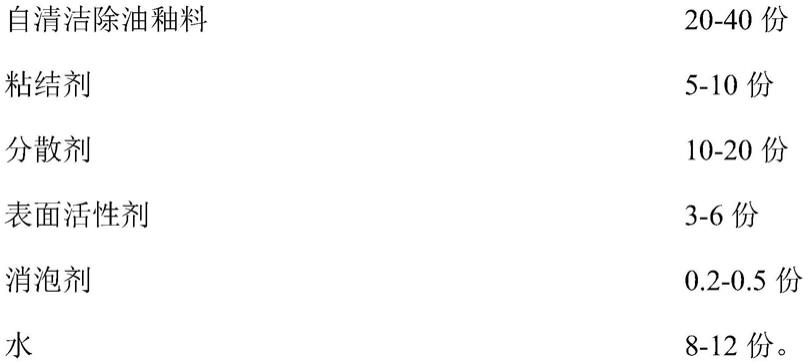
1.本发明属于材料技术领域,涉及一种釉面材料,尤其涉及一种自清洁除油釉料及其制备方法与应用。
背景技术:
2.厨房中会产生大量油烟,虽然利用抽油烟机等能够实现油烟的外排,当仍有部分油烟会沉积在厨房墙面与地面,从而产生油污。这些油污难以清除,且需要经常清理,严重影响着人们的生活品质。
3.cn 110387150a公开了一种自清洁陶瓷涂料组合物、涂料及其涂层和厨房用电器;所述自清洁陶瓷涂料组合物包括a剂和b剂,所述a剂含有含铬氧化物、含锰氧化物、具有光催化活性的纳米粒子和发泡剂;所述b剂含有硅源、有机溶剂、硅酸烷基酯和羧酸,相对于100重量份的所述a剂,所述b剂的用量为300
‑
650重量份。由发明的自清洁陶瓷涂料组合物形成的涂层可吸附烤制食物时出现的油烟与油脂等,油烟与油脂在高温环境下的涂层内催化剂的催化下,分解成二氧化碳与水排入空气中,从而使烤箱等厨房电器免于油污的清洁。但所述催化剂的催化需要在高温下进行,而且无法持续进行。
4.cn 211585704u公开了一种厨房废气清洁处理装置,包括处理装置主体,处理装置主体的底端通过螺钉固定有废气收纳口护板,处理装置主体的内部通过螺钉固定有第一抽气扇,第一抽气扇的顶端焊接有滤板定位块,滤板定位块的内部由上到下依次固定有植物纤维滤板、活性炭滤板和hepa精滤板。所述厨房废气清洁处理装置通过在内部增加过滤催化的转换结构,使大型厨房内充斥的油烟废气通过净化后得到催化产生热能,传输至蓄水加热结构中,对水进行加温,使得厨房废气得到了二次利用,且通过在装置上增加了负离子生成结构,使得装置可以对厨房内部的空气进行净化与除菌,增强了厨房内部的空气质量。但该装置无法完全避免油烟在厨房内的沉积,且所需在厨房内设置额外的装置,提高了厨房除油烟的成本。
5.cn 105802367a公开了一种复合镀膜型自清洁无机生态装饰板及其制备方法,该制备方法包括如下步骤:(1)以无机生态装饰板为基体,在无机生态装饰板表面经吹尘清洁处理后,采用光触媒亲水性涂料通过喷塑、喷涂或溶胶
‑
凝胶法镀膜负载,得到负载tio2的无机生态装饰板;(2)将步骤(1)所得负载tio2的无机生态装饰板烘干或紫外固化,烘干温度为50
‑
85℃,烘干时间为0.5
‑
3h,经自然冷却后,即得到复合镀膜型自清洁无机生态装饰板。该技术方案以无机生态装饰板为基体,能够实现对厨卫油烟、有机物、污水以及污垢的自清洁,但该自清洁需要在满足光催化的条件下进行。
6.对此,需要提供一种能够在室温下持续进行,且能够有效去除厨房内油污的自清洁除油釉料及其制备方法与应用。
技术实现要素:
7.针对现有技术存在的不足,本发明的目的在于提供一种自清洁除油釉料及其制备
方法与应用,所述自清洁除油釉料通过成分的选择能够对残余油气进行吸附,而后利用材料本身具有的光催化性能,实现对残余油气的持续分解,具有对油气进行持续处理的能力。
8.为达此目的,本发明采用以下技术方案:
9.第一方面,本发明提供了一种自清洁除油釉料,以重量份数计,所述自清洁除油釉料的制备原料包括:光催化剂2
‑
5份、助催化剂1
‑
2份、氧化锌3
‑
5份、荧光材料2
‑
4份、石英20
‑
30份、高岭土2
‑
4份、钾长石20
‑
30份。
10.所述荧光材料包括氧化钇、氧化钬、氧化轧或氧化铕中的任意一种或至少两种的组合,典型但非限制性的组合包括氧化钇与氧化钬的组合,氧化钬与氧化轧的组合,氧化轧与氧化铕的组合,或氧化钇、氧化钬、氧化轧与氧化铕的组合。
11.本发明提供的釉料通过成分的选择能够对残余油气进行吸附,而后利用材料本身具有的光催化性能,实现对残余油气的持续分解,具有对油气进行持续处理的能力。其中光催化剂与氧化锌的协同配合,使所述自清洁除油釉料制备得到的釉面具有吸油的性能,便于光催化剂对油气成分的捕捉。
