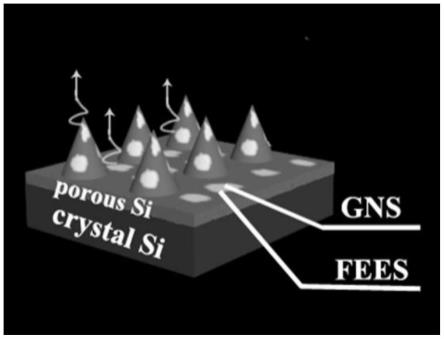
1.本发明属于石墨烯材料技术领域,尤其涉及一种石墨烯基复合材料及其制备方法、应用。
背景技术:
2.碳纳米管因为具有稳定的电子发射、低开启场强和大的正向发射电流密度,被认为是冷阴极制备的优选材料,然而,碳纳米管冷阴极材料的广泛应用仍然受到的一些固有问题的困扰,例如,碳纳米管的管状结构将电子发射限制在顶尖位置,因此对于层状碳纳米管薄膜会表现出不均匀的发射,此外,碳纳米管之间的静电屏蔽不可忽略,因此开发其它碳阴极材料极具科学性和必要性。
3.作为替代碳纳米管最有前途的冷阴极材料,近年来石墨烯受到越来越多的关注。与碳纳米管相比,石墨烯具有更高的纵横比(横向尺寸与厚度比)、独特的电学性能、高的透明度、固有的柔性结构和良好的机械性能,比碳纳米管更适合做柔性冷阴极材料,此外,石墨烯的边缘缺陷点可以作为有源场发射点增强石墨烯的电场发射强度,这使得石墨烯在低电压电子隧穿中的应用更优于碳纳米管。
4.为了充分利用石墨烯边缘缺陷点的高电子发射特性,现有技术中采用石墨烯垂直于基板的结构来最大限度利用石墨烯场发射边沿点(fees),获得高强度的电子发射,例如,通过微波等离子体增强化学气相沉积法制备少层石墨烯使其垂直于基板排列;通过丝网印刷石墨烯薄膜使其垂直于基底或者构建刀片状电子发射体。然而结合参考文献,这些垂直放置的石墨烯在稍高的电压下,发射电流就不太稳定,并且多次循环加压之后,材料的发射电流密度会逐渐减小:典型的以alexander malesevic小组制备的垂直基底生长的石墨烯为例(malesevic a, kemps r, vanhulsel a, et al., field emission from vertically aligned few-layer graphene[j]. j appl phys, 2008, 104: 084301-084301-084305),经过五个循环,不仅发射电流密度发生了明显的衰减,并且场增强因子的浮动范围也较大,在3000~5000之间。
[0005]
因此,如何在保持高发射电流密度的情况下,提高电子发射的稳定性是石墨烯基冷阴极材料在发展过程中需要解决的关键问题。
技术实现要素:
[0006]
本发明实施例的目的在于提供一种石墨烯基复合材料的制备方法,旨在解决上述背景技术中存在的问题。
[0007]
本发明实施例是这样实现的,一种石墨烯基复合材料的制备方法,包括以下步骤:提供硅纳米孔柱阵列;在硅纳米孔柱阵列上沉积催化剂镍纳米晶;以沉积有镍纳米晶的硅纳米孔柱阵列作为基底,以甲烷作为碳源,以氩气和氢气的混合气体作为载气,通过化学气相沉积法得到石墨烯基复合材料,所述复合材料中石墨
烯平行基底生长。
[0008]
优选地,所述硅纳米孔柱阵列采用化学水热腐蚀法制备。
[0009]
优选地,所述硅纳米孔柱阵列采用化学水热腐蚀法制备的步骤具体包括:利用丙酮去除硅片表面的有机污染物,再进行清洗;将 fe(no3)3和hf水溶液构成的腐蚀液放入装有聚四氟乙烯内衬的高压釜中,将硅片夹在聚四氟乙烯固定支架中后放入高压釜,再将高压釜放入加热炉中升温,再经过保温、降温,得到所述硅纳米孔柱阵列。
[0010]
优选地,所述硅片为重掺杂p型单晶硅,所述掺杂浓度10
17
~10
19
cm-3
。
[0011]
优选地,所述在硅纳米孔柱阵列上沉积催化剂镍纳米晶的步骤采用化学水浴沉积法。
[0012]
