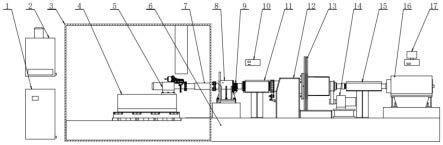
采用惯性台架进行制动器带驱动总成的实车模拟试验方法
1.(母案为:中国专利2022104249658)
技术领域
2.本发明属于汽车制动系统和驱动系统安全可靠性测试与验证技术领域,具体涉及一种采用惯性台架进行制动器带驱动总成的实车模拟试验方法。
背景技术:
3.随着汽车智能化、网联化的迅速发展,线控制动和线控驱动技术已成为车企及跨界企业的研究热点,一是汽车上以气压/液压为介质工作的相关部件,正逐渐被以电力为传递介质的部件所替代;二是汽车的驱动模式正在由发动机舱布置的燃油发动机或驱动电机驱动,逐渐往中央电驱桥驱动、轮边电驱动桥、轮边电驱动总成等方向发展;三是汽车的运动控制方式,正从单一的制动系统控制和单一的驱动系统控制逐渐发展到制动和驱动相集成的协同控制方向发展,如上坡辅助、制动能量回收等。其中线控制动和线控驱动部件的典型代表emb(电子机械制动系统)电动机械制动器、轮边电驱动总成及控制系统等。
4.现有技术中,对于该部件的测试试验台和测试方法均是在对应的试验台上单独进行制动或驱动试验,其在试验时需要进行多次安装,从而导致试验繁琐,且无法开展制动与驱动相结合的系统级试验。
技术实现要素:
5.本发明拟提出一种采用惯性台架进行制动器带驱动总成的实车模拟试验方法,对于制动和驱动集成的部件,能在同一个试验台架上进行制动和驱动试验。
6.为此,本发明所采用的技术方案为:一种采用惯性台架进行制动器带驱动总成的实车模拟试验方法,所述台架包括用于模拟实际环境下温湿度和风速的环境模拟箱,所述环境模拟箱罩设在试验台的左端,所述试验台位于环境模拟箱内设置有用于安装样件的安装台,所述试验台上设置有中间支撑座,且中间支撑座位于环境模拟箱外,所述中间支撑座的左侧设置有第一传动轴,所述第一传动轴伸入到环境模型箱内与样件输出轴连接,所述中间支撑座的右侧设置有第二传动轴,所述第一传动轴与第二传动轴之间设置有扭矩传感器,所述第二传动轴的右侧设置有飞轮轴,所述飞轮轴安装在试验台的飞轮架上,所述飞轮轴上套设有至少一个飞轮盘,所述飞轮轴的右侧设置有第三传动轴,所述第三传动轴的右端与固定在试验台右端的台架电机相连,所述第一传动轴、第二传动轴、飞轮轴和第三传动轴的组合成为主轴;
7.还包括控制系统、与样件的制动器连接的制动压力模拟器、与样件的再生制动系统和控制器电连接的电池模拟器、用于模拟样件内冷却介质温度的液体冷却循环系统、用于模拟陡坡启动的坡道阻力加载装置,所述制动压力模拟器通过输入的制动压力模拟踩下制动踏板时输入到样件内制动器的压力,所述电池模拟器通过输入到样件的控制器的电压模拟汽车的电池供电,电池模拟器还用于模拟样件回收再生制动工况下的制动能量,所述
制动压力模拟器、扭矩传感器、电池模拟器均与控制系统电连接,所述液体冷却循环系统与样件的冷却系统通过管道相连,所述坡道阻力加载装置包括坡道加载电机,所述坡道加载电机的输出端设置有降速增扭器和限扭组件,所述限扭组件与飞轮轴之间设置有传动组件;
8.将样件模拟实车状态安装在安装台上,同时样件的输出轴与第一传动轴连接,连接好电池模拟器、液体冷却循环系统、制动压力模拟器、控制系统,所述实车状态为通过调整飞轮轴上能与其一起转动的飞轮盘的数量,并通过控制系统和台架电机模拟转动惯量,使主轴上有与样件安装在实车上时启动相同的载荷;然后进行样件的加速性能试验,或陡坡起步模拟试验,或制动性能试验,或道路耐久试验,或再生制动模拟试验,在试验过程中需要使用的公式包括模拟实车状态时对应主轴的转动惯量的计算公式、主轴转速与车速换算公式、模拟坡道控制时需施加在主轴上的扭矩计算公式;
9.模拟实车状态时对应主轴的转动惯量的计算公式如下:
10.i=gmr211.式中:i为转动惯量计算值,单位为kg
·
