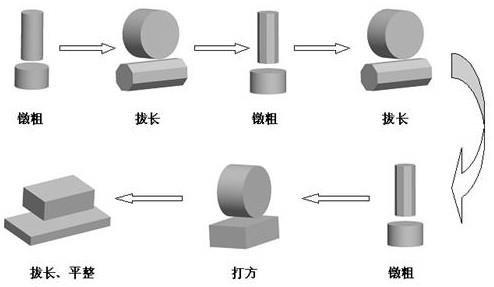
1.本发明属于金属材料技术领域,具体涉及一种高强韧、低淬火敏感性的厚大截面铝合金锻件及其制备方法。
2.
背景技术:
3.7000系铝合金具有超高强、高韧、耐蚀等较高的综合性能,是航空工业领域常用的金属材料之一,主要用于飞机机身主承力框梁、接头等重要主承力部位。随着飞机尺寸的增加以及对整体结构件需求的增加,铝合金半成品,如板材、锻件的尺寸规格也越来越大,其中对锻件厚度规格的需求已经达到300mm以上。对于超厚锻件,高力学性能已经不是单一的控制目标,力学性能沿厚度方向的均匀性以及不同批次之间性能的稳定性、耐蚀性能、疲劳性能等优良的综合性能才是决定锻件能否在航空领域安全、稳定使用的关键因素。7000系铝合金的合金成分主要包括主合金元素(zn、mg、cu等)、微合金元素(zr、mn等)以及杂质元素(fe、si等),其中zn、mg、cu元素的成分范围以及锻造工艺对锻件组织、性能及均匀性起到关键作用。
4.
技术实现要素:
5.研究发现,锻件性能是否能沿着厚度方向均匀分布取决于合金成分以及微观组织是否均匀分布,锻件在固溶淬火过程中,如若合金成分控制不精确、不合理,会发生固溶体“脱溶”现象,析出粗大第二相,导致锻件在厚度方向上表面和心部性能差异大,这种性能差异即淬火敏感性。7000系合金是高强铝合金系,具有高合金化特征,在热处理过程中不同厚度位置降温速度不同会导致铝合金锻件微观组织及性能不均匀,心部性能显著低于表面性能,尤其表现在强度、断裂韧度和腐蚀性能,厚度方向性能越不均匀即表明合金的淬火敏感性越高,而淬火敏感性高的合金不适合制备厚大截面的铝合金制品,不同厚度均匀性主要表现在强度的变异系数cv值。
6.为了改善现有技术中厚大截面铝合金锻件淬火敏感性较高,强度、断裂韧度和腐蚀性能较差的问题,本发明提供一种高强韧、低淬火敏感性的厚大截面铝合金锻件及其制备方法。通过精确控制合金成分范围,避免固溶体“脱溶”导致析出粗大第二相,进一步配合本发明的多级均匀化退火、强变形处理、多级高温固溶淬火、冷压缩和双级时效处理,获得的厚大截面铝合金锻件具有高强韧、低残余应力、抗腐蚀、低淬火敏感性、性能均匀、批次稳定的特点。
7.本发明中,所述厚大截面铝合金锻件的截面是指宽度和厚度所形成的平面。
8.本发明目的是通过如下技术方案实现的:一种厚大截面铝合金锻件,按重量百分比计,所述厚大截面铝合金锻件的合金成
分包括:zn 7.3%~7.9%、mg 1.5%~1.8%、cu 1.5%~1.8%、zr 0.09%~0.14%、fe≤0.07%、si≤0.07%,其余杂质总量《0.05%,余量为铝;所述厚大截面铝合金锻件的制备方法包括如下步骤:1)将铝锭、镁锭、锌锭、铝铜中间合金和铝锆中间合金加热熔融,得到铝合金熔体;2)将步骤1)的铝合金熔体进行精炼、扒渣、除气;3)将步骤2)的铝合金熔体进行铸造,制备得到超大规格铸锭;4)对步骤3)的超大规格铸锭采用多级处理工艺进行均匀化退火;5)对步骤4)的均匀化退火后的超大规格铸锭进行强变形处理;6)对步骤5)的强变形处理后的锻件采用多级处理工艺进行固溶淬火;7)沿步骤6)的固溶淬火后的锻件的厚度方向进行冷压缩,压缩量为2%~4%;8)对步骤7)的冷压缩后的锻件采用双级时效处理,制备得到所述厚大截面铝合金锻件。
9.根据本发明的实施方式,按重量百分比计,所述厚大截面铝合金锻件的合金成分包括:zn 7.3%、7.4%、7.5%、7.6%、7.7%、7.8%或7.9%。
