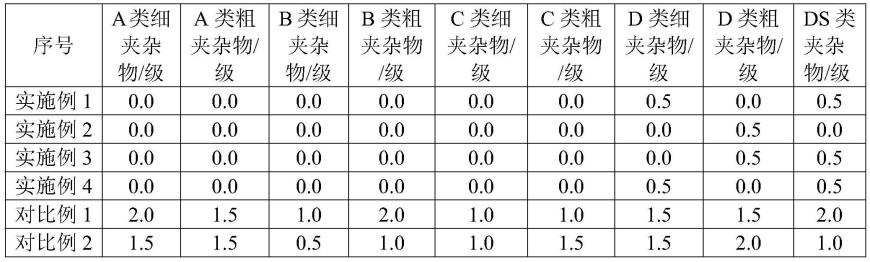
0.15%,mo:≤0.1%,cu:≤0.15%,b:≤0.005%,ti:≤0.003%,ce:≤0.006%,o:≤0.0012%,n:0.008-0.016%,余量为铁和不可避免的杂质。
11.上述高碳铬风电轴承钢,进一步地,所述轴承钢的碳当量ceq=[c mn/6 (cr mo v)/5 (ni cu)/15]*100%=1.40%-1.46%,合金化提高强度,改善浇铸性能、减少缩松、缩孔等缺陷和铸造应力,si/c为0.45-0.53,降低断面敏感性,mn-si为0.26-0.32%,si与mn的差值控制提高轴承钢强度,轴承钢的抗拉强度为1852-1924mpa,冲击功akv为24-28j,硬度为66-71hrc。
[0012]
上述高碳铬风电轴承钢的成分设计依据为:
[0013]
(1)c含量的确定:随着c含量的增加,屈服点和抗拉强度升高,提高淬透性、硬度、耐磨性,但c含量过高容易产生大块碳化物液析,塑性、韧性下降,增加铸坯中心偏析,淬火后会得到粗大的马氏体组织,导致脆性增大,本发明c含量的范围确定为0.98-1.02%;
[0014]
(2)si含量的确定:si是炼钢过程中的脱氧元素,在钢中能溶入铁素体固溶强化,减少碳在共晶体及奥氏体中的溶解度,提高稳定系平衡温度和回火稳定性,增加碳化物颗粒数据、减小碳化物尺寸和间距而提高屈服点和抗拉强度,但si含量过高使冷加工性能变坏,本发明si含量的范围确定为0.42-0.61%;
[0015]
(3)mn含量的确定:mn是炼钢过程中的脱氧元素,同时在钢中能溶入铁素体强化基体,在轧后冷却时能增加凝固过程中奥氏体和珠光体的枝晶含量,同时降低共晶转变温度、促使珠光体片细化,片间距减小,提高钢的淬透性,但mn含量过高容易造成mn在晶界处的偏析影响内部质量,增加材料的回火脆性,本发明mn含量的范围确定为0.75-0.84%;
[0016]
(4)cr含量的确定:cr可降低钢种碳的活度、提高钢中碳扩散的激活能,优先凝聚于碳化物使碳化物硬度增高、增加组织中奥氏体枝晶数量,能提高钢的淬透性、减轻钢的脱碳倾向,与锰共用效果更好,但cr含量过高会增加白口倾向,增大形成缩松和缩孔的倾向,成本和生产难度增加,本发明cr含量的范围确定为1.32-1.55%;
[0017]
(5)ni、mo含量的确定:在钢中强化铁素体并细化珠光体,ni能提高钢的强度,而又保持良好的塑性和韧性,对钢的淬透性也有一定的提高作用,但ni过高不能提高铁素体的蠕变抗力,相反会使珠光体体钢热脆性增大,本发明ni含量的范围确定为0.1-0.15%;mo能提高钢的脆透性和热强性,提高碳化物的稳定性,但mo过高会恶化钢的抗氧化性,本发明mo确定为≤0.1%。
[0018]
(6)s、p含量的确定:s会使钢产生热脆性,降低钢的塑韧性;p熔于铁素体易形成偏析、夹杂等缺陷,增加回火脆性;本发明s含量的范围确定为≤0.015%,p含量的范围确定为≤0.015%;
[0019]
(7)b含量的确定:b能抑制铁素体析出提高淬透性但与o、n结合易引起淬透性不稳定,b含量的范围确定为≤0.005%;
[0020]
(8)n、ti含量的确定:ti与n结合可细化晶粒,但ti过高,tin、ti(cn)在钢中作为硬脆的夹杂物易引起应力集中、劣化钢材的疲劳寿命,ti含量的的范围确定为≤0.003%;
[0021]
(9)ce含量的确定:通过ce与s的结合降低mns析出时的凝固分率,形成弥散分布尺寸为2-5μm球形s-o-ce类夹杂,减少9-11μm的mns夹杂物,通过夹杂物的球化、细化和弥散分布减少裂纹萌发,提高强韧性且不影响组织连续性,但ce过多导致mns抗变形能力增大,本发明ce含量的范围确定为≤0.006%。
[0022]
一种高碳铬风电轴承钢的生产工艺,其工艺包括如下步骤:
[0023]
s1、电炉冶炼:将炼钢原料经铁水预处理kr脱硫、以氧气顶吹和双渣法电炉冶炼得到钢水,铁水预处理kr脱硫的脱硫剂按每吨钢水采用5-7kg石灰和1-3kg萤石,碱度r为2.0-5.0,使炉渣具有良好的流动性,控制s≤0.005%,控制出钢终点碳含量为0.42~0.48%,终点磷含量≤0.008%,出钢温度控制在1625℃~1675℃;
[0024]
挡渣出钢且出钢过程进行脱氧合金化,按90-110t/炉钢水出钢1/3-1/2后加入3.5-3.8kg/t的铝锭预脱氧,出钢3/5-2/3后加入5-7kg/t的硅锰合金(femn64si16)、0.5-1.0kg/t的硅铁合金(fesi75a12.0-c)和8-10kg/t微碳铬铁合金(fecr69c0.1)进行合金化,出钢3/4后一次性加入4.2-5.8kg/t的石灰和2-3kg/t的铝酸钙造渣料,防止出钢过程al2o
3-sio
2-mno夹杂物生成,形成精炼初渣;
[0025]