m2;gm为将汽车最大设计总质量按制动力分配比设计值分配给样件中制动器所对应车轮承受的那部分质量,单位为kg;r为车轮滚动半径,单位为m;
12.主轴转速与车速换算公式如下:
13.n=2.65v/r
14.式中:n为主轴转速,单位是r/min;v为模拟的实车车速,单位为km/h;
15.模拟坡道控制时需施加在主轴上的扭矩计算公式如下:
16.ts=gm×
sin(arctan(i/100))
×r17.式中:ts为模拟坡道控制需施加的扭矩,单位为r/min;i为坡道坡度,单位为%。
18.进一步优选,所述加速性能试验包括以下步骤,
19.s1:让台架电机处于可自由旋转状态,或保持转动惯量模拟保持运行状态;
20.s2:保持样件中制动器处于释放状态;
21.s3:模拟电子油门最大开度,通过控制系统控制样件的控制器输出,使样件的驱动电机加速启动,记录从给定控制输入信号开始,到样件的驱动电机启动至主轴转动达到模拟实车车速100km/h的时间,并绘制时间为横坐标,车速为纵坐标的加速性能曲线图。
22.进一步优选,所述陡坡起步模拟试验包括以下步骤,
23.s1:让台架电机处于可自由旋转状态;
24.s2:通过控制系统操控样件的控制器,模拟踩下制动踏板或驻车工况,使主轴处于锁止状态,当样件的控制器处于驻车工况时,先通过控制系统操控样件控制器,模拟先踩下制动踏板,再解除驻车工况;
25.s3:根据需要模拟的坡道,按照公式计算出相应的扭矩值,并通过坡道阻力加载装置沿倒车反向施加在主轴上;
26.s4:通过控制系统模拟松开制动踏板,停顿规定时间间隔后,迅速踩下油门踏板至设定开度,使样件的驱动电机启动直至主轴转速大于10r/min,然后解除坡道阻力加载装置施加的扭矩,记录松开制动踏板信号、踩下油门踏板控制信号、主轴转速和坡道阻力加载装置上施加扭矩等变量随时间变化的关系曲线,从而能得到陡坡起步模拟试验曲线。
27.进一步优选,当进行制动性能试验时,样件模拟实车状态安装,样件的驱动电机和控制器不参与工作或处于非使能状态,或将样件的制动器部分单独进行试验,试验步骤按照标准要求进行。
28.进一步优选,所述道路耐久试验包括以下步骤,
29.s1:试验循环工况按照标准根据样件所配车辆类型进行选取,或根据使用对象要求制定的多级道路谱;
30.s2:在模拟实车状态对应的转动惯量要求下,通过控制系统控制台架电机模拟行驶阻力,通过改变电子油门的开度来控制样件电机,从而模拟汽车的加速、保持或滑行,通过改变制动踏板开度来控制样件的制动器制动,从而模拟汽车的减速,当减速过程中有再生制动控制参与时,按实车控制器的控制策略进行,使主轴转速对应的车速与试验循环工况逐秒数据对应,并连续运行至规定循环结束;
31.s3:循环结束后,按要求检测样件各部件的异常情况,以及耐久后的各项性能和功能衰减。
32.进一步优选,所述再生制动模拟试验包括以下步骤,
33.s1:开启制动能量回收功能;
34.s2:按照规定选择制动初速度,并在规定的制动压力范围内取不少于五点进行试验,且各个试验垫之间的间隔相等,每个制动初速度对应的每种制动压力各进行一次制动试验,并记录每次制动试验过程中实测的电池模拟器电压和回馈电流,以及每次制动试验的制动初速度、制动初始温度、制动最高温度、制动时间、制动压力和输出制动力矩,通过回收的制动能量计算公式计算回收的制动能量,
[0035][0036]
式中:e1为单次制动过程中,由再生制动系统回收,最终回馈至电池模拟器的能量,单位为wh;i为单次制动过程中,回馈至电池模拟器的电流,单位为a;u为单次制动过程中,电池模拟器两端的电压,单位为v;t1为有效制动时间段的开始时间,单位为s;t2为有效制动时间段的结束时间,单位为s。
[0037]