10.根据本发明的实施方式,按重量百分比计,所述厚大截面铝合金锻件的合金成分包括:mg 1.5%、1.55%、1.6%、1.65%、1.7%、1.75%或1.8%。
11.根据本发明的实施方式,按重量百分比计,所述厚大截面铝合金锻件的合金成分包括:cu 1.5%、1.55%、1.6%、1.65%、1.7%、1.75%或1.8%。
12.根据本发明的实施方式,按重量百分比计,所述厚大截面铝合金锻件的合金成分包括:zr 0.09%、0.1%、0.11%、0.12%、0.13%或0.14%。
13.根据本发明的实施方式,所述厚大截面铝合金锻件的厚度t满足:305mm≥t≥200mm,例如为200mm、210mm、220mm、230mm、240mm、250mm、260mm、270mm、280mm、290mm、300mm或305mm。
14.根据本发明的实施方式,所述厚大截面铝合金锻件的宽度大于铝合金锻件的厚度,示例性地,所述厚大截面铝合金锻件的宽度≥200mm。
15.根据本发明的实施方式,所述厚大截面铝合金锻件满足如下条件中的至少一项:(1)抗拉强度达到540mpa以上;(2)屈服强度达到520mpa以上;(3)延伸率达到10%以上;(4)断裂韧度达到25mpa
·m1/2
以上;(5)剥落腐蚀性能达到ea级;(6)疲劳强度极限达到300mpa以上;(7)在310mpa下应力腐蚀20天不开裂;(8)锻件表面残余应力低于
±
100mpa。
16.根据本发明的实施方式,所述厚大截面铝合金锻件满足如下条件中的至少一项:(a)不同厚度位置的屈服强度变异系数达到3%以下;(b)不同厚度位置的抗拉强度变异系数达到3%以下;(c)不同厚度位置的断裂韧度大于等于25mpa
ּm1/2
且差值小于3mpa
ּm1/2
。
17.本发明中,不同厚度位置是指沿厚大截面铝合金锻件厚度方向,铝合金锻件的表
面到t/2部位(如表面、t/5部位、t/4部位、t/3部位、t/2部位),t是指铝合金锻件的厚度,t/2部位是指铝合金锻件的心部。
18.根据本发明的实施方式,所述厚大截面铝合金锻件满足不同批次间抗拉强度变异系数达到4%以下,批次数不小于10批。
19.根据本发明的实施方式,所述厚大截面铝合金锻件满足不同批次间屈服强度变异系数达到4%以下,批次数不小于10批。
20.本发明中,所述变异系数(cv, coefficient of variation)用于表征厚大截面铝合金锻件的不同厚度位置的强度(抗拉强度或屈服强度)的离散程度的大小,以及用于表征不同批次间厚大截面铝合金锻件的强度(抗拉强度或屈服强度)的离散程度的大小;计算公式为:标准偏差(sd, standard deviation)/平均值
×
100%。
21.本发明还提供上述厚大截面铝合金锻件的制备方法,所述方法包括如下步骤:1)将铝锭、镁锭、锌锭、铝铜中间合金和铝锆中间合金加热熔融,得到铝合金熔体;2)将步骤1)的铝合金熔体进行精炼、扒渣、除气;3)将步骤2)的铝合金熔体进行铸造,制备得到超大规格铸锭;4)对步骤3)的超大规格铸锭采用多级处理工艺进行均匀化退火;5)对步骤4)的均匀化退火后的超大规格铸锭进行强变形处理;6)对步骤5)的强变形处理后的锻件采用多级处理工艺进行固溶淬火;7)沿步骤6)的固溶淬火后的锻件的厚度方向进行冷压缩,压缩量为2%~4%;8)对步骤7)的冷压缩后的锻件采用双级时效处理,制备得到所述厚大截面铝合金锻件。
22.根据本发明的实施方式,步骤1)中,以铝锭、镁锭、锌锭、铝铜中间合金、铝锆中间合金为原料,且按照上述铝合金的组成成分进行配料。
