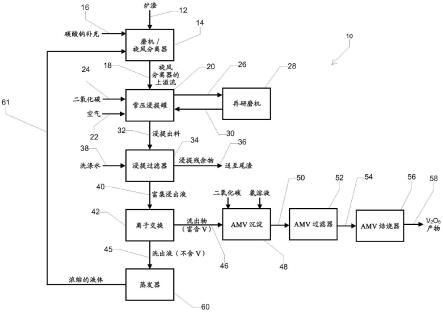
1.本发明涉及从碱性进料、特别是二级材料例如钢渣中回收钒的方法。更具体而言,本发明的方法适用于通过湿法冶金加工从这些进料中回收钒。
背景技术:
2.下面对背景技术的讨论仅旨在帮助对本发明的理解。该讨论并非肯定或承认所提到的任何资料是截至本技术的优先权日的公知常识的一部分。
3.钒最明显在磁铁矿的矿床中发现,并通常存在于铁回收工艺期间生成的炉渣中。为了提取或回收钒,通常用所谓的“盐焙烧法”处理浓缩物或炉渣。在盐焙烧法中,将钒渣与一种或多种碱金属盐混合并通常在800-900℃进行焙烧以生产偏钒酸钠。这些有价值的钒物质随后用水选择性地浸提。随后在精制工艺中回收有价值的钒,此工艺包括从浸出溶液中沉淀出偏钒酸铵或多钒酸铵,这两者都可以在高温下处理以脱铵并转化成产物五氧化二钒。此工艺和特别初始高温的盐焙烧步骤是高度能量密集的,因此在进料中的钒含量需要处于特定水平以使该方法经济可行。
4.许多不同的湿法冶金工艺已用于加工炉渣以回收钒。这样的工艺通常包括酸浸提步骤以将钒提取到溶液中。通过湿法冶金手段回收钒所面临的主要问题在于:在酸浸提步骤期间通常与钒共同提取出其它金属物质,例如铁、钛、钙、镁和二氧化硅。在浸出溶液中回收钒时也必须考虑这些物质在浸出溶液中的存在。从也包含溶解的铁物类的浸出溶液中分离钒带来重大挑战。可实现这一点的大多数方法是不经济的。钒和铁都可以多重氧化态存在,并且存在多重与不同浸提体系的配位度,仅含有这些元素的物类的混合物就相当复杂。因此,许多传统分离技术和已确立的试剂不能将钒与铁有效地分开。为了解决这个问题,大多数方法要求在可以回收钒之前首先处理浸出溶液以除去这些杂质,特别是铁和钛。这增加了工艺的复杂性和总成本。
5.cao和其它碱性材料也通常存在于炉渣材料中。所以,对这些材料进行酸浸提时的另一个问题是由于高的碱性含量而大量消耗酸。另外,当硫酸用作浸提剂时,浸提的副产物是固体caso4.xh2o,其以大体积形成。此产物必须与最终的流出物中和固体一起处置。
6.用于从所述进料回收钒的碱或碱性浸提体系迄今尚未广泛用于工业中。这种体系的主要复杂性表现为由于从进料释放钒的效果差而导致回收受到限制。
7.在整个说明书中,除非上下文另行要求,词语“包含”或其变体形式将被理解为意味着包括指定的实体(integer)或实体组合,但不排除任何其它实体或实体组合。
8.发明概述
9.根据本发明的第一个方面,提供一种从含钒的进料流中回收钒的方法,此方法包括以下步骤:
10.使钒进料流进行浸提步骤,所述浸提步骤包括使钒进料流与碱性碳酸盐浸提溶液接触以形成浸出浆料,所述浸出浆料包含含钒的富集浸出溶液(pregnant leach solution)和固体残余物;
11.将所述浸出浆料送入固/液分离步骤以产生含钒的富集浸出溶液;和
12.从所述富集浸出溶液中回收钒产物。
13.本发明人发现,本发明的碱性碳酸盐浸提对于钒的选择性高于对于可存在于进料中的其他金属和二氧化硅的选择性。
14.在整个说明书中,除非上下文另行要求,词语“碱性碳酸盐浸提溶液”或相似变体形式将被理解为表示包含碱金属的碳酸盐或碳酸氢盐或者碱土金属的碳酸盐或碳酸氢盐的水溶液。
15.发现本发明的方法适合用于碱性进料。预期本发明方法可以用于从不同来源回收钒,包括炉渣、残渣和工业工艺的其它副产物。在整个说明书中,除非上下文另行要求,词语“碱性进料”将被理解为表示此进料包含一种或多种碱金属化合物和碱土金属化合物,或当与水混合时形成碱性溶液或浆料。
16.本发明的方法优选适用于从来自钢铁工业的炉渣材料中回收钒产物。除了钒之外,这些材料还含有铁以及其它物类,例如锰、钛和铬。本发明的方法能够从这些材料以比其它杂质金属更高的选择性浸提出钒。发现这能简化随后从富集浸出溶液中回收钒的过程。
17.在本发明的一种形式中,含钒的进料流包含钢渣。在整个说明书中,除非上下文另行要求,术语“钢渣”将被理解为是指钢铁制造过程的炉渣副产物。如本领域技术人员会认识到,当含铁材料暴露于高温时,至少一部分的杂质或脉石材料从熔融金属中分离并作为炉渣取出。这种炉渣随后进行冷却并形成固体材料。
18.在本发明的一种形式中,碱性碳酸盐浸提溶液包含碳酸钠(na2co3)、碳酸氢钠(nahco3)和氢氧化钠(naoh)中的一种或多种。在本发明的一种形式中,碱性碳酸盐浸提溶液包含碳酸钾(k2co3)、碳酸氢钾(khco3)和氢氧化钾(koh)中的一种或多种。在本说明书中提到的任何钠盐或钠物质应当理解为类似于使用钾盐或钾物质和任何其它碱金属或碱土金属的碳酸盐和碳酸氢盐或其混合物的情形。如本领域技术人员会认识到,碳酸盐、碳酸氢盐和氢氧化物一起在水溶液中在浸提步骤期间在浸提溶液中以动态平衡存在。在强碱性条件下,氢氧根和碳酸根离子占主导地位,而在弱碱性条件下,碳酸氢根离子更占主导地位。
19.在本发明的一种形式中,碱性碳酸盐浸提溶液包含碳酸铵。
20.在本发明的一种形式中,浸提步骤是在氧化条件下进行。优选地,浸提步骤是在氧化剂的存在下进行。更优选地,氧化剂是选自氧气、空气和过氧化氢。作为另一种选择,进料与氧化剂在浸提步骤之前混合。合适的氧化剂包括mno2。在本发明的另一种形式中,在浸提步骤中不加入氧化剂。
21.在本发明的一种形式中,将氧化剂加入浸提步骤。优选地,氧化剂的添加将以相对于ag/agcl参比电极》-100mv的溶液eh为目标。
22.在本发明的一个实施方案中,所述方法进一步包括以下步骤:
23.在使进料流进行浸提步骤之前,进料流进行预处理工艺。
24.优选地,预处理工艺包括一个或多个尺寸缩减步骤。更优选地,所述一个或多个尺寸缩减步骤包括压碎步骤、研磨步骤和碾磨步骤中的一种或多种。
25.在本发明的一种形式中,预处理工艺包括一个或多个选矿步骤。优选地,所述一个或多个选矿步骤包括重力分级步骤、磁力分级步骤和浮选步骤中的一种或多种。
26.在本发明的一种形式中,进料流在浸提步骤之前进行预浸提步骤。优选地,预浸提步骤包括使进料流与碱性液接触以产生预浸出浆料。在本发明的一种形式中,碱性液是碱性碳酸盐浸提溶液。优选地,碱性液包含碳酸钠和/或碳酸氢钠。在本发明的一种形式中,碱性液包含氢氧化钠。在本发明的一种形式中,碱性液包含碳酸钾和/或碳酸氢钾。在本发明的一种形式中,碱性液包含氢氧化钾。在本发明的一种形式中,至少一部分的碱性液可以由循环料流补充。如上所述,碳酸盐、碳酸氢盐和氢氧化物一起在水溶液中以动态平衡形式存在。预期所有这三种物质将按照不同的比例存在于碱性浸提溶液中。
27.在本发明的一种形式中,预浸提步骤是在进料经过一个或多个尺寸缩减步骤之后进行。在本发明的一种形式中,使预浸出浆料进行一个或多个尺寸缩减步骤。
28.在本发明的一种形式中,将二氧化碳料流注入预浸提步骤中。
29.在本发明的一种形式中,所述使进料流进行浸提以形成包含含有溶解的钒的富集浸出溶液和固体残余物的浆料的步骤更具体地包括使进料流在一个或多个浸提反应器中进行浸提步骤。优选地,该步骤包括使进料流在两个或更多个浸提反应器中进行浸提步骤。更优选地,该步骤包括使进料流在三个或更多个浸提反应器中进行浸提步骤。更优选地,该步骤包括使进料流在四个或更多个浸提反应器中进行浸提步骤。更优选地,该步骤包括使进料流在五个或更多个浸提反应器中进行浸提步骤。
30.在本发明的一种形式中,使进料流进行浸提步骤的步骤是在大气压下进行。在本发明的一种形式中,使进料流进行浸提步骤的步骤是在升高的压力下进行。
31.在本发明的一种形式中,使进料流进行浸提步骤的步骤是在环境温度下进行。在本发明的一种形式中,使进料流进行浸提步骤的步骤是在升高的温度下进行。
32.在本发明的一种形式中,浸提步骤是在7.5以上的ph下进行。
33.在本发明的一种形式中,控制浸提步骤的ph。优选地,浸提步骤保持在7.5-14的ph下。更优选地,浸提步骤保持在9-10的ph下。
34.在本发明的一种形式中,将二氧化碳料流注入浸提步骤中。优选地,二氧化碳料流用于控制浸提步骤的ph。作为另一种选择,可以将碳酸加入浸提步骤中。
35.在本发明的一种形式中,进行浸提步骤直到碳酸盐浓度降低到目标浓度。优选地,目标浓度是在5g/l以下。
36.在本发明的一种形式中,至少一部分的浸出浆料进行尺寸缩减步骤。在本发明的一种形式中,尺寸缩减步骤是在浸提步骤期间进行。在本发明的另一种形式中,将至少一部分的浸出浆料送入尺寸缩减步骤以产生具有减小的粒度的工艺料流。在本发明的一种形式中,此工艺料流返回浸提步骤。在本发明的另一种形式中,此工艺料流进行二级浸提步骤。优选地,二级浸提步骤包括使此工艺料流与碱性碳酸盐浸提溶液接触以形成包含含钒的富集浸出溶液和固体残余物的二级浸出浆料。在本发明的一种形式中,二级浸提步骤是在氧化剂的存在下进行。在本发明的一种形式中,将二氧化碳料流注入二级浸提步骤中。在本发明的一种形式中,使二级浸出浆料进行固液分离步骤以回收富集浸出溶液。优选地,固体残余物进行一个或多个进一步的尺寸缩减步骤,其中每个尺寸缩减步骤之后是进一步的浸提步骤。
37.在本发明的另一种形式中,使三级浸提溶液进行一个或多个进一步的尺寸缩减步骤,其中每个尺寸缩减步骤之后是进一步的浸提步骤。在本发明的一种形式中,使二级浸出
浆料进行尺寸缩减步骤以产生具有减小的粒度的工艺料流。在本发明的一种形式中,使此工艺料流进行三级浸提步骤。优选地,三级浸提步骤包括使此工艺料流与碱性碳酸盐浸提溶液接触以形成包含含钒的富集浸出溶液和固体残余物的三级浸出浆料。在本发明的一种形式中,将三级浸出浆料送入固液分离步骤以回收富集浸出溶液。在本发明的另一种形式中,使三级浸提溶液进行一个或多个进一步的尺寸缩减步骤,其中每个尺寸缩减步骤之后是进一步的浸提步骤。
38.在本发明的一种形式中,将浸出浆料送入分级装置,其中将上溢流(overflow)送入固液分离步骤,并将底流(underflow)循环返回浸提步骤、预浸提步骤或尺寸缩减步骤。
39.在本发明的一种形式中,固/液分离步骤包括在过滤装置中的浆料处理。在一个实施方案中,固/液分离步骤包括位于过滤装置上游的增稠装置。
40.在本发明的另一种形式中,固/液分离步骤包括在逆流倾析(ccd)回路中的浆料处理。在一个实施方案中,ccd回路包括串联布置的两个或更多个增稠器。
