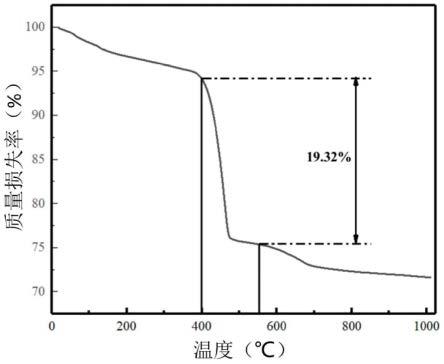
1.本发明涉及c04b28技术领域,尤其涉及一种利用钙基固废固定二氧化碳的方法及其应用。
背景技术:
2.随着城市化、工业化进程的加速,二氧化碳的资源化利用与产业化发展已成为社会亟需解决的问题。伴随着城市规模扩大、人口膨胀,垃圾处理的速度已远远赶不上垃圾废品的排放速度,而低碳技术作为从根源上解决碳排放问题的关键技术,已经成为当前背景下最优异的解决方案。
3.现有建材领域所采用的主要低碳化方法为矿化,比如中国专利申请文献cn113087484a提供了一种固废电石泥钢渣新型绿色环保碳化砖的制备方法,对固体废弃进行破碎、球磨、过筛处理,按照一定的配方进行混合并压制后进行碳化,碳化温度在60-80℃。中国专利cn109970378b提供了一种基于协同理论及碳化/高温技术的固废基胶凝材料制备工艺的方法,原材料通过粉磨、烘干处理后,按照一定的配方混合后进行压制,碳化温度在60℃以上,这部分热量提高了整个工艺的碳排放。
4.可见,现有技术中的碳化反应多在加热条件下进行。而实际的碳化反应中,二氧化碳与固废中可矿化钙反应是放热反应,但现有的固碳技术不仅未能利用放热的矿化反应产生的热量,还需要额外加热值温度进行反应,这无疑是对能源的巨大浪费。因此,本技术中提供一种新的方法,在无需外加热源的情况下完成二氧化碳的固定,并同时将矿化反应产生的热量进行合理利用。
技术实现要素:
5.本发明通过提供一种利用钙基固废固定二氧化碳的方法,解决了现有固废利用率低,再生合成的制品的综合性能差,无法满足实际应用需求的技术问题,通过简便可行的再生工艺手段,制得强度优异、固碳性能良好的建材制品,在节约能源消耗的同时实现了co2的高效利用。
6.本发明第一方面提供了一种利用钙基固废固定二氧化碳的方法,通过调节反应装置中的坯体填充,控制矿化反应程度;利用矿化反应放出的热量使体系中的水分变为水蒸气,进而发生水热反应。
7.发明人在完成本发明的过程中发现,通过调节反应装置中的坯体填充,可以将矿化反应放出的热量控制在一定范围内,在满足矿化反应自身所需温度的同时,还可将坯体中的水分变为水蒸气,使体系满足水热反应所需条件,从而在无需外加热源和水蒸气的条件下实现复合矿化反应(既发生矿化反应,又发生水热反应),从而充分利用此前的研究中被忽略的矿化反应热。
8.在一些优选的实施方式中,所述利用钙基固废固定二氧化碳的方法将固体废弃物转化为建筑制品。
9.在一些优选的实施方式中,所述利用钙基固废固定二氧化碳的方法包括如下步骤:
10.s1.使用钙基固废制备坯体;
11.s2.将坯体与含co2气体接触,在在无外加热源和水源的条件下,进行复合矿化反应(所谓复合矿化反应是指并非单纯进行矿化反应,在本体系中,既发生矿化反应,也发生水热反应)。
12.在一些优选的实施方式中,所述s1步骤包括:通过调节反应装置中的坯体填充,控制矿化反应程度;利用矿化反应放出的热量使体系中的水分变为水蒸气,进而发生水热反应。
13.在具体实施方式中,可以采用将混合料压制成型的方式,也可以采用浇筑成型的方式。
14.进一步优选,所述压制过程中压实压力为5-100mpa。
15.在一些优选的实施方式中,所述利用钙基固废固定二氧化碳的方法满足:m>
16.[h 3.593*v*105/t0 4.446*v*106(p-37.315/t0)-4.356*p 2.344*108/(373.15-t0)]/[1.538*109*a*k/(373.15-t0) 2.344*10
11
/(373.15*ρ*v-t0*ρ*v) 3.593*108/(t0*ρ) 4.446*109*(p-37.315/t0)/ρ-1.321*10
6-4.1*105*a-9.86*105*a*k];
[0017]
