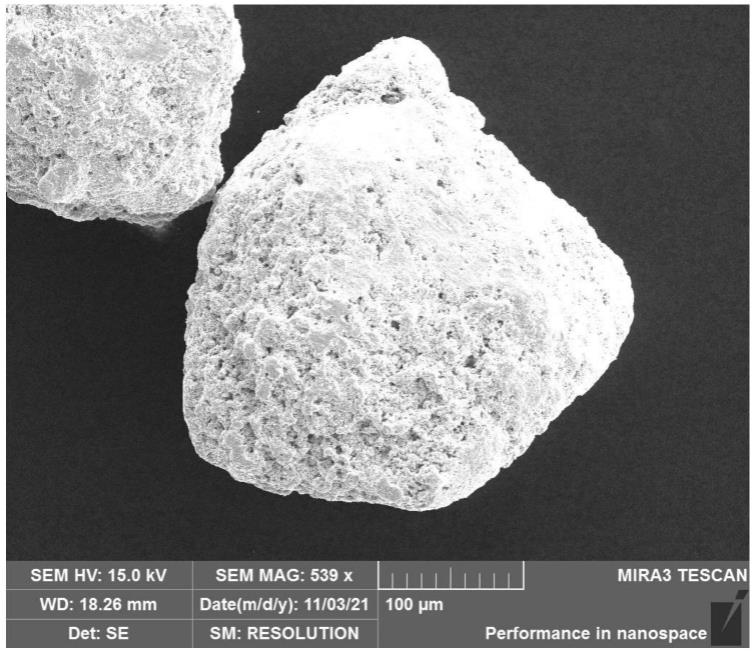
1.本发明属于涂层的制备和应用技术领域,具体涉及一种基于表面高硬度凸点强化的高耐磨超疏水涂层及其大面积制备方法。
背景技术:
2.人工超疏水涂层在防腐、防覆冰、自清洁、减阻、油水分离等诸多领域具有广阔应用前景。受荷叶效应的启发,人们通过对植物叶子表面超疏水性的系统研究,发现表面既有微纳尺度的粗糙结构,又被低表面能物质覆盖是具备超疏水性能的必要充分条件。目前的研究表明,这种超疏水表面不仅具有自清洁功能,还具有防腐及防止生物附着、防覆冰、防雾及防霜冻等特殊功能,因此在海洋舰船及海洋平台表面防护、电力输送户外设备及线路,建筑等领域具有广阔的应用前景。
3.然而,超疏水涂层的实际应用主要受制于两个因素。第一,超疏水涂层的抗机械损伤能力尤其是耐磨性能较差,人工超疏水表面所需的微纳尺度粗糙结构在受到服役环境中的外来物体接触、碰撞、弯曲、特别是摩擦作用时,自身结构的损坏会导致超疏水特性的下降甚至消失。第二,现有的超疏水涂层制备的工艺方法中,气相沉积、电镀、化学镀、自组装等为代表的自下而上的制备工艺需要昂贵而复杂的精密设备,成本较高,制备周期较长,部分工艺中溶液(金属离子)的使用增加了环境污染的风险。并且绝大多数的工艺方法均要在溶液、真空条件下实现微纳尺度粗糙结构的制备,难以大面积制备,不具备应用前景,使得人工超疏水表面目前还难以走出实验室,实现大规模的成功应用。因此,基于开发出既能提高超疏水表面微纳尺度粗糙结构的抗机械损伤性能,又能大面积绿色制备的超疏水涂层工艺需求,雒晓涛等人提出一种采用冷喷涂技术在材料表面制备具有柔性结构的金属微纳尺寸结构的工艺,利用外部物体碰触或摩擦表面时,柔性结构的可变形性可保证微纳尺寸粗糙结构的完整性,该方法制得的涂层与常规人工超疏水涂层相比,具有柔性结构超疏水涂层的耐磨性能显著提升,但是该方法制备得到的涂层在摩擦磨损等测试中依然难以满足工业应用需求。
技术实现要素:
4.为了克服上述现有技术的缺点,本发明的目的在于提供一种基于表面高硬度(硬度≥650hv)凸点强化的高耐磨超疏水涂层及其大面积制备方法,能够有效解决现有技术的超疏水涂层耐磨性能差的技术问题。
5.为了达到上述目的,本发明采用以下技术方案予以实现:
6.本发明公开了一种基于表面高硬度凸点强化的高耐磨超疏水涂层,该超疏水涂层表面分布有少量的高硬度凸点结构和大面积的具有微纳尺度的粗糙结构,其中,高硬度凸点结构在工件表面的覆盖率为8%~35%,具有微纳尺度的粗糙结构在工件表面的覆盖率为70%~92%,二者覆盖率之和为100%。
7.本发明还公开了上述的基于表面高硬度凸点强化的高耐磨超疏水涂层的大面积制备方法,包括以下步骤:
8.1)采用喷涂法在待制备涂层的金属工件表面制备弥散分布的高硬度凸点结构;
9.2)在经步骤1)处理后的工件表面采用喷涂法制备具有微纳尺度的粗糙结构;
10.3)对步骤2)得到的涂层表面进行低表面能物质修饰,即在工件表面制备得到基于表面高硬度凸点强化的高耐磨超疏水涂层。