进一步优选,每个飞轮盘均能通过对应地可拆卸固定结构固定在飞轮架上,所述可拆卸固定结构包括两个位于对应飞轮盘外侧且固设在飞轮架上的固定支架,所述飞轮轴上设置有能与对应飞轮盘卡紧的凸起;当飞轮盘与飞轮轴一起转动时,飞轮盘套设在凸起上并通过螺栓与飞轮轴连接,且固定支架与飞轮盘之间不连接,当飞轮盘不与飞轮轴一起转动时,飞轮盘套设飞轮轴除凸起外的地方同时断开与飞轮轴之间的螺栓连接,且固定支架与飞轮盘之间通过螺栓连接。
[0038]
本发明的有益效果:本试验方法适用于商用汽车制动器总成(包括气压盘式制动器总成、鼓式制动器总成、电动机械制动器)、轮边电驱动总成及控制器等的产品开发、研究、质量检测机质量改进等;对于制动和驱动集成的部件,能在同一个试验台架上进行制动和驱动试验,只需一次安装完成多项试验,减少试验的繁琐,还可进行制动与驱动相结合的系统级试验。
附图说明
[0039]
图1为本发明中台架的示意图。
[0040]
图2为本发明中加速性能曲线的示意图。
[0041]
图3为本发明中陡坡起步模拟试验曲线的示意图。
[0042]
图4为本发明进行道路耐久试验时所依据的中国城市客车行驶工况曲线图。
[0043]
图5为本发明进行道路耐久试验时所依据的中国普通客车行驶工况曲线图。
[0044]
图6为本发明进行道路耐久试验时所依据的中国货车(gvw≤5500kg)行驶工况曲线图。
[0045]
图7为本发明进行道路耐久试验时所依据的中国货车(gvw>5500kg)行驶工况曲线图。
[0046]
图8为本发明进行道路耐久试验时所依据的中国自卸汽车行驶工况曲线图。
[0047]
图9为本发明进行道路耐久试验时所依据的中国半挂牵引车列车行驶工况曲线图。
具体实施方式
[0048]
下面通过实施例并结合附图,对本发明作进一步说明:
[0049]
如图1所示,一种采用惯性台架进行制动器带驱动总成的实车模拟试验方法,其中台架主要由试验台6、环境模拟箱3、安装台4、第一传动轴7、中间支撑座8、扭矩传感器9、第二传动轴11、飞轮架12、飞轮轴、飞轮盘13、第三传动轴15和台架电机16组成,其中环境模拟箱3用于模拟实际环境下温湿度和风速,且环境模拟箱3罩设在试验台6的左端,在试验台6位于环境模拟箱3内设置有用于安装样件5的安装台4,在试验台6上设置有中间支撑座8,且中间支撑座8位于环境模拟箱3外。在中间支撑座8的左侧设置有第一传动轴7,且第一传动轴7伸入到环境模型箱3内与样件5输出轴连接,在中间支撑座8的右侧设置有第二传动轴11,且第一传动轴7与第二传动轴11之间设置有扭矩传感器9。在第二传动轴11的右侧设置有飞轮轴,飞轮轴安装在试验台的飞轮架12上,在飞轮轴上套设有至少一个飞轮盘13,在飞轮轴的右侧设置有第三传动轴15,且第三传动轴15的右端与固定在试验台6右端的台架电机17相连。为方便第二传动轴11与第三传动轴15的支撑,其中第一传动轴7、第二传动轴11、飞轮轴和第三传动轴15的组合成为主轴。为保证整个主轴的防护,在第二传动轴11与第三传动轴15外均套设有固定在试验台6上的传动轴防护罩,当整个试验台6均有防护罩时,传动轴防滑罩可以不设置。安装台4可根据实际试验进行更换。
[0050]
还设置有控制系统17、与样件5的制动器连接的制动压力模拟器10、与样件5的再生制动系统和控制器电连接的电池模拟器1,制动压力模拟器10通过输入的制动压力模拟踩下制动踏板时输入到样件内制动器的压力,电池模拟器1通过输入到样件的控制器的电压模拟汽车的电池供电,电池模拟器1还可用于模拟样件回收再生制动工况下的制动能量,制动压力模拟器10、扭矩传感器9、电池模拟器1均与控制系统17电连接。电池模拟器1的具体结构是一个带回馈功能的程控电源,然后在电池的输出电路上设置有电流表,电池的两端设置有电压表,可通过改变其输出电压的大小模拟电子油门的开度。
[0051]
制动压力模拟器10可以根据具体情况选择为对应的制动电压模拟装置、制动液压模拟装置或制动气压模拟装置。对于气压制动系统的商用车,车辆上踩下制动踏板时,就会