41.在本发明的一种形式中,在固液分离步骤中回收的固体进行三级浸提步骤以进一步提取钒。优选地,三级浸提步骤包括使所述固体与碱性溶液接触。更优选地,三级浸提步骤包括使所述固体与碱性碳酸盐溶液接触。在本发明的一种形式中,将二氧化碳料流注入三级浸提步骤中。
42.在本发明的一种形式中,从富集浸出溶液回收钒产物的步骤包括沉淀富含钒的固体,并将富含钒的固体与贫化浸出溶液分离开。在本说明书中,术语“贫化浸出溶液”将理解为表示其中至少一部分钒已被回收的浸提溶液。应当理解其包括含有钒的溶液。
43.在本发明的另一种形式中,从富集浸出溶液回收钒产物的步骤包括使富集浸出溶液与离子交换介质接触以选择性地回收钒,并将其与贫化浸出溶液分离开。
44.在本发明的另一种形式中,从富集浸出溶液回收钒产物的步骤包括使富集浸出溶液与包含钒萃取剂的有机溶液接触,并将负载的有机溶液与贫化浸出溶液分离开。优选地,负载的有机溶液与洗涤溶液接触。在本发明的一种形式中,用反萃取溶液从所述负载的有机溶液回收钒。优选地,反萃取溶液是氢氧化钠或氢氧化钾。
45.在其中含有钒萃取剂的有机溶液用于从富集浸出溶液回收钒的实施方案中,本发明还包括从反萃取溶液回收钒产物的步骤。在一个实施方案中,钒产物的回收包括沉淀富含钒的固体,并将富含钒的固体与贫化反萃取溶液分离开。
46.在本发明的另一种形式中,从富集浸出溶液回收钒产物的步骤包括使富集浸出溶液经过纳米过滤体系,其中从钒物质优先除去碳酸氢根离子。优选地,将碳酸氢盐料流返回浸提步骤。
47.在本发明的另一种形式中,从富集浸出溶液回收钒产物的步骤包括将富集浸出溶液通入结晶回路,在这里相对于钒物质,碳酸钠和/或碳酸氢钠盐选择性地结晶。优选地,结晶回路包括一个或多个结晶阶段。在本发明的一种形式中,除去结晶固体并循环到浸提步骤。
48.在本发明的其中浸提步骤进行直到碳酸盐浓度降低到目标浓度的一种形式中,从富集浸出溶液回收钒产物的步骤优选包括将富集浸出溶液通入结晶回路,在这里钒物质进行选择性地结晶。
49.从富集浸出溶液回收钒产物的步骤获得贫化浸出溶液。在本发明的一种形式中,
将至少一部分的贫化浸出溶液循环到浸提步骤。在本发明的一种形式中,贫化浸出溶液在被循环到浸提步骤之前进行碳酸盐化。在其中在二氧化碳料流的存在下进行浸提步骤的实施方案中,贫化浸出溶液可以被直接循环到浸提步骤。
50.在本发明的一种形式中,将至少一部分的贫化浸出溶液循环到预浸提步骤。优选地,贫化浸出溶液用于补充至少一部分的碱性碳酸盐浸提溶液。在本发明的一种形式中,贫化浸出溶液在被循环到浸提步骤之前进行碳酸盐化。
51.在本发明的一种形式中,将至少一部分的贫化浸出溶液循环到二级或三级浸提步骤。优选地,贫化浸出溶液用于补充至少一部分的碱性碳酸盐浸提溶液。在本发明的一种形式中,贫化浸出溶液在被循环到三级浸提步骤之前进行碳酸盐化。
52.在本发明的一种形式中,贫化浸出溶液用于在固液分离步骤中的洗涤水中。
53.在本发明的一种形式中,贫化浸出溶液用于进料或中间的尺寸缩减步骤中。
54.附图简述
55.在本发明的若干非限制性实施方案的以下描述中更充分地描述本发明的进一步特征。该描述只是为了举例说明本发明。其不应被理解为对如上所述的本发明的宽泛概述、公开或描述的限制。参考附图进行描述,其中:
56.图1是本发明方法的流程图;
57.图2是本发明的一种可选实施方案的流程图,其中包括将来自外部来源的二氧化碳料流引入循环;
58.图3是本发明的一种可选实施方案的流程图,其中包括将来自浸提残余物的二氧化碳料流引入循环;
59.图4是本发明的一种可选实施方案的流程图,其中在浸提步骤中没有再生碳酸盐;
60.图5是本发明的一种可选实施方案的流程图;
61.图6是本发明的一种可选实施方案的流程图,其中包括单个浸提步骤;
62.图7是本发明的一种可选实施方案的流程图,其中包括溶剂萃取步骤;
63.图8是用于检测研磨尺寸对钒提取的影响的试验的结果的图表;
64.图9是用于检测温度对钒提取的影响的试验的结果的图表;
65.图10是用于检测碳酸钠浓度对钒提取的影响的试验的结果的图表;
66.图11是用于检测固体百分含量对钒提取的影响的试验的结果的图表;
67.图12是用于检测添加氧化剂对钒提取的影响的试验的结果的图表;
68.图13是用于检测在二级浸提期间钒提取的试验的结果的图表;
69.图14是用于检测在三级浸提期间钒提取的试验的结果的图表;
70.图15是用于检测在随后浸提工艺中钒提取的试验的结果的图表;
71.图16是用于检测使用有机萃取剂从合成浸提溶液萃取钒的试验的结果的图表;和
72.图17是用于检测使用有机萃取剂从回收的浸提溶液萃取钒的试验的结果的图表。
73.实施方案的描述
74.本发明的方法涉及从含钒的进料流中回收钒。在非常广泛的意义上,所述方法包括以下步骤:
75.使钒进料流进行浸提步骤,所述浸提步骤包括使钒进料流与碱性碳酸盐浸提溶液接触以形成浸出浆料,所述浸出浆料包含含钒的富集浸出溶液和固体残余物;
76.将所述浸出浆料送入固/液分离步骤以产生含钒的富集浸出溶液;和
77.从所述富集浸出溶液中回收钒产物。
78.本发明人发现本发明的碳酸盐浸提显示对钒的选择性高于对于可能存在于进料中的其它金属的选择性。
79.发现本发明方法适合用于碱性进料。在进料中存在的碱性物质对通过采用湿法冶金工艺用酸作为初级浸提剂来处理这些进料的情况提出挑战。这种工艺的主要缺点是大量的酸被碱性物质消耗,这增加了操作成本。另外,可溶于酸的杂质也被提取到浸出溶液中,需要进一步的加工以除去这些杂质。另外,会产生大量的钙盐、浸提残余物和/或流出物中和废料,处理这些物质的操作导致工艺效率低和/或增加工艺成本。
80.本发明可以考虑用于从不同的来源回收钒,包括炉渣、残渣和/或工业工艺的其它副产物。
81.本发明方法优选用于从来自钢铁工业的炉渣材料回收钒产物。除了钒之外,这些材料还含有铁以及其他物质,例如钛。本发明方法能从这些材料以比其它杂质金属更高的选择性浸提出钒。发现本发明方法简化了从富集浸出溶液回收钒的工艺。
82.在图1中,显示根据本发明的一个实施方案从进料流12回收钒10的方法。进料流12可以在加工之前进行一个或多个尺寸缩减步骤(未显示)。进料12应当具有《200μm的目标粒度,优选《100μm的目标粒度,更优选《75μm。本领域技术人员可获得的常规压碎和研磨装置可以用于减小进料12的粒度。此进料可以进行一个或多个选矿步骤(未显示)以除去进料12中的过量的低价值附带组分。如上文所讨论,一个或多个选矿步骤可以包括重力分级步骤、磁力分级步骤和浮选步骤中的一种或多种。本发明人发现在二氧化硅玻璃中能捕捉在钢渣中的显著比例的钒。发现一个或多个尺寸缩减步骤能将钒从这些材料释放出来,允许随后在浸提步骤中溶解。可以考虑使用湿和干方式的粒度缩减装置。
83.在如1图所示的实施方案中,将进料12送入预浸提步骤14,在这里与碱性液16和循环工艺水(负载的洗涤溶液)接触,由此形成预浸出浆料18。碱性液16优选包含氢氧化钠,以及碳酸钠和/或碳酸氢钠。碱性液16可以由循环液61来补充(如下文所述),此循环液优选含有碳酸钠/碳酸氢钠和氢氧化钠。进料12与碱性液16的接触将开始将钒从进料12提取到溶液中。这种浸提的程度将取决于碱性液16、在进料中的钒含量和进料的粒度。
84.在一个实施方案中,预浸提步骤14是在浸提容器中进行。
85.在本发明的另一种形式中,预浸提步骤14可以在湿磨机装置中进行。如本领域技术人员已知,湿磨机装置通过研磨、切割或压碎将固体材料破裂成更小的材料。合适的磨机装置包括球磨机、棒磨机、自磨型(ag)磨机和半自磨型(sag)磨机。通过在湿磨机装置中进行预浸提步骤14,可以实现在进料12和碱性液16之间的更紧密接触,增加有效接触时间,从而实现进一步的提取。
86.可以将预浸出浆料18送入湿分级装置,例如旋风分离器装置,从而防止筛上粒子从预浸提步骤14转移。在这种实施方案中,可以将筛上粒子返回到预处理磨机,同时将过筛粒子送入浸提回路。
87.预浸提条件
88.在一个实施方案中,预浸提是在环境温度下进行。在一个实施方案中,预浸提是在升高的温度下进行。优选地,预浸提是在高于40℃的温度下进行。
108.naoh co2→
nahco3109.2naoh co2→
na2co3 h2o
110.na2co3 h2o co2→
2nahco3111.所以,发现添加二氧化碳能够在浸提溶液中从cao反应期间所产生的naoh再生na2co3/nahco3,这允许进一步从进料提取钒。
112.二氧化碳可以从许多来源获得。在一个实施方案中,从大气中捕捉至少一部分的二氧化碳。在一个实施方案中,从废气料流捕获至少一部分的二氧化碳。优选地,废气料流是从高炉排出的废气。在一个实施方案中,从焙烧器排出的废气捕获至少一部分的二氧化碳。优选地,二氧化碳是从石灰石的焙烧工艺捕获。
113.在本发明的一种形式中,直接从一种或多种来源捕获二氧化碳。在本发明的另一种形式中,二氧化碳在吸附工艺中被中间试剂所捕获,随后从中间试剂再生。从中间试剂传递的co2可以通过化学解吸或热解吸进行。当从大气或废气料流捕捉co2时,这是特别有用的。
114.在一个实施方案中,使二氧化碳进行杂质去除步骤。在一个实施方案中,经提纯的气体料流直接用作二氧化碳的来源。
115.在一个实施方案中,二氧化碳在使用之前进行浓缩。在气体料流中的二氧化碳浓度优选是》20%。更优选,在气体料流中的二氧化碳浓度是》90%。
116.在一个实施方案中,在浸提步骤中控制浸提溶液的ph。在一个实施方案中,浸提溶液保持在7.5以上的ph。在一个实施方案中,浸提溶液保持在8以上的ph。在一个实施方案中,浸提溶液保持在8.5以上的ph。在一个实施方案中,浸提溶液保持在9以上的ph。
117.在一个实施方案中,浸提溶液保持在7.5-14的ph。在一个实施方案中,ph保持为8-11。在一个实施方案中,ph保持为9-10。本发明人发现,浸提溶液的ph将在浸提工艺过程中自然地提高,这是因为在碱性碳酸盐和cao/ca(oh)2的反应过程中形成naoh。但是,在高于14的ph下,二氧化硅的溶解性提高,并将被浸提到溶液中。也发现在ph低于9的情况下,少量的杂质例如锰、镁、铁和钛开始溶解。这会增加复杂性,并可以影响随后从浸提溶液回收钒。通过使ph保持为9-14,可以实现钒的提取,同时最少的二氧化硅被浸提到溶液中。
