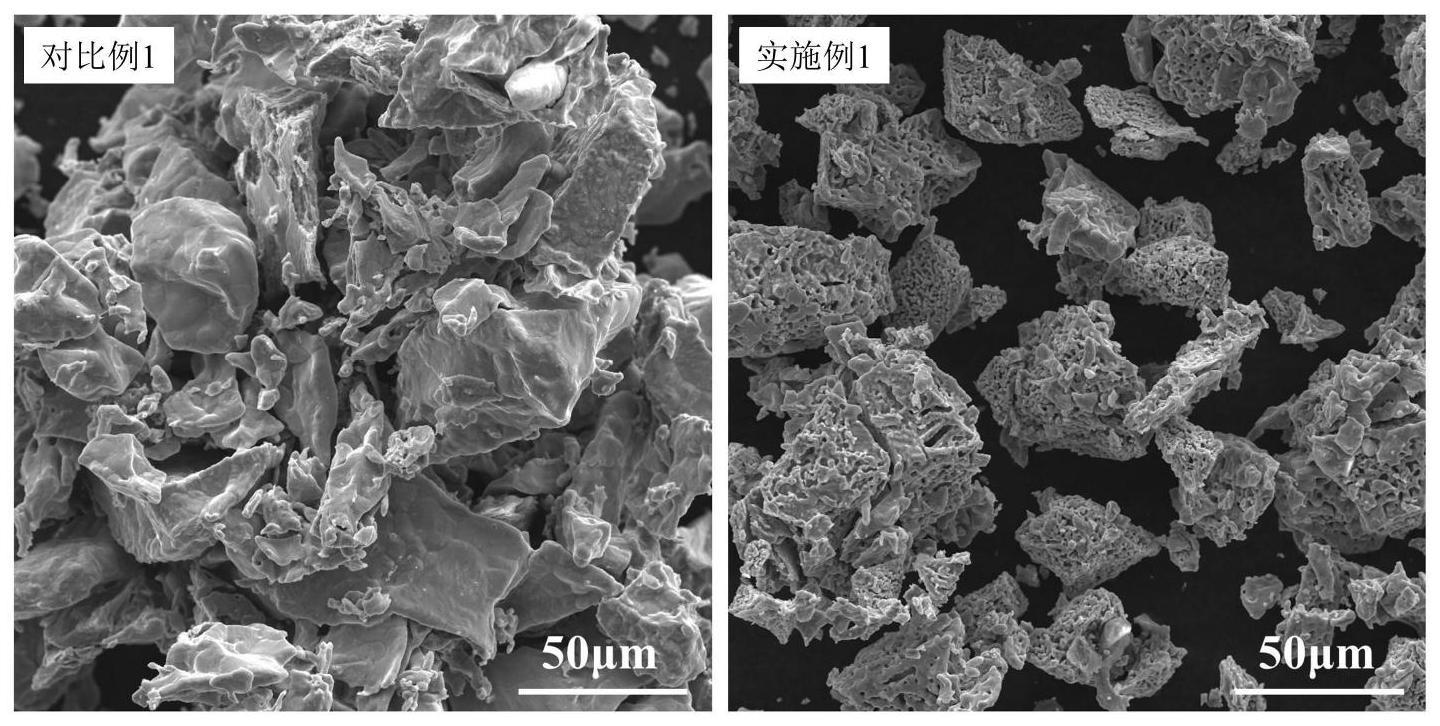
1.本发明涉及一种铁精矿氢还原制备铁粉的方法,特别涉及一种通过机械活化耦合氧化活化提高粗粒级铁精矿氢还原活性、降低氢还原温度,且获得高分散性常规粒级铁粉的方法,属于金属粉末材料制备技术领域。
背景技术:
2.还原铁粉是现代工业中应用最为广泛的金属材料之一,可用于粉末冶金、焊材、软磁材料、火焰切割与不锈钢切割、金刚石工具及硬质合金领域。据统计,2020年我国铁粉出货量约占世界总量的29%,且产量呈逐年增长趋势,其中还原铁粉占铁粉总产量的50%以上。随着我国工业、制造业的高质量发展,还原铁粉需求量必将不断增加。
3.目前,还原铁粉一般是以铁鳞或超纯铁精矿为原料,经过碳-氢两步还原法制备得到。未来还原铁粉制备工艺必将逐渐向全氢还原发展;另一方面,铁鳞作为轧钢工序的副产物,也存在性能波动大、产量受限的问题。随着铁精矿资源开采及选别工艺技术的进步,超纯铁精矿的产量逐年增加、性质相对稳定,以及冶金行业绿色低碳发展,利用超纯铁精矿氢还原制取铁粉具有广阔的发展和应用前景。
4.还原铁粉按照粒度划分为不同的类别:150~500μm的粗粉、45~150μm的中等粉、10~45μm的细粉、0.5~10μm的极细粉以及小于0.5μm的超细粉。其中,10μm以上的常规还原铁粉需求量最大,约占还原铁粉总产量的85%以上。由于低温还原时得到的铁粉纯度较低,目前,常规还原铁粉的制备工艺都在900℃以上的高温条件下进行,以获得较高的铁粉纯度,不仅工序能耗较高,而且在高温还原过程中,超纯铁精矿颗粒局部熔化及表面产生铁晶须等因素都会造成颗粒的团聚与黏结,会使铁粉出现板结现象。并且,温度越高铁粉板结现象越严重,还原后往往需要进行研磨才能获得分散良好的铁粉。然而,由于铁本身良好的延展性,很难低成本地将板结铁粉磨细,磨矿能耗较高。同时,需要采用特殊保护机制的设备或方法避免研磨过程引入氧及其他杂质,如采用氮气气流分级机或在氮气室内进行破碎等,这也增加了工序成本。
5.目前,已有的降低超纯铁精矿氢还原温度的方法主要是通过超细研磨等手段,将超纯铁精矿粒度减小至10μm以下,从而大幅提高超纯铁精矿比表面积与反应活性,降低氢还原温度。但由于超纯铁精矿粒级的极大细化,用于制备常规粒级铁粉时也面临着适应性以及经济成本方面的问题。
6.因此,如果能在不大幅降低超纯铁精矿粒级的情况下,提高超纯铁精矿的反应活性,降低氢还原温度,则可缓解传统氢还原过程的铁粉结块现象,一步法直接制备得到分散良好的常规粒级铁粉,从而降低工序能耗与成本,对于10μm以上常规粒级还原铁粉低碳绿色制备技术的发展具有重要意义。
技术实现要素:
7.针对目前10μm以上常规还原铁粉高温还原易结块、二次研磨能耗及成本高,低温
还原时铁粉纯度难以满足要求的问题,本发明的目的是在于提供一种基于耦合活化的铁精矿氢还原制备铁粉的方法,该方法对铁精矿进行高压辊磨和氧化的耦合活化手段,促进铁精矿的微裂纹产生、活性表面增加、晶格活化与无定形,从而在不大幅减小铁精矿粒级的情况下提高其反应活性,降低氢还原温度,无需二次研磨即可获得分散良好的常规粒级铁粉,降低了常规还原铁粉制备工序的能耗与成本,具有工艺简单、节能环保的优点。