优选地,所述化学水浴沉积法的步骤具体包括:配置含有氟化铵与乙酸镍的混合溶液;将硅纳米孔柱阵列放入混合溶液中进行反应,反应结束后清洗,即可得到沉积有镍纳米晶的硅纳米孔柱阵列。
[0013]
优选地,所述氟化铵与乙酸镍的摩尔比为30~80:1。
[0014]
优选地,所述通过化学气相沉积法得到石墨烯基复合材料的步骤具体包括:将沉积有镍纳米晶的硅纳米孔柱阵列放入磁舟,再推入清洗干净的石英管中,将石英管两端用法兰固定好,将石英管中空气排掉;向石英管中通入氩气和氢气的混合气体,升高炉温至指定温度,向混合气体中通入甲烷,再将石英管推出加热区至室温区进行冷却,在此过程中继续通入氩气和氢气的混合气体,得到所述石墨烯基复合材料。
[0015]
本发明实施例的另一目的在于提供一种上述石墨烯基复合材料的制备方法制备得到的石墨烯基复合材料。
[0016]
本发明实施例的又一目的在于提供一种上述石墨烯基复合材料在制备场发射器件上的应用。
[0017]
本发明实施例提供的一种石墨烯基复合材料的制备方法,是针对垂直基底石墨烯结构中场发射性能不稳定限制其实际应用的问题而提出的,通过在硅纳米孔柱阵列上沉积催化剂纳米级金属镍,生长平行于基底的石墨烯纳米片,通过石墨烯平行基底的结构,克服垂直基底的结构不稳定,与石墨烯垂直基底的结构相比,在电子发射过程中极大的增强了发射稳定性,同时石墨烯的横向纳米尺度具有比较高的周长面积比,边沿发射点的数量较多,保证了材料的场发射密度,另外,硅纳米孔柱阵列表面的多重取向和粗糙度,增加了石墨烯的生长面积,进而增加了发射体的数量,硅纳米孔柱阵列特殊几何结构也将大大降低发射器之间的静电屏蔽,并大幅增加场增强因子β,提高发射电流强度。
附图说明
[0018]
图1为本发明实施例1中制备得到的石墨烯-硅复合材料的结构示意图(其中,gns代表石墨烯纳米片,fees代表石墨烯场发射边沿点);图2为本发明实施例1中制备得到的石墨烯-硅复合材料的扫描电子显微镜照片;图3为本发明实施例1中制备得到的石墨烯-硅复合材料的x射线衍射谱;
图4为本发明实施例1中制备得到的石墨烯-硅复合材料的场发射性能和稳定性测试图(其中,a表示样品在四个电压周期测量的j-e曲线;b表示样品在四个测量循环相应的f-n图)。
具体实施方式
[0019]
为了使本发明的目的、技术方案及优点更加清楚明白,以下结合附图及实施例,对本发明进行进一步详细说明。应当理解,此处所描述的具体实施例仅仅用以解释本发明,并不用于限定本发明。
[0020]
一种石墨烯基复合材料,所述石墨烯基复合材料为石墨烯-硅复合材料,其制备方法包括以下步骤:s1:制备si纳米孔柱阵列:采用化学水热腐蚀法制备,其中,si片为单晶p型重掺杂,掺杂浓度为10
17 ~10
19 cm-3
,《111》取向;腐蚀前,用丙酮浸泡去除表面的有机污染物,装入样品架采用标准的cra流程清洗,腐蚀液由fe(no3)3和水溶液构成,放入装有聚四氟乙烯内衬的高压釜中,si片夹在聚四氟乙烯固定支架中,放入高压釜,再将高压釜放入加热炉中,升温至120~140℃,保温22~30 min后,放入通风处降温;s2:si纳米孔柱阵列沉积ni纳米晶催化剂:采用化学水浴沉积法制备ni纳米晶,首先,配置含有氟化铵与乙酸镍的混合溶液,将si纳米孔柱阵列放入混合溶液中,反应5~20min,去离子水清洗待用,其中,氟化铵与乙酸镍的摩尔比为(30~80):1;s3:制备graphene-si复合材料(石墨烯-硅复合材料):采用化学气相沉积法制备,先用水和乙醇的混合液将石英管冲洗干净晾干,将沉积ni纳米晶催化剂的si纳米孔柱阵列放入磁舟,再推入石英管,将石英管两端用法兰固定好,真空泵抽至0.1 