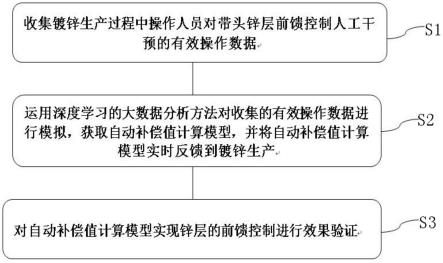
1.本发明涉及计算机控制技术领域,更具体地,涉及一种基于深度学习的热镀锌带钢镀层的控制方法。
背景技术:
2.在钢铁企业冷轧热镀锌机组控制系统中,镀层重量的控制是一个非常重要的生产环节,其控制好坏直接影响产品质量。虽然已有很多钢铁企业在热镀锌生产系统中建立了相应的控制系统,但由于在钢带镀锌过程中,影响钢带镀层重量的因素是复杂的、非线性的,导致该类控制系统的控制精确度不高。
3.热镀锌锌锅设备以及镀层厚度控制原理如说明书附图中的图1和图2所示。镀层厚度控制的执行单元为气刀1,气刀1是两个沿带钢3宽度方向布置在带钢两面的喷嘴,其控制镀层的因素主要有:喷嘴吹扫气体的压力和喷嘴与带钢的距离,镀层厚度控制的反馈单元为镀层测厚仪2。由于镀层测厚仪一般测量冷态下的锌层厚度,所以其布置在熔融态的锌层厚度控制单元气刀后面。稳定的锌层厚度控制参数设定受带钢的速度、锌锅4的锌液成分、温度、锌锅液面高度、气刀唇口纵向孔形、气刀唇口横向形状及开口度、气刀的水平和垂直位置、边缘控制器、喷嘴压力等众多因素影响。不难理解,影响镀锌层厚度及均匀性控制的因素复杂而具有不确定性。通常,镀层闭环控制按照不同钢卷的锌层厚度和规格分为前馈和反馈两部分。前馈控制为根据锌层厚度事先设定气刀1的气压和离带钢的距离进行生产;反馈控制是根据测厚仪测量的平均值对气刀进行调节,即当锌层测厚仪的测量值发生改变时,气刀的气压和离带钢的距离会根据闭环模式下计算的值发生改变。但是,由于锌层测厚仪距离锌锅气刀还有约100-200米,因而每个钢卷带头 100-200米由于没有锌层厚度实绩值无法实现反馈控制,只能根据钢卷的目标锌层厚度进行前馈控制。由于镀锌产品不同规格不同锌层厚度切换过程中较复杂,生产计算机系统给出的气刀距离和压力的前馈值可能导致带头锌层厚度不足,不能满足锌层控制的需求。操作工通常会根据生产经验提前人工输入锌层变化的补偿值,确保前馈控制不会导致带头锌层厚度不符。如果没有操作工的人为干预,需要经过100-200米的过渡过程才能达到产品要求,而在操作工的干预调节下,主要通过锌层补偿调整气刀与带钢距离或调整气刀压力,可以在较短的过渡过程后达到符合要求的锌层厚度。
4.专利号为cn201510843605.1的文献公开一种镀层控制方法,在带钢离开镀液液面的过程中,先采用超声波对带钢带出液面的镀液进行超声波震动处理,再采用气刀装置进行喷吹处理实现对镀层厚度的精确控制。专利号为 cn201822057031.7的文献公开了涂层厚度自动控制系统通过所述自动测厚装置与所述动力牵引装置和/或加热装置的自动配合很好的实现了对涂层厚度的控制,提高了产品的良率。专利号为cn201910652846.6的文献发明公开了一种热镀铝硅带钢镀层的控制方法。专利号为cn201810446630.x的文献提供一种冷轧热镀锌钢板横向镀层均匀性控制方法。专利号为 cn201310705897.3的文献在热镀锌plc中增设镀层厚度自适应控制单元,气刀压力反馈模型控制单元及气刀位置偏移控制
单元,分别建立镀层厚度自适应前馈控制模型,气刀压力反馈修正模型和气刀操作侧和传动侧位置偏移计算模型,实现镀锌过程中镀层厚度的自动控制。目前检索到的上述专利均没有涉及每个钢卷带头100-200米的过渡过程,由于没有锌层厚度的实际值只能进行前馈控制,如何提高前馈控制的精度方法,尤其是应用大数据深度学习的最新成果学习前馈过程依赖人工经验干涉锌层的控制,从而提高包括带头过渡区域在内的整个钢卷锌层控制良品率,是非常必要的,有重要的意义。
技术实现要素:
5.本发明的目的在于提供一种基于深度学习的热镀锌带钢镀层的控制方法,通过收集镀锌生产中操作人员对带头锌层前馈控制人工干预值,运用深度学习的大数据分析方法,模拟出规格切换时带头锌层前馈值,达到控制好带钢头尾锌层厚度均匀,减少操作干预控制锌层的方法。
