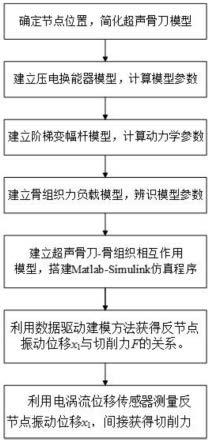
基于反节点振动位移的超声骨切削力的间接测量方法
1.发明名称
2.基于反节点振动位移的超声骨切削力的间接测量方法。
技术领域
3.本发明属于机器人超声骨刀加工应用领域,具体涉及基于反节点振动位移的超声骨切削力的间接测量方法。
背景技术:
4.超声骨刀作为一种新型手术器械,高频电信号通过磁致伸缩换能器或压电陶瓷换能器转化为高频机械振动,激起刀具的高频纵向振动模态,实现上百微米级振幅的超声振动进行切削。相对于传统的骨切削工具,超声骨刀具有低切削力、低切削温度和组织选择性等优点,近年来一直作为手持工具被外科医生广泛应用于脊柱外科、颌面外科、整形外科等领域,然而超声骨刀在骨科机器人中的应用尚未见报道。超声骨刀对末端切削力敏感,切削力的大小会影响切削稳定性(改变骨刀谐振频率、振动幅值)、切削质量,进而影响手术效果。因此,超声骨刀切削力的检测模型,是超声骨刀应用在机器人辅助手术中的一个亟待解决的问题,对在手术过程中实现骨质层感知、切削力控制具有重要意义。
技术实现要素:
5.针对现有技术存在的问题,本发明提供基于反节点振动位移的超声骨切削力的间接测量方法。
6.本发明的技术方案是:
7.基于反节点振动位移的超声骨切削力的间接测量方法,包括以下步骤:
8.步骤1:确定超声骨刀节点位置,得到超声骨刀的简化模型。
9.步骤2:建立压电换能器模型,计算模型参数,获得压电换能器的振动位移。
10.步骤3:建立阶梯变幅杆模型,根据特征值、特征向量和能量守恒原则计算动力学参数。
11.步骤4:建立骨组织的力负载模型,辨识模型参数。
12.步骤5:建立超声骨刀-骨组织相互作用模型,搭建matlab-simulink仿真程序。
13.步骤6:基于matlab-simulink仿真程序,利用数据驱动建模方法,以反节点振动位移x1的有效值x
1rms
、振动频率f
x1
为输入,输出切削力的有效值f
rms
,获得反节点振动位移x1与切削力f的关系。
14.步骤7:利用电涡流位移传感器测量反节点振动位移的有效值x
1rms
及振动频率f
x1
,根据步骤6获得的关系计算切削力的有效值f
rms
。
15.有益效果
16.本发明将超声骨刀这一个复杂的连续系统(具有无限多个自由度)简化为一个2自由度的离散系统,该模型具有原始系统的属性,同时可以用于仿真。开发的一维数值计算模
型处理所需信息的速度比有限元、实验快得多,易于建立数据集。超声骨刀切削力的间接检测方法将促进超声骨刀在骨科机器人中的应用,为骨科机器人在手术过程中实现骨质层感知、切削力控制提供理论基础。
附图说明
17.图1是本发明具体实施方式的超声骨刀简化模型图;
18.图2是本发明具体实施方式的特征值特征向量获得示意图;
19.图3是本发明具体实施方式的骨组织的力负载模型图;
20.图4是本发明具体实施方式的matlab-simulink仿真模型示意图;
21.图5是本发明具体实施方式的反节点振动位移测量示意图;
22.图6是本发明具体实施方式的基于反节点振动位移的超声骨切削力的间接测量方法流程图。
具体实施方式
23.下面结合附图对本发明的具体实施方式做详细说明。
24.基于反节点振动位移的超声骨切削力的间接测量方法,如图6所示,包括以下步骤:
25.步骤1:确定超声骨刀节点位置,得到超声骨刀的简化模型。
26.超声骨刀的简化模型如图1,超声骨刀在纵向模态振动工作时,整个超声骨刀(不考虑刀头)有两个节点:一个位于两片压电陶瓷中间,另一个位于变幅杆台阶处;由于两片压电陶瓷中间存在节点,可防止超声波向后传播,因此忽略了节点左侧部分,超声骨刀的简化模型由两部分组成:压电换能器模型、阶梯变幅杆模型。