8.为了实现上述技术目的,本发明提供了一种基于耦合活化的铁精矿氢还原制备铁粉的方法,该方法是将铁精矿原料依次进行高压辊磨活化和氧化活化后,通过氢还原焙烧,即得铁粉。
9.本发明技术方案的关键是在于采用高压辊磨和氧化的耦合活化技术手段,能够促进铁精矿的微裂纹产生、活性表面增加、晶格活化与无定形,有利于后续的氢还原过程。一方面,高压辊磨不同于球磨、搅拌磨、振动磨等以磨矿介质与粉体相互作用为主的机械活化方式,高压辊磨活化是以粉体之间相互作用为主的料层层压粉碎方式,机械力对粉体粒度的影响相对较小,主要是作用于颗粒内部微裂纹产生、颗粒表面粗糙度增加以及晶格畸变与无定形化,可在不大幅减小铁精矿粒级的情况下增加铁精矿的活性表面,提高其气固反应活性;另一方面,氧化活化过程fe3o4的晶型转变与体积收缩,改善了颗粒表面与孔隙结构,同时,氧化活化后形成的α-fe2o3在后续氢还原过程中发生晶体结构转变与体积膨胀,使得超纯铁精矿进一步产生内部裂纹与晶体结构缺陷,有利于气相的扩散与还原反应的进行。第三方面,高压辊磨活化与氧化活化具有耦合效应,高压辊磨活化后超纯铁精矿内部微裂纹的产生、活性表面的增加以及晶格无定形化均有利于预氧化反应进行,可降低预氧化温度,从而避免预氧化后料层结块,并且耦合活化后的铁精矿反应活性更高,有利于后续氢还原温度的降低。综上,在经过高压辊磨和氧化的耦合活化技术手段后,可以在不大幅减小铁精矿粒级的情况下提高其反应活性,降低还原铁粉制备过程的氢还原温度,无需二次研磨即可得到分散良好的铁粉。
10.作为一个优选的方案,所述铁精矿原料主要物相为磁铁矿,tfe质量含量大于71.5%,粒度为20~150μm,且粒径d
50
不小于45μm,水分质量百分比含量为6.5~7.5%。铁精矿原料为粒径10μm以上的常规粒径铁精矿,优选的铁精矿粒度为20~150μm。铁精矿原料为tfe质量含量大于71.5%的超纯铁精矿,铁精矿纯度越高,相应可以获得纯度越高的还原铁粉。而水分控制在合适的范围内有利于高压辊磨过程,适宜的水分含量有利于提高颗粒之间的分子与毛细作用力,从而在层压粉碎过程中获得更高的颗粒间剪切应力,提高辊磨活化效果;但当水分含量过高时,料层挤压形成的料饼塑性提升,高压辊磨活化效率降低。
11.作为一个优选的方案,所述高压辊磨活化的条件为:压力为2.1~2.45mpa,圆辊转速为20~23r/min。作为进一步优选的方案,高压辊磨是采用合金钢镶嵌硬质合金柱钉的高压辊磨机,辊面间距1~2mm。合金柱钉辊面具有更好的耐磨性能,控制合理的辊面间距有利于提升高压辊磨机械力作用效率。高压辊磨活化过程中,足够的辊磨压力能够保证超纯铁精矿的充分活化。但辊磨压力过高会使得超纯铁精矿粒度细化程度过大,同时辊磨过程的能效降低,因此要严格控制辊磨压力的上限与下限。在高压辊磨活化过程中,随着高压辊磨圆辊转速加快,料层加压速度提高,辊磨处理能力增大,但圆辊转速过快时辊磨活化效果较差。
12.作为一个优选的方案,所述高压辊磨活化所得铁精矿的粒径d
50
大于30μm,微裂纹
含量增长率ξh=(lh-l0)/l0,颗粒粗糙度相对变化rh=(fh-f0)/f0,无定形度增加比例ηh=(xh-x0)/x0;其中,l0和lh分别为铁精矿原料和高压辊磨活化后铁精矿的微裂纹含量,单位为cm3/g;f0和fh分别为铁精矿原料和高压辊磨活化后铁精矿的分形维数,无量纲;x0和xh分别为铁精矿原料和高压辊磨活化后铁精矿的晶体无定形度,单位为%。通过调控适宜的高压辊磨机械活化工艺参数,可以促进铁精矿活性表面的增加、晶格的活化与无定形,从而提高铁精矿的反应活性,且由于反应活性的提升,后续氧化活化的适宜温度降低至t