6.为了实现上述目的,本发明采用以下技术方案:
7.依据本发明的一个方面,提供了一种基于深度学习的热镀锌带钢镀层的控制方法,包括以下步骤:
8.s1.收集镀锌生产过程中操作人员对带头锌层前馈控制人工干预的有效操作数据;
9.s2.运用深度学习的大数据分析方法对收集的有效操作数据进行模拟,获取自动补偿值计算模型,并将自动补偿值计算模型实时反馈到镀锌生产;
10.s3.对自动补偿值计算模型实现锌层的前馈控制进行效果验证。
11.根据本发明以上方面的一种基于深度学习的热镀锌带钢镀层的控制方法,其中s1包括以下步骤:
12.s11.对带头锌层前馈控制人工干预值历史数据进行清洗,去除掉历史数据中由于机组运行故障或是维修而造成的数据偏差;
13.s12.从所有的历史数据中提取出人工干预操作生效的带钢过渡切换过程数据;
14.s13.将能够有效减少不达标带钢长度的人工干预数据筛选出来。
15.根据本发明以上方面的一种基于深度学习的热镀锌带钢镀层的控制方法,其中s2包括以下步骤:
16.s21.将所有的有效操作数据划分为训练集和测试集;
17.s22.在训练集中通过设定不同的随机数种子从中抽选出部分数据来进行大数据算法模型训练;
18.s23.使用测试集数据对大数据算法模型进行评判,得到不同的权重,融合成为最终算法模型。
19.根据本发明以上方面的一种基于深度学习的热镀锌带钢镀层的控制方法,其中s22中的大数据算法模型包括knn算法模型和gbdt算法模型;
20.所述knn算法模型的公式如下式:
[0021][0022]
所述gbdt算法模型的公式如下式:
[0023][0024]
根据本发明以上方面的一种基于深度学习的热镀锌带钢镀层的控制方法,其中s23包括以下步骤:
[0025]
s231.对大数据算法模型计算误差;
[0026]
s232.结合knn模型算法与gbdt模型算法进行加权融合输出结果;
[0027]
s233.使用测试集数据对对knn模型算法与gbdt模型算法评判,得到不同的权重,融合成为最终算法模型;
[0028]
s234.将最终算法模型结果输出到生产系统,将生产过程中所收集到的连续数据进行离散分类处理,得到合理的人工干预值;
[0029]
s235.人工干预值的结果实时反馈到生产的计算机界面中,实现带钢镀层的前馈控制。
[0030]
根据本发明以上方面的一种基于深度学习的热镀锌带钢镀层的控制方法,其中s232中加权融合输出结果的公式如下:
[0031]
y=∑iω
ifi
(x)。
[0032]
根据本发明以上方面的一种基于深度学习的热镀锌带钢镀层的控制方法,其中s232中最终算法模型公式如下:
[0033][0034]
其中,th
pre
为前卷厚度,th为当前厚度,v为钢卷速度,w
pre
为前卷镀层重量,w为当前镀层重量,g为当前钢种(取值为1,2,3),c
1 c
16
为模型参数。
[0035]
根据本发明以上方面的一种基于深度学习的热镀锌带钢镀层的控制方法,其中s234中连续数据进行离散分类处理考虑的因素包括后卷带钢的钢种、前卷带钢和后卷带钢的厚度及厚度差异、前卷带钢和后卷带钢的目标镀层厚度以及目标厚度差异。
[0036]
根据本发明以上方面的一种基于深度学习的热镀锌带钢镀层的控制方法,其中s234包括以下具体步骤:
[0037]
s2341.将带钢分为三类,即软钢、高强钢和超高强钢;
[0038]
s2342.将带钢厚度变化分为十三类,即
△
th≦-0.55,-0.55《
△
th≦
ꢀ‑
0.45,-0.45《
△
th≦-0.35,-0.35《
△
th≦-0.25,-0.25《
△
th≦-0.15,-0.15《
ꢀ△
th≦-0.05,-0.05《
△
th≦0.05,0.05《
△