118.在一个实施方案中,通过向浸提溶液加入二氧化碳来保持ph。如上文所述,二氧化碳将naoh转化成na2co3/nahco3。作为另一种选择,通过添加酸来保持ph。
119.在一个优选实施方案中,浸提步骤20在ph约为10的情况下进行,从而防止上述杂质被浸提到溶液中。在分离出未溶解的固体之后,富集浸出溶液的ph可以随后降低到9-9.5,从而从该溶液沉淀出至少一部分的二氧化硅。可以加入促凝剂以帮助去除二氧化硅。沉淀的固体可以然后从该溶液过滤出去。
120.浸提步骤14优选包含浸提回路,其包括串联布置的一个或多个浸提容器。
121.浸提条件
122.在一个实施方案中,进料具有p
80 106μm的粒度。在一个实施方案中,进料具有p
80
75μm的粒度。在一个实施方案中,进料具有p
80 53μm的粒度。在一个实施方案中,进料具有p
100 25μm的粒度。
123.在一个实施方案中,在环境温度下进行浸提。在一个实施方案中,浸提是在升高的温度下进行。优选地,浸提步骤是在至多沸点的温度下进行。在一个实施方案中,浸提步骤
是在高于50℃的温度下进行。在一个实施方案中,浸提步骤是在高于60℃的温度下进行。在一个实施方案中,浸提步骤是在高于70℃的温度下进行。在一个实施方案中,浸提步骤是在高于80℃的温度下进行。在一个实施方案中,浸提步骤是在高于90℃的温度下进行。
124.在一个实施方案中,浸提步骤是在环境压力下进行。在一个实施方案中,浸提步骤是在升高的压力下进行。可以考虑将二氧化碳注入浸提反应器的顶部空间中。
125.在一个实施方案中,浸提步骤的浆料密度是10-50%。在一个实施方案中,浆料密度是20-40%。
126.在一个实施方案中,在浸提溶液中的na2co3/nahco3浓度是2-35%。在一个实施方案中,在浸提溶液中的na2co3/nahco3浓度是至少50g/l。在一个实施方案中,在浸提溶液中的na2co3/nahco3浓度是至少75g/l。在一个实施方案中,在浸提溶液中的na2co3/nahco3浓度是至少125g/l。
127.在其中将二氧化碳喷入浸提容器的实施方案中,在浸提溶液中的na浓度是至少40g/l。
128.在一个实施方案中,浸提步骤的停留时间是大于1小时。在一个实施方案中,浸提步骤的停留时间是大于2小时。在一个实施方案中,浸提步骤的停留时间是大于3小时。在一个实施方案中,浸提步骤的停留时间是大于4小时。在一个实施方案中,浸提步骤的停留时间是大于5小时。在一个实施方案中,浸提步骤的停留时间是大于6小时。在一个实施方案中,浸提步骤的停留时间是大于7小时。在一个实施方案中,浸提步骤的停留时间是大于8小时。在一个实施方案中,浸提步骤的停留时间是大于9小时。在一个实施方案中,浸提步骤的停留时间是大于10小时。在一个实施方案中,浸提步骤的停留时间是大于11小时。在一个实施方案中,浸提步骤的停留时间是大于12小时。
129.在一个实施方案中,保持相对于ag/agcl参比电极的》-100mv的溶液eh。在一个实施方案中,保持相对于ag/agcl参比电极的》-90mv溶液eh。在一个实施方案中,保持相对于ag/agcl参比电极的》-80mv的溶液eh。在一个实施方案中,保持相对于ag/agcl参比电极的》-70mv的溶液eh。在一个实施方案中,保持相对于ag/agcl参比电极的》-60mv的溶液eh。在一个实施方案中,保持相对于ag/agcl参比电极的》-50mv的溶液eh。在一个实施方案中,保持相对于ag/agcl参比电极的》-40mv的溶液eh。在一个实施方案中,保持相对于ag/agcl参比电极的》-30mv的溶液eh。在一个实施方案中,保持相对于ag/agcl参比电极的》-20mv的溶液eh。在一个实施方案中,保持相对于ag/agcl参比电极的》-10mv的溶液eh。在一个实施方案中,保持相对于ag/agcl参比电极的》0mv的溶液eh。在一个实施方案中,保持相对于ag/agcl参比电极的》50mv的溶液eh。在一个实施方案中,保持相对于ag/agcl参比电极的》100mv的溶液eh。在一个实施方案中,保持相对于ag/agcl参比电极的》200mv的溶液eh。在一个实施方案中,保持相对于ag/agcl参比电极的》300mv的溶液eh。在一个实施方案中,保持相对于ag/agcl参比电极的》400mv的溶液eh。
130.再研磨回路
131.在一个实施方案中,将一部分的浸出浆料26送入尺寸缩减步骤28。在尺寸缩减步骤28中处理此浆料以降低在浸出浆料26中的固体的粒度。从尺寸缩减步骤28排出的经处理的料流30返回到浸提步骤20。也可以考虑将所述经处理的料流送入二级浸提步骤(未显示)。
132.如上文所述,na2co3和nahco3将与cao反应形成固体caco3。不希望受限于任何理论,本发明人认为这些物质将与在进料粒子的暴露表面处的cao反应或与在溶液中的ca
2
反应,由此形成固体caco3。至少一部分的沉淀caco3将作为在进料上的涂层形成,从而阻碍钒的进一步浸提。本发明人发现,通过使经涂覆的(部分浸提的)进料进行尺寸缩减步骤28,可以除去至少一部分的caco3,暴露出进料的表面并允许进一步浸提钒。
133.任何合适的碾磨装置可以用于尺寸缩减步骤28中。合适装置的例子包括球磨机、棒磨机、自磨型(ag)磨机、半自磨型(sag)磨机、搅拌介质型磨机和搅拌介质型磨耗机。
134.在如图1所示的实施方案中,尺寸缩减步骤28是与浸提步骤20平行地进行,其中从浸提步骤20取出一部分的浸出浆料并将其送入尺寸缩减步骤28,然后循环返回到浸提步骤20。考虑尺寸缩减步骤28的实际布置将受到在浸提步骤20中所用的具体浸提回路的影响。例如,如果多个浸提容器串联排列,则考虑可以将最后浸提容器的底流例如送入尺寸缩减步骤28,其中经处理的料流30返回到先前的浸提容器。以此方式,在经处理的料流30中的固体粒子在浸提步骤20中在足够的停留时间内提供,从而能提高钒的提取。在另一个实施方案中,经处理的料流30可以被送入二级浸提步骤(未显示),在这里与新鲜或再生的碳酸盐液体接触以进一步提取钒。二级浸提步骤可以在与浸提步骤20相似的条件下进行,并且可以将氧化剂料流和二氧化碳料流注入浸提容器。此实施方案的优点是:经处理的料流30在二级浸提步骤中的停留时间可以得到准确的控制,从而确保最大程度的回收。在再一个实施方案中,浸提步骤20可以在湿磨机装置中进行。在此实施方案中,连续地从进料的表面除去所形成的caco3固体。
135.在一个实施方案中,尺寸缩减步骤将粒度减小到p
80 38μm。在一个实施方案中,尺寸缩减步骤将粒度减小到p
95 38μm。在一个实施方案中,尺寸缩减步骤将粒度减小到p
80 10μm。
136.从浸提步骤20排出的浸出浆料32包含富集浸出溶液,其含有溶解的钒和固体残余物。将浸出浆料32送入固液分离步骤34以除去固体残余物料流36。洗涤水38用于固液分离步骤34中以确保将所夹带的液体充分地与固体残余物36分离。循环液61可以在第一次洗涤中用作洗涤水38。固体残余物料流优选被送至尾渣。固液分离步骤34可以在过滤装置中进行,例如带式过滤器。其它固液分离装置可以用于固液分离步骤34中。也可以考虑使用位于过滤器之前的增稠器。
137.在一个实施方案中,逆流洗涤工艺用于固液分离步骤34中以使钒的回收最大化。
138.在一个实施方案中,在回收钒产物之前调节富集浸出溶液40的ph。在一个实施方案中,将ph调节到8.5-9.5。在一个实施方案中,将ph是调节到9.0-9.5。ph调节可以使用co2进行或在添加少量酸的情况下进行。
139.在一个实施方案中,将富集浸出溶液40送入浓缩步骤(未显示)。在浓缩步骤中,在富集浸出溶液中的钒浓度增加。优选地,在将富集浸出溶液40送入钒回收回路42之前进行浓缩步骤。
140.在一个实施方案中,将富集浸出溶液40送入提纯步骤(未显示)。在提纯步骤中,从富集浸出溶液40除去一种或多种杂质。优选地,提纯步骤包括使富集浸出溶液40从纳米过滤/膜体系通过。优选地,在将富集浸出溶液40送入钒回收回路42之前进行提纯步骤。
141.在一个实施方案中,同时进行浓缩步骤和提纯步骤。
142.将富集浸出溶液40送入钒回收回路42以从富集浸出溶液40提取钒产物。可以考虑在钒回收回路42中使用许多不同的回收方式。在如图1所示的实施方案中,将富集浸出溶液40送入离子交换步骤44,由此分别得到贫化浸出溶液45与富含钒的洗脱液46。将富含钒的洗脱液46送入沉淀步骤48,在这里与氨和/或硫酸铵接触,优选在硫酸的存在下接触,由此沉淀出偏钒酸铵。将所得的浆料50送入固液分离步骤52。将所得的固体料流54送入焙烧步骤56以获得v2o5产物58。在一个实施方案中,在沉淀步骤48之前,将富含钒的洗脱液46送入二氧化硅去除步骤(未显示)。二氧化硅去除步骤可以涉及用硫酸调节ph和添加硫酸铝,由此沉淀出富含硅铝酸盐的粒子并在回收偏钒酸铵之前降低硅含量。
143.在本发明的另一种形式中,将富集浸出溶液40送入沉淀步骤,在这里从富集浸出溶液40沉淀出钒固体。沉淀的固体随后与贫化浸出溶液45分离开,并送入进一步加工中。钒酸钠可以直接从富集浸出溶液40结晶。作为另一种选择,富集浸出溶液40可以与铵物质接触以沉淀出nh4vo3。所得的沉淀物可以回收并送入焙烧步骤以获得v2o5产物。
144.在本发明的另一种形式中,将富集浸出溶液40送入溶剂萃取回路。在溶剂萃取回路中,富集浸出溶液40与有机萃取剂接触以将钒离子从水相萃取到负载的有机相中。负载的有机相可以与贫化浸出溶液45分离。负载的有机相可以然后与洗涤液接触以从负载的有机相置换被夹带的水相或杂质。负载的有机相然后与反萃取水溶液接触以从负载的有机相回收钒。然后可以通过常规方式从反萃取水溶液回收钒,例如沉淀、结晶或电解或如上所述。
145.在本发明的另一种形式中,富集浸出溶液40可以与离子交换树脂接触以使钒负载到树脂上。一旦负载的树脂与贫化浸出溶液45分离开,就可以使用合适的反萃取剂将钒从负载的树脂反萃取出来。在一个实施方案中,反萃取剂是硫酸。在此实施方案中,硫酸氧钒可以直接从反萃取溶液结晶。