pa,通入氩气,至管内达大气压,再用真空泵抽至真空,如此反复三次将管中空气排掉,继续通入氩气和氢气的混合气体,将炉温以10 ℃/min 的速度升至800~1000℃,保持18~20 min 后,在混合气体中加入ch4,通入ch4后,将石英管推出加热区至室温区进行冷却,在此过程中继续通入氩气、氢气混合保护气体8~10 min,最终制得graphene-si复合材料。
[0021]
以下结合具体实施例对本发明的具体实现进行详细描述。
[0022]
实施例1一种石墨烯基复合材料,其制备方法包括以下步骤:s1:制备si纳米孔柱阵列:采用化学水热腐蚀法制备,其中,si片的电阻率为0.015 ω
·
cm,为单晶p型重掺杂,掺杂浓度为10
18 cm-3
,《111》取向;腐蚀前,用丙酮浸泡去除表面的有机污染物,装入样品架采用标准的cra流程清洗,腐蚀液由0.04 mol/l fe(no3)3和13 mol/l hf水溶液构成,放入装有聚四氟乙烯内衬的高压釜中,si片夹在聚四氟乙烯固定支架中,放入高压釜,再将高压釜放入加热炉中,升温至140℃,保温25 min后,放入通风处降温;s2:si纳米孔柱阵列沉积ni纳米晶催化剂:采用化学水浴沉积法制备ni纳米晶,首先,配置含有4 mol/l氟化铵与0.05 mol/l
乙酸镍的混合溶液20ml,将si纳米孔柱阵列放入混合溶液中,反应15min,去离子水清洗待用;s3:制备graphene-si复合材料:采用化学气相沉积法制备,先用水和乙醇的混合液将石英管冲洗干净晾干,将沉积ni纳米晶催化剂的si纳米孔柱阵列放入磁舟,再推入石英管,将石英管两端用法兰固定好,真空泵抽至0.1 pa,通入200 sccm氩气,至管内达大气压,再用真空泵抽至真空,如此反复三次将管中空气排掉,继续通入200 sccm氩气和65 sccm氢气的混合气体,将炉温以10 ℃/min 的速度升至1000℃,保持20 min 后,在混合气体中加入10 sccm的ch4,通入ch4后,将石英管推出加热区至室温区进行冷却,在此过程中继续通入氩气、氢气混合保护气体10 min,最终制得graphene-si复合材料。
[0023]
性能测试:(1)graphene-si复合材料的结构图如图1所示;(2)对graphene-si复合材料进行电子显微镜扫描,结果如图2所示;(3)通过对graphene-si复合材料进行x射线衍射,结果如图3所示;(3)对graphene-si复合材料进行场发射性能测试:通过hall 仪,四探针法测得graphene-si复合材料的载流子浓度为5.45
´
10
24
cm-3
,平面电阻率为2.52
´
10-8
ω
·
cm;在室温下,采用二极管结构模型,在大约2
×
10-4 pa压力的真空室中进行,使用氧化锡铟(ito)涂覆的玻璃(ρ= 8
×
10-4 ω ·
cm)作为阳极,graphene-si复合材料为阴极,阳极和阴极间通过云母绝缘片隔离,云母片的厚度为375μm,用数字万用表(sourcemeter-2400,keithley)记录电流-电压数据,结果如图4所示,典型的开启场强为2.85 v/μm,在4.2 v/μm的电场下,可以获得53.9 μa/cm2的电流密度,并且经过4个循环,电流强度没有明显改变,f-n曲线没有出现较大改变;综上所示,本发明实施例制备得到复合体系采用四探针法在hall仪上测得具有高的载流子浓度5.45