其中m为坯体的质量,h为反应装置的热容,v为反应装置的体积,ρ为坯体的真密度(真密度(true density)指材料在绝对密实的状态下单位体积的固体物质的实际质量,即去除内部孔隙或者颗粒间的空隙后的密度),t0为反应初始温度,p为反应压力,a为混合料中cax的质量分数,k为经验反应常数。
[0018]
所述其中mi为反应装置中釜体各组成部分对应材料的质量m1、m2、m3…mn
,ci为反应装置釜体各材料对应的比热容c1、c2、c3…cn
。
[0019]
其中反应装置的材料由釜体及保温材料构成,其中釜体材料可以是碳锰钢、不锈钢、锆、镍基(哈氏、蒙乃尔)合金及其它复合材料等其中的一种或一种以上;保温材料可以是稀土保温材料、岩棉、无机硅酸盐浆料、新型无机保温材料、聚苯板、聚氨酯发泡材料、玻璃棉、硅酸铝棉等其中的一种或一种以上。
[0020]
在一些优选的实施方式中,m同时满足如下条件中的至少1个:
[0021]
(1)m<0.5*ρ0*v*10-3
;
[0022]
(2)
[0023]
m<[h 3.593*v*105/t0 4.446*v*106(p-47.315/t0)-3.435*p 2.344*108/(473.15-t0)]/[1.538*109*a*k/(473.15-t0) 2.344*10
11
/(473.15*ρ*v-t0*ρ*v) 3.593*108/(t0*ρ) 4.446*109*(p-47.315/t0)/ρ-1.321*10
6-4.1*105*a-9.86*105*a*k];
[0024]
其中ρ0为坯体的表观密度;k为0.7~1;优选为0.84~1。
[0025]
进一步优选,m需同时满足条件(1)和(2)。
[0026]
其中:m为建材预制品的质量,单位为t,h为反应釜的热容,单位为j/k;v为反应釜的体积,单位为m3;ρ0为建材预制品的真密度(真密度(true density)指材料在绝对密实的状态下单位体积的固体物质的实际质量,即去除内部孔隙或者颗粒间的空隙后的密度),单位为kg/m3;t0为反应初始温度,单位为k;p为反应压力,单位为mpa;a为反应原料中钙基成分的质量分数(本技术实施例中为氢氧化钙的总质量分数),单位为%;k为经验反应常数,单
位为1。
[0027]
在一些优选的实施方式中,所述s2步骤中将坯体与含co2气体接触时,先将坯体放入反应装置中,反应装置的填充率为5.00-55.00%;进一步优选为20.00-50.00%。其中,填充率是指坯体填充占反应釜体积的比例。
[0028]
本技术经过大量实验探究发现,通过控制反应装置中的坯体填充调控反应装置中的矿化反应程度,通过矿化反应放热可使体系温度达到水热反应所需温度,无需外加热源,无需额外通入水蒸气,节省大量能源并减少碳排放,能够实现co2的有效利用。进一步的,当控制反应装置的填充率为5.00-55.00%时,所制得的成品砖既具有较高的固碳率,同时具有优异的机械强度,而当填充率过高或过低时,或制品对co2的吸收效率降低,或制品强度无法满足应用需求,或固碳率和机械强度同时不达标。
[0029]
在一些优选的实施方式中,所述反应压力p为0.01-2.0mpa;优选的,p为0.05-1.0mpa。
[0030]
在一些优选的实施方式中,所述s2步骤的反应时间t为0.5-10h;优选的,t为1-8h。
[0031]
在一些优选的实施方式中,所述s1步骤中固废混合料与水的固液比为100:(2-40)。
[0032]
进一步优选,所述固废混合料与水的固液比为100:(5-30)。
[0033]
在一些优选的实施方式中,所述钙基固废中cax的质量分数>80%;cax包括ca(oh)2,cao,caco3,caso4,ca5(po4)3f中的至少一种;优选的,cax包括ca(oh)2和cao中的至少一种。
[0034]
作为钙基固体废弃物的实例,包括但不限于电石渣、白泥、飞灰等。
[0035]
作为硅铝质固体废弃物的实例,包括但不限于粉煤灰、底灰、红泥、建筑垃圾、废旧水泥、尾矿、矿石原料等。
[0036]
在一些优选的实施方式中,所述含co2气体中co2的体积分数为5-98%。