146.在本发明的另一种形式中,可以将富集浸出溶液送入结晶回路(未显示),在这里,碳酸钠和/或碳酸氢钠可以从富集浸出溶液选择性地结晶出来,而钒物质留在溶液中。可以考虑利用碳酸钠/碳酸氢钠和钒物质的不同溶解度限度以允许这些物质的选择性沉淀。在碳酸钠和碳酸氢钠都沉淀的情况下,这些物质可以同时或依次结晶。在任一种所述物质结晶之前,可以将二氧化碳注入浸提溶液以确保形成碳酸盐/碳酸氢盐。固体碳酸钠/碳酸氢钠可以循环,例如通过再溶解和用于浸提阶段中,或与进料和水加入一起磨机中。
147.贫化浸出溶液45包含在溶液中的未使用的na2co3、nahco3和naoh的混合物。在如图1所示的实施方案中,将贫化浸出溶液45送入蒸发器60以得到循环液61,从而降低水含量。循环液61可以循环到预浸提步骤14,在这里补充至少一部分的碱性液16。作为另一种选择,循环液61可以循环到浸提步骤20(未显示),在这里补充至少一部分的碱性碳酸盐浸提液。在其中二氧化碳料流24未注入浸提步骤20的情况下,循环液61可以与二氧化碳接触以从在循环液61中的naoh再生na2co3/nahco3。即使将co2注入浸提步骤20,浸提液的碳酸盐组分也可以通过使返回的贫化溶液61进行碳酸盐化来增加。
148.如上文所述,本发明的方法适合用于从炉渣材料回收有价值的物质,炉渣材料通常从钢制造工业产生。钢制造工艺通常在高炉中进行。在典型的工艺中,将原铁矿、焦炭和石灰石送入高炉,在这里在高温下处理以将液体铁与液体炉渣分离开。在此工艺期间,在铁矿石中的铁氧化物被还原成铁,并释放出co2气体。焦炭在炉内点燃,并立即反应生成热和
co2。石灰石在这些温度下转化成cao,并释放出co2气体。每个这些工艺产生显著量的co2作为废产物,并且co2可以是从高炉排放的顶部气体的主要组分。高炉顶部气体排放到大气中,这对全球温室气体排放有显著影响。
149.在本发明的一个实施方案中,在本发明方法中所用的至少一部分的co2可以来自工业来源,例如高炉顶部气体。如上文所述,在本发明中,co2用于从naoh再生naco3。co2可以直接注入浸提容器和/或可以注入贫化浸出溶液中,然后回收钒。本发明人考虑从高炉顶部气体回收co2能降低操作成本,因为不需要使用新鲜的co2。另外,从顶部气体回收co2能最终减少释放到大气中的co2量,所以为co2生产者带来益处。
150.在图2中,显示根据本发明的另一个实施方案从高炉炉渣100回收钒的方法。在图2中,含有铁矿石的进料流102送入高炉104以得到金属相106和炉渣材料108。此工艺也产生含有显著量co2的顶部气体110。炉渣材料108含有钒,并可以送入进一步加工以回收钒。尤其是,炉渣材料108适合用于上文所述的回收钒10的方法。此工艺的简化流程如图2所示。但应当理解的是,可以采用用于回收钒的其它方式。将炉渣材料108送入初级尺寸缩减步骤112。经压碎/研磨的材料114进入钒浸提回路116,在这里与碱性碳酸盐浸提溶液接触以将钒提取到溶液中。与上述回收钒10的方法相似,钒浸提回路116可以包含额外的碾磨步骤、预浸提步骤、再研磨步骤和随后的浸提步骤。如果需要的话,可以将额外的碳酸钠118加入钒浸提回路116。所得的浸出浆料120进入固液分离步骤122以得到富集浸出溶液124和浸提残余物126。浸提残余物126进行洗涤以在弃除之前回收可溶解的钒盐和钠盐。将富集浸出溶液124送入钒回收回路128(涉及如上文所述的溶剂萃取、离子交换、纳米过滤或结晶的一种或多种操作),由此从富集浸出溶液124回收钒产物130,并留下贫化浸出溶液132。然后,贫化(或贫钒的)浸出溶液132可以循环到钒浸提回路116以至少部分地补充浸提溶液。作为另一种选择,可以将贫化浸出溶液132送入此方法的其它部分。
151.来自高炉的顶部气体110包含co2。可以从顶部气体110回收co2料流134。在一个实施方案中,通过中间试剂或技术从废气回收co2,并再生成为更浓缩或更干净的气体料流以用于此工艺中,在另一个实施方案中,含有co2的废气直接用作co2进料,并引入浸提或试剂循环体系中,从而提高试剂的碳酸盐化程度。co2料流134可以进入用于回收钒的装置的各种部分。在一个实施方案中,co2料流134进入钒浸提回路116。作为另一种选择或额外地,可以将co2料流134注入贫化浸出溶液132中,然后循环到钒浸提回路116。
152.浸提残余物126含有碳酸钙,并需要处置。在如图2所示的实施方案中,全部或一部分的浸提残余物126循环返回到高炉104,由此部分地补充用于高炉104中的石灰、碳酸钙或石灰石。浸提残余物126也含有铁。通过使浸提残余物126返回到高炉,可以在高炉104中回收至少一部分的所述铁,由此提高铁产率。
153.在图3中显示根据本发明另一个实施方案的从高炉炉渣200回收钒的方法。在此实施方案中,浸提残余物126进入焙烧步骤202,在这里加热以将浸提残余物126中的caco3转化成cao,同时释放出co2。从焙烧步骤202捕获co2料流204,并将此料流送入钒浸提回路116,或送入返回的贫化浸出溶液132以再生碳酸钠。来自焙烧步骤202的固体料流206被送至尾渣处置。作为另一种选择,因为固体料流206包含cao,所以可以将此料流送入高炉。固体料流206也包含铁。通过将固体料流206返回到高炉,可以在高炉104中回收至少一部分的所述铁,从而提高铁产率。
154.如上文所述,石灰石通常用于高炉中,并随后转化成cao和co2。本发明人发现,在浸提残余物124中或来自其他来源的石灰石的焙烧,既可以用作co2的来源,也可以用作减少在高炉中生成co2的手段,从而减少排放。
155.在图4中显示根据本发明另一个实施方案的用于从进料流302回收钒300的方法。
156.将进料流302送入初级研磨步骤304,在这里将进料流的粒度降低到目标尺寸。将初级研磨出料送入旋风分离器305以分离初级进料流306。尺寸过大的底流返回到初级研磨步骤304以进一步加工。上溢流306应当具有《200μm的目标粒度,目标粒度优选《100μm,更优选《75μm。可以考虑使用其它尺寸分级装置。
157.将初级进料流306送入初级浸提步骤308,在这里与碱性碳酸盐浸提溶液310接触。在选择钠物质作为载体的情况下,碱性碳酸盐浸提溶液310将优选含有碳酸钠和/或碳酸氢钠。碱性碳酸盐浸提溶液310可以还包含氢氧化钠。虽然如图4所示的碱性碳酸盐浸提溶液310是从该流程的其它部分产生的料流,但是也可以考虑使用新鲜试剂代替或补充此料流。在初级浸提步骤308期间,浸提溶液将钒提取到溶液中。初级浸提步骤308是在基本上与浸提步骤20相同的条件下操作。根据所用的准确进料材料,在进料中的钒物质可以许多不同的形式存在。例如,钒酸钙物质可以包括ca(vo3)2、cav2o6.3h2o、cav2o6.4h2o、cav6o
16
.9h2o、ca
2v2
o7.9h2o、ca
3v10o28
.16h2o。作为示例,在进料中的钒酸钙可以在浸提过程中与碱性液16按照下式反应:
158.ca(vo3)2 m2co3=caco3 2mvo3159.ca
2v2
o7 2m2co3=caco3 m
4v2
o7160.(其中m是碱金属或碱土金属)
161.如本领域技术人员所理解,上述反应仅仅用于说明目的,并不是在浸提步骤期间出现的反应的穷尽性列表。
162.如上文关于方法10所述,在进料中存在的cao将与浸提溶液中的na2co3/nahco3反应以得到固体caco3和naoh。如果没有其他碳酸盐被引入浸提溶液,则随着碳酸盐被转化成固体,在浸提溶液中的碳酸盐浓度将降低。这将使得浸提溶液基本上包含氢氧化物,阻止钒被进一步提取到溶液中。在方法10中,将二氧化碳料流注入浸提步骤以在浸提溶液中从naoh再生na2co3/nahco3。虽然发现以此方式可以确保更完全地从进料提取钒,但是所得的富集浸出溶液将具有高的碳酸盐含量。碳酸盐含量会增加从所述浸出溶液回收钒所需的工艺的复杂性。
163.在如4图所示的实施方案中,二氧化碳未被引入浸提步骤以再生碳酸盐,并且允许进行浸提步骤直到在浸提溶液中的至少显著量的碳酸盐被消耗。在采用间歇浸提工艺的情况下,浸提步骤的停留时间足以允许碳酸盐含量降低到目标浓度。作为另一种选择,在使用多个浸提罐的情况下,这些罐可以布置为按照能确保在最终阶段中的碳酸盐含量被降低到目标浓度的方式进行操作。在使用多个浸提阶段的情况下,可以考虑将二氧化碳引入较早的浸提反应器中。
164.选择限制在初级浸提步骤308中的碳酸盐浓度将会限制从初级进料提取钒。虽然这减少在初级浸提步骤308中回收的钒的量,但是富集浸出溶液是具有低碳酸盐浓度的氢氧化钠溶液。钒酸钠可以从这种溶液直接结晶,从而简化回收回路。
165.从初级浸提步骤得到的浆料进入固液分离步骤311,由此从富集浸出溶液313除去
浸提残余物312。富集浸出溶液313进入初级浸提液罐314以进一步加工。在初级浸提液罐314中的溶液345的一部分可以循环到初级浸提步骤308以提高钒浓度。
166.由于浸提的限制,浸提残余物312可以仍然含有高的钒含量,并可以进一步加工以进一步回收钒。在如图4所示的实施方案中,将浸提残余物312送入尺寸缩减步骤316以减低粒度。在一个实施方案中,目标最大粒度优选是约75微米,或者较小的最大粒度可以用于实现更大程度的释放和钒回收。如在方法10中所讨论,本发明人认为固体caco3将在进料的表面上作为涂层形成。本发明人发现,通过使涂覆的(部分浸提的)进料进行尺寸缩减步骤316,可以除去至少一部分的caco3,暴露出进料的表面,并允许进一步浸提钒。可以考虑在尺寸缩减步骤316中使用任何合适的碾磨装置。合适装置的例子包括球磨机、棒磨机、自磨型(ag)磨机和半自磨型(sag)磨机。
167.来自尺寸缩减步骤316的出料进入二级浸提步骤318,在这里与碱性碳酸盐浸提溶液322接触以将钒提取到溶液中。与初级浸提步骤308不同,保持在二级浸提步骤318中的碳酸盐含量以确保最大程度的提取。按照需要,可以将新鲜试剂、例如碳酸钠送入二级浸提步骤318。溶液的ph优选保持在9至10的范围内以尽可能减少二氧化硅的溶解。将浸出浆料324送入增稠步骤326,由此将二级浸提溶液330与固体料流328分离开。将二级浸提溶液330送入二级浸提液罐332以进一步加工。将固体料流328送入过滤步骤334,并且将初级滤液336送入二级浸提液罐332。滤饼用水洗涤,经洗涤的滤液338循环到初级研磨步骤304以尽可能减少钒的损失。作为另一种选择,可以将全部或一部分的经洗涤的滤液338送入初级或二级磨机或浸提反应器,从而帮助钒和钠的回收以及回路水的平衡。将固体残余物340送入尾渣或可以送至其它应用。
