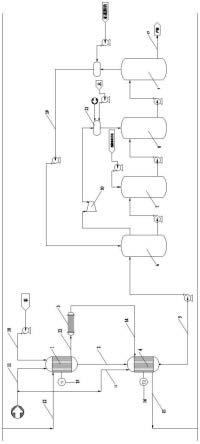
1.本发明涉及一种制备间苯二酚的磺化工艺,具体地说,是以微通道反应器为磺化反应装置,以苯和三氧化硫为原料,连续化制备间苯二酚的方法,属于化工生产领域。
背景技术:
2.间苯二酚,是一种白色结晶性粉末状有机化合物,又名1,3-苯二酚。由于其苯结构上含有两个羟基取代基,易发生加氢、卤化、胺化、酰化和磺化等反应,因此其作为一种重要的精细化工原料广泛地用于染料、医药、聚烯烃的紫外线稳定剂、特殊防水粘合剂、合成树脂、化妆品以及农药等生产工艺过程。间苯二酚合成的间甲树脂,因其在高温条件下以及制品加工成型过程中表现出优异的耐久性,作为补强橡胶广泛地用于轮胎、胶带、胶管等制备过程。2020年中国间苯二酚需求占比前三的领域为橡胶加工、木材黏合剂、染料,占比分别为53%、17%、8%。同时间苯二酚作为合成间氨基酚清洁工艺的主要颜料,因间氨基酚为原料生产的压敏、热敏信息染料市场的增加,加大了对上游原料间苯二酚的需求量。
3.目前工业上生产间苯二酚的主要方法为以下几种:苯磺化碱熔法、苯酚羟基化法、间二异丙苯氧化法、芳基化法。苯磺化碱熔法因其工艺简单、技术已成熟,是我国工业生产间苯二酚的主要方法。苯磺化碱熔法以苯为原料,发烟硫酸作为磺化剂,通过两步磺化反应后将生成的物料通过与氢氧化钠进行中和、碱熔后,再进行酸化制得间苯二酚,通过加入乙醚、异丙醚或正丁醇萃取,蒸馏获得间苯二酚产物。在整个工艺中,中和酸与化过程生成大量的硫酸钠,以及碱熔过程生成的亚硫酸钠都会使得后续的副产物处理难度加大、处理成本升高,且磺化过程中为解决磺化反应过程中生成的水是硫酸浓度下降、反应速率减慢的问题,因而使用过量的发烟硫酸,磺化、碱熔、酸化过程中使用的氢氧化钠、硫酸等都为强酸、强碱,危险系数较高且对环境损害较大。例如:生成1吨的间苯二酚其在中和酸化步骤共生成副产物硫酸钠量为7.6吨,而在碱熔过程中产生的副产物亚硫酸钠量为3.4吨,后续对副产物的处理是一个较为棘手的问题。
技术实现要素:
4.针对以上现有技术存在的缺点和不足之处,提供一种基于微通道反应器体系的磺化反应体系,该反应系统能极大地提高磺化的转化率与选择性,同时确保放热反应的热量及时移出,使得工艺的安全性得以提高。
5.本发明的第二个目的是提供上述反应的反应方法。
6.为此,本发明提供的第一个技术方案是这样的:
7.一种基于微通道反应器制备间苯二酚的磺化反应系统,包括一磺化反应微通道反应器,所述的一磺化反应微通道反应器通过第一产物管道与二磺化反应微通道反应器连通,所述的第一产物管道上还设有换热器,所述的二磺化反应微通道反应器通过第二反应通道与中和反应罐连通,所述中和反应罐通过管路与碱熔反应罐连通,所述碱熔反应罐通过管路与酸化反应罐连通,所述酸化反应罐通过管路与分离反应罐连通;
8.所述的一磺化反应微通道反应器上部设有苯进料管、磺化剂第一进样管和冷却水进料管;
9.所述的二磺化反应微通道反应器上部设有磺化剂第二进样管、加热水进料管;
10.所述的分离反应罐设有间苯二酚出料管。
11.进一步的,上述的一种基于微通道反应器制备间苯二酚的磺化反应系统,所述的一磺化反应微通道反应器上设有第一温度计;所述的二磺化反应微通道反应器上设有第二温度计。