12.所述荧光材料的添加使自清洁除油釉料在外界无光或弱光条件下能够发出荧光,并利用荧光进行光催化,从而使光催化能够全天24h不间断进行。
13.以重量份数计,所述自清洁除油釉料的制备原料中,光催化剂为2
‑
5份,例如可以是2份、2.5份、3份、3.5份、4份、4.5份或5份,但不限于所列举的数值,数值范围内其它未列举的数值同样适用,优选为3
‑
4份。
14.以重量份数计,所述自清洁除油釉料的制备原料中,助催化剂为1
‑
2份,例如可以是1份、1.2份、1.4份、1.5份、1.6份、1.8份或2份,但不限于所列举的数值,数值范围内其它未列举的数值同样适用。
15.以重量份数计,所述自清洁除油釉料的制备原料中,氧化锌为3
‑
5份,例如可以是3份、3.2份、3.5份、3.8份、4份、4.2份、4.5份、4.8份或5份,但不限于所列举的数值,数值范围内其它未列举的数值同样适用。
16.以重量份数计,所述自清洁除油釉料的制备原料中,荧光材料为2
‑
4份,例如可以是2份、2.4份、2.5份、2.8份、3份、3.2份、3.5份、3.6份或4份,但不限于所列举的数值,数值范围内其它未列举的数值同样适用,优选为3
‑
4份。
17.以重量份数计,所述自清洁除油釉料的制备原料中,石英为20
‑
30份,例如可以是20份、21份、22份、23份、24份、25份、26份、27份、28份、29份或30份,但不限于所列举的数值,数值范围内其它未列举的数值同样适用,优选为24
‑
28份。
18.以重量份数计,所述自清洁除油釉料的制备原料中,高岭土为2
‑
4份,例如可以是2份、2.4份、2.5份、2.8份、3份、3.2份、3.5份、3.6份或4份,但不限于所列举的数值,数值范围内其它未列举的数值同样适用。
19.以重量份数计,所述自清洁除油釉料的制备原料中,钾长石为20
‑
30份,例如可以是20份、21份、22份、23份、24份、25份、26份、27份、28份、29份或30份,但不限于所列举的数值,数值范围内其它未列举的数值同样适用,优选为24
‑
28份。
20.优选地,所述助催化剂包括四方相氧化锆。
21.优选地,所述四方相氧化锆的平均粒径为40
‑
80μm,例如可以是40μm、45μm、50μm、55μm、60μm、65μm、70μm、75μm或80μm,但不限于所列举的数值,数值范围内其它未列举的数
值同样适用。
22.优选地,所述光催化剂包括tio2。
23.优选地,所述tio2的平均粒径为40
‑
80μm,例如可以是40μm、45μm、50μm、55μm、60μm、65μm、70μm、75μm或80μm,但不限于所列举的数值,数值范围内其它未列举的数值同样适用。
24.优选地,所述氧化锌的平均粒径为40
‑
80μm,例如可以是40μm、45μm、50μm、55μm、60μm、65μm、70μm、75μm或80μm,但不限于所列举的数值,数值范围内其它未列举的数值同样适用。
25.优选地,所述荧光材料的平均粒径为30
‑
60μm,例如可以是30μm、35μm、40μm、45μm、50μm、55μm或60μm,但不限于所列举的数值,数值范围内其它未列举的数值同样适用。
26.作为本发明优选地技术方案,所述tio2为cu改性tio2。示例性的,所述cu改性tio2的制备方法包括如下步骤:
27.(1)配置cu
2
溶液,加入氨水使溶液的ph值为8
‑
10;
28.(2)溶液中加入tio2粉体,室温下搅拌4
‑
6h;
29.(3)依次进行烘干与煅烧,得到cu改性tio2。
30.其中,cu与tio2的摩尔比为(0.05
‑
0.3):1,例如可以是0.05:1、0.1:1、0.15:1、0.2:1、0.25:1或0.3:1,但不限于所列举的数值,数值范围内其它未列举的数值同样适用。
31.第二方面,本发明提供了一种如第一方面所述的自清洁除油釉料的制备方法,所述制备方法包括如下步骤:
32.(1)按配方量,球磨混合光催化剂、助催化剂、荧光材料与钾长石,得到混合料;