th≦0.15,0.15《
△
th≦0.25,0.25《
ꢀ△
th≦0.35,0.35《
△
th≦0.45,0.45《
△
th≦0.55,0.55《
△
th;
[0039]
s2343.将带钢镀层厚度分为七类,即'30≦w《40','40≦w《47','47≦ w《49','49≦w《54','54≦w《60','60≦w《100'以及'100≦w'。
[0040]
采用上述技术方案,本发明具有以下优点:
[0041]
本发明提供了一种基于深度学习的热镀锌带钢镀层的控制方法,在收集镀锌生产中操作人员对带头锌层前馈控制人工干预值,运用深度学习的大数据分析方法,模拟出规格切换时带头锌层前馈值,达到控制好带钢头尾锌层厚度均匀,减少操作干预控制锌层的方法,可以较为快速且准确地控制带钢在热镀锌生产过程中不同钢种、不同规格以及不同
锌层切换过程钢卷锌层的厚度,替代人工锌层控制的干预操作。
附图说明
[0042]
通过阅读参照以下附图对非限制性实施例所作的详细描述,本发明的其它特征、目的和优点将会变得更明显。
[0043]
图1是现有技术中热镀锌锌锅设备的结构示意图;
[0044]
图2是现有技术中热镀锌锌层厚度控制的结构示意图;
[0045]
图3是本发明基于深度学习的热镀锌带钢镀层的控制方法的流程图;
[0046]
图4是本发明深度学习算法的整体流程图;
[0047]
图5是本发明一个实施例中表格模型与人工补偿值差距截屏;
[0048]
图6a是带钢厚度分布异常数据截屏;
[0049]
图6b是带钢厚度分布整体数据截屏;
[0050]
图7是对数据进行深度学习运算后表格模型与人工补偿值差距截屏;
[0051]
图8是经过深度学习模型计算后形成的锌层智能补偿结构表格左半部分截屏;
[0052]
图9是经过深度学习模型计算后形成的锌层智能补偿结构表格右半部分截屏。
具体实施方式
[0053]
以下结合说明书附图对本发明的技术方案进行具体说明,在具体实施方式中详细叙述本发明的详细特征以及优点,其内容足以使任何本领域技术人员了解本发明的技术内容并据以实施,且根据本说明书所揭露的说明书、权利要求及附图,本领域技术人员可轻易地理解本发明相关的目的及优点。
[0054]
图3示出了本发明基于深度学习的热镀锌带钢镀层的控制方法的流程图;一种基于深度学习的热镀锌带钢镀层的控制方法具体如图3所示,包括以下步骤:
[0055]
s1.收集镀锌生产过程中操作人员对带头锌层前馈控制人工干预的有效操作数据;
[0056]
其中s1包括以下步骤:
[0057]
s11.历史数据清洗:为了从历史数据中,分析得到人工干预操作的本质,需要对历史数据进行清洗,去除掉历史数据中由于机组运行故障或是维修而造成的数据偏差;
[0058]
s12.补偿过程提取:从所有的历史数据中提取出人工干预操作生效的带钢过渡切换过程,即锌层反馈控制未能建立的前223米中的锌层厚度数据;
[0059]
s13.优秀数据筛选:将能够有效减少不达标带钢长度的人工干预数据筛选出来,使用大数据分析的方法找到人工干预的规律。
[0060]
图4示出了本发明深度学习算法的整体流程图;
[0061]
s2.运用深度学习的大数据分析方法对收集的有效操作数据进行模拟,获取自动补偿值计算模型,并将自动补偿值计算模型实时反馈到镀锌生产;
[0062]
其中,s2具体包括以下步骤如图4所示:
[0063]
s21.将所有的有效操作数据划分为训练集和测试集;
[0064]
s22.在训练集中通过设定不同的随机数种子从中抽选出部分数据来进行大数据算法模型训练,得到多个单一的knn算法模型或是gbdt算法模型;通常采用2种常用的大数
据算法对收集的有效操作数据进行模拟训练。大数据算法模型包括knn算法模型和gbdt算法模型。
[0065]
