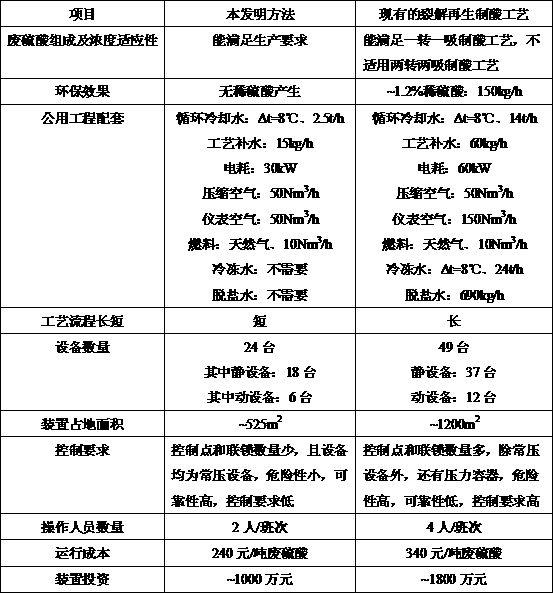
1.本发明涉及一种工业磺化废硫酸资源化利用的装置及方法,属于废硫酸治理领域。
背景技术:
2.工业磺化废硫酸主要产自精细化工企业,绝大部分企业的废硫酸产量较小,年产量主要集中在1000~2000吨之间,且这些企业分布零散,无法集中统一处理,存在偷排和污染转移问题。磺化工艺通常采用发烟硫酸作为磺化剂,硫酸仅作为溶剂和传热介质,并不参与反应,从而转化为大量副产废硫酸。由于磺化反应为强放热反应,而硫酸是强氧化剂,故磺化过程中生成大量深色副产物,导致废硫酸呈棕黑色,且具有很高cod值。工业磺化废硫酸如不妥善处理将会对社会和环境造成巨大危害。如何既安全彻底又经济有效地处理工业磺化废酸一直是业内人士关注的焦点。
3.工业磺化废硫酸治理主要有以下特点:1.精细化工企业规模较小,公用工程配套能力较弱,2.企业自身盈利能力有限,对工业磺化废酸治理装置投资和运行成本要求严格;3.工业磺化废硫酸组成复杂,浓度差异大;4.常用的工业磺化废硫酸治理方法有:吸附法﹑萃取法及氧化法。采用上述方法作为有机磺化废硫酸的净化方法存在下述问题:废硫酸处理量极小,且均处于实验室研究阶段,无工业化应用实例;运行成品高;产品硫酸浓度较低;有机杂质无法彻底治理,易引起二次污染;经上述方法处理得到的硫酸产品仅能应用于少数对硫酸品质较低的化工生产领域。
4.目前,我国工业废硫酸处理主要有浓缩﹑裂解再生﹑生产化肥﹑化学氧化﹑萃取﹑中和处理等6种途径。由于工业废硫酸中含有大量杂质,浓缩﹑生产化肥﹑化学氧化﹑萃取﹑中和处理等技术无法将杂质处理,且回收的产品质量差,仅适合特定用途等问题。废硫酸裂解再生技术是基于高温下废硫酸﹑硫酸盐及其他有机﹑无机杂质发生分解或燃烧,最终生成含so2的烟气,这部分烟气采用接触法工艺生产洁净的浓硫酸(或发烟硫酸)或其它硫化工产品。裂解再生技术具有最终产品纯度高﹑无二次污染等优点。近年来,裂解再生制硫酸技术在国内推广较快,应用领域不断发展。主要应用有:c4烷基化装置配套废酸裂解再生环保装置;天然气乙炔废酸和电石干法乙炔废酸裂解再生装置;配套丙烯腈和mma废液处理的裂解再生装置;焦化厂脱硫废液裂解再生装置。现有的裂解再生制酸技术普遍采用一转一吸或者两转两吸制酸工艺,适合处理流量大﹑硫含量高的废硫酸。
5.尽管废硫酸裂解再生制酸技术已经取得了一定程度的进展,但仍存在一些问题:废硫酸浓要求高﹑有大量稀硫酸产生﹑公用工程配套要求高﹑工艺流程长﹑设备数量多﹑占地面积大﹑控制要求高﹑操作人员多﹑运行成本高和装置投资高等。因此,针对工业磺化废硫酸治理的特点,开发一种废酸浓度适应范围宽﹑环保效果好﹑公用工程配套少﹑工艺流程短﹑设备数量少﹑占地面积小﹑控制要求低﹑操作人员少﹑运行成本低和装置投资低的工业磺化废
酸资源化利用装置及方法迫在眉睫。
技术实现要素:
6.本发明针对上述存在的问题提供一种工业磺化废硫酸资源化利用的装置及方法,解决现有工业磺化废硫酸治理存在的问题:采用常用的工业磺化废硫酸治理方法存在技术不成熟,产品硫酸浓度低及品质差等缺点;采用现有废硫酸裂解再生制酸技术存在废硫酸浓度要求高﹑有大量稀硫酸产生﹑公用工程配套要求高﹑工艺流程长﹑设备数量多﹑占地面积大﹑控制要求高﹑操作人员多﹑运行成本高和装置投资高等缺点。
