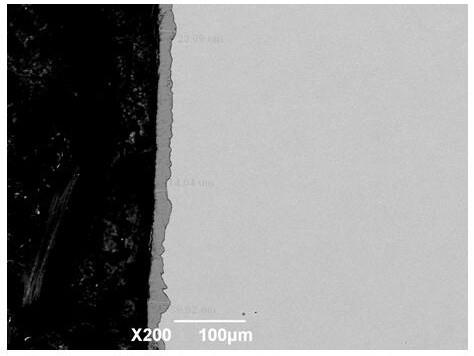
1.本发明属于低合金钢生产技术领域,涉及一种高强韧耐候桥梁钢板的生产方法。
背景技术:
2.随着经济的快速发展,跨江、跨海、跨山等桥梁建设的需求日益增加。从轻量化设计、安全可靠性、低维护成本及使用寿命等方面考虑,具有高强韧的耐候桥梁钢已成为当今桥梁结构用钢的主要发展方向。
3.合金元素对耐候桥梁钢耐大气腐蚀性能的影响已有大量研究,通常cu、ni、cr等合金元素含量越高,钢的耐大气腐蚀性能越出色。然而除了合金元素影响耐候性能之外,钢的组织尤其是表面组织状况对耐大气腐蚀性能的影响也至关重要,因此,钢板表面氧化铁皮即锈层的控制是耐候桥梁钢工程应用当中必不可少的环节。中国专利cn113621873b提出了一种具有稳定化锈层的耐候结构钢及其制备方法,通过周期性洒水的快锈处理和喷洒5%~10%的磷酸钾溶液的稳定化处理,使表面迅速形成一层稳定的锈层;中国专利cn113881935a提供了一种基于硅烷偶联剂的耐候钢表面锈层稳定化处理剂,可以防止耐候钢服役初期的锈液流挂与飞散以及促进稳定的保护性锈层形成;中国专利cn113529152a公开了一种实现钢铁材料快速生锈的表面处理方法,对钢的表面进行电解氧化处理,然后作湿润处理和脱水处理,使迅速在其表面形成均匀锈层。但这些方法不仅需要场地进行喷洒、浸涂、刷涂、雾化、电解等操作,而且增加了成本、延长了交货期,且采用的化学剂常对环境有一定污染。
技术实现要素:
4.本发明提供一种高强韧耐候桥梁钢板的生产方法,目的是使钢板表面生成一层粘附性极强的致密且均匀的氧化铁皮而提高钢板的耐大气腐蚀能力,同时钢板具有良好的强韧性,屈服强度≥500mpa、抗拉强度≥600mpa、-40℃冲击吸收功≥120j。
5.本发明的技术方案:一种高强韧耐候桥梁钢板的生产方法,钢的重量百分组成为c=0.05%~0.08%、si=0.10%~0.30%、mn=1.20%~1.50%、p≤0.015%、s≤0.005%、al=0.020%~0.050%、ti=0.010%~0.030%、nb=0.030%~0.050%、cu=0.30%~0.50%、ni=0.30%~0.60%、cr=0.40%~0.60%、mo=0.10%~0.20%,余量为fe和不可避免的杂质元素;关键工艺步骤包括:(1)加热:加热前对铸坯表面进行涂层处理,采用含有mg离子的油性涂料;然后采用步进梁式加热炉加热,控制炉内残氧量≤3.0%,控制均热温度为1200
±
20℃、加热时间≤300min;(2)轧制:铸坯出加热炉后经除鳞箱进行初除鳞,除鳞高压水压力不低于22mpa、除鳞速度不大于1.0m/s;初除鳞后板坯表面温度≥1100℃,然后将板坯摆动空冷待温1~3min,再开始进行两阶段控制轧制,第一阶段控制板坯表面温度≥1000℃,第二阶段控制板坯表面温度为a
r3
~900℃,其中a
r3
为过冷奥氏体向铁素体转变的开始温度,两个轧制阶段间将板坯返回至除鳞箱,再通过高压水除鳞降温,控制两个阶段间隔时间在60s以内;轧制过程高
压水除鳞,第一道次不除鳞、第二道次除鳞,之后每隔≥30s才进行一道除鳞但每隔≤60s至少要进行一道除鳞;(3)冷却:轧后钢板冷却一直到表面温度低于a
r3
之前都进行空冷,之后以10~20℃/s的表面冷却速度加速冷却,使钢板表面温度冷却到250℃之下;整个冷却过程中不使用拉弯矫直;(4)精整:采用离线火焰切边、定尺;(5)热处理:进行回火处理,回火前钢板表面不抛丸,控制回火温度为200~250℃。