11.优选地,高硬度凸点结构的高度在30~800μm之间,具有微纳尺度的粗糙结构的厚度在5~50μm之间,高硬度凸点结构的高度为具有微纳尺度的粗糙结构厚度的1.5倍以上。
12.优选地,高硬度凸点结构的水平尺寸介于50~300μm之间,高硬度凸点结构之间的间距为直径的2~10倍之间。
13.优选地,制备高硬度凸点结构采用的原料为氧化铝陶瓷粉末、氧化铝钛陶瓷粉末、碳化硅陶瓷粉末、wc-co系陶瓷粉末或nicr-crc系陶瓷粉末,选用原料的维氏硬度值≥650hv,粉末的粒径介于50-300μm之间。
14.优选地,制备具有微纳尺度的粗糙结构采用的原料为氧化铝陶瓷粉末、氧化铝钛陶瓷粉末、碳化硅陶瓷粉末、wc-co系陶瓷粉末、nicr-crc系陶瓷粉末,且上述陶瓷粉末均经过团聚及烧结处理;团聚是指将纳米或亚微米级原始粉末微粒通过胶黏剂进行黏结,形成数微米到数十微米尺度的大尺寸颗粒。进一步通过烧结可去除胶黏剂,同时通过扩散烧结作用使原始纳米或亚微米级微粒实现化学结合,但整个大尺寸颗粒的外表仍然能看出原始纳米或亚微米尺寸轮廓。即得到宏观为数十到百微米量级的颗粒,颗粒表面有纳米尺寸粗糙结构。
15.或者,选择以纳米或亚微米团聚烧结的金属钼粉末、金属钨粉末、金属钽粉末或者电解方法制备的金属镍粉末;
16.其中,所选原料的粉末粒径介于5~50μm之间。
17.优选地,步骤1)中,制备高硬度凸点结构的喷涂方法有火焰喷涂、等离子喷涂;所喷涂的陶瓷粉末或金属陶瓷粉末处于表层熔化、内部不熔化的状态,使得陶瓷粉末或金属陶瓷粉末在工件表面撞击、凝固后形成高度满足要求的高硬度凸点结构,高硬度凸点结构在工件表面的覆盖率通过粉末输送速率和喷枪扫描速度调控;
18.所述陶瓷粉末或金属陶瓷粉末为多角形形貌,使得喷涂过程中粉末在固态高速碰撞时嵌入工件的金属基材表面,形成高度满足要求的高硬度凸点结构。
19.优选地,步骤2)中,制备具有微纳尺度的粗糙结构的喷涂方法有火焰喷涂、超音速火焰喷涂,所喷涂的团聚后陶瓷粉末或金属陶瓷粉末处于表层微熔化状态,使得团聚粉末内部的原始微纳尺寸结构得以保留,在工件表层形成具有微纳尺度的粗糙结构。
20.优选地,步骤3)所述的低表面能物质修饰是采用聚氨酯、氟硅烷或硬脂酸对涂层表面进行修饰。
21.优选地,在步骤1)喷涂之前,还包括对待制备涂层的金属工件表面进行清洗与除油处理的操作。
22.与现有技术相比,本发明具有以下有益效果:
23.本发明公开的基于表面高硬度凸点强化的高耐磨超疏水涂层,主要由两部分构成,一部分是离散分布(少量)的高硬度凸点结构,另一部分是大面积涂覆地具有微纳尺度
地粗糙结构层。具有微纳尺度的粗糙结构使得金属工件的表面具有疏水性能,当外部物体摩擦涂层表面时(如受到服役环境中的外来物体接触、碰撞、弯曲及摩擦),高硬度凸点结构则能起到保护微纳尺度的粗糙结构不被破坏的作用,使得涂层疏水性能不因磨损而退化,因此表面超疏水性得以保留,从而有效解决了现有技术的超疏水涂层耐磨性能差的技术问题。
24.本发明还公开了上述基于表面高硬度凸点强化的高耐磨超疏水涂层的制备方法,优点体现在:1)高硬度凸点结构和具有微纳尺度的粗糙结构层的原材料选择灵活,因此可以根据实际服役环境的需要选择合适的材料;2)采用冷喷涂与热喷涂的方法制备超疏水涂层,涂层与基体的结合力更强,不用担心涂层剥落的情况发生;3)采用喷涂法(冷喷涂和热喷涂均可)制备超疏水涂层,几乎适用于所有材质的基材,对基材表面质量要求低。
