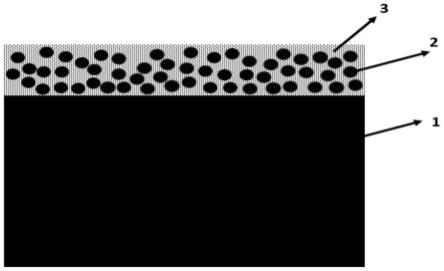
1.本发明涉及钕铁硼磁体生产领域,尤其涉及一种钕铁硼磁体矫顽力提升方法以及由该方法制备的磁体。
背景技术:
2.钕铁硼烧结永磁体被广泛的应用于空调、汽车、医疗及工业等领域。随着时代的发展,一方面钕铁硼烧结永磁体要求更加小型化和薄片化,另一方面钕铁硼烧结永磁体要求具有更高的剩磁和矫顽力。
3.在钕铁硼烧结永磁体的合金中,通过加入铽,镝元素均可提高钕铁硼烧结永磁体的矫顽力,但采用传统的成分配比方法,会使镝或铽元素进入主相晶粒内,会明显降低其剩磁和消耗大量的重稀土元素。
4.公开号为cn107578912a的中国专利公开了一种具有高矫顽力的钕铁硼磁体的制备方法,将重稀土粉末与防氧化剂、粘结剂、有机溶剂混合制得悬浊液后涂覆在钕铁硼磁体表面,烘干后进行高温扩散及时效处理,增加磁体矫顽力。该方法生产效率高、材料利用率高,因此被广泛的采用。但是采用此方法制备的重稀土涂层由于硬度和强度较低,很容易划伤或磨损造成局部重稀土元素的缺损进而影响扩散效果;且此类涂覆膜层在扩散升温过程中容易产生不规则的收缩,造成钕铁硼磁体表面局部重稀土元素的缺损和部分区域重稀土元素的过量聚集,使得钕铁硼磁体扩散后的性能均匀性较差。
5.钕铁硼磁体表面的涂覆层在高温扩散时,重稀土元素会在短期过量供应,造成钕铁硼磁体表面与重稀土元素过量反应消耗过量的重稀土,而钕铁硼磁体内部又由于重稀土元素的供应不足导致扩散不良,最终导致扩散后磁体表层与中心处性能差异较大且消耗的稀土总量过多。
技术实现要素:
6.发明目的:为了解决现有技术中重稀土涂覆层硬度强度低、生产过程中容易产生划伤磨损、扩散过程中易收缩以及由于重稀土元素在短期过量供应导致的扩散均匀性差、重稀土消耗量大的问题,本发明提供一种钕铁硼磁体矫顽力提升方法及由该方法制备的磁体。
7.技术方案:为实现上述目的,本发明的一种钕铁硼磁体矫顽力提升方法,包括以下步骤:
8.(s1)将重稀土扩散源粉末、有机粘接剂、球形耐高温陶瓷粉末、有机溶剂、混合并搅拌后制备重稀土浆料,其中要求球形耐高温陶瓷粉末的粒度是扩散源粉末的粒度的5-10倍,球形耐高温陶瓷粉末的重量为重稀土扩散源粉末重量的10%-30%;
9.(s2)将上述重稀土浆料涂覆到钕铁硼磁体表面并进行烘干形成重稀土涂层,该重稀土涂层由球形耐高温陶瓷粉末组成基本的骨架结构,重稀土扩散源粉末分布在球形耐高温陶瓷粉末形成的骨架结构缝隙内,并呈三维网状分布;
10.(s3)在真空条件或者氩气保护条件下对覆盖有重稀土涂层的钕铁硼磁体进行高温扩散和时效处理。
11.优选地,在所述(s1)中,其中的重稀土扩散源粉末为纯铽、纯镝、氢化镝、氢化铽粉末中的至少一种,所述重稀土扩散源粉末平均粒度范围为2-10μm。
12.优选地,在所述(s1)中,其中的有机粘接剂为树脂型粘接剂或者橡胶型粘接剂。
13.优选地,在所述(s1)中,其中有机溶剂为酮类、苯类或脂类溶剂。
14.优选地,在所述(s1)中,其中球形耐高温陶瓷粉末为球形氧化铝陶瓷粉、球形氧化锆陶瓷粉、球形氮化硼陶瓷粉中的至少一种;所述球形耐高温陶瓷粉末的粒度范围为10-100μm。
15.优选地,在所述步骤(s1)中,所述重稀土扩散源粉末与球形耐高温陶瓷粉末的重量总和占重稀土浆料的40%-80%,有机粘接剂的重量占重稀土浆料的5%-10%,剩余为有机溶剂。
16.优选地,在所述(s2)中,重稀土浆料涂覆方式为丝网印刷或者喷涂。