33.(2)按配方量球磨混合氧化锌、石英、高岭土与步骤(1)所得混合料,实现所述自清洁除油釉料的制备。
34.优选地,步骤(1)所述球磨为湿法球磨。
35.优选地,所述湿法球磨时采用无水乙醇浸没原料。
36.优选地,步骤(1)所述混合料的平均粒径为30
‑
40μm,例如可以是30μm、32μm、35μm、36μm、37μm、38μm、39μm或40μm,但不限于所列举的数值,数值范围内其它未列举的数值同样适用。
37.优选地,步骤(2)所述球磨为湿法球磨。
38.优选地,所述湿法球磨时采用无水乙醇浸没原料。
39.优选地,步骤(2)所得自清洁除油釉料的平均粒径为20
‑
35μm,例如可以是20μm、21μm、24μm、25μm、27μm、28μm、30μm、32μm或35μm,但不限于所列举的数值,数值范围内其它未列举的数值同样适用。
40.第三方面,本发明提供了一种如第一方面所述自清洁除油釉料的应用,其特征在于,所述应用包括如下步骤:
41.(a)按配方量配制自清洁除油釉料浆料;
42.(b)基底表面涂覆步骤(1)所得自清洁除油釉料浆料,烧结后得到自清洁除油釉面成品。
43.优选地,以重量份数计,步骤(a)所述自清洁除油釉料浆料的组成原料包括:
[0044][0045]
所述自清洁除油釉料浆料中自清洁除油釉料的重量份数为20
‑
40份,例如可以是20份、24份、25份、27份、30份、32份、35份、36份或40份,但不限于所列举的数值,数值范围内其它未列举的数值同样适用。
[0046]
所述自清洁除油釉料浆料中粘结剂的重量份数为5
‑
10份,例如可以是5份、6份、7份、8份、9份或10份,但不限于所列举的数值,数值范围内其它未列举的数值同样适用。
[0047]
所述自清洁除油釉料浆料中分散剂的重量份数为10
‑
20份,例如可以是10、11份、12份、13份、14份、15份、16份、17份、18份、19份或20份,但不限于所列举的数值,数值范围内其它未列举的数值同样适用。
[0048]
所述自清洁除油釉料浆料中表面活性剂的重量份数为3
‑
6份,例如可以是3份、4份、5份或6份,但不限于所列举的数值,数值范围内其它未列举的数值同样适用。
[0049]
所述自清洁除油釉料浆料中消泡剂的重量份数为0.2
‑
0.5份,例如可以是0.2份、0.3份、0.4份或0.5份,但不限于所列举的数值,数值范围内其它未列举的数值同样适用。
[0050]
所述自清洁除油釉料浆料中水的重量份数为8
‑
12份,例如可以是8份、9份、10份、11份或12份,但不限于所列举的数值,数值范围内其它未列举的数值同样适用。
[0051]
示例性的,所述粘结剂包括但不限于环氧树脂和/或酚醛树脂。
[0052]
所述分散剂包括但不限于十二烷基硫酸钠和/或聚丙烯酰胺。
[0053]
所述表面活性剂包括但不限于十八烷基二羟乙基氧化胺、十四烷基二羟乙基氧化胺或十八酰胺丙基氧化胺中的任意一种或至少两种的组合。
[0054]
所述消泡剂包括但不限于聚二甲基硅氧烷。
[0055]
优选地,步骤(b)所述烧结包括如下步骤:
[0056]
(i)以5
‑
6℃/min的升温速率升高至450
‑
500℃,保温40
‑
60min;
[0057]
(ii)以7
‑
9℃/min的升温速率升高至900
‑
1000℃,保温40
‑
60min;
[0058]
(iii)以10
‑
12℃/min的升温速率升高至1200
‑
1300℃,保温80
‑
100min;
[0059]
(iv)自然降温至室温,完成烧结。
[0060]
烧结过程中,步骤(i)的升温速率为5
‑
6℃/min,例如可以是5℃/min、5.5℃/min或6℃/min,但不限于所列举的数值,数值范围内其它未列举的数值同样适用。
[0061]
烧结过程中,步骤(i)的升温温度为450
‑
500℃,例如可以是450℃、460℃、470℃、480℃、490℃或500℃,但不限于所列举的数值,数值范围内其它未列举的数值同样适用。