27.根据反节点个数将变幅杆简化为2自由度质量-弹簧-阻尼(msd)系统,它具有两个谐振频率,第一谐振频率对应于m1,m2同相振动。第二谐振频率对应于m1,m2反相振动。
28.步骤2:建立压电换能器模型,计算模型参数,获得压电换能器的振动位移。
29.压电换能器的工作原理是通过在压电陶瓷两端施加交变电压激励,利用压电材料的逆压电特性,使其产生纵向振动的压缩或膨胀变形。在不考虑压电材料的非线性的假设下,压电陶瓷的电气和机械行为之间的相互作用可以用以下线性关系来描述:
[0030][0031]
式中:s是应变,t是应力,se是恒定电场下的弹性柔度,d是压电电荷常数,d是介电位移,e是电场强度,ε
t
是恒定应力下的介电常数。
[0032][0033]
式中:s0是压电陶瓷截面积,l0是压电陶瓷厚度,x0是压电陶瓷的振动位移,f0是变幅杆施加到压电换能器的力,u是激励电压。
[0034]
将式(2)带入式(1),可得压电换能器的振动位移为
[0035]
[0036]
式中:为弹性柔度,d
33
为电荷常数,为介电常数。
[0037]
步骤3:建立阶梯变幅杆模型,根据特征值、特征向量和能量守恒原则计算动力学参数。
[0038]
步骤3-1:动力学建模
[0039]
根据euler-lagrange方程,无负载超声骨刀的动力学方程可以写成:
[0040][0041]
压电陶瓷与2-dof模型之间的相互作用力f0可表示为:
[0042][0043]
式中:m1,m2,k1,k2,c1,c2分别为等效质量、等效刚度和等效阻尼。x0为压电陶瓷的振动位移,x1,x2分别为m1,m2的振动位移。
[0044]
根据边界条件,超声骨刀的纵向振动位移可表示为:
[0045][0046]
式中:v1,v2为m1,m2的振动幅值,κ为圆波数,l0为变幅杆大圆柱长度,l1为变幅杆全长。
[0047]
步骤3-2:动力学参数辨识
[0048]
系统的质量矩阵、刚度矩阵、特征值、特征向量可以表示为:
[0049][0050]
式中:ω1为1阶固有频率,ω2为2阶固有频率,ψ1为与ω1对应的振幅比,ψ2为与ω2对应的振幅比。
[0051]
由特征方程mλψ=kψ,可得
[0052][0053]
然而,对于式(8)有四个未知参数(m1,m2,k1,k2)只有三个独立的方程,因此解是无限组合(无限个解)。根据能量守恒原则可以补充方程
[0054][0055]
联立方程式(8)、式(9)可得
[0056]
[0057]
由此,可以求解系统动力学参数(m1,m2,k1,k2)。
[0058]
系统特征值测量:利用ansys workbench 20.0软件中模态分析模块modal对超声骨刀进行模态分析,以获得2个纵向振动模态对应的振动频率ω1、ω2。
[0059]
系统特征向量测量:如图2特征值特征向量获得示意图,在超声骨刀模型前后两端创建两个参考点,连接参考点形成路径,通过ansysworkbench 20.0软件中的mems act插件和谐响应分析模块harmonic response对超声骨刀进行谐响应分析,对超声骨刀分别施加ω1,ω2频率的电压,得到超声骨刀沿路径的轴向振动位移分布曲线,计算对应频率的振幅比ψ1、ψ2后即可求得特征向量。
[0060]
通过调整系数c1,c2以调整模拟的超声波振动幅值x1,x2与实验测量值v1,v2相匹配。
[0061]
步骤4:建立骨组织的力负载模型,辨识模型参数。
[0062]
步骤4-1:力负载模型建立。
[0063]
