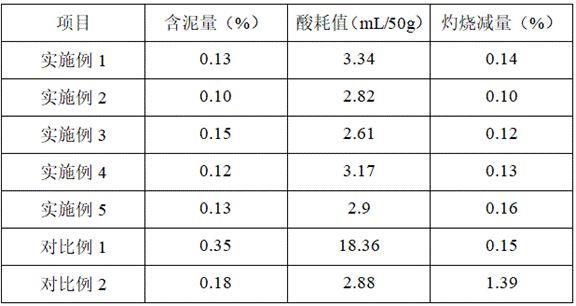
1.本发明涉及旧砂再生技术领域,具体的,涉及一种含有树脂类有机粘结剂的铸造粘土混合旧砂再生方法。
背景技术:
2.我国是铸造大国,铸造生产中产生的大量旧砂如得不到再生回用而废弃,不仅是对资源的极大浪费,而且还会产生粉尘污染和固体废弃物污染,给环境带来巨大的危害。铸造生产的发展趋势是绿色清洁生产,为了实现砂型铸造的绿色清洁生产,旧砂的全部再生回用是关键。
3.根据旧砂再生原理的不同,旧砂再生方法分为干法再生、湿法再生、热法再生。其中,干法再生是利用空气或机械的方法将旧砂粒加速至一定的速度,靠旧砂粒与金属构件间或砂粒互相之间的碰撞、摩擦作用再生旧砂,设备简单,目前主要用作粘土砂的再生。湿法再生是利用水的溶解、擦洗作用及机械搅拌作用,去除旧砂粒表面的残留粘结剂、盐、酯等水溶性物质,目前主要用作水玻璃砂的再生。热法再生是通过焙烧炉将旧砂加热到一定温度,以脆化、分解或烧掉旧砂颗粒表面残留的粘结剂,目前主要用作覆膜砂、热硬树脂砂等有机粘结剂砂的再生。
4.但是实际生产中废弃的旧砂大部分是粘土湿型旧砂和混入粘土砂中的树脂砂(包括冷芯盒砂、热芯盒砂和覆膜砂等),现有的旧砂再生技术基本上都是针对单一型砂进行的,而对于混合废旧砂的再生回用则没有很成熟的技术,采用传统单一再生方法很难实现混合旧砂的完全再生。因此,需结合不同方法优势,通过联合再生获得高性能再生砂。
5.专利cn103170575a公开了一种粘土旧砂完全再生用成套设备,包括高温脆化装置、冷却装置、多排磨轮再生机、微粉分离装置、再生砂改性装置和三回程滚筒,其再生方法本质上为热法 干法联合再生。热-干法联合再生工艺原理为通过加热使旧砂表面的粘土残留物烧结脆化,再通过强力摩擦去除脆化层,为了保证残留物尽可能脆化的同时又不能形成厚的鲕化层,需要专用的焙烧设备且加热温度窗口窄,获得的再生砂存在含泥量偏高问题,需要专用的焙烧炉,再生成本高。
6.专利cn103406490a公开了一种铸造废砂再生回用方法及设备,通过前处理、清洗、干燥、覆膜处理获得再生砂制备的覆膜砂,其再生工艺本质上属于湿法 低温加热(烘干)联合再生。该工艺获得的再生砂存在酸耗值和灼烧减量偏高的问题,再生砂膨胀系数大,只能用于生产尺寸精度要求不高的铸件。
技术实现要素:
7.本发明提出一种含有树脂类有机粘结剂的铸造粘土混合旧砂再生方法,解决了现有技术中的旧砂再生方法得到的再生砂含泥量、酸耗值和灼烧减量偏高,再生砂膨胀系数大的问题。
8.本发明的技术方案如下:
一种含有树脂类有机粘结剂的铸造粘土混合旧砂再生方法,包括以下步骤:s1、将含有树脂类有机粘结剂的铸造粘土经过破碎、筛分、磁选得到非磁性混合旧砂;s2、对所述非磁性混合旧砂依次进行第一阶段水洗和第二阶段水洗,第一阶段水洗过程中加入碱性溶液,第二阶段水洗过程中加入酸性溶液;s3、水洗完成后静置脱水得到水洗砂;s4、将水洗砂焙烧后冷却至室温得到再生砂。
9.作为进一步的技术方案,所述步骤s1中筛分采用振动筛进行筛分,去除筛上旧砂,振动筛目数优选为40目。
10.作为进一步的技术方案,筛下旧砂再经磁选机进行2-3次磁选,得到非磁性混合旧砂。
11.作为进一步的技术方案,水洗在擦洗机中进行,擦洗机转速为300-400rad/min。
12.作为进一步的技术方案,所述步骤s2中酸性溶液包括草酸、乙酸或者磷酸中的一种或多种,浓度为0.02-0.2mol/l。
13.作为进一步的技术方案,所述步骤s2中碱性溶液的浓度为0.02-0.2mol/l。
14.作为进一步的技术方案,所述碱性溶液包括氢氧化钠、氢氧化钾、氢氧化钙中的一种或多种。
15.作为进一步的技术方案,所述步骤s2中第一阶段水洗和第二阶段水洗均进行2-4次;每次水洗时,水的质量与非磁性混合旧砂的质量比为1.5-2:1。
16.作为进一步的技术方案,所述碱性溶液在第一阶段水洗过程中每次水洗时加入,加入量为每次水洗时水的质量的5%-15%。
17.作为进一步的技术方案,所述酸性溶液在第二阶段水洗过程中每次水洗时加入,加入量为每次水洗时水的质量的8%-20%。