17.优选地,在所述(s2)中,涂覆到钕铁硼磁体表面的重稀土涂层中重稀土扩散源粉末重量为钕铁硼磁体重量的0.3%-1.5%。
18.优选地,在所述(s3)中,高温扩散的扩散温度为850-950℃、扩散时间为3-48h;时效处理的时效温度为450-650℃、时效时间为3-10h。
19.由上述方法可得到具有高矫顽力的磁体,该磁体包括钕铁硼磁体以及覆设在钕铁硼磁体表面的重稀土涂层;其中,重稀土涂层包括由球形耐高温陶瓷粉末组成基本的骨架结构以及填充在骨架结构中的重稀土扩散源粉末。
20.本发明的一种钕铁硼磁体矫顽力提升方法及磁体,至少具有以下技术效果:
21.(1)通过在重稀土浆料中添加一定比例和尺寸的球形耐高温陶瓷粉末,使其涂覆烘干后形成的重稀土涂层具有特殊的结构,该特殊结构包括球形耐高温陶瓷粉末组成基本的骨架结构,以及分布在骨架结构缝隙内并呈连续的三维网状分布的重稀土扩散源。重稀土涂层中球形耐高温陶瓷粉末形成基本骨架结构,一方面提高了膜层的整体硬度和强度,增强了膜层的耐磨和耐划伤性,另一方面防止了扩散升温过程中重稀土膜层的收缩,因此扩散过程中重稀土的分布更加均匀。
22.(2)在重稀土涂层中,重稀土扩散源存在于球形耐高温陶瓷粉末形成的骨架缝隙中并呈连续的三维网状连续,在高温扩散过程中重稀土涂覆层中的重稀土扩散源沿陶瓷粉末之间的缝隙持续稳定的向钕铁硼磁体扩散,杜绝了重稀土扩散源的短期过量供应,提高了扩散性能和扩散均匀性,减少重稀土的浪费。另外球形陶瓷粉的存在将重稀土膜层中的重稀土成分进行分割形成均匀连续且网状分布,减缓了空气中的氧元素从涂层外表面向涂层内部的扩散,提高了重稀土涂层的抗氧化性。
23.(3)涂覆实施过程中由于球形陶瓷粉末的加入,增加了浆料的流动性和悬浮性,提高了涂覆精度和涂覆稳定性,另外陶瓷粉末的增加,提高了重稀土中的脱气通道利于重稀土浆料中有机溶剂等的挥发,提高了生产稳定性。
附图说明
24.图1为钕铁硼磁体表面涂覆重稀土涂层后的示意图;
25.图2为钕铁硼磁体沿扩散方向进行切割的示意图;
26.在图1中,1表示钕铁硼磁体基体;2表示球形耐高温陶瓷粉末;3表示重稀土扩散源。
27.在图2中,1#和5#为沿扩散方向最表层样品,3#为沿扩散方向最中心样品。
具体实施方式
28.以下结合图1至图2对本发明的原理和特征进行描述,所举实例只用于解释本发明,并非用于限定本发明的范围。
29.实施例1
30.(s1)使用粒度为2μm的纯tb粉末作为重稀土扩散源,橡胶类粘接剂,酮类有机溶剂,粒度为10μm的球形氧化铝陶瓷粉共4种原料作为重稀土浆料的原料,首先将纯tb粉末与球形氧化铝粉末混合,其中球形氧化铝陶瓷粉的重量为纯tb粉重量的10%,并将混合后的粉末作为扩散源中间体,之后将扩散源中间体与橡胶类粘接剂,酮类有机溶剂分别按照占比为40%,5%,55%的比例混合并搅拌均匀后制备成重稀土浆料。
31.(s2)将上述重稀土浆料使用丝网印刷的方式涂覆到上述10*10*5mm的钕铁硼基体上的两个10*10mm的表面上,并进行烘干后形成具有特殊结构的重稀土涂覆层,并控制涂覆层中重稀土的重量与钕铁硼基体的重量比例为0.8%;其中,钕铁硼基体为经过熔炼,制粉,成型,烧结时效工序制得n48h牌号毛坯,并经过加工得到10*10*5mm尺寸的基体。
32.(s3)将涂覆有重稀土涂覆层的钕铁硼磁真空下进行扩散时效,扩散时效工艺为850℃*48h 500℃*5h,之后对扩散完成后的产品测试整体磁性能。
33.对扩散完成后的产品沿扩散方向均匀切割成5个,测试扩散后的沿扩散方向不同位置处的磁体的磁性能。
