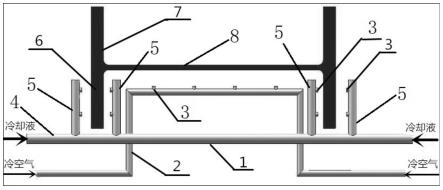
一种高强韧建筑用热轧h型钢及其制备方法
技术领域
1.本发明属于钢铁冶炼技术及轧制成型技术领域,具体地,本发明涉及一种高强韧建筑用热轧h型钢及其制备方法。
背景技术:
2.随着国内建筑工程质量的要求逐渐提高,国家对建筑结构钢的发展提出了更高的要求。尤其是装配式建筑方面,国家陆续出台政策,加大力度进行推广。装配式建筑具有良好的抗震性能、自重轻、施工速度快、工业化程度高、构件预制率高等技术优势,钢结构的使用满足先天的装配优势,施工工期相比传统工期有较大优势,装配式钢结构中的构件多为钢材,属于绿色环保建材,在回收和二次利用方面相比混凝土有着不可比拟的绿色环保优势。我国的装配式建筑占比较国外发达国家低很多。因此,国家要求按照适用、经济、安全、绿色、美观的要求,推动建造方式创新,大力发展装配式混凝土建筑和钢结构建筑,不断提高装配式建筑在新建建筑中的比例,完善钢结构建筑防火、防腐等性能与技术措施,加大热轧h型钢、耐候钢和耐火钢应用,推动钢结构建筑关键技术和相关产业全面发展。
3.热轧h型钢作为建筑结构用的主要材料,不同工况对其力学性能和耐蚀性能,耐火性能,结构稳定性能等提出了更高的要求。其中抗层状撕裂性能成为了重要的指标,来保证建筑结构钢的安全性和结构稳定性。抗层状撕裂性能钢又称z向钢,它主要采用钢板厚度方向拉伸试验的断面收缩率z来评价抗层状撕裂能力。对厚度超过15mm的钢材,只要结构件产生沿板厚方向的拉力或疲劳应力,一般都需要进行z向抗层状撕裂能力进行检验。对于普通建筑结构型钢而言只需要进行翼缘z向性能指标,对腹板也提出z向性能指标的较少。因此,为了满足装配式建筑和高层建筑用钢需求,综合抗层状撕裂性能优良的重要标志即翼缘和腹板z性能同时满足要求,随着厚度增加难度相应提高。
4.专利申请cn113564480a公开了一种具有z向性能的厚重热轧h型钢及其生产方法,所述热轧h型钢包括以下化学成分:c、si、mn、nb、ti、n、b、als,余量为铁和不可避免的杂质;所述生产方法包括以下步骤:铁水预处理
→
转炉冶炼
→
吹氩精炼
→
rh
→
异型坯全保护浇注
→
堆垛缓冷
→
轧制
→
轧后空冷;本发明通过合理的成分配比和工艺控制,通过开坯轧制 万能轧制 轧后空冷工艺,利用相变 析出 细晶组合强化的方式,调控第二向粒子析出数量,获得轧后粒状贝氏体含量在10~20%之间,使得翼缘厚度80mm以下重型热轧h型钢具备优良强韧性、z向性能,z向性能为65~80%。该专利通过贝氏体组织实现强化,但是贝氏体是跟冷速相关,因此,获得稳定均匀的贝氏体组织控制难度大,同时贝氏体钢无明显屈服现象。
5.专利cn103334051b公开了一种具有z向性能的建筑用热轧h型钢及其生产方法。本发明通过对冶炼工艺、轧制工艺进行优化,严格产品质量控制手段和产品生产过程控制,得到具有优良的z向性能和力学性能的钢种。h型钢包含的化学成分以重量百分比计为:c:0.06%~0.18%,si:0.10%~0.25%,mn:0.90%~1.60%,少于等于0.10%的v,少于等于0.060%的nb,少于等于0.030%的ti,以及余量的铁和不可避免的杂质。
6.专利号cn102418037b提供了一种具有抗层状撕裂性能的热轧h型钢及其生产方
