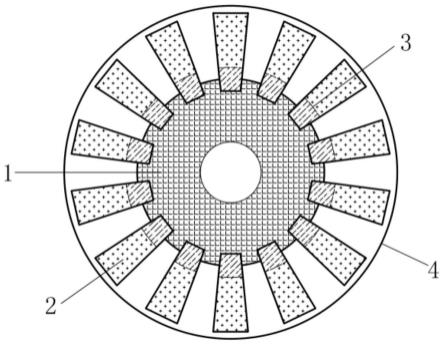
1.本发明属于航空发动机技术领域,涉及一种涡轮叶盘预制体,还涉及上述涡轮叶盘预制体纤维体积分数工艺设计方法。
背景技术:
2.涡轮叶盘预制体是将预制体单元叠层经z向穿刺缝合成型。涡轮叶盘预制体单元的结构设计是该预制体设计的关键技术。极性编织结构是将径向纤维沿圆周放射状排布,周向连续纤维与径向纤维交织形成平纹组织的一种预制体结构。发动机涡轮叶盘在工作中主要受力方向是周向和径向,对比经纬纱呈90
°
正交的机织平纹结构,极性编织结构中的纤维沿着周向和径向分布,更有利于发挥纤维在发动机涡轮叶盘中的承力作用,高性能纤维预制体是陶瓷基复合材料的骨架材料,研制结构轻、耐高温、整体力学性能优良的涡轮叶盘预制体对打破航空发动机发展技术壁垒,推进航空发动机产业发展起着重要的助推作用。
3.纤维体积分数是高性能纤维预制体的一项关键技术指标,是保障陶瓷基复合材料力学性能的重要因素。航空发动机涡轮叶盘陶瓷基复合材料对预制体的纤维体积分数提出了明确的要求,其中包括整体预制体的体积分数以及各部位如中心叶盘、齿根、叶片等径向纤维和周向纤维的体积分数。因此,涡轮叶盘预制体的体积分数工艺设计方法对实现涡轮叶盘预制体纤维体积分数可设计性、满足其设计技术指标至关重要。
4.发明专利《一种平面极坐标圆形织物的织造方法及设备》(公开号:cn108866755b,公开日:20211116),提出了一种极性编织结构的圆形织物的织造方法及编织设备,设计了一种整体叶盘纤维均匀排布的预制体结构,该专利中仅提出根据预制体的设计尺寸和所需的纤维体积含量,确定不同半径长度处径向编织纱的根数以及所对应半径处环向编织纱的根数,从而计算分区,但
技术实现要素:
及实施例并未根据预制体体积分数的技术指标进行预制体各部位结构的纤维工艺设计,因此,不能保证其工艺设计方法满足该体积分数的技术指标要求;另外,其整体叶盘纤维均匀排布的设计思路也不能满足涡轮叶盘对各部位如中心叶盘、齿根部位及叶片部位等不同的纤维体积分数结构设计要求。
发明内容
5.本发明的目的是提供一种涡轮叶盘预制体,具有结构稳定,纤维承力性能优良的特点。
6.本发明的另一目的是提供上述涡轮叶盘预制体纤维体积分数工艺设计方法,通过研究各结构设计参数与纤维体积分数之间的关系,实现了涡轮叶盘预制体各部位结构体积分数的可设计性。
7.本发明所采用的技术方案是,涡轮叶盘预制体,由预制体单元叠层铺放再经z向穿刺缝合形成,预制体单元包括中心叶盘,中心叶盘外围均匀布置有若干叶片,中心叶盘与叶片衔接区域为齿根;中心叶盘、叶片、齿根结构为由连续周向纤维和放射状径向纤维交织而成的极性编织结构。
8.本发明的特点还在于:
9.周向纤维由中心叶盘盘体中心原点向四周螺旋发散,直至叶片边缘,径向纤维包括初始径向纤维和径向增补纤维,初始径向纤维成列自盘体中心处放射状径向伸出,径向增补纤维挂在盘绕半径逐渐增加的周向纤维上并呈径向放射状伸出。
10.中心叶盘的径向纤维体积分数不大于周向纤维体积分数,齿根的周向纤维体积分数和径向纤维体积分数相同,叶片的周向纤维体积分数不大于径向纤维体积分数。
11.本发明的另一技术方案是,涡轮叶盘预制体纤维体积分数工艺设计方法,具体按照以下步骤实施:
12.步骤1、根据涡轮叶盘预制体设计尺寸参数和纤维体积分数要求,分别计算出预制体单元数量以及预制体单元各部位的纤维体积、各部位周向纤维长度用量和径向纤维长度用量;
