型的目的是为了克服在模拟航空发动机执行器故障的难度大、成本高、操作难等问题,提供一种航空发动机可调静子叶片压力故障模拟装置。通过设定九种故障模式分别作用到本装置控压模块的溢流阀当中,直接模拟可调静子叶片电液伺服阀的压力变化,间接模拟系统压力故障对可调静子叶片控制造成的影响,并建立压力故障模型。
4.本实用新型包括油泵模块、溢流阀控压模块、压力故障检测建模模块三部分;油泵模块、溢流阀控压模块、压力故障检测建模模块依次连接;所述油泵模块用于提供液油压动力供给,所述溢流阀控压模块用于通过对溢流阀角度的控制实现压力故障注入,所述压力故障检测建模模块用于压力故障的检测以及故障模型的建立;
5.所述油泵模块包括油箱、齿轮油泵、步进电机、吸油油滤器、回油滤清器、高压滤油器、球阀;油箱与齿轮油泵相连,齿轮油泵与电机连接;所述步进电机与溢流阀通过齿轮进行连接;所述吸油油滤器、回油滤清器、高压滤油器、球阀为油泵模块基础部件;
6.所述溢流阀控压模块包括微控制器、齿轮轴、角位移传感器、fpga信号采集板卡、射流管伺服阀;所述角位移传感器设在齿轮轴上,角位移信号反馈至微控制器以实现对设定故障模式的精确控制;溢流阀与油滤对应连接,所述微控制器接收来自上位机的故障模式控制指令,通过fpga信号采集板卡将输出控制信号传输至步进电机,控制步进电机的转动以及转动方向,实现溢流阀角度的控制;不同的溢流阀角度对应不同的可调静子叶片电液伺服阀的压力,实现系统压力故障的注入;
7.所述压力故障检测建模模块设有可调静子叶片作动筒、磁滞位移传感器,可调静子叶片作动筒通过油管与溢流阀连接,磁滞位移传感器设在可调静子叶片作动筒左侧,可调静子叶片作动筒上方安装有射流管伺服阀并通过导线与控制器连接,作动筒作动单元后
接负载;所述磁滞位移传感器将作动单元位移信号传送至信号采集板,而后变送给控制器,微控制器接收来自作动筒磁滞位移传感器的位移信号以及来自射流管伺服阀的压力信号后,进行分析计算并上传至上位机,上位机依据所得数据建立可调静子叶片压力故障数学模型。
8.优选地,所述油泵模块还设有双路温控仪、热电偶、过温报警器、液压管路安全系统,液压管路安全系统可设有液压表报警、稳压器、溢流阀、蓄能器、专用急停按钮,若发生高压泄露,则自动启用专用急停按钮关闭电机和泵,切断压力,确保安全。
9.优选地,所述步进电机选用飞迈科技86步进电机12nm,用于实现压力故障模式的产生;
10.优选地,所述微控制器通过数据线与步进电机连接通信,所述步进电机通过齿轮轴与溢流阀相连,所述齿轮轴右端设有角位移传感器。
11.优选地,所述微控制器为arm嵌入式开发板,型号为imx6q。
12.优选地,所述arm嵌入式开发板设定九种故障模式,九种压力故障模式相对应的压强分别为:2mpa、3mpa、4mpa、6mpa、7mpa、8mpa、1~5mpa、3~7mpa、2~8mpa,对应步进电机的九种转动模式,所述步进电机通过齿轮轴带动溢流阀转动,可产生不同开度,进而成功实现压力故障以及压力波动故障注入。
13.优选地,所述可调静子叶片作动筒可采用朴鲁液压ck1
‑
150
‑
dn
‑
la。
14.优选地,所述磁滞位移传感器可采用朴鲁液压30
‑
300
‑
e。
15.与现有技术相比,本实用新型具有如下突出的优点:
16.本实用新型装置中溢流阀控压模块是压力故障模拟装置的关键;本实用新型通过外置步进电机并采用齿轮轴与溢流阀连接,通过外置一个微控制器直接控制步进电机的转动以及转动方向,实现溢流阀角度的控制,间接实现系统压力故障的注入;所述装置的正常运行压强为5mpa,与所注入九种压力故障模式相对应的压强分别为:2mpa、3mpa、4mpa、6mpa、7mpa、8mpa、1~5mpa、3~7mpa、2~8mpa,通过压力故障的注入,实现系统的带故障运行,进而采集可调静子叶片在故障压力输入下的系统输出响应数据,将所采集数据传输至上位机进行数据分析,并根据本实用新型所采集数据建立压力故障数学模型,为容错控制算法建立基础。
附图说明
17.图1是本实用新型的结构示意图;
18.图2是本实用新型的溢流阀控压模块结构示意图。
19.图中各标记为:1
‑
上位机,2
‑
双路温控仪,3
‑
油箱,4
‑
齿轮油泵,5
‑
步进电机,6
‑
油滤,7
‑
油管,8
‑
作动筒,9
‑
作动筒底座,10
‑
作动筒作动单元,11
‑
负载,12
‑
角位移传感器,13
‑
溢流阀,14
‑
磁滞位移传感器,15
‑
射流管伺服阀,16
‑
数据线,17
‑
arm嵌入式开发板,18
‑
fpga信号采集板,19
‑
热电偶,20
‑
步进电机转轴,21
‑
齿轮轴,22
‑
溢流阀口,23
‑
油滤口,24
‑
出油口,25
‑
液压表报警器,26
‑
进油口,27
‑
溢流阀齿口。
具体实施方式
20.以下实施例将结合附图对本实用新型的技术方案进行详细描述。
21.本实用新型包括油泵模块、溢流阀控压模块、压力故障检测建模模块三部分;
22.所述油泵模块由ycs
‑
d iii动力站实现,用于提供液油压动力供给,所述油泵模块包括油箱、齿轮油泵、步进电机、吸油油滤器、回油滤清器、高压滤油器、球阀;所述油箱中装有双路温控仪及热电偶;所述齿轮油泵与电机连接;所述步进电机与溢流阀通过齿轮进行连接,通过控制调节溢流阀角度实现系统压力的故障注入,设计输入控制指令,获得系统在不同压力故障模式下的输出响应数据;所述吸油油滤器、回油滤清器、高压滤油器、球阀为油泵模块基础部件;
23.所述溢流阀控压模块通过对溢流阀角度的控制实现压力故障注入,其结构是:外置步进电机通过齿轮轴与溢流阀连接,通过外置一个微控制器直接控制步进电机的转动以及转动方向,实现溢流阀角度的控制,间接实现系统压力故障的注入;所述步进电机选用飞迈科技86步进电机12nm,用于实现压力故障模式的产生;所述齿轮轴上安装有角位移传感器,通过其反馈至微控制器的角位移信号实现对设定故障模式的精确控制;所述微控制器为arm嵌入式开发板,型号为imx6q,控制器接收来自上位机的故障模式控制指令,通过fpga信号采集板卡把输出控制信号传输到步进电机,对溢流阀开度进行控制,不同的溢流阀角度对应不同的可调静子叶片电液伺服阀的压力;所述溢流阀与一个外置油滤对应连接;
24.所述压力故障检测建模模块用于压力故障的检测以及故障模型的建立,其结构是:可调静子叶片作动筒通过油管与溢流阀连接,作动筒左侧装有一磁滞位移传感器,上方安装有射流管伺服阀并通过导线与控制器连接,作动筒作动单元后接负载;所述可调静子叶片作动筒为朴鲁液压ck1
‑
150
‑
dn
‑
la;所述磁滞位移传感器为朴鲁液压30
‑
300
‑
e,其将作动单元位移信号传送至信号采集板,而后变送给控制器,控制器接收来自作动筒磁滞位移传感器的位移信号以及来自射流管伺服阀的压力信号,对其进行分析计算并上传至上位机,上位机依据所上传数据建立可调静子叶片压力故障数学模型。
25.优选地,油泵模块中采用双路温控仪、热电偶以及过温报警器。针对液压管路安全,采用了液压表报警、稳压器、溢流阀、蓄能器、专用急停按钮,发生高压泄露,将自动启用专用急停按钮关闭电机和泵,切断压力,确保安全。