knn(k-nearst neighbor)算法模型是通过测量不同特征值之间的距离进行分类。它的思路是:如果一个样本在特征空间中的k个最相似(特征空间中最邻近)的样本中的大多数属于某一个类别,则该样本也属于这个类别。k通常是不大于20 的整数。knn算法中,所选择的邻居都是已经正确分类的对象。该方法在定类决策上只依据最邻近的一个或者几个样本的类别来决定待分样本所属的类别。
[0066]
knn算法模型的公式如下式:
[0067]
设特征空间x是n维实数向量空间rn,xi,xj∈x, xi,xj的l
p
距离定义为:
[0068][0069]
这里p≥1
[0070]
当p=1时,称为曼哈顿距离(manhattan distance),公式为:
[0071][0072]
当p=2时,称为欧式距离(euclidean distance),即
[0073][0074]
当p=∞时,它是各个坐标距离的最大值,计算公式为:
[0075][0076]
gbdt(gradient boosted decision tree)是一种基于迭代的决策树算法,生成的模型由多棵决策树组成,并将所有树的结论累加作为最终结果。gbdt 被认为是一种泛化能力较强的算法,对于线性不可分数据(无法用一个线性函数完全将两类样本数据区分),gbdt往往能取得很好的效果。相较于神经网络,gbdt的参数空间要小很多,训练速度更快,因此在很多场景上更加适合。
[0077]
gbdt算法模型的公式如下式:
[0078][0079]
x为输入样本,f为分类回归树,h为学习器,l是损伤函数,γm是分类回归树每棵树的权重。
[0080]
我们使用损失函数的负梯度来拟合下一棵回归数,当使用均方误差做损失函数的情况下,这一梯度值就等于当前拟合结果与标签值的残差,之后我们通过线性搜索得到这棵回归树的最优系数如下式:
[0081][0082]
s23.使用测试集数据对大数据算法模型进行评判,得到不同的权重,融合成为最终算法模型。
[0083]
其中s23具体包括以下步骤:
[0084]
s231.对大数据算法模型计算误差;
[0085]
s232.结合knn模型算法与gbdt模型算法进行加权融合输出结果;模型融合通常可
以在各种不同的机器学习任务中使结果获得提升。顾名思义,模型融合就是综合考虑不同模型的情况,并将它们的结果融合到一起。本发明中加权融合的方式结合knn算法模型与gbdt算法模型输出结果,其加权融合的公式如下:
[0086]
y=∑iω
ifi
(x)
[0087]
s233.使用测试集数据对对knn模型算法与gbdt模型算法评判,得到不同的权重,融合成为最终算法模型;最终算法模型形式如下,
[0088][0089]
其中:th
pre
为前卷厚度,th为当前厚度,v为钢卷速度,w
pre
为前卷镀层重量,w为当前镀层重量,g为当前钢种(取值为1,2,3),c
1 c
16
为模型参数。
[0090]
上下表面的拟合参数如下:
[0091]-0.03208338,0.04883628,0.0488729,0.05681063,0.38138293, 0.46125552,0.7859489,-5.42717619,7.51021011,6.98208145,
ꢀ‑
1.29637566,-19.415768,1.49983458,,0.03843442,-4.13771428,
ꢀ‑
99.38952538;
[0092]
0.021639053,0.00786637,0.072418322,0.039552197,0.260276435, 0.048002523,-0.25645579,-7.33088329,7.61388319,7.87145222, 0.122959102,-18.6862614,3.88698816,-1.35841714,-7.2584534,
ꢀ‑
