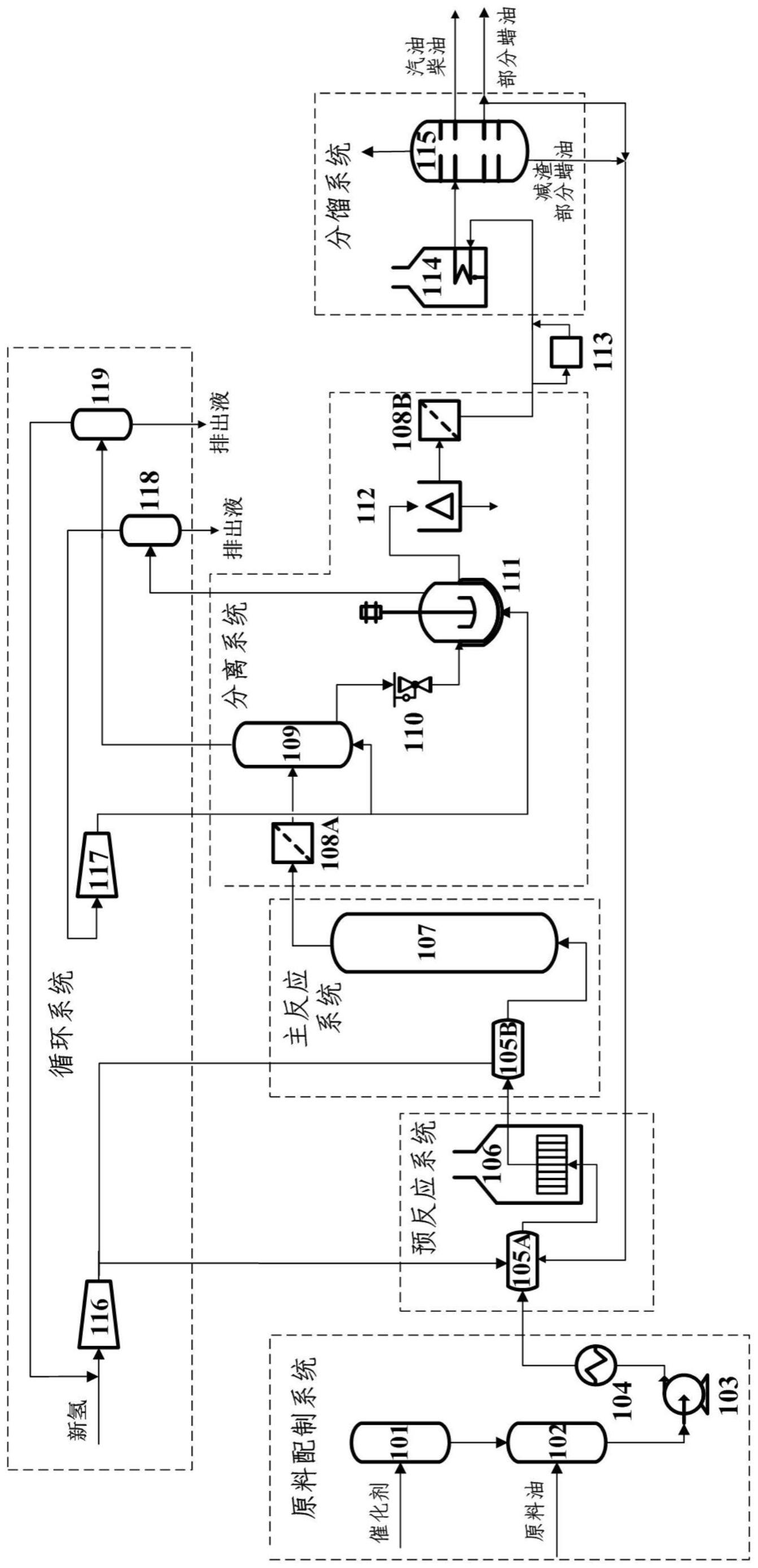
1.本发明涉及一种劣质重油浆态床加氢裂化处理设备和处理方法,属于重油深加工中重油轻质化领域。
背景技术:
2.随着全球石油资源劣质化、重质化趋势日益严峻,劣质石油在原油中的比例超过30%。在此背景下,我国炼油行业也面临大量劣质、重质石油的加工难题。
3.针对上述高硫、高金属、高残炭的劣质重质石油资源,采用重油浆态床加氢裂化技术是当前符合提高资源利用率发展趋势的适宜工艺技术。
4.目前,世界主要的重油浆态床加氢工艺有:eni的est工艺、委内瑞拉国家石油公司与法国axens联合开发的hdhplus-shp工艺、chevron的vrsh工艺、kbr和bp的vcc工艺、uop的uniflex工艺,上述工艺各具特点,但在催化剂类型、操作条件、工艺方案、运行周期等方面存在差异。
5.est工艺所用的是一种油溶型催化剂,在反应器中转化为纳米级薄层形式的无载体的mos2,并采用复杂的反应器内工艺控制技术,其工艺的主要特点:采用未转化油多次循环工艺,原料油总转化率高,没有燃料油或焦炭产物;产品质量较优,汽柴油满足欧ⅳ标准;原料油中的金属基本脱除;成本较高的催化剂的消耗较少。
6.hdhplus-shp工艺采用两台具有复杂内构件的浆态床反应器串联的形式,使用固体颗粒催化剂,添加一定量的助剂,其在原料油中的分散性不好,采用较苛刻的反应工艺条件,需要外甩10%左右的未转化尾油,否则装置运行周期将大为缩短。
7.vcc工艺采用一种非金属催化剂,采用多台反应器串联工艺,以克服返混的影响。操作压力为18~20mpa,调整反应工艺条件可以使渣油的单程转化率达到95%。在热分离器中,轻组分与未转化尾油分离,未转化尾油从热分离器底部全部排出,不进行循环处理,通过外排尾油达到控制生焦,维持装置稳定运行的目的。该工艺的装置经济性不足,如需加工劣质渣油等重油原料或维持较高的单程转化率,则装置运行周期也将缩短。
技术实现要素:
8.为了使劣质重油浆态床加氢裂化设备能够维持连续稳定运行,本发明提供一种劣质重油浆态床加氢裂化处理设备和处理方法,其中:
9.本发明一方面提供一种一种劣质重油浆态床加氢裂化处理设备,包括依次连接的原料配制系统、反应系统、分离系统以及分馏系统,其中:
10.所述反应系统包括依次连接的第一劣质重油混氢器、列管式加热预反应炉、第二劣质重油混氢器以及浆态床反应器;
11.所述分离系统包括依次连接的第一过滤器组、高压分离器、减压阀、低压稳定分离罐、脱固离心机组以及第二过滤器组;
12.所述第一劣质重油混氢器与所述原料配制系统连接;所述第一过滤器组与所述浆
态床反应器连接;所述第二过滤器组与所述分馏系统连接。
13.本发明另一方提供一种基于上述设备的劣质重油浆态床加氢裂化处理方法,其中包括:
14.原料配制过程:在原料配制系统中配制出含有催化剂的原料油;
15.预反应过程:由第一劣质重油混氢器将所述原料油与从氢气循环压缩机提供的氢气混合后进入列管式加热预反应炉进行浆态床加氢裂化预反应,得到的预反应产物;
16.主反应过程:由第二劣质重油混氢器将上述预反应产物与从氢气循环压缩机提供的氢气混合后进入浆态床反应器进行深度加氢裂化反应,得到的主反应产物;
17.一级分离过程:将所述主反应产物经第一过滤器组去除大于50μm的颗粒物后进入高压分离器进行一级气液分离;
18.二级分离过程:将所述一级气液分离后得到的液相产物经减压阀减压后进入低压稳定分离罐进行二级气液分离,将所得的液相产物经脱固离心机组进入第二过滤器组去除大于5μm的颗粒物;