34.为了充分展示本专利方案与传统涂覆扩散方案的相比所具有的技术优势,设置以下对比例1。
35.对比例1
36.(s1)使用粒度为2μm的纯tb粉末作为重稀土扩散源,橡胶类粘接剂,酮类有机溶剂粉共3种原料作为重稀土浆料的原料,将纯tb粉扩散源与橡胶类粘接剂,酮类有机溶剂分别按照占比为40%,5%,55%的比例混合并搅拌均匀后制备成重稀土浆料。
37.(s2)将上述重稀土浆料使用丝网印刷的方式涂覆到上述10*10*5mm的钕铁硼基体上的两个10*10mm的表面上,并进行烘干后形成重稀土涂覆层,并控制涂覆层中重稀土的重量与钕铁硼基体的重量比例为0.8%;其中,钕铁硼基体为经过熔炼,制粉,成型,烧结时效工序制得n48h牌号毛坯,并经过加工得到10*10*5mm尺寸的基体。
38.(s3)将涂覆后重稀土涂覆层的钕铁硼磁体在真空下进行扩散时效,扩散工艺为850℃*48h 500℃*5h,之后对扩散完成后的产品测试整体磁性能。
39.对扩散完成后的产品沿扩散方向均匀切割成5个,测试扩散后的沿扩散方向不同位置处的磁体的磁性能。
40.为了对比实施例和对比例中重稀土涂覆层的耐划伤性,将实施例1中涂覆有重稀土涂覆层的样品与对比例1中涂覆有特殊结构的重稀土涂覆层的样品的涂覆面接触进行相互摩擦实验,统计实施例1和对比例1中的样品表面的重稀土膜层划伤并漏出基体的面积占
总涂覆面积的比例,将统计数据记录在表1中并命名为划伤比。
41.为了对比实施例和对比例中重稀土涂覆层在高温扩散过程中的耐收缩性,分别取实施例1和对比例1中的扩散品各100片,统计扩散后存在重稀土膜层收缩现象的样品数量与总统计数量的比例,将统计数据记录在表1中并命名为收缩比。
42.将扩散前的钕铁硼磁体性能,实施例1中扩散完成的钕铁硼磁体的整体性能,对比例1中扩散完成的钕铁硼磁体的整体性能进行对比,对比表格1如下。
43.表1通过实施例1和对比例1得到的磁体性能对比
44.样品名称划伤比收缩比br(kgs)hcj(koe)hk/hcjn48h基体//13.817.100.982实施例120%7%13.6227.500.975对比例10%0%13.6026.900.968
45.由表1可见,对比例1中涂覆有特殊结构重稀土涂覆层的样品在与实施例1中涂覆有重稀土涂覆层的样品进行相互摩擦实验时没有划伤,而实施例1中的样品存在划伤,划伤比例为20%,说明对比例1中的重稀土涂覆层的耐划伤性更强。另外实施例1中样品表面的重稀土涂覆层在高温扩散过程中存在收缩的情况所占比例为7%,而对比例1中样品表面的重稀土涂覆层在高温扩散过程中没有出现收缩的情况,说明对比例1中所制备的具有特殊结构的重稀土涂覆层与实施例1中制备的重稀土涂覆层相比具有更强的耐收缩性。
46.由表1可见,在相同的重稀土增重条件下,实施例1中的磁体扩散后br下降了0.18kgs,hcj增长了10.4koe,方形度下降了0.007。对比例1中的磁体扩散后br下降了0.2kgs,hcj增加了9.8koe,方形度下降了0.014。从上述结果可以看出实施例1和对比例1的扩散方案均能实施钕铁硼磁体的性能提升,但是实施例1中的方案的在重稀土增重量相同的条件下,剩磁降低量更少,矫顽力增加幅度更高,方形降低更少。
47.将扩散前的钕铁硼磁体,实施例1中扩散完成的钕铁硼磁体,对比例1中扩散完成的钕铁硼磁体,分别沿扩散方向均匀切割成5份后进行磁性能测试,对比扩散后的磁体性能均匀性,对比表格2如下。