168.进入二级浸提液罐332的溶液可以包含高的naoh含量,所以将其与二氧化碳蒸气342接触以再生na2co3/nahco3。然后,此溶液可以作为碱性碳酸盐浸提溶液310送入初级浸提步骤308。一部分的此溶液也可以作为碱性碳酸盐浸提溶液320送入二级浸提步骤318。在碱性碳酸盐浸提溶液310中的钒物质将进入初级或二级浸提溶液310或320以进行随后的回收。
169.将一部分的初级浸提溶液345返回到初级浸提步骤308。初级浸提溶液345循环到初级浸提反应器308,这能以受控方式提高钒浓度,且不会相似地增加总钠浓度。在合适的v:na比率下,可以选择进行一种或多种钒物质(例如navo3或na3vo4)的浓缩和结晶。一部分的初级浸提溶液从初级浸提液罐314送入结晶步骤344以使钒酸钠结晶。因为初级浸提溶液基本上不含碳酸盐物质,所以结晶可以在简单的蒸发结晶器中进行。
170.将所得的浆料送入过滤步骤346以回收固体钒酸钠产物348。洗涤水350用于除去残余的钠杂质。滤液和洗涤水352是含有残余钒的naoh溶液,其被送入二级浸提液罐332以再生碳酸盐。在本发明的一种形式中,将滤液送入离子交换步骤(未显示)以回收钒物质。
171.将固体钒酸钠产物348送入钒回收回路354。在如图4所示的实施方案中,将固体钒酸钠产物348送入溶解步骤356,在这里再溶解在水或稀硫酸溶液中。可以加入硫酸铝以改进硅的去除。在此阶段中,二氧化硅和其它不溶性物质可以需要从此溶液过滤出去。将所得的溶液送入沉淀步骤358,在这里与硫酸铵360接触以沉淀出偏钒酸铵。将所得的浆料送入过滤步骤362,并且将所回收的固体送入焙烧步骤364以脱除铵和随后获得固体v2o
5 366。废气368可以送到洗涤步骤370,在这里与硫酸接触以回收硫酸铵372。所回收的硫酸铵372可
以然后返回到沉淀步骤358。
172.将来自过滤步骤362的贫化液374送入结晶步骤376以回收硫酸钠晶体。将所得的浆料送入过滤步骤378,将所回收的固体送入干燥步骤380以回收最终的硫酸钠产物382。初级滤液383循环返回到结晶步骤376,并将经洗涤的滤液384送入溶解步骤356。在本发明的一种形式中,将贫化液374或初级滤液383送入离子交换步骤(未显示)以回收残余的钒物质。
173.在图5中显示根据本发明另一个实施方案的用于从进料流402回收钒400的方法。
174.将进料流402送入初级研磨步骤404,在这里将进料流的粒度降低到目标尺寸。将初级研磨出料406送入浸提步骤408,在这里与碱性碳酸盐浸提溶液410接触。在如图5所示的实施方案中,钠或钾可以用作载体,并且碱性碳酸盐浸提溶液410将优选包含钠或钾的碳酸盐/碳酸氢盐。在此实施方案中,将新鲜的碳酸钠/碳酸钾溶液直接加入浸提步骤408。在初级浸提步骤408期间,所述浸提溶液将钒提取到溶液中。初级浸提步骤408是在基本上与浸提步骤20相同的条件下操作。根据所用的准确进料材料,在进料中的钒物质可以许多不同的形式存在。例如,钒酸钙物质可以包括ca(vo3)2、cav2o6.3h2o、cav2o6.4h2o、cav6o
16
.9h2o、ca
2v2
o7.9h2o、ca
3v10o28
.16h2o。作为示例,在进料中的钒酸钙可以在浸提过程中与碱性液16按照下式反应:
175.ca(vo3)2 m2co3=caco3 2mvo3176.ca
2v2
o7 2m2co3=caco3 m
4v2
o7177.(其中m是碱金属或碱土金属)
178.如本领域技术人员所理解,上述反应仅仅用于说明目的,并不是在浸提步骤期间出现的反应的穷尽性列表。
179.在如图5所示的实施方案中,二氧化碳未被引入浸提步骤以再生碳酸盐,并且允许浸提步骤进行直到在浸提溶液中的至少显著量的碳酸盐被消耗。在采用间歇浸提工艺的情况下,浸提步骤的停留时间足以允许碳酸盐含量降低到目标浓度。作为另一种选择,在使用多个浸提罐的情况下,这些罐可以布置为按照能确保在最终阶段中的碳酸盐含量被降低到目标浓度的方式进行操作。
180.来自初级浸提步骤的所得浆料送入固液分离步骤(未显示)以从富集浸出溶液414除去浸提残余物412。
181.初级浸提溶液414送入钒回收回路416。在如图5所示的实施方案中,将初级浸提溶液418送入结晶步骤420以使钒酸钠/钒酸钾结晶。因为初级浸提溶液414基本上不含碳酸盐物质,所以结晶可以在简单的蒸发结晶器中进行。
182.所得的浆料送入过滤步骤(未显示)以回收固体钠/钾钒酸盐产物422。贫化富集浸出溶液424含有氢氧化钠/氢氧化钾,并被送入结晶步骤426,在这里与硫酸接触以使硫酸钠/硫酸钾428结晶。
183.固体的钒酸钠/钒酸钾产物422溶解在硫酸溶液428中,并将所得的溶液送入沉淀步骤430,在这里与氨/硫酸铵432接触以沉淀出偏钒酸铵。所回收的固体(amv)送入焙烧步骤434以脱除铵和随后回收v2o
5 436。废气438可以进行处理以回收硫酸铵440。所回收的硫酸铵440可以然后返回到沉淀步骤430。
184.在如图5所示的实施方案中,为了简化流程,没有进行从贫化的富集浸出溶液再生
碳酸盐的操作。实际上,将新鲜的试剂410直接加入初级浸提步骤408。虽然在初级浸提步骤408中使用新鲜的试剂将增加所用试剂的成本,但是本发明人发现这可以通过有价值的副产物硫酸钠/硫酸钾固体来补偿。虽然在此实施方案中也可以使用钠或钾,但是硫酸钠副产物的价值似乎小于硫酸钾副产物的价值。
185.在图6中显示根据本发明另一个实施方案的用于从进料流402回收钒500的方法。方法500具有许多与方法400相似之处,并且相似的符号表示相似的部件。
186.将进料流402送入初级研磨步骤404,在这里将进料流的粒度降低到目标尺寸。将初级研磨出料406送入浸提步骤408,在这里与碱性碳酸盐浸提溶液410接触。碱性碳酸盐浸提溶液410将优选包含碳酸钠/碳酸氢钠或碳酸钾/碳酸氢钾。在此实施方案中,将碱性碳酸盐溶液直接加入浸提步骤408。在初级浸提步骤408期间,此浸提溶液将钒提取到溶液中。初级浸提步骤408是在基本上与浸提步骤20相同的条件下操作。
187.在如图6所示的实施方案中,二氧化碳未被引入浸提步骤以再生碳酸盐,并且允许浸提步骤进行直到在浸提溶液中的至少显著量的碳酸盐被消耗。在采用间歇浸提工艺的情况下,浸提步骤的停留时间足以允许碳酸盐含量降低到目标浓度。作为另一种选择,在使用多个浸提罐的情况下,这些罐可以布置为按照能确保在最终阶段中的碳酸盐含量被降低到目标浓度的方式进行操作。
188.来自初级浸提步骤的所得浆料被送入固液分离步骤(未显示)以从富集浸出溶液414除去浸提残余物412。
189.将初级浸提溶液414送入钒回收回路416。在如图6所示的实施方案中,将初级浸提溶液418送入结晶步骤420以使钒酸盐固体结晶。因为初级浸提溶液414基本上不含碳酸盐物质,所以结晶可以在简单的蒸发结晶器中进行。
190.将所得的浆料送入过滤步骤(未显示)以回收固体钒酸盐产物422。贫化的富集浸出溶液502含有氢氧化钠/氢氧化钾,并循环到浸提步骤408。贫化的富集浸出溶液502可以与二氧化碳503接触以从氢氧化物溶液再生碳酸盐。
191.将固体钒酸钠/钒酸钾产物422溶解在硫酸428中,并将所得溶液送入沉淀步骤430,在这里与氨/硫酸铵432接触以沉淀出偏钒酸铵。所回收的固体进入焙烧步骤434以进行脱铵和随后结晶出固体v2o5片料436。废气可以进行处理以回收硫酸铵,如图5,400所示。所回收的硫酸铵可以然后返回到沉淀步骤430。来自沉淀步骤430的滤液503进入结晶步骤504以回收硫酸钠或硫酸钾506。
192.在图7中显示根据本发明另一个实施方案的用于从进料流702回收钒700的方法。
193.将进料流702送入筛子,并将筛上物料分配到粗料储存库704。将筛下物料送入储存斗706。在储存斗706中的材料以受控速率添加到进料传送器708上。将加满的(top-up)固体碳酸钠710按照所需速率添加到在传送器上的材料上。合并的料流711进入初级研磨步骤712,在这里将进料流的粒度降低到目标尺寸。在初级研磨步骤712中将工艺水加入装有进料的磨机中。工艺水溶解了固体碳酸钠710,由此形成碱性碳酸盐溶液,该溶液开始从合并的料流711浸提有价值的钒物质。工艺水也可以包含已溶解的碱性碳酸盐材料,并且循环含水料流可以从工艺的其他部分循环,例如sx萃余液。初级研磨出料713进入旋风分离器714以分离出初级进料流716(旋风分离器的上溢流)。超过尺寸的底流718返回到初级研磨步骤712以进一步加工。上溢流的料流716应当具有《200μm的目标粒度,优选的目标粒度是《100μ
m,更优选《75μm。
194.初级进料流716进入初级浸提步骤720,在这里,溶解于溶液中的碳酸钠和/或碳酸氢钠将有价值的钒物质进一步提取到溶液中。此浸提溶液优选加热到目标温度范围,并保持此溶液的ph。优选的温度范围是70℃至90℃。初级浸提步骤720是在基本上与浸提步骤20相同的条件下操作。
195.如上文关于方法10所述,在进料材料中存在的cao或ca(oh)2将与浸提溶液中的na2co3/nahco3反应,由此得到固体caco3和naoh。如果没有其他碳酸盐被引入浸提溶液中,此浸提溶液的碳酸盐浓度将随着碳酸盐被转化成固体而降低。这留下基本上包含氢氧化物的浸提溶液,限制将钒进一步提取到溶液中,并提高溶液的ph,由此促进一些杂质进一步溶解。将二氧化碳料流722注入浸提步骤以在浸提溶液中从naoh再生na2co3/nahco3,并保持ph处于8.0-11.0的目标范围内,优选9.5-10的范围。