19.分馏过程,在分馏系统中将所述二级分离过程后的产物进行分馏处理。
20.本发明又一方面提供一种上述设备在对劣质重油进行加氢裂化处理中的应用。
21.本发明实施例至少实现了如下技术效果:本发明可以有效抑制生焦,稳定反应产物体系,固液高效、快速分离,提高加氢反应效率和装置操作灵活度,降低装置氢耗,延长装置稳定运行周期。
22.本发明的其它特征和优点将在随后的说明书中阐述,并且,部分地从说明书中变得显而易见,或者通过实施本发明而了解。本发明的目的和其他优点可通过在所写的说明书、权利要求书、以及附图中所记载的结构来实现和获得。
23.下面通过附图和实施例,对本发明的技术方案做进一步的详细描述。
附图说明
24.附图用来提供对本发明的进一步理解,并且构成说明书的一部分,与本发明的实施例一起用于解释本发明,并不构成对本发明的限制。在附图中:
25.图1为本发明实施例提供的劣质重油浆态床加氢裂化处理设备的结构及工艺流程示意图。
26.图2为常规渣油浆态床加氢裂化设备的结构及工艺流程示意图。
具体实施方式
27.下面将参照附图更详细地描述本公开的示例性实施例。虽然附图中显示了本公开的示例性实施例,然而应当理解,可以以各种形式实现本公开而不应被这里阐述的实施例所限制。相反,提供这些实施例是为了能够更透彻地理解本公开,并且能够将本公开的范围完整的传达给本领域的技术人员。
28.这里将详细地对示例性实施例进行说明,其示例表示在附图中。下面的描述涉及附图时,除非另有表示,不同附图中的相同数字表示相同或相似的要素。以下示例性实施例中所描述的实施方式并不代表与本发明相一致的所有实施方式。相反,它们仅是与如所附权利要求书中所详述的、本发明的一些方面相一致的装置和方法的例子。
29.针对上述现有技术,发明人研究后发现:
30.中国专利cn00110716.x公开了一种重、渣油加氢转化方法,该方法将混合催化剂、氢气的原料在第一浆态床反应器进行低温长时间预处理,然后进入第二浆态床反应器进行高温短时间深度加氢转化。采用一次通过工艺,经过一反预处理后,提高了渣油的氢碳比及胶体稳定性,进入二反时降低了反应生焦量,一定程度上延长了装置的运行周期。但该工艺没有对反应产物中的焦炭、催化剂等固体颗粒进行后处理,装置长期运行将有堵塞设备及管线的隐患,并且该工艺进入二反的原料为一反的全馏分生成油,含有一定量的轻组分,稀释了反应物料,导致二反氢耗增加,同时存在轻组分过度裂化的风险。
31.中国专利cn201510176719.5及cn201510173962.1公开了一种劣质重油和/或劣质渣油的加工方法,该方法控制劣质原料的转化率分别小于50%和40%,达到控制生焦量并稳定装置运行的目的。虽然低转化率运行使得装置运行时间延长但其技术经济性不好。此外,该工艺使用的催化剂为固体颗粒的废、旧加氢处理催化剂,其在原料中的分散性不好,催化剂利用率低且抑制生焦能力较差。
32.中国专利cn201510190769.9公开了一种两段重油浆态床加氢设备和方法,该方法设置两级浆态床加氢裂化系统,每级设置一个含上升管、下降管的反应器和一个分离器,并在反应器内设计分布器、除沫器、扩大段等强化反应物料流动的部件。该方法反应器内构件多、结构复杂,一旦在反应器内生焦将难以清理,同时该复杂结构的反应器也给装置稳定操作带来困难,使用的是粉末状催化剂,在劣质重油中难于有效分散,并且该发明关于反应产物的后续处理及装置稳定运行的问题未作说明。