法。根据本发明的制造h型钢的方法,不采用al脱氧,而是在出钢过程中向钢液中添加si以将钢液中的si调整至占钢液总重量的0.10%~0.15%来进行硅镇静脱氧,然后向钢液中加入预定量的ti和zr中的至少一种,其中,钢种需要的si含量可以在精炼时补加。根据本发明的热轧h型钢具有抗层状撕裂性能,能够满足一定的厚度方向的z向性能要求。
7.上述现有技术中,简单的微合金化不利于提高铸坯表面质量,对韧性提升受到严重制约;同时过高的碳含量容易造成焊接缺陷,引起轧机负荷大,轧件弯曲和偏头、尺寸不易控制,对设备要求高,导致h型钢综合性能和成品尺寸合格率比较低。
8.目前型钢生产中,控制冷却一直是困扰着性能均匀的严重问题。尤其是对于厚规格产品,翼缘和腹板厚度尺寸差距较大,采用单一冷却模式对最终性能的影响较大,同时会影响到z向性能的均匀性,导致差距较大,影响到结构的安全性。如何解决这一难题,兼顾成本和效率,一直是行业内的难题之一。部分企业采用超块冷设备,但是投资较大,同时对于单一有需求的产品品种而言经济性方面不合适。因此,对于整体z向性能均有需求的建筑结构钢产品,需要设计特殊的冷却设备满足性能要求。
技术实现要素:
9.为满足装配式建筑结构用钢的需求,本发明中针对上述需求对冷却系统进行特殊设计。提供一种屈服强度达到420mpa级别高强韧抗层状撕裂性能优良的建筑结构用热轧h型钢及其制备方法。此型钢产品适应于装配式建筑结构工程领域使用,其腹板和翼缘均具有较高的z向性能,均超过z35水平。为实现翼缘和腹板处z向性能优良,结合钢的成分设计,轧制过程设计增加翼缘和腹板温度均匀性控制装置,实现-20℃低温条件下良好冲击韧性,具有优良耐腐蚀性能以及焊接性能、低屈强比等特点,满足了普通地区和寒冷地区装配式建筑结构等钢建筑领域热轧h型钢材料应用需求。
10.为实现上述目的,本发明采用技术方案具体要求如下:
11.本发明提供一种420mpa级建筑用热轧h型钢,所述h型钢的化学成分按重量百分比为(wt%):c:0.06~0.10;si:≤0.25;mn:0.8~1.30;p≤0.015;s≤0.008;cu:0.15~0.25;cr:0.25~0.60;ni:0.10~0.19,v:0.01~0.03;al:0.01~0.03;re:0.009~0.019;as sn zn pb ca mg≤0.035。其余为fe及不可避免的杂质。冶炼过程控制钢中气体按重量百分比计,n≤0.008;t.[o]≤0.002。
[0012]
为降低屈强比,在低碳成分设计基础上仅采用钒氮合金单一的微合金化设计,同时严格控制含量,降低沉淀强化对屈服强度的影响,最终所述h型钢屈强比≤0.8。为提升耐低温韧性严格控制夹杂物数量和尺寸,在添加re元素进行夹杂物改质的基础上,控制其他残余元素含量优选as sn zn pb ca mg≤0.035。
[0013]
本发明所述的具有优良综合抗层状撕裂性能(z向性能)420mpa级钢结构用建筑用h型钢中添加各化学元素发挥作用如下:
[0014]
碳:根据强度420mpa级要求,低碳成分设计能够确保建筑结构钢具有一定的耐低温性能,同时保证产生一定的珠光体组织改善屈强比,适合建筑结构钢使用需求。在添加耐腐蚀元素后,较低碳含量能够避免产生魏氏体等异常组织。对于异型坯,易于控制横向和纵向腹板裂纹,因此考虑到组织性能和冶炼成本,本发明中碳的含量控制在0.06%~0.10%。