pr
=850-150
×
[0.5
×
(ξ
h2
r
h2
)]
0.5
-120
×
ηh。
[0013]
作为一个较优选的方案,所述高压辊磨活化所得铁精矿微裂纹含量增长率ξh不低于30%,颗粒粗糙度相对变化rh不低于15%,无定形度增加比例ηh大于50%。
[0014]
作为一个优选的方案,所述氧化活化的条件为:温度t
pr
=850-150
×
[0.5
×
(ξ
h2
r
h2
)]
0.5
-120
×
ηh,单位为℃,时间为10~20min。氧化活化时间过长或氧化活化温度过高,则容易导致铁精矿板结,当氧化活化温度较低或氧化活化时间相对过短时,达不到氧化活化的效果。在基于高压辊磨活化的基础上,可以在相对较低的温度下达到氧化活化效果,且避免铁精矿板结。
[0015]
作为一个较优选的方案,所述氧化活化所得铁精矿裂纹含量增长率ξm=(lm-l0)/l0,颗粒粗糙度相对变化rm=(fm-f0)/f0,氧化程度wm=(w0-wm)/w0;l0和lm分别为铁精矿原料和氧化活化后铁精矿的微裂纹含量,单位为cm3/g;f0和fm分别为铁精矿原料和氧化活化后铁精矿的分形维数,无量纲;w0和wm分别为氧化活化前和氧化活化后铁精矿的feo质量含量,单位为%。
[0016]
作为一个优选的方案,所述氧化活化所得铁精矿的氧化程度wm大于85%。氧化活化过程中,颗粒表面与孔隙结构的改善伴随着fe3o4晶型转变与体积收缩,氧化程度越高,铁精矿活化效果越好。
[0017]
作为一个优选的方案,所述氢还原焙烧的条件为:温度t
re
=950-120
×
[0.5
×
(ξ
m2
r
m2
)]
0.5
-90
×wm2
,单位为℃,时间为2~4h,氢气通入量为800~1200nm3/t铁精矿;其中,ξm=(lm-l0)/l0,rm=(fm-f0)/f0,wm=(w0-wm)/w0;l0和lm分别为铁精矿原料和氧化活化后铁精矿的微裂纹含量,单位为cm3/g;f0和fm分别为铁精矿原料和氧化活化后铁精矿的分形维数,无量纲;w0和wm分别为氧化活化前和氧化活化后铁精矿的feo质量含量,单位为%。本发明的氢还原焙烧过程是还原经过高压辊磨活化耦合氧化活化所得铁精矿,铁精矿的孔隙结构明显改善,增加其新生活性表面、无定形度与晶格活化程度,可将后续氢还原适宜温度降低至t
re
=950-120
×
[0.5
×
(ξ
m2
r
m2
)]
0.5
-90
×wm2
。氢还原焙烧的时间在2小时以上,可以保证铁粉的充分还原,但过长的氢还原时间容易导致铁粉板结。进一步优选的方案,在铁精矿氢还原焙烧过程中,可以通过采用氢气预热器将氢气预先加热至还原温度。由于氢还原反应为吸热反应,将氢气预先加热至还原温度可以避免由于热交换导致的铁精矿温度下降,提高还原反应效率。
[0018]
作为一个优选的方案,所述氧化活化和所述氢还原焙烧在钢带气氛加热炉或推舟气氛加热炉中进行,铁精矿原料的布料厚度为5~15mm。预氧化和氢还原是在钢带气氛加热炉或推舟气氛加热炉中进行的,有利于还原反应的充分进行。而铁精矿原料的布料厚度影响料层的透气率,因此不宜过高,最好是控制在15mm以下。