33.中国专利cn200810176207.9公开了一种浆态床反应器固液分离装置和方法,该方法在浆态床反应器后依次设置固液沉降分离系统、固液旋流分离系统和膜分离系统。其中,固液旋流分离系统由1~50套旋流单管组成;膜分离系统由1~20套陶瓷膜分离组件组成。主要用于费托合成工艺的浆态床反应产物的固液分离,该工艺的梯级分离的思想是科学合理的,但该技术不适用于反应工况更为苛刻的劣质重油浆态床加氢裂化过程。
34.中国专利cn201220538100.6及cn201220538103.x均公开了一种采用沉降罐及过滤组件对浆态床反应产物进行固液分离的工艺,通过上述两个单元设备对反应物料的后处理,可实现连续、快速的固液分离,从而维持装置的稳定运行,但上述工艺仅通过物理手段对反应产物进行固液分离,对浆态床反应体系及其工艺过程未采取控制及优化技术,因而无法从源头控制反应生焦,进一步的无法保证采用该工艺的浆态床加氢裂化装置的长周期稳定运行。
35.中国专利cn201410367441.5、cn201410276723.4、cn201210241249.2公开了关于劣质重油/渣油加氢处理的工艺,均采用“浆态床 固定床”的工艺流程,将劣质重油原料经浆态床反应器处理,再经分馏设备分离轻重组分后进入固定床反应器进行精制处理得到优质的轻质馏分油。上述方法未设置液体脱固设备,且无混氢器、预反应器及在线控制等反应系统优化设备,其反应生焦无法有效抑制,随着装置运行时间的延长,反应生焦及催化剂的固体颗粒杂质将堵塞固定床反应器的床层导致反应器压降升高,影响装置稳定运行周期。
36.综上所述,关于劣质重油浆态床加氢裂化工业示范装置的运行周期。uop公司的报告中提到montreal炼油厂的5000bbl/d工业示范装置的平均开工率是5年;采用est工艺的意大利百万吨级装置于2013年开工,运行总周期为3年,期间出现事故导致停车。
37.即使工业示范装置可以长周期运转,也不能保证工业装置能够长周期稳定运行。例如,采用浆态床合成油技术的卡塔尔oryx天然气合成油厂,自2006年投产以来,一直无法实现长周期稳定运转。根据最新报道显示,国内延长石油集团采用vcc工艺加工煤焦油的两套工业装置,其连续运行周期均小于300天。
38.工业装置安全、稳定、长周期运转是渣油浆态床加氢裂化技术成熟的一个重要标志。关于劣质重油浆态床加氢裂化装置的连续稳定运行技术,需要通过对现有核心技术的优化整合以及新技术和装备的开发应用,确保装置长周期运行,由于上述技术属于各研发机构的核心技术,在现有公开的资料中均未有明确表述。
39.因此,发明人发现,研发适于劣质重油浆态床加氢裂化装置连续稳定运行的工艺技术成为本领域急需解决的主要问题。
40.针对上述问题,本发明实施例提供一种劣质重油浆态床加氢裂化处理设备,如图1所示,该设备包括依次连接的原料配制系统、反应系统以及分离系统和分馏系统,可选地,还可以外接有在线分析系统113和循环系统。如图所示:
41.原料配制系统中依次连接有催化剂配制罐组101、原料油配制罐组102、原料泵103和换热器104。
42.反应系统可以分为预反应系统和主反应系统,其中依次连接有第一劣质重油混氢器105a、列管式加热预反应炉106、第二劣质重油混氢器105b和浆态床反应器107。
43.其中的预反应系统包括:第一劣质重油混氢器105a和列管式加热预反应炉106。列管式加热预反应炉106可以包括:列管式反应炉管和圆形加热炉体,列管式反应炉管在圆形加热炉内优选圆形排布。