23.根据本发明的实施方式,步骤1)中,所述加热熔融具体为:将熔炉升温至335℃~360℃,加入铝锭、锌锭、铝铜中间合金和铝锆中间合金,继续升温至760℃~780℃后保温熔炼,随后降温至680~690℃加入镁锭,继续保温熔炼。
24.根据本发明的实施方式,步骤1)中,所述加热熔融是在搅拌的条件下进行的,搅拌的时间为15min~30min,搅拌的速度为300r/min~550r/min。
25.根据本发明的实施方式,步骤1)中,为了减少合金中杂质含量,采用高纯度原料,例如,所述铝锭的纯度≥99.95%,所述镁锭的纯度≥99.95%,所述锌锭的纯度≥99.9%,所述铝铜中间合金中铜的含量≥50%,所述铝锆中间合金中锆的含量≥10%。
26.根据本发明的实施方式,步骤2)中,所述除气是通过在线除气装置和过滤装置的配合,对所述铝合金熔体进行除气过滤,使所述铝合金熔体中氢含量小于0.1μg/g,这样操作可降低铝合金熔体中氢对铝合金锻件抗应力腐蚀开裂敏感性、疲劳性能的影响。
27.根据本发明的实施方式,步骤3)中,所述铸造的温度为730℃~740℃,所述铸造的速度为50mm/min~55mm/min,所述铸造的水流量为31m3/h~35m3/h。
28.根据本发明的实施方式,步骤3)中,所述超大规格铸锭为直径1000mm以上的圆铸锭,或者厚度420mm以上的扁铸锭。
29.根据本发明的实施方式,步骤4)中,所述均匀化退火包括如下步骤:在350℃~430℃下保温10h~24h进行第一级均匀化退火处理,随后在440℃~450℃
下保温10h~24h进行第二级均匀化退火处理,最后在460℃~475℃下保温36h~48h进行第三级均匀化退火处理。
30.示例性地,在350℃~430℃(如350℃、360℃、370℃、380℃、390℃、400℃、420℃或430℃)下保温10h~24h进行第一级均匀化退火处理,随后在440℃~450℃(如440℃、441℃、442℃、443℃、444℃、445℃、446℃、447℃、448℃、449℃或450℃)下保温10h~24h进行第二级均匀化退火处理,最后在460℃~475℃(如460℃、461℃、462℃、463℃、464℃、465℃、466℃、467℃、468℃、469℃、470℃、471℃、472℃、473℃、474℃或475℃)下保温36h~48h进行第三级均匀化退火处理。
31.根据本发明的实施方式,步骤4)中,第一级均匀化退火处理的目的在于弥散析出纳米al3zr粒子;第二级均匀化退火处理的目的是使铸锭中大尺寸枝晶相溶解;第三级均匀化退火处理是通过高温均匀化使残余相进一步溶解,完全消除成分偏析。三级均匀化退火处理之间还能产生协同作用,即通过采用多级处理工艺进行均匀化退火能够均匀地析出纳米弥散相,且该纳米弥散相能够在后续的强变形处理工艺中抑制再结晶、钉扎晶界,显著提升锻件的疲劳性能、强度和断裂韧性,即为后续的强变形处理提供保障。
32.根据本发明的实施方式,步骤5)中,所述强变形处理包括如下步骤:(1)对均匀化退火处理后的铸锭进行铣削加工,将铣削加工后的铸锭加热至(430~440)
±
10℃并保温10h~20h;(2)在410℃~440℃温度下,将步骤(1)的铣削加工后的铸锭依次进行一次镦粗、一次倒棱拔长和二次镦粗;镦粗过程中模具的下压速度为10~15mm/s,倒棱拔长过程中模具的下压速度为10~15mm/s,镦粗方向与倒棱拔长方向垂直;且一次镦粗后的坯料的高度和二次镦粗后的坯料的高度相同,为h/2~h/3;一次倒棱拔长后的坯料的直径为(0.7~0.9)φ;h为铣削加工后的铸锭的高度,φ为铣削加工后的铸锭的直径;(3)将步骤(2)的坯料回炉加热保温,当坯料的温度为300℃以下时,坯料回炉加热保温的温度为(430~440)
