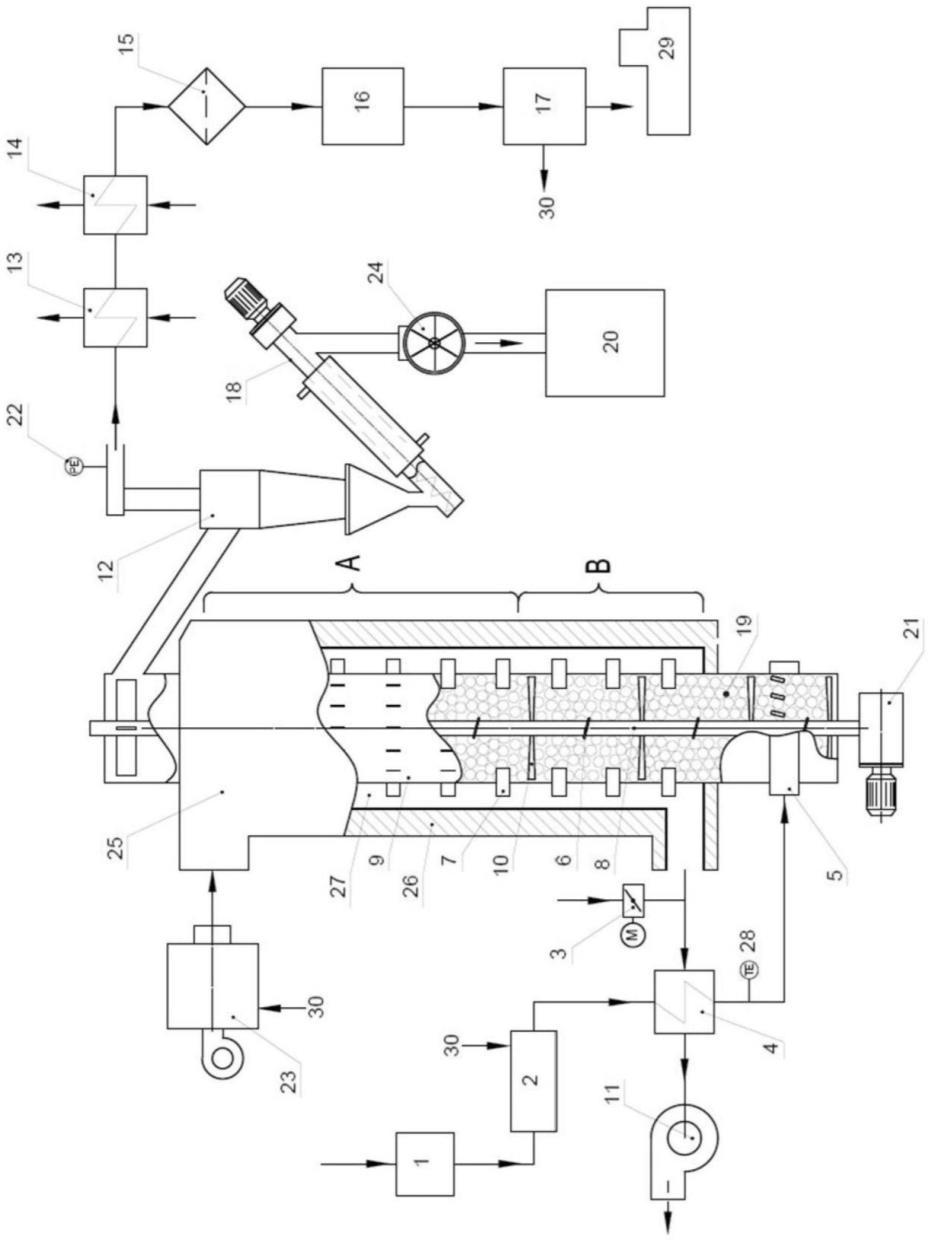
1.本发明涉及化学工业,可用于在制备氢气、碳黑和其他可燃气时处理甲烷和其他挥发性、液态、固态可熔烃。
背景技术:
2.最接近本发明的技术方案参见2020年10月16日第2020134076号俄罗斯联邦专利申请。
3.已知技术方案中,使用一个热交换器,其外部空间用于供应给入的烟气,所述烟气可加热进入热交换器内部空间的原料,所述用于原料给入的热交换器的内部空间包含一个以位于旋转轴上的叶片形状的搅拌器。已知方案在用于热解固态烃时效率很高,但由于热交换面积小,以及在热交换器的内部空间中无法从反应器中排出碳黑,因此无法处理气态和液态烃。
技术实现要素:
4.本发明解决的技术问题是开发一种技术,该技术能在将分离出的碳转化为碳黑并从反应器中排出的情况下,从原料中最大限度地提取氢气。
5.本发明使用所取得的技术成果是,通过在大气压下快速高温热解,在不接触氧气和不产生co2的情况下实现氢和碳的高度分离。并且提高气态烃的热解效率,降低热污染和大气中的二氧化碳排放量。
6.技术成果的实现在于,在所述烃的热解方法中,在位于被炉墙围砌的空间内的热解反应器内,由空气和气态烃的富氢混合物燃烧得到的烟气进行加热,使得大气中的co2排放量得到最大限度的降低,烟气在炉壁和反应器间隔处垂直向下移动,预热过的烃被送入反应器下方,而热解产生的氢气和碳黑从反应器上部被排出,利用贯通反应器壁的导热金属元件来增加反应器从烟气到热解产物的热传递;通过用对气态烃及其热解产物呈惰性的陶瓷球填充反应器的内部空间来形成主要的烧蚀表面。依靠陶瓷球的异向运动使得反应器的导热元件和内壁上的碳黑得到清除,固定在旋转轴上的叶片使陶瓷球在反应器的外围外壳附近向上移动,在靠近旋转轴的反应器中央部分向下移动。其中烃可采用天然气,例如甲烷、伴生气。此外,可采用液态预热烃、燃料油、废油、油泥,在压力下通过安装在反应器底部的喷嘴给入。亦可采用固态可熔烃,例如废塑料,通过熔化将其转化为液态烃。在特定情况下,反应器加热采用烃热解产生的空气和烃气的富氢混合物。实施该方法时,炉壁和反应器间隔处的烟气从上到下移动,使反应器上部的温度处于950℃至1150℃的范围内,而反应器下部的温度处于750℃至950℃的范围内,使得渗碳链式反应得以进行,烃与烟气流向相逆自下而上进入反应器,使得受热均匀。在进入反应器之前将液态和气态烃加热到390℃-410℃,而可熔烃被加热到300℃-320℃。
7.反应器中的气体升温速度达到0.1秒内300℃,使得碳与烃分离的链式反应能够发生和进行。反应器中烃气保持一定的流速,使反应器中气流的加热温度处于300℃至1050℃