44.其中主反应系统包括第二劣质重油混氢器105b和浆态床反应器107。浆态床反应器107为无内构件的空桶形式。
45.上述的第一劣质重油混氢器105a和第二劣质重油混氢器105b均为强化氢气传质的技术装备,可以选用超重力混氢器、微界面混氢器、文丘里管式混氢器等设备,优选适用于氢气在劣质重油中传质的混氢器,需要达到传统管道混氢设备混氢量的5-10倍。
46.分离系统中依次连接有第一过滤器组108a、高压分离器109、减压阀110、低压稳定分离罐111、脱固离心机组112和第二过滤器组108b。其中脱固离心机组112设置于低压稳定分离罐111和第二过滤器组108b之间,在脱固离心机组112和第二过滤器组108b的共同作用下,去除反应产物中大于5μm的颗粒物。其中的第一过滤器组108a和第二过滤器组108b中的每一个优选至少包含两级过滤器,其内部设置具有反冲洗功能的不同过滤效率的内构件。其中的低压稳定分离罐111中设置有带调速电机的搅拌设备。
47.分馏系统中依次连接有分馏加热炉114和分馏塔组115,该分馏塔组115优选一台常压塔串联一台减压塔的形式。
48.在线分析系统113可以包含:在线密度计、在线模拟蒸馏分析仪、甲苯不溶物快速分析仪、信号传输及控制计算机等,通过控制反应产物的密度、馏程及生焦量及时调整反应工艺参数和分馏塔操作参数。
49.循环系统中包括:氢气循环压缩机116,其输出端分别与第一劣质重油混氢器105a和第二劣质重油混氢器105b连接;富气循环压缩机117,其输出端分别连接高压分离器109和低压稳定分离罐111;富气压缩机脱液及缓冲罐118,其输出端连接富气循环压缩机117的
输入端,其输入端连接低压稳定分离罐111;氢气压缩机脱液及缓冲罐119,其输出端连接氢气循环压缩机116,其输入端连接高压分离器109。
50.在现有劣质油浆态床加氢裂化工艺设备的基础上设置劣质重油混氢器105a和105b、列管式加热预反应炉106、过滤器组108a和108b、低压稳定分离罐111、脱固离心机组112等设备,从劣质重油浆态床反应工艺过程控制和反应产物后处理两个关键工艺过程优化现有工艺,可以有效抑制生焦,并将反应生焦适时移除,稳定反应产物体系,固液高效、快速分离,提高加氢反应效率和装置操作灵活度,降低装置氢耗,延长装置稳定运行周期。
51.实验表明,可以使加工金属杂质ni v的含量》200g/g、残碳》18wt%、s含量》1wt%的劣质油原料的减压渣油总转化率大于90%,装置连续运行2000h以上。
52.以下结合图1所示设备的结构示意图,说明本实施提供的劣质重油浆态床加氢裂化处理方法的工艺流程,包括如下步骤:
53.步骤(1):在原料配制系统中配制出含有催化剂的原料油进入预反应系统。
54.具体地,可以在催化剂配制罐组101中,在搅拌条件下将油溶性催化剂与携带油混合成催化剂油,然后在原料配制罐组102中,伴热90-120℃、在搅拌条件下将原料油与催化剂油混合得到含有催化剂的原料油。然后由原料泵103将含有催化剂的原料油泵送给换热器104,经换热后进入预反应系统。
55.其中,上述携带油可以为富含芳香烃、环烷烃的催化柴油、焦化柴油、加氢裂化柴油、焦化蜡油等二次加工油所构成的混合物中的至少一种。上述油溶性催化剂可以采用油溶型高分散钼基催化剂,使用时不需要预硫化,升温至激活温度即可。上述原料油具体可以为催化油浆、高硫高金属渣油、常压渣油、减压渣油、超稠重质原油、油砂沥青等劣质油所构成的混合物中的至少一种。