[0062]
烧结过程中,步骤(i)的保温时间为40
‑
60min,例如可以是40min、45min、50min、
55min或60min,但不限于所列举的数值,数值范围内其它未列举的数值同样适用。
[0063]
烧结过程中,步骤(ii)的升温速率为7
‑
9℃/min,例如可以是7℃/min、7.5℃/min、8℃/min、8.5℃/min或9℃/min,但不限于所列举的数值,数值范围内其它未列举的数值同样适用。
[0064]
烧结过程中,步骤(ii)的升温温度为900
‑
1000℃,例如可以是900℃、910℃、920℃、930℃、940℃、950℃、960℃、970℃、980℃、990℃或1000℃,但不限于所列举的数值,数值范围内其它未列举的数值同样适用。
[0065]
烧结过程中,步骤(ii)的保温时间为40
‑
60min,例如可以是40min、45min、50min、55min或60min,但不限于所列举的数值,数值范围内其它未列举的数值同样适用。
[0066]
烧结过程中,步骤(iii)的升温速率为10
‑
12℃/min,例如可以是10℃/min、10.5℃/min、11℃/min、11.5℃/min或12℃/min,但不限于所列举的数值,数值范围内其它未列举的数值同样适用。
[0067]
烧结过程中,步骤(iii)的升温温度为1200
‑
1300℃,例如可以是1200℃、1210℃、1220℃、1230℃、1240℃、1250℃、1260℃、1270℃、1280℃、1290℃或1300℃,但不限于所列举的数值,数值范围内其它未列举的数值同样适用。
[0068]
烧结过程中,步骤(iii)的保温时间为80
‑
100min,例如可以是80min、85min、90min、95min或100min,但不限于所列举的数值,数值范围内其它未列举的数值同样适用。
[0069]
不同于现有技术中的升温速率逐渐降低,本发明通过使烧结过程中的升温速率逐渐升高,使烧结所得釉面具有一定的粗糙度,从而便于釉面对油气的吸附。
[0070]
与现有技术相比,本发明的有益效果为:
[0071]
(1)本发明提供的釉料通过成分的选择能够对残余油气进行吸附,而后利用材料本身具有的光催化性能,实现对残余油气的持续分解,具有对油气进行持续处理的能力;
[0072]
(2)本发明提供的釉料通过光催化剂与氧化锌的协同配合,使所述自清洁除油釉料制备得到的釉面具有吸油的性能,便于光催化剂对油气成分的捕捉;
[0073]
(3)本发明提供的釉料通过荧光材料的添加使自清洁除油釉料在外界无光或弱光条件下能够发出荧光,并利用荧光进行光催化,从而使光催化能够全天24h不间断进行。
具体实施方式
[0074]
下面通过具体实施方式来进一步说明本发明的技术方案。
[0075]
实施例1
[0076]
本实施例提供了一种自清洁除油釉料的制备方法,所述制备方法包括如下步骤:
[0077]
(1)按配方量,湿法球磨混合光催化剂、助催化剂、荧光材料与钾长石,得到平均粒径35μm的混合料;所述湿法球磨时采用无水乙醇浸没原料;
[0078]
(2)按配方量湿法球磨混合氧化锌、石英、高岭土与步骤(1)所得混合料,得到平均粒径25μm的自清洁除油釉料。
[0079]
所述光催化剂为平均粒径60μm的tio2;所述助催化剂为平均粒径60μm的四方相氧化锆;所述荧光材料为平均粒径40μm的氧化钇;所述氧化锌的平均粒径为60μm。
[0080]
以重量份数计,所述自清洁除油釉料的制备原料包括:光催化剂3份、助催化剂1.5份、氧化锌4份、荧光材料3份、石英25份、高岭土3份以及钾长石25份。
[0081]
实施例2
[0082]
本实施例提供了一种自清洁除油釉料的制备方法,所述制备方法包括如下步骤:
[0083]