s2、lf精炼:将步骤s1的钢水进lf站之后采用预熔精炼渣与sic按质量比2:1联合脱氧,少量多次加在渣面上,总加入量为0.5-1.0kg/t钢水,白渣时间≥25min,预熔精炼渣的组成成分按质量百分数计包括cao:43-55%,al2o3:23-37%,mgo:6-15%,sio2:9-12%,caf2:3-12%、na2o:3-9%,促进夹杂物的吸收,钢中mg含量抑制xcao
·
yal2o3的生成,避免这种硬脆夹杂影响轴承钢的疲劳寿命,提高渣碱度并增加炉渣流动性和吸附性,以减少大颗粒d类夹杂物,生成以细小镁铝尖晶石、ca-mg-al-o复合夹杂共存的d类夹杂,caf2能减轻侵蚀钢包包衬和污染、na2o能提高脱硫效果,以提高轴承钢质量;
[0026]
精炼前期氩气流量为200-300nl/min,适当调大氩气搅拌促进脱氧及合金化;精炼中期使用低铝硅铁合金(fesi75a10.5-b)、高硅硅锰(femn64si27)、低碳锰铁(femn88c0.4)、硅铁(fesi45)、钼铁(femo55-b),氩气流量为130-160nl/min,保持氩气中等氩气强度进行成分微调;
[0027]
精炼后期钢水的活度氧≤2.8*10-6
,按每炉钢水加入80-90kg稀土铈铁合金(cefe-20),氩气流量60-110nl/min,期避免钢水翻滚氧化;通过ce与s的结合降低mns析出时的凝固分率,将大尺寸(fe、mn)s、(fe、mn)o夹杂物变为小尺寸同时减少大尺寸长条状mns夹杂物数量,避免凝固过程中发生偏析而富集,ce-o和ce-s的混合相形成小尺寸夹杂并碎化弥散起到变形作用,同时稀土铝酸盐可提高及杂物塑性,随后以2-4m/s的喂丝速度喂入2.5-3.5m/t钛铁合金包芯线(ti:29.5%),降低烧损提高ti-fe合金回收率,增加共晶团数量提高抗拉强度,严禁进行钙处理,避免cas、cao夹杂物造成水口结瘤和可浇性劣化,喂丝期间调整氩气流量,确保钢水不裸露,使钢水中成分达标出站,出站温度为1600-1620℃;
[0028]
s3、vd真空:将步骤s2的钢水进vd站进行vd真空脱气处理,极限真空度≤68pa,保压时间不小于20min,保证造渣及脱氧去除夹杂物,软吹氩时间≥35min,氩气流量为10-30nl/min,使非金属夹杂物充分上浮,钢中氢脱至1.4*10-6
以下,破空后以1-2m/s的喂丝速度喂入1.2-1.5m/t硼铁合金包芯线(b:15.5%),降低烧损提高b-fe合金回收率,以便使b吸附在晶界上填充缺陷、增加奥氏体稳定性而提高淬透性,严禁裸露钢水和大氩气量搅拌降温,利用高碱度精炼渣进行渣-钢精炼,配合真空处理和适宜的底吹搅拌进行精炼成分控制,利于提高钢的纯净性和基体连续性,得到符合成分要求的精炼钢水,提高钢水可浇性,出钢温度为1520-1620℃;
[0029]
s4、连铸:将步骤s3的钢水采用八机八流连铸机连铸时钢包到中间包用带氩封长水口,中间包到结晶器用浸入式水口全保护浇铸,中间包用碱度>2.5的覆盖剂防止钢水二
次氧化,防止增氮增氧,钢水浇铸温度为1512-1545℃,降低浇铸温度提高凝固前结晶形核速率、减小凝固坯壳和中心钢液的温度梯度、抑制柱状晶,控制过热度为10-25℃,低过热度浇注提高液态金属形核率、促进形成等轴晶;
[0030]
控制结晶器水流量为1800-1850l/min,结晶器电磁搅拌参数为电流200-400a、频率2-4hz,末端电磁搅拌参数为电流90-130a、频率8-10hz,结晶器液面波动≤
±
1.8mm,保证结晶器液位稳定、避免皮下夹杂;
[0031]
二冷比水流量为0.68-0.85l/kg,二冷区弱冷避免二冷比水流量过大造成铸坯表面温度低温脆性产生皮下裂纹,同时避免二冷比水流量过小造成坯壳厚度较薄和液相穴深度提高而产生漏拉和内部裂纹;拉速控制在1.0-1.4m/min,采用低拉速降低材料的偏析,辊缝收缩量为10-10.3mm,避免铸坯鼓肚及矫直应力过大造成液相静压力膨胀和内部裂纹,从而减小中心疏松和裂纹缺陷,改善材料组织,铸坯经矫直机矫直、定尺切割后及时入坑缓冷,控制铸坯入坑温度≥665℃,缓冷时间≥60h,出坑温度≤220℃,得到铸坯;
[0032]
有效控制低倍质量及中心偏析,铸坯的低倍组织均匀细致,表面质量良好,中心偏析≤0.5级、缩孔≤1.5级、中心疏松≤1.0级、角部裂纹≤0.5级,皮下裂纹、中心裂纹、中间裂纹均为0级;a类夹杂物、b类夹杂物、c类夹杂物为0级,d类夹杂物≤0.5级;
[0033]
s5、加热:将铸坯进入三段步进式加热炉,控制预热段温度为650-900℃,加热段温度为1190-1230℃,均热段温度为1195~1210℃,总加热时间控制在10~20h,控制铸坯表面温度在1195-1200℃保温1.5-3h,铸坯心部温度在1195-1200℃保温1-2.5h,避免温度过高导致晶粒粗大、形成难以去除的氧化皮,避免温度过低不利于心部偏析扩散,有效地控制细化晶粒,保证奥氏体成分与组织均匀化,得到钢坯;
[0034]
s6、高压水除鳞:在除鳞水压≥22mpa下除去钢坯表面氧化铁皮、确保产品表面质量;