56.步骤(2):在预反应系统中,由第一劣质重油混氢器105a将上述经换热后的含有催化剂的原料油与从氢气循环压缩机116提供的氢气混合后进入列管式加热预反应炉106进行浆态床加氢裂化预反应,得到的预反应产物进入主反应系统。
57.其中,列管式加热预反应炉106的操作条件为:反应温度390~420℃,反应压力10.0~18.0mpa,体积空速1.0~2.0h-1
,氢油体积比500~1000。
58.步骤(3):在主反应系统中,由第二劣质重油混氢器105b将上述预反应产物与从氢气循环压缩机116提供的氢气混合后进入浆态床反应器107进行深度加氢裂化反应,得到的主反应产物进入分离系统。
59.其中,浆态床反应器107的操作条件为:反应温度400~440℃,反应压力10.0~20.0mpa,体积空速0.2~1.0h-1
,氢油体积比400~1000。
60.步骤(4):在分离系统中,上述主反应产物经第一过滤器组108a去除大于50μm的颗粒物后进入高压分离器109进行一级气液分离得到高分气和液相产物。
61.其中,所得的高分气在氢气压缩机脱液及缓冲罐119进行脱液后得到的气体循环回氢气循环压缩机116,再由氢气循环压缩机116提供给第一劣质重油混氢器105a进行混氢处理。
62.其中,高压分离器109的操作压力可以为10.0~20.0mpa。
63.步骤(5):在分离系统中,经上述一级气液分离所得到的液相产物经减压阀110减压后进入低压稳定分离罐111进行二级气液分离得到富烃混合气和液相产物。
64.其中,所得的液相产物经脱固离心机组112进入第二过滤器组108b去除大于5μm的颗粒物后的反应产物进入分馏系统。
65.其中,所得的富烃混合气在富气压缩机脱液及缓冲罐118中进行脱液后得到的气体经富气循环压缩机117分别注入所述高压分离器109和低压稳定分离罐111。通过向高压分离器109和低压稳定分离罐111的底部注入反应生成的富烃混合气,起到抑制大分子烃自由基反应缩合生焦及生焦前驱物的聚并增长的作用,有利于维持液相物料相态稳定。
66.其中,低压稳定分离罐111内设置有带调速电机的搅拌设备,其电机搅拌速率为60~600r/min,搅拌设备和富烃混合气气提两种方式可以同时作用或单独使用,其操作压力可以为0.5~1.5mpa。其中,气提指的是使用气体将液相物料中的气相杂质分离出来的过程,如使用蒸汽进行该过程则为汽提。
67.步骤(6):在分馏系统中,对步骤(5)的反应产物进行分馏处理得到汽油、柴油、蜡油、减渣,并将全部减渣和部分蜡油循环回预反应系统。
68.具体地,可以使反应产物先经过分馏炉114加热后进入分馏塔组115进行分馏处理,得到的汽油、柴油和蜡油是所需的产品,为提高渣油转化率和工艺的经济性,减渣需要循环回预反应系统中的第一劣质重油混氢器105a,与新鲜的原料油混合后再次参与反应。为了维持劣质原料油在浆态床加氢裂化工艺中的稳定性及可裂化性,需要调合一定量的富含芳烃的稳定组分进入劣质原料中,达到稳定劣质原料的胶体体系、抑制沥青质的缩聚并能提供一定量的氢自由基的目的,经试验研究发现,本发明工艺所获得的蜡油馏分具有原料稳定组分的特点。因此,本发明优选将全部减渣和部分蜡油一同循环。
69.可选地,可以通过在线分析系统113通过控制来自于所述第二过滤器组(108b)的反应产物的密度、馏程及生焦量来调整反应工艺参数和分馏塔操作参数。