(1)按配方量,湿法球磨混合光催化剂、助催化剂、荧光材料与钾长石,得到平均粒径35μm的混合料;所述湿法球磨时采用无水乙醇浸没原料;
[0084]
(2)按配方量湿法球磨混合氧化锌、石英、高岭土与步骤(1)所得混合料,得到平均粒径25μm的自清洁除油釉料。
[0085]
所述光催化剂为平均粒径60μm的tio2;所述助催化剂为平均粒径60μm的四方相氧化锆;所述荧光材料为平均粒径40μm的氧化钇;所述氧化锌的平均粒径为60μm。
[0086]
以重量份数计,所述自清洁除油釉料的制备原料包括:光催化剂2份、助催化剂2份、氧化锌5份、荧光材料2份、石英20份、高岭土2份以及钾长石30份。
[0087]
实施例3
[0088]
本实施例提供了一种自清洁除油釉料的制备方法,所述制备方法包括如下步骤:
[0089]
(1)按配方量,湿法球磨混合光催化剂、助催化剂、荧光材料与钾长石,得到平均粒径35μm的混合料;所述湿法球磨时采用无水乙醇浸没原料;
[0090]
(2)按配方量湿法球磨混合氧化锌、石英、高岭土与步骤(1)所得混合料,得到平均粒径25μm的自清洁除油釉料。
[0091]
所述光催化剂为平均粒径60μm的tio2;所述助催化剂为平均粒径60μm的四方相氧化锆;所述荧光材料为平均粒径40μm的氧化钇;所述氧化锌的平均粒径为60μm。
[0092]
以重量份数计,所述自清洁除油釉料的制备原料包括:光催化剂5份、助催化剂1份、氧化锌3份、荧光材料4份、石英30份、高岭土4份以及钾长石20份。
[0093]
实施例4
[0094]
本实施例提供了一种自清洁除油釉料的制备方法,所述制备方法包括如下步骤:
[0095]
(1)按配方量,湿法球磨混合光催化剂、助催化剂、荧光材料与钾长石,得到平均粒径30μm的混合料;所述湿法球磨时采用无水乙醇浸没原料;
[0096]
(2)按配方量湿法球磨混合氧化锌、石英、高岭土与步骤(1)所得混合料,得到平均粒径20μm的自清洁除油釉料。
[0097]
所述光催化剂为平均粒径40μm的tio2;所述助催化剂为平均粒径40μm的四方相氧化锆;所述荧光材料为平均粒径30μm的氧化钇与氧化铕(质量比1:1);所述氧化锌的平均粒径为40μm。
[0098]
以重量份数计,所述自清洁除油釉料的制备原料包括:光催化剂3份、助催化剂1.5份、氧化锌4份、荧光材料3份、石英25份、高岭土3份以及钾长石25份。
[0099]
实施例5
[0100]
本实施例提供了一种自清洁除油釉料的制备方法,所述制备方法包括如下步骤:
[0101]
(1)按配方量,湿法球磨混合光催化剂、助催化剂、荧光材料与钾长石,得到平均粒径40μm的混合料;所述湿法球磨时采用无水乙醇浸没原料;
[0102]
(2)按配方量湿法球磨混合氧化锌、石英、高岭土与步骤(1)所得混合料,得到平均粒径35μm的自清洁除油釉料。
[0103]
所述光催化剂为平均粒径80μm的tio2;所述助催化剂为平均粒径80μm的四方相氧化锆;所述荧光材料为平均粒径60μm的氧化钇与氧化钬(质量比1:1);所述氧化锌的平均粒
径为80μm。
[0104]
以重量份数计,所述自清洁除油釉料的制备原料包括:光催化剂3份、助催化剂1.5份、氧化锌4份、荧光材料3份、石英25份、高岭土3份以及钾长石25份。
[0105]
实施例6
[0106]
本实施例提供了一种自清洁除油釉料的制备方法,除光催化剂为cu改性tio2外,其余均与实施例1相同。
[0107]
所述cu改性tio2采用如下方法制备:
[0108]
(1)配置cu
2
溶液,加入氨水使溶液的ph值为9;
[0109]
(2)溶液中加入tio2粉体,室温下搅拌5h;
[0110]
(3)依次进行烘干与煅烧,得到cu改性tio2。
[0111]
其中,cu与tio2的摩尔比为0.2:1。
[0112]
实施例7
[0113]
本实施例提供了一种自清洁除油釉料的制备方法,除光催化剂为cu改性tio2外,其余均与实施例1相同。
[0114]
