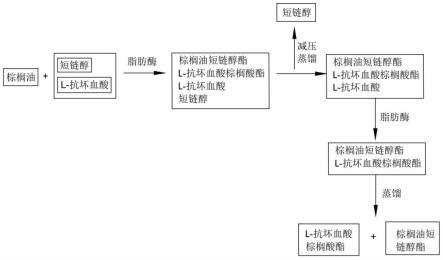
一种联产l-抗坏血酸棕榈酸酯和生物柴油的工艺方法
技术领域
1.本发明涉及生物化工领域,具体涉及一种联产l-抗坏血酸棕榈酸酯和生物柴油的工艺方法。
背景技术:
2.l-抗坏血酸(l-ascorbic acid)是一种常用的天然抗氧化剂,其分子结构中具有活性连烯二醇,易受光线和温度等外界因素影响而氧化,从而具有强抗氧化能力。然而,由于l-抗坏血酸的亲水性强,不易溶解于油脂等疏水性液体中,故极大地限制了它的应用,而将l-抗坏血酸转化为其脂肪酸酯则可解决该难题。l-抗坏血酸脂肪酸酯不仅保持了l-抗坏血酸的抗氧化性能和生理活性,而且在非水体系中的溶解性和稳定性均有显著提高,增加了对自由基的清除能力,已成为一种高效、安全、无毒的抗氧化剂。
3.目前,采用棕榈酸、硬脂酸和月桂酸等脂肪酸直接作为酰基供体,通过化学法制备l-抗坏血酸脂肪酸酯的研究较为广泛;生物酶法反应条件温和,特异性强,产物分离纯化方法简单,酶催化合成l-抗坏血酸脂肪酸酯具有很好的开发应用前景。
4.在生物酶法制备l-抗坏血酸脂肪酸酯的过程中,由于l-抗坏血酸的亲水性强,在长链脂肪酸酯的制备过程中难与酰基供体互溶,使得过程中常常需要引入包括叔丁醇、丙酮在内的疏水性溶剂,以促进反应的进行,此种方式需额外引入有机溶剂,直接增加操作成本,且反应过程产品单一。
技术实现要素:
5.为了克服上述技术问题,本发明公开了一种联产l-抗坏血酸棕榈酸酯和生物柴油的工艺方法。
6.本发明为实现上述目的所采用的技术方案是:
7.一种联产l-抗坏血酸棕榈酸酯和生物柴油的工艺方法,其包括以下步骤:
8.步骤1,将l-抗坏血酸和棕榈油进行一次酶催化反应,得到一次酶催化混合物;
9.步骤2,将所述一次酶催化混合物进行分层和减压蒸馏处理,得到一次酶催化产物;
10.步骤3,将所述一次酶催化产物进行二次酶催化反应,得到二次酶催化混合物;
11.步骤4,将所述二次酶催化混合物于在线脱水条件下进行蒸馏处理,获得l-抗坏血酸棕榈酸酯和生物柴油(即棕榈油短链醇酯)。
12.上述的联产l-抗坏血酸棕榈酸酯和生物柴油的工艺方法,其中在步骤1中,所述一次酶催化反应是在脂肪酶的催化作用下与短链醇反应进行的;所述脂肪酶为液体脂肪酶或固定化脂肪酶。
13.上述的联产l-抗坏血酸棕榈酸酯和生物柴油的工艺方法,其中所述步骤1采用液体脂肪酶催化;所述一次酶催化反应的条件为:液体脂肪酶用量为棕榈油质量的300-3000个标准酶活单位,l-抗坏血酸用量为棕榈油摩尔数的0.2~0.8倍,短链醇用量为棕榈油摩
尔数的3~5倍,水含量为棕榈油质量的2~5%;所述一次酶催化反应于一级或多级酶反应器中进行,温度控制在35~60℃,反应6~18小时。通常情况下,l-抗坏血酸的转化率达到80%以上,棕榈油短链醇酯得率为理论得率的90%以上。
14.上述的联产l-抗坏血酸棕榈酸酯和生物柴油的工艺方法,其中所述步骤1采用固定化脂肪酶催化;所述一次酶催化反应的条件为:固定化脂肪酶用量为棕榈油质量的300-2000个标准酶活单位,l-抗坏血酸用量为棕榈油摩尔数的0.2~0.8倍,短链醇用量为棕榈油摩尔数的3~65倍;所述一次酶催化反应于一级或多级环流反应器中进行,温度控制在35~60℃,反应5~18小时。通常情况下,l-抗坏血酸的转化率达到90%以上,棕榈油短链醇酯得率为理论得率的95%以上。