[0035]
s7、轧制:采用大压下轧制工艺加工步骤s6的铸坯,包括6道次粗轧、6道次中轧、6道次预精轧、4道次精轧工序,开轧温度为950~1000℃,精轧阶段累计变形量≥18%,降低碳化物组织偏析,中轧、精轧前后均采用水冷机组控冷时,每个控冷段控制冷却水量逐渐降低、保证铸坯表面和心部冷却至控制温度,预精轧前温度为820-945℃,终轧温度为800~845℃,采用低温轧制在奥氏体未再结晶区和低温两相区累积变形轧制控制碳化物网状,保证细化晶粒及碳化物的弥散析出,得到棒材;
[0036]
s8、缓冷:在倍尺冷床中进行缓冷,冷却速度为1.5-2.5℃/s,避免沿晶界析出粗大的半封闭网状分布的碳化物而增加脆性、在材料相变过程中产生裂纹,下冷床温度为380-440℃,下冷线后进缓冷罩堆缓冷48-72h;
[0037]
s9、热处理:将步骤s8的棒材加热到760-775℃保温1-2h,按10-15℃/s缓冷至620℃以下空冷,使体心立方的铁素体转变为面心立方的奥氏体、部分片状碳化物溶解于奥氏体中,剩余碳化物逐渐由片状向粒状或球状转化,奥氏体中c、cr、mn向晶界处聚集趋势减弱,消除铸造偏析、降低棒材硬度,硬度为172-195hbw,达到晶粒细化,避免冷速过小产生粗大碳化物或冷速过大析出片状碳化物;
[0038]
之后采用淬火 低温回火处理,淬火温度750-840℃,在炉时间系数2~2.8min/mm,淬火后冷却介质为水,冷却速率20~30℃/s,淬硬层深度为0.5-1mm,粒状或球状碳化物在奥氏体中扩散并均匀化,冷却时奥氏体转变为马氏体,用于提高钢的硬度和强度;回火温度
180-240℃,在炉时间系数1.8~2.5min/mm,用于消除淬火时产生的内应力、提高韧性,避免碳化物析出粗化颗粒、合金沿晶界析出连续或不连续的网状脆性,降低亚结构中的孪晶比例,避免形成淬火显微裂纹,保持高硬度和高耐磨性的前提下降低内应力和脆性,稳定材料组织和尺寸,形成回火马氏体 少量残余奥氏体 均匀细小碳化物的组织,降低整个截面的力学性能波动,得到符合综合力学性能的轴承钢。
[0039]
与现有技术相比,本发明的有益效果是:
[0040]
(1)提高钢强度和硬度、降低钢整个截面力学性能波动:轴承钢的碳当量ceq合金化提高强度,以si提高稳定系平衡温度和回火稳定性,控制si/c降低断面敏感性,控制mn-si提高轴承钢强度,以mn、b提高钢的淬透性,以ti细化晶粒,使淬硬层深度为0.5-1mm,降低晶粒表面和内部间化学成分的差异以及晶界杂质或内应力。
[0041]
(2)提高钢水纯净度、降低夹杂物影响:电炉冶炼铝锭预脱氧后采用硅锰合金、硅铁合金和微碳铬铁合金合金化,石灰和铝酸钙造渣料进行脱氧合金化,lf精炼采用预熔精炼渣与sic联合脱氧,以稀土铈铁合金形成小尺寸夹杂并碎化弥散起到变形作用,喂钛铁合金包芯线增加共晶团数量,vd真空破空后喂硼铁合金包芯线,提高钢的纯净性和基体连续性,a类夹杂物、b类夹杂物、c类夹杂物为0级,d类夹杂物≤0.5级。
[0042]
(3)改善铸坯缺陷:减小凝固坯壳和中心钢液的温度梯度、抑制柱状晶、促进形成等轴晶,保证结晶器液位稳定、避免皮下夹杂,二冷区弱冷避免皮下裂纹,低拉速降低材料的偏析,减小中心疏松和裂纹缺陷,有效控制低倍质量及中心偏析。
[0043]
(4)控制碳化物网状:累计变形量降低碳化物组织偏析,每个控冷段控制冷却水量逐渐降低、保证铸坯表面和心部冷却至控制温度,低温轧制在奥氏体未再结晶区和低温两相区累积变形轧制,缓冷避免析出粗大的半封闭网状分布的碳化物和碳化物偏析增大组织脆性。
[0044]
(5)稳定材料组织和尺寸:加热缓冷后空冷消除铸造偏析、降低棒材硬度,淬火 低温回火降低亚结构中的孪晶比例,保持高硬度和高耐磨性的前提下降低内应力和脆性,形成回火马氏体 少量残余奥氏体 均匀细小碳化物的组织。
[0045]
从而综上,得到符合综合力学性能的轴承钢。
具体实施方式
[0046]
下面详细描述本发明的实施例,旨在用于解释本发明,而不能理解为对本发明的限制。
[0047]
实施例1:
[0048]
本发明所述一种高碳铬风电轴承钢的一种较佳实施方式,其组成成分按质量百分数计为:c:1.01%,si:0.52%,mn:0.79%,s:0.012%,p:0.013%,cr:1.38%,ni:0.13%,mo:0.02%,cu:0.06%,b:0.003%,ti:0.002%,ce:0.004%,o:0.001%,n:0.009%,余量为铁和不可避免的杂质;所述轴承钢的碳当量ceq=[c mn/6 (cr mo v)/5 (ni cu)/15]*100%=1.43%,si/c为0.51,mn-si为0.27%。
[0049]
上述高碳铬风电轴承钢的生产工艺,规格为包括以下步骤:
[0050]
s1、电炉冶炼:将炼钢原料经铁水预处理kr脱硫、以氧气顶吹和双渣法电炉冶炼得到钢水,铁水预处理kr脱硫的脱硫剂按每吨钢水采用6.2kg石灰和1.5kg萤石,碱度r为3.5;
