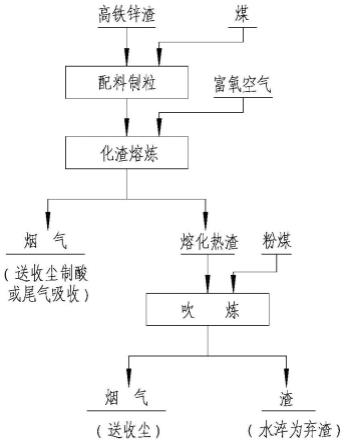
1.本发明涉及一种高铁锌渣的处理方法,属于火法冶金技术领域。
背景技术:
2.锌湿法冶金方法一般分为常规法及高温高酸法,含铁低的锌精矿适应于采用常规法,铁浸出进入溶液少,大多留在渣中,锌浸出渣一般采用回转窑处理,也有锌浸出渣与铅精矿或铅渣搭配处理的方法。含铁高的锌精矿适应于采用高温高酸法,铁浸出进入溶液多,根据不同的溶液除铁方法,可产出含铁高的黄钾铁矾渣、针铁矿渣或赤铁矿渣,而氧压浸出高铁锌精矿(如铁闪锌矿)时,可同时浸锌除铁,氧浸渣经浮选也产出高铁氧浸尾渣,以上高铁锌渣含锌低而含铁高(zn 2~5wt%,fe 25~55wt%),一般都放置渣场堆存,由于日益严格的环保要求,锌浸出渣都需无害化处理。采用火法处理高铁锌渣,因渣含铁高,为减少渣量,一般不配入熔剂,由于渣中铁高,在熔炼过程中需提升炉温但会发生铁被还原而增加渣粘度影响放渣的问题,严重时会因结渣被迫停炉。我国目前将锌浸出渣经火法处理后都认定为一般固废,渣中铅锌含量可小于2%,其中铅一般在0.1~0.5%,这种渣在某些国家或地区可以堆存、销售;但也有某些国家或地区的环保要求认定,火法处理的弃渣中锌小于2%,铅小于0.01%,才是一般固废。如渣中铅锌超过上述含量还是被认定为危险固废,只能堆存,不能销售。而火法处理锌浸出渣中锌小于2%不难,但铅小于0.01%难度大。随着环保要求的不断提高,对火法处理锌浸出渣也提出了更高要求。
技术实现要素:
3.针对现有技术的不足,本发明的目的在于提供一种高铁锌渣的处理方法,以获得可满足更高环保要求的弃渣。
4.为了解决上述技术问题,本发明的技术方案如下:
5.一种高铁锌渣的处理方法,包括如下步骤:
6.s1、将高铁锌渣与碳源混合均匀,造粒,获得渣粒;
7.s2、将渣粒连续地加入熔炼炉中,对所述渣粒进行熔炼,获得熔渣;
8.s3、将所述熔渣间断地输入烟化炉,于1300-1350℃条件下吹炼50-60min,获得炉渣和烟气;
9.其中,所述烟化炉包括炉体,炉体的顶部设有进料口和烟道,炉体的底侧设有放渣口、第一喷嘴和第二喷嘴,所述第一喷嘴和第二喷嘴均位于放渣口的下方,第一喷嘴的喷吹方向与水平面平行,第二喷嘴的喷吹方向倾斜向上且与水平面的夹角为10-15
°
;
10.吹炼期间,控制烟化炉内渣位高度为500-600mm,按700-800nm3/t-高铁锌渣的量通过第一喷嘴和第二喷嘴向烟化炉内鼓入空气,控制各喷嘴的鼓风压力为60-80kpa,同时,以所述鼓入的空气作为载煤风,按150-200kg/t-高铁锌渣的量通过第一喷嘴和第二喷嘴喷入粉煤;
11.s4、对所述炉渣进行水淬,获得弃渣;
12.其中,所述弃渣中,zn的含量《0.5wt%,pb的含量<0.01wt%。
13.进一步地,s1中,所述碳源为煤。
14.进一步地,s1中,所述高铁锌渣中,zn的含量为2-5wt%,fe的含量为25-55wt%,pb的含量≤5wt%,s的含量≤15wt%。
15.进一步地,s1中,所述高铁锌渣包括氧浸尾渣、针铁矿渣、黄钾铁矾渣、赤铁矿渣中的一种或几种。
16.进一步地,所述氧浸尾渣中,fe含量为32-38%,zn含量为1-4%,pb含量为1.5-4.5%,s含量为10-18.0%,水含量为10-14%。