12.进一步的,上述的一种基于微通道反应器制备间苯二酚的磺化反应系统,所述的分离反应罐顶部通过亚硫酸钠管道连通中和反应罐,所述的亚硫酸钠管道上还设有亚硫酸钠混合器。
13.进一步的,上述的一种基于微通道反应器制备间苯二酚的磺化反应系统,所述的中和反应罐通过管道依次与酸化混合器、酸化反应罐相连,所述的反应罐与酸化混合器之间的管道设有压缩机。
14.进一步的,上述的一种基于微通道反应器制备间苯二酚的磺化反应系统,所述的一磺化反应微通道反应器下部设有冷却水出料管,出料冷却水经换热器后通过加热水进料管通入二磺化反应微通道反应器;
15.所述的二磺化反应微通道反应器下部设有加热水出料管道。
16.进一步的,上述的一种基于微通道反应器制备间苯二酚的磺化反应系统,所述的一磺化反应微通道反应器、二磺化反应微通道反应器的内部均由微混合器和微通道两部分组成。
17.进一步的,上述的一种基于微通道反应器制备间苯二酚的磺化反应系统,所述的一磺化反应微通道反应器、二磺化反应微通道反应器均选用t型微通道反应器、w型微通道反应器、y型微通道反应器、分割-重组型微通道反应器的其中之一。
18.进一步的,上述的一种基于微通道反应器制备间苯二酚的磺化反应系统,所述的微通道反应器的管径为0.5-5mm。
19.本发明提供的第二个技术方案是:
20.一种基于微通道反应器制备间苯二酚的磺化反应系统制备间苯二酚的方法,该方法依次包括下述步骤:
21.1)一磺化反应
22.向一磺化反应微通道反应器内以78-160kg/h进料量通入苯,以80-240kg/h进料量通入so3,苯与so3的摩尔比为1-1:1.5,通过调控冷却水使一磺化反应的反应温度在20-50℃,反应物料在微通道反应器内的停留时间为0.5-2h,得到一产物苯磺酸;
23.2)二磺化反应
24.向二磺化反应微通道反应器以40-300kg/h的进料通量通入so3,一产物苯磺酸的进料量为150-320kg/h,使苯与so3的摩尔比为1-1:1.7,通过加热器调节加热物料的温度使二磺化反应的反应温度在140-250℃,物料在微通道反应器内的停留时间为0.5-3h,得到二产物间苯二磺酸;
25.3)中和反应
26.向中和反应罐以64-360kg/h进料通量通入中和剂亚硫酸钠,二产物间苯二磺酸段
进料通量为230kg/h-480kg/h,使苯与亚硫酸钠的摩尔比在1-1:1.4之间,得到中和反应产物间苯二磺酸钠、二氧化硫、水;
27.4)碱熔反应
28.向碱熔反应罐以160-560kg/h进料通量通入熔融氢氧化钠,中和反应产物进料通量为250-565kg/h,控制苯与氢氧化钠的摩尔比在1:4-1:7,反应温度在320-380℃,碱熔反应时间为0.5-2h,得碱熔产物间苯二酚钠、亚硫酸钠、水;
29.5)酸化反应
30.向酸化反应罐以35-340kg/h进料总通量通入so2,碱熔反应产物进料通量为155-560kg/h,水的通量为10-90kg/h,当ph=4.3-5.4时,停止酸化反应,而后将产物通入分离反应罐分离获得间苯二酚产物。
31.与现有技术相比,本发明的有益效果是:
32.1、本发明使用微通道反应器作为磺化反应场所,利用微通道反应器内部线性尺寸减小所带来高混合度、高传质传热效率、高反应面积的优势,大大提升了磺化反应的转化率与选择性,同时确保放热反应的热量及时移出,使得工艺的安全性得以提高,同时通过微通道反应器数增的方式就可以快速实现工业化生产。