控制制动阀输出一定压力的制动气压到制动器上,制动气压模拟装置就是一个能调节输出气压的气压调节装置,通过气压管路与样件制动器连接。对于液压系统的车辆,踩下踏板就会输出一定压力的液压到制动器上,制动液压模拟装置就是一个能调节输出液压的液压调节装置,通过液压管路与样件制动器连接。对于emb电动机械制动器,踩下踏板时,就会根据踏板踩下的开度,输出相应的电压到制动器上,制动电压模拟装置就是一个能改变输出电压的电源,通过导线与样件控制器电连接。
[0052]
还设置有用于模拟样件内冷却介质温度的液体冷却循环系统2,液体冷却循环系统2与样件5的冷却系统通过管道相连。液体冷却循环系统主要由过滤器、水泵、冷凝器、加热装置组成。
[0053]
还设置用于模拟陡坡启动的坡道阻力加载装置14,坡道阻力加载装置14包括坡道加载电机,坡道加载电机的输出端设置有降速增扭器和限扭组件,限扭组件与飞轮轴之间设置有传动组件,其中限扭组件可采用离合器,传动组件可以是带传动、齿轮传动等,降速增扭器可以是与传动组件一起设置的传动比小于1的传动组件。
[0054]
每个飞轮盘13均能通过对应地可拆卸固定结构固定在飞轮架12上,可拆卸固定结构包括两个位于对应飞轮盘13外侧且固设在飞轮架12上的固定支架,飞轮轴上设置有能与对应飞轮盘卡紧的凸起;当飞轮盘13与飞轮轴一起转动时,飞轮盘13套设在凸起上并通过螺栓(还可以是销连接)与飞轮轴连接,且固定支架与飞轮盘13之间不连接,当飞轮盘13不与飞轮轴一起转动时,飞轮盘13套设飞轮轴除凸起外的地方并断开与飞轮轴之间的连接,且固定支架与飞轮盘13之间通过螺栓连接。可拆卸固定结构也可设置为吊装结构,其能将不随飞轮轴一起转动的飞轮盘吊装起来。
[0055]
将样件5模拟实车状态安装在安装台4上,同时样件5的输出轴与第一传动轴7连接,同时连接好电池模拟器1、液体冷却循环系统2、制动压力模拟器10、控制系统17,其中实车状态为通过调整飞轮轴上能与其一起转动的飞轮盘的数量,并通过控制系统17和台架电机16模拟转动惯量,使主轴上有与样件安装在实车上时启动相同的载荷,样件外表面的环境温湿度、风速,以及样件内蓄电池电压、电机及控制器电压、流经样件内部的冷却循环介质温度等按实际要求加以控制。本台架未考虑样件所受的车辆垂向方向载荷,如有需要可通过加装液压伺服系统加载实现。其中样件5选用集商用汽车制动器(可以为气压盘式制动器总成、鼓式制动器总成或电动机械制动器emb)、轮边电驱动总成及控制器一体。样件的安装形式可根据不同试验项目选择带轮毂的常规结构(包括带轮胎的)、独立轮边结构、带空气悬架结构或整桥(轴)结构等。
[0056]
安装好样件的试验台架能进行样件的加速性能试验、制动性能试验、热裂纹试验、高负荷试验、制动冲击试验、温升试验、陡坡起步模拟试验、道路模拟耐久试验、再生制动模拟试验等用于产品开发、研究、质量检测及质量改进等台架试验,当样件不配备上坡辅助功能时,不进行陡坡起步模拟试验。在上述试验中,通过控制飞轮盘及台架电机来精确模拟整车载荷;通过台架电机或轮边电驱动总成电机(即样件的驱动电机)控制主轴转速模拟车速;通过坡道阻力加载装置和台架电机模拟道路坡道负荷或行驶阻力;通过制动压力模拟器模拟制动踏板输入;通过电池模拟器来精准控制轮边电驱动总成电机及控制器输入电压和回收再生制动工况下的制动能量;通过液体冷却循环系统来控制轮边电驱动总成及控制器内部介质温度;通过环境试验仓来模拟各种高温、低温、湿度等极端试验环境。
[0057]
在进行试验时需要使用到的公式包括模拟实车状态时对应主轴的转动惯量的计算公式、主轴转速与车速换算公式、模拟坡道控制时需施加在主轴上的扭矩(在本试验台架中,陡坡起步模拟试验时通过坡道阻力加载装置模拟该扭矩,道路耐久试验时,通过台架电机16模拟道路坡道负荷或行驶阻力)计算公式。
[0058]