13.步骤2、根据步骤1得到的各部位的周向纤维长度用量和径向纤维长度用量,分别计算预制体单元各部位周向纤维排列密度和径向纤维的加纱工艺,即得到各部位纤维体积分数对应的纤维工艺设计参数。
14.本发明的特点还在于:
15.步骤1中,尺寸参数包括预制体单元尺寸、各部位纤维体积分数、各部位的内径和外径,计算步骤为,根据涡轮叶盘预制体厚度确定预制体单元的数量,根据尺寸参数分别计算中心叶盘、齿根和叶片的体积以及各部位的纤维体积,根据l=v
纤
×
ρ/λ,其中λ为纤维的线密度,ρ为纤维的体密度,l为纤维长度用量,计算预制体单元各部位的周向纤维长度用量和径向纤维长度用量。
16.步骤2中,各部位周向纤维排列密度计算方式为:记预制体单元一部位的内径为r
内
,外径为r
外
,相邻两圈周向纤维间距γ,周向纤维长度用量l
周
为每一圈周向纤维的长度总和,则此部位的l
周
=2
×
π
×r内
2
×
π
×
(r
内
1
×
γ)
……
2
×
π
×r外
,根据上述公式,分别计算出预制体单元各部位的周向纤维间距γ,再根据rw=1/γ 1,分别计算得到各部位的周向纤维排列密度rw。
17.步骤2中,径向纤维的加纱工艺具体计算为:
18.2.1、将预制体单元的一部位沿径向均分成n个区域,每个区域各加一次纱,第一个区域的初始径向纤维记作第一次加纱,其余加纱纤维记作径向增补纤维7,则第n个区域为第n次加纱,计算加纱间距β:
19.β=(r
外-r
内
)
÷nꢀꢀꢀꢀ
(1)
20.则第n个区域的内边界线半径为:
21.rn=r
内
(n-1)
×
β
ꢀꢀꢀꢀ
(2);
22.2.2、将加纱位置到外径r
外
之间的距离记为加纱长度l,第一次加纱长度l1=r
外-r1,第n次加纱长度ln为:
23.ln=r
外-rnꢀꢀꢀꢀꢀ
(3);
24.2.3、记各区域内径向纤维根数n,加纱根数为c,径向纤维密度排列为rj,则第n个区域内的径向纤维根数nn为:
25.nn=2
×
π
×rn
×rj
ꢀꢀꢀꢀꢀ
(4)
26.则第n个区域的加纱根数cn为:
27.cn=n
n-n
n-1
ꢀꢀꢀꢀꢀ
(5);
28.2.4、径向纤维长度用量l
径
为:
29.l
径
=c1×
l1 c2×
l2
…
cn×
lnꢀꢀꢀꢀꢀ
(6)
30.将式1、式2、式3、式5代入式6中,计算得到加纱间距β、区域个数n和径向纤维排列密度rj,再将β值、n值和rj值分别代入式3、式4、式5中,计算得到加纱长度l、径向纤维根数n和加纱根数c;
31.2.5、重复2.1-2.4分别计算出预制体单元各部位的加纱间距β、区域个数n、径向纤维排列密度rj、加纱长度l、径向纤维根数n和加纱根数c,即得到各部位径向纤维的加纱工艺。
32.本发明的有益效果是:
33.(1)本发明的涡轮叶盘预制体,基于极性编织原理,采用涡轮叶盘预制体整体成型编织技术,预制体单元包括中心叶盘、齿根部位和叶片,并对预制体单元各部位进行纤维体积分数设计,提高涡轮叶盘预制体的结构稳定性和纤维承力性能;
34.(2)本发明的涡轮叶盘预制体纤维体积分数工艺设计方法,根据极性编织预制体结构中径向纤维和周向纤维的纤维体积分数设计要求,通过研究各结构设计参数与纤维体积分数之间的关系,计算排纱方式,进行涡轮叶盘预制体工艺设计;