[0019]
与现有技术相比,本发明技术方案的优点在于:
[0020]
(1)本发明利用高压辊磨料层层压粉碎过程中“以粉体间相互作用为主”的机械活化方式,利用机械力作用于颗粒内部微裂纹的产生、颗粒表面粗糙度的增加,以及晶格畸变与无定形化,可在不大幅减小铁精矿粒级的情况下,增加超纯铁精矿的活性表面,提高其气固反应活性,同时,由于高压辊磨是采用挤压排料的连续作用过程,其具有更高的机械活化效率与作业能力。
[0021]
(2)本发明利用预氧化过程中fe3o4的晶型转变与体积收缩,改善了颗粒表面与孔隙结构,促进了超纯铁精矿的晶格畸变与无定形化,预氧化后形成的α-fe2o3在氢还原过程中会再次发生晶体结构转变与体积膨胀,进一步产生内部裂纹与晶体结构缺陷,有利于气相的扩散与后续还原反应的进行,降低氢还原温度。
[0022]
(3)本发明采用的高压辊磨活化和氧化活化具有明显的耦合效应,一方面高压辊磨活化后,超纯铁精矿内部微裂纹的产生、活性表面的增加以及晶格无定形化均有利于预氧化反应进行,从而降低预氧化温度,避免预氧化后料层结块。另一方面,预氧化后超纯铁精矿表面与孔隙结构的改善以及α-fe2o3在还原过程的体积膨胀,可以弥补高压辊磨后铁精矿粒度细化带来的料层结构致密等不利因素,并且耦合活化后的铁精矿反应活性更高,有利于后续氢还原温度的降低。
[0023]
(4)本发明采用高压辊磨和氧化的耦合活化方法,能够促进铁精矿的微裂纹产生、活性表面增加、晶格活化与无定形,从而在不大幅减小铁精矿粒级的情况下提高其反应活性,降低氢还原温度。同时,氧化活化过程能够将超纯铁精矿进行预先加热,避免了传统氢还原升温过程中氢气利用率低的问题,结合氢气预热等方式,使得料床温度场更加均匀、稳定,可以提高氢气利用率,有利于低温下氢还原反应的快速、充分进行。
[0024]
综上所述,本发明利用高压辊磨层压粉碎的机械活化原理耦合预氧化活化,在不大幅减小铁精矿粒级的情况下提高其反应活性,同时结合还原过程的氢气预热等方式,可将常规粒级超纯铁精矿的氢还原温度降低至850℃以下,还原后无需二次研磨即可获得分散良好的高纯铁粉,降低了常规粒级还原铁粉制备工序的能耗与成本,具有工艺简单、节能环保的优点。
附图说明
[0025]
图1为对比例1与实施例1中所得铁粉的颗粒形貌图。
具体实施方式
[0026]
为了进一步说明本发明的内容,下文将结合较佳的实施例对本发明作更全面、细致地描述,但本发明的保护范围并不限于以下具体的实施例。除非另有定义,下文中所使用的所有专业术语与本领域技术人员通常理解的含义相同。本文中所使用的专业术语只是为了描述具体实施例的目的,并不是旨在限制本发明的保护范围。
[0027]
以下实施例中涉及参数测试方法均为本领域常规的测试方法:
[0028]
其中,微裂纹含量l是采用bet法测得的铁精矿微孔及介孔孔容。
[0029]
分形维数f是通过图像处理软件统计铁精矿颗粒(不少于3000个)的面积s和周长a,将lns与lna作图,采用最小二乘法拟合所得直线的斜率,即为铁精矿颗粒的分形维数。
[0030]
晶体无定形度x是根据铁精矿xrd衍射图谱(扫描速度不超过2
°
/min),计算出活化
后铁精矿相对未活化标准磁铁矿的衍射峰面积变化率,即晶体无定形度=(未活化标准磁铁矿衍射峰面积-活化后铁精矿衍射峰面积)/(未活化标准磁铁矿衍射峰面积)。
