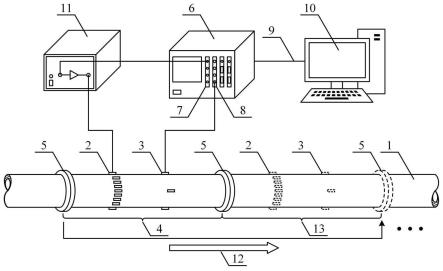
一种基于反射的l(0,1)导波的连续管道腐蚀定量检测方法
技术领域
1.本发明属于工程结构检测技术领域,具体来说是采用在连续管道中制造不连续的方式生成反射的l(0,1)导波,使用反射的l(0,1)导波对连续管道的腐蚀程度进行定量检测。
背景技术:
2.管道是重要的基础设施,广泛应用于水、石油、天然气等物资的输送。管道的运行环境通常较为恶劣,且具有一定的腐蚀性。管道内部和外部腐蚀介质的作用,以及内部输送介质的高速冲刷等会导致管道发生全面腐蚀。管道的全面腐蚀会减少管道的壁厚,从而降低管道的承载力和完整性,威胁管道的运行安全,造成巨大的经济损失。因此,为了保障管道的运行安全,有效检测腐蚀引起的管道的壁厚损失十分重要。腐蚀的发生和发展是一个复杂的动态过程,在各种复杂因素的影响下,腐蚀速率可能会加速,导致管道在常规检测前突发失效。另外,管道结构较长,有些区域难以接近。因此,需要检测技术不仅具有较高的壁厚损失分辨率,而且能够快速、全面、定量地检测整个管道结构的腐蚀。
3.传统的超声测试技术可以精确测量管道的壁厚。但是,该方法需要逐点扫描管道表面,操作复杂,检测低效,不能检测管道上隐蔽和无法到达的区域,不适用于对长距离管道进行快速、全面的检测。而且,超声测试对检测条件要求高,易受外界因素干扰;例如,当超声探头和管道表面耦合效果不足,或管道表面积累较多沉积物时,其检测精度显著降低。另外,涡流、漏磁、x-射线等传统的检测技术也被广泛用于腐蚀检测,但是都存在和超声测试类似的不足。
4.超声导波技术可以有效检测管道腐蚀。超声导波可以沿整个管壁传播较长的距离、且衰减小;该方法简单高效,能够快速、全面地检测长距离管段,包括物理上无法到达的区域。然而,现有的基于导波的检测方法主要能够对管道腐蚀深度提供定性的评价,没有从理论上建立评价指标与腐蚀深度之间的定量关系模型,难以有效量化腐蚀引起的管道的壁厚损失。此外,如何提高对微小腐蚀的分辨率也充满了挑战。
技术实现要素:
5.为了解决上述存在的问题,本发明提出:一种基于反射的l(0,1)导波的连续管道腐蚀定量检测方法,包括如下步骤:s1、选择激励信号,根据导波的频散方程,通过频散分析软件计算待检测连续管道的群速度频散曲线,选择频散范围内的l(0,1)导波作为激励模态,利用l(0,1)导波的走时变化识别腐蚀引起的管道的壁厚损失;
6.s2、导波激励阵列和接收阵列的布设,分别将激励阵列和接收阵列布设在待检测管段内部的两个对称的位置,激励阵列和接收阵列分别由若干沿管道周向等间距分布的压电传感器组成,激励阵列激发导波信号,接收阵列中各接收传感器单独接收导波信号,各接收传感器所在的待检测管段的轴向路径作为该传感器的检测路径;
7.s3、在连续管道中制造不连续和生成反射的l(0,1)导波,制作两个相同的可快速
拆卸和重复使用的金属环,每个金属环分别由两个相同的半金属环组成,在待检测管段的两端各粘贴一个金属环,从而在连续管道中制造不连续和形成轴对称的结构特征,所激发的l(0,1)导波在制造的不连续处会生成反射的l(0,1)导波;
8.s4、建立反射的l(0,1)导波的走时变化与壁厚损失的定量关系模型,根据反射的l(0,1)导波的累积传播长度,通过频散分析软件获取不同壁厚损失引起的反射的l(0,1)导波的走时变化,得到反射的l(0,1)导波的走时变化与壁厚损失的定量关系模型,所选频散范围内的l(0,1)导波的走时变化与其传播长度呈正相关,与直达的l(0,1)导波相比,反射的l(0,1)导波在确定的范围有更长的累积传播长度,通过累积传播长度的增加实现对壁厚损失的高分辨率测量,待检测管段的壁厚损失及其对应的反射的l(0,1)导波的走时变化的表达式为:
[0009][0010]
其中,δd和δtr分别为待检测管段的壁厚损失和对应的反射的l(0,1)导波的走时变化;dh和dc分别为待检测管段初始状态和腐蚀后的壁厚;t
rh
和t
rc
分别为反射的l(0,1)导波在待检测管段初始状态和腐蚀后的走时;c
gh
和c
gc