[0015]
硅:适量si有利于强度的提高;太高si含量容易产生贝氏体等组织;为避免再加热
过程产生大量fe2sio4从而影响表面质量,因此将si含量的上限设定为0.25%以下,优选0.25%以下,更优选为0.20%以下。
[0016]
锰:奥氏体稳定元素,可以显著增加钢的淬透性,同时以固溶强化的形式提高钢的强度,但是过高容易导致产生偏析,不同部位差别较大。厚规格建筑结构型钢不同部位组织有所差距,因此为了保证强度,同时降低淬透性,避免出现大量异常组织,优选将mn含量上限设定为1.30%。综合各种因素,本发明h型钢中控制mn含量在0.8~1.30%范围内;为获得420mpa级别强度,根据vn合金加入量,优选区间1.0~1.20%范围。
[0017]
磷:尽管高磷含量容易提高耐腐蚀性能,但是磷元素过高容易在脆化晶界导致恶化耐低温性能,因此磷控制越低效果越好,提高低温韧性;p控制在0.015%以下;
[0018]
硫:硫元素过高容易产生较多的mns等硫化物,在断面复杂型钢不同部位产生大量长条形mns夹杂物,降低低温韧性,同时不利于耐腐蚀性能提高,影响断面收缩率,即影响钢的抗层状撕裂性能,因此严格控制s≤0.008%;
[0019]
铜:提高钢材耐腐蚀性能基本元素,cu能够促进钢产生阳极钝化,从而降低钢的腐蚀速率,作为耐腐蚀钢的常用元素之一。其在锈层中富集能极大地改善锈层的保护性能;为达到锈层中cu富集效果,要求cu大于0.20%以上。但过高的cu含量不利于建筑结构型钢的焊接性能,而且也易产生铜脆现象。采用异型连铸坯生产抗层装撕裂性能型钢过程中,腿部角部容易由于铜的富集产生裂纹,严重影响铸坯表面质量,导致钢的塑性变差,在满足装配式建筑结构型钢耐腐蚀性能要求基础上,本发明cu含量控制在0.15~0.25%。
[0020]
镍:通过固溶强化提高钢材的强度,也是提高低温韧性有效元素,同时能够提高钢在连铸过程中的高温塑性,减少铸坯表面缺陷产生。ni一方面起到扩大奥氏体区,提高淬透性作用,另一方面能够细化珠光体片层细化珠光体,起到细晶强化作用。结合cu含量控制比例,该钢将ni含量控制在0.10~0.19%范围内。
[0021]
铬:提高淬透性、增加回火稳定性有助于钢的强度提高的元素,同时也是有助于提高钢材耐腐蚀性能的元素。它与cu、ni元素配合使用能显著提高钢的耐腐蚀性能。在c含量较低的情况下,添加适量的cr可以提高钢的硬度和强度,也能提高型钢的耐蚀性能。过量添加将降低材料的韧性、焊接性能和火焰切割性能。在组织控制方面,过多的cr元素影响钢的组织转变,产生贝氏体等异常组织。考虑到强度和提升耐腐蚀性能方面,本发明控制其含量在cr:0.25~0.60%。
[0022]
钒:是微合金化钢最常用也是最有效的强化元素之一。钒的作用是通过形成vn、v(cn)来影响钢的组织和性能,它主要是在奥氏体晶界的铁素体中沉淀析出,细化铁素体晶粒,从而提高材料的强度和低温韧性。考虑到沉淀强化对屈服强度的影响较大,同时提高强度,因此添加v在0.01~0.03%。
[0023]
稀土:稀土净化钢质,变质夹杂,减少点蚀和晶间腐蚀。钢中固溶稀土提高钢基体的极化电阻和自腐蚀电位,有利于提高钢基体的耐蚀性,改变锈层的组织结构,形成粘附性好、致密耐蚀性好的锈层,提高了高强耐候钢的耐蚀性。考虑到re稀土元素对mns等夹杂物改质需要进行适量添加,所以选择范围在re:0.009~0.019%,re稀土元素是一种复合添加的元素,考虑到经济性和性价比等因素,本技术中主要以镧和铈系元素为主,起到球化夹杂物作用。