15.上述的联产l-抗坏血酸棕榈酸酯和生物柴油的工艺方法,其中在所述一次酶催化反应中的短链醇以分步添加的方式加入,分步添加条件为短链醇在2个小时内匀速加入。
16.上述的联产l-抗坏血酸棕榈酸酯和生物柴油的工艺方法,其中经过一次酶催化反应后获得的一次酶催化混合物在进行二次酶催化反应之前,需要去除当中残余的短链醇等物质,以便于后续获得较纯的生物柴油;在步骤2中,所述分层处理可选取离心或静止分层,以分离出含脂肪酶的重相和含有粗生物柴油的轻相,轻相进一步减压蒸馏取釜液以备进行后续的步骤3,且减压蒸馏的目的在于去除多余的短链醇。
17.上述的联产l-抗坏血酸棕榈酸酯和生物柴油的工艺方法,其中在步骤3中,所述二次酶催化反应是在固定化脂肪酶的催化作用下反应进行的,所述固定化脂肪酶用量为棕榈油质量的300-2000个标准酶活单位;所述二次酶催化反应于一级或多级环流反应器中进行,温度控制在35~60℃,反应10~18小时。优选地,一级或多级环流反应器与在线脱水设备相偶联,以在线除去反应体系中的水分;通常情况下,l-抗坏血酸的转化率达到95%以上,棕榈油短链醇酯得率为理论得率的98%以上。
18.上述的联产l-抗坏血酸棕榈酸酯和生物柴油的工艺方法,其中在步骤4的反应过程中,引入分子筛、膜等在线脱水条件下进行,以在线除去反应体系中的水分,进而可获得质量合格的l-抗坏血酸棕榈酸酯和生物柴油;蒸馏所得馏出液为棕榈油短链醇酯,即为生物柴油,釜液为l-抗坏血酸棕榈酸酯。
19.上述的联产l-抗坏血酸棕榈酸酯和生物柴油的工艺方法,其中所述短链醇为甲醇、乙醇、丙醇或丁醇。
20.上述的联产l-抗坏血酸棕榈酸酯和生物柴油的工艺方法,其中所述脂肪酶包括来源于酵母细胞、霉菌细胞、细菌或其它微生物的脂肪酶。
21.l-抗坏血酸作为一种常用的天然抗氧化剂,因其亲水性强,不易溶解于油脂等疏水性液体,极大地限制了其于脂溶性疏水体系中的应用。为了提高l-抗坏血酸的应用性能,如何提高生物酶法对其的催化转化率是制备l-抗坏血酸脂肪酸酯的关键。目前,棕榈酸、硬脂酸和月桂酸等脂肪酸直接作为酰基供体,但在制备过程中,酰基供体难与l-抗坏血酸互溶,故通常需要引入疏水性溶剂以改善反应体系中的疏水程度,传统的疏水性溶剂可选包括叔丁醇、丙酮等,但若引入上述溶剂则增加操作成本,同时反应所得产品种类单一。
22.在进行一次酶催化反应或二次酶催化反应时,可选用生物催化剂,包括多种脂肪酶,包括液体脂肪酶、固定化脂肪酶以及含有脂肪酶的菌体或固定化菌体;脂肪酶催化剂具有原料适应性广、反应条件温和等优点,特别适用于高酸价油脂的酶催化反应;液体脂肪酶
为游离液态,价格相对低廉,通常含有较高的水分含量,且其对油脂的酶催化具有较高的反应速率;固定化脂肪酶相比于液体脂肪酶具有抗逆性好、易于回收等优点。本发明中采用两步式酶催化反应,包括一次酶催化反应采用的是液体脂肪酶或固定化脂肪酶催化,二次酶催化反应采用的是固定化脂肪酶催化,其中采用液体脂肪酶催化是在油水的乳化体系下进行,液态脂肪酶分散于油水两相界面上催化反应进行,进而促进酶催化效率,此外,由于油水的不互溶性会造成反应体系的乳化,而这种乳化作用会导致由吸附法制得的固定化脂肪酶的蛋白脱落和失活,致使表观酶活降低,故本发明采用固定化脂肪酶催化时反应体系为无溶剂体系,即不添加如水等有机溶剂作为反应介质,此时反应体系为均相,不存在乳化现象,需特别说明的是由于l-抗坏血酸和棕榈油、棕榈油和短链醇之间的酯化反应中生成水,而酯化反应为平衡反应,为进一步促进反应向酯化反应进行,在进行二次酶催化反应时,反应体系可与在线脱水设备相偶联,以在线除去体系中的水分,可快速推动反应达到平衡状态,进而有效地提高l-抗坏血酸的转化率和产物得率。