分别为l(0,1)导波在待检测管段初始状态和腐蚀后的群速度;lr为反射的l(0,1)导波的累积传播长度。
[0011]
s5、在连续管道初始状态下激发和采集导波信号,模块化机箱包括波形发生器和示波器,通过连接线与计算机连接,由波形发生器生成的导波信号,经过功率放大器后输入激励阵列激发l(0,1)导波,示波器分别连接各接收传感器采集反射的l(0,1)导波信号,进一步传送至计算机,所采集的信号作为基准信号;
[0012]
s6、在连续管道不同腐蚀状态下,再分别按s5激发和采集导波信号,得到不同腐蚀程度下的反射的l(0,1)导波信号;
[0013]
s7、分析腐蚀前后反射的l(0,1)导波的走时,判断走时增加即为发生了腐蚀,提取反射的l(0,1)导波的走时变化,并结合s4建立的定量关系模型推导出待检测管段的壁厚损失;
[0014]
s8、连续管道腐蚀的分布式检测,由上述各步骤完成该管段腐蚀的检测后,沿着连续管道的检测方向,将远离下一管段的金属环拆卸并安装在下一管段的另一侧,使用该方法对下一管段检测,以此类推,实现对连续管道的大范围和分布式检测。
[0015]
本发明的有益效果为:这种基于反射的l(0,1)导波的连续管道腐蚀定量检测方法,只需要将两个相同的金属环粘贴在待检测管段的两端,就可以在该管段两端制造不连续和形成轴对称结构特征,从而实现反射的l(0,1)导波的生成。通过计算不同腐蚀程度下反射的l(0,1)导波的走时变化,并结合建立的反射的l(0,1)导波的走时变化与壁厚损失的定量关系模型,便可量化该管段的壁厚损失,反射的l(0,1)导波在确定范围内有更长的累积传播长度,大大增加了壁厚损失所引起的l(0,1)模态的走时变化,从而实现了对壁厚损失的高分辨率测量。该方法与已有的导波方法相比,对壁厚损失具有更高的分辨率和量化精度。另外,将这种检测方法应用于不同的管段就可以大范围、分布式检测连续管道的腐蚀。因此,该方法可以全面评估管道的承载力和完整性,有效预测管道的剩余使用寿命。相比传统的点式检测技术,该方法简单高效,仅使用少量永久检测点就可以快速、全面检测整
个管道的腐蚀,不会漏检。在管道中制造不连续的装置拆卸方便,可以重复使用,检测成本低。
附图说明
[0016]
图1为本发明的基于反射的l(0,1)导波的连续管道腐蚀定量检测方案示意图;
[0017]
图2为本发明制作的金属环示意图;
[0018]
图3为本发明的反射的l(0,1)导波的走时变化和壁厚损失的定量关系模型;
[0019]
图4为本发明的在连续管道初始状态和不同腐蚀时间下单一接收传感器接收的导波数据;
[0020]
图5为本发明的在连续管道不同腐蚀时间下分别由本发明方法和超声测试测量的壁厚损失。
[0021]
图中:1、连续管道,2、激励阵列,3、接收阵列,4、待检测管段,5、金属环,6、模块化机箱,7、波形发生器,8、示波器,9、连接线,10、计算机,11、功率放大器,12、检测方向,13、下一管段。
具体实施方式
[0022]
提出一种基于反射的l(0,1)导波的连续管道腐蚀定量检测方法,具体实现如下:
[0023]
实施例1
[0024]
图1出示了基于反射的l(0,1)导波的连续管道腐蚀定量检测方案示意图,图2出示了制作的金属环示意图。这种基于反射的l(0,1)导波的连续管道腐蚀定量检测方法包括下列步骤:
[0025]
第一步、激励信号的选择,根据导波的频散方程,通过频散分析软件计算待检测连续管道1的群速度频散曲线,选择频散范围内的l(0,1)导波作为激励模态,由于l(0,1)导波在频散范围内其走时受管道壁厚影响,利用其走时变化可识别腐蚀引起的管道的壁厚损失;
[0026]
第二步、导波激励阵列2和接收阵列3的布设,分别将激励阵列2和接收阵列3布设在待检测管段4内部的两个对称的位置,激励阵列2和接收阵列3分别由若干沿管道周向等间距分布的压电传感器组成,激励阵列2激发导波信号,接收阵列3中各接收传感器单独接收导波信号,各接收传感器所在的待检测管段4的轴向路径作为该传感器的检测路径;
[0027]