70.本发明的技术优势在于:
71.①
设置劣质重油混氢器、列管式加热预反应炉并采用减渣全循环加部分蜡油循环的工艺,改善氢气在劣质原料油中的传质效果,采用逐级反应的工艺,提高渣油转化率,并使反应物料相态体系相对稳定;
72.②
设置在线分析系统,根据生产需求灵活调整工艺参数,并且通过对反应产物的关键指标的精确控制,维持反应系统的稳定运行;
73.③
在高压分离器底部注入富烃混合气,实现抑制液相物流中焦炭颗粒物聚集、沉积的目的;
74.④
设置低压稳定分离罐,设置搅拌设备并在其底部注入富烃混合气,实现气液快速分离,稳定反应产物的胶体体系和相态体系的目的;
75.⑤
设置过滤器组和脱固离心机组,将反应生成的焦炭等固体杂质颗粒物逐级、连续、快速脱除,保护后续设备的安全稳定运行。
76.实施例1~4,采用百吨级渣油浆态床加氢裂化中试装置进行试验并得出结果。对比例1为常规渣油浆态床加氢裂化工艺的运行方案;实施例1~2为采用本发明工艺的低转化率运行方案(》500℃馏分转化率》60%);实施例3~4为采用本发明工艺的高转化率运行方案(》500℃馏分转化率》90%)。
77.对比例1采用图2所示的常规设备,该设备包括:催化剂配制罐201、原料油配制罐202、原料泵203、换热器204、原料加热炉205、浆态床反应器206、高压分离器207、减压阀
208、低压分离器209、分馏加热炉210、分馏塔211、氢气循环压缩机212、低分脱液及缓冲罐213、压缩机脱液及缓冲罐214。
78.实施例1~4采用本发明图1所示的设备。对比例1和实施例1~4所用的原料性质见表1,对比例1和实施例1~4所用的工艺条件列于表2,对比例1和实施例1~4的评价结果见表3。
79.表1原料油基本物性
[0080][0081]
表2操作条件
[0082][0083][0084]
表3评价结果
[0085][0086]
由表1~3可知,在达到相当的重油转化率(》500℃馏分转化率》90%)时,使用普通工艺方案的对比例1比采用本发明工艺高转化率(控制全馏分产物的密度降幅为12.5~14.5%,则》500℃馏分转化率》90%)运行方案的实施例3的反应温度高10℃、压力高4mpa、氢油比高400,实施例3生成油的硫、氮、残碳、金属杂质ni v及甲苯不溶物含量均低于对比例1。在试验条件下,对比例1的脱硫率为89.52%、脱氮率为86.10%、焦炭产率为3.9%、脱残碳率为88.49%、ni v脱除率为88.45%、》500℃馏分转化率为95.5%;实施例3的脱硫率为91.75%、脱氮率为88.74%、焦炭产率为1.83%、脱残碳率为83.63%、ni v脱除率为90.75%、》500℃馏分转化率为92.1%。除脱残碳率略低于对比例1外,其余关键控制指标均优于对比例1,且实施例3的装置稳定运行时间远高于对比例1的装置运转时间(通过本技术的实施,控制反应产物中甲苯不溶物含量《2.0%,分离系统采用较适宜的工况,装置运行时间延长至大于3000h)。
[0087]
通常,按照炼油加氢装置放大的普遍规律,由中试到工业装置的稳定运行时间对应关系为:中试装置连续运行1500h则工业装置可稳定运行3年,中试装置连续运行3000h则工业装置可稳定运行6年。
[0088]