196.由于限制浸提(包括粒度、钒的释放和碳酸钙沉淀),浸提残余物可以仍然含有高的钒含量,并可以进一步加工以进一步回收钒。在如图7所示的实施方案中,将浸提出料浆料送入尺寸缩减步骤724以降低固体的粒度。在一个实施方案中,目标最大粒度优选是约75微米,或者可以使用较小的最大粒度以实现更大程度的释放和钒回收。如在方法10中所讨论,本发明人认为固体caco3将在进料表面上作为涂层形成。本发明人发现,通过使涂覆的(部分浸提的)进料进行尺寸缩减步骤724,可以除去至少一部分的caco3,并降低粒度,暴露出未反应的进料的表面,且允许进一步浸提钒。可以考虑在尺寸缩减步骤724中使用任何合适的磨机装置。合适装置的例子包括球磨机、棒磨机(包括竖式辊磨机)、自磨型(ag)磨机和半自磨型(sag)磨机。如果在磨机内的液体中存在碳酸盐/碳酸氢盐,则可以在再研磨机724中发生额外的浸提。
197.将来自尺寸缩减步骤724的出料送入二级浸提步骤726,在这里在溶液中的已溶解的碳酸钠和/或碳酸氢钠将有价值的钒进一步提取到溶液中。浸提溶液优选加热到目标温度范围,并保持溶液的ph。二级浸提步骤726是在基本上与浸提步骤720相同的条件下操作。将二氧化碳料流725注入二级浸提步骤726以在浸提溶液中从naoh再生na2co3/nahco3,并保持所需的ph。
198.将浸出浆料728送入固液分离步骤730以将固体料流732与二级浸提溶液734分离开。将二级浸提溶液734送入浸提液调整阶段736。所回收的固体732在过滤器上用来自蒸发器的水或盐水和溶剂萃余液洗涤,如下文详述。将所得的浆料送入尺寸缩减步骤742以按照与步骤724相似的方式降低固体的粒度。作为另一种选择,浸出浆料728可以送入一个或多个尺寸缩减步骤,其中每个尺寸缩减步骤之后是浸提步骤。
199.将来自尺寸缩减步骤742的出料送入三级浸提步骤744以进一步提取钒。将二氧化碳料流746注入此浸提步骤以在浸提溶液中从naoh再生na2co3/nahco3。在三级浸提步骤744期间,按照与所述初级和二级浸提阶段相似的方式将溶液的温度和ph保持为目标值。如上所述,按照需要可以在三级浸提步骤744之后进一步组合多个尺寸缩减步骤和浸提步骤。
200.将三级浸出浆料748送入固液分离步骤750以将固体料流752与三级浸提溶液754分离开。将三级浸提溶液754送入浸提液调整步骤736。过滤后的固体在过滤器上进行一次或多次洗涤,优选按照逆流方式进行,从而从滤饼回收任何夹带的溶液和任何可溶性钒或钠。收集经洗涤的回收固体,并可以送至储存或其它应用。
201.将来自二级浸提步骤726和三级浸提步骤744的合并浸出溶液送入调整步骤736。在调整步骤736中,调节ph和温度,并加入促凝剂以帮助除去胶态二氧化硅。将所得的溶液送入固液分离步骤756以从经处理的浸出溶液758除去任何固体。
202.将经处理的浸出溶液758送入钒溶剂萃取回路的萃取阶段,在这里与包含钒萃取剂760的有机溶液接触。钒被负载到钒萃取剂上,并将负载的有机溶液762与含水浸提溶液分离开。然后,从负载的有机溶液762回收钒产物。
203.在如图7所示的实施方案中,钒萃取回路包含萃取阶段764、洗涤阶段766和反萃取阶段768,由此从经处理的浸出溶液758将钒选择性地回收到钒反萃取液770中。
204.不含钒的(或贫化钒的)sx萃余液772进行过滤以除去夹带的固体和有机物,并送入储存罐以进一步加工。sx萃余液772主要用于初级碾磨回路中。将过量的sx萃余液772送入蒸发器774以提高钠浓度。浓缩的溶液可以然后循环到浸提阶段或尺寸缩减步骤之一。
205.在本发明的一个实施方案中,萃取阶段764包括一个或多个溶剂萃取接触器,例如混合澄清器或柱接触器。更优选地,萃取阶段764包括两个或更多个溶剂萃取混合澄清器。进一步优选地,萃取阶段764包括三个或更多个溶剂萃取混合澄清器。
206.在其中萃取阶段764包括两个或更多个溶剂萃取混合澄清器的一个实施方案中,两个或更多个溶剂萃取混合澄清器是串联布置的。
207.在其中萃取阶段764包含串联布置的两个或更多个溶剂萃取混合澄清器的一个实施方案中,混合澄清器布置用于逆流操作。
208.将经处理的浸提溶液758送入第一个混合澄清器,在这里与包含钒萃取剂760的有机溶液接触,由此从经处理的浸提溶液758选择性地萃取钒。经处理的浸提溶液758和包含钒萃取剂760的有机溶液按照逆流布置的方式接触,以使萃取效率最大化。
209.在本发明的一个优选形式中,钒萃取剂是季铵萃取剂。优选地,钒萃取剂是aliquat 336.
210.在本发明的一种形式中,有机溶液包含改进剂。在本发明的一种形式中,有机溶液包含0%至50%的改进剂。在一个实施方案中,有机溶液包含25%至35%的改进剂。在一个实施方案中,有机溶液包含5%至10%的改进剂。如本领域技术人员所理解,改进剂可以用于改进溶剂萃取体系的化学或物理性能。在本发明的一种形式中,改进剂是选自十三烷醇、异癸醇或异十三烷醇。
211.在本发明的一种形式中,有机溶液不进行稀释。在本发明的一种形式中,用稀释剂将有机萃取剂稀释到目标浓度。优选地,目标浓度是基于体积计的20%至40%。更优选地,目标浓度是基于体积计的约25%。在一个实施方案中,目标浓度是5%至10%。如本领域技术人员所理解,有机溶液的稀释是用于控制粘度和改进相分离。在本发明的一种形式中,其中用稀释剂稀释有机溶液,稀释剂是煤油或shellsol 2046。
212.在本发明的一种形式中,在萃取阶段中有机相与水相之间的比率是12:1至1:12。优选地,在萃取阶段中有机相与水相之间的比率是4:1至1:4。更优选地,在萃取阶段中有机相与水相之间的比率是1:1至1:2。如本领域技术人员所理解,在萃取阶段中有机相与水相之间的比率取决于在富集浸出溶液中的钒含量以及在有机相上的钒负载。一种计算萃取剂的平衡浓度的方法是使用物质平衡,即其等于在萃取剂的总(分析)浓度与在溶剂相中的所有溶解物质的总和之间的差异。如溶剂萃取领域的技术人员所熟知,掌控在钒萃取和反萃
取阶段中的o:a比率可以用于同时提高在最终的反萃取溶液中的钒浓度,并同时改进产物钒溶液的纯度。
213.在本发明的一种形式中,在萃取阶段中的富集浸出溶液的目标ph是8至11。在本发明的一种形式中,在萃取阶段中的富集浸出溶液的目标ph是9至10。在本发明的另一种形式中,不控制ph。
214.负载的有机溶液762进入洗涤阶段766。在洗涤阶段766中,负载钒的有机溶液762与一部分的洗涤液接触。洗涤液置换在萃取阶段764中被负载到有机溶液762中的任何弱负载的或夹带的杂质元素。在一个优选实施方案中,洗涤液是从稀释的反萃取液制得。在洗涤阶段中控制o:a比率以确保在接触器中的合理的o:a比率,同时仅仅较少量的负载的洗涤液进入萃取阶段764。在本发明的一个实施方案中,负载钒的有机溶液与含水洗涤液之间的比率是基于体积计的1:1至1:2(有机相:水相)。
215.在本发明的一个实施方案中,洗涤阶段766包括一个或多个混合澄清器。
216.来自洗涤阶段766的水相返回到第一个萃取混合澄清器764。来自洗涤阶段766的负载的有机溶液进入反萃取阶段768。在反萃取阶段768中,负载的有机溶液与反萃取溶液776接触,以将在有机相上的大部分钒离子置换到水相中,由此得到钒反萃取液770。
217.在本发明的一个实施方案中,反萃取溶液是选自下组:碳酸钠,碳酸铵,氯化铵,碳酸铵,氨,硫酸,氢氧化钠和氢氧化钾。在一个优选实施方案中,反萃取溶液是氢氧化钠溶液。优选地,至少一部分的氢氧化钠是从工艺的其它部分循环而得。
218.在一个实施方案中,反萃取阶段768包括一个或多个混合澄清器。优选地,反萃取阶段768包括两个或更多个混合澄清器。更优选地,反萃取阶段768包括三个或更多个混合澄清器。在其中反萃取阶段768包括两个或更多个混合澄清器的实施方案中,两个或更多个混合澄清器按照串联方式布置。
219.在本发明的一种形式中,负载钒的有机溶液与含水反萃取溶液之间的比率是基于体积计的2:1至10:1(有机相:水相),优选此比率是基于体积计的5:1至7:1(有机相:水相)。
220.从反萃取阶段768排出的有机相778循环到萃取阶段764,在这里再次负载钒。以此方式,有机相778保持处于钒溶剂萃取回路内的闭合回路中。来自反萃取阶段768的钒反萃取液770被送入钒回收操作。
221.在如图7所示的实施方案中,将钒反萃取液770送入脱硅步骤780中,在这里与铝盐、例如硫酸铝接触,从而沉淀出铝二氧化硅化合物。二氧化硅的去除可以需要进行ph调节,这在大多数情况下可以用少量硫酸实现。
222.沉淀的固体和其它不溶性物质在固液分离步骤782中被除去。
223.将滤液送入沉淀步骤784,在这里与硫酸铵786接触以沉淀出偏钒酸铵。可以将硫酸加入沉淀步骤以控制溶液的ph,从而优化钒的回收。优选的目标ph是8
–
9。所得的浆料进入增稠步骤788,并且澄清的上溢流溶液(amv贫化液)790进入离子交换步骤792。增稠器的底流进入过滤步骤794,并且滤液相似地进入离子交换步骤792。过滤所得的固体用稀硫酸铵溶液洗涤以除去任何夹带的液体,并进一步提纯滤饼。所回收的固体796进入焙烧步骤798以进行脱铵,随后进行粉末熔融,并得到固体v2o5片料800。废气802可以进入洗涤步骤804,在这里与硫酸接触以回收氨和形成硫酸铵806。所回收的硫酸铵806可以然后返回到沉淀步骤784。
224.增稠器的上溢流790和来自过滤步骤794的滤液与来自蒸发器774的渗出溶液合并。在此流程中,合并的低钒含量液体进入任选的离子交换回路以进行钒回收。另一种相似的流程可以不包括此阶段,并仍然在硫酸钠回路之后回收剩余的钒。在如图7所示的实施方案中,此溶液进入离子交换步骤792以从该溶液将钒回收到离子交换介质上。随后使用氢氧化钠从离子交换介质反萃取出钒,并将反萃取溶液776送入反萃取阶段768。ix萃余液810进入结晶步骤812以回收硫酸钠晶体。所得的浆料进入固液分离步骤814,例如进行离心,并且将所回收的固体送入干燥步骤816以回收最终的硫酸钠产物820。初级滤液(或浓缩物)822循环返回到沉淀步骤784。
225.实施例1
226.将400g的钢渣(lulea复合材料)样品以15重量%固体的浆料密度加入400gpl碳酸钠溶液(在perth scheme水中配制)中,并在玻璃反应器中搅拌。定期加入过氧化氢以保持eh接近零。此试验在90℃下保持12小时。在12小时后停止试验,并使浆料进行过滤、分析和储存。原始数据如表1所示。