所述cu改性tio2采用如下方法制备:
[0115]
(1)配置cu
2
溶液,加入氨水使溶液的ph值为8;
[0116]
(2)溶液中加入tio2粉体,室温下搅拌4h;
[0117]
(3)依次进行烘干与煅烧,得到cu改性tio2。
[0118]
其中,cu与tio2的摩尔比为0.05:1。
[0119]
实施例8
[0120]
本实施例提供了一种自清洁除油釉料的制备方法,除光催化剂为cu改性tio2外,其余均与实施例1相同。
[0121]
所述cu改性tio2采用如下方法制备:
[0122]
(1)配置cu
2
溶液,加入氨水使溶液的ph值为10;
[0123]
(2)溶液中加入tio2粉体,室温下搅拌6h;
[0124]
(3)依次进行烘干与煅烧,得到cu改性tio2。
[0125]
其中,cu与tio2的摩尔比为0.3:1。
[0126]
对比例1
[0127]
本对比例提供了一种釉料的制备方法,除将助催化剂替换为等重量份数的光催化剂外,其余均与实施例1相同。
[0128]
对比例2
[0129]
本对比例提供了一种釉料的制备方法,除将氧化锌替换为等重量份数的高岭土外,其余均与实施例1相同。
[0130]
对比例3
[0131]
本对比例提供了一种釉料的制备方法,除将荧光材料替换为等重量份数的光催化剂外,其余均与实施例1相同。
[0132]
应用例1
[0133]
本应用例对实施例1提供的自清洁除油釉料进行应用,所述应用包括如下步骤:
[0134]
(a)按配方量配制自清洁除油釉料浆料;
[0135]
(b)基底表面涂覆步骤(1)所得自清洁除油釉料浆料,烧结后得到自清洁除油釉面成品。
[0136]
以重量份数计,步骤(a)所述自清洁除油釉料浆料的组成原料包括:自清洁除油釉料20份、粘结剂5份、分散剂20份、表面活性剂3份、消泡剂0.5份以及水12份。
[0137]
所述粘结剂为市售环氧树脂,所述分散剂为十二烷基硫酸钠,所述表面活性剂为十八烷基二羟乙基氧化胺,所述消泡剂为市售聚二甲基硅氧烷。
[0138]
步骤(b)所述烧结包括如下步骤:
[0139]
(i)以5℃/min的升温速率升高至450℃,保温60min;
[0140]
(ii)以7℃/min的升温速率升高至900℃,保温60min;
[0141]
(iii)以10℃/min的升温速率升高至1200℃,保温100min;
[0142]
(iv)自然降温至室温,完成烧结。
[0143]
应用例2
[0144]
本应用例对实施例2提供的自清洁除油釉料进行应用,所述应用的步骤与应用例1相同。
[0145]
应用例3
[0146]
本应用例对实施例3提供的自清洁除油釉料进行应用,所述应用的步骤与应用例1相同。
[0147]
应用例4
[0148]
本应用例对实施例4提供的自清洁除油釉料进行应用,所述应用的步骤与应用例1相同。
[0149]
应用例5
[0150]
本应用例对实施例5提供的自清洁除油釉料进行应用,所述应用的步骤与应用例1相同。
[0151]
应用例6
[0152]
本应用例对实施例6提供的自清洁除油釉料进行应用,所述应用的步骤与应用例1相同。
[0153]
应用例7
[0154]
本应用例对实施例7提供的自清洁除油釉料进行应用,所述应用的步骤与应用例1相同。
[0155]
应用例8
[0156]
本应用例对实施例8提供的自清洁除油釉料进行应用,所述应用的步骤与应用例1相同。
[0157]
应用例9
[0158]
本应用例对实施例1提供的自清洁除油釉料进行应用,所述应用包括如下步骤:
[0159]
(a)按配方量配制自清洁除油釉料浆料;
[0160]
(b)基底表面涂覆步骤(1)所得自清洁除油釉料浆料,烧结后得到自清洁除油釉面成品。
[0161]
以重量份数计,步骤(a)所述自清洁除油釉料浆料的组成原料包括:自清洁除油釉料40份、粘结剂10份、分散剂10份、表面活性剂6份、消泡剂0.2份以及水8份。
[0162]
