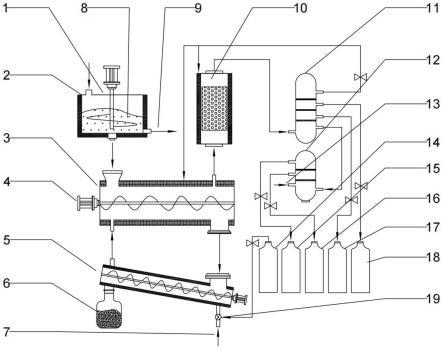
1.本发明涉及有机固废脱氯、脱硅及催化热解技术领域,特别是涉及一种废塑料水热耦合串级催化制备单环芳烃系统及方法。
背景技术:
2.世界范围内填埋或弃置于环境中的混合废塑料积累量达49亿吨,带来了严重的环境污染及资源浪费问题。通过催化热解将废塑料转化为高价值的单环芳烃类基础化学品是实现其高价值利用的一种绿色途径。然而实际工业回收的主要是包含多类型废塑料(聚乙烯、聚丙烯、聚苯乙烯、聚氯乙烯等)以及大量沙土的含氯、含硅混合物,其直接热解转化的液相产品中非均质杂质含量高、氯/硅污染物脱除难、单环芳烃产率低。为脱除无机硅对混合废塑料清洗破碎需要较高的成本,为脱除有机氯需要额外的预处理过程,且目前的热解脱氯、催化脱氯技术脱氯率较低。此外,尽管通过引入石油工业中的沸石类催化剂有效提升了催化产物中单环芳烃的选择性,但油产物产率下降幅度巨大,单环芳烃实际产率提升程度有限,且由于高浓度氯/硅带来的催化剂失活与毒化问题亟待解决。
技术实现要素:
3.本发明提供了一种废塑料水热耦合串级催化制备单环芳烃的系统及方法,解决了传统热解方法产物收率低、污染物脱除难的技术问题。
4.本发明的技术方案如下:
5.一种废塑料水热耦合串级催化制备单环芳烃系统,包括水热批处理装置、原位催化热解装置、催化剂再生回收装置、非原位催化热解装置和产物收集利用装置;
6.水热批处理装置包括物料入口、物料出口和循环水出口;水热批处理装置还包括高温承压反应釜体与螺带式搅拌器;物料通过物料入口进入水热批处理装置内经过螺带式搅拌器对物料进行脱氯/脱硅预处理,将混合物料均一化,并削弱其分子间连接键的键能;
7.原位催化热解装置包括进料口、催化剂入口a、热解馏分出口和催化剂出口a;进料口与水热批处理装置的物料出口连接;催化剂通过催化剂入口a进入原位催化热解装置内,与经过预处理后的物料混合进行断键预处理;
8.催化剂再生回收装置包括催化剂入口b、催化剂出口b;催化剂出口b与原位催化热解装置的催化剂入口a连接;催化剂再生回收装置回收并再生原位催化热解装置中的催化剂;
9.非原位催化热解装置与原位催化热解装置上的热解馏分出口连接,对原位催化热解产生的热解蒸汽进行深度重整;
10.产物收集利用装置分离液相产物中的单环芳烃,分离所得残余气体通过燃烧为原位催化及非原位催化装置供热。
11.其进一步技术方案为:
12.水热批处理装置的高温承压反应釜内批次循环填充度为50%的低浓度碱溶液,碱
溶液为氢氧化钠、碳酸钠、碳酸氢钠中的一种或多种,碱浓度为0.1m~0.2m。
13.原位催化热解装置为套筒结构,外筒设有燃烧室,对内筒供热;
14.内筒设有物料入口与催化剂入口a,内筒中设有螺旋绞龙,混合物料与催化剂;
15.催化剂采用介孔结构金属负载碳基催化剂,其碳基基底选用活性炭、生物质炭、氮化碳、石墨烯、碳纳米管中的一种或多种;
16.负载金属中的主催化剂选用铁、镍、锌中的一种或多种,负载比例为1wt%~3wt%;
17.负载金属中的助催化剂选用钼,负载比例为0.5wt%;造孔剂为三聚氰胺、尿素、碳酸氢钠的一种或多种。
18.催化剂再生回收装置包括螺旋绞龙输送机、储碳罐和还原气瓶,螺旋输送机循环再生介孔催化剂,其前端设有新催化剂入口与回收催化剂入口,后端设有催化剂出口b与催化剂回收口;
19.新催化剂入口通过球阀与还原气瓶连接,催化剂回收口与储碳罐连接;
20.还原气瓶提供还原气氛,为氮气、氦气、氢气中的一种。
21.非原位催化热解装置为套筒结构,外筒设有燃烧室;内筒中设有蜂窝结构的微孔分子筛催化剂,分子筛催化剂硅铝比为20~40,孔道直径为0.5nm~1nm。
22.产物收集利用装置包括分馏塔、萃取蒸馏塔、苯罐、甲苯罐、乙苯罐以及二甲苯罐,分馏塔分离苯、甲苯以及不凝气体;
23.萃取蒸馏塔分离乙苯与二甲苯,所用萃取剂可为苯酚、甲酸甲酯、硝基甲苯、二硝基甲苯中的任意一种,萃取剂由萃取剂入口添加。