[0024]
铝:al在低温钢制备过程中作为强脱氧元素添加使用。为了保证钢中氧含量尽可能地低,降低夹杂物含量,并且脱氧后多余的铝还可以和钢中的氮元素能形成aln析出物,
在加热和热轧过程细化奥氏体晶粒。所以,作为脱氧元素和细晶强化元素,铝含量控制在0.01~0.03%范围内。
[0025]
as、sn、zn、pb、ca、mg:作为钢中的残余元素对低温冲击韧性影响较大,同时对表面质量也有很大的影响。因此,作为钢中不能完全去除的元素,应该尽量减少其含量。结合生产实践及设备能力以及成本控制,残余元素总量控制在as sn zn pb ca mg≤0.035范围。
[0026]
氮:n含量太高,容易诱发铸坯质量缺陷;同时要保证vn合金化效果,因此本发明要求氮含量0.008%以下。
[0027]
氧:为了避免形成大颗粒的氧化物夹杂,恶化钢的韧性和塑性,本发明要求全氧含量t.[o]≤0.0020%。
[0028]
本发明的h型钢产品综合力学性能优良,屈服强度≥420mpa,抗拉强度≥520mpa,延伸率≥19%;-20℃纵向冲击功≥50j,适合低温条件地区建筑结构使用。腹板和翼缘z向性能优良,断面收缩率均≥60%。
[0029]
上述适合不同区域建筑结构应用的具有优良抗层状撕裂性能热轧h型钢制备方法主要包括如下步骤:铁水预处理—转炉冶炼—lf精炼—rh精炼—钢坯表面缺陷清理—异型连铸坯浇铸—钢坯步进式加热炉再加热—高压水除鳞—控温轧制 控制冷却—低温矫直—定尺锯切—收集码垛。
[0030]
将铁水、废钢在转炉 精炼炉(lf rh设备)中经冶炼、精炼及连铸工艺获得异型连铸坯,表面进行缺陷检测及清理后进入轧制成型工序。钢坯首先进入步进式加热炉进行再加热获得尺寸合适的奥氏体组织,经过粗轧和精轧后轧制成材,轧制过程进行控制轧制与冷却。需要说明的是在精轧最后一道次进行精准控温,通过开发的特殊冷却装置(参见附图2冷却装置图)满足h型钢的上下腿和翼缘上下两侧温度基本一致,保证了组织均匀条件下的翼缘和腹板z向性能的一致性,保证了装配式建筑结构使用该产品时候的结构稳定性和安全性。
[0031]
轧制过程控制轧制与冷却的主要工艺为:加热温度控制在1250~1300℃,根据尺寸不同粗轧末道次温度为1150~1050℃之间,累计变形率40%~60%,其余在精轧阶段完成。粗轧后进行三机架精轧,精轧终轧温度精准控制在800℃~850℃之间,使得奥氏体组织完全转变为珠光体和铁素体,实现细晶控制轧制。由于h型钢上下腿翼缘和腹板上下两侧均存在着30~50℃温差,在精轧最后道次出轧机后进行冷却控制,利用设计的冷却设备进行下腿和腹板采用喷嘴喷水精准控制冷却,根据检测温差进行相应的水流量控制。冷却后实现上下腿翼缘相同部位温差缩小到10℃以内,腹板上下表面缩小到5℃以内,从而保证了h型钢上下腿翼缘和腹板整体z向性能基本一致。出精轧后轧件通过输送辊道,根据环境温度采用保温罩进行冷却速率控制,避免不同季节环境温度出现较大的波动,影响最终性能。出精轧机后在冷床进行自然冷却,产品温度降至100℃以下后进矫直机进行矫直。轧材成品规格翼缘厚度范围为15-50mm。在h型钢翼缘部位和腹板中间部位取样进行力学性能检测。通过上述工艺生产的h型钢翼缘和腹板z向拉伸断面收缩率偏差控制在5%以下。