控制s≤0.005%,控制出钢终点碳含量为0.45%,终点磷含量≤0.008%,出钢温度控制在1652℃;
[0051]
挡渣出钢且出钢过程进行脱氧合金化,按104t/炉钢水出钢1/3后加入3.6kg/t的铝锭预脱氧,出钢3/5后加入5.6kg/t的硅锰合金(femn64si16)、0.8kg/t的硅铁合金(fesi75a12.0-c)和9.1kg/t微碳铬铁合金(fecr69c0.1)进行合金化,出钢3/4后一次性加入4.74kg/t的石灰和2.5kg/t的铝酸钙造渣料,形成精炼初渣;
[0052]
s2、lf精炼:将步骤s1的钢水lf精炼炉进站之后采用预熔精炼渣与sic按质量比2:1联合脱氧,少量多次加在渣面上,总加入量为0.68kg/t钢水,白渣时间≥25min,预熔精炼渣的组成成分按质量百分数计包括cao:49%,al2o3:26%,mgo:7%,sio2:11%,caf2:4%、na2o:3%;
[0053]
精炼前期氩气流量为250nl/min;精炼中期使用低铝硅铁合金(fesi75a10.5-b)、高硅硅锰(femn64si27)、低碳锰铁(femn88c0.4)、硅铁(fesi45)、钼铁(femo55-b),氩气流量为145nl/min进行成分微调;
[0054]
精炼后期钢水的活度氧≤2.8*10-6
,按每炉钢水加入82kg稀土铈铁合金(cefe-20),氩气流量85nl/min;随后以2.5m/s的喂丝速度喂入3m/t钛铁合金包芯线(ti:29.5%),使钢水中成分达标出站,出站温度为1615℃;
[0055]
s3、vd真空:将步骤s2的钢水进vd站进行vd真空脱气处理,极限真空度≤68pa,保压时间35min,软吹氩时间40min,氩气流量为15nl/min,钢中氢脱至1.4*10-6
以下,破空后以1.2m/s的喂丝速度喂入1.4m/t硼铁合金包芯线(b:15.5%),得到符合成分要求的精炼钢水,出钢温度为1583℃;
[0056]
s4、连铸:将步骤s3的钢水采用八机八流连铸机连铸时钢包到中间包用带氩封长水口,中间包到结晶器用浸入式水口全保护浇铸,中间包用碱度>2.5的覆盖剂,钢水浇铸温度为1532℃,控制过热度为10-25℃;
[0057]
控制结晶器水流量为1825l/min,结晶器电磁搅拌参数为电流300a、频率3hz,末端电磁搅拌参数为电流120a、频率9hz,结晶器液面波动≤
±
1.3mm;
[0058]
二冷比水流量为0.7l/kg,拉速控制在1.3m/min,辊缝收缩量为10.2mm,经矫直机矫直、定尺切割后及时入坑缓冷,控制铸坯入坑温度670℃,缓冷时间62h,出坑温度200℃,得到铸坯;
[0059]
s5、加热:将铸坯进入三段步进式加热炉,炉内保证弱还原性气氛,控制预热段温度为720-780℃,预热时间为6h,加热段温度为1190-1220℃,加热时间为5h,均热段温度为1195~1205℃,总加热时间控制在14.5h,得到钢坯;
[0060]
s6、高压水除鳞:在除鳞水压26mpa下除去钢坯表面氧化铁皮;
[0061]
s7、轧制:采用大压下轧制工艺加工步骤s6的铸坯,包括6道次粗轧、6道次中轧、6道次预精轧、4道次精轧工序,开轧温度为975℃,精轧阶段累计变形量22.5%,中轧、精轧前后均采用水冷机组控冷时,每个控冷段控制冷却水量逐渐降低、保证铸坯表面和心部冷却至控制温度,预精轧前温度为880℃,终轧温度为830℃,得到棒材;
[0062]
s8、缓冷:在倍尺冷床中进行缓冷,冷却速度为2.2℃/s,下冷床温度为410℃,下冷线后进缓冷罩堆缓冷56h;
[0063]
s9、热处理:将步骤s8的棒材加热到772℃保温1.4h,按12.8℃/s缓冷至595℃空
冷,之后采用淬火 低温回火处理,淬火温度810℃,在炉时间系数2.3min/mm,淬火后冷却介质为水,冷却速率25℃/s,淬硬层深度为0.8mm;回火温度210℃,在炉时间系数1.9min/mm,得到符合综合力学性能的轴承钢。
[0064]
实施例2:
[0065]
本发明所述一种高碳铬风电轴承钢的一种较佳实施方式,其组成成分按质量百分数计为:c:1.0%,si:0.53%,mn:0.81%,s:0.01%,p:0.08%,cr:1.41%,ni:0.14%,mo:0.03%,cu:0.05%,b:0.004%,ti:0.002%,ce:0.004%,o:0.001%,n:0.008%,余量为铁和不可避免的杂质;所述轴承钢的碳当量ceq=[c mn/6 (cr mo v)/5 (ni cu)/15]*100%=1.44%,si/c为0.53,mn-si为0.28%。
[0066]
上述高碳铬风电轴承钢的生产工艺,规格为包括以下步骤:
[0067]
s1、电炉冶炼:将炼钢原料经铁水预处理kr脱硫、以氧气顶吹和双渣法电炉冶炼得到钢水,铁水预处理kr脱硫的脱硫剂按每吨钢水采用5.3kg石灰和2.1kg萤石,碱度r为2.8;控制s≤0.005%,控制出钢终点碳含量为0.46%,终点磷含量≤0.008%,出钢温度控制在1645℃;