33.2、本发明以so3作为磺化剂,选用微通道反应器作磺化反应场所。对比传统苯磺化碱熔法工艺,传统工艺以发烟硫酸作磺化剂,反应生成的水使硫酸浓度下降、反应速率减慢,因此要使用过量的磺化剂,既不节能经济又不安全。以so3作磺化剂时,由于so3过于活泼,当so3过量时容易生成砜类等副产物,因此不利于传统的大规模工业生产方法,而本发明选用微通道反应器作磺化反应场所,由于微通道反应器所特有的构造,通过控制微通道反应器进料的流速以及物料停留时间,就可以达到精确调整反应物料配比的效果,使得反应单位面积不会有过量的so3积累,解决了磺化时砜类副产物的产生。
34.3、本发明中和反应与酸化反应中所分别使用中和剂与酸化剂都是源于生产过程中回收利用的副产物,中和剂为亚硫酸钠,中和后产生间苯二磺酸钠以及副产物水和二氧化硫,而二氧化硫可作为酸化剂亚硫酸氢的原料。中和反应所使用的亚硫酸钠盐为碱熔过程和酸化过程的副产物,经过分离反应后,完成间苯二酚的提取,同时完成亚硫酸盐的回收利用。此方法使大量副产物得以循环利用,解决了副产物的后处理问题,是一种减少成本、绿色环保的间苯二酚生产工艺。
附图说明
35.图1为本发明所述的基于微通道反应器的间苯二酚磺化反应体系示意图。
36.附中附件代表元件名称如下:
37.一磺化反应微通道反应器1,第一产物管道2,换热器3,二磺化反应微通道反应器4,第二反应通道5,中和反应罐6,碱熔反应罐7,酸化反应罐8,分离反应罐9,苯进料管10,磺化剂第一进样管11,冷却水进料管12;磺化剂第二进样管13,加热水进料管14,第一温度计15,第二温度计16,间苯二酚出料管17,亚硫酸钠混合器18,亚硫酸钠管道19,压缩机20,酸化混合器21,冷却水出料管22,加热水出料管道23。
具体实施方式
38.下面结合实施例对本发明做进一步详细的描述,但本发明的实施方式不限于此。
39.实施例1
40.本发明提供一种基于微通道反应器制备间苯二酚的磺化反应系统,参阅图1,包括一磺化反应微通道反应器1,所述的一磺化反应微通道反应器1用于苯和三氧化硫在低温下反应生成苯磺酸,所述的一磺化反应微通道反应器1通过第一产物管道2与二磺化反应微通道反应器4连通,使得一磺化反应微通道反应器1内反应后的产物苯磺酸通入二磺化反应微通道反应器4;
41.所述二磺化反应微通道反应器4用于苯磺酸和三氧化硫在高温下取代反应生成间苯二磺酸,所述的第一产物管道2上还设有换热器3,所述换热器3与冷却水出料管22相连用于加热出料冷却水后通过加热水进料管14通入二磺化反应微通道反应器4,所述的二磺化反应微通道反应器4下部设有加热水出料管道23;
42.所述的二磺化反应微通道反应器4通过第二反应通道5与中和反应罐6连通,所述中和反应罐6通过管路与碱熔反应罐7连通所述碱熔反应罐7通过管路与酸化反应罐8连通,所述酸化反应罐8通过管路与分离反应罐9连通;
43.所述的中和反应罐6通过管道依次与酸化混合器21、酸化反应罐8相连,所述的中和反应罐6与酸化混合器21之间的管道设有压缩机20,使得产生的so2通过管道经过压缩机20压缩后进入酸化混合器21,与直接通入的so2混合,混合后进入酸化反应罐8,进行酸化反应;