±
10℃,时间为10~15h;当坯料的温度为300℃以上时,坯料回炉加热保温的温度为(430~440)
±
10℃,时间为2.5~10h;(4)将步骤(3)的坯料依次进行二次倒棱拔长、三次镦粗和打方;倒棱拔长过程中模具的下压速度为20~25mm/s,镦粗过程中模具的下压速度为20~25mm/s,镦粗方向与倒棱拔长方向垂直,打方方向与镦粗方向垂直且与倒棱拔长方向平行;且三次镦粗后的坯料的高度和二次镦粗后的坯料的高度相同;二次倒棱拔长后的坯料的直径与一次倒棱拔长后的坯料的直径相同;(5)将步骤(4)的坯料回炉加热保温,当坯料的温度为300℃以下时,坯料回炉加热保温的温度为(430~440)
±
10℃,时间为10~15h;当坯料的温度为300℃以上时,坯料回炉加热保温的温度为(430~440)
±
10℃,时间为2.5~10h;(6)将步骤(5)的坯料进行拔长、平整,并控制终锻温度≥350℃。
33.根据本发明的实施方式,步骤(1)中,加热过程中,铸锭的装炉量不超过额定装炉量的60%,相邻铸锭的间距≥200mm,铸锭放置于加热炉有效区间的中心区域。
34.根据本发明的实施方式,步骤(2)中,镦粗和倒棱拔长前对模具进行加热处理,加热的温度为450℃,加热的时间≥10h。
35.根据本发明的实施方式,步骤(2)中,单道次镦粗变形量为40%~70%。
36.根据本发明的实施方式,步骤(2)中,镦粗方向为沿着铸锭的高度方向,倒棱拔长方向为沿铸锭的径向方向。
37.根据本发明的实施方式,步骤(3)中,加热过程中,坯料的装炉量不超过额定装炉量的60%,相邻坯料的间距≥200mm,坯料放置于加热炉有效区间的中心区域。
38.根据本发明的实施方式,步骤(4)中,镦粗、倒棱拔长和打方前对模具进行加热处理,加热的温度为450℃,加热的时间≥10h。
39.根据本发明的实施方式,步骤(4)中,单道次镦粗变形量为40%~70%。
40.根据本发明的实施方式,步骤(4)中,倒棱拔长方向为沿坯料的径向方向,镦粗方向为沿着坯料的高度方向,打方方向为沿坯料的径向方向。
41.根据本发明的实施方式,步骤(5)中,加热过程中,坯料的装炉量不超过额定装炉量的60%,相邻坯料的间距≥200mm,坯料放置于加热炉有效区间的中心区域。
42.根据本发明的实施方式,步骤(6)中,所述拔长至t 25mm~t 50mm,t为铝合金锻件的厚度,单位mm,25~50mm作为余量用于铣削加工。
43.根据本发明的实施方式,所述强变形处理过程为:铸锭
→
镦粗
→
倒棱拔长
→
镦粗
→
回炉加热保温
→
倒棱拔长
→
镦粗
→
打方
→
回炉加热保温
→
拔长、平整,通过采用这样的强变形处理过程,既能增大变形程度,也能增加铝合金锻件的组织均匀性,使坯料变形充分、达到消除铸造组织缺陷以及改善坯料心部死区变形状况的目的。
44.根据本发明的实施方式,步骤6)中,具体包括如下步骤:在400℃~450℃下保温2h~4h进行第一级固溶处理,随后在455℃~465℃下保温2h~4h进行第二级固溶处理,随后在475℃~480℃下保温4h~8h进行第三级固溶处理,保温结束后出炉淬火,淬火转移时间≤15s。
45.根据本发明的实施方式,步骤6)中,第一级固溶处理可以使铝合金锻件中低熔点共晶相溶解,第二级固溶处理可以使铝合金锻件中大量的高熔点共晶相溶解,第三级固溶处理可以使铝合金锻件中高熔点及难溶相进一步溶解。
46.根据本发明的实施方式,步骤6)中,铝合金锻件的淬火水温为35℃~55℃。这是因为厚大截面铝合金锻件的热量更高,因此需要更低的水温,避免因为锻件入水后本身的热量高而导致水温快速升高,进而导致铝合金锻件表面降温速度变慢,心部降温速度更慢,造成铝合金锻件心部和表面性能不均匀。