之间。实施该方法时,氢气和未分解的烃气的混合物从反应器的上部排出,利用膜过滤器从混合物中分离出纯氢,一部分烃气和氢气的混合物被送到燃烧器中以制备烟气,另一部分则被重新送入反应器进行热解。
8.该烃热解装置包含一个带炉壁的壳体,其中内置一个立式反应器,所述反应器壁由导热元件制成,而其内部装有对气态烃及其热解产物呈惰性的陶瓷球,所属反应器置有一个可旋转的带叶片的竖轴,其叶片的形状使颗粒以一定的角度向水平方向移动,其中:
9.顶部装有进口集气管,可将烟气从燃烧器给到反应器和炉壁的间隔处;
10.反应器底部装有可从反应器排出烟气的集气管;
11.反应器底部装有可给入待处理烃的进料口;
12.反应器顶部装有集气管,可将热解产物从反应器内部排出,
13.所述装置包含一个旋风分离器,其入口与反应器的上部集气管相连,所述旋风分离器净化后气体的出口与板式冷却器和过滤分离器相连,所述过滤分离器出气口与压缩泵相连,所述压缩泵的出口与膜过滤器的入口相连,所述膜过滤器可将混合气分离成纯氢和含氢混合气;
14.其中,用于排出含氢混合气的膜过滤器的出口与燃烧器相连,所述燃烧器的烟气出口与反应器的烟气进口集气管相连,而
15.旋风分离器的锥体部分与螺旋输送机相连,所述螺旋输送机通过锁风卸料阀将锥体部分中沉积的碳黑卸入料斗。当该装置用于气态烃热解时,用于将预热待处理的气态烃送入反应器的入料口为集气管形式,当用于液态烃热解时,用于将待处理烃给入的入料口为喷嘴装置形式,而当用于固态可熔烃的热解时,该装置还包含一个与泵连接的固态烃的熔化装置,所述泵可将熔化后的烃给入到喷嘴。为实现所述目的,安装在旋转轴上的所述叶片具有使得陶瓷球可以运动的形状,以清除导热元件、反应器壁和球本身上沉积的碳黑,靠近轴的和靠近热交换器内部壁的所述叶片具有相反节距,所述导热元件可以穿过反应器壁,能够使同一个导热元件既在反应器外部与烟气接触,又在反应器内部与球和热解产物接触。
附图说明
16.图1所示为实施本发明的热解反应器。
具体实施方式
17.如图所示,热解反应器25是通过吹入气体燃烧器23中的烟气来进行加热。热解反应器内上部区域a的温度保持在950℃至1150℃,以保证热解过程的稳定。温度超过1150℃时,反应器的工作效率下降,其结构元件可能会受损,而温度低于950℃时,热解过程速度下降。为了达到待处理烃加热和分解的均匀性和最大化,所述待处理烃会从底部送入反应器,流向与从顶部送入的烟气相反。为了有效利用反应器中的所有空间,对原料和烟气给入浓度进行调节,使得反应器出口处的烟气温度为700℃-800℃,因为低于700℃时,热解过程进行缓慢,而高于800℃时,会析出过量的氢和碳,导致气体受热不均,氢产率明显下降。反应器的尺寸和处理量直接决定反应器的加热温度;处理量越大和反应器的尺寸越大,则反应器需达到的加热温度就越高。