[0037]
本发明第二方面提供了一种如上所述的利用钙基固废固定二氧化碳的方法在建筑材料领域的应用。
[0038]
有益效果:
[0039]
本技术提供的利用钙基固废固定二氧化碳的方法具有以下优点:
[0040]
1.本技术提供的方法能够充分利用钙基固废固定二氧化碳时产生的大量反应热,与工业来源的含co2气体协同制备出性能优异的建材制品,所得建材制品的固碳性能优异,且物理机械性能良好;该方法极大程度上降低了固废处置成本,既解决了大宗固废的处理处置问题,又解决了现有高碳行业co2的利用有效率低的问题,具有极高的推广和应用价值;
[0041]
2.在利用钙基固废固定二氧化碳的方法中,通过控制反应装置中的坯体填充调控反应装置中的矿化反应程度,有序控制反应体系温度,在无外加热源的基础上提升了矿化反应效率,使环境温度一方面能满足矿化反应的最佳条件,另一方面使体系内发生水热反应提升制品性能。既减少了原材料损耗,还有效提高了工业生产效率,同时赋予了制品良好的固碳率及强度性能;
[0042]
3.本技术在调控反应装置中坯体填充的同时,进一步确定了适宜的反应条件,经过大量实验探究,发现在一定坯体填充的条件下,能够最大程度上平衡矿化反应和水热反
应;以纯大宗固废为原材料,配合含co2气体直接进行矿化养护,在简便的操作工艺下高效制成性能优异的建材制品,有效实现工业固废的高效资源化利用;
[0043]
4.本技术制备得到的建材产品在保证强度满足需求同时具有极高的经济、环保属性,其相比于传统的硅酸盐水泥制品,真正做到了“负碳”生产,可为建筑行业低碳化提供一种全新、可行的发展思路。
附图说明
[0044]
下面结合附图和实施例对本技术进一步说明。
[0045]
图1是电石渣的tg图;
[0046]
图2是本技术实施例2和实施例6所得成品砖的固碳率对比。
具体实施方式
[0047]
本技术实施例中所用原料及反应装置信息如下:
[0048]
(1)原料
[0049]
钙基固废:选取某煤化工厂电石渣作为碳化材料。
[0050]
硅铝质固废:某煤化工厂粉煤灰作为辅助材料,某建材厂建筑垃圾再生骨料作为骨料;将各原料进行xrf分析,其化学成分和其重量百分比信息见表1-3;
[0051]
所述电石渣的含水率为31.73%,粉煤灰的含水率为2%,建筑垃圾再生骨料的含水率为1%。
[0052]
含co2气体:选取来自于合肥某盐煤化工厂的尾气,其气体组成及其体积百分比见表4。
[0053]
表1电石渣的主要元素组成
[0054][0055]
表2粉煤灰的主要元素组成
[0056][0057]
表3再生骨料的主要元素组成
[0058][0059]
表4合肥某盐煤化工厂所产出的尾气气体组成(体积分数)
[0060]
气体组成co2n2soxnoxvocs煤化工尾气76.5%18.9%2.3%2%0.3%
[0061]
(2)部分条件
[0062]
反应釜参数为:反应釜的体积v为178m3,钢材厚度10mm,钢材密度为7950kg/m3,保温岩棉厚度100mm,岩棉的密度120kg/m3,反应装置的热容h为23345514j/k,坯体的真密度与表观密度可以近似为1700kg/m3。初始反应温度为298.15k,电石渣的氢氧化钙含量为15%(上述表格中cao与ca(oh)2存在转化关系,其中坯体中含有27.66%的电石渣,其含水率为31.73%,则绝干的电石渣的含量18.88%,图1为电石渣的tg图,其中400-550℃处对应的质量减少量代表氢氧化钙分解后水的质量,其占比为19.32%,则氢氧化钙占电石渣的比例为19.32%/18*74=79.43%,故氢氧化钙占坯体的百分比含量为15.00%,即a为15.00%)(其中硅铝质固废(骨料及辅助材料)中ca0为惰性碳酸钙,不参与反应,因此仅计算电石渣中活性钙成分),经验反应常数k为1。
[0063]
将上述参数带入公式可得:29.16t<m<151.94t。
[0064]
实施例1.