47.根据本发明的实施方式,步骤6)中,沿铝合金锻件宽度和厚度所形成的平面优先入水,多件同时入水时,锻件间隔大于300mm,锻件在水中浸泡的时间满足(0.15t~0.2t)min,t是指铝合金锻件的厚度。
48.根据本发明的实施方式,步骤6)中,淬火炉水槽中设置循环水搅拌装置,并在淬火前开启循环水搅拌装置直到淬火结束,所述循环水搅拌装置的开启能够加强淬火炉水槽内水的流动性,提高热交换效率。
49.根据本发明的实施方式,步骤6)中,铝合金锻件淬火入水后应立即在淬火炉水槽中进行升降操作,且升降处理至少10min,升降的目的是为了防止淬火过程中产生的气泡附着于锻件表面,降低淬火效果。
50.示例性地,在400℃~450℃(如400℃、410℃、420℃、430℃、440℃或450℃)下保温2h~4h进行第一级固溶处理,随后在455℃~465℃(如455℃、456℃、457℃、458℃、459℃、460
℃、461℃、462℃、463℃、464℃或465℃)下保温2h~4h进行第二级固溶处理,随后在475℃~480℃(如475℃、476℃、477℃、478℃、479℃或480℃)下保温4h~8h进行第三级固溶处理。
51.根据本发明的实施方式,步骤7)中,在完成淬火处理后的4个小时内进行冷压缩处理。所述冷压缩处理能够消减锻件的残余应力。
52.根据本发明的实施方式,步骤7)中,所述冷压缩是指在室温下进行的压缩处理。
53.根据本发明的实施方式,步骤8)中,具体包括如下步骤:在115℃~125℃下保温2h~6h进行第一级时效处理,随后在155℃~160℃下保温8h~10h进行第二级时效处理,从第一级时效处理的温度到第二级时效处理的温度的升温速率为0.5~1℃/min。
54.示例性地,所述双级时效处理为120℃/4h 157℃/9~10h。
55.本发明中,铝合金锻件的低淬火敏感性通过厚度及厚度方向性能均匀性来表征,稳定性由不同批次锻件强度变异系数(屈服强度变异系数和抗拉强度变异系数)来表征,只有低淬火敏感性的合金成分和工艺才能做出性能均匀、批次稳定的厚大截面铝合金锻件;若沿厚度方向从表面至心部,铝合金锻件的强度显著降低,则说明其不满足低淬火敏感性。
56.本发明的有益效果:本发明提供了一种高强韧、低淬火敏感性的厚大截面铝合金锻件及其制备方法。沿本发明的铝合金锻件厚度方向具有高强高韧且性能均匀的特点,制备厚大截面铝合金锻件需要大规格铸锭,通过精确控制可以使铸锭各位置的成分波动大幅度降低,使铸锭成分更加均匀;另外精确控制合金范围还可以降低锻件批次间的性能差异。在此基础上,搭配本发明的多级均匀化退火、强变形处理、多级高温固溶淬火、冷压缩和双级时效处理,获得的厚大截面铝合金锻件具有高强韧、低残余应力、抗腐蚀、低淬火敏感性、性能均匀、批次稳定的特点。
57.附图说明
58.图1为本发明的厚大截面铝合金锻件的强变形处理工艺流程图。
59.具体实施方式
60.下文将结合具体实施例对本发明的技术方案做更进一步的详细说明。应当理解,下列实施例仅为示例性地说明和解释本发明,而不应被解释为对本发明保护范围的限制。凡基于本发明上述内容所实现的技术均涵盖在本发明旨在保护的范围内。
61.下述实施例中所使用的实验方法如无特殊说明,均为常规方法;下述实施例中所用的试剂、材料等,如无特殊说明,均可从商业途径得到。
62.下述实施例中采用纯度99.95%以上的工业级铝锭、纯度99.95%以上的工业级镁锭、纯度为99.9%以上的锌锭、铜的含量≥50%的铝铜中间合金,锆的含量≥10%的铝锆中间合金进行熔炼铸造。