[0068]
挡渣出钢且出钢过程进行脱氧合金化,按102t/炉钢水出钢1/2后加入3.7kg/t的铝锭预脱氧,出钢2/3后加入5.7kg/t的硅锰合金(femn64si16)、0.6kg/t的硅铁合金(fesi75a12.0-c)和9.3kg/t微碳铬铁合金(fecr69c0.1)进行合金化,出钢3/4后一次性加入4.8kg/t的石灰和2.3kg/t的铝酸钙造渣料,形成精炼初渣;
[0069]
s2、lf精炼:将步骤s1的钢水lf精炼炉进站之后采用预熔精炼渣与sic按质量比2:1联合脱氧,少量多次加在渣面上,总加入量为0.9kg/t钢水,白渣时间≥25min,预熔精炼渣的组成成分按质量百分数计包括cao:44%,al2o3:31%,mgo:8%,sio2:9%,caf2:4%、na2o:4%;
[0070]
精炼前期氩气流量为240nl/min;精炼中期使用低铝硅铁合金(fesi75a10.5-b)、高硅硅锰(femn64si27)、低碳锰铁(femn88c0.4)、硅铁(fesi45)、钼铁(femo55-b),氩气流量为140nl/min进行成分微调;
[0071]
精炼后期钢水的活度氧≤2.8*10-6
,按每炉钢水加入83kg稀土铈铁合金(cefe-20),氩气流量74nl/min;随后以23m/s的喂丝速度喂入2.9m/t钛铁合金包芯线(ti:29.5%),使钢水中成分达标出站,出站温度为1610℃;
[0072]
s3、vd真空:将步骤s2的钢水进vd站进行vd真空脱气处理,极限真空度≤68pa,保压时间25min,软吹氩时间40min,氩气流量为20nl/min,钢中氢脱至1.4*10-6
以下,破空后以1.7m/s的喂丝速度喂入1.4m/t硼铁合金包芯线(b:15.5%),得到符合成分要求的精炼钢水,出钢温度为1605℃;
[0073]
s4、连铸:将步骤s3的钢水采用八机八流连铸机连铸时钢包到中间包用带氩封长水口,中间包到结晶器用浸入式水口全保护浇铸,中间包用碱度>2.5的覆盖剂,钢水浇铸温度为1530℃,控制过热度为10-25℃;
[0074]
控制结晶器水流量为1840l/min,结晶器电磁搅拌参数为电流200a、频率2hz,末端电磁搅拌参数为电流130a、频率10hz,结晶器液面波动≤
±
1.5mm;
[0075]
二冷比水流量为0.82l/kg,拉速控制在1.2m/min,辊缝收缩量为10.2mm,经矫直机矫直、定尺切割后及时入坑缓冷,控制铸坯入坑温度672℃,缓冷时间63h,出坑温度215℃,
得到铸坯;
[0076]
s5、加热:将铸坯进入三段步进式加热炉,炉内保证弱还原性气氛,控制预热段温度为740-880℃,预热时间为5.5h,加热段温度为1195-1220℃,加热时间为5.5h,均热段温度为1195~1210℃,总加热时间控制在14h,得到钢坯;
[0077]
s6、高压水除鳞:在除鳞水压24mpa下除去钢坯表面氧化铁皮;
[0078]
s7、轧制:采用大压下轧制工艺加工步骤s6的铸坯,包括6道次粗轧、6道次中轧、6道次预精轧、4道次精轧工序,开轧温度为990℃,精轧阶段累计变形量19.7%,中轧、精轧前后均采用水冷机组控冷时,每个控冷段控制冷却水量逐渐降低、保证铸坯表面和心部冷却至控制温度,预精轧前温度为920℃,终轧温度为815℃,得到棒材;
[0079]
s8、缓冷:在倍尺冷床中进行缓冷,冷却速度为1.8℃/s,下冷床温度为410℃,下冷线后进缓冷罩堆缓冷65h;
[0080]
s9、热处理:将步骤s8的棒材加热到770℃保温1h,按13℃/s缓冷至610℃空冷,之后采用淬火 低温回火处理,淬火温度815℃,在炉时间系数2.5min/mm,淬火后冷却介质为水,冷却速率26℃/s,淬硬层深度为0.7mm;回火温度200℃,在炉时间系数2.2min/mm,得到符合综合力学性能的轴承钢。
[0081]
实施例3:
[0082]
本发明所述一种高碳铬风电轴承钢的一种较佳实施方式,其组成成分按质量百分数计为:c:1.01%,si:0.51%,mn:0.77%,s:0.01%,p:0.01%,cr:1.33%,ni:0.11%,mo:0.06%,cu:0.04%,b:0.003%,ti:0.002%,ce:0.004%,o:0.001%,n:0.01%,余量为铁和不可避免的杂质;所述轴承钢的碳当量ceq=[c mn/6 (cr mo v)/5 (ni cu)/15]*100%=1.43%,si/c为0.50,mn-si为0.26%。
[0083]
上述高碳铬风电轴承钢的生产工艺,规格为包括以下步骤:
[0084]
s1、电炉冶炼:将炼钢原料经铁水预处理kr脱硫、以氧气顶吹和双渣法电炉冶炼得到钢水,铁水预处理kr脱硫的脱硫剂按每吨钢水采用6.4kg石灰和1.4kg萤石,碱度r为4.3;控制s≤0.005%,控制出钢终点碳含量为0.45%,终点磷含量≤0.008%,出钢温度控制在1660℃;
