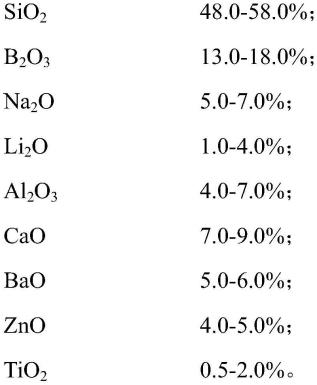
1.本发明属于放射性废物的处理与处置领域,特别是涉及一种碱硼硅酸盐固化玻璃及其制备方法和应用,尤其涉及高硫高钠废液玻璃固化处理的固化材料。
背景技术:
2.放射性废液处理是核能安全利用、可持续发展的最后一环。高放废液(即高浓度放射性废液)具有成分复杂、放射性强、生物毒性大、半衰期长等特点。核设施运行和退役产生和积累了-定数量的高放废液,长期贮存于专门的地下贮槽中,其较高的放射性水平和易于扩散的液态贮存方式,对国土和环境安全构成了潜在的巨大威胁。因此必须采取措施,尽早将其固化处理,转化为一种稳定的形式,以便于对它进行长期、安全、有效地贮存,并为今后的深地质永久处置提供条件。固化技术是目前国际上普遍认同的处理高放废液的最佳途径。高硫高钠废液为高放废液中的一种。
3.由于玻璃态内能高于同组成的晶态,因而玻璃总是存在析晶的趋势,而在玻璃固化体中,其碱、碱土含量高,而硅含量较低,使玻璃结构网络松散,料性长,自发析晶趋势明显。
4.硫在硼硅酸盐玻璃中溶解度较低,一般为0.6~0.8wt%(以so3形式表示),而未能完全溶解进入玻璃中的硫,以na2so4的形式分离成液态的黄相,漂浮在熔融玻璃池的顶部,在运行期间富集起来。黄相有非常不利的物理、化学性能,例如,钠盐易溶于水、抗浸出性能低,对放射性核素如cs和sr有很强的萃取倾向、极易在深地质处置中导致放射性核素从玻璃固化体中释放到环境中,同时对玻璃熔池壁耐材有很强的腐蚀作用、减弱炉体使用寿命等。因此,黄相的存在对高放废液的处理过程和玻璃产品的质量控制等方面非常不利,影响玻璃固化生产运行和导致产品质量的问题。
5.目前,影响固化玻璃析晶性能主要有两种因素:
6.(1)玻璃本身析晶:这通常可以通过调整组分(例如添加大量sio2、al2o3)来降低其析晶率,但是缺点是同时熔体的高温粘度和电阻率会增加。
7.(2)焦耳炉玻璃固化体析晶:
8.焦耳炉运行对玻璃固化体高温性能有严苛要求。当前我国引进国外第三代焦耳炉玻璃固化技术处理现存的高硫高钠废液。焦耳加热陶瓷熔炉内部为特制耐火陶瓷材料,炉体采用电极直接加热玻璃熔体的方式,运行温度可达1100~12000℃;该工艺采用连续加料,基础玻璃和高放废液的加入是按废液包容量投入;要求1150℃玻璃熔体的粘度值40
±
20dpa
·
s范围内。因此传统玻璃析晶性能调控的方法不适用。焦耳炉玻璃固化体析晶主要有两种方式:
9.(2.1)焦耳炉内部析晶:
10.焦耳炉中,控制出料方式为底部冻融法,冻融法卸料是由冻融法卸料装置完成,所述冻融法卸料装置主要包括出料管以及辅助加热线圈。卸料时,通过线圈加热管内凝玻璃,使玻璃熔化、出料。这意味这玻璃熔体在底部出料管中要经历从熔化温度到卸料温度长时
间的保温,反复升降温循环。此时,玻璃中含有贵金属及多种高价、溶解度低的氧化物,起到了晶核剂的作用,使玻璃成核析晶的趋势得到加强。当固化体中有晶体析出时,由于晶体熔化温度更高,熔体粘度将会增大,导致出料不畅,甚至堵塞现象的发生。放射性环境下,堵塞现象一旦发生,将带来无法估量的损失。
11.(2.2)玻璃固化体贮存过程中析晶:
12.高放废液经固化后形成的玻璃固化体仍具有放射性,在贮存过程中,将释放出大量热量。贮存初期,玻璃固化体的温度可能超过玻璃化转变温度,这同样会造成具有热力学平衡状态的晶体相析出。由于放射性核素衰变产生的辐射热,玻璃固化体将从其熔化温度开始经历缓慢冷却,块体中心与外表面的温度梯度随温度缓慢降低而下降,这种延迟冷却会导致更多晶相沉积。固化体中晶相的产生增加了相界面,放射性核素倾向于集中在相界面,相界面可能优先发生水的腐蚀,造成玻璃固化体的化学稳定性降低,放射性核素释放到环境中。玻璃固化体在储存过程的析晶导致玻璃固化体的化学稳定性降低。
13.目前,针对焦耳炉实际固化过程中玻璃固化体析晶的研究较少,因此,对固化体抗析晶性能提出严苛要求。
14.文献“模拟高放玻璃固化体的析晶行为”发现模拟高放废液玻璃固化体在600~900℃范围内析出辉石、方铈矿、斜长石等晶相。
15.文献“模拟高放废液玻璃固化体析晶率的测定”测定得到我国现行的高硫高钠玻璃固化体在730℃热处理28d后透辉石(camgsi2o6)析晶率约为20~25%。
16.中国专利cn 109273130 b公布了一种高硫高钠高放废液玻璃陶瓷固化体的制备方法,玻璃陶瓷固化尚不能适用于当前焦耳炉工程化应用的要求。
17.现行核行业标准ej-1186规定的固化体性能抗析晶性能要求为:固化体自然冷却后析晶率小于5vol%。在实际焦耳炉运行过程中,对固化体析晶性能的要求更为苛刻,国外相关报道规定固化体在一定温度下保温28d,固化体析晶率小于5vol%。
18.因此,针对我国遗留高放废液高硫高钠的特点,如何突破元素含量变化带来的玻璃固化体析晶、黄相及工艺实用性等技术瓶颈,成为一个亟待解决的技术问题。
技术实现要素:
19.本发明针对我国遗留高放废液高硫高钠的特点,突破元素含量变化带来的玻璃固化体析晶、黄相、工艺实用性等技术瓶颈,提出了一种满足高硫酸盐包容的基础固化玻璃,制备得到固化体能够满足焦耳炉运行工艺参数要求(1150℃时粘度40
±
20dpa
·
s范围内)具有优异包容效果(核素浸出率)、以及低析晶率。
20.本发明提供了一种用于固化高硫高钠废液的基础固化玻璃,其包括以质量百分比计的如下组分:
[0021][0022]
本发明还提供了
[0023]
一种高硫高钠废液的固化方法,包括:
[0024]
(1)根据上述基础固化玻璃组分,制备基础固化玻璃粉末;
[0025]
(2)称取所需量的基础固化玻璃粉末记为第一物料;
[0026]
(3)称取所需量的高硫高钠废液或经处理的高硫高钠废液物料记为第二物料;
[0027]
(4)对第一物料和第二物料进行混合,得到第一混合物;
[0028]
(5)将所述第一混合物熔融、成型、退火,得到所述玻璃固化体。
[0029]
其中,所述步骤(3)中,所述经处理的高硫高钠废液物料包括对高硫高钠废料进行干燥、和/或煅烧后得到的物料。
[0030]
其中,所述步骤(3)中,所述经处理的高硫高钠废液物料为模拟高硫高钠废液氧化物,其由以质量百分比计的以下组分组成:
[0031][0032]
其中,所述步骤(2)中,所述基础固化玻璃粉末的用量为80-85wt%(优选84wt%)。
[0033]
其中,所述步骤(3)中,所述高硫高钠废液或经处理的高硫高钠废液物料的用量为15-20wt%(优选16wt%)。
[0034]
其中,所述步骤(1)中,制备基础固化玻璃粉末的步骤包括:称量原料、混合、熔融、澄清、成型、退火,得到所述基础固化玻璃,然后将所述基础固化玻璃制成粉末。
[0035]
其中,所述步骤(1)中,制备基础固化玻璃粉末的步骤包括:
[0036]
(3.1)根据所述基础固化玻璃的组分含量,称量原料,进行研磨、混合、过筛2-4次(优选3次),使原料充分混合均匀;
[0037]