18.作为进一步的技术方案,每次水洗时间为5-10min,总水洗时间为20-60min。
19.作为进一步的技术方案,所述第一阶段水洗水温为60-90℃,第二阶段水洗水温为5-30℃。
20.作为进一步的技术方案,所述树脂类有机粘结剂为酚醛树脂和/或呋喃树脂。
21.作为进一步的技术方案,所述步骤s4中焙烧温度为680-880℃,焙烧时间5-15min。
22.本发明所采用的焙烧工艺目的为使水洗后残留的树脂等在高温下通过烧损去除,传统加热设备均可满足要求,且加热温度窗口范围广,操作简单,降低设备成本。
23.作为进一步的技术方案,所述步骤s4中,冷却具体为:以1.2-1.6℃/min的速率冷却至600℃;以0.8-1.2℃/min的速率冷却至500℃;以6-8℃/min的速率快速冷却至室温。
24.本发明中通过控制680-880℃高温焙烧,可完全去除混合旧砂中的残留树脂,另外结合阶段冷却工艺,在高温阶段缓冷促使全部旧砂实现石英到鳞石英的转变,降低了再生砂的热膨胀性,在低温阶段快速冷却,提高再生效率。焙烧温度680-880℃能够使得硅砂发生石英向鳞石英的转变,然后再通过缓慢冷却使得硅砂转变为鳞石英的低温变体。相比石英,鳞石英变体在加热过程中发生的相变具有低的体积膨胀率,从而降低石英砂的热膨胀
性,改善铸件产生夹砂、结疤和脉纹等缺陷并提高铸件尺寸精度。
25.本发明的有益效果为:1、经本发明处理所得再生砂,含泥量可降至0.1%,提高了混合旧砂脱膜率,再生成品率达到97%以上,混合旧砂再生后酸耗值可降至2.6ml/50g,混合旧砂再生后灼烧减量为0.06%,能实现100%的冷芯盒造型使用。
26.2、本发明对铸造混合旧砂进行多次水洗,可以有效去除易溶于水的各类杂质。同时在水洗时加入碱性溶液作为反应剂,可与不易溶于水的粘土烧结残留物发生反应达到去除的目的,有效降低了再生砂含泥量。通过在水洗过程中加入酸性溶液作为改性剂,有效降低了再生砂酸耗值。同时本发明优选的改性剂为弱酸性,相比其他报道的加入盐酸等强酸,本发明的添加剂对设备的腐蚀作用低,可延长擦洗机使用寿命。
27.3、经水洗后的旧砂仅残留树脂包裹物,可经后续高温焙烧去除,使水洗残留的树脂完全烧损。与传统热法再生工艺焙烧是为了使砂粒表面残留粘土脆化形成脆化层相比,本发明不需要专用的焙烧炉,再生成本低,且焙烧温度可选择范围广(粘土脆化层形成过程中焙烧温度不能太低,否则不能完全烧结脆化,温度也不能太高,否则形成高硬度的鲕化层很难再去除掉),能充分发挥焙烧处理的优势。
28.4、本发明中通过高温焙烧,在降低再生砂灼烧减量的同时,促使硅砂发生石英向鳞石英的转变,从而降低石英砂的热膨胀性,改善铸件产生夹砂、结疤和脉纹等缺陷并提高铸件尺寸精度。相比热法 机械擦磨联合再生工艺,水洗法操作简单,设备成本低,可有效降低再生砂的杂质含量。
具体实施方式
29.下面将结合本发明实施例,对本发明实施例中的技术方案进行清楚、完整地描述,显然,所描述的实施例仅仅是本发明一部分实施例,而不是全部的实施例。基于本发明中的实施例,本领域普通技术人员在没有作出创造性劳动前提下所获得的所有其他实施例,都涉及本发明保护的范围。
30.实施例1一种含有树脂类有机粘结剂的铸造粘土混合旧砂再生方法,包括以下步骤:s1、预处理:将含有树脂类有机粘结剂的铸造粘土破碎后经过40目振动筛进行筛分,去除筛上旧砂、筛下旧砂再经磁选机磁选得到非磁性混合旧砂;s2、水洗:对非磁性混合旧砂导入擦洗机,控制擦洗机转速300-400rad/min,依次进行第一阶段水洗和第二阶段水洗:第一阶段水洗4次,过程中,控制水温60-70℃,每次水洗时加入氢氧化钠溶液(0.02mol/l),水的质量与非磁性混合旧砂的质量比为1.5:1,氢氧化钙溶液为每次水洗时水的质量的5%,每次水洗时间为5min;第二阶段水洗4次,过程中,控制水温20-30℃,第四次水洗时加入草酸溶液(0.02mol/l),水的质量与非磁性混合旧砂的质量比为1.5:1,草酸溶液为水洗时水的质量的8%,每次水洗时间为5min;s3、水洗完成后静置脱水得到水洗砂;s4、将水洗砂焙烧后冷却至室温得到再生砂,焙烧温度为680-700℃,焙烧时间