48.表2由实施例1和对比例1得到的磁体性能均匀性对比
[0049][0050]
由表2可见,在相同的重稀土增重和扩散工艺条件下,实施例1中的磁体扩散后沿扩散方向最表层位置样品与最中心样品的矫顽力偏差为1.85koe,且最中心位置处的样品的hcj较基体提高了8.7koe。对比例1中的磁体扩散后沿扩散方向最表层位置样品与最中心样品的矫顽力偏差为2.3koe,且最中心位置处的样品的hcj较基体提高了8koe,另外实施例1中磁体扩散后中心位置处的性能比对比例1中扩散后磁体中心位置处的性能高0.7koe,通
过上述对比可知实施例1中的磁体扩散深度更深,扩散更加均匀。
[0051]
实施例2
[0052]
(s1)使用粒度为5μm的氢化镝粉末和纯镝粉末按照1:1混合后作为重稀土扩散源粉末,树脂类粘接剂,酯类有机溶剂,粒度为35μm的球形氧化锆陶瓷粉共4种原料作为重稀土浆料的原料,首先将重稀土扩散源粉末与球形氧化锆粉末混合,其中氧化锆陶瓷粉的重量为重稀土扩散源粉末重量的15%,并将混合后的粉末作为扩散源中间体,之后将扩散源中间体与树脂类粘接剂,酯类有机溶剂分别按照占比为60%,10%,30%的比例混合并搅拌均匀后制备成重稀土浆料。
[0053]
(s2)将上述重稀土浆料使用丝网印刷的方式涂覆到上述10*10*3mm的钕铁硼基体上的两个10*10mm的表面上,并进行烘干后形成具有特殊结构的重稀土涂覆层,并控制涂覆层中重稀土的重量与钕铁硼基体的重量比例为0.3%;其中钕铁硼基体为经过熔炼,制粉,成型,烧结时效工序制得n55h牌号毛坯,并经过加工得到10*10*3mm尺寸的基体。
[0054]
(s3)将涂覆后重稀土涂覆层的钕铁硼磁体在氩气保护氛围下进行扩散时效,扩散工艺为900℃*3h 450℃*3h,之后对扩散完成后的产品测试整体磁性能。
[0055]
对扩散完成后的产品沿扩散方向均匀切割成3个,测试扩散后的沿扩散方向不同位置处的磁体的磁性能。为了充分展示本专利方案与传统涂覆扩散方案的相比所具有的技术优势,设置有对比例2。
[0056]
(s1)使用粒度为5μm的氢化镝粉末和纯镝粉末按照1:1混合后作为重稀土扩散源粉末,树脂类粘接剂,酯类有机溶剂共3种原料作为重稀土浆料的原料,将重稀土扩散源粉末与树脂类粘接剂,酯类有机溶剂分别按照占比为60%,10%,30%的比例混合并搅拌均匀后制备成重稀土浆料。
[0057]
(s2)将上述重稀土浆料使用丝网印刷的方式涂覆到上述10*10*3mm的钕铁硼基体上的两个10*10mm的表面上,并进行烘干后形成具有特殊结构的重稀土涂覆层,并控制涂覆层中重稀土的重量与钕铁硼基体的重量比例为0.3%;其中,钕铁硼基体为经过熔炼,制粉,成型,烧结时效工序制得n55h牌号毛坯,并经过加工得到10*10*3mm尺寸的基体。
[0058]
(s3)将涂覆后重稀土涂覆层的钕铁硼磁体在氩气保护氛围下进行扩散时效,扩散工艺为900℃*3h 450℃*3h,之后对扩散完成后的产品测试整体磁性能。
[0059]
对扩散完成后的产品沿扩散方向均匀切割成3个,测试扩散后的沿扩散方向不同位置处的磁体的磁性能。
[0060]
为了对比实施例和对比例中重稀土涂覆层的耐划伤性,将实施例2中涂覆有重稀土涂覆层的样品与对比例2中涂覆有特殊结构的重稀土涂覆层的样品的涂覆面接触进行相互摩擦实验,统计实施例2和对比例2中的样品表面的重稀土膜层划伤并漏出基体的面积占总涂覆面积的比例,将统计数据记录在表3中并命名为划伤比。