17.进一步地,所述针铁矿渣中,fe含量为32-40%,zn含量为3-7%,pb含量为1-5%,s含量为2-6%,水含量为10-14%。
18.进一步地,所述黄钾铁矾渣中,fe含量为20-30%,zn含量为2-6%,pb含量为2-4.5%,s含量为2-10%,水含量为10-14%。
19.进一步地,所述赤铁矿渣中,fe含量为50-60%,zn含量为1-5%,硫含量为2-6%。
20.进一步地,s2中,对所述渣粒进行富氧侧吹熔炼;熔炼时,通入氧气浓度为70-80wol%的富氧空气,控制熔炼温度为1250-1300℃,熔炼时间1.5~2.5h。
21.进一步地,s2中,将渣粒按12-22t/h的速度连续地加入熔炼炉中,更进一步为15-19t/h。
22.进一步地,s3中,每隔1.5-2.5h,向烟化炉输入1次熔渣,每次的输入量为14-32t,更进一步为16-29t。
23.进一步地,s3中,所述第一喷嘴和第二喷嘴设置于炉体的两个相对的侧壁上,同一侧壁上的第一喷嘴和第二喷嘴交错设置,第二喷嘴的数量占喷嘴总量的1/3~1/4。
24.可选地,将s3产出的烟气送收尘,产出的烟尘送入铅、锌冶炼系统进一步处理。
25.本发明将高铁锌渣与碳源混合造粒后熔炼,再将熔渣放入烟化炉进行还原吹炼,采用弱还原控温吹炼技术,即无熔剂强风溢煤—低渣位短周期吹炼方式,通过第二喷嘴斜向上喷入空气及粉煤,使部分粉煤溢出渣面燃烧以保持炉膛温度,这部分粉煤不参与还原反应,通过第一喷嘴喷入熔渣中的粉煤参与还原反应,由此既可将炉温保持在目标温度又可提供弱还原气氛,从而保证锌、铅挥发效果。采用低渣位使得部分粉煤可溢出渣面燃烧,同时因渣量少可加快吹炼速度,短周期可减少吹炼时间,而不让铁还原。通过避免铁被还原,可避免渣的粘度增加而影响放渣。
26.先造粒再熔炼,一方面可将高铁锌渣与碳源更好地混合均匀;另一方面,可避免细小的高铁锌渣与碳源飞扬而落不到熔池,导致原料浪费并影响熔炼效果,并造成环境污染。
27.与现有技术相比,本发明的有益效果如下:
28.(1)本发明的处理方法利用高铁锌渣中铁造渣,无需另外配入熔剂,有助于降低渣量,避免带来额外的处理负担。
29.(2)通过控制吹炼温度为1300-1350℃,可降低高铁渣型粘度,方便放渣;降低渣面,可减少吹炼时间,并使得部分粉末溢出渣面成为可能,解决了渣中铁因吹炼时间长而被还原的问题。
30.(3)采用倾斜喷吹的第二喷嘴,加强二次风量,达到了提升炉温而不使渣中铁还原的效果。
31.(4)本发明可获得满足更高环保要求的弃渣,zn《0.5wt%,pb《0.01wt%,实现了对高铁锌渣的进一步无害化处理,且铅、锌等元素富集进入烟尘,可进一步得到资源化利用。
附图说明
32.图1是本发明一种处理方法的工艺流程图。
33.图2是本发明的一种烟化炉的结构示意图。
34.图3是本发明的一种烟化炉的俯视图。
具体实施方式
35.以下将结合实施例来详细说明本发明。需要说明的是,在不冲突的情况下,本发明中的实施例及实施例中的特征可以相互组合。为叙述方便,下文中如出现“上”、“下”、“左”、“右”字样,仅表示与附图本身的上、下、左、右方向一致,并不对结构起限定作用。若无特别说,本发明中的相关百分数是指质量百分数。
36.实施例1