227.表1:浸提分析
[0228][0229]
这证明了所述浸提对于钒的选择性高于对于其它钛和铁的选择性。
[0230]
实施例2
[0231]
将含有2.4%v的炉渣进行湿碾磨到p80 75微米。然后,经碾磨的产物使用含有50g/l碳酸钠的溶液以15%固体进行碱性碳酸盐浸提。此试验在环境条件、25-30℃和大气压下进行。通过喷入二氧化碳,ph降低并保持在ph 10.0。钒的提取率在浸提5小时达到47%。
[0232]
将浸出浆料过滤并洗涤,所得残余物研磨到更细的尺寸(p80《75微米)。经研磨的残余物然后使用含有50g/l碳酸钠的溶液以15%固体进行碱性碳酸盐浸提。此试验在环境条件、25-30℃和大气压下进行。通过喷入二氧化碳,ph降低并保持在ph 10.0。在进一步浸提5小时后,钒的总提取率(在两个浸提阶段之后)达到75%。
[0233]
实施例3
[0234]
含有3.1g/l v的碱性碳酸盐浸提溶液与有机溶液接触,所述有机溶液含有在shellsol 2046中的10%aliquat 336和5%异癸醇,o/a比率为1:5。所得的萃余液含有140ppm v,并且负载的有机相含有14.8g/l v。这得到单个阶段中的提取率为95%。
[0235]
实施例4
[0236]
将含有1.9%v和15.5%fe的炉渣样品进行湿碾磨到p80 75微米。然后,碾磨的产物使用含有200g/l碳酸钠的溶液以25%固体进行碱性碳酸盐浸提。此试验在喷入二氧化碳的情况下于25℃进行。ph降低并在浸提反应期间保持为ph 9.0-9.5。在8小时的浸提之后,
钒的提取率达到48%,且《1%的铁被浸提。
[0237]
实施例5
[0238]
将含有1.9%v和15.5%fe的炉渣样品进行湿碾磨到p80 75微米。然后,碾磨的产物使用含有200g/l碳酸钠的溶液以25%固体进行碱性碳酸盐浸提。此试验在喷入二氧化碳的情况下于65℃进行。ph降低并在浸提反应期间保持为ph 9.0-9.5。在8小时的浸提之后,钒的提取率达到55%,且《1%的铁被浸提。
[0239]
实施例6
[0240]
将含有1.9%v和15.5%fe的炉渣样品进行湿碾磨到p80 75微米。然后,碾磨的产物使用含有200g/l碳酸钠的溶液以25%固体进行碱性碳酸盐浸提。此试验在喷入二氧化碳的情况下于90℃进行。ph降低并在浸提反应期间保持为ph 9.0-9.5。在8小时的浸提之后,钒的提取率达到63%,且《1%的铁被浸提。
[0241]
实施例7
[0242]
将含有1.9%v和15.5%fe的炉渣样品进行湿碾磨到p80 38微米。然后,碾磨的产物使用含有200g/l碳酸钠的溶液以25%固体进行碱性碳酸盐浸提。此试验在喷入二氧化碳的情况下于90℃进行。ph降低并在浸提反应期间保持为ph 9.0-9.5。在8小时的浸提之后,钒的提取率达到63%,且《1%的铁被浸提。
[0243]
实施例8
[0244]
将含有1.9%v和15.5%fe的炉渣样品进行湿碾磨到p80 75微米。然后,碾磨的产物使用含有200g/l碳酸钠的溶液以15%固体进行碱性碳酸盐浸提。此试验在770kpa的过压下使用50:50的co2:o2气体混合物于150℃进行。ph降低并在浸提反应期间保持为ph 9.5-10.0。在6小时的浸提之后,钒的提取率达到68%。
[0245]
将浸出浆料过滤并洗涤,所得残余物研磨到更细的尺寸(p80《38微米)。经研磨的残余物然后使用含有200g/l碳酸钠的溶液以7%固体进行碱性碳酸盐浸提。此试验在90℃和大气压下进行。通过喷入二氧化碳,ph降低并保持在ph 10.0。在进一步浸提6小时后,钒的总提取率(在两个浸提阶段之后)达到84%,且《1%的铁被浸提。
[0246]
实施例9
[0247]
将含有1.9%v和15.5%fe的炉渣样品进行湿碾磨到p80 38微米。然后,碾磨的产物使用含有200g/l碳酸钠的溶液以15%固体进行碱性碳酸盐浸提。此试验在770kpa的过压下使用50:50的co2:o2气体混合物于150℃进行。ph降低并在浸提反应期间保持为ph 9.0-9.5。在6小时的浸提之后,钒的提取率达到75%,且《1%的铁被浸提。
[0248]
实施例10
[0249]
从钢生产设备获得钢渣样品。将这些样品压碎到3.35mm的粒度,并组合以提供母料复合样品。母料样品进行头部分析(head assay)。发现此复合材料含有2.41%v、28.7%ca、4.06%si、0.91%al和17.0%fe。此复合材料的样品通过定量xrd进行分析。结果列于表2中。
[0250]
表2:母料复合材料的矿物组成
[0251][0252]
进行一系列浸提试验以评估各种浸提参数对从进料提取钒的影响。
[0253]
进行初始的基线浸提试验以进行对比。此试验包括在相同的p80 75μm、50℃和20%固体以及用二氧化碳喷射到目标ph 9.0的情况下浸提母料复合材料。浆料的ph在喷射二氧化碳5分钟内从ph》12.0降低到ph9.0,这表明游离氢氧根离子与二氧化碳的较快反应。在第一小时内,钒提取效率达到38%,此后的变化很小。
[0254]
粒度的影响:
[0255]
研磨尺寸的影响通过浸提母料复合材料样品来测定,其中在所有其他条件与基线实验相同的情况下,研磨尺寸为p80 106μm、75μm、53μm和p100 25μm。结果如图8所示。当在研磨尺寸为p80 106μm的情况下进行浸提时,显示钒提取率显著降低(约10%)。当在p80 75μm和p80 53μm的情况下浸提时,钒提取效率没有明显差异。但是当将进料研磨到p100 25μm时,钒提取效率显著提高( 25%)。这些结果显示研磨尺寸对于高的钒提取效率而言是重要的。
[0256]
温度的影响:
[0257]
温度的影响通过使被研磨到p80 75μm的母料复合材料在90℃下进行浸提来测定,其中所有其他条件与基线试验相同。结果如图9所示。在90℃下的钒提取效率稍微高于在50℃下的情况。
[0258]
碳酸钠浓度的影响:
[0259]
碳酸钠浓度的影响通过使被研磨到p80 75μm的母料复合材料在75g/l na2co3和125g/l na2co3中浸提来测定,其中所有其他条件与基线试验相同。结果如图10所示。钒提取率随着碳酸钠浓度的增加而升高,和在基线试验条件下在使用125g/l na2co3的情况下达到47%。但是,也应注意到随着碳酸钠浓度的增加,经浸提的固体的钠含量略微提高。对于50g/l、75g/l和125g/l na2co3的浸提试验,经浸提的固体分别含有0.73%na、0.77%na和0.78%na。
[0260]
固体百分比的影响:
[0261]
固体百分比的影响通过使被研磨到p80 75μm的母料复合材料用125g/l na2co3以55%固体在50-75℃下浸提来测定。此试验中没有使用50g/l na2co3,因为这种情况会导致在反应器中存在化学计算量不足的碳酸钠。结果如图11所示,并与基线试验以及与使用125g/l na2co3和20%固体的试验进行比较。钒的提取率与基线试验相比显著改进。应当说明的是,由于二氧化碳和氢氧化钠之间的放热反应,浆料的温度在此试验中提高到75℃。与基线试验相比,此试验的温度提高是更明显的,这是由于在液体中的较高浓度的钠和钒。在1小时后的浸提液含有48g/l的na和18g/l的v。
[0262]
氧化还原电势的影响:
[0263]
氧化还原电势(orp)的影响通过在基线试验条件下并且添加过氧化氢到》200mv的目标以浸提母料复合材料来测定。过氧化氢添加量(30%(v/v)是160kg/t炉渣。第二个试验是在基线试验条件下并且添加高锰酸钾(20kg/t)到》400mv的目标来进行。对于此试验,在14小时后,温度升高到90℃。结果如图12所示,并且与基线试验比较。
[0264]
显示添加氧化剂能改进钒的提取。在添加过氧化氢的情况下,在4小时后的钒提取率比基线试验高出8.7%。在添加高锰酸钾的情况下,在加热到90℃之后钒提取率提高15.5%。虽然氧化剂的添加导致比基线试验更高的钒提取率,但是没有提供与较细的研磨尺寸情况相比更高的提取率。这表明orp不是影响钒提取效率的唯一因素。
[0265]
实施例11
[0266]
钒提取效率理解为依赖于在炉渣中存在的钙反应形成碳酸钙的程度。本发明人认为在浸提步骤期间在炉渣粒子的表面上形成碳酸钙,阻止在炉渣中的钙被进一步浸提。进行一系列的浸提试验以评估经浸提的炉渣进行研磨和再浸提的影响,以尝试使更多的钙与碳酸盐反应。
[0267]
进行整体(bulk)浸提以制得经初级浸提的固体,其随后用于再研磨和浸提试验操作中。此试验包括经研磨的炉渣(p80 75μm)使用125g/l na2co3以48%固体进行浸提,其中二氧化碳喷入达到目标ph为9.2-10。在1、2、4和6小时的浸提之后获取动力学样品。钒提取的动力学是快速的,在1小时内达到51%v提取率,且在此之后没有明显变化。此试验的ph在初始的4小时内是10.0,然后在剩余2小时期间降低到9.20。
[0268]
经整体浸提的固体在机械搅拌式再研磨机中使用3-6mm陶瓷以50%固体被研磨到p80 38μm。然后,经研磨的产物使用125g/l na2co3以50%固体和在喷入二氧化碳达到ph为10.0的情况下进行浸提。此试验使用更细的粒度(p95 38μm)重复进行。结果如图13所示。数据表明较细的再研磨粒度导致较高的提取率;在p95 38μm的情况下达到37%v提取率,而在p80 38μm的情况下达到30%v提取率。从炉渣经由两个阶段的浸提和再研磨所达到的钒提取率分别计算为68.6%和65.2%。用于计算钒提取率所需的增重是使用钙作为内标来计算。
[0269]
实施例12
[0270]
进行此试验以确定是否能从实施例11的再研磨和浸提试验所得的炉渣进一步提取钒。p80 38μm的经浸提的固体在机械搅拌式再研磨机中使用3-6mm陶瓷以50%固体进行再研磨。然后,经研磨的产物使用125g/l na2co3以50%固体和在喷入二氧化碳达到ph为10.0的情况下进行浸提。结果如图14所示。在6小时后,三级浸提的钒提取率达到53%。从炉渣经由三个阶段的浸提和再研磨所达到的钒提取率计算为81.5%。用于计算钒提取率所需