26.优选地,所述压力故障模拟装置中,微控制器arm嵌入式开发板通过数据线与步进电机连接通信,所述步进电机通过齿轮轴与溢流阀相连,所述齿轮轴右端设有角位移传感器。
27.优选地,所述微控制器arm嵌入式开发板设定九种故障模式,对应步进电机的九种转动模式,所述步进电机通过齿轮轴带动溢流阀转动,可产生不同开度,进而成功实现压力故障以及压力波动故障注入。
28.优选地,所述压力故障模拟装置中作动筒左端设有磁滞位移传感器,所述磁滞位移传感器与微控制器相连,所述微控制器从磁滞位移传感器以及射流管伺服阀分别获取作动筒位移信号与系统压力信号,并将其传输至上位机,将所获取信号数据进行分析处理得到压力故障下可调静子叶片数学模型。
29.如图1和2所示,本实施例包括油泵模块、溢流阀控压模块、压力故障检测建模模块,油泵模块包含油箱3、齿轮油泵4,油箱中设有双路温控仪2与热电偶19,溢流阀控压模块包含步进电机5,步进电机5通过齿轮轴21与溢流阀13连接,溢流阀13下方接有一个油滤6,作动筒8置于作动筒底座9上通过油管7与溢流阀13连接,作动筒8左侧装有一磁滞位移传感
器14,作动筒8上方安装有射流管伺服阀15,射流管伺服阀15通过导线与arm嵌入式开发板17连接,arm嵌入式开发板17将所设定的九种压力故障模式控制指令依次发送至步进电机5,步进电机5响应控制器指令控制步进电机转轴20做出特定方向、圈数的转动,通过齿轮轴21带动溢流阀齿口27与溢流阀口22扭转一定角度,实现溢流阀角度的控制,液压表报警器25置于溢流阀进油口26上,溢流阀下端油滤口23下接油滤6,溢流阀出油口24通过油管7与射流管伺服阀15相连接,作动筒作动单元10后接负载11,fpga信号采集板18采集来自负载11及磁滞位移传感器14的数据,并传输给上位机1与arm嵌入式开发板17,arm嵌入式开发板17采集来自fpga信号采集板18负载位移数据与射流管伺服阀15压力数据,将所采集数据传输至上位机1进行数据分析,上位机1利用由本实用新型所采集数据建立压力故障数学模型,为容错控制算法建立基础。
30.进一步地,arm嵌入式开发板17通过数据线16与步进电机5连接通信,所述步进电机通过齿轮轴21与溢流阀13相连,所述齿轮轴右端设有角位移传感器12。
31.进一步地,arm嵌入式开发板17设定九种故障模式,所述装置的正常运行压强为5mpa,所注入九种压力故障模式相对应的压强分别为:2mpa、3mpa、4mpa、6mpa、7mpa、8mpa、1~5mpa、3~7mpa、2~8mpa,对应步进电机5的九种转动模式,步进电机5响应微控制器指令控制步进电机转轴20做出特定方向、圈数的转动,通过齿轮轴21带动溢流阀齿口27与溢流阀口22扭转一定角度,实现溢流阀角度的控制,进而成功实现压力故障以及压力波动故障注入。
32.进一步地,所述压力故障模拟装置中作动筒8左端设有磁滞位移传感器14,所述磁滞位移传感器与微控制器arm嵌入式开发板17相连,所述微控制器从磁滞位移传感器14以及射流管伺服阀15分别获取在压力故障注入后作动筒位移响应信号及数据与系统压力信号及数据,并将其传输至上位机1,将所获取信号数据进行分析处理得到压力故障下可调静子叶片数学模型。
33.以上所述仅为本实用新型的优选实施方式,并非因此限制本实用新型的专利范围,凡是利用本实用新型说明书及附图内容所作的等效结构或其他任何形式的等效变换,都包含在本实用新型的保护范围内。
再多了解一些
本文用于企业家、创业者技术爱好者查询,结果仅供参考。