第三步、在连续管道1中制造不连续和生成反射的l(0,1)导波,制作两个相同的可快速拆卸和重复使用的金属环5,每个金属环5分别由两个相同的半金属环组成,在待检测管段4的两端各粘贴一个金属环5,从而在连续管道1中制造不连续和形成轴对称的结构特征,所激发的l(0,1)导波在制造的不连续处会生成反射的l(0,1)导波;
[0028]
第四步、建立反射的l(0,1)导波的走时变化与壁厚损失的定量关系模型,根据反射的l(0,1)导波的累积传播长度,通过频散分析软件获取不同壁厚损失引起的反射的l(0,1)导波的走时变化,得到反射的l(0,1)导波的走时变化与壁厚损失的定量关系模型,所选频散范围内的l(0,1)导波的走时变化与其传播长度呈正相关,与直达的l(0,1)导波相比,反射的l(0,1)导波在确定的范围有更长的累积传播长度,通过累积传播长度的增加实现对壁厚损失的高分辨率测量,待检测管段4的壁厚损失及其对应的反射的l(0,1)导波的走时
变化的表达式为:
[0029][0030]
其中,δd和δtr分别为待检测管段4的壁厚损失和对应的反射的l(0,1)导波的走时变化;dh和dc分别为待检测管段4初始状态和腐蚀后的壁厚;t
rh
和t
rc
分别为反射的l(0,1)导波在待检测管段4初始状态和腐蚀后的走时;c
gh
和c
gc
分别为l(0,1)导波在待检测管段4初始状态和腐蚀后的群速度;lr为反射的l(0,1)导波的累积传播长度。
[0031]
第五步、在连续管道1初始状态下激发和采集导波信号,模块化机箱6包括波形发生器7和示波器8,模块化机箱6通过连接线9与计算机10连接,由波形发生器7生成的导波信号,经过功率放大器11后输入激励阵列2激发l(0,1)导波,示波器8分别连接各接收传感器采集反射的l(0,1)导波信号,进一步传送至计算机10,所采集的信号作为基准信号;
[0032]
第六步、在连续管道1不同腐蚀状态下,再分别按步骤五激发和采集导波信号,得到不同腐蚀程度下的反射的l(0,1)导波信号;
[0033]
第七步、分析腐蚀前后反射的l(0,1)导波的走时,判断走时增加即为发生了腐蚀,提取反射的l(0,1)导波的走时变化,并结合步骤四建立的定量关系模型推导出待检测管段4的壁厚损失;
[0034]
第八步、连续管道1腐蚀的分布式检测,由上述各步骤完成该管段4腐蚀的检测后,沿着连续管道1的检测方向12,将远离下一管段13的金属环5拆卸并安装在下一管段13的另一侧,使用该方法对下一管段13检测,以此类推,实现对连续管道1的大范围和分布式检测。
[0035]
所述连续管道1仅针对连续式的直管道,而对于分段式或含有弯头等更为复杂的管道则不在此方法的适用范围之内。
[0036]
所述连续管道1的腐蚀仅针对全面腐蚀,而对于局部腐蚀则不在此方法的适用范围之内。
[0037]
所述压电传感器为长度伸缩型,激励阵列2中压电传感器同时激发,且数量足够,可以只激发出纵向模态。
[0038]
所述l(0,1)导波的频率低于l(0,2)导波的截止频率,作用在激励阵列2的压电传感器上可以激发出单一的l(0,1)导波。
[0039]
各接收传感器采集的导波信号主要包含该传感器所在轴向路径的腐蚀信息,因此,接收传感器的数量需根据实际需要检测的轴向路径数目确定。
[0040]
激发的单一的l(0,1)导波为纵向轴对称模态,其从轴对称结构特征处反射的模态仅包含l(0,1)模态。
[0041]
在保证从不连续处反射的l(0,1)导波较清晰,且可以与其他位置反射的导波有效分离的条件下,尽量选择在待检测管段4内多次反射的l(0,1)导波,进一步增加累积传播长度,从而获取更高的壁厚损失分辨率。
[0042]
所述计算机10包含控制程序,用于激励信号的设置、采集的导波信号的显示和储存。
[0043]
本发明所提出的基于反射的l(0,1)导波的连续管道腐蚀定量检测方法,通过在待检测管段的两端制造不连续,实现反射的l(0,1)导波的生成。建立反射的l(0,1)导波的走