35.(3)本发明的涡轮叶盘预制体纤维体积分数工艺设计方法,实现了航空发动机涡轮叶盘陶瓷基复合材料对预制体纤维体积分数技术指标的要求,实现了涡轮叶盘预制体结构体积分数的可设计性;
36.(4)本发明提出的涡轮叶盘预制体,作为骨架支撑材料,结构设计满足航空发动机涡轮叶盘陶瓷基复合材料各部位的承力需求,有利于航空发动机涡轮叶盘陶瓷基复合材料整体力学性能的提升。
附图说明
37.图1是本发明涡轮叶盘预制体的结构示意图;
38.图2是本发明涡轮叶盘预制体的极性编织结构示意图;
39.图3为涡轮叶盘预制体周向纤维间距示意图;
40.图4为涡轮叶盘预制体中预制体单元缝合结构示意图。
41.图中:1.中心叶盘,2.叶片,3.齿根,4.预制体单元,5.周向纤维,6.初始径向纤维,7.径向增补纤维。
具体实施方式
42.下面结合附图和具体实施方式对本发明进行详细说明。
43.本发明的涡轮叶盘预制体,结构如图1和图4所示,由预制体单元4叠层铺放再经z向穿刺缝合形成,如图1和图2所示,预制体单元4包括中心叶盘1,中心叶盘1外围均匀布置有若干叶片2,中心叶盘1与叶片2衔接区域为齿根3。
44.中心叶盘1主承力方向为周向,径向纤维体积分数不大于周向纤维体积分数;叶片2部位主承力方向为径向,周向纤维体积分数不大于径向纤维体积分数;齿根3部位为结构薄弱环节,周向纤维体积分数等于径向体积分数;通过设计预制体单元的纤维体积分数表
征整体预制体的纤维体积分数,提高结构稳定性及纤维承力性能。如图2所示,中心叶盘1、叶片2、齿根3结构均为由连续周向纤维5和放射状径向纤维交织而成的极性编织结构,周向纤维5由中心叶盘1盘体中心原点向四周螺旋发散,直至叶片2边缘,径向纤维包括初始径向纤维6和径向增补纤维7,初始径向纤维6成列自盘体中心处放射状径向伸出,径向增补纤维7挂在盘绕半径逐渐增加的周向纤维5上并呈径向放射状伸出。随着预制体外径的增加,径向纤维之间的间距逐渐增大,采取增加径向纤维的工艺技术来满足体积分数要求。
45.本发明的涡轮叶盘预制体,作为骨架支撑材料,通过实现各个部位周向和径向纤维体积分数的可设计性,结构设计满足航空发动机涡轮叶盘陶瓷基复合材料各部位的承力需求,待陶瓷化复合成型后打磨出叶片,可用于制备航空发动机涡轮叶盘陶瓷基复合材料,有利于航空发动机涡轮叶盘陶瓷基复合材料整体力学性能的提升。
46.本发明的涡轮叶盘预制体纤维体积分数工艺设计方法,具体按照以下步骤实施:
47.步骤1、根据涡轮叶盘预制体设计尺寸参数和纤维体积分数要求,分别计算出预制体单元4数量以及预制体单元4各部位的纤维体积、各部位周向纤维5长度用量和径向纤维长度用量;
48.步骤1中,尺寸参数包括预制体单元4尺寸、各部位纤维体积分数、各部位的内径和外径,所述计算步骤为,根据涡轮叶盘预制体厚度确定预制体单元4的数量,根据预制体单元4的外形尺寸可得到预制体单元的体积v,根据尺寸参数分别计算中心叶盘1、齿根3和叶片2的体积以及各部位的纤维体积v
纤
,纤维体积分数vf=v
纤
÷v×
100%,其中纤维体积分数vf为技术指标要求值,可以计算出纤维体积v
纤
,再根据l=v
纤
×
ρ/λ,其中λ为纤维的线密度,ρ为纤维的体密度,λ和ρ是纤维的特性值,l为纤维长度用量,计算预制体单元4各部位的周向纤维5长度用量和径向纤维长度用量。
49.步骤2、根据步骤1得到的各部位的周向纤维5长度用量和设计尺寸参数,分别计算各部位周向纤维间距,得到各部位周向纤维排列密度rw,即为1cm内周向纤维的排列根数;周向纤维的张力是影响预制体单元外观平整度的重要因素,在编织过程中张力不可控,通过控制周向纤维的排列密度来表征周向纤维的张力;