[0061]
为了对比实施例和对比例中重稀土涂覆层在高温扩散过程中的耐收缩性,分别取实施例2中的扩散品和对比例2中的扩散品各100片,统计扩散后存在重稀土膜层收缩现象的样品数量与总统计数量的比例,将统计数据记录在表3中并命名为收缩比。
[0062]
将扩散前的钕铁硼磁体性能,实施例2中扩散完成的钕铁硼磁体的整体性能,对比例2中扩散完成的钕铁硼磁体的整体性能进行对比,对比表格3如下。
[0063]
表3通过实施例1和对比例1得到的磁体性能对比
[0064]
样品名称划伤比收缩比br(kgs)hcj(koe)hk/hcjn55h基体//14.6115.520.989实施例210%11%14.5219.330.981对比例20%0%14.5118.820.980
[0065]
由表3可见,对比例2中涂覆有特殊结构重稀土涂覆层的样品在与实施例2中涂覆有重稀土涂覆层的样品进行相互摩擦实验时没有划伤,而实施例2中的样品存在划伤,划伤比例为10%,说明对比例2中的重稀土涂覆层的耐划伤性更强。另外实施例2中样品表面的重稀土涂覆层在高温扩散过程中存在收缩的情况所占比例为11%,而对比例2中样品表面的重稀土涂覆层在高温扩散过程中没有出现收缩的情况,说明对比例2中所制备的具有特殊结构的重稀土涂覆层与实施例2中制备的重稀土涂覆层相比具有更强的耐收缩性。
[0066]
由表3可见,在相同的重稀土增重条件下,实施例2中的磁体扩散后br下降了0.09kgs,hcj增长了3.81koe,方形度下降了0.008。对比例2中的磁体扩散后br下降了0.1kgs,hcj增加了3.3koe,方形度下降了0.009。从上述结果可以看出实施例2和对比例2的扩散方案均能实施钕铁硼磁体的性能提升,但是实施例2中的方案的在重稀土增重量相同的条件下,矫顽力增加幅度更高。
[0067]
将扩散前的钕铁硼磁体,实施例2中扩散完成的钕铁硼磁体,对比例2中扩散完成的钕铁硼磁体,分别沿扩散方向均匀切割成3份后进行磁性能测试,对比扩散后的磁体性能均匀性,对比表格4如下。
[0068]
表4由实施例2和对比例2得到的磁体性能均匀性对比
[0069][0070]
由表4可见,在相同的重稀土增重和扩散工艺条件下,实施例2中的磁体扩散后沿扩散方向最表层位置样品与最中心样品的矫顽力偏差为0.8koe,且最中心位置处的样品的hcj较基体提高了3koe。对比例2中的磁体扩散后沿扩散方向最表层位置样品与最中心样品的矫顽力偏差为1.3koe,且最中心位置处的样品的hcj较基体提高了2.06koe,另外实施例2中磁体扩散后中心位置处的性能比对比例2中扩散后磁体中心位置处的性能高0.94koe,通过上述对比可知实施例2中的磁体扩散深度更深,扩散更加均匀。
[0071]
实施例3
[0072]
(s1)使用粒度为10μm的氢化铽粉末作为重稀土扩散源,橡胶类粘接剂,苯类有机溶剂,粒度为100μm的球形氮化硼陶瓷粉共4种原料作为重稀土浆料的原料,首先将氢化铽粉末与球形氮化硼粉末混合,其中氮化硼陶瓷粉的重量为氢化铽粉末重量的10%,并将混合后的粉末作为扩散源中间体,之后将扩散源中间体与橡胶类粘接剂,苯类有机溶剂分别按照占比为80%,6%,14%的比例混合并搅拌均匀后制备成重稀土浆料。
[0073]
(s2)将上述重稀土浆料使用喷涂的方式涂覆到上述10*10*6mm的钕铁硼基体上的两个10*10mm的表面上,并进行烘干后形成具有特殊结构的重稀土涂覆层,并控制涂覆层中