(3.2)将混合均匀的原料置于坩埚内,随后将坩埚放入升降炉中,于1250-1350℃(优选1300℃)进行高温熔化、澄清2~4h,期间对玻璃熔体进行搅拌;其中,所述坩埚为铂金坩埚或刚玉坩埚;所述搅拌为用石英玻璃棒进行搅拌;
[0038]
(3.3)取出升降炉中的坩埚,迅速将玻璃熔体浇筑进预热模具内,待玻璃熔体凝固成型后,置于马弗炉中退火,于500℃-450℃保温4-5h,之后随炉冷却至室温,再将得到的基础固化玻璃制成粉末,得到所述基础固化玻璃粉末;其中,预热模具的预热温度为400-500℃(优选450℃)。
[0039]
其中,所述步骤(4)中,对第一物料和第二物料进行球磨、混合均匀。
[0040]
其中,所述步骤(5)中,将第一混合物置于坩埚中,然后放入熔炉中,于1130-1150℃(优选1150℃)进行熔融1-3h(优选2h)。其中,所述坩埚为铂金坩埚或刚玉坩埚,所述熔炉为升降熔炉或焦耳炉。
[0041]
其中,所述步骤(5)中,在熔融期间,对玻璃熔体进行搅拌,优选机械搅拌,每15-25min(优选每20min)搅拌一次,以保持玻璃熔体的均匀性,同时有利于硫在玻璃中的溶解。
[0042]
其中,所述步骤(5)中,所述成型、退火步骤包括:将玻璃熔体浇筑进已预热的模具内,待玻璃熔体凝固成型后,将其置于马弗炉内退火,退火温度为500-450℃,退火保温时间为4-5h,冷却后,得到所述玻璃固化体。其中,模具的预热温度为400-500℃(优选450℃)。
[0043]
本发明的有益效果为:
[0044]
(1)本发明采用碱硼硅酸盐固化基材,通过调整玻璃基材的组成,调节熔制工艺条件,可有效固化15-20wt%的高硫高钠高放废液,同时固化体在恒温热处理后具有较低的析晶率。
[0045]
(2)本发明的高硫高钠高放废液玻璃固化体氧化物组成中,sio2、b2o3是玻璃的基本成分,al2o3是玻璃和高放废液引入的成分,三者作为主要的玻璃网络形成氧化物。na2o主要来自于高放废液。
[0046]
引入al2o3 zno中间体氧化物:在高放废液玻璃固化体中,当玻璃中游离氧较多时,zno以锌氧四面体存在,进入硅氧四面体中充当网络形成体;当游离氧较少时,zno则以锌氧八面体存在,作为网络变形体,即成为网络外体;铝离子可以通过取代硅以[alo4]四面体形式进入三维硼硅网络,玻璃网络聚合,提高其抗析晶性能。
[0047]
(3)本发明所得到的固化高硫高钠高放废液后的玻璃固化体,均匀性较好,无分相;耐析晶,液相线温度≤900℃;结晶倾向低,750℃保温28天后结晶率小于10vol%;硫酸盐包容量大,可固化15-20wt%的高硫高钠高放废液。
[0048]
(4)本发明采用两步法熔制工艺,通过高温熔融热处理工艺,先制备了基础固化玻璃,再与高硫高钠废液组成混合,适用于实际焦耳炉玻璃微珠与高硫高钠高放废液的混合过程,保证了固化体在焦耳炉运行温度1150℃下完全熔融。玻璃熟料与模拟废液混合,加快了na2so4在高温液相中的分解(~890℃),避免配合料分解气体加速硫的挥发,采用机械搅拌的形式加速so
42-在玻璃熔体中的溶解,最终使更多硫包容进入玻璃体中。即,玻璃固化体中硫酸盐包容率高,对于固化模拟高硫高钠高放废液的玻璃固化体而言,其全成分模拟玻
璃固化体中可包容高达0.7wt%so3而无黄相。
[0049]
(5)本发明的工艺实用性强:本发明研制的玻璃固化体配方,能够满足焦耳炉运行工艺参数(高温粘度、电阻率)要求和现行核行业标准ej-1186规定的固化体抗析晶性能要求。