附图说明
25.图1为高耐磨金属陶瓷颗粒表面形貌;
26.图2为具有微纳双尺度粗糙结构的金属粉末表面形貌;
27.图3为高硬度硬质合金凸点强化超疏水涂层原理示意图;
28.图4为经冷喷涂制备的超疏水涂层表面形貌;
29.图5为经过摩擦磨损实验之后的涂层表面形貌。
具体实施方式
30.为了使本技术领域的人员更好地理解本发明方案,下面将结合本发明实施例中的附图,对本发明实施例中的技术方案进行清楚、完整地描述,显然,所描述的实施例仅仅是本发明一部分的实施例,而不是全部的实施例。基于本发明中的实施例,本领域普通技术人员在没有做出创造性劳动前提下所获得的所有其他实施例,都应当属于本发明保护的范围。
31.需要说明的是,本发明的说明书和权利要求书及上述附图中的术语“第一”、“第二”等是用于区别类似的对象,而不必用于描述特定的顺序或先后次序。应该理解这样使用的数据在适当情况下可以互换,以便这里描述的本发明的实施例能够以除了在这里图示或描述的那些以外的顺序实施。此外,术语“包括”和“具有”以及他们的任何变形,意图在于覆盖不排他的包含,例如,包含了一系列步骤或单元的过程、方法、系统、产品或设备不必限于清楚地列出的那些步骤或单元,而是可包括没有清楚地列出的或对于这些过程、方法、产品或设备固有的其它步骤或单元。
32.下面结合附图对本发明做进一步详细描述:
33.实施例1:以烧结破碎法制备的具有多角形特征、粒径介于80~200μm之间的wc10co4cr金属陶瓷粉末,如图1所示。以及具有微纳尺度粗糙结构的粒径介于5~50μm之间的纳米粉体烧结团聚的w粉为喷涂粉末如图2所示。以铝合金作为基材,表面无需喷砂。首先对铝合金基材表面进行清洗,除去表面杂质油污等。之后在气体压力为4.5mpa,气体温度为600℃,喷枪扫描速度为800mm/s,送粉速率为0.5r/s,喷枪距离为30mm的条件下对铝合金基材表面冷喷涂制备wc
10
co4cr涂层,与冷喷涂制备连续涂层相比,在较低的送粉速率和较高的喷枪扫描速度下,扫描电镜表征结果表明:wc10co4cr高硬度凸点在基材表面覆盖率为
15%,平均间距约为0.45mm,约为凸点直径的2~5倍。激光共聚焦显微镜表征结果表明:wc10co4cr高硬度凸点的高度约为60~160μm之间。其次以气体压力为3.5mpa,气体温度500℃,喷枪扫描速度800mm/s,喷枪距离30mm,送粉速率1.5r/s条件下冷喷涂制备w层,由于烧结团聚粉末的表面呈现为纳米尺度w粉单元,且烧结粉末自身为微米尺度,因此扫描电镜表征结果显示该层具有微纳双尺度结构且覆盖除硬质凸点的其他所有区域。图3概念性的表示了该种结构。最后,采用聚氨酯有机溶液喷雾的方式对涂层进行低表面能物质修饰。待有机溶剂在室温下2h挥发完后,涂层即具有疏水性能。接触角测试结果显示涂层的疏水角为157
°
,滚动角仅为1
°