[0065]
本实施例提供了一种利用钙基固废固定二氧化碳的方法,具体包括如下步骤:
[0066]
s1.将钙基固废、硅铝质固废与水混合,得到混合料,将混合料放入模具中压制形成坯体;
[0067]
s2.将坯体与含co2气体接触,在无外加热源和水蒸气的条件下,进行混合固碳反应复合矿化反应。
[0068]
所述s1步骤具体为:按照重量百分比计,将27.66%电石渣和32.56%粉煤灰,32.56%再生料混合,加入7.22%的水得到混合料,其中混合料的总重为15.1t,将混合料送入粉混系统,搅拌至混合料混合均匀,然后将粉混后的物料送入消解系统消解40分钟;消解后的物料送入机械成型系统,并压制成块体,压实压力为11.5mpa,压制得到砖型为200mm*95mm*53mm的坯体,用机器人码垛在摆渡车上;
[0069]
所述s2步骤具体为:将s1步骤压制成型的坯体送入反应装置中,控制反应装置的填充率为5.00%;关闭反应装置的门并通入含co2气体进行反应,反应的初始温度为室温(25℃),总体反应时间为6h,釜内压力为0.6mpa,反应完成后得成品砖。
[0070]
实施例2.
[0071]
本实施例提供了一种利用钙基固废固定二氧化碳的方法,具体实施方式同实施例1;不同点在于,混合料的总重为30.39t,坯体送入反应装置后反应装置的填充率为10.00%。
[0072]
实施例3.
[0073]
本实施例提供了一种利用钙基固废固定二氧化碳的方法,具体实施方式同实施例1;不同点在于,不同点在于,混合料的总重为45.58t,坯体送入反应装置后反应装置的填充率为15.01%。
[0074]
实施例4.
[0075]
本实施例提供了一种利用钙基固废固定二氧化碳的方法,具体实施方式同实施例1;不同点在于,不同点在于,混合料的总重为60.77t,坯体送入反应装置后反应装置的填充率为20.00%。
[0076]
实施例5.
[0077]
本实施例提供了一种利用钙基固废固定二氧化碳的方法,具体实施方式同实施例1;不同点在于,不同点在于,混合料的总重为75.97t,坯体送入反应装置后反应装置的填充率为25.00%。
[0078]
实施例6.
[0079]
本实施例提供了一种利用钙基固废固定二氧化碳的方法,具体实施方式同实施例1;不同点在于,不同点在于,混合料的总重为91.16t,坯体送入反应装置后反应装置的填充率为30.00%。
[0080]
实施例7.
[0081]
本实施例提供了一种利用钙基固废固定二氧化碳的方法,具体实施方式同实施例1;不同点在于,不同点在于,混合料的总重为121.55t,坯体送入反应装置后反应装置的填充率为40.00%。
[0082]
实施例8.
[0083]
本实施例提供了一种利用钙基固废固定二氧化碳的方法,具体实施方式同实施例1;不同点在于,不同点在于,混合料的总重为136.74t,坯体送入反应装置后反应装置的填充率为45.00%。
[0084]
实施例9.
[0085]
本实施例提供了一种利用钙基固废固定二氧化碳的方法,具体实施方式同实施例1;不同点在于,不同点在于,混合料的总重为151.94t,坯体送入反应装置后反应装置的填充率为50.00%。
[0086]
实施例10.