7.为达到上述目的,本发明提供一种工业磺化废硫酸资源化利用的方法,包括以下步骤:第一步,裂解:燃料和助燃空气进行燃烧,在高温条件下降雾化后的废硫酸进行裂解,生成高温含so2的工业气体;第二步,降温除尘:对第一步生成的高温含so2的工业气体进行降温除尘处理;第三步,转化:在催化剂作用下,将来自降温除尘后的含so2工艺气体中so2氧化为so3;第四步,冷凝:通过换热降温将转化生成的so3冷凝,生成硫酸;第五步,尾气处理:对冷凝so3后排出的尾气进一步处理,脱除尾气中残留的so2和酸雾,得到洁净的尾气送入烟囱排放,尾气处理产生的稀酸与冷凝生成的硫酸混合。
8.作为上述技术方案的进一步改进,所述第一步中,废硫酸采用压缩空气进行雾化,燃料为气体或液体燃料中的至少一种,裂解过程中采用裂解炉,裂解炉选用立式炉或卧式炉,裂解生成含so2的工业气体在裂解炉内停留时间控制在5s-16s,控制裂解炉内温度为950-1200摄氏度。
9.作为上述技术方案的进一步改进,所述第二步中,高温含so2工艺气体采用热辐射式炉气冷却器进行降温,高温含so2工艺气体除尘过程采用旋风除尘器﹑膜除尘器和保安除尘器的组合;膜除尘器的膜管选用金属间化合物非对称膜管或高温陶瓷膜管;保安除尘器为固定床除尘器,固定床选用石英砂;保安除尘器出口含so2工艺气体含尘量≤5mg/nm3。
10.作为上述技术方案的进一步改进,所述第三步中,转化为一次两段转化,采用转化器转化,转化器包含两个催化剂床层,进一段和二段转化的含so2工艺气体温度为380~440摄氏度。
11.作为上述技术方案的进一步改进,所述第四步中,采用冷凝器进行冷凝,冷凝器的换热管采用石英管或含硼砂玻璃管,冷凝器的冷却介质为空气,冷凝器采用卧式冷凝器或立式冷凝器,选用卧式冷凝器,工艺气走壳程,空气走管程;选用立式冷凝器,工艺气走管程,空气走壳程,进冷凝器工艺气温度为250~295摄氏度。
12.作为上述技术方案的进一步改进,所述第五步中,尾气处理过程中采用双氧水脱硫工艺。
13.一种用于实现权利要求1所述方法的装置,包括裂解单元、降温除尘单元、转化单元、冷凝单元和尾气处理单元,所述裂解单元的输出端与降温除尘单元相连,所述降温除尘单元的输出端与转化单元相连,所述转化单元的输出端与冷凝单元相连,所述冷凝单元的输出端与尾气处理单元相连。
14.作为上述技术方案的进一步改进,所述裂解单元包括:助燃空气过滤器﹑助燃风机﹑废酸罐﹑废酸泵和裂解炉;所述降温除尘单元包括:炉气冷却器﹑旋风除尘器﹑膜除尘器﹑保安除尘器和第i气气换热器;所述转化单元包括:转化器﹑第ii气气换热器和第iii气气换热器;冷凝单元包括:冷凝器﹑冷却空气过滤器﹑冷却风机﹑酸循环槽﹑酸循环泵和酸冷却器;所述尾气处理单元:气体洗涤器﹑气体洗涤器循环泵﹑电除雾器﹑尾气风机和烟囱。
15.本发明的优点是:本发明的有益效果:1、与常用的工业磺化废硫酸治理方法相比,本发明所提供的装置及方法具有:a.技术成熟可靠,装置设备均为常规设备,可工业化应用;b.裂解单元﹑降温除尘单元﹑转化单元﹑冷凝单元及尾气处理单元均有成熟工业应用;c.产品为93wt%~98wt%工业级硫酸,浓度高且无杂质。
16.2﹑与现有废硫酸裂解再生制酸技术相比,本发明所提供的装置及方法具有:a﹑对废硫酸组成及浓度等波动适应性强现有废硫酸裂解再生制酸技术仅能适用于废硫酸中硫酸浓度≥75wt%;对于硫酸浓度<75wt%的废硫酸,由于工业磺化废硫酸中含有大量有机物,废硫酸裂解过程中,有机物会消耗大量空气中氧气,导致工艺气中so2浓度较低,无法满足现有废硫酸裂解再生技术转化单元对so2浓度的要求,只能通过补充富氧空气或在转化工段补充系统外热源等手段满足现有废硫酸裂解再生技术的应用。而本发明所提供的装置及方法转化单元能适用于低至1%左右的so2浓度,因此对废硫酸中硫酸的浓度适用范围较现有废酸裂解再生制酸技术要宽。