81.52097439
[0093]
s234.将最终算法模型结果输出到生产系统,将生产过程中所收集到的连续数据进行离散分类处理,得到合理的人工干预值;根据操作工的操作经验,在带钢切换过程中想要得到合理的人工干预值,连续数据进行离散分类处理考虑的因素包括后卷带钢的钢种、前卷带钢和后卷带钢的厚度及厚度差异、前卷带钢和后卷带钢的目标镀层厚度以及目标厚度差异。
[0094]
根据生产前后钢卷接续的分类情况,s234包括以下具体步骤:
[0095]
s2341.将带钢分为三类,即软钢、高强钢和超高强钢;
[0096]
s2342.将带钢厚度变化分为十三类,即
△
th≦-0.55,-0.55《
△
th≦
ꢀ‑
0.45,-0.45《
△
th≦-0.35,-0.35《
△
th≦-0.25,-0.25《
△
th≦-0.15,-0.15《
ꢀ△
th≦-0.05,-0.05《
△
th≦0.05,0.05《
△
th≦0.15,0.15《
△
th≦0.25,0.25《
ꢀ△
th≦0.35,0.35《
△
th≦0.45,0.45《
△
th≦0.55,0.55《
△
th;
[0097]
s2343.将带钢镀层厚度分为七类,即'30≦w《40','40≦w《47','47≦ w《49','49≦w《54','54≦w《60','60≦w《100'以及'100≦w'。
[0098]
s235.人工干预值的结果实时反馈到生产的计算机界面中,实现带钢镀层的前馈控制。
[0099]
s3.对自动补偿值计算模型实现锌层的前馈控制进行效果验证。
[0100]
在一个具体的实施例中,图5示出了本发明一个实施例中表格模型与人工补偿值差距截屏;从2019年7月1日至2019年9月15日,共提取到970个有效的过渡过程,表格模型给出的补偿值与人工补偿值的差值具体如图5所示,在图5中,大于零的部分表示表格模型给出的补偿值大于操作工给出的补偿值。其中197次表格模型输出值小于人工补偿值1g及以
上,其中132次表格模型输出值小于人工补偿值2g及以上。模型拟合的结果较好地满足了生产需求,钢卷的锌层控制前馈可以通过模型自动输出补偿值,消除了人工干预。
[0101]
图6a示出了带钢厚度分布异常数据截屏;图6b示出了带钢厚度分布整体数据截屏;图7示出了对带钢镀层数据进行深度学习运算后表格模型与人工补偿值差距截屏。通过图6a、图6b可以发现异常数据中带钢厚度大于1000 的比例明显更大。在统计到的132个异常数据中如图7所示,106个来自表格模型中的历史优秀数据,26个来自表格模型中由人工经验填充的数据。使用操作工给出的补偿值重新填充表格模型中对应的过渡过程。经过修正后,表格模型输出值与人工补偿值的差值如图7所示,其中补偿不足的部分大大减少,模型精度得到了提高。
[0102]
图8示出了经过深度学习模型计算后形成的锌层智能补偿结构表格左半部分截屏;图9示出了经过深度学习模型计算后形成的锌层智能补偿结构表格右半部分截屏。在一个具体的实施例中如图8、图9所示,经过深度学习模型计算后,不同钢种的软钢、高强钢和超高强钢,带钢厚度等级、钢卷锌层的厚度、机组速度得到了很好的补偿,达到控制好带钢头尾锌层厚度均匀,可较为快速且准确地控制带钢在热镀锌生产过程中不同钢种、不同规格以及不同锌层切换过程钢卷锌层的厚度,替代人工锌层控制的干预操作。
[0103]
最后,需要指出的是,虽然本发明已参照当前的具体实施例来描述,但是本技术领域中的普通技术人员应当认识到,以上的实施例仅是用来说明本发明,而并非用作为对本发明的限定,在不脱离本发明构思的前提下还可以作出各种等效的变化或替换,因此,只要在本发明的实质精神范围内对上述实施例的变化、变型都将落在本发明的权利要求书范围内。
再多了解一些
本文用于创业者技术爱好者查询,仅供学习研究,如用于商业用途,请联系技术所有人。