18.气体燃烧器23中的炉气沿着反应器外腔通过通道27,所述通道27处于耐火炉壁26和反应器壳体9外壁的炉壁之间,所述反应器壳体9装有对气态烃及其热解产物呈惰性的陶瓷球19。烟气同时加热炉壁26、反应器壳体9、与反应器内部的烟气、陶瓷球和气态烃相接触的贯穿式导热元件7。
19.通过利用电动阀门3稀释进入引风机11的换热器前的烟气,可自动保持进入板式换热器4用于预热气态烃的烟气温度。进入处理过程的气体温度由温度传感器28测得,阀门3根据所述温度传感器28气体温度的示数对烟气温度自动调节。
20.配气站1中的主气体进入关闭调节装置2,所有调节和限制动作通过所述装置送去处理的气体实施。所述装置2的气体送入板式换热器4并在此加热到350℃至450℃,使得装有颗粒的换热器空间得到最大限度的利用。
21.预热气体通过烃的入料口、集气管5进入反应器的下部,加热到700℃-800℃,之后与陶瓷球和热解过程中气体中析出的碳黑接触,并随着陶瓷球在叶片搅拌下向下移动。此外,所述气体与反应器壳体9的壁和反应器的内部导热元件7接触,因此气体在b区迅速加热至600℃-700℃并部分分解成氢气和含碳蒸气。固定在轴8上的叶片的结构使得陶瓷球在距所述轴轴线不同距离处相对于水平线进行异向运动。例如,在轴附近处叶片的水平线的角度使得球向下移动,而反应器内部外围区域中的叶片的角度使得球向上移动。在垂直方向运动的过程中,球捕获析出的碳黑颗粒并将其均匀地分布在反应器的内部空间中,球在水平方向上的必然运动使得其与导热肋板相接触,相应地,使得反应器内部加热均匀,同时碳黑在反应器所有空间内起到催化剂和渗碳中心的作用,而过量的碳黑则在自身相互作用下从反应器的内表面和陶瓷球上分离出来,在气态热解产物的定向流动作用下被带出反应器。
22.烃也可采用液态烃,所述液态烃通过喷嘴(图中未示出)给入反应器5的下部。
23.在特定情况下,位于轴附近的短螺旋叶片或叶片6使反应器中的陶瓷球向下移动,所述陶瓷球携带部分可起到催化剂或渗碳中心的作用的碳黑,使得热解反应在反应器的下部就已开始进行,而长叶片10使球向上移动,同时通过彼此之间,以及与反应器壳体壁9之间的和反应器的板7之间的相互作用,球自身得到清洁并使反应器结构元件上从气体中析出的碳黑得到清除。所述碳黑是一种减摩材料,可防止陶瓷球磨损。当气态烃采用甲烷时,在反应器的下部区域b甲烷的转化率不超过5-20%。
24.然后,气体混合物和由气流携带的碳黑,在进入处理过程的气体的背压和压缩机16在反应器上腔产生的负压的作用下,进入反应器的上部区域a,所述混合物在0.1-0.3秒内被加热到800℃-1050℃。生成碳黑的链式反应正是在这个区域发生,且由于气体温度变化率达到0.1秒内300℃,甲烷的主要转化率为80-90%。