´
10
24 cm-3
和低的平面电阻率2.52
´
10-8 ω ·
cm,比大多数的金属电阻率要低两个数量级,为发射电子的石墨烯提供了足够的传导电子,保证了稳定且连续的发射电流;本发明实施例制备得到的graphene-si基材料,与石墨烯垂直基底的结构相比,场发射稳定性得到了大幅提高,考虑到graphene/si-npa的发射面积为1 cm2,在石墨烯基场发射阴极材料中,具有相当强的场发射性能,例如,根据现有技术中公开的内容,氮钝化过的垂直排列的少层石墨烯,发射面积为0.2 cm2,而开启电场达到4.6 v/μm(10.0 μa/cm2),而同样从尺寸为1.0
×
1.0 cm的石墨烯薄膜边缘发射的场电子,开启场强需要50 v/μm,并且在hall仪中通过四探针法测试得到,在开启电压下的导通电流只有10-4
μa/cm2,明显可以看出,在场强相同的情况下,其电流密度没有本发明实施例制备得到的复合材料强,发射面小于本发明实施例的复合材料,而同样发射面积的,没有本发明实施例的复合材料的开启场强大,另外,本发明实施例制备工艺简单,易于大面积大规模生产,适用于低电压冷阴极器件。
[0024]
实施例2一种石墨烯基复合材料,其制备方法包括以下步骤:
s1:制备si纳米孔柱阵列:采用化学水热腐蚀法制备,其中,si片为单晶p型重掺杂,掺杂浓度为10
17 cm-3
,《111》取向;腐蚀前,用丙酮浸泡去除表面的有机污染物,装入样品架采用标准的cra流程清洗,腐蚀液由fe(no3)3和hf水溶液构成,放入装有聚四氟乙烯内衬的高压釜中,si片夹在聚四氟乙烯固定支架中,放入高压釜,再将高压釜放入加热炉中,升温至120℃,保温30min后,放入通风处降温;s2:si纳米孔柱阵列沉积ni纳米晶催化剂:采用化学水浴沉积法制备ni纳米晶,首先,配置含有氟化铵与乙酸镍的混合溶液,将si纳米孔柱阵列放入混合溶液中,反应15min,去离子水清洗待用,氟化铵与乙酸镍的摩尔比为30:1;s3:制备graphene-si复合材料:采用化学气相沉积法制备,先用水和乙醇的混合液将石英管冲洗干净晾干,将沉积ni纳米晶催化剂的si纳米孔柱阵列放入磁舟,再推入石英管,将石英管两端用法兰固定好,真空泵抽至0.1 pa,通入200 sccm氩气,至管内达大气压,再用真空泵抽至真空,如此反复三次将管中空气排掉,继续通入200 sccm氩气和65 sccm氢气的混合气体,将炉温以10 ℃/min 的速度升至800℃,保持20 min 后,在混合气体中加入10 sccm的ch4,通入ch4后,将石英管推出加热区至室温区进行冷却,在此过程中继续通入氩气、氢气混合保护气体10 min,最终制得graphene-si复合材料。
[0025]
实施例3一种石墨烯基复合材料,其制备方法包括以下步骤:s1:制备si纳米孔柱阵列:采用化学水热腐蚀法制备,其中,si片为单晶p型重掺杂,掺杂浓度为10
17 cm-3
,《111》取向;腐蚀前,用丙酮浸泡去除表面的有机污染物,装入样品架采用标准的cra流程清洗,腐蚀液由fe(no3)3和水溶液构成,放入装有聚四氟乙烯内衬的高压釜中,si片夹在聚四氟乙烯固定支架中,放入高压釜,再将高压釜放入加热炉中,升温至130
º