37.将黄钾铁矾渣17t(含fe 25.5%,zn 4.0%,pb 3.4%,s 8.2%,水份12%)与煤进行配料制粒后(配煤率为25%,即配入4.25t煤),连续地加入侧吹炉(进料速度为21.25t/h),通入氧气浓度为70~80vol%的富氧空气,控制温度1250℃进行化渣熔炼,采用连续加料间断放渣的方式(即将物料连续地加入侧吹炉,将熔化热渣间断地放入烟化炉),将熔化热渣间断地放入烟化炉(每隔2h放渣1次,每次输入量为22.4t),通过第一喷嘴和第二喷嘴向烟化炉内喷入二次风和粉煤(175kg/t-黄钾铁矾渣),控制温度1300℃,渣位高度500mm,吹炼50min,获得炉渣和烟气,炉渣经水淬得到弃渣14.8t(含fe 25.8%,zn 0.48%,pb《0.01%,s 0.48%);烟气经收尘获得烟尘;
38.吹炼时,二次风(空气)的鼓入量为800nm3/t-黄钾铁矾渣,喷嘴的鼓风压力为70kpa。
39.其中,所述烟化炉包括炉体1,炉体1的顶部设有进料口2和烟道3,炉体1的底侧设有放渣口4、第一喷嘴5和第二喷嘴6,所述第一喷嘴5和第二喷嘴6均位于放渣口4的下方,第一喷嘴5的喷吹方向与水平面平行,第二喷嘴6的喷吹方向倾斜向上且与水平面的夹角为13
°
;所述第一喷嘴5和第二喷嘴6设置于炉体1的两个相对的侧壁上,同一侧壁上的第一喷嘴和第二喷嘴交错设置,第二喷嘴6的数量占喷嘴总量的1/3。
40.实施例2
41.将针铁矿渣17t(含fe 36.4%,zn 5.0%,pb 2.9%,s 4.5%,水份12%)与煤进行配料制粒后(配煤率为28%),连续地加入侧吹炉(进料速度为17t/h),通入氧气浓度为70~80vol%的富氧空气,控制温度1250℃进行化渣熔炼,采用连续加料间断放渣的方式(即将物料连续地加入侧吹炉,将熔化热渣间断地放入烟化炉),将熔化热渣间断地放入烟化炉(每隔2h放渣1次,每次输入量为23.5t),通过第一喷嘴和第二喷嘴向烟化炉内喷入二次风和粉煤(185kg/t-针铁矿渣),控制温度1300℃,渣位高度500mm,吹炼时间50min,获得炉渣和烟气,炉渣经水淬得到弃渣15.3t(含fe 35.6%,zn 0.42%,pb《0.01%,s 0.42%);烟气经收尘获得烟尘;
42.吹炼时,二次风(空气)的鼓入量为780nm3/t-针铁矿渣,喷嘴的鼓风压力为70kpa。
43.其中,所述烟化炉包括炉体1,炉体1的顶部设有进料口2和烟道3,炉体1的底侧设有放渣口4、第一喷嘴5和第二喷嘴6,所述第一喷嘴5和第二喷嘴6均位于放渣口4的下方,第一喷嘴5的喷吹方向与水平面平行,第二喷嘴6的喷吹方向倾斜向上且与水平面的夹角为13
°
;所述第一喷嘴5和第二喷嘴6设置于炉体1的两个相对的侧壁上,同一侧壁上的第一喷嘴和第二喷嘴交错设置,第二喷嘴6的数量占喷嘴总量的1/3。
44.实施例3
45.将氧浸尾渣17t(含fe 35.8%,zn 2.8%,pb 2.4%,s14.0%,水份12%)与煤进行配料制粒后(配煤率为12%),连续地加入侧吹炉(进料速度为17t/h),通入氧气浓度为70~80vol%的富氧空气,控制温度1250℃进行化渣熔炼,采用连续加料间断放渣的方式(即将物料连续地加入侧吹炉,将熔化热渣间断地放入烟化炉),将熔化热渣间断地放入烟化炉(每隔2h放渣1次,每次输入量22.6t),通过第一喷嘴和第二喷嘴向烟化炉内喷入二次风和粉煤(160kg/t-氧浸尾渣),控制温度1300℃,渣位高度500mm,吹炼时间50min,获得炉渣和烟气,炉渣经水淬得到弃渣14.2t(含fe 37.8%,zn 0.38%,pb《0.01%,s 0.33%);烟气经收尘获得烟尘;