的增重是使用钙作为内标来计算。此数据表明进一步的研磨和浸提能提取更多的钒。
[0271]
实施例13
[0272]
通过经由一系列的浸提和再研磨试验在不进行过滤和试剂补充的情况下加工炉渣来评估从炉渣提取钒的效果。进行此试验以确定是否能经由浆料单程通过数个再研磨/浸提步骤达到高的钒提取率。结果如图15所示。钒提取率在初级浸提之后达到65%。钒提取率在初级再研磨之后提高到69%,然后在二级浸提之后达到75%。钒提取率在二级再研磨之后稍微降低(74%),然后在三级浸提之后提高到77%。
[0273]
实施例14
[0274]
通过溶剂萃取从浸提溶液回收钒的效果是使用在shellsol 2046中的aliquat 336和异癸醇来评估。在开始时使用合成浸提液进行ph和分布等温试验。使用不同的试剂浓度进行两个ph等温试验。第一个试验使用在shellsol 2046中的5%aliquat 336和5%异癸醇,第二个试验使用在shellsol 2046中的10%aliquat 336和5%异癸醇。此试验包括将有机液和合成浸提液按照o/a比率为1:1进行混合,并在不同的ph下提取样品。使用50%naoh溶液提高ph。结果表明在8.5-9.5的ph范围内出现最佳的钒提取率。与使用5%aliquat 336的情况相比,在使用10%aliquat 336时的钒提取率显著更高,这表明5%aliquat 336是不充足的萃取剂。钒和二氧化硅的提取率随着ph的增加而降低,这可能是在ph 10.0下从负载的有机溶液选择性地洗涤二氧化硅。
[0275]
萃取分布等温线是通过合成浸提液与10%aliquat 336和5%异癸醇按照不同的o/a比率接触来产生。结果如图16所示。此数据表明,在使用3个阶段在o/a比率为0.8:1的情况下,可以将钒萃取达到在萃余液中《0.1g/l v。
[0276]
使用从浸提试验回收的浸提液进行萃取等温试验,此浸提液在ph 9.30下含有11.8g/l的v和0.49g/l的si。有机相含有在shellsol 2046中的20%aliquat 336和10%异癸醇。由于高的钒浓度,在此试验中使用比先前试验更高的有机相浓度。等温线如图17所示。此等温线显示在两个阶段中的钒提取率为约82%。但是等温线下凹,并在第三和第四阶段中预计提取率仅仅稍微提高。与钒相比,硅的萃取程度较低。在o/a比率为1:1的情况下,负载的有机相含有8.74g/l的v和0.177g/l的si。
[0277]
实施例15
[0278]
进行一系列试验以检测负载有机相的硅含量是否能在洗涤步骤中降低。
[0279]
在shellsol 336中含有10%aliquat 336和5%异癸醇的有机溶液用含有5.5g/l v、0.51g/l si和85g/l nahco3的合成溶液按照o/a比率为1:2进行负载。负载的有机溶液含有4.8g/l的v和0.13g/l的si。负载的有机溶液在与含有4.95g/l v的合成溶液在ph 10.0下单次接触来进行洗涤。经洗涤的有机相含有7.8g/l v和0.053g/l si。对于硅的洗涤效率在单个阶段中是59%,并且v/si比率从37:1提高到150:1。预期在第二洗涤阶段中达到更高的洗涤效率。使用在浸提试验中得到的浸提液重复进行负载和洗涤试验。负载的有机相含有12.5g/l的v和0.23g/l的si,并使用3g/l naoh按照o/a比率为1:1进行洗涤。经洗涤的有机相含有12.4g/l的v和0.20g/l的si;洗涤效率为30%。
[0280]
实施例16
[0281]
进行多个试验以评估反萃取液的组成对于从负载的aliquat 336和异癸醇进行反萃取的钒反萃取效率的影响。使用以下反萃取溶液进行试验。
[0282]
碳酸钠
[0283]
在shellsol 2046中的10%aliquat 336和5%异癸醇通过与含有3.3g/l v的浸提液在ph 9.0和o/a比率为1:10的情况下接触来负载钒。负载的有机相预期含有约5g/l的v。负载的有机相与含有200g/l na2co3的溶液按照o/a比率分别为5:1、2:1和1:1接触,所得的钒浓度分别为2.3g/l v、2.6g/l v和2.6g/l v,这表现为等温线凹陷。
[0284]
碳酸铵
[0285]
在shellsol 2046中的10%aliquat 336和5%异癸醇通过与含有3.3g/l v的浸提液在ph 9.0和o/a比率为1:10的情况下接触来负载钒。负载的有机相预期含有约5g/l的v。负载的有机相与含有200g/l(nh4)2co3的溶液按照o/a比率分别为2:1和1:1接触,所得的钒浓度分别为2.7g/l v和2.3g/l v,这表现为等温线凹陷。
[0286]
氯化铵/碳酸铵和氨
[0287]
在shellsol 2046中的10%aliquat 336和5%异癸醇用合成钒液负载并洗涤,由此得到含有约8g/l v的负载的有机相。负载的有机相与含有1.5m nh4cl和3m nh3的溶液分别按照o/a比率为5:1、2:1、1:1、1:2和1:5在50℃下接触。在所有接触的情况下出现结晶,并且在较高的o/a比率时结晶更显著。这些晶体含有钒。在去除晶体之后的液体分别含有1.7、0.98、0.86、0.77和1.2g/l的v。此试验使用1.5m(nh4)2co3和3m nh3重复进行。观察到相似的结晶。
[0288]
硫酸
[0289]
在shellsol 2046中的10%aliquat 336和5%异癸醇10%与含有5g/l v和85g/l nahco3的合成浸提液在o/a比率为1:2的情况下接触。含有2.2g/l v的负载的有机相与含有20g/l h2so4的溶液在o/a比率为1:1的情况下接触。随后降低ph以评估ph对钒反萃取的影响。使用20g/l h2so4在o/a比率为1:1的情况下达到较高的反萃取效率(65%),且平衡ph为1.25。在ph为0.81时,反萃取效率提高到80%。
[0290]
氢氧化钠
[0291]
评估使用氢氧化钠溶液作为钒反萃取剂从负载的有机相进行反萃取的情况。反萃取等温试验是使用含有在shellsol 2046中的20%aliquat 336、10%异癸醇、12.5g/l v和0.2g/l si的有机溶液以及含有125g/l naoh的反萃取溶液进行。预计在三个阶段中按照o/a比率为约5:1达到高的反萃取效率(90%)。预计负载的反萃取液含有55g/l的v。在使用125g/l naoh作为反萃取剂的情况下,负载的反萃取液将具有na/v比率为1.31(摩尔比率为3:1)。钒是作为原钒酸钠(na3vo4)存在于负载的反萃取液中。
[0292]
氢氧化钾
[0293]
也评估使用氢氧化钾溶液作为钒反萃取剂从负载的有机相进行反萃取的情况。反萃取等温试验使用含有在shellsol 2046中的20%aliquat 336、10%异癸醇和11.8g/l v的有机溶液以及含有130g/l koh的反萃取溶液进行。预计在三个阶段中按照o/a比率为约3:1达到高的反萃取效率(》85%)。预计负载的反萃取液含有35g/l的v。在使用130g/l koh作为反萃取剂的情况下,负载的反萃取液将具有k/v质量比率为2.60(摩尔比率为3.3:1)。钒是作为原钒酸钾(k3vo4)存在于负载的反萃取液中。
[0294]
实施例17
[0295]
进行一系列试验以从负载的反萃取液回收钒产物。对于这些试验,选择氢氧化钠
作为反萃取剂。初始试验致力于通过酸化(ph 5.0)和添加硫酸铵来沉淀。结果如表3所示。
[0296]
表3:使用含有原钒酸钠的反萃取液进行的钒酸铵试验
[0297][0298]
钒回收至固体的效率高,并达到97.4%。此产物含有40.3%的v,但是钠含量高达3.85%na。
[0299]
使用含有原钒酸钾的反萃取液通过酸化(ph 3.0)和添加硫酸铵来进行钒沉淀试验。结果如表4所示。
[0300]
表4:使用含有原钒酸钾的反萃取液进行的钒酸铵试验
[0301][0302]
钒回收至固体的效率较低,并达到79.5%。此产物含有46.3%的v,但是钾含量高达5.82%k。
[0303]
实施例18
[0304]
为了减少与钒共沉淀的硅的量,进行此试验以从反萃取液除去硅。从小型装置回收的含有钒酸钠的负载反萃取液使用98%硫酸进行酸化达到ph 8.0,并添加化学计算量的硫酸铝(作为35g/l al溶液)。此试验在70℃下进行4小时。结果如表5所示
[0305]
表5:脱硅试验
[0306][0307]
脱硅试验是成功的,其中》93%的硅沉淀。在脱硅之后,在负载的反萃取液中的硅浓度仅仅是4ppm。此固体含有高的钠和钒浓度,但是损失为《0.6%。考虑通过将这些固体送入浸提回路来回收钒。
[0308]
脱硅滤液与硫酸铵在30℃下反应6小时。硫酸铵的添加量是按照在进料液中所含的每公吨五氧化二钒计添加2公吨的硫酸铵。为了防止钠的共沉淀。在此试验中不添加酸,不像在脱硅试验中调节ph那样。结果如表6所示。
[0309]
表6:钒酸铵试验
[0310][0311]
钒酸铵沉淀试验是成功的。钒回收率是99.2%,钒酸铵含有42.9%的v和仅仅0.14%的na、0.08%的si、0.03%的fe和0.70%的s。
[0312]
实施例19
[0313]
所回收的钒酸铵在间歇式窑中进行焙烧。窑的温度在2小时内从环境温度升高到600℃,然后在600℃下保持2小时,随后冷却到环境温度。结果如表7所示。
[0314]
表7:五氧化二钒试验
[0315]
[0316]
钒酸铵的脱铵是成功的,获得五氧化二钒产物,其含有57%的v、0.19%的na、0.08%的si和0.03%的fe。如果没有其它有价值的杂质,则此产物含有》99.5%的v2o5。
[0317]
本领域技术人员能够理解,本文描述的本发明可以相对于具体描述的内容进行变化和改进。本发明包括所有这些变化和改进。本发明也包括在本说明书中提到或指出的所有的步骤、特征、配制剂和化合物,它们是单独或集合的形式以及任何两个或更多个步骤或特征的任何和所有组合。
再多了解一些
本文用于创业者技术爱好者查询,仅供学习研究,如用于商业用途,请联系技术所有人。