23.本发明的有益效果为:本发明利用l-抗坏血酸在短链醇里的溶解性,促进l-抗坏血酸与棕榈油互溶,采用两步式酶催化反应在温和条件下反应,实现以脂肪酶催化l-抗坏血酸和棕榈油反应生成l-抗坏血酸棕榈酸酯的同时,催化棕榈油和短链醇反应生成生物柴油,实现了多种高附加值产品的一体化联产,显著提高了棕榈油的附加值和反应过程的综合经济效益;整个反应过程环境温和友好,既能最大限度地保留l-抗坏血酸的生物活性,又能充分利用了原材料组分,极大地提高酶催化效率和产物得率;同时,反应过程中直接以短链醇代替常规的有机溶剂,不需要额外引入常规工艺中采用的叔丁醇、丙酮等有机溶剂,解决l-抗坏血酸在棕榈油里难溶需额外加入有机溶剂的问题,省去了常规l-抗坏血酸棕榈酸酯制备过程中额外加入有机溶剂的繁琐工艺,综合经济效益显著提高,该工艺具有很好的市场推广应用前景。
附图说明
24.下面结合附图和实施例对本发明进一步说明。
25.图1为本发明中工艺方法的反应过程示意图;
26.图2为本发明中工艺方法的主要流程示意图。
具体实施方式
27.下面通过具体实施例对本发明作进一步说明,以使本发明技术方案更易于理解、掌握,而非对本发明进行限制。若未特别指明,实施例中所用的技术手段为本领域技术人员所熟知的常规手段,所用原料均为市售商品。
28.实施例1:本实施例提供一种联产l-抗坏血酸棕榈酸酯和生物柴油的工艺方法,其包括以下步骤:
29.步骤1,将10g棕榈油、基于油脂质量2%的水、基于油脂摩尔数0.2倍的l-抗坏血酸,基于油脂质量400个标准酶活单位的来源于米曲霉aspergillus oryzae的液体脂肪酶,基于油脂摩尔数3倍的甲醇置于一级或多级酶反应器中于35℃下反应10小时,得到一次酶催化混合物;其中,所述一次酶催化混合物中l-抗坏血酸转化率达到80%,棕榈油甲酯得率90%;
30.步骤2,将所述一次酶催化混合物经离心分层后,分离出重相和轻相,取轻相进一步经过减压蒸馏除去里面多余的短链醇,得到一次酶催化产物;
31.步骤3,将所述一次酶催化产物置于一级或多级环流反应器中,加入基于油脂质量300个标准酶活单位的来自米曲霉aspergillus oryzae的固定化脂肪酶,反应温度控制在55℃,反应12小时,得到二次酶催化混合物;
32.步骤4,将所述二次酶催化混合物于在线脱水条件下进行蒸馏处理,获得l-抗坏血酸棕榈酸酯和生物柴油;其中l-抗坏血酸转化率达到95%,棕榈油甲酯得率98%。
33.实施例2:本实施例提供一种联产l-抗坏血酸棕榈酸酯和生物柴油的工艺方法,其包括以下步骤:
34.步骤1,将20g棕榈油、基于油脂质量5%的水、基于油脂摩尔数0.5倍的l-抗坏血酸,基于油脂质量2000个标准酶活单位的来源于南极假丝酵母candida antarctica的液体脂肪酶,基于油脂摩尔数4倍的乙醇置于一级或多级酶反应器中于45℃下反应18小时,得到一次酶催化混合物;其中,所述一次酶催化混合物中l-抗坏血酸转化率达到85%,棕榈油乙酯得率90%;