由表1~3可知,采用本发明工艺方案的实施例1~2,采用低转化率(控制全馏分产物的密度降幅为10.0~13.5%,则》500℃馏分转化率》60%,在本发明的试验获得的实施例1~2的》500℃馏分转化率》80%)运行方案时,由于试验工艺条件更加缓和,其反应生焦量进一步降低(通过本技术的实施,控制反应产物中甲苯不溶物含量《1.0%),分离系统的负荷将更低,后续的高压分离器、低压稳定分离罐的操作条件也更为缓和,劣质油浆态床加氢裂化中试装置运行周期进一步延长,可以稳定运行超过3500h。其中,在比对比例1运行工况更缓和的工艺条件下(反应温度低25℃、反应压力低4mpa、氢油比低800),实施例2的脱硫率、脱氮率及脱金属率均略低于对比例1。实施例2的脱硫率为88.11%、脱氮率为85.27%、镍钒脱除率为87.86%、脱残碳率为79.20%、》500℃馏分转化率为87.9%。而采用更加苛刻的工艺条件的实施例4,在维持较长的装置运行时间(稳定运行2500h)的同时,其》500℃馏分转化率为95.9%(略高于对比例1)、脱硫率为94.18%、脱氮率为90.81%、镍钒脱除率为
91.99%(实施例4的各项指标均优于对比例1)。
[0089]
由于本发明采用多点补氢、在线分析系统和包含列管式加热预反应炉的反应工艺,工艺条件可根据实际生产及反应产物性质灵活调整操作参数,反应苛刻度降低;通过设置低压稳定分离罐、过滤器组和脱固离心机组,实现气液快速分离、稳定反应产物的胶体体系和相态体系、将反应生成的焦炭等固体杂质颗粒物逐级-连续-快速脱除,最终实现劣质重油浆态床加氢裂化装置稳定运行的目标。
[0090]
本领域内的技术人员应明白,本发明的实施例可提供为方法、系统、或计算机程序产品。因此,本发明可采用完全硬件实施例、完全软件实施例、或结合软件和硬件方面的实施例的形式。而且,本发明可采用在一个或多个其中包含有计算机可用程序代码的计算机可用存储介质(包括但不限于磁盘存储器和光学存储器等)上实施的计算机程序产品的形式。
[0091]
本发明是参照根据本发明实施例的方法、设备(系统)、和计算机程序产品的流程图和/或方框图来描述的。应理解可由计算机程序指令实现流程图和/或方框图中的每一流程和/或方框、以及流程图和/或方框图中的流程和/或方框的结合。可提供这些计算机程序指令到通用计算机、专用计算机、嵌入式处理机或其他可编程数据处理设备的处理器以产生一个机器,使得通过计算机或其他可编程数据处理设备的处理器执行的指令产生用于实现在流程图一个流程或多个流程和/或方框图一个方框或多个方框中指定的功能的装置。
[0092]
这些计算机程序指令也可存储在能引导计算机或其他可编程数据处理设备以特定方式工作的计算机可读存储器中,使得存储在该计算机可读存储器中的指令产生包括指令装置的制造品,该指令装置实现在流程图一个流程或多个流程和/或方框图一个方框或多个方框中指定的功能。
[0093]
这些计算机程序指令也可装载到计算机或其他可编程数据处理设备上,使得在计算机或其他可编程设备上执行一系列操作步骤以产生计算机实现的处理,从而在计算机或其他可编程设备上执行的指令提供用于实现在流程图一个流程或多个流程和/或方框图一个方框或多个方框中指定的功能的步骤。
[0094]
最后应说明的是:以上实施例仅用以说明本发明的技术方案,而非对其限制;尽管参照前述实施例对本发明进行了详细的说明,本领域的普通技术人员应当理解:其依然可以对前述各实施例所记载的技术方案进行修改,或者对其中部分技术特征进行等同替换;而这些修改或者替换,并不使相应技术方案的本质脱离本发明各实施例技术方案的精神和范围。
再多了解一些
本文用于创业者技术爱好者查询,仅供学习研究,如用于商业用途,请联系技术所有人。