6.优选地,步骤(2)中,当初除鳞后板坯表面温度≥1150℃时,板坯摆动空冷待温时间1~2min;当初除鳞后板坯表面温度介于1100~1150℃时,板坯摆动空冷待温时间2~3min。
7.优选地,步骤(2)中,控制终轧道次压下率低于5%。
8.优选地,步骤(4)中,如若板形不良,优先使用压平机进行压平。
9.本发明对钢板表面氧化铁皮的控制原理:对含较多ni、cr、cu的耐候桥梁钢,加热前采用含有mg离子的油性涂料对钢坯表面进行涂层,并结合均热温度、加热时间及炉内气氛、初除鳞工艺等的控制,目的是减少一次氧化铁皮的生成,并使其变得疏松,可以通过高压水除鳞完全去除;然后轧制前使板坯在较高温度下空冷氧化一段时间,以获得一层均匀完整的二次氧化铁皮,并通过轧制将这层氧化铁皮均匀压入基体,同时控制除鳞间隔时间,目的是一方面使压入的氧化铁皮逐渐变厚,另一方面又要防止长时间的氧化引起氧化铁皮起皮后再被压入而导致出现凹坑、应力集中等不利于耐大气腐蚀性能的缺陷。最终钢板经轧制后表面形成一层粘附性极强的致密且均匀的氧化铁皮。之后,为保护这层氧化铁皮的完整性和稳定性,采用的技术手段包括:(1)为减小冷却过程的表面拉应力,过冷奥氏体相变前采用低冷速的空冷方式来减小表面热应力,而一旦开始发生相变,就采用加速冷却使表面发生冷缩,并以此来抵消随之发生相变带来的体积膨胀。这里要注意表面冷却速度的控制,冷却速度太低,冷缩小,不足以抵消相变膨胀量,且容易生成对耐大气腐蚀不利的珠光体组织;冷却速度太高,冷缩大,又远超过相变产生的膨胀量,且生成较多的对韧性不利的马氏体组织;(2)为避免钢板表面氧化铁皮中发生feo的先共析转变和共析转变,而保留较多的粘附性更好的feo,采用加速冷却使钢板表面温度快速冷却到250℃之下,以及回火热处理时控制回火温度在250℃以下;(3)确保整个冷却过程中不使用拉弯矫直钢板,并为此创造条件,终轧优选采用小道次压下率以得到良好的轧制板形,同时冷却后如若板形不良,优先使用压平机进行压平,对防止氧化铁皮的脱落有利;(4)采用离线火焰切边、定尺以防止机械切割破坏边部的氧化铁皮,以及采用回火热处理以减小表面氧化铁皮的残余应力等。
10.本发明的有益效果为:(1)本发明通过精细调配耐候桥梁钢的化学组成和加热、轧制、冷却、精整及热处理工艺,使钢板表面获得一层粘附性极强的致密且均匀的氧化铁皮,起到“以锈止锈”的作用,同时钢板还具有高强韧性,屈服强度≥500mpa、抗拉强度≥650mpa、-40℃冲击吸收功≥120j;(2)本发明提出的一种高强韧耐候桥梁钢的生产方法,其过程工艺稳定可控,可批量生产。按照所述生产方法生产的成品钢板,其力学性能均匀、表面质量好,无需其它处理即可用于桥梁钢结构的制造和裸露使用。
附图说明
11.图1为本发明实施例1的耐候桥梁钢板表面氧化铁皮的微观形貌图。
具体实施方式
12.以下结合实施例及附图对本发明的内容作进一步说明。
13.实施例1高强韧耐候桥梁钢板的生产方法,钢的化学组成重量百分比为c=0.06%、si=0.19%、mn=1.34%、p=0.011%、s=0.002%、al=0.036%、ti=0.015%、nb=0.038%、cu=0.38%、ni=0.50%、cr=0.52%、mo=0.16%,余量为fe和不可避免的杂质元素;关键工艺步骤包括:(1)加热:加热前对铸坯表面进行涂层处理,采用含有mg离子的油性涂料;然后采用步进梁式加热炉加热,加热过程炉内残氧量最高为2.2%,均热温度为1200
±