50.各部位的周向纤维排列密度具体计算如下:以中心叶盘1为例,记中心叶盘1的内径为r
内
,外径为r
外
,周向纤维间距γ即为均匀排布的相邻两根周向纤维之间的距离,如图3所示,周向纤维长度用量l
周
为每一圈周向纤维的长度总和,则中心叶盘1的l
周
=2
×
π
×r内
2
×
π
×
(r
内
1
×
γ)
……
2
×
π
×r外
,将步骤1中得到的中心叶盘1的周向纤维长度用量值代入上述公式,可计算得到中心叶盘1的周向纤维间距γ,再根据rw=1/γ 1,计算得到中心叶盘1的周向纤维排列密度rw;
51.根据上述方式,分别计算叶片2、齿根3的周向纤维间距和周向纤维排列密度;
52.同时,根据步骤1得到的各部位的径向纤维长度用量和设计尺寸参数,分别计算各部位径向纤维的加纱工艺;
53.加纱工艺具体计算为:
54.同样以中心叶盘1为例,
55.2.1、将中心叶盘1沿径向均分成n个区域,每个区域各加一次纱,第一个区域的初始径向纤维6记作第一次加纱,其余加纱纤维记作径向增补纤维7,则第n个区域为第n次加纱,计算加纱间距β:
56.β=(r
外-r
内
)
÷nꢀꢀꢀꢀꢀꢀꢀꢀꢀꢀꢀꢀꢀꢀ
(1)
57.则区域1内边界线的半径r1=r
内
,区域2内边界线的半径r2=r
内
1
×
β,则第n个区域的内边界线半径为:
58.rn=r
内
(n-1)
×
β
ꢀꢀꢀꢀꢀꢀꢀꢀꢀꢀꢀ
(2);
59.2.2、将加纱位置到外径r
外
之间的距离记为加纱长度l,第一次加纱长度l1=r
外-r1,第二次加纱长度:l2=r
外-r2,第n次加纱长度ln为:
60.ln=r
外-rnꢀꢀꢀꢀꢀꢀꢀꢀꢀꢀꢀꢀꢀꢀꢀ
(3);
61.2.3、中心叶盘1的内径向纤维根数为n,径向纤维排列密度为rj,即区域1的初始径向纤维6根数n1=2
×
π
×
r1×rj
;区域2的径向纤维根数n2=2
×
π
×
r2×rj
;则第n个区域内的径向纤维根数nn为:
62.nn=2
×
π
×rn
×rj
ꢀꢀꢀꢀꢀꢀꢀꢀꢀꢀꢀꢀꢀꢀ
(4)
63.相邻区域的内边界线排列的纤维根数的差值,即为加纱根数c,区域1的加纱根数c1=n1,区域2的加纱根数c2=n
2-n1,则第n个区域的加纱根数cn为:
64.cn=n
n-n
n-1
ꢀꢀꢀꢀꢀꢀꢀꢀꢀꢀꢀꢀꢀ
(5);
65.2.4、径向纤维长度用量l
径
为:
66.l
径
=c1×
l1 c2×
l2
…
cn×
lnꢀꢀꢀꢀꢀꢀꢀ
(6)
67.将式1、式2、式3、式5代入式6中,计算得到中心叶盘1的加纱间距β、区域个数n、径向纤维排列密度为rj,再将β值、n值和rj值分别代入式3、式4、式5中,计算得到中心叶盘1的加纱长度l、径向纤维根数n和加纱根数c;
68.2.5、重复2.1-2.4,再分别计算出叶片2、齿根3的加纱间距β、区域个数n、径向纤维排列密度rj加纱长度l、径向纤维根数n和加纱根数c,即得到预制体单元4的各部位径向纤维的加纱工艺。
69.通过周向纤维和径向纤维体积分数计算,精准进行涡轮叶盘预制体纤维排纱工艺设计;
70.再根据步骤2得到的各部位周向纤维排列密度和各部位径向纤维的加纱工艺在极性编织设备上进行排纱,形成平纹组织,整体编织得到预制体单元4;重复此步骤,满足步骤1得到的预制体单元4数量后,将得到的预制体单元4铺层叠放,用纤维在z向进行穿刺缝合,形成整体的涡轮叶盘预制体。