模拟实车状态时对应主轴的转动惯量的计算公式如下:
[0059]
i=gmr2[0060]
式中:i为转动惯量计算值,单位为kg
·
m2;gm为将汽车最大设计总质量按制动力分配比设计值分配给样件中制动器所对应车轮承受的那部分质量,单位为kg;r为车轮滚动半径,单位为m;
[0061]
主轴转速与车速换算公式如下:
[0062]
n=2.65v/r
[0063]
式中:n为主轴转速,单位是r/min;v为模拟的实车车速,单位为km/h;
[0064]
模拟坡道控制时需施加在主轴上的扭矩计算公式如下:
[0065]
ts=gm×
sin(arctan(i/100))
×r[0066]
式中:ts为模拟坡道控制需施加的扭矩,单位为r/min;i为坡道坡度,单位为%。
[0067]
上述中加速性能试验具体包括以下步骤,
[0068]
第一步:让台架电机处于可自由旋转状态,或保持转动惯量模拟保持运行状态;
[0069]
第二步:保持样件中制动器处于释放状态;
[0070]
第三步:模拟电子油门最大开度,(通过电池模拟器向样件的控制器输入电子油门最大开度时的电压),通过控制系统控制样件的控制器输出,使样件的驱动电机加速启动,记录从给定控制输入信号开始,到样件的驱动电机启动至主轴转动达到模拟实车车速100km/h的时间,即百公里加速时间,并绘制时间为横坐标,车速为纵坐标的加速性能曲线图,如附图2所示,图中t1为加速反应的时间,t2为从0km/h到vkm/h的加速时间,当v等于100km/h时,定义为百公里加速时间。
[0071]
上述中陡坡起步模拟试验具体包括以下步骤,
[0072]
第一步:让台架电机处于可自由旋转状态;
[0073]
第二步:通过控制系统操控样件的控制器,模拟踩下制动踏板或驻车工况,使主轴处于锁止状态,当样件的控制器处于驻车工况时,先通过控制系统操控样件控制器,模拟先踩下制动踏板,再解除驻车工况;
[0074]
第三步:根据需要模拟的坡道,按照如下公式计算出相应的扭矩值,并通过坡道阻力加载装置沿倒车反向施加在主轴上;
[0075]
第四步:通过控制系统模拟松开制动踏板,停顿规定时间间隔后,迅速踩下油门踏板至设定开度,使样件的驱动电机启动直至主轴转速大于10r/min,然后解除坡道阻力加载装置施加的扭矩,记录松开制动踏板信号、踩下油门踏板控制信号、主轴转速和坡道阻力加载装置上施加扭矩等变量随时间变化的关系曲线,从而能得到陡坡起步模拟试验曲线,如图3所示,图中a表示制动保持阶段,陡坡模拟准备阶段,b表示制动释放且未踩下油门踏板阶段,上坡辅助功能检查阶段,c表示踩下油门踏板,模拟汽车正常起步阶段,d表示主轴转速达到10r/min以上,陡坡起步模拟结束阶段。
[0076]
通过观察记录曲线上,从模拟松开制动踏板至踩下油门踏板期间,以及油门踏板
在设定开度下,控制试验台主轴转速直至达到10r/min的起步过程中,主轴转速是否出现负数,可观察是否出现后退溜车现象,当出现负数时,即有后退溜车现象。
[0077]
当进行制动性能试验时,样件模拟实车状态安装,样件的驱动电机和控制器不参与工作或处于非使能状态,或将样件的制动器部分单独进行试验,由于该部分试验内容属于常规制动性能实现,具体试验方法可参考qc/t 239《商用车辆行车制动器技术要求及台架试验方法》、gb/t 34422《汽车用制动盘》、gb/t 37336《汽车制动鼓》等标准要求进行,此处不再赘述。如果样件制动器为电动机械制动器,仅需将标准中规定的制动气压(液压)输入,更换为制动电压输入即可。
[0078]
上述中道路耐久试验具体包括以下步骤,
[0079]
第一步:试验循环工况按照标准根据样件所配车辆类型进行选取,或根据使用对象要求制定的多级道路谱。具体循环工况可参考gb/t 38146.2-2019《中国汽车行驶工况第2部分:重型商用车辆》根据样件所配车辆类型进行选取,主要包括中国城市客车行驶工况、中国普通客车行驶工况、中国货车(gvw(车辆总重量)≤5500kg)行驶工况、中国货车(gvw>5500kg)行驶工况、中国自卸汽车行驶工况和中国半挂牵引车列车行驶工况。
