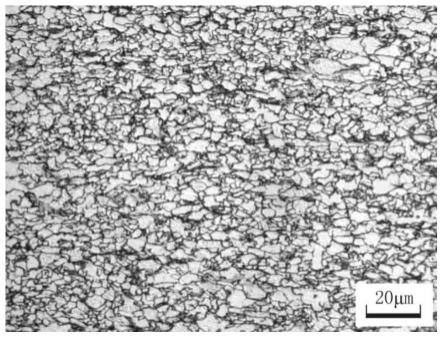
一种基于csp工艺的450mpa级磁极钢及其制造方法
技术领域
1.本发明涉及钢铁冶炼技术领域,具体涉及一种基于csp工艺的450mpa级磁极钢及其制造方法。
背景技术:
2.磁极是发电机转子的重要组成部件,为保证机组稳定高速运行,要求钢板具有良好的力学性能和磁性能,有良好的尺寸精度。磁感应强度的大小是衡量磁极钢性能的好坏的重要指标,为减小发电机组能量转换的损失,即减少涡流损失,因此磁极钢要求具有优良的磁感应强度。
3.为了提高磁极钢的强度,通常采用添加合金元素的方式来提高材料的强度,但强度提高也伴随着磁感强度b50的降低。且随着钢铁企业竞争越来越激烈,如何绿色低成本生产高性能的钢铁材料也为各个企业重点研发的方向。
4.csp(compact strip production)采用热态铸坯进行轧制,csp产线与常规热轧产线相比,减少了常规热轧中的铸坯冷却和二次加热,具有流程短、能耗低、效率高、生产相同钢级所用合金成本低等优势,吨钢投资比常规热轧19~34%,能耗降低约20%,同时所生产产品组织均匀、性能更均匀稳定,各向异性小。
5.申请号为cn200610019773.x的专利公开了一种基于csp工艺的450mpa级磁极钢的生产方法,它包括:(1)将板坯加热至1160-1230℃;(2)热轧的步骤;其开轧温度为1070-1130℃,终轧温度为870-930℃;冷却至620-680℃卷取;(3)冷却到70℃以下时进行酸洗;(4)冷轧的步骤;(5)罩式炉退火;退火控制温度为620-680℃;(6)平整,制成450mpa级的冷轧磁极钢;板坯的主要化学成分的重量百分比为:c 0.06-0.1%,si 0.10-0.30%,mn0.80-1.20%,nb 0.025-0.045%,ti:0.025-0.045%,als 0.02-0.07%,p≤0.025%,s≤0.010%,余量为fe。申请号为cn201610268171.1的专利公开了一种屈服强度450mpa级高磁感低成本冷轧磁极钢及其制造方法,该钢的化学成分质量百分比为:c:0.05~0.09%,mn:0.75~1.15%,p≤0.025%,s≤0.01%,al:0.015~0.05%,n≤0.01%,nb:0.005~0.02%,ti:0.05~0.09%,其余为fe和不可避免的杂质,且须满足:ti≥0.03% 3.43*n。以上两个专利涉及的方法均采用常规热轧工艺生产磁极钢带,生产流程长、耗能及成本更高。
6.通常在磁极钢中添加c、si、mn、nb、ti等合金元素起到强化的作用,锰的添加起到固溶强度的作用,可以显著提高钢的强度,但过高的mn会影响其磁性能;c元素为最经济的强化元素,主要以固溶或碳化物的形式存在于钢基中,过高的c也会影响其磁感应强度。si可提高钢材的强度,减小磁阻,但随着添加量的增加表面易形成条带状氧化铁皮缺陷。nb、ti可以起到细晶强化的作用,且能与多余的碳形成nbc,起到固c的作用。锰铁、铌铁的原料成本较高,过多的添加使得材料的合金成本的增加。
7.连续退火和罩式退火是冷轧板生产中两种退火热处理技术,其中连续退火炉生产可以较高的通板速率进行生产获得最终产品,生产效率高;罩式退火产线投资小,生产规格和产量较为灵活,但罩式退火板型较连续退火差,且罩式退火生产钢板的表面质量较连续
退火要差,材料收得率也低于连续退火。
8.如何通过新成分与新工艺解决以上技术难点,生产出一种具有良好的磁性能的450mpa级磁极用钢,成为本专利的要点。
技术实现要素:
9.为了解决上述技术问题,本发明的目的在于提供一种基于csp工艺的低成本、高磁感、组织均匀的450mpa级磁极钢及其制造方法。
10.为实现上述目的,本发明的技术方案如下:
11.一方面,本发明提供一种基于csp工艺的450mpa级磁极钢,所述磁极钢的化学成分按重量百分比包括::c:0.03~0.065%,mn:0.5~0.8%,si:0.5~0.8%,als:0.020~0.0.05%,p≤0.02%,s≤0.0020%,n≤0.005%,cu≤0.02,ti:0.03~0.06%,t[o]≤0.002%,其余为fe和不可避免的杂质。
[0012]
优选地,所述磁极钢的屈服强度rp
0.2
≥450mpa,抗拉强度rm≥520mpa,磁感应强度b50≥1.63t。
[0013]
另一方面,本发明提供一种制备基于csp工艺的450mpa级磁极钢的方法,包括炼钢
→
lf精炼
→
rh精炼
→
连铸
→
热轧
→
卷取
→
酸洗
→
冷轧
→
连续退火
→
平整。
[0014]
优选地,连铸控制中包钢水过热度为15~35℃,铸坯厚度50~70mm,铸坯拉速4~6m/min;铸坯入均热炉前进行除鳞处理,除鳞水的压力≥210bar;对铸坯进行均热,板坯进轧机前采用高压水除鳞,除鳞水压力≥260bar。
[0015]
优选地,板坯加热温度为1150~1220℃,开轧温度为1030~1080℃,终轧结束温度860~910℃,卷取600~700℃,精轧出口厚度2~6mm。
[0016]
优选地,冷轧总压下率65~80%。
[0017]
优选地,一次冷轧压下率40~50%,轧制出口厚度0.6~2.0mm。
[0018]
优选地,连续退火步骤中,均热温度800~840℃,缓冷终止温度670~710℃,缓冷速率≤15℃/s,快冷速率≥40℃/s,过时效温度370~430℃。
[0019]
优选地,控制退火炉内露点-20~-50℃,炉内氢气含量h2在3~10%,残氧1~20ppm。退火炉内露点、残氧和氢气含量控制有利于获得更优的表面质量,从而达到最佳的强度。
[0020]
优选地,所述磁极钢厚度为0.6~2.0mm,对应的平整延伸率为1.0~2.0%。
[0021]
进一步地,所述磁极钢厚度为0.6~1.2mm时,平整延伸率为1.0~1.4%;所述磁极钢厚度为1.2~2.0mm时,平整延伸率为1.4~2.0%。
[0022]
对本发明中主要化学成分的作用及机理分析如下:
[0023]
c:碳的加入可以有效提高钢材的强度,但随钢板强度明显的增加会降低钢板的塑性和成形性能,且无论c固溶于钢基或以碳化物的形式存在,均不利于磁极钢的磁性能,控制较低的碳含量有利于减少固溶c及渗碳体在晶界的析出,因此钢中的c含量选择为0.03%~0.065%。
[0024]
mn:mn是一种固溶强化元素。mn含量增加降低产品韧性,弱化延伸率、扩孔和冷弯性能,且随着mn含量的提升,磁性能减弱,因此本发明中mn含量为0.5~0.8%。
[0025]
si:si是固溶强化元素,可显著提高钢材的强度,减小磁阻,使钢更容易发生磁化,
但过高的si含量热轧过程中易于在钢板表面形成2feo
·
sio2(铁橄榄石)氧化皮,热轧除鳞不易去除,si的含量不宜太高,因此本发明中si含量为0.5~0.8%。
[0026]
als:al为脱氧剂,降低钢中的氧含量,减少钢中的夹杂物,提高钢材韧性,但al含量太高易形成粗大的aln粒子,降低钢材的韧性,因此本发明中al含量为0.02~0.05%。
[0027]
p:p为钢中的杂质元素,易于在晶界偏聚,影响产品的韧性与磁性能,因此其含量越低越好,根据实际控制水平与成本因素考虑,控制在0.02%以下。
[0028]