71.本发明的涡轮叶盘预制体纤维体积分数工艺设计方法,通过计算各部位纤维的排纱工艺,实现了涡轮叶盘预制体结构体积分数的可设计性,满足涡轮叶盘预制体各部位纤维体积分数技术指标的要求。
72.实施例1
73.涡轮叶盘预制体由中心叶盘1部位、齿根3部位、叶片3部位构成,各部位的周向和径向的纤维体积分数的技术指标均不同,但设计方法均相同,以中心叶盘为例进行体积分数工艺设计。
74.涡轮叶盘预制体单元内半径的1cm,外半径为11cm,厚度为0.03cm。其中,中心叶盘内半径为1cm,外半径为6cm;齿根部位内半径为6cm,外半径为8cm;叶片部位内半径为8cm,外半径为11cm。纤维原料选择碳化硅纤维,线密度λ为0.18g/m,体密度ρ为2.74g/cm3,要求设计以下体积分数的预制体工艺方案。中心叶盘中纤维体积含量占中心叶盘体积的比值:
周向30%,径向14%;齿根部位中纤维体积含量占齿根体积的比值:周向、径向体积分数均为20%;叶片部位中纤维体积含量占叶片体积的比值:周向10%,径向30%。分别对三个部位进行编织工艺设计,中心叶盘工艺设计具体步骤为:
75.(1)预制体体积(v):v=π
×
(6
2-12)
×
0.03=3.3cm3;
76.(2)周向纤维排列密度(rw):
77.①
周向纤维体积:v
周
=3.3
×
30%=0.99cm378.②
周向纤维总长:l
周
=v
×
ρ/λ=0.99
×
2.74
÷
0.18=15.07m=1507cm
79.③
周向纤维间距:
80.可计算出γ为0.079cm
81.④
周向纤维排列密度:rw=1
÷
γ 1,可计算出rw为13.7根/cm
82.(3)径向加纱工艺:
83.①
径向纤维体积:v
径
=3.3
×
14%=0.462cm384.②
径向向纤维总长:l
径
=v
×
ρ
÷
λ=0.46
×
2.74
÷
0.18=7.00m
85.③
加纱次数(区域数)、加纱长度和加纱根数:
86.r1=1l1=6-r1n1=2πr1×rj
c1=n187.l2=6-r2n2=2πr2×rj
c2=n
2-n188.l3=6-r3n3=2πr3×rj
c3=n
3-n2[0089][0090]
ln=6-rnnn=2πrn×rjcn
=n
n-n
n-1
[0091]
l
径
=c1×
l1 c2×
l2
…
cn×
ln[0092]
联合上述式子计算结果为:径向纤维排列密度为9.9根/cm;加纱次数为2,加纱间距为2.5cm;第一次加纱长度为5cm,加纱根数为62根;第二次加纱长度为2.5cm,加纱根数为156根。
[0093]
用上述方法分别计算齿根部位和叶片部位的工艺,计算结果如下:
[0094]
齿根部位:周向纤维排列密度为9.5根/cm;径向纤维排列密度为10.5根/cm;加纱次数为1次,加纱间距为2cm,加纱长度为2cm,加纱根数为178根。
[0095]
叶片部位:周向纤维排列密度为5.3根/cm;径向纤维排列密度为14.5根/cm;加纱次数为3次,加纱间距为1cm;叶片部位第一次加纱长度为3cm,加纱根数为333根;第二次加纱长度为2cm,加纱根数为91根;第三次加纱长度为1cm,加纱根数为91根。
再多了解一些
本文用于创业者技术爱好者查询,仅供学习研究,如用于商业用途,请联系技术所有人。