63.实施例1(1)配料:按照重量百分比zn 7.3~7.9%、mg 1.5~1.8%、cu 1.5~1.8%、zr 0.09~
0.14%进行配料。
64.(2)熔炼:将熔炼升温至350℃,加入铝锭、锌锭、铝铜中间合金和铝锆中间合金,升温、并控制熔炼温度为770℃,待合金原料熔化后降温至680℃加入镁锭,继续保温熔炼;熔炼过程中合金原料开始熔化后开启电磁搅拌,保证熔炉内原材料快速熔化且温度及成分均匀;搅拌的速度为350 r/min,搅拌的时间为20min。
65.(3)精炼:向熔体中加入精炼剂进行精炼,精炼后静置10min。
66.(4)扒渣:精炼静置后,使用扒渣车扒去熔体表面浮渣。
67.(5)在线除气:扒渣后,测定合金成分为在按照重量百分比计:zn 7.6%、mg 1.5%、cu 1.6%、zr 0.14%、fe≤0.05%、si≤0.05%;向熔体中通入高纯氩气并搅拌熔体,利用氩气出去熔体中的杂质气体。
68.(6)过滤:使用60ppi泡沫陶瓷过滤板过滤除气后的熔体。
69.(7)铸造:采用半连续铸造法进行铸造,控制铸造温度为735℃,铸造速度为50mm/min,铸造水流量为32m3/h,得到规格ф1000
×
1800mm的铝合金圆铸锭。
70.(8)采用三级均匀化退火工艺,第一级均匀化退火是400℃下保温18h,目的在于弥散析出纳米al3zr粒子;第二级均匀化退火是440℃下保温16h,目的是使铸锭中大尺寸枝晶相溶解;第三级均匀化退火是470℃下保温48h,采用高温均匀化可以使残余相进一步溶解,完全消除成分偏析。
71.(9)采用铸锭规格ф1000
×
1800mm的圆铸锭,铣削加工后铸锭规格为ф775
×
1550mm,将模具在450℃下加热10h以上,将铣削加工后铸锭加热至440
±
10℃,保温时间10h;加热过程中,铸锭的装炉量不超过额定装炉量的60%,相邻铸锭的间距≥200mm,铸锭放置于加热炉有效区间的中心区域。
72.在430℃下,将铣削加工后的铸锭依次进行一次镦粗至高度h1=630mm
→
一次倒棱拔长至直径φ2=700mm
→
二次镦粗至高度h3=630mm;镦粗过程中模具的下压速度为15mm/s,倒棱拔长过程中模具的下压速度为15mm/s,镦粗方向为沿着铸锭的高度方向,倒棱拔长方向为沿铸锭的径向方向;将坯料回炉加热保温加热至430℃,保温时间10h;加热过程中,坯料的装炉量不超过额定装炉量的60%,相邻坯料的间距≥200mm,坯料放置于加热炉有效区间的中心区域。
73.在430℃下,将坯料二次倒棱拔长至直径φ4=700mm
→
三次镦粗至高度h5=630mm
→
打方至550mm
×
800mm
×
1400mm;镦粗过程中模具的下压速度为25mm/s,倒棱拔长过程中模具的下压速度为25mm/s,倒棱拔长方向为沿坯料的径向方向,镦粗方向为沿着坯料的高度方向,打方方向为沿坯料的径向方向;将坯料回炉加热保温加热至430℃,保温时间10h;加热过程中,坯料的装炉量不超过额定装炉量的60%,相邻坯料的间距≥200mm,坯料放置于加热炉有效区间的中心区域。
74.将坯料拔长至325mm
×
820mm
×
2350mm,并控制终锻温度≥350℃;采用机加工方式获得最终尺寸为300mm
×
800mm
×
2300mm的超厚规格铝合金锻件。
75.(10)固溶工艺采用多级高温的处理工艺:400℃/4h 455℃/4h 475℃/8h。