重稀土的重量与钕铁硼基体的重量比例为1.0%;其中,所述钕铁硼基体为经过熔炼,制粉,成型,烧结时效工序制得n55h牌号毛坯,并经过加工得到10*10*6mm尺寸的基体。
[0074]
(s3)将涂覆后重稀土涂覆层的钕铁硼磁体在氩气保护氛围下进行扩散时效,扩散工艺为950℃*30h 600℃*10h,之后对扩散完成后的产品测试整体磁性能。
[0075]
对扩散完成后的产品沿扩散方向均匀切割成5个,测试扩散后的沿扩散方向不同位置处的磁体的磁性能。为了充分展示本专利方案与传统涂覆扩散方案的相比所具有的技术优势,我们还设置有对比例3。
[0076]
对比例3
[0077]
(s1)使用粒度为10μm的氢化铽粉末作为重稀土扩散源,橡胶类粘接剂,苯类有机溶剂粉共3种物质作为重稀土浆料的原料,将氢化铽粉末与橡胶类粘接剂,苯类有机溶剂分别按照占比为80%,6%,14%的比例混合并搅拌均匀后制备成重稀土浆料;
[0078]
(s2)将上述重稀土浆料使用喷涂的方式涂覆到上述10*10*6mm的钕铁硼基体上的两个10*10mm的表面上,并进行烘干后形成具有特殊结构的重稀土涂覆层,并控制涂覆层中重稀土的重量与钕铁硼基体的重量比例为1.0%;其中,钕铁硼基体为经过熔炼,制粉,成型,烧结时效工序制得n55h牌号毛坯,并经过加工得到10*10*6mm尺寸的基体。
[0079]
(s3)将涂覆后重稀土涂覆层的钕铁硼磁体在氩气保护氛围下进行扩散时效,扩散工艺为950℃*30h 600℃*10h,之后对扩散完成后的产品测试整体磁性能。
[0080]
对扩散完成后的产品沿扩散方向均匀切割成5个,测试扩散后的沿扩散方向不同位置处的磁体的磁性能。
[0081]
为了对比实施例和对比例中重稀土涂覆层的耐划伤性,将实施例3中涂覆有重稀土涂覆层的样品与对比例3中涂覆有特殊结构的重稀土涂覆层的样品的涂覆面接触进行相互摩擦实验,统计实施例3和对比例3中的样品表面的重稀土膜层划伤并漏出基体的面积占总涂覆面积的比例,将统计数据记录在表5中并命名为划伤比。
[0082]
为了对比实施例和对比例中重稀土涂覆层在高温扩散过程中的耐收缩性,分别取实施例3中的扩散品和对比例3中的扩散品各100片,统计扩散后存在重稀土膜层收缩现象的样品数量与总统计数量的比例,将统计数据记录在表5中并命名为收缩比。
[0083]
将扩散前的钕铁硼磁体性能,实施例3中扩散完成的钕铁硼磁体的整体性能,对比例3中扩散完成的钕铁硼磁体的整体性能进行对比,对比表格5如下。
[0084]
表5通过实施例1和对比例1得到的磁体性能对比
[0085]
样品名称划伤比收缩比br(kgs)hcj(koe)hk/hcjn55h基体//14.6115.520.989实施例39%6%14.3826.80.980对比例30%0%14.36260.975
[0086]
由表5可见,对比例3中涂覆有特殊结构重稀土涂覆层的样品在与实施例3中涂覆有重稀土涂覆层的样品进行相互摩擦实验时没有划伤,而实施例3中的样品存在划伤,划伤比例为9%,说明对比例3中的重稀土涂覆层的耐划伤性更强。另外实施例3中样品表面的重稀土涂覆层在高温扩散过程中存在收缩的情况所占比例为6%,而对比例3中样品表面的重稀土涂覆层在高温扩散过程中没有出现收缩的情况,说明对比例3中所制备的具有特殊结构的重稀土涂覆层与实施例3中制备的重稀土涂覆层相比具有更强的耐收缩。
[0087]