44.所述的分离反应罐9设有间苯二酚出料管17。所述的分离反应罐9顶部通过亚硫酸钠管道19连通中和反应罐6,所述的亚硫酸钠管道19上还设有亚硫酸钠混合器18,使得分离反应罐中的亚硫酸钠通过管道进入亚硫酸钠混合器18,与直接通入的亚硫酸混合,混合后经亚硫酸钠管道19进入中和反应罐5,进行中和反应。
45.所述的一磺化反应微通道反应器1上部设有苯进料管10、磺化剂第一进样管11和冷却水进料管12;
46.所述的二磺化反应微通道反应器4上部设有磺化剂第二进样管13、加热水进料管14;
47.为了便于检测微道反应器内的温度,所述的一磺化反应微通道反应器上设有第一温度计15;所述的二磺化反应微通道反应器上设有第二温度计16。
48.更具体的书,所述的一磺化反应微通道反应器1、二磺化反应微通道反应器3的内部均由微混合器和微通道两部分组成,所述的微通道反应器的管径为0.5-5mm,优选2mm。
49.所述的一磺化反应微通道反应器、二磺化反应微通道反应器均选用t型微通道反应器、w型微通道反应器、y型微通道反应器、分割-重组型微通道反应器的其中之一。
50.实施例2
51.本发明提供的一种基于微通道反应器的间苯二酚磺化反应工艺,采用实施例1所设计的基于微通道反应器制备间苯二酚的磺化反应系统,其具体过程包括:
52.1)选用y型结构的六接口微通道反应器,微通道的管径为2.5mm,原料苯经过苯进料管10,磺化剂so3经过磺化剂第一进样管11通入一磺化微通道反应器1内,苯的进料通量为78kg/h,so3的进料通量为96kg/h,苯与so3的摩尔比为1:1.2,冷却水物料经过冷却水进料
管12通入一磺化微通道反应器中,通过监测一磺化微反应器1上的第一温度计15,调控反应温度在30℃。反应物料在一磺化微混合器中完成混合后,进入一磺化微通道内进行磺化反应,在微通道反应停留时间为1h,生成一产物苯磺酸。
53.2)一产物苯磺酸与磺化剂so3分别通过第一产物管道2与磺化剂第二进样管13通入二磺化微通道反应器4后,先在二磺化微混合器4中完成混合后进行二磺化反应,so3的进料通量为112kg/h,一产物进料通量为158kg/h。冷却水出料管22与换热器3相连,出料冷却水在换热器3中加热后经加热水进料管14通入二磺化反应微通道反应器4,通过监测二磺化反应微通道反应器4上的第二温度计16,调节二磺化反应的反应温度在160℃,反应物料在二磺化微通道反应器内的停留时间为2h,生成二产物间苯二磺酸经过第二反应通道5通入中和反应罐6,反应完成后的加热水经二磺化反应微通道反应器4下部的加热水出料管道23流出。
54.3)二产物间苯二磺酸通入中和反应罐6,中和剂由分离反应罐中产生的亚硫酸钠与直接加入的亚硫酸钠在经亚硫酸钠混合器18混合后通过亚硫酸钠管道19通入中和反应罐6,中和剂进料通量为177kg/h,中和至ph=6~7时停止反应,生成三产物间苯二磺酸钠、二氧化硫和水,除生成的二氧化硫通入酸化反应罐8外,其余产物均通入碱熔反应罐7。
55.4)将熔融的氢氧化钠通入碱熔反应罐7中,氢氧化钠的进料通量为220kg/h,苯与氢氧化钠的摩尔比为1:5.5,反应温度为330℃,碱熔反应时间为1.5h,生成四产物间苯二酚钠、亚硫酸钠和水,将其通入酸化反应罐8中。