76.(11)淬火工艺:沿铝合金锻件宽度和厚度所形成的平面优先入水,水温保持在35~45℃,且铝合金锻件在水中浸泡的时间为50min;淬火炉水槽中设置循环水搅拌装置,并在淬火前开启循环水搅拌装置直到淬火结束,铝合金锻件淬火入水后应立即在淬火炉水槽中
进行升降操作,且升降处理至少10min;(12)冷压缩工艺:在完成淬火处理后的4个小时内进行,沿铝合金锻件的厚度方向,在室温下进行压缩,压缩量为4%;(13)时效工艺采用双级时效工艺:121℃/4h 157℃/9h,从第一级时效处理的温度到第二级时效处理的温度的升温速率为0.5℃/min。
77.实施例2其他操作同实施例1,区别在于如下步骤:(9)采用铸锭规格ф1000
×
1800mm的圆铸锭,铣削加工后铸锭规格为ф775
×
1550mm,将模具在450℃下加热10h以上,将铣削加工后铸锭加热至440
±
10℃,保温时间10h;加热过程中,铸锭的装炉量不超过额定装炉量的60%,相邻铸锭的间距≥200mm,铸锭放置于加热炉有效区间的中心区域。
78.在430℃下,将铣削加工后的铸锭依次进行一次镦粗至高度h1=600mm
→
一次倒棱拔长至直径φ2=720mm
→
二次镦粗至高度h3=600mm;镦粗过程中模具的下压速度为12mm/s,倒棱拔长过程中模具的下压速度为12mm/s,镦粗方向为沿着铸锭的高度方向,倒棱拔长方向为沿铸锭的径向方向;将坯料回炉加热保温加热至430℃,保温时间10h;加热过程中,坯料的装炉量不超过额定装炉量的60%,相邻坯料的间距≥200mm,坯料放置于加热炉有效区间的中心区域。
79.在430℃下,将坯料二次倒棱拔长至直径φ4=720mm
→
三次镦粗至高度h5=600mm
→
打方至500mm
×
800mm
×
1540mm;镦粗过程中模具的下压速度为20mm/s,倒棱拔长过程中模具的下压速度为20mm/s,倒棱拔长方向为沿坯料的径向方向,镦粗方向为沿着坯料的高度方向,打方方向为沿坯料的径向方向;将坯料回炉加热保温加热至430℃,保温时间10h;加热过程中,坯料的装炉量不超过额定装炉量的60%,相邻坯料的间距≥200mm,坯料放置于加热炉有效区间的中心区域。
80.将坯料拔长至275mm
×
820mm
×
2730mm,并控制终锻温度≥350℃;采用机加工方式获得最终尺寸为250mm
×
800mm
×
2650mm的超厚规格铝合金锻件。
81.对比例1对比例1为其他操作同实施例1,区别仅在于步骤(1)采用如下步骤进行替换:配料:按照重量百分比zn 7.0~8.0%、mg 1.2~2.0%、cu 1.2~2.0%、zr 0.08~0.15%进行配料。在线除气后获得的合金成分为:按照重量百分比计:zn 7.3%、mg 1.4%、cu 1.9%、zr 0.08%、fe≤0.03%、si≤0.02%。
82.对比例2对比例2为其他操作同实施例2,区别仅在于步骤(1)采用如下步骤进行替换:配料:按照重量百分比zn 7.0~8.0%、mg 1.2~2.0%、cu 1.2~2.0%、zr 0.08~0.15%进行配料。在线除气后获得的合金成分为:按照重量百分比计:zn 7.3%、mg 1.4%、cu 1.9%、zr 0.08%、fe≤0.04%、si≤0.03%。
83.对比例3对比例3为其他操作同实施例1,区别仅在于步骤(8)采用如下步骤进行替换:采用二级均匀化退火工艺,第一级均匀化退火是400℃下保温4h;第二级均匀化退火是460℃下保温24h。
84.对比例4
对比例4为其他操作同实施例1,区别仅在于步骤(9)采用如下步骤进行替换:采用铸锭规格ф1000
×
1800mm的圆铸锭,铣削加工后铸锭规格为ф775
×
1550mm,将模具在450℃下加热10h以上,将铣削加工后铸锭加热至440