。在400g的作用载荷下,于400#的碳化硅砂纸上直线移动220mm然后回到原位置为一个工作周期(涂层面积为25cm2),以每五次磨损循环为步长测量滚动角和静态接触角,在300周次摩擦循环之后,测量静态接触角能否保持在150
°
以上且滚动角不大于2
°
(依然具有超疏水性)。采用中性盐雾腐蚀对该涂层的耐腐蚀性能进行测试,由于超疏水特性以及涂层材质均为耐腐蚀材料,500h盐雾腐蚀后,涂层依然完整,表面未出现鼓包,开裂或者剥落现象。
34.实施例2:以粒径介于150~300μm之间的氧化铝粉末和具有微纳尺度粗糙结构的粒径介于15~45μm之间的纳米团聚氧化铝粉末为喷涂原料,以45#碳钢为基材,表面无需喷砂。首先对碳钢基材表面进行清洗,除去表面杂质油污等。首先,以粒径介于150~300μm之间的氧化铝粉末为喷涂原料,采用等离子喷涂方法,在喷涂功率为30kw,喷嘴直径为10mm,ar流量为40slm,h2流量为5slm的条件下,使得上述大粒径氧化铝粉末处于半熔化状态,在表面沉积时获得高硬度凸点。通过控制送粉速率为0.5rpm,喷枪扫描速度为800mm/s,喷枪距离为80mm的条件下在碳钢基材表面制备弥散分布的氧化铝凸点,扫描电镜表征结果表明:氧化铝高硬度凸点在基材表面覆盖率为13%,平均间距约为0.52mm,约为凸点直径的3-7倍。激光共聚焦显微镜表征结果表明:氧化铝高硬度凸点的高度约为105-220μm之间,略小于原始粉末直径。其次,以粒径介于15~45μm之间的纳米团聚氧化铝粉末为喷涂原料,选用氧乙炔火焰喷涂技术,在氧气流量为7slm,乙炔流量为20slm的参数条件下,使得该粉末处于半熔化状态,在喷枪扫描速度为300mm/s,喷枪距离100mm,送粉速率1.0rpm条件下制备具有微纳尺度的氧化铝层,由于半熔化团聚氧化铝粉末的表面呈现为纳米尺度氧化铝纳米单元,且半熔化粉末颗粒自身为微米尺度,因此扫描电镜表征结果显示该层具有微纳双尺度结构且覆盖包括硬质凸点的所有区域,如图4所示最后,采用聚氨酯有机溶液喷雾的方式对涂层进行低表面能物质修饰,待有机溶剂在室温下2h挥发完后,涂层即具有疏水性能,由于所有面积均被微纳尺度粗糙结构覆盖,因此接触角测试结果显示涂层的疏水角为164
°
,滚动角仅为1
°
。在400g的作用载荷下,于400#的碳化硅砂纸上直线移动220mm然后回到原位置为一个工作周期(涂层面积为25cm2),以每五次磨损循环为步长测量滚动角和静态接触角,在500周次摩擦循环之后,测量静态接触角能否保持在152
°
以上且滚动角不大于2
°
,依然具有超疏水性。图5为经过摩擦磨损实验之后的扫描电镜对试样表面的表征结果。在圆片试样的所有面均制备涂层,采用3.5wt.%nacl水溶液腐蚀浸泡试验在室温下对该涂层的耐腐蚀性能进行测试,由于超疏水特性以及涂层材质均为耐腐蚀材料,3个月后,涂层表面无锈点,涂层未出现鼓包、开裂或者剥落等现象。
35.以上内容仅为说明本发明的技术思想,不能以此限定本发明的保护范围,凡是按照本发明提出的技术思想,在技术方案基础上所做的任何改动,均落入本发明权利要求书
的保护范围之内。
再多了解一些
本文用于创业者技术爱好者查询,仅供学习研究,如用于商业用途,请联系技术所有人。