56.5)四产物、二氧化硫与水混合通入酸化反应罐8中。中和反应罐产生的二氧化硫通过管道经过压缩机20压缩后进入酸化混合器21,与直接通入的so2混合,混合后进入酸化反应罐8,so2的进料总通量为64kg/h,水的通量为20kg/h,当ph=4.5时,停止酸化反应,完成酸化后将其通入分离反应罐9中,使用乙醚萃取分离得间苯二酚产物,萃取完成后的间苯二酚经间苯二酚出料管17流出。
57.实施例3
58.本发明提供的一种基于微通道反应器的间苯二酚磺化反应工艺,采用实施例1所设计的基于微通道反应器制备间苯二酚的磺化反应系统,其具体过程包括:
59.1)选用y型结构的六接口微通道反应器,微通道的管径为3mm,原料苯经过苯进料管10,磺化剂so3经过磺化剂第一进样管11通入一磺化微通道反应器1内,苯的进料通量为100kg/h,so3的进料通量为140kg/h,苯与so3的摩尔比为1:1.4,冷却水物料经过冷却水进料管12通入一磺化微通道反应器中,通过监测一磺化微反应器1上的第一温度计15,调控反应温度在40℃。反应物料在一磺化微混合器中完成混合后,进入一磺化微通道内进行磺化反应,在微通道反应停留时间为0.5h,生成一产物苯磺酸。
60.2)一产物苯磺酸与磺化剂so3分别通过第一产物管道2与磺化剂第二进样管13通入二磺化微通道反应器4后,先在二磺化微混合器4中完成混合后进行二磺化反应,so3的进料通量为130kg/h,一产物进料通量为198kg/h。冷却水出料管22与换热器3相连,出料冷却水在换热器3中加热后经加热水进料管14通入二磺化反应微通道反应器4,通过监测二磺化反应微通道反应器4上的第二温度计16,调节二磺化反应的反应温度在200℃,反应物料在二磺化微通道反应器内的停留时间为1h,生成二产物间苯二磺酸经过第二反应通道5通入中和反应罐6,反应完成后的加热水经二磺化反应微通道反应器4下部的加热水出料管道23
流出。
61.3)二产物间苯二磺酸通入中和反应罐6,中和剂由分离反应罐中产生的亚硫酸钠与直接加入的亚硫酸钠在经亚硫酸钠混合器18混合后通过亚硫酸钠管道19通入中和反应罐6,中和剂进料通量为220kg/h,中和至ph=6~7时停止反应,生成三产物间苯二磺酸钠、二氧化硫和水,除生成的二氧化硫通入酸化反应罐8外,其余产物均通入碱熔反应罐7。
62.4)将熔融的氢氧化钠通入碱熔反应罐7中,氢氧化钠的进料通量为325kg/h,苯与氢氧化钠的摩尔比为1:6.5,反应温度为350℃,碱熔反应时间为1h,生成四产物间苯二酚钠、亚硫酸钠和水,将其通入酸化反应罐8中。
63.5)四产物、二氧化硫与水混合通入酸化反应罐8中。中和反应罐产生的二氧化硫通过管道经过压缩机20压缩后进入酸化混合器21,与直接通入的so2混合,混合后进入酸化反应罐8,so2的进料总通量为70kg/h,水的通量为30kg/h,当ph=5.2时,停止酸化反应,完成酸化后将其通入分离反应罐9中,使用正丁醇萃取分离得间苯二酚产物,萃取完成后的间苯二酚经间苯二酚出料管17流出。
64.需要说明的是,本技术采用的微通道反应器均通过商业渠道直接采购的,y型结构的六接口微通道反应器采购于昆山复希工程技术有限公司。
65.上述实施例为本发明较佳的实施方式,但本发明的实施方式并不受上述实施例的限制,其他的任何未背离本发明的精神实质与原理下所做的改变、修饰、替代、组合、简化,均应为等效的置换方式,都包含在本发明的保护范围之内。
再多了解一些
本文用于创业者技术爱好者查询,仅供学习研究,如用于商业用途,请联系技术所有人。