所述粘结剂为市售环氧树脂,所述分散剂为十二烷基硫酸钠,所述表面活性剂为十八烷基二羟乙基氧化胺,所述消泡剂为市售聚二甲基硅氧烷。
[0163]
步骤(b)所述烧结包括如下步骤:
[0164]
(i)以6℃/min的升温速率升高至500℃,保温40min;
[0165]
(ii)以9℃/min的升温速率升高至1000℃,保温40min;
[0166]
(iii)以12℃/min的升温速率升高至1300℃,保温80min;
[0167]
(iv)自然降温至室温,完成烧结。
[0168]
应用例10
[0169]
本应用例对实施例1提供的自清洁除油釉料进行应用,除步骤(b)所述烧结包括如下步骤:
[0170]
(i)以10℃/min的升温速率升高至450℃,保温60min;
[0171]
(ii)以7℃/min的升温速率升高至900℃,保温60min;
[0172]
(iii)以5℃/min的升温速率升高至1200℃,保温100min;
[0173]
(iv)自然降温至室温,完成烧结。
[0174]
其余均与应用例1相同。
[0175]
对比应用例1
[0176]
本对比应用例利用对比例1提供的釉料进行应用,所述应用的步骤与应用例1相同。
[0177]
对比应用例2
[0178]
本对比应用例利用对比例2提供的釉料进行应用,所述应用的步骤与应用例1相同。
[0179]
对比应用例3
[0180]
本对比应用例利用对比例3提供的釉料进行应用,所述应用的步骤与应用例1相同。
[0181]
对应用例1
‑
10以及对比应用例1
‑
3所得成品的去除vocs能力进行测试,测试方法为:取10cm
×
10cm的成品,放置于相同体积的密闭空间内,密闭空间中通入一定浓度的甲醛气体,每间隔12h进行12h的光照,48h后对密闭空间中的甲醛气体浓度进行测试,得到vocs去除率。
[0182]
所述vocs去除率=[(初始甲醛浓度
‑
终点甲醛浓度)/初始甲醛浓度]
×
100%
[0183]
所得结果如表1所示。
[0184]
表1
[0185] vocs去除率(%)应用例163.5应用例261.7应用例361.2应用例462.3应用例562.6应用例665.9应用例764.7
应用例865.1应用例963.2应用例1057.6对比应用例150.8对比应用例253.4对比应用例345.7
[0186]
由表1可知,本技术提供的自清洁除油釉料能够有效去除以甲醛为代表的vocs,其vocs去除率为60%以上。
[0187]
由应用例10与应用例1的比较可知,烧结升温速率逐渐降低不利于提高所得釉面成品的vocs去除率。
[0188]
由对比应用例1与应用例1的比较可知,助催化剂的使用能够有效提高所得釉面成品的vocs去除率。
[0189]
由对比应用例2与应用例1的比较可知,氧化锌的使用能够通过提高对vocs的吸附性能,有效提高所得釉面成品的vocs去除率。
[0190]
由对比应用例3与应用例1的比较可知,荧光材料的使用能够通过提高催化过程的持续性,有效提高所得釉面成品的vocs去除率。
[0191]
综上所述,本发明提供的釉料通过成分的选择能够对残余油气进行吸附,而后利用材料本身具有的光催化性能,实现对残余油气的持续分解,具有对油气进行持续处理的能力;本发明提供的釉料通过光催化剂与氧化锌的协同配合,使所述自清洁除油釉料制备得到的釉面具有吸油的性能,便于光催化剂对油气成分的捕捉;本发明提供的釉料通过荧光材料的添加使自清洁除油釉料在外界无光或弱光条件下能够发出荧光,并利用荧光进行光催化,从而使光催化能够全天24h不间断进行。
[0192]
以上所述的具体实施例,对本发明的目的、技术方案和有益效果进行了进一步详细说明,所应理解的是,以上所述仅为本发明的具体实施例而已,并不用于限制本发明,凡在本发明的精神和原则之内,所做的任何修改、等同替换、改进等,均应包含在本发明的保护范围之内。
再多了解一些
本文用于企业家、创业者技术爱好者查询,结果仅供参考。