±
10℃,保温时间10h;加热过程中,铸锭的装炉量不超过额定装炉量的60%,相邻铸锭的间距≥200mm,铸锭放置于加热炉有效区间的中心区域。
85.在430℃下,将铣削加工后的铸锭依次进行一次镦粗至高度h1=630mm
→
一次倒棱拔长至直径φ2=700mm
→
二次镦粗至高度h3=630mm
→
打方至550mm
×
800mm
×
1400mm;镦粗过程中模具的下压速度为15mm/s,倒棱拔长过程中模具的下压速度为15mm/s,倒棱拔长方向为沿坯料的径向方向,镦粗方向为沿着坯料的高度方向,打方方向为沿坯料的径向方向;将坯料回炉加热保温加热至430℃,保温时间10h;加热过程中,坯料的装炉量不超过额定装炉量的60%,相邻坯料的间距≥200mm,坯料放置于加热炉有效区间的中心区域。
86.将坯料拔长至325mm
×
820mm
×
2350mm,并控制终锻温度≥350℃;采用机加工方式获得最终尺寸为300mm
×
800mm
×
2300mm的超厚规格锻件。
87.对比例5对比例5为其他操作同实施例1,区别仅在于步骤(11)和步骤(12)。
88.步骤(11)采用如下步骤进行替换:沿铝合金锻件宽度和长度所形成的平面优先入水,水温保持在60~70℃,且铝合金锻件在水中浸泡的时间为25min;淬火炉水槽中设置循环水搅拌装置,并在淬火前开启循环水搅拌装置直到淬火结束,铝合金锻件淬火入水后应立即在淬火炉水槽中进行升降操作,且升降处理至少10min;步骤(12)采用如下步骤进行替换:在完成淬火处理后的4个小时内进行,沿铝合金锻件的厚度方向,在室温下进行压缩,压缩量为1%。
89.表1 实施例和对比例的铝合金锻件的性能结果
表1中强度取样方向为l向,断裂韧度取样方向为l-t。
90.表2 批次稳定性(强度变异系数cv/%)统计结果
对比例1与实施例1工艺相同,但对比例1的合金范围较实施例更宽。因此,锻件不同厚度位置合金成分分散度增加,导致锻件沿厚度方向强度变异系数增大,个别厚度位置抗应力腐蚀性能不合格,批次间变异系数也增大。
91.对比例2与实施例2工艺相同,但对比例2的合金范围较实施例更宽。因此,锻件不同厚度位置合金成分分散度增加,导致锻件沿厚度方向强度变异系数增大,个别厚度位置抗应力腐蚀性能不合格,批次间变异系数也增大。
92.对比例3较实施例1改变了均匀化处理工艺,将三级高温均匀化改为二级常规均匀化工艺,铸锭成分枝晶溶解效果降低,成分偏析消除效果减弱,间接导致了固溶过程中过饱和固溶体形成不够充分。因此,对比例3的锻件强度、断裂韧度、疲劳极限、性能均匀性及批次稳定性均显著降低。
93.对比例4较实施例1改变了强变形工艺,将三向大变形锻造工艺改为传统的两镦两拔,锻造变形量降低,导致锻件变形程度不足,心部与表面性能差异增大;另外,变形量不足将导致铸锭中冶金缺陷无法弥合,显著降低了锻件疲劳极限和断裂韧度。
94.对比例5较实施例1改变了淬火入水方式及冷压缩方式,锻件沿厚度方向入水,导致入水面中心部位淬火过程中形成的气泡不易消散,中心部存在水流动性差热交换效率低,导致淬火过程中锻件心部冷却速率慢,产生较大的残余应力,尤其优先入水的表面残余应力更大;冷压缩时沿着厚度方向压缩且压缩量不足,优先入水表面成为压缩过程的变形死区,不产生塑性变形,因此残余应力消除效果降低。
95.以上,对本发明的实施方式进行了说明。但是,本发明不限定于上述实施方式。凡在本发明的精神和原则之内,所做的任何修改、等同替换、改进等,均应包含在本发明的保护范围之内。
再多了解一些
本文用于创业者技术爱好者查询,仅供学习研究,如用于商业用途,请联系技术所有人。