[0031]
feo质量含量依据gb/t 6730.8-2016测得。
[0032]
对比例1
[0033]
采用表1的超纯铁精矿,将其在压力2.1mpa,铁精矿水分7.5%,圆辊转速23r/min,辊面间距1.5mm的条件下进行高压辊磨活化。机械活化后的超纯铁精矿d
50
为43μm,微裂纹含量增长率ξh为31%,颗粒粗糙度相对变化rh为15%,无定形度增加比例ηh为52%。
[0034]
将机械活化后的超纯铁精矿在钢带气氛加热炉中进行氢还原,料层高度为5mm。由于未经氧化活化处理,活化的超纯铁精矿微裂纹含量增长率ξh为31%,颗粒粗糙度相对变化rh为15%,氧化程度wm为0%。在氢还原温度950-120
×
[0.5
×
(0.312 0.152)]
0.5
-90
×02
=921(单位为℃),还原时间2h,氢气用量为800nm3/t超纯铁精矿的条件下,还原后得到的铁粉发生结块,如图1所示,铁粉纯度95.53%。
[0035]
对比例2
[0036]
采用表1的超纯铁精矿,将其依次在钢带气氛加热炉中进行预氧化与氢还原,料层高度5mm。在预氧化温度751℃,预氧化时间10min的条件下,活化后的超纯铁精矿微裂纹含量增长率ξh为7%,颗粒粗糙度相对变化rh为14%,氧化程度wm为75%。
[0037]
进一步地,在氢还原温度950-120
×
[0.5
×
(0.072 0.142)]
0.5
-90
×
0.752=886(单位为℃),还原时间2h,氢气用量为800nm3/t超纯铁精矿的条件下,还原后得到的铁粉发生结块,铁粉纯度为95.11%。
[0038]
对比例3
[0039]
采用表1的超纯铁精矿,将其在压力1.7mpa,铁精矿水分5.5%,圆辊转速20r/min,辊面间距2mm的条件下进行高压辊磨活化。机械活化后的超纯铁精矿d
50
为47μm,微裂纹含量增长率ξh为23%,颗粒粗糙度相对变化rh为11%,无定形度增加比例ηh为31%。
[0040]
将机械活化后的超纯铁精矿在推舟气氛加热炉中进行预氧化与氢还原,料层高度为5mm。在预氧化温度850-150
×
[0.5
×
(0.232 0.112)]
0.5
-120
×
0.31=786(单位为℃),预氧化时间10min的条件下,耦合活化的超纯铁精矿微裂纹含量增长率ξh为29%,颗粒粗糙度相对变化rh为26%,氧化程度wm为82%。
[0041]
进一步地,在氢还原温度950-120
×
[0.5
×
(0.292 0.262)]
0.5
-90
×
0.822=856(单位为℃),还原时间3h,氢气用量为1000nm3/t超纯铁精矿的条件下,还原后得到的铁粉无结块现象,铁粉纯度为97.01%。
[0042]
由于辊磨压力以及铁精矿水分含量较低,在层压粉碎过程中颗粒剪切应力不足,颗粒微裂纹、粗糙度以及无定形度增加比例相对较低,导致机械活化效果较差。在适宜制度下进行预氧化活化后,铁精矿氧化程度仅为82%,耦合活化的铁精矿活性不足。在相应氢还原制度下,所得铁粉虽无结块现象,但纯度较低。
[0043]
实施例1
[0044]
采用表1的超纯铁精矿,将其在压力2.1mpa,铁精矿水分7.5%,圆辊转速23r/min,辊面间距1.5mm的条件下进行高压辊磨活化。机械活化后的超纯铁精矿d