[0085]
挡渣出钢且出钢过程进行脱氧合金化,按96t/炉钢水出钢1/3后加入3.7kg/t的铝锭预脱氧,出钢3/5后加入6.1kg/t的硅锰合金(femn64si16)、0.7kg/t的硅铁合金(fesi75a12.0-c)和9.2kg/t微碳铬铁合金(fecr69c0.1)进行合金化,出钢3/4后一次性加入4.7kg/t的石灰和2.6kg/t的铝酸钙造渣料,形成精炼初渣;
[0086]
s2、lf精炼:将步骤s1的钢水lf精炼炉进站之后采用预熔精炼渣与sic按质量比2:1联合脱氧,少量多次加在渣面上,总加入量为0.75kg/t钢水,白渣时间≥25min,预熔精炼渣的组成成分按质量百分数计包括cao:45%,al2o3:24%,mgo:11%,sio2:10%,caf2:4%、na2o:6%;
[0087]
精炼前期氩气流量为260nl/min;精炼中期使用低铝硅铁合金(fesi75a10.5-b)、高硅硅锰(femn64si27)、低碳锰铁(femn88c0.4)、硅铁(fesi45)、钼铁(femo55-b),氩气流量为140nl/min进行成分微调;
[0088]
精炼后期钢水的活度氧≤2.8*10-6
,按每炉钢水加入83kg稀土铈铁合金(cefe-20),氩气流量70nl/min;随后以3m/s的喂丝速度喂入2.7m/t钛铁合金包芯线(ti:29.5%),
使钢水中成分达标出站,出站温度为1610℃;
[0089]
s3、vd真空:将步骤s2的钢水进vd站进行vd真空脱气处理,极限真空度≤68pa,保压时间25min,软吹氩时间40min,氩气流量为15nl/min,钢中氢脱至1.4*10-6
以下,破空后以1.3m/s的喂丝速度喂入1.4m/t硼铁合金包芯线(b:15.5%),得到符合成分要求的精炼钢水,出钢温度为1570℃;
[0090]
s4、连铸:将步骤s3的钢水采用八机八流连铸机连铸时钢包到中间包用带氩封长水口,中间包到结晶器用浸入式水口全保护浇铸,中间包用碱度>2.5的覆盖剂,钢水浇铸温度为1530℃,控制过热度为10-25℃;
[0091]
控制结晶器水流量为1825l/min,结晶器电磁搅拌参数为电流400a、频率4hz,末端电磁搅拌参数为电流120a、频率10hz,结晶器液面波动≤
±
1.5mm;
[0092]
二冷比水流量为0.8l/kg,拉速控制在1.1m/min,辊缝收缩量为10.1mm,经矫直机矫直、定尺切割后及时入坑缓冷,控制铸坯入坑温度675℃,缓冷时间70h,出坑温度215℃,得到铸坯;
[0093]
s5、加热:将铸坯进入三段步进式加热炉,炉内保证弱还原性气氛,控制预热段温度为700-840℃,预热时间为5h,加热段温度为1190-1230℃,加热时间为5h,均热段温度为1195~1210℃,总加热时间控制在14.5h,得到钢坯;
[0094]
s6、高压水除鳞:在除鳞水压23mpa下除去钢坯表面氧化铁皮;
[0095]
s7、轧制:采用大压下轧制工艺加工步骤s6的铸坯,包括6道次粗轧、6道次中轧、6道次预精轧、4道次精轧工序,开轧温度为968℃,精轧阶段累计变形量20.5%,中轧、精轧前后均采用水冷机组控冷时,每个控冷段控制冷却水量逐渐降低、保证铸坯表面和心部冷却至控制温度,预精轧前温度为875℃,终轧温度为819℃,得到棒材;
[0096]
s8、缓冷:在倍尺冷床中进行缓冷,冷却速度为2.1℃/s,下冷床温度为415℃,下冷线后进缓冷罩堆缓冷61h;
[0097]
s9、热处理:将步骤s8的棒材加热到782℃保温1.4h,按14℃/s缓冷至614℃空冷,之后采用淬火 低温回火处理,淬火温度810℃,在炉时间系数2.4min/mm,淬火后冷却介质为水,冷却速率24℃/s,淬硬层深度为0.7mm;回火温度234℃,在炉时间系数2.2min/mm,得到符合综合力学性能的轴承钢。
[0098]
实施例4:
[0099]
本发明所述一种高碳铬风电轴承钢的一种较佳实施方式,其组成成分按质量百分数计为:c:0.99%,si:0.50%,mn:0.82%,s:0.01%,p:0.012%,cr:1.42%,ni:0.12%,mo:0.03%,cu:0.04%,b:0.003%,ti:0.002%,ce:0.004%,o:0.001%,n:0.009%,余量为铁和不可避免的杂质;所述轴承钢的碳当量ceq=[c mn/6 (cr mo v)/5 (ni cu)/15]*100%=1.43%,si/c为0.50,mn-si为0.32%。
[0100]
上述高碳铬风电轴承钢的生产工艺,规格为包括以下步骤:
[0101]
s1、电炉冶炼:将炼钢原料经铁水预处理kr脱硫、以氧气顶吹和双渣法电炉冶炼得到钢水,铁水预处理kr脱硫的脱硫剂按每吨钢水采用5.8kg石灰和2.2kg萤石,碱度r为3.4;控制s≤0.005%,控制出钢终点碳含量为0.45%,终点磷含量≤0.008%,出钢温度控制在1655℃;