46.吹炼时,二次风(空气)的鼓入量为710nm3/t-氧浸尾渣,喷嘴的鼓风压力为70kpa。
47.其中,所述烟化炉包括炉体1,炉体1的顶部设有进料口2和烟道3,炉体1的底侧设有放渣口4、第一喷嘴5和第二喷嘴6,所述第一喷嘴5和第二喷嘴6均位于放渣口4的下方,第一喷嘴5的喷吹方向与水平面平行,第二喷嘴6的喷吹方向倾斜向上且与水平面的夹角为13
°
;所述第一喷嘴5和第二喷嘴6设置于炉体1的两个相对的侧壁上,同一侧壁上的第一喷嘴和第二喷嘴交错设置,第二喷嘴6的数量占喷嘴总量的1/3。
48.实施例1-3所得烟尘中铅、锌含量如表1所示。
49.表1实施例1-3所得烟尘中铅、锌含量情况表
50.组别zn/wt%pb/wt%实施例137.6335.61实施例242.8727.85实施例337.2337.05
51.可见,铅、锌富集到了烟尘中,可送入铅、锌冶炼系统进一步处理。
52.对比例1
53.重复实施例1,区别仅在于:控制烟化炉中渣位高度为700mm。
54.炉渣经水淬得到弃渣15.0t(含fe 25.9%,zn 0.55%,pb 0.08%,s 0.68%)。
55.对比例2
56.重复实施例1,区别仅在于:控制烟化炉中渣位高度为400mm。
57.炉渣经水淬得到弃渣15.1t(含fe 26.0%,zn 0.60%,pb 0.07%,s 0.66%)。
58.上述对比例1和2表明,当渣位高于600mm,部分粉煤难以溢出渣面燃烧,反应气氛和温度控制受到影响;当渣位低于500mm时,粉煤冲破渣层,造成喷嘴喷入的空气和粉煤对熔体的搅拌效果差;上述两种情况,在相同的吹炼时间内,铅、锌的挥发率受到影响,水淬渣含铅》0.01%。
59.对比例3
60.重复实施例1,区别在于:第二喷嘴6的喷吹方向倾斜向上且与水平面的夹角为5
°
。
61.炉渣经水淬得到弃渣15.1t(含fe 25.8%,zn 0.78%,pb 0.10%,s 0.80%)。
62.对比例4
63.重复实施例1,区别在于:第二喷嘴6的喷吹方向倾斜向上且与水平面的夹角为18
°
。
64.炉渣经水淬得到弃渣15.1t(含fe 26.1%,zn 0.72%,pb 0.09%,s 0.64%)。
65.上述对比例3和4表明,当第二喷嘴6采用小于10
°
的倾角粉煤喷嘴时,部分粉煤难以溢出渣面燃烧,反应气氛和温度控制受到影响;当第二喷嘴6采用大于15
°
的倾角粉煤喷嘴时,粉煤冲破渣层,造成喷嘴喷入的空气和粉煤对熔体的搅拌效果差;上述两种情况,在相同的吹炼时间内,铅、锌的挥发率受到影响,水淬渣含铅》0.01%。
66.上述实施例阐明的内容应当理解为这些实施例仅用于更清楚地说明本发明,而不用于限制本发明的范围,在阅读了本发明之后,本领域技术人员对本发明的各种等价形式的修改均落入本技术所附权利要求所限定的范围。
再多了解一些
本文用于创业者技术爱好者查询,仅供学习研究,如用于商业用途,请联系技术所有人。