5℃、加热时间为280min;(2)轧制:铸坯出加热炉后经除鳞箱进行初除鳞,除鳞高压水压力为22mpa、除鳞速度为1.0m/s;初除鳞后板坯表面温度为1170℃,然后将板坯摆动空冷待温100s,再开始进行两阶段控制轧制,第一阶段板坯表面温度为1145~1080℃,第二阶段板坯表面温度为805~900℃(过冷奥氏体向铁素体转变的开始温度a
r3
为730℃),两个轧制阶段间将板坯返回至除鳞箱,再通过高压水除鳞降温,两个阶段间隔时间为52s;轧制过程高压水除鳞道次安排:第一道次不除鳞、第二道次除鳞,之后每隔≥30s才进行一道除鳞但每隔≤60s至少要进行一道除鳞;具体各轧制道次及轧制钢板表面温度、距上一次除鳞的间隔时间、是否除鳞的情况见表1;终轧道次压下率为3.3%;(3)冷却:轧后钢板冷却一直到表面温度为730℃之前都进行空冷,之后以15℃/s的表面平均冷却速度加速冷却,使钢板表面温度冷却到220~250℃;整个冷却过程中不使用拉弯矫直;(4)精整:采用离线火焰切边、定尺;(5)热处理:进行回火处理,回火前钢板表面不抛丸,回火温度为240
±
5℃。
14.对实施例1的耐候桥梁钢板表面氧化铁皮进行扫描电镜观察,如图1所示。可见实施例1钢板表面的氧化铁皮与钢基体结合紧密,完整性好,主要为feo,致密且均匀,厚度在14~30um。
15.对实施例1钢板进行力学性能检测,屈服强度为525mpa、抗拉强度为656mpa、断后伸长率为28%、-40℃夏比冲击功为173/178/182j。可见实施例1钢板具有良好的强韧性。
16.实施例2高强韧耐候桥梁钢板的生产方法,钢的化学组成重量百分比为c=0.07%、si=0.22%、mn=1.36%、p=0.012%、s=0.003%、al=0.038%、ti=0.020%、nb=0.036%、cu=0.32%、ni=0.41%、cr=0.42%、mo=0.11%,余量为fe和不可避免的杂质元素;关键工艺步骤包括:(1)加热:加热前对铸坯表面进行涂层处理,采用含有mg离子的油性涂料;然后采用步进梁式加热炉加热,加热过程炉内残氧量最高为2.9%,均热温度为1200
±
5℃、加热时间为240min;(2)轧制:铸坯出加热炉后经除鳞箱进行初除鳞,除鳞高压水压力为22mpa、除鳞速度为0.8m/s;初除鳞后板坯表面温度为1145℃,然后将板坯摆动空冷待温150s,再开始进行
两阶段控制轧制,第一阶段板坯表面温度为1100~1000℃,第二阶段板坯表面温度为780~890℃(过冷奥氏体向铁素体转变的开始温度a
r3
为741℃),两个轧制阶段间将板坯返回至除鳞箱,再通过高压水除鳞降温,两个阶段间隔时间为45s;轧制过程高压水除鳞道次安排:第一道次不除鳞、第二道次除鳞,之后每隔≥30s才进行一道除鳞但每隔≤60s至少要进行一道除鳞;具体各轧制道次及轧制钢板表面温度、距上一次除鳞的间隔时间、是否除鳞的情况见表2;终轧道次压下率为4.3%;(3)冷却:轧后钢板冷却一直到表面温度为740℃之前都进行空冷,之后以15℃/s的表面平均冷却速度加速冷却,使钢板表面温度冷却到220~250℃;整个冷却过程中不使用拉弯矫直;(4)精整:采用离线火焰切边、定尺;使用压平机对钢板进行压平;(5)热处理:进行回火处理,回火前钢板表面不抛丸,回火温度为220
±
5℃。
17.对实施例2钢板进行力学性能检测,屈服强度为511mpa、抗拉强度为642mpa、断后伸长率为29%、-40℃夏比冲击功为153/161/143j。可见实施例2钢板具有良好的强韧性。
18.表1实施例1的各轧制道次及钢板表面温度、除鳞情况。
19.表2实施例2的各轧制道次及钢板表面温度、除鳞情况。
再多了解一些
本文用于创业者技术爱好者查询,仅供学习研究,如用于商业用途,请联系技术所有人。