[0102]
挡渣出钢且出钢过程进行脱氧合金化,按96t/炉钢水出钢1/2后加入3.6kg/t的铝
锭预脱氧,出钢3/5后加入6kg/t的硅锰合金(femn64si16)、0.7kg/t的硅铁合金(fesi75a12.0-c)和9kg/t微碳铬铁合金(fecr69c0.1)进行合金化,出钢3/4后一次性加入5.2kg/t的石灰和2.4kg/t的铝酸钙造渣料,形成精炼初渣;
[0103]
s2、lf精炼:将步骤s1的钢水lf精炼炉进站之后采用预熔精炼渣与sic按质量比2:1联合脱氧,少量多次加在渣面上,总加入量为0.7kg/t钢水,白渣时间≥25min,预熔精炼渣的组成成分按质量百分数计包括cao:46%,al2o3:24%,mgo:6%,sio2:10%,caf2:9%、na2o:5%;
[0104]
精炼前期氩气流量为290nl/min;精炼中期使用低铝硅铁合金(fesi75a10.5-b)、高硅硅锰(femn64si27)、低碳锰铁(femn88c0.4)、硅铁(fesi45)、钼铁(femo55-b),氩气流量为145nl/min进行成分微调;
[0105]
精炼后期钢水的活度氧≤2.8*10-6
,按每炉钢水加入84kg稀土铈铁合金(cefe-20),氩气流量75nl/min;随后以2.5m/s的喂丝速度喂入2.8m/t钛铁合金包芯线(ti:29.5%),使钢水中成分达标出站,出站温度为1612℃;
[0106]
s3、vd真空:将步骤s2的钢水进vd站进行vd真空脱气处理,极限真空度≤68pa,保压时间30min,软吹氩时间40min,氩气流量为26nl/min,钢中氢脱至1.4*10-6
以下,破空后以1.6m/s的喂丝速度喂入1.4m/t硼铁合金包芯线(b:15.5%),得到符合成分要求的精炼钢水,出钢温度为1585℃;
[0107]
s4、连铸:将步骤s3的钢水采用八机八流连铸机连铸时钢包到中间包用带氩封长水口,中间包到结晶器用浸入式水口全保护浇铸,中间包用碱度>2.5的覆盖剂,钢水浇铸温度为1532℃,控制过热度为10-25℃;
[0108]
控制结晶器水流量为1830l/min,结晶器电磁搅拌参数为电流300a、频率3hz,末端电磁搅拌参数为电流90a、频率8hz,结晶器液面波动≤
±
1.8mm;
[0109]
二冷比水流量为0.7l/kg,拉速控制在1.2m/min,辊缝收缩量为10.2mm,经矫直机矫直、定尺切割后及时入坑缓冷,控制铸坯入坑温度682℃,缓冷时间64h,出坑温度208℃,得到铸坯;
[0110]
s5、加热:将铸坯进入三段步进式加热炉,炉内保证弱还原性气氛,控制预热段温度为668-754℃,预热时间为6h,加热段温度为1190-1223℃,加热时间为4.5h,均热段温度为1195~1210℃,总加热时间控制在13h,得到钢坯;
[0111]
s6、高压水除鳞:在除鳞水压24mpa下除去钢坯表面氧化铁皮;
[0112]
s7、轧制:采用大压下轧制工艺加工步骤s6的铸坯,包括6道次粗轧、6道次中轧、6道次预精轧、4道次精轧工序,开轧温度为990℃,精轧阶段累计变形量19%,中轧、精轧前后均采用水冷机组控冷时,每个控冷段控制冷却水量逐渐降低、保证铸坯表面和心部冷却至控制温度,预精轧前温度为874℃,终轧温度为824℃,得到棒材;
[0113]
s8、缓冷:在倍尺冷床中进行缓冷,冷却速度为2.3℃/s,下冷床温度为410℃,下冷线后进缓冷罩堆缓冷62h;
[0114]
s9、热处理:将步骤s8的棒材加热到770℃保温1.2h,按13.5℃/s缓冷至600℃空冷,之后采用淬火 低温回火处理,淬火温度795℃,在炉时间系数2.4min/mm,淬火后冷却介质为水,冷却速率25℃/s,淬硬层深度为0.9mm;回火温度190℃,在炉时间系数2.3min/mm,得到符合综合力学性能的轴承钢。
[0115]
对比例1:
[0116]
一种轴承钢,其组成成分按质量百分数计为:c:1.04%,si:0.25%,mn:0.34%,s:0.015%,p:0.02%,cr:1.45%,ni:0.2%,mo:0.05%,cu:0.02%,o:0.015%,n:0.014%,余量为铁和不可避免的杂质;所述轴承钢的碳当量ceq=[c mn/6 (cr mo v)/5 (ni cu)/15]*100%=1.41%,si/c为0.24,mn-si为0.09%。
[0117]
上述轴承钢的生产工艺,其工艺按电炉冶炼
→
lf精炼
→
vd真空
→
连铸
→
加热
→
高压水除鳞
→
轧制
→
缓冷
→
热处理流程,具体地:
[0118]
与实施例1的区别在于,电炉冶炼终点目标按c:0.4%,p≤0.01%,s≤0.03%控制,出钢过程一次性加入3.7kg/t铝锭、0.65kg/t锰铁合金(femn68c7.0)、5.2kg/t的石灰;lf精炼加入铝豆 sic脱氧,造白渣,终渣碱度为4.0,不加入稀土铈铁合金,喂1.1m/t钙线;vd真空软吹氩时间30min,不喂硼铁合金包芯线;连铸过热度为30-35℃,结晶器液面波动≤