[0080]
其中中国城市客车行驶工况(chtc-b)包括低速(1部)、高速(2部)2个速度区间,工况市场共计1310s,工况逐秒数据见gb/t 38146.2-2019附录a中的表a.1,工况曲线如图4所示。中国普通客车行驶工况(chtc-c)包括市区(1部)、城郊(2部)和高速(3部)3个速度区间,工况时长共计1800s,工况逐秒数据见gb/t 38146.2-2019附录a中的表a.2,工况曲线如图5所示。中国货车(gvw≤5500kg)行驶工况(chtc-lt)包括市区(1部)、城郊(2部)和高速(3部)3个速度区间,工况时长共计1652s,工况逐秒数据见gb/t 38146.2-2019附录a中的表a.3,工况曲线如图6所示。中国货车(gvw>5500kg)行驶工况(chtc-ht)包括市区(1部)、城郊(2部)和高速(3部)3个速度区间,工况时长共计1800s,工况逐秒数据见gb/t 38146.2-2019附录a中的表a.4,工况曲线如图7所示。中国自卸汽车行驶工况(chtc-d)包括低速(1部)、高速(2部)2个速度区间,工况时长共计1300s,工况逐秒数据见gb/t 38146.2-2019附录a中的表a.5,工况曲线如图8所示。中国半挂牵引车列车行驶工况(chtc-tt)包括低速(1部)、高速(2部)2个速度区间,工况时长共计1800s,工况逐秒数据见gb/t 38146.2-2019附录a中的表a.6,工况曲线如图9所示。
[0081]
第二步:在模拟实车状态对应的转动惯量要求下,通过控制系统控制台架电机模拟行驶阻力,通过电池模拟器输入到样件控制器的电压模拟电子油门的开度控制样件电机,从而实现汽车的加速、保持或滑行,通过制动压力模拟器输入到样件制动器内的压力模拟制动踏板开度控制样件的制动器制动,从而实现汽车的减速。当减速过程中有再生制动控制参与时,按实车控制器的控制策略进行,使主轴转速对应的车速与试验循环工况逐秒数据对应,并连续运行至规定循环结束。
[0082]
第二步:循环结束后,按要求检测样件各部件的磨损、开裂、变形、失效等异常情况,以及耐久后的加速、制动、能量回收率等各项性能和功能衰减。还可更具需要,测算样件在某循环工况下的百公里电量消耗。
[0083]
上述中的再生制动模拟试验具体包括以下步骤,
[0084]
第一步:开启制动能量回收功能,且保持电池模拟器处于能量回馈模式。
[0085]
第二步:按照规定选择制动初速度(n1类车辆为50km/h、80km/h,其它类车辆为
30km/h、60km/h),并在规定的制动压力范围内取不少于五点进行试验,且各个试验垫之间的间隔相等,每个制动初速度对应的每种制动压力各进行一次制动试验,并记录每次制动试验过程中实测的电池模拟器电压和回馈电流,以及每次制动试验的制动初速度、制动初始温度、制动最高温度、制动时间、制动压力和输出制动力矩,通过回收的制动能量计算公式计算回收的制动能量,
[0086][0087]
式中:e1为单次制动过程中,由再生制动系统回收,最终回馈至电池模拟器的能量,单位为wh;i为单次制动过程中,回馈至电池模拟器的电流,单位为a;u为单次制动过程中,电池模拟器两端的电压,单位为v;t1为有效制动时间段的开始时间,单位为s;t2为有效制动时间段的结束时间,单位为s。
[0088]
根据实际需要,也可采用工况法进行制动能量回收效率试验。试验循环工况可参考道路耐久试验中循环工况进行选取,试验方法可参考qc/t 1089-2017标准b.4条。
再多了解一些
本文用于创业者技术爱好者查询,仅供学习研究,如用于商业用途,请联系技术所有人。