时变化与腐蚀引起的壁厚损失的定量关系模型,结合实测的反射的l(0,1)导波的走时变化和该定量关系模型量化该管段的壁厚损失,通过累积传播长度的增加实现对壁厚损失的高分辨率测量。另外,将该方法应用于不同管段的腐蚀检测,便可实现对连续管道的壁厚损失的分布式和大范围检测。相比已有导波方法,该方法对壁厚损失有更高的分辨率和量化精度,有效保障了连续管道的运行安全。
[0044]
试验案例
[0045]
为了验证本发明对连续管道腐蚀定量检测的有效性,选取一根长度5.06m,外径60mm,壁厚7mm的钢管进行腐蚀检测试验。通过绘制该管道的频散曲线,选取中心频率为25khz,汉宁窗调制的20周期正弦波作为激励信号。激励阵列和接收阵列分别布设在距管道左端2.055m和3.005m的位置,压电传感器的型号为p51。两个相同的金属环分别粘贴在距激励阵列左侧1.055m和距接收阵列右侧1.055m的管道位置处,从而在管道中制造不连续,进而生成反射的l(0,1)导波。由于试验管道长度的限制,仅选择第一个反射的l(0,1)导波,根据第一个反射的l(0,1)导波的累积传播长度,建立了反射的l(0,1)导波的走时变化和壁厚损失的定量关系模型,如图3所示。采用外加直流电源的方法加速管道整个内壁的腐蚀,试验工况共包括5种,即管道初始状态、腐蚀140h、200h、327h、470h。在每种工况下,利用激励阵列激发l(0,1)导波,使用单个接收传感器接收导波信号,结果如图4所示。在不同腐蚀时间下,使用本发明方法测量了待检测管段上该接收传感器对应检测路径的壁厚损失,另外,采用了超声波测厚仪测量了该检测路径的壁厚损失,将本发明方法测量的壁厚损失和超声测试测量的壁厚损失进行了对比,结果如图5所示。
[0046]
由图4可以看出,反射的l(0,1)导波可以在制造的不连续处明显生成。随着腐蚀时间的增加,导波信号逐渐向右偏移,当腐蚀程度较小时,直达的l(0,1)导波的走时变化较小,反射的l(0,1)导波的走时变化较大。相同腐蚀时间下,反射的l(0,1)导波的走时变化远大于直达的l(0,1)导波的走时变化,表明反射的l(0,1)导波对腐蚀更加敏感,可以更加准确地提供腐蚀发生和发展的信息。
[0047]
由图5可知,随着腐蚀时间的增加,由该方法测量的壁厚损失逐渐增加,没有波动情况。整个腐蚀过程中,在相同腐蚀时间下,由该方法测量的壁厚损失与超声测试测量的壁厚损失较为一致,表明该检测方法可以精确测量腐蚀引起的壁厚损失。另外,该方法不仅具有较高的壁厚损失分辨率,而且具有较大的壁厚损失检测范围。该试验仅使用第一个反射的l(0,1)导波就可以有效量化待检测管段的壁厚损失。连续管道结构通常较长,实际应用中,在保证从不连续处反射的l(0,1)导波较清晰,且可以与其他位置反射的导波有效分离的条件下,尽量选择在待检测管段内多次反射的l(0,1)导波,进一步增加累积传播长度,从而获取更高的壁厚损失分辨率。
[0048]
试验结果表明了该检测方法可以定量检测连续管道的腐蚀,根据该方法测量的壁厚损失,可以进一步有效评估连续管道的承载力和完整性,保障连续管道的运行安全。
[0049]
该方法通过在待检测管段的两端制造不连续实现反射的l(0,1)导波的生成,并建立反射的l(0,1)导波的走时变化和壁厚损失的定量关系模型,结合实测的反射的l(0,1)导波的走时变化和该定量关系模型测量该管段的壁厚损失,反射的l(0,1)导波在确定的范围具有更长的累积传播长度,增加了相同壁厚损失所引起的导波走时变化,从而增加了对壁厚损失的敏感性,实现了对壁厚损失的高分辨率测量,与已有的导波方法相比,该方法具有
更高的壁厚损失分辨率和检测精度。另外,该方法可以应用于不同管段的壁厚损失的测量,实现对连续管道腐蚀的大范围和分布式检测,大大提高了检测效率,克服了传统的点式检测技术的缺陷,为确保连续管道的安全运行提供了有效保障。
[0050]
以上所述,仅为本发明较佳的具体实施方式,但本发明的保护范围并不局限于此,任何熟悉本技术领域的技术人员在本发明披露的技术范围内,根据本发明的技术方案及其构思加以等同替换或改变,都应涵盖在本发明的保护范围之内。
再多了解一些
本文用于创业者技术爱好者查询,仅供学习研究,如用于商业用途,请联系技术所有人。