24.一种废塑料水热耦合串级催化制备单环芳烃方法,包括以下具体步骤:
25.s1、废塑料原料进入水热批处理装置进行温和水热脱氯/脱硅预处理,通过亚临界碱液环境一步脱除有机氯污染物与无机硅杂质,并弱化废塑料分子间连接键,实现混合物料均一化,预处理结束后系统冷却分离废液与固体物料,该废液经低温蒸发后可重新应用于水热处理;
26.s2、预处理原料进入原位催化热解装置进行预断键反应产生初步热解馏分:物料与从催化剂再生回收装置给入的介孔碳基催化剂在绞龙作用下充分混合,在400℃~500℃下断键转化为c6~c
20
的链烯烃及少部分单环芳烃,碳基催化剂经过催化剂再生回收装置在还原气氛下再生后进入新的反应循环,并定期更换;
27.s3、热解馏分进入非原位催化热解装置深度重整:热解馏分在低硅铝比、小孔道直径的分子筛催化剂中催化提质,利用其择形效果生成富含单环芳烃的液体产物及部分低碳烯烃气体,分子筛催化剂定期煅烧再生;
28.s4、气液产物经过产物收集利用装置进行分离提纯:通过分馏塔实现苯、甲苯与不凝气体的分离,通过萃取蒸馏塔实现乙苯与二甲苯的分离;不凝气体进入原位催化及非原位催化装置的燃烧室,经燃烧后为所述装置供热。
29.其进一步技术方案为:
30.废塑料原料进入水热批处理装置进行脱氯/脱硅,预处理温度为200℃~240℃,预处理时间为2h,螺带搅拌桨转速为150rpm~300rpm,批处理后冷却温度为80℃;
31.预处理物料及碳基催化剂进入原位催化热解装置进行断键反应,催化温度为400
℃~500℃;
32.热解馏分进入非原位催化热解装置进行深度重整,催化温度为450℃~650℃。
33.分馏塔塔底温度为100℃~120℃,塔顶温度为30℃~60℃;萃取蒸馏塔(12)塔底温度为150℃~180℃,塔顶温度为100℃~130℃。
34.与现有技术相比,本发明具有如下有益的技术效果:
35.本发明提出了的混合废塑料水热一步温和脱氯/脱硅的方法,相对于传统多步预处理工艺,新技术能耗更低,污染物脱除效率显著提升。
36.开发了碳基/沸石基双催化剂串级催化的新模式,提供了碳基催化剂在线再生与回收的方法,大幅提升单环芳烃产率与长时间制备稳定性的同时有效降低了催化剂的加工成本。
37.本发明构建了含氯/硅混合塑料废弃物水热-串级催化高产率清洁回收单环芳烃的工艺系统,极大地提高了能源利用率,整体经济性大幅提升。
附图说明
38.图1为本发明实施例的系统结构示意图;
39.图2为本发明实施例的长时间测试单环芳烃产量以及结焦量示意图。
40.附图标记:1、水热批处理装置;2、物料入口;3、原位催化热解装置;4、螺旋绞龙;5、催化剂再生回收装置;6、储碳罐;7、新催化剂入口;8、低浓度碱溶液;9、循环水出口;10、非原位催化热解装置;11、分馏塔;12、萃取蒸馏塔;13、萃取剂入口;14、还原气瓶;15、乙苯罐;16、二甲苯罐;17、甲苯罐;18、苯罐;19、球阀。
具体实施方式
41.实施例1
42.本实施例的水热脱氯/脱硅耦合串级催化制备单环芳烃的系统,如图1所示,包括:
43.水热批处理装置1,用于对物料进行脱氯/脱硅预处理,将混合物料均一化,并削弱其分子间连接键的键能,包括物料入口2、物料出口以及循环水出口9;
44.原位催化热解装置3,用于对预处理后的物料进行断键预处理,包括物料入口、催化剂入口、热解馏分出口和催化剂出口,物料入口与所述水热批处理装置1的物料出口连接;
45.催化剂再生回收装置5,用于回收并再生原位催化热解装置3中的催化剂,包括催化剂入口、催化剂出口,催化剂出口与原位催化热解装置3的催化剂入口连接;
46.非原位催化热解装置10,与热解馏分出口连接,用于对原位催化热解产生的热解蒸汽进行深度重整;
47.产物收集利用装置,用于分离液相产物中的单环芳烃,分离所得残余气体通过燃烧为原位催化及非原位催化装置供热。