17.b﹑环保效果好,不产生稀硫酸现有废硫酸裂解再生制酸技术在净化工段会产生大量稀硫酸,需外送处理。
18.c﹑对公用工程配套要求低本发明所提供的装置及方法与现有废硫酸裂解再生制酸技术相比,循环冷却水用量﹑工艺补水量﹑电耗﹑压缩空气及仪表空气用量均大幅减少,且现有废硫酸裂解再生制酸技术需配建冷冻水及脱盐水装置。
19.d﹑工艺流程短﹑设备数量少;本发明所提供的装置及方法与现有废硫酸裂解再生制酸技术相比,工艺流程大幅缩短,设备数量减少约50%。
20.e﹑装置占地面积小;本发明所提供的装置及方法与现有废硫酸裂解再生制酸技术相比,装置占地面积仅仅需要不到一半。
21.f﹑该装置设备均为常压设备,控制要求低,危险性小,可靠性高;g﹑操作人员少;h﹑装置运行成本低;i﹑装置投资低。
附图说明
22.图1是本发明的实施例的设备工艺流程图。
23.其中:1﹑助燃空气过滤器,2﹑助燃风机,3﹑废酸罐,4﹑废酸泵,5﹑裂解炉,6﹑炉气冷却器,7﹑旋风除尘器,8﹑膜除尘器,9﹑保安除尘器,10﹑第i气气换热器,11﹑转化器,12﹑第ii气气换热器,13﹑第iii气气换热器,14﹑冷凝器,15﹑冷却空气过滤器,16﹑冷却风机,17﹑酸循环槽,18﹑酸循环泵,19﹑酸冷却器﹑20﹑气体洗涤器,21﹑气体洗涤器循环泵,22﹑电除雾器,23﹑尾气风机,24﹑烟囱。
具体实施方式
24.一种工业磺化废硫酸资源化利用的方法,包括以下步骤:第一步,裂解:燃料和助燃空气进行燃烧,在高温条件下降雾化后的废硫酸进行裂解,生成高温含so2的工业气体;第二步,降温除尘:对第一步生成的高温含so2的工业气体进行降温除尘处理;第三步,转化:在催化剂作用下,将来自降温除尘后的含so2工艺气体中so2氧化为so3;第四步,冷凝:通过换热降温将转化生成的so3冷凝,生成硫酸;第五步,尾气处理:对冷凝so3后排出的尾气进一步处理,脱除尾气中残留的so2和酸雾,得到洁净的尾气送入烟囱排放,尾气处理产生的稀酸与冷凝生成的硫酸混合。
25.作为上述技术方案的进一步改进,所述第一步中,废硫酸采用压缩空气进行雾化,燃料为气体或液体燃料中的至少一种,裂解过程中采用裂解炉,裂解炉选用立式炉或卧式炉,裂解生成含so2的工业气体在裂解炉内停留时间控制在5s-16s,控制裂解炉内温度为950-1200摄氏度。
26.作为上述技术方案的进一步改进,所述第二步中,高温含so2工艺气体采用热辐射式炉气冷却器进行降温,高温含so2工艺气体除尘过程采用旋风除尘器﹑膜除尘器和保安除尘器的组合;膜除尘器的膜管选用金属间化合物非对称膜管或高温陶瓷膜管;保安除尘器为固定床除尘器,固定床选用石英砂;保安除尘器出口含so2工艺气体含尘量≤5mg/nm3。
27.作为上述技术方案的进一步改进,所述第三步中,转化为一次两段转化,采用转化器转化,转化器包含两个催化剂床层,进一段和二段转化的含so2工艺气体温度为380~440摄氏度。
28.作为上述技术方案的进一步改进,所述第四步中,采用冷凝器进行冷凝,冷凝器的换热管采用石英管或含硼砂玻璃管,冷凝器的冷却介质为空气,冷凝器采用卧式冷凝器或立式冷凝器,选用卧式冷凝器,工艺气走壳程,空气走管程;选用立式冷凝器,工艺气走管程,空气走壳程,进冷凝器工艺气温度为250~295摄氏度。