15min;冷却具体为:以1.2℃/min的速率冷却至600℃;以0.8℃/min的速率冷却至500℃;以6℃/min的速率快速冷却至室温。
31.实施例2一种含有树脂类有机粘结剂的铸造粘土混合旧砂再生方法,包括以下步骤:s1、预处理:将含有树脂类有机粘结剂的铸造粘土破碎后经过40目振动筛进行筛分,去除筛上旧砂、筛下旧砂再经磁选机磁选得到非磁性混合旧砂;s2、水洗:对非磁性混合旧砂导入擦洗机,控制擦洗机转速300-400rad/min,依次进行第一阶段水洗和第二阶段水洗:第一阶段水洗2次,过程中,控制水温80-90℃,每次水洗时加入氢氧化钙溶液(0.2mol/l),水的质量与非磁性混合旧砂的质量比为2:1,氢氧化钙溶液为每次水洗时水的质量的15%,每次水洗时间为10min;第二阶段水洗3次,过程中,控制水温5-10℃,第三次水洗时加入乙酸溶液(0.2mol/l),水的质量与非磁性混合旧砂的质量比为2:1,乙酸溶液为水洗时水的质量的20%,每次水洗时间为10min;s3、水洗完成后静置脱水得到水洗砂;s4、将水洗砂焙烧后冷却至室温得到再生砂,焙烧温度为850-880℃,焙烧时间5min;冷却具体为:以1.6℃/min的速率冷却至600℃;以1.2℃/min的速率冷却至500℃;以8℃/min的速率快速冷却至室温。
32.实施例3一种含有树脂类有机粘结剂的铸造粘土混合旧砂再生方法,包括以下步骤:s1、预处理:将含有树脂类有机粘结剂的铸造粘土破碎后经过40目振动筛进行筛分,去除筛上旧砂、筛下旧砂再经磁选机磁选得到非磁性混合旧砂;s2、水洗:对非磁性混合旧砂导入擦洗机,控制擦洗机转速300-400rad/min,依次进行第一阶段水洗和第二阶段水洗:第一阶段水洗3次,过程中,控制水温70-80℃,每次水洗时加入氢氧化钙溶液(0.1mol/l),水的质量与非磁性混合旧砂的质量比为2:1,氢氧化钙溶液为每次水洗时水的质量的10%,每次水洗时间为5min;第二阶段水洗4次,过程中,控制水温15-20℃,第三时加入磷酸溶液(0.2mol/l),水的质量与非磁性混合旧砂的质量比为2:1,磷酸溶液为水洗时水的质量的20%,每次水洗时间为5min;s3、水洗完成后静置脱水得到水洗砂;s4、将水洗砂焙烧后冷却至室温得到再生砂,焙烧温度为700-750℃,焙烧时间5min;
冷却具体为:以1.5℃/min的速率冷却至600℃;以1℃/min的速率冷却至500℃;以8℃/min的速率快速冷却至室温。
33.实施例4与实施例1相比,冷却具体为:以1.2℃/min的速率冷却至600℃;以6℃/min的速率快速冷却至室温;其他与实施例1均相同。
34.实施例5与实施例1相比,焙烧温度为600-620℃,焙烧时间15min;其他与实施例1均相同。
35.对比例1与实施例1相比,水洗时只进行第一阶段水洗,不进行第二阶段水洗,其他与实施例1均相同。
36.对比例2与实施例1相比,焙烧温度为350-370℃,焙烧时间15min;其他与实施例1均相同。
37.实施例和对比例进行再生的旧砂均为同一批次。
38.将实施例和对比例得到的再生砂进行按照《gb/t 2684-2009 铸造用砂及混合料试验方法》测试含泥量、酸耗值、灼烧减量,测试再生成品率。结果如表1所示:表1 实施例和对比例再生砂性能测试通过上表数据可以发现,对比例1中仅进行第一阶段水洗,不进行第二阶段水洗,导致再生砂的含泥量和酸耗值都大幅度增大,不利于旧砂的回收再利用。实施例5与实施例1相比,降低了煅烧温度,灼烧减量有一定程度的降低,对其他性能没有显著影响。但是对比例2中进一步降低煅烧温度,会导致再生砂的灼烧减量显著偏高。
39.以上仅为本发明的较佳实施例而已,并不用以限制本发明,凡在本发明的精神和原则之内,所作的任何修改、等同替换、改进等,均应包含在本发明的保护范围之内。
再多了解一些
本文用于创业者技术爱好者查询,仅供学习研究,如用于商业用途,请联系技术所有人。