±
2.8mm,二冷比水流量为0.9l/kg,拉速控制在1.7m/min,辊缝收缩量为10.5mm。
[0119]
对比例2:
[0120]
一种轴承钢,其组成成分按质量百分数计为:c:1.05%,si:0.22%,mn:0.32%,s:0.015%,p:0.02%,cr:1.33%,ni:0.15%,mo:0.04%,cu:0.02%,o:0.015%,n:0.013%,余量为铁和不可避免的杂质;所述轴承钢的碳当量ceq=[c mn/6 (cr mo v)/5 (ni cu)/15]*100%=1.39%,si/c为0.21,mn-si为0.1%。
[0121]
上述轴承钢的生产工艺,其工艺按电炉冶炼
→
lf精炼
→
vd真空
→
连铸
→
加热
→
高压水除鳞
→
轧制
→
缓冷
→
热处理流程,具体地:
[0122]
与实施例4的区别在于:lf精炼不加入稀土铈铁合金;vd真空软吹氩时间30min,不喂硼铁合金包芯线;加热工序预热段温度为680-810℃,预热4h,加热段温度为1220-1230℃,加热,加热3h,均热段温度为1225~1228℃,总加热时间控制在9h;除鳞水压20mpa;开轧温度为1108℃,每个控冷段控制冷却水量保持一致、预精轧前温度为975℃,终轧温度为915℃,精轧阶段累计变形量15.5%;热处理加热到790℃保温1.5h,按9.5℃/s缓冷至630℃空冷,淬火温度700℃,在炉时间系数2.2min/mm,淬火后冷却介质为水,冷却速率22℃/s,淬硬层深度为0.4mm,回火温度160℃,在炉时间系数2.7min/mm。
[0123]
将实施例1-4、对比例1-2的铸坯按照gb/t 10561检测夹杂物成分,其结果如下表1:
[0124]
表1
[0125][0126]
可见,电炉冶炼铝锭预脱氧后采用硅锰合金、硅铁合金和微碳铬铁合金合金化,石灰和铝酸钙造渣料进行脱氧合金化,lf精炼采用预熔精炼渣与sic联合脱氧,以稀土铈铁合金形成小尺寸夹杂并碎化弥散起到变形作用,喂钛铁合金包芯线增加共晶团数量,vd真空
破空后喂硼铁合金包芯线,提高钢的纯净性和基体连续性,a类夹杂物、b类夹杂物、c类夹杂物为0级,d类夹杂物≤0.5级。
[0127]
将实施例1-4、对比例1-2的铸坯按照gb/t1979测试结构钢低倍组织缺陷,其结果如下表2:
[0128]
表2
[0129][0130]
可见,通过减小凝固坯壳和中心钢液的温度梯度、抑制柱状晶、促进形成等轴晶,保证结晶器液位稳定、避免皮下夹杂,二冷区弱冷避免皮下裂纹,低拉速降低材料的偏析,减小中心疏松和裂纹缺陷,有效控制低倍质量及中心偏析,铸坯的低倍组织均匀细致,表面质量良好,中心偏析≤0.5级、缩孔≤1.5级、中心疏松≤1.0级、角部裂纹≤0.5级,皮下裂纹、中心裂纹、中间裂纹均为0级。
[0131]
将实施例1-4、对比例1-2的棒材按照gb/t2828.1-规定的抽样程序抽样,按照gb231-84《金属布氏硬度试验方法》测试热处理加热空冷后和回火后的棒材硬度,将实施例1-4、对比例1-2的轴承钢按检测标准:en iso 6892-1进行拉伸性能测试,按检测标准:en iso 148-1进行冲击性能测试,其结果如下表3:
[0132]
表3
[0133]
序号空冷后硬度/hbw回火后硬度/hrc抗拉强度(σb/mpa)冲击功(akv/j)实施例119268191126实施例218469187525实施例317570189424实施例418668188028对比例12186289422对比例224260108521
[0134]
可见,轴承钢的碳当量ceq合金化提高强度,以si提高稳定系平衡温度和回火稳定性,控制si/c降低断面敏感性,控制mn-si提高轴承钢强度,以mn、b提高钢的淬透性,以ti细化晶粒,使淬硬层深度为0.5-1mm,降低晶粒表面和内部间化学成分的差异以及晶界杂质或内应力,通过每个控冷段控制冷却水量逐渐降低、保证铸坯表面和心部冷却至控制温度,低温轧制在奥氏体未再结晶区和低温两相区累积变形轧制,缓冷避免析出粗大的半封闭网状分布的碳化物和碳化物偏析增大组织脆性,通过加热缓冷后空冷消除铸造偏析、降低棒材硬度,硬度为172-195hbw,淬火 低温回火降低亚结构中的孪晶比例,保持高硬度和高耐磨性的前提下降低内应力和脆性,轴承钢的抗拉强度为1852-1924mpa,冲击功akv为24-28j,硬度为66-71hrc。
[0135]
上文所列出的一系列的详细说明仅仅是针对本发明的可行性实施例的具体说明,
它们并非用以限制本发明的保护范围,凡未脱离本发明技艺精神所作的等效实施例或变更均应包含在本发明的保护范围之内。
再多了解一些
本文用于创业者技术爱好者查询,仅供学习研究,如用于商业用途,请联系技术所有人。