35.步骤2,将所述一次酶催化混合物经离心分层后,分离出重相和轻相,取轻相进一步经过减压蒸馏除去里面多余的短链醇,得到一次酶催化产物;
36.步骤3,将所述一次酶催化产物置于一级或多级环流反应器中,加入基于油脂质量2000个标准酶活单位的来自米曲霉aspergillus oryzae的固定化脂肪酶,反应温度控制在45℃,反应12小时,得到二次酶催化混合物;
37.步骤4,将所述二次酶催化混合物于在线脱水条件下进行蒸馏处理,获得l-抗坏血酸棕榈酸酯和生物柴油;其中l-抗坏血酸转化率达到98%,棕榈油乙酯得率98%。
38.实施例3:本实施例提供一种联产l-抗坏血酸棕榈酸酯和生物柴油的工艺方法,其包括以下步骤:
39.步骤1,将30g棕榈油、基于油脂摩尔数0.8倍的l-抗坏血酸,基于油脂质量1500个标准酶活单位的来源于米黑根毛霉rhizomucormiehei的固定化脂肪酶,基于油脂摩尔数5倍的甲醇置于一级或多级环流反应器中于55℃下反应10小时,得到一次酶催化混合物;其中,所述一次酶催化混合物中l-抗坏血酸转化率达到91%,棕榈油甲酯得率96%;
40.步骤2,将所述一次酶催化混合物经离心分层后,分离出重相和轻相,取轻相进一步经过减压蒸馏除去里面多余的短链醇,得到一次酶催化产物;
41.步骤3,将所述一次酶催化产物置于一级或多级环流反应器中,加入基于油脂质量1000个标准酶活单位的来自南极假丝酵母candida antarctica的固定化脂肪酶,反应温度控制在55℃,反应10小时,得到二次酶催化混合物;
42.步骤4,将所述二次酶催化混合物于在线脱水条件下进行蒸馏处理,获得l-抗坏血酸棕榈酸酯和生物柴油;其中l-抗坏血酸转化率达到96%,棕榈油甲酯得率98%。
43.实施例4:本实施例提供一种联产l-抗坏血酸棕榈酸酯和生物柴油的工艺方法,其包括以下步骤:
44.步骤1,将50g棕榈油、基于油脂摩尔数0.2倍的l-抗坏血酸、基于油脂质量2000个标准酶活单位的来源于米黑根毛霉rhizomucormiehei的固定化脂肪酶,基于油脂摩尔数5倍的丁醇置于一级或多级环流反应器中于50℃下反应15小时,得到一次酶催化混合物,其
中,丁醇在前2个小时内匀速流加入反应器中;所述一次酶催化混合物中l-抗坏血酸转化率达到90%,棕榈油丁酯得率95%;
45.步骤2,将所述一次酶催化混合物经离心分层后,分离出重相和轻相,取轻相进一步经过减压蒸馏除去里面多余的短链醇,得到一次酶催化产物;
46.步骤3,将所述一次酶催化产物置于一级或多级环流反应器中,加入基于油脂质量1000个标准酶活单位的来自米曲霉aspergillus oryzae的固定化脂肪酶,反应温度控制在55℃,反应12小时,得到二次酶催化混合物;反应过程中采取如图2所示的在线脱水;
47.步骤4,将所述二次酶催化混合物于在线脱水条件下进行蒸馏处理,获得l-抗坏血酸棕榈酸酯和生物柴油;其中l-抗坏血酸转化率达到96%,棕榈油丁酯得率98%。
48.实施例5:本实施例提供一种联产l-抗坏血酸棕榈酸酯和生物柴油的工艺方法,其包括以下步骤:
49.步骤1,将30g棕榈油、基于油脂质量4%的水、基于油脂摩尔数0.8倍的l-抗坏血酸,基于油脂质量1800个标准酶活单位的来源于南极假丝酵母candida antarctica的液体脂肪酶,基于油脂摩尔数6倍的乙醇置于一级或多级酶反应器中于45℃下反应16小时,得到一次酶催化混合物;其中,所述一次酶催化混合物中l-抗坏血酸转化率达到80%,棕榈油乙酯得率92%;
50.步骤2,将所述一次酶催化混合物经离心分层后,分离出重相和轻相,取轻相进一步经过减压蒸馏除去里面多余的短链醇,得到一次酶催化产物;
51.步骤3,将所述一次酶催化产物置于一级或多级环流反应器中,加入基于油脂质量1800个标准酶活单位的来自南极假丝酵母candida antarctica的固定化脂肪酶,反应温度控制在55℃,反应18小时,得到二次酶催化混合物;
52.步骤4,将所述二次酶催化混合物于在线脱水条件下进行蒸馏处理,获得l-抗坏血酸棕榈酸酯和生物柴油;其中l-抗坏血酸转化率达到97%,棕榈油乙酯得率99%。
53.实施例6:本实施例提供一种联产l-抗坏血酸棕榈酸酯和生物柴油的工艺方法,其包括以下步骤:
54.步骤1,将2g棕榈油、基于油脂摩尔数0.3倍的l-抗坏血酸、基于油脂质量900个标准酶活单位的来源于米曲霉aspergillus oryzae的固定脂肪酶、基于油脂摩尔数4倍的甲醇置于一级或多级环流反应器中于45℃下反应12小时,得到一次酶催化混合物;其中,所述一次酶催化混合物中l-抗坏血酸转化率达到92%,棕榈油甲酯得率95%;
55.步骤2,将所述一次酶催化混合物经离心分层后,分离出重相和轻相,取轻相进一步经过减压蒸馏除去里面多余的短链醇,得到一次酶催化产物;
56.步骤3,将所述一次酶催化产物置于一级或多级环流反应器中,加入基于油脂质量2000个标准酶活单位的来自南极假丝酵母candida antarctica的固定化脂肪酶,反应温度控制在50℃,反应18小时,得到二次酶催化混合物;反应过程中采取如图2所示的在线脱水;
57.步骤4,将所述二次酶催化混合物于在线脱水条件下进行蒸馏处理,获得l-抗坏血酸棕榈酸酯和生物柴油;其中l-抗坏血酸转化率达到97%,棕榈油甲酯得率99%。
58.本发明利用l-抗坏血酸在短链醇里的溶解性,促进l-抗坏血酸与棕榈油互溶,采用两步式酶催化反应在温和条件下反应,实现以脂肪酶催化l-抗坏血酸和棕榈油反应生成l-抗坏血酸棕榈酸酯的同时,催化棕榈油和短链醇反应生成生物柴油,实现了多种高附加
值产品的一体化联产,显著提高了过程的综合经济效益;整个反应过程环境温和友好,既能最大限度地保留l-抗坏血酸的生物活性,又能充分利用了原材料组分,极大地提高酶催化效率和产物得率;同时,反应过程中不需要额外引入常规工艺中采用的叔丁醇、丙酮等有机溶剂,综合经济效益显著提高,该工艺具有很好的市场推广应用前景。
59.以上所述,仅是本发明的较佳实施例而已,并非对本发明作任何形式上的限制。任何熟悉本领域的技术人员,在不脱离本发明技术方案范围情况下,都可利用上述揭示的技术手段和技术内容对本发明技术方案做出许多可能的变动和修饰,或修改为等同变化的等效实施例。故凡是未脱离本发明技术方案的内容,依据本发明之形状、构造及原理所作的等效变化,均应涵盖于本发明的保护范围。
再多了解一些
本文用于创业者技术爱好者查询,仅供学习研究,如用于商业用途,请联系技术所有人。