c,保温25min后,放入通风处降温;s2:si纳米孔柱阵列沉积ni纳米晶催化剂:采用化学水浴沉积法制备ni纳米晶,首先,配置含有氟化铵与乙酸镍的混合溶液,将si纳米孔柱阵列放入混合溶液中,反应15min,去离子水清洗待用,其中,氟化铵与乙酸镍的摩尔比为40:1;s3:制备graphene-si复合材料:采用化学气相沉积法制备,先用水和乙醇的混合液将石英管冲洗干净晾干,将沉积ni纳米晶催化剂的si纳米孔柱阵列放入磁舟,再推入石英管,将石英管两端用法兰固定好,真空泵抽至0.1 pa,通入氩气,至管内达大气压,再用真空泵抽至真空,如此反复三次将管中空气排掉,继续通入氩气和氢气的混合气体,将炉温以10 ℃/min 的速度升至850℃,保持18min 后,在混合气体中加入ch4,通入ch4后,将石英管推出加热区至室温区进行冷却,在此过程中继续通入氩气、氢气混合保护气体8min,最终制得graphene-si复合材料。
[0026]
实施例4一种石墨烯基复合材料,其制备方法包括以下步骤:
s1:制备si纳米孔柱阵列:采用化学水热腐蚀法制备,其中,si片为单晶p型重掺杂,掺杂浓度为10
18 cm-3
,《111》取向;腐蚀前,用丙酮浸泡去除表面的有机污染物,装入样品架采用标准的cra流程清洗,腐蚀液由fe(no3)3和水溶液构成,放入装有聚四氟乙烯内衬的高压釜中,si片夹在聚四氟乙烯固定支架中,放入高压釜,再将高压釜放入加热炉中,升温至140℃,保温30min后,放入通风处降温;s2:si纳米孔柱阵列沉积ni纳米晶催化剂:采用化学水浴沉积法制备ni纳米晶,首先,配置含有氟化铵与乙酸镍的混合溶液,将si纳米孔柱阵列放入混合溶液中,反应20min,去离子水清洗待用,其中,氟化铵与乙酸镍的摩尔比为50:1;s3:制备graphene-si复合材料:采用化学气相沉积法制备,先用水和乙醇的混合液将石英管冲洗干净晾干,将沉积ni纳米晶催化剂的si纳米孔柱阵列放入磁舟,再推入石英管,将石英管两端用法兰固定好,真空泵抽至0.1 pa,通入氩气,至管内达大气压,再用真空泵抽至真空,如此反复三次将管中空气排掉,继续通入氩气和氢气的混合气体,将炉温以10 ℃/min 的速度升至900℃,保持18min 后,在混合气体中加入ch4,通入ch4后,将石英管推出加热区至室温区进行冷却,在此过程中继续通入氩气、氢气混合保护气体10 min,最终制得graphene-si复合材料。
[0027]
实施例5一种石墨烯基复合材料,其制备方法包括以下步骤:s1:制备si纳米孔柱阵列:采用化学水热腐蚀法制备,其中,si片为单晶p型重掺杂,掺杂浓度为10
19 cm-3
,《111》取向;腐蚀前,用丙酮浸泡去除表面的有机污染物,装入样品架采用标准的cra流程清洗,腐蚀液由fe(no3)3和水溶液构成,放入装有聚四氟乙烯内衬的高压釜中,si片夹在聚四氟乙烯固定支架中,放入高压釜,再将高压釜放入加热炉中,升温至120℃,保温30min后,放入通风处降温;s2:si纳米孔柱阵列沉积ni纳米晶催化剂:采用化学水浴沉积法制备ni纳米晶,首先,配置含有氟化铵与乙酸镍的混合溶液,将si纳米孔柱阵列放入混合溶液中,反应18min,去离子水清洗待用,其中,氟化铵与乙酸镍的摩尔比为60:1;s3:制备graphene-si复合材料:采用化学气相沉积法制备,先用水和乙醇的混合液将石英管冲洗干净晾干,将沉积ni纳米晶催化剂的si纳米孔柱阵列放入磁舟,再推入石英管,将石英管两端用法兰固定好,真空泵抽至0.1 pa,通入氩气,至管内达大气压,再用真空泵抽至真空,如此反复三次将管中空气排掉,继续通入氩气和氢气的混合气体,将炉温以10 ℃/min 的速度升至950℃,保持20 min 后,在混合气体中加入ch4,通入ch4后,将石英管推出加热区至室温区进行冷却,在此过程中继续通入氩气、氢气混合保护气体10 min,最终制得graphene-si复合材料。