[0032]
作为优选,本发明提供的420mpa级抗层状撕裂性能优良的装配式建筑用热轧h型钢及其制备方法及具体工艺控制具体包括下面几个方面:
[0033]
1冶炼工序
[0034]
1)转炉冶炼
[0035]
转炉按照基本操作进行控制,主要工序包括严格控制高炉铁水中硫、砷等残余元
素含量并进行铁水质量优选处理,其中砷和锡均小于0.008%;转炉终渣碱度在2.1-3.9范围并采用挡渣出钢,出钢过程采用铝锰铁脱氧合金化。出钢过程分批加入脱氧剂、硅铁、金属锰、钒氮合金、铌铁合金、镍板等,最终转炉成分达到内控目标要求。
[0036]
2)精炼lf rh双联控制
[0037]
精炼过程采用lf rh双联控制气体和夹杂物。lf采用碳化钙、硅钙钡、铝粒调渣,出站前顶渣要做到白渣或黄白渣。进站取初样后定氧控制在[o]≤20ppm;喂钙线前加入re,全程按工艺要求进行底吹氮,软吹时间不低于20分钟,精炼周期不少于30分钟,lf精炼结束时刻钢水温度控制在1600~1620℃,提高钢水温度,以抵消rh处理时刻钢水的温降,rh处理时刻严禁采用“加铝产生化学热的方法升温”。
[0038]
rh精炼采用本处理模式,环流时间大于15min,纯脱气时间大于5分钟,处理结束后,每炉喂入200~250m钙铝线,软吹时间不低于10分钟,rh冶炼周期控制在40~50分钟。
[0039]
全程保护浇铸是指大包至中间包采用长水口并进行氩封保护;中间包采用覆盖剂结合碳化稻壳进行覆盖;中间包至结晶器采用浸入式水口并采用氩封保护;结晶器液面采用包晶钢保护渣;优选地,按重量百分比,包晶钢保护渣的成分为25%≤sio≤35%、35%≤cao≤45%、1.90%≤mgo≤3.00%、3.00%≤al2o3≤4.00%。
[0040]
3)连铸
[0041]
连铸过程采用全保护浇注工艺,使用大包长水口,增加密封圈控制;中间包采用塞棒包浇铸钢水;为提高效率异型连铸坯拉速1.0~1.2m/min;过热度控制在20℃-30℃以下能够防止水口堵塞;将冶炼好的钢水浇铸成近终型断面异型坯3个尺寸规格,由于合金量较多,为避免出现表面裂纹产生,异型坯浇铸成型后在保温坑或者沙坑或者使用保温毡进行缓冷处理。
[0042]
2轧制工序
[0043]
1)加热
[0044]
坯料采用在加热炉内进行奥氏体化均匀加热,加热及均热阶段温度控制在1250~1300℃,加热时间90~120min,然后出炉进行轧制。加热采用高温短时间加热,控制奥氏体均匀化和细化。
[0045]
2)控制轧制与控制冷却
[0046]
在大型产线采用控制轧制/控制冷却工艺。粗轧工序实现以形状为主的孔型轧制,轧制道次小于9道;精轧过程进行性能控制轧制,轧制道次小于7道。精轧终轧温度控制在800℃~850℃。冷床冷却轨道保持400℃以上的温度,产品在冷床进行集中缓慢冷却,防止冷速过快影响最终性能。产品温度降至200~300℃进矫直机进行矫直,保证表面初生氧化铁皮的完整性。
[0047]
本发明提供一种用于提高综合性能的冷却装置,轧制过程采用专门设计冷却装置进行腹板和翼缘综合冷却,冷却装置安装在精轧机后面,其中,冷却装置包括若干间隔分布的冷却液管道1和若干间隔分布的冷空气管道2,所述冷却液管道1,用于冷却翼缘,设置在热轧h型钢的下翼缘6下方,包括与腹板平行的第一翼缘管道4和与第一翼缘管4道垂直并连通的两组第二翼缘管道,每组第二翼缘管道各自对应一个翼缘;其中,所述每组第二翼缘管道包括两平行的下翼缘管道5,所述下翼缘管道5与下翼缘6相对的面设置有若干喷嘴3,用于冷却翼缘,h型钢的下翼缘6均置于两平行下翼缘管道5之间;所述冷空气管道2,用于冷却