超声骨刀切削过程中,刀具与骨组织之间的相互作用会对振动系统产生力负载,可用kelvin-voigt模型表示如图3,负载可以等效成一个弹性系数为k的线性弹簧和一个阻尼系数为c的阻尼器的模型。负载模型的动态响应可以由下式表示:
[0064][0065]
式中:k为刚度系数;c为阻尼系数;x2为刀具的振动位移;δ为初始干涉。
[0066]
步骤4-2:力负载模型参数辨识
[0067]
通过调整初始干涉、刚度系数和阻尼系数的值以匹配在超声骨切削有限元仿真中获得的切削力。
[0068]
步骤5:建立超声骨刀-骨组织相互作用模型,搭建matlab-simulink仿真程序。
[0069]
有负载超声骨刀的动力学方程可以写成:
[0070][0071]
式中:ψ2(ωf)为与ωf对应的振幅比。
[0072]
由式(12)可以看出,切削力f变化将导致超声骨刀谐振频率、振型发生变化,进而使振动位移x1或x2的变化,切削力f和振动位移x1或x2存在某种对应关系。因此,可以通过测量振动位移x1或x2的变化来反映切削力f。然而,一方面狭窄的切削区,不易固定安装传感器;另一方面冷却水雾、血液等恶劣的工作环境。这两方面导致振动位移x2无法测量,因此本文提出一种基于反节点振动位移x1的超声骨切削力的间接测量方法。
[0073]
根据式(3)、(5)、(11)建立matlab-simulink仿真模型如图4。切削力将导致超声骨刀谐振频率发生漂移,为保证骨刀以谐振频率工作,需要进行频率追踪。通过给系统输入50khz脉冲激励,测量系统输出,时间步长为1e-6,采样频率分辨率1hz,根据频响函数定义,将输入、输出数据进行傅里叶变换再相除,得到超声骨刀的频响函数,由此确定谐振频率。在仿真过程中超声骨刀采用恒压驱动策略,且使驱动电压频率=谐振频率,以模拟骨刀的
追频功能。
[0074]
步骤6:基于matlab-simulink仿真程序,利用数据驱动建模方法,以反节点振动位移x1的有效值x
1rms
、振动频率f
x1
为输入,输出切削力的有效值f
rms
,获得反节点振动位移x1与切削力f的关系。
[0075]
首先,将刚度系数设置为m水平,将阻尼系数设置为n水平,利用全因子实验设计m*n组仿真实验。接着,根据设计的实验在matlab-simulink仿真模型改变刚度系数和阻尼系数,并重置驱动电压频率,使其与刚度系数和阻尼系数对应的谐振频率相等进行仿真。然后记录反节点振动位移x1的有效值x
1rms
、振动频率f
x1
(与谐振频率相等)和切削力f的有效值f
rms
。最后,利用数据驱动建模方法获得反节点振动位移x1与切削力f的关系。
[0076]
步骤7:利用电涡流位移传感器测量反节点振动位移的有效值x
1rms
及振动频率f
x1
,根据步骤6获得的关系计算切削力的有效值f
rms
。
[0077]
如图5反节点振动位移测量示意图,包括外壳1、电涡流位移传感器2、标记物3、变幅杆4、安装有分析软件的计算机5、信号发生器6、功率放大器7。在变幅杆反节点x1位置安装标记物,标记物随变幅杆一起轴向方向往复振动。在骨刀外壳安装电涡流位移传感器,外壳与变幅杆节点连接,无运动。
[0078]
电涡流位移传感器2采用基恩士ex-305v,采样频率40khz,用于测量反节点振动位移x1信号。
[0079]
信号采集系统5采用ni 9234采集卡,用于采集来自位移位传感器的信号;
[0080]
安装有分析软件的计算机1用于对信号采集系统获得的位移信号进行分析,获得反节点振动位移x1的有效值x
1rms
、振动频率f
x
,进而计算切削力f的有效值f
rms
。
再多了解一些
本文用于创业者技术爱好者查询,仅供学习研究,如用于商业用途,请联系技术所有人。