[0028]
实施例6一种石墨烯基复合材料,其制备方法包括以下步骤:s1:制备si纳米孔柱阵列:
采用化学水热腐蚀法制备,其中,si片为单晶p型重掺杂,掺杂浓度为10
19 cm-3
,《111》取向;腐蚀前,用丙酮浸泡去除表面的有机污染物,装入样品架采用标准的cra流程清洗,腐蚀液由fe(no3)3和水溶液构成,放入装有聚四氟乙烯内衬的高压釜中,si片夹在聚四氟乙烯固定支架中,放入高压釜,再将高压釜放入加热炉中,升温至140
º
c,保温28 min后,放入通风处降温;s2:si纳米孔柱阵列沉积ni纳米晶催化剂:采用化学水浴沉积法制备ni纳米晶,首先,配置含有氟化铵与乙酸镍的混合溶液,将si纳米孔柱阵列放入混合溶液中,反应20min,去离子水清洗待用,其中,氟化铵与乙酸镍的摩尔比为70:1;s3:制备graphene-si复合材料:采用化学气相沉积法制备,先用水和乙醇的混合液将石英管冲洗干净晾干,将沉积ni纳米晶催化剂的si纳米孔柱阵列放入磁舟,再推入石英管,将石英管两端用法兰固定好,真空泵抽至0.1 pa,通入氩气,至管内达大气压,再用真空泵抽至真空,如此反复三次将管中空气排掉,继续通入氩气和氢气的混合气体,将炉温以10 ℃/min 的速度升至1000℃,保持20 min 后,在混合气体中加入ch4,通入ch4后,将石英管推出加热区至室温区进行冷却,在此过程中继续通入氩气、氢气混合保护气体10 min,最终制得graphene-si复合材料。
[0029]
实施例7一种石墨烯基复合材料,其制备方法包括以下步骤:s1:制备si纳米孔柱阵列:采用化学水热腐蚀法制备,其中,si片为单晶p型重掺杂,掺杂浓度为10
19 cm-3
,《111》取向;腐蚀前,用丙酮浸泡去除表面的有机污染物,装入样品架采用标准的cra流程清洗,腐蚀液由fe(no3)3和水溶液构成,放入装有聚四氟乙烯内衬的高压釜中,si片夹在聚四氟乙烯固定支架中,放入高压釜,再将高压釜放入加热炉中,升温至120℃,保温22 min后,放入通风处降温;s2:si纳米孔柱阵列沉积ni纳米晶催化剂:采用化学水浴沉积法制备ni纳米晶,首先,配置含有氟化铵与乙酸镍的混合溶液,将si纳米孔柱阵列放入混合溶液中,反应5min,去离子水清洗待用,其中,氟化铵与乙酸镍的摩尔比为80:1;s3:制备graphene-si复合材料:采用化学气相沉积法制备,先用水和乙醇的混合液将石英管冲洗干净晾干,将沉积ni纳米晶催化剂的si纳米孔柱阵列放入磁舟,再推入石英管,将石英管两端用法兰固定好,真空泵抽至0.1 pa,通入氩气,至管内达大气压,再用真空泵抽至真空,如此反复三次将管中空气排掉,继续通入氩气和氢气的混合气体,将炉温以10 ℃/min 的速度升至800℃,保持18 min 后,在混合气体中加入ch4,通入ch4后,将石英管推出加热区至室温区进行冷却,在此过程中继续通入氩气、氢气混合保护气体8min,最终制得graphene-si复合材料。
[0030]
以上所述仅为本发明的较佳实施例而已,并不用以限制本发明,凡在本发明的精神和原则之内所作的任何修改、等同替换和改进等,均应包含在本发明的保护范围之内。
再多了解一些
本文用于创业者技术爱好者查询,仅供学习研究,如用于商业用途,请联系技术所有人。