由表5可见,在相同的重稀土增重条件下,实施例3中的磁体扩散后br下降了0.23kgs,hcj增长了11.28koe,方形度下降了0.009。对比例3中的磁体扩散后br下降了0.25kgs,hcj增加了10.48koe,方形度下降了0.014。从上述结果可以看出实施例3和对比例3的扩散方案均能实施钕铁硼磁体的性能提升,但是实施例3中的方案的在重稀土增重量相同的条件下,矫顽力增加幅度更高。
[0088]
将扩散前的钕铁硼磁体,实施例3中扩散完成的钕铁硼磁体,对比例3中扩散完成的钕铁硼磁体,分别沿扩散方向均匀切割成5份后进行磁性能测试,对比扩散后的磁体性能均匀性,对比表格6如下。
[0089]
表6由实施例1和对比例1得到的磁体性能均匀性对比
[0090][0091]
由表6可见,在相同的重稀土增重和扩散工艺条件下,实施例3中的磁体扩散后沿扩散方向最表层位置样品与最中心样品的矫顽力偏差为1.7koe,且最中心位置处的样品的hcj较基体提高了10koe。对比例3中的磁体扩散后沿扩散方向最表层位置样品与最中心样品的矫顽力偏差为2.55koe,且最中心位置处的样品的hcj较基体提高了8.8koe,另外实施例3中磁体扩散后中心位置处的性能比对比例3中扩散后磁体中心位置处的性能高1.2koe,通过上述对比可知实施例3中的磁体扩散深度更深,扩散更加均匀。
[0092]
实施例4
[0093]
(s1)使用粒度为5μm的氢化铽粉末作为重稀土扩散源,树脂类粘接剂,酯类有机溶剂,粒度为50μm的球形氧化锆陶瓷粉共4种原料作为重稀土浆料的原料,首先将氢化铽粉末与球形氧化锆粉末混合,其中氧化锆陶瓷粉的重量为氢化铽粉末重量的30%,并将混合后的粉末作为扩散源中间体,之后将扩散源中间体与树脂类粘接剂,酯类有机溶剂分别按照占比为60%,8%,32%的比例混合并搅拌均匀后制备成重稀土浆料。
[0094]
(s2)将上述重稀土浆料使用喷涂的方式涂覆到上述10*10*8mm的钕铁硼基体上的两个10*10mm的表面上,并进行烘干后形成具有特殊结构的重稀土涂覆层,并控制涂覆层中重稀土的重量与钕铁硼基体的重量比例为1.5%;其中,钕铁硼基体为经过熔炼,制粉,成型,烧结时效工序制得n42h牌号毛坯,并经过加工得到10*10*8mm尺寸的基体。
[0095]
(s3)将涂覆后重稀土涂覆层的钕铁硼磁体在真空下进行扩散时效,扩散工艺为900℃*40h 650℃*8h,之后对扩散完成后的产品测试整体磁性能。
[0096]
对扩散完成后的产品沿扩散方向均匀切割成5个,测试扩散后的沿扩散方向不同位置处的磁体的磁性能。为了充分展示本专利方案与传统涂覆扩散方案的相比所具有的技术优势,设置有对比例4。
[0097]
对比例4
[0098]
(s1)使用粒度为5μm的氢化铽粉末作为重稀土扩散源,树脂类粘接剂,酯类有机溶剂共3种物质作为重稀土浆料的原料,将氢化铽粉末与树脂类粘接剂,酯类有机溶剂分别按照占比为60%,8%,32%的比例混合并搅拌均匀后制备成重稀土浆料。
[0099]
(s2)将上述重稀土浆料使用喷涂的方式涂覆到上述10*10*8mm的钕铁硼基体上的两个10*10mm的表面上,并进行烘干后形成具有特殊结构的重稀土涂覆层,并控制涂覆层中重稀土的重量与钕铁硼基体的重量比例为1.5%;其中,所述钕铁硼基体为经过熔炼,制粉,成型,烧结时效工序制得n42h牌号毛坯,并经过加工得到10*10*8mm尺寸的基体。
[0100]
(s3)将涂覆后重稀土涂覆层的钕铁硼磁体在真空下进行扩散时效,扩散工艺为900℃*40h 650℃*8h,之后对扩散完成后的产品测试整体磁性能。
[0101]