具体实施方式
[0050]
下面结合具体实施例对本发明作进一步详细的描述。但应理解这些实施例仅用于说明而不用于限制本发明的范围。此外应理解,在阅读了本发明讲授的内容之后,本领域技术人员可以对本发明作各种改动或修改,这些等价形式同样落于本技术权利要求书所限定的范围。
[0051]
根据表1所示的基础固化玻璃组成,采用如下方法,固化模拟前述模拟高硫高钠废液氧化物,制备对比例1-2和实施例1-4的玻璃固化体。
[0052]
其中,所述模拟高硫高钠废液氧化物由以质量百分比计的以下组分组成:
[0053][0054][0055]
所述方法包括步骤:
[0056]
(1)根据表1所示基础固化玻璃组分,制备基础固化玻璃粉末:
[0057]
(1.1)根据表1所示基础固化玻璃组分,称量原料,进行研磨、混合、过筛3次,使原料充分混合均匀;
[0058]
(1.2)将混合均匀的原料置于铂金坩埚内,随后将铂金坩埚放入升降炉中,于1300℃进行高温熔化、澄清4h,期间用石英玻璃棒对玻璃熔体进行搅拌;
[0059]
(1.3)取出升降炉中的坩埚,迅速将玻璃熔体浇筑进450℃的预热模具内,待玻璃熔体凝固成型后,置于马弗炉中退火,于500℃保温4h,之后随炉冷却至室温,再将得到的玻璃体制成粉末,得到所述基础固化玻璃粉末;
[0060]
(2)称取84wt%的基础固化玻璃粉末记为第一物料;
[0061]
(3)称取16wt%的模拟高硫高钠废液氧化物记为第二物料;
[0062]
(4)对第一物料和第二物料进行混合、球磨,得到第一混合物;
[0063]
(5)将所述第一混合物置于铂金坩埚中,于1150℃熔融2h,期间,采用机械搅拌的方法搅动玻璃熔体,每20min搅拌一次,以保持玻璃熔体的均匀性,同时该措施有利于硫在
玻璃中的溶解;
[0064]
(6)待玻璃熔体凝固成型后,置于马弗炉中退火,475℃保温4h,冷却后,制备得到固化了模拟高硫高钠废液氧化物的玻璃固化体。
[0065]
表1对比例1-2和实施例1-4的基础固化玻璃组成
[0066][0067]
表2公开了对比例1-2和实施例1-4的性能测试结果。
[0068]
表2对比例1-2和实施例1-4的性能测试结果
[0069][0070]
由表1-表2可知:
[0071]
对比例1-2,玻璃网络形成体含量低,碱土金属氧化物氧化钙含量高,高温下易分相,促进析晶。
[0072]
实施例1-4,调整b2o3、al2o3、zno,降cao,以减弱ca
2
的高温分相。增加al2o3 zno中间体氧化物,当玻璃中游离氧较多时,zno以锌氧四面体存在,进入硅氧四面体中充当网络形成体,也就是网络形成体;当游离氧较少时,zno则以锌氧八面体存在,作为网络变形体,即成为网络外体;铝离子可以通过取代硅以[alo4]四面体形式进入三维硼硅网络,玻璃网络增强,提高其抗析晶性能。由此,实施例1-4获得了较低的析晶率、la元素浸出率及合适的高温粘度,同时可固化16%的模拟高硫高钠废液氧化物。
[0073]
显然,上述实施例仅仅是为清楚地说明所作的举例,而并非对实施方式的限定。对于所属领域的普通技术人员来说,在上述说明的基础上还可以做出其它不同形式的变化或变动。这里无需也无法对所有的实施方式予以穷举。而由此所引伸出的显而易见的变化或变动仍处于本发明创造的保护范围之中。
再多了解一些
本文用于创业者技术爱好者查询,仅供学习研究,如用于商业用途,请联系技术所有人。