50
为43μm,微裂纹含量增长率ξh为31%,颗粒粗糙度相对变化rh为15%,无定形度增加比例ηh为52%。
[0045]
将机械活化后的超纯铁精矿在钢带气氛加热炉中进行预氧化与氢还原,料层高度
为5mm。在预氧化温度850-150
×
[0.5
×
(0.312 0.152)]
0.5
-120
×
0.52=751(单位为℃)预氧化温度10min的条件下,耦合活化的超纯铁精矿微裂纹含量增长率ξh为42%,颗粒粗糙度相对变化rh为35%,氧化程度wm为91%。
[0046]
进一步地,在氢还原温度950-120
×
[0.5
×
(0.422 0.352)]
0.5
-90
×
0.912=829(单位为℃),还原时间2h,氢气用量为800nm3/t超纯铁精矿的条件下,还原后得到的铁粉无结块现象,如图1所示,铁粉纯度为98.83%。
[0047]
实施例2
[0048]
采用表1的超纯铁精矿,将其在压力2.45mpa,铁精矿水分6.5%,圆辊转速20r/min,辊面间距1mm的条件下进行高压辊磨活化。机械活化后的超纯铁精矿d
50
为35μm,微裂纹含量增长率ξh为46%,颗粒粗糙度相对变化rh为27%,无定形度增加比例ηh为72%。
[0049]
将机械活化后的超纯铁精矿在钢带气氛加热炉中进行预氧化与氢还原,料层高度为15mm。在预氧化温度850-150
×
[0.5
×
(0.462 0.272)]
0.5
-120
×
0.72=707(单位为℃),预氧化温度20min的条件下,耦合活化的超纯铁精矿微裂纹含量增长率ξh为53%,颗粒粗糙度相对变化rh为45%,氧化程度wm为89%。
[0050]
进一步地,在氢还原温度950-120
×
[0.5
×
(0.532 0.452)]
0.5
-90
×
0.892=820(单位为℃),还原时间4h,氢气用量为1200nm3/t超纯铁精矿的条件下,还原后得到的铁粉无结块现象,铁粉纯度为98.71%。
[0051]
实施例3
[0052]
采用表1的超纯铁精矿,将其在压力2.35mpa,铁精矿水分7.5%,圆辊转速23r/min,辊面间距1mm的条件下进行高压辊磨活化。机械活化后的超纯铁精矿d
50
为34μm,微裂纹含量增长率ξh为44%,颗粒粗糙度相对变化rh为28%,无定形度增加比例ηh为70%。
[0053]
将机械活化后的超纯铁精矿在推舟气氛加热炉中进行预氧化与氢还原,料层高度为5mm。在预氧化温度850-150
×
[0.5
×
(0.442 0.282)]
0.5
-120
×
0.70=711(单位为℃),预氧化温度10min的条件下,耦合活化的超纯铁精矿微裂纹含量增长率ξh为55%,颗粒粗糙度相对变化rh为47%,氧化程度wm为96%。
[0054]
进一步地,在氢还原温度950-120
×
[0.5
×
(0.552 0.472)]
0.5
-90
×
0.962=806(单位为℃),还原时间2h,氢气用量为800nm3/t超纯铁精矿的条件下,还原后得到的铁粉无结块现象,铁粉纯度为99.07%。
[0055]
表1超纯铁精矿化学成分(/wt.%)及粒度(/μm)
[0056]
再多了解一些
本文用于创业者技术爱好者查询,仅供学习研究,如用于商业用途,请联系技术所有人。