s:s为钢中的杂质元素,易在晶界产生偏聚,且与钢中的fe、mn形成低熔点的硫化物夹杂,应控制在较低的水平,因此控制在0.002%以下。
[0029]
n:n为钢中的杂质元素,降低钢材的韧性,因此尽量降低其含量,应控制在0.005%以下。
[0030]
cu:cu可提高钢材的耐蚀性,cu含量的增加可以增加钢的强度,特别是屈强比,因此本发明中cu含量为≤0.02%。
[0031]
ti:ti可以起到析出强化的作用,细化带钢晶粒,减少带钢的各向异性,且ti可与c形成tic第二相粒子,从而减少钢中固溶和析出的碳化物的含量,但过高的ti含量也使得材料强度的增加以及生产成本的增加,因此本发明中ti的含量为:0.03~0.06%。
[0032]
t[o]:含量高容易形成氧化系夹杂物,因此应降低钢中t[o]的含量,本发明中t[o]≤0.002%。
[0033]
对本发明中主要工艺理由分析如下:
[0034]
采用lf精炼可以降低钢中的s和o含量,降低钢硫化物、氧化物含量,提升产品的韧性。
[0035]
采用rh真空可以降低钢水中c、n、h等元素含量,降低钢中碳化物、氮化物和有害气体含量,提高钢质纯净度,有利于磁性能的提高。
[0036]
热轧采用奥氏体相区轧制,带钢进入精轧机前,处于γ相区,避免终轧温度低于ar3进入两相区,从开始精轧到出精轧都处于奥氏体相区,避免两相区轧制带来的混晶现象。热轧卷取温度600~700℃,高温卷曲有利于热轧板形的控制,避免卷曲温度低带来的板型波动、出现浪型等现象,但太高容易形成粗大晶粒,因此选取600~700℃。
[0037]
酸洗盐酸浓度100~250ml/l,酸洗带速80~150m/min,酸洗温度70~90℃,因钢中添加了一定量的si,si是一种易于形成氧化铁皮元素,适当的酸洗工艺,保证表面氧化铁皮的有效去除。
[0038]
冷轧过程中采用高的冷轧压下率,起到细化钢中的组织作用,有利于保持一定尺寸的晶粒,因此本发明中冷轧总压下率65~80%。
[0039]
冷轧采用五机架轧制,过程中一次压下率为40~50%,可充分细化钢中的组织,在后续四个机架轧制变形较小,获得更好的表面与尺寸精度,因此本发明中一次冷轧压下率40~50%,冷轧出口厚度为0.6~2.0mm。
[0040]
连续退火包括带钢加热、均热、缓冷、快冷、过时效等阶段,其中均热温度800~840℃,缓冷终止温度670~710℃,缓冷速率≤15℃/s,快冷速率≥40℃/s,过时效温度370~430℃。均热温度在800~840℃容易得到均匀的铁素体晶粒组织,晶粒可以充分长大,消除各向异性。
[0041]
本发明采用湿平整工艺,湿平整比干平整工艺平整机的轧制力更小,减少能耗,有
利于钢板屈服平台的消除,且成品表面质量更优。同时采用1.0~2.0%的平整延伸率,最终获得具有良好表面及尺寸精度的磁极钢。
[0042]
与现有技术相比,本发明具有以下优点:
[0043]
(1)本发明提出了一种基于csp工艺的450mpa级磁极钢,产品由铁素体及少量珠光体组成,产品屈服强度rp
0.2
≥450mpa,抗拉强度rm≥520mpa,磁感应强度b50≥1.63t。
[0044]
(2)本发明产品中的采用csp工艺配合可获得更优板型与表面质量的连续退火产线,实现钢材的屈服强度为450mpa的磁极钢产品生产。
[0045]
(3)本发明提出了一种基于csp工艺的450mpa级磁极钢的制造方法,整个生产周期更短,能耗水平更低,有益于生产成本的控制。
附图说明
[0046]
图1为本发明450mpa级磁极钢的典型组织图。
具体实施方式
[0047]