对扩散完成后的产品沿扩散方向均匀切割成5个,测试扩散后的沿扩散方向不同位置处的磁体的磁性能。
[0102]
为了对比实施例和对比例中重稀土涂覆层的耐划伤性,将实施例4中涂覆有重稀土涂覆层的样品与对比例4中涂覆有特殊结构的重稀土涂覆层的样品的涂覆面接触进行相互摩擦实验,统计实施例4和对比例4中的样品表面的重稀土膜层划伤并漏出基体的面积占总涂覆面积的比例,将统计数据记录在表7中并命名为划伤比。
[0103]
为了对比实施例和对比例中重稀土涂覆层在高温扩散过程中的耐收缩性,分别取实施例4中的扩散品和对比例4中的扩散品各100片,统计扩散后存在重稀土膜层收缩现象的样品数量与总统计数量的比例,将统计数据记录在表7中并命名为收缩比。
[0104]
将扩散前的钕铁硼磁体性能,实施例4中扩散完成的钕铁硼磁体的整体性能,对比例4中扩散完成的钕铁硼磁体的整体性能进行对比,对比表格7如下。
[0105]
表7通过实施例1和对比例1得到的磁体性能对比
[0106]
样品名称划伤比收缩比br(kgs)hcj(koe)hk/hcjn42h基体//13.2018.050.981实施例421%13%12.92300.972对比例40%0%12.8829.450.968
[0107]
由表7可见,对比例4中涂覆有特殊结构重稀土涂覆层的样品在与实施例4中涂覆有重稀土涂覆层的样品进行相互摩擦实验时没有划伤,而实施例4中的样品存在划伤,划伤比例为21%,说明对比例4中的重稀土涂覆层的耐划伤性更强。另外实施例4中样品表面的重稀土涂覆层在高温扩散过程中存在收缩的情况所占比例为13%,而对比例4中样品表面的重稀土涂覆层在高温扩散过程中没有出现收缩的情况,说明对比例4中所制备的具有特殊结构的重稀土涂覆层与实施例4中制备的重稀土涂覆层相比具有更强的耐收缩。
[0108]
由表7可见,在相同的重稀土增重条件下,实施例4中的磁体扩散后br下降了0.28kgs,hcj增长了11.95koe,方形度下降了0.009。对比例4中的磁体扩散后br下降了0.32kgs,hcj增加了11.4koe,方形度下降了0.013。从上述结果可以看出实施例4和对比例4的扩散方案均能实施钕铁硼磁体的性能提升,但是实施例4中的方案的在重稀土增重量相同的条件下,矫顽力增加幅度更高。
[0109]
将扩散前的钕铁硼磁体,实施例4中扩散完成的钕铁硼磁体,对比例4中扩散完成的钕铁硼磁体,分别沿扩散方向均匀切割成5份后进行磁性能测试,对比扩散后的磁体性能均匀性,对比表格8如下。
[0110]
表8由实施例1和对比例1得到的磁体性能均匀性对比
[0111][0112]
由表8可见,在相同的重稀土增重和扩散工艺条件下,实施例4中的磁体扩散后沿扩散方向最表层位置样品与最中心样品的矫顽力偏差为2.81koe,且最中心位置处的样品的hcj较基体提高了10.02koe。对比例4中的磁体扩散后沿扩散方向最表层位置样品与最中心样品的矫顽力偏差为3.75koe,且最中心位置处的样品的hcj较基体提高了9.09koe,另外实施例4中磁体扩散后中心位置处的性能比对比例4中扩散后磁体中心位置处的性能高1.11koe,通过上述对比可知实施例4中的磁体扩散深度更深,扩散更加均匀。
[0113]
以上所述仅为本发明的较佳实施例,并不用以限制本发明,凡在本发明的精神和原则之内,所作的任何修改、等同替换、改进等,均应包含在本发明的保护范围之内。
再多了解一些
本文用于创业者技术爱好者查询,仅供学习研究,如用于商业用途,请联系技术所有人。