25.然后,含有在转化过程中析出的氢气和产生的过量碳黑的混合物进入旋风过滤器12,碳黑和其他固态颗粒(若存在)与在此与所述气体分离,碳黑通过斜式螺旋输送机18从旋风过滤器中排出,所述过程中所述碳黑可以利用位于输送机顶部的热交换器进行冷却。
26.然后,碳黑通过锁风卸料阀24从工艺中导到料斗20,以便后续包装和销售。
27.在旋风过滤器12中得到净化的气体,由氢气和7%至10%的甲烷组成,在板式煤气-空气冷却器13中冷却到250℃,然后所述气体进入煤气-空气冷却器14并被冷却到20℃-30℃,之后在精细过滤器15中被净化,并通过低压压缩机站16,进入氢气最终清洗的膜站
17。
28.压缩机16,由自动采用真空计22的读数的自动化系统控制,其真空度保持在2-6mbar,以对旋风分离器12的阻力进行补偿,使反应器25在大气压下运行。膜站将从旋流器出来的气体分离成80-85%的纯氢和20-15%的甲烷和氢气混合物。甲烷和氢气混合物30在燃烧器23中作为反应器25的燃料,同样被送往装置2,与主气体混合后送到预热器4。经膜站17净化的氢气被储存在气罐29中或装入钢瓶中。
29.该方法的主要特点是提高了热能的利用率,并从气态烃中生产出氢气,而不向大气中排放co2。在所述同一反应器壳体中持续进行三个过程,即高速烧蚀高温热解、由饱和烃生成碳黑和从反应器中清除碳黑。在反应器中被加热到850℃的碳黑,对生成的气体起到了催化剂和过滤器的作用。为了增加烧蚀表面,在反应器容器中装填具有高导热性和热容量的耐热陶瓷球。
30.通过在反应器燃烧器中使用被氢气稀释过的甲烷,制氢反应器加热过程中的co2排放量得以减少,因此,所述制氢方法根据欧盟的分类为蓝色等级,基本无co2排放,所述co2排放不超过所制氢气量的10%,而在用灰渣水热裂解法制氢时,co2排放超过所制氢气量的100%。此外,整个烧蚀表面,包括球、反应器壁、加热或导热元件,都得到持续清洁,碳黑也从工艺中排出。在反应器的下区和上区之间设置一个高达200℃的可控温差,使渗碳链式反应得以发生。通过烟气预热,将用于反应器预热和工艺维持的气体消耗减少到送入处理的气体的7-10%。在现代工业制氢技术中,加氢裂化用于工艺维持所需的气体消耗达100%。
31.所述技术成果是通过在一个装有陶瓷球和催化剂的立式连续作业反应器中进行高速高温催化烧蚀热解,使得气体降解并渗氢渗碳而实现的。其中,从甲烷分解过程中获得并加热到850℃的碳黑用作催化剂。将碳黑颗粒和陶瓷球的尺寸计算入内的烧蚀表面积比现有的类似发明大很多倍。本发明的另一个重要特征是,以可控的方式将反应器的下部的反应器壳体加热至750℃-950℃,上部的反应器壳体加热至950℃至1150℃,为析出固态碳(碳黑)的链式反应的进行提供条件。
再多了解一些
本文用于创业者技术爱好者查询,仅供学习研究,如用于商业用途,请联系技术所有人。