29.作为上述技术方案的进一步改进,所述第五步中,尾气处理过程中采用双氧水脱硫工艺。
30.一种用于实现权利要求1所述方法的装置,包括裂解单元、降温除尘单元、转化单元、冷凝单元和尾气处理单元,所述裂解单元的输出端与降温除尘单元相连,所述降温除尘单元的输出端与转化单元相连,所述转化单元的输出端与冷凝单元相连,所述冷凝单元的输出端与尾气处理单元相连。
31.作为上述技术方案的进一步改进,所述裂解单元包括:助燃空气过滤器﹑助燃风机﹑废酸罐﹑废酸泵和裂解炉;所述降温除尘单元包括:炉气冷却器﹑旋风除尘器﹑膜除尘器﹑保安除尘器和第i气气换热器;所述转化单元包括:转化器﹑第ii气气换热器和第iii气气换热器;冷凝单元包括:冷凝器﹑冷却空气过滤器﹑冷却风机﹑酸循环槽﹑酸循环泵和酸冷却器;所述尾气处理单元:气体洗涤器﹑气体洗涤器循环泵﹑电除雾器﹑尾气风机和烟囱。
实施例
32.实施例1:以某润滑油助剂生产企业产出磺化废硫酸资源化利用为例说明本发明所述工业磺化废硫酸资源化利用的方法。该企业产出2000吨/年废硫酸。废硫酸中75wt%为h2so4,其余为有机物。
33.具体工艺流程及工艺参数为:第一步,裂解单元:来自废酸罐3废硫酸经废酸泵4加压送入雾化喷枪,与压缩空气充分接触雾化进入裂解炉5,同时在裂解炉5内燃料与经助燃风机2加压后助燃空气充分燃烧产生高温,使得废硫酸高温下完全裂解,废硫酸中的硫裂解生成so2,调节燃料量控制含硫废液裂解炉5出口工艺气温度~1150℃。
34.第二步,降温除尘单元:裂解炉5出口含so2工艺气经炉气冷却器6后温度降至~600℃,后经旋风除尘器7﹑膜除尘器8及保安除尘器9除尘至含尘量≤5mg/nm3,然后经第i气气换热器10与空气换热降温至~400℃。
35.来自冷凝器空气经过第i气气换热器10壳程升温至~260℃后进入第iii气气换热器13。
36.第三步,转化单元:经第i气气换热器10降温至~400℃含so2工艺气进入转化器11一段进行转化反应升温至~500℃,然后送入第ii气气换热器12进行换热降温至390℃,后送入转化二段进行转化反应升温至400℃,然后经第iii换热器13降温至285℃后送入冷凝器14。
37.来自第i气气换热器10空气依次经过第iii气气换热器12和第ii气气换热器11进行换热后送入烟囱排放。
38.第四步,冷凝单元:在冷凝器14中,工艺气体与来自冷却风机16的冷空气逆流冷却至~100℃后进入气体洗涤器20。
39.冷却空气过滤器15过滤后空气经冷却风机16加压后进入冷凝器14与工艺气进行换热,空气升温至~170℃送入第i气气换热器10。
40.第五步,尾气处理单元:冷凝器14出口工艺气进入气体洗涤器20与喷淋的含过氧化氢的稀硫酸接触进一步脱除so2,然后工艺气送入电除雾器22除去夹带的液滴,后进入烟囱24进行高空达标排放。
41.以该企业产出磺化废硫酸资源化利用为例,本发明方法与传统废酸裂解再生制酸技术两转两吸制酸工艺比较见下表:
以上仅以实施例来进一步说明本发明的技术内容,以便于读者更容易理解,但不代表本发明的实施方式仅限于此,任何依本发明所做的技术延伸或者再创造,均受本发明的保护。
再多了解一些
本文用于创业者技术爱好者查询,仅供学习研究,如用于商业用途,请联系技术所有人。