[0087]
本实施例提供了一种利用钙基固废固定二氧化碳的方法,具体实施方式同实施例1;不同点在于,不同点在于,混合料的总重为167.13t,坯体送入反应装置后反应装置的填充率为55.00%。
[0088]
性能测试方法
[0089]
1.固碳率测试
[0090]
固碳率的测试步骤具体为:
[0091]
1)取实施例1-10中制备得到的成品砖体积的1/8,全部破碎成粉,进行整体固碳率测试;
[0092]
2)利用破碎机对整体固碳率测试用的粉状样品进行破碎,破碎后取50g的样品,在105℃烘箱中烘干12h,烘干时不抽真空,保持烘箱密闭,并在烘箱中放置一大烧杯的naoh颗粒;烘干后,取出5g样品,在研钵中磨细至没有颗粒感(约1-2分钟即可),装在小自封袋中;小自封袋放在大袋中,并在大袋中放硅胶干燥剂。
[0093]
3)将制备的样品放入样品仓内,设置实验氛围为n2,温度范围为室温至1000℃,升温速率10℃/min。采用德国耐弛(netzsch)公司制造的sta409ep综合热分析仪进行测试分析;
[0094]
4)测试结束得到tg/dtg热重分析曲线
[0095]
注:本专利以co2的吸收率来评价样品的吸碳效果,其为固废吸收co2质量占试块质量的百分比例,固体废弃物吸收co2的含量是通过测试矿化产物的tg/dtg热重分析曲线所
得,矿化制品吸收二氧化碳的含量为605-820℃的质量减少量,试块的质量为矿化产物在105℃的质量。
[0096]
2.抗压强度测试
[0097]
抗压强度按照gbt4111-2013《混凝土砌块和砖试验方法》测得,将实施例1-8制得的成品砖自然气干24h后测定强度。其具体操作如下:抗压实验使用ye-30型液压式压力实验机,每个成品砖设置5个平行样品测得抗压强度的平均值。如果所测得的样品抗压强度值与平均值的差不大于15%,则用该平均值作为抗压强度;如果有某测定值与平均值之差大于15%,则将此值舍去,以其余的值计算平均值;如果有2个以上的测定值与平均值之差大于15%,则重新进行实验。
[0098]
抗压强度可用下式计算:σd=p1/f=4p/πd2=p/0.875d2[0099]
式中σd为抗压强度,kgf/cm2;p1为压碎负荷,kgf;d为颗粒试样平均直径,cm。
[0100]
性能测试数据
[0101]
表5.实施例1-10制得的成品砖的性能测试结果
[0102] 抗压强度(mpa)固碳率(%)实施例15.134.09实施例26.234.41实施例37.275.67实施例48.217.03实施例59.328.58实施例610.4710.40实施例713.7210.70实施例816.4111.13实施例917.318.17实施例1016.114.13
[0103]
从表5可知,当实施例2-9中坯体质量在根据本技术公式计算结果(29.16<m<151.94)范围内时,所得成品砖的抗压强度可达到6.23-17.31mpa,固碳率可达到4.41-11.13%,可以在获得较高抗压强度的同时具有较高的固碳率。而当实施例1的坯体质量为15.19t,低于按本技术公式计算结果范围时,所得成品砖的抗压强度为5.13mpa,固碳率为4.09%,均较低。当实施例10的坯体质量为167.13t,高于按本技术公式计算结果范围时,所得成品砖的抗压强度虽然达到16.11mpa,但固碳率仅为4.13%。说明按本技术公式计算可获得能够制得抗压强度和固碳率均较优的坯体质量,在已确定固废组成的情况下,配合反应釜的选择,可根据本技术的公式计算获得坯体质量,从而获得抗压强度和固碳率都更优的成品砖。
[0104]
如表5结果所示,实施例1反应装置的填充率和坯体质量较低,所得成品砖的强度及固碳率较低。实施例2-6的固碳率随着填充率和坯体质量的提高迅速提高,而实施例6-8随着填充率和坯体质量的上升固碳率提升逐渐变缓;实施例2-6的成品砖的强度随着固碳率的提升上升缓慢,而实施例6-8随着填充率和坯体质量的上升试块的强度迅速提升;主要原因是随着填充率增加,使得反应釜中的温度上升,致使反应装置中co2扰动较大,使得co2与钙基固废接触几率较大,进而增加了产品的固碳率,但由于在反应装置中的填充率和坯
体质量较低时,反应装置的温度较低,使得此时矿化反应占主导,水热反应较少,产物多为碳酸钙,对产品的强度贡献较低;但当填充率和坯体质量达到一定程度,反应釜的温度升高到一定程度,此时钙质固废与硅铝质发生大量水热反应,生成较多的csh凝胶,使得产品的强度进一步提高。实施例9-10随着填充率和坯体质量的提升,试块固碳迅速下降,试块的强度下降。主要原因是随着填充率和坯体质量的进一步提升,使得反应初期矿化程度较高,反应釜升温较快达到一定温度,使得剩余大量的氢氧化钙及氧化钙与硅铝质发生水热反应生成大量csh,过量的水热反应无法形成稳定的晶状结构导致强度下降,同时可矿化的氢氧化钙及氧化钙迅速减少使得固碳率迅速下降。
再多了解一些
本文用于创业者技术爱好者查询,仅供学习研究,如用于商业用途,请联系技术所有人。