48.水热批处理装置1的结构包括高温承压反应釜体与螺带式搅拌器,釜内批次循环填充度为50%的低浓度碱溶液8,该碱溶液可为氢氧化钠、碳酸钠、碳酸氢钠的一种或多种,所述碱浓度为0.1m~0.2m。
49.原位催化热解装置3呈现外筒包含内筒的套筒结构,外筒设有燃烧室,用于对内筒
供热;内筒设有物料入口与催化剂入口,内筒中设有螺旋绞龙4,用于混合物料与催化剂;催化剂采用介孔结构金属负载碳基催化剂,其碳基基底可选用活性炭、生物质炭、氮化碳、石墨烯、碳纳米管的一种或多种;负载金属中的主催化剂选用铁、镍、锌中的一种或多种,负载比例为1wt%~3wt%;负载金属中的助催化剂选用钼,负载比例为0.5wt%;造孔剂为三聚氰胺、尿素、碳酸氢钠的一种或多种。
50.催化剂再生回收装置5包括螺旋绞龙输送机、储碳罐6和还原气瓶14,螺旋输送机用于循环再生介孔催化剂,其前端设有新催化剂入口7与回收催化剂入口,后端设有催化剂出口与催化剂回收口;新催化剂入口7通过球阀19与还原气瓶连接,催化剂回收口与储碳罐连接;还原气瓶用于提供还原气氛,可为氮气、氦气、氢气中的一种。
51.非原位催化热解装置10呈现外筒包含内筒的套筒结构,外筒设有燃烧室;内筒中设有蜂窝结构的微孔分子筛催化剂,该分子筛催化剂硅铝比为20~40,孔道直径为0.5nm~1nm。
52.产物收集利用装置包括分馏塔11、萃取蒸馏塔12、苯罐18、甲苯罐17、乙苯罐15以及二甲苯罐16,分馏塔用于分离苯、甲苯以及不凝气体;萃取蒸馏塔用于分离乙苯与二甲苯,萃取剂可为苯酚、甲酸甲酯、硝基甲苯、二硝基甲苯中的任意一种,该萃取剂由萃取剂入口13添加。
53.本实施例的水热脱氯/脱硅耦合串级催化制备单环芳烃的方法,包括以下步骤:
54.废塑料原料进入水热批处理装置1进行温和水热脱氯/脱硅预处理,通过亚临界碱液环境一步脱除有机氯污染物与无机硅杂质,并弱化废塑料分子间连接键,实现混合物料均一化。预处理温度为200℃~240℃,预处理时间为2h,螺带搅拌桨转速为150rpm~300rpm,批处理后冷却至80℃分离废液与固体物料,该废液经低温蒸发可重新应用于水热处理。经批处理后脱氯率与脱硅率可达99.9%。
55.预处理原料进入原位催化热解装置3进行预断键反应产生初步热解馏分:物料与从催化剂再生回收装置给入的介孔碳基催化剂在绞龙作用下充分混合,在400℃~500℃的催化温度下断键转化为c6~c
20
的链烯烃及少部分单环芳烃,碳基催化剂经过催化剂再生回收装置在还原气氛下再生后进入新的反应循环,并于定期更换。
56.热解馏分进入非原位催化热解装置10深度重整:热解馏分在低硅铝比、小孔道直径的分子筛催化剂中于450℃~650℃下催化提质,利用其择形效果生成富含单环芳烃的液体产物及部分低碳烯烃气体,分子筛催化剂可定期煅烧再生。如图2所示,实验结果表明,串级催化后苯、甲苯、乙苯以及二甲苯的总产率可超过350g/kg,且连续运行6h下产率下降幅度低于15%,催化剂结焦率低于5wt%。
57.气液产物经过产物收集利用装置进行分离提纯:通过分馏塔11实现苯、甲苯与不凝气体的分离,分馏塔11塔底温度为100℃~120℃,塔顶温度为30℃~60℃,通过萃取蒸馏塔12实现乙苯与二甲苯的分离,萃取蒸馏塔12塔底温度为150℃~180℃,塔顶温度为100℃~130℃。苯、甲苯、乙苯以及二甲苯的分离纯度接近100%。不凝气体进入原位催化及非原位催化装置的燃烧室,经燃烧后为上述装置供热。
58.本技术构建了混合废塑料水热脱硅/脱氯耦合串级催化一体化清洁制备单环芳烃的工艺,在温和水热条件下实现混合废塑料中有机氯与无机硅的高效脱除,通过耦合碳基/沸石双催化剂串级催化,显著提升了单环芳烃的产率,实现了废塑料的高值化回收利用。此
外,本技术提供了碳基催化剂在线再生与回收的方法,大幅提升单环芳烃产率与长时间催化稳定性的同时有效降低了催化剂加工成本,能源利用率及技术经济性大幅提升。
再多了解一些
本文用于创业者技术爱好者查询,仅供学习研究,如用于商业用途,请联系技术所有人。