腹板,呈凸型,设置在下翼缘6与腹板8之间,与腹板8平行且靠近的冷空气管道上设置有若干喷嘴3,用于冷却腹板8。冷空气管道的形状与下翼缘和腹板形成的形状相匹配。冷却速度根据腹板和翼缘厚度可以进行控制(参见图1)。该冷却装置安装在精轧机后面,在轧制最后一道次开启,安装翼缘和腹板分开进行冷却方式进行。图1中,编号1的冷却液管道用于翼缘冷却;由于翼缘厚度大,根据冷速需要采用冷却水或者其他冷却介质进行冷却。冷却液流量大小根据上翼缘7和下翼缘6在线测温装置进行温差测定后通过喷嘴3进行调节。由于腹板厚度较翼缘薄,因此采用冷却空气即可满足需要。编号2的冷空气管道用于腹板冷却;由于腹板上下部位温差较小,因此根据需要适当调节喷嘴3冷却空气的流量实现冷却。通过上述装置,满足了上下腿翼缘温差在5~10℃范围内,腹板温差在3~6℃范围内。从而保证了组织的均匀性,提升了建筑结构型钢的腹板和翼缘的z向性能。上述设备配合钒微合金化设计,能够实现最终热轧h型钢的性能要求,同时保证腹板和翼缘z向性能均达到较高水平。
[0048]
3)精整工序
[0049]
产品下线后进行表面和尺寸精整处理;为保证材料性能真实准确,在精整工序进行试样取样分析产品性能。
[0050]
与现有技术相比,本发明的优势在于:
[0051]
(1)低碳 微量vn合金化 re成分设计,与其他合金化相比简单高效,减少铸坯缺陷的发生率;(2)钢水低残余元素及杂质元素控制,有利于提高钢的塑性和低温韧性;(3)添加一定量的re元素,钢中夹杂物细小有利于同时提高翼缘和腹板抗层状性能;(4)采用异型坯单侧浇铸控制技术实现al脱氧工艺,提高钢水纯净度,同时避免长水口浇铸过程堵塞问题。(5)通过设计的专用喷水装置实现腹板翼缘均匀冷却工艺,实现腹板翼缘整体组织均匀性提高,抗层状撕裂性能同步控制和提升,整体提高h型钢综合强韧性能。(6)通过上述工艺,制备的h型钢屈服强度达到420mpa以上级别,实现了建筑结构钢减重,同时具有良好的耐腐蚀性能,z向性能,耐低温韧性等综合性能,完全满足目前装配式建筑结构钢的工程化需求。
附图说明
[0052]
图1(a)为本发明涉及h型钢生产冷却设置平面结构图;
[0053]
图1(b)为本发明涉及h型钢生产冷却设置立体结构图;
[0054]
图2(a)为本发明实施例1所得h型钢上腿显微组织图;
[0055]
图2(b)为本发明实施例1所得h型钢下腿显微组织图;
[0056]
图2(c)为本发明实施例1所得h型钢翼缘显微组织图;
[0057]
图3(a)为本发明实施例6所得h型钢上腿显微组织图;
[0058]
图3(b)为本发明实施例6所得h型钢下腿显微组织图;
[0059]
图3(c)为本发明实施例6所得h型钢翼缘显微组织图;
[0060]
附图标记:
[0061]
1、冷却液管道,2、冷空气管道,3、喷嘴,4、第一翼缘管道,5、下翼缘管道,6、下翼缘,7、上翼缘,8、腹板之间。
具体实施方式
[0062]
下面结合具体实施例对本发明作进一步说明。
[0063]
下面对本发明予以详细描述:
[0064]
表1为本发明各实施例及对比例的化学成分列表;
[0065]
表2为本发明各实施例及对比例的主要工艺参数列表;
[0066]
表3为本发明各实施例及对比例的性能检测列表。
[0067]
本发明各实施例均按照以下步骤进行生产:
[0068]
1)优选低磷低硫以及低残余元素铁水入炉后在转炉内冶炼后进入lf rh双联进行成分及夹杂物控制;lf精炼结束时刻钢水温度控制在1600~1620℃,提高钢水温度,以抵消rh处理时刻钢水的温降,rh处理时刻严禁采用“加铝产生化学热的方法升温”;rh精炼采用本处理模式,环流时间大于15min,纯脱气时间大于5分钟,处理结束后,每炉喂入200~250m钙铝线,软吹时间不低于10分钟,rh冶炼周期控制在40~50分钟。
[0069]
最终连铸成异型坯,根据翼缘厚度不同分为三个坯型。铁水残余元素严格控制在as sn zn pb ca mg≤0.035;浇铸过程控制浇铸过热度小于20℃,在拉坯速度为1.0~1.18m/min内任选其中一个数值作为恒定拉坯速度,矫直温度不低于850℃。
[0070]
2)轧制工序,坯料采用在加热炉内再加热温度控制在1250~1300℃,加热时间90~120min,然后出炉进行轧制。采用控制轧制/控制冷却工艺。bd粗轧工序轧制道次小于9道;精轧tm过程轧制道次小于7道。精轧终轧温度控制在800℃~850℃。冷床冷却轨道保持400℃以上的温度,产品在冷床进行集中缓慢冷却15min分钟以上。产品温度降至200~300℃进矫直机进行矫直。
[0071]
3)精整工序,产品下线后进行表面和尺寸精整处理;在精整工序进行试样取样分析产品性能。
[0072]
表1本发明各实施例及对比例的化学成分(wt.%)
[0073][0074]
[0075]
精炼主要工艺参数见表2
[0076]
表2精炼主要工艺参数
[0077][0078]
连铸过程具体工艺参数见表3。
[0079]
表3连铸过程工艺参数
[0080][0081]
表3为本发明各实施例及对比例的主要工艺参数列表;
[0082]
表4主要工艺参数
[0083][0084][0085]
表5为本发明各实施例及对比例的性能检测列表。
[0086]
表5:轧材力学性能记录表
[0087][0088][0089]
对试制产品抽样进行性能检验,力学性能所用的试样取样位置在h型钢翼缘由边部到心部1/3处,腹板取样在中间部位,参照标准为bs en iso 377-1997《力学性能试验试样的取样位置和制备》;屈服强度、抗拉强度、延伸率的试验方法参照标准iso 6892-1-2009
《金属材料室温拉伸试验方法》;冲击功试验方法参照标准iso148-1《金属材料夏比摆锤冲击试验》,结果参见表5。通过对比发现,利用本专利涉及的制备方法生产的h型钢翼缘和腹板z向性能均优于目前的专利产品中的产品。
[0090]
本发明未详细说明的内容均可采用本领域的常规技术知识。
[0091]
最后所应说明的是,以上实施例仅用以说明本发明的技术方案而非限制。尽管参照实施例对本发明进行了详细说明,本领域的普通技术人员应当理解,对本发明的技术方案进行修改或者等同替换,都不脱离本发明技术方案的精神和范围,其均应涵盖在本发明的权利要求范围当中。
再多了解一些
本文用于创业者技术爱好者查询,仅供学习研究,如用于商业用途,请联系技术所有人。