为了使本领域的技术人员更好地理解本发明的技术方案,下面结合具体实施例对本发明的优选实施方案进行描述,但是不能理解为对本专利的限制。
[0048]
下述实施例中所述试验方法或测试方法,如无特殊说明,均为常规方法;所述试剂和材料,如无特殊说明,均从常规商业途径获得,或以常规方法制备。
[0049]
本发明各实施例按照以下步骤生产:
[0050]
主要工艺流程:炼钢
→
lf精炼
→
rh精炼
→
连铸
→
热轧
→
卷取
→
酸洗
→
冷轧
→
连续退火
→
湿平整
→
成品;
[0051]
主要控制工艺参数及结果为:
[0052]
(1)采用脱硫精炼铁水,按预定的成分进行冶炼、铸造成板坯;连铸控制中包钢水过热度为15~35℃,铸坯厚度50~70mm,铸坯拉速4~6m/min;铸坯入均热炉前进行除鳞处理,除鳞水的压力≥210bar;对铸坯进行均热,板坯进轧机前采用高压水除鳞,除鳞水压力≥260bar。
[0053]
(2)将板坯加热后进行热轧,热轧板坯加热温度为1150~1220℃,开轧温度为1030~1080℃,终轧结束温度860~910℃,卷取600~700℃,精轧出口厚度2~6mm。
[0054]
(3)热轧板冷却后经酸洗-连轧机组进行酸洗与轧制,冷轧采用五机架轧制,冷轧压下率为65~80%,机组焊接采用搭接焊焊机;一次冷轧压下率40~50%,轧制出口厚度0.6~2.0mm。
[0055]
(4)在连续退火机组进行退火热处理,其工艺包括带钢加热、均热、缓冷、快冷、过时效等阶段,其中均热温度800~840℃,缓冷终止温度670~710℃,缓冷速率≤15℃/s,快冷速率≥40℃/s,过时效温度370~430℃。控制退火炉内露点-20~-50℃,炉内氢气含量h2在3~10%,残氧1~20ppm。
[0056]
(5)平整压下率1.0~2.0%,根据成品厚度设定对应平整延伸率:成品厚度≤1.2mm时,平整延伸率1.0~1.4%;成品厚度>1.2mm时,平整延伸率1.4~2.0%。
[0057]
表1本发明各实施例及对比例的化学成分列表(wt%)
[0058]
序号csimnalsnpscutit[o]
实施例10.0570.770.580.0260.00420.0120.00110.0160.0400.0015实施例20.0510.680.770.0290.00360.0110.00120.0130.0360.0013实施例30.0480.710.740.0280.00350.0120.00120.0150.0380.0014实施例40.0620.590.760.0270.00370.0090.00150.0150.0450.0016实施例50.0390.730.790.0280.00360.0140.00130.0180.0480.0011
[0059]
表2本发明各实施例主要工艺参数列表
[0060][0061]
表3本发明各实施例力学性能检测结果列表
[0062][0063]
从表3中实施例1-5可以看出,本发明生产出的磁极钢屈服强度rp
0.2
≥450mpa,抗拉强度rm≥520mpa,磁感应强度b50≥1.63t,上述性能均达到目标,同时不同成品厚度的钢板(0.6~2.0mm),性能保持稳定,图1为本发明的典型组织。
[0064]
以上仅是本发明的优选实施方式,应当指出的是,上述优选实施方式不应视为对本发明的限制,本发明的保护范围应当以权利要求所限定的范围为准。对于本技术领域的普通技术人员来说,在不脱离本发明的精神和范围内,还可以做出若干改进和润饰,这些改进和润饰也应视为本发明的保护范围。
再多了解一些
本文用于创业者技术爱好者查询,仅供学习研究,如用于商业用途,请联系技术所有人。