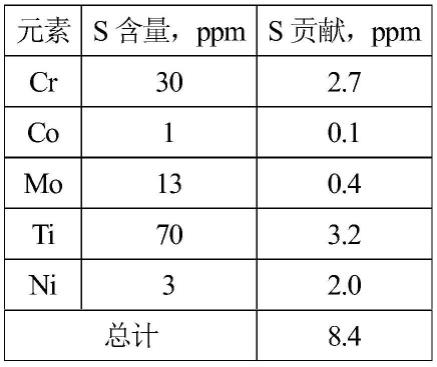
:
1.本发明涉及金属熔炼、铸造领域,具体涉及一种用于高温合金深度脱硫的冶炼方 法。
背景技术:
2.高温合金被广泛应用于制造航空航天发动机和燃气轮机的关键结构件,其优异的 高温力学性能主要得益于其具有较强的高温氧化抗性、较高的固溶强化水平,以及高 体积分数的γ
′‑
ni3al第二相强化。其中,合金的高温氧化抗性是考量合金承温能力的 重要指标之一。研究表明,高温合金的高温抗氧化性与合金中的s含量密切相关,研 究表明,合金中的s易在合金表面偏聚,并降低nicral合金氧化层的粘附性,进而 加剧表面晶界的氧化速率,降低合金的高温蠕变抗力,即使s含量降低至0.001wt%以 下,s元素仍具有强烈的表面偏聚倾向,使合金表面的氧化膜极易剥落并促进表面裂 纹萌生。此外,当in718合金中的s含量由0.005%增加至0.0175wt%时,合金在 650℃/620mpa下的持久寿命由250h降低至80h,且合金在650℃下的抗拉强度及延 伸率均有不同程度的下降。目前常用的脱s手段为加入ca、mg、稀土元素,或使用 电渣重熔工艺,通过高温精炼阶段形成硫化物浮渣进行脱s。但上述方法的脱s的效 果有限,通常仅可将合金中的硫脱除至0.002wt%(20ppm)左右。目前高纯净度高温 合金、高代次单晶中的s含量要求通常可达0.0005wt%(5ppm)以下甚至更低,只能 通过使用更高纯净度的原材料保证合金纯净度,但会大幅度增加合金的原材料成本。 因此,提出一种低成本、高效深度脱硫的高温合金纯净化冶炼方法,对我国高品质高 温合金的制备和应用具有十分重要且深远的意义。
3.cao坩埚具有烧结温度低、高温稳定性强的特点,并且由于其为碱性材质,在合 金熔炼期间与p、s等酸性杂质元素的反应速率较快,可将合金中的s含量降低至 0.0005wt%(5ppm)以下,是高纯高温合金深度脱s较为理想的坩埚材质。但cao坩 埚的抗热震性较差,在工程化应用时难以连续多次使用,并且形成的脱s产物(cas、 cas
·
al2o3)通常附着在坩埚壁,会逐渐降低cao坩埚的脱硫效果,导致cao坩埚的 使用具有一定的局限性。申请人前期研究发现,向k417g合金熔体中加入少量cao 粉末,并进行一段时间的高温精炼可将熔体中的s含量进一步降低至5ppm以下,达 到深度脱s的效果,并且精炼期间cao在熔体表面快速烧结,可被浇注过滤系统过滤, 不增加合金中的ca、o含量。
4.但由于cao属碱性材质,目前高温合金真空冶炼时多使用al质坩埚,为酸性材 质,当冶炼体积较大或精炼时间较长时,易发生cao侵蚀坩埚壁现象,且由于反应产 物为低熔点mcao
·
nal2o3液相渣,可随熔体扰动进入合金熔体,不仅容易污染合金, 更容易减薄坩埚壁厚,造成漏钢风险,成为了cao脱硫无法实现工程化应用的主要因 素之一。
5.因此,设计一种操作做简单、经济实用,用于高温合金母合金纯净化冶炼的cao 深度脱s方法,不仅有助于提高高温合金母合金的纯净度,还有助于提高高温合金的 高温性能,降低高温合金制备期间的原材料成本,有利于推动高纯度高温合金的产业 化,对合金冶炼技术发展具有重要的社会意义和经济意义。
技术实现要素:
6.为了解决现有技术的缺点和不足,本发明的目的在于提供一种用于高温合金深度 脱硫的冶炼方法,该冶炼方法制定的脱硫工艺,能够深度降低母合金中的s含量,且 使用的脱硫剂及脱硫产物为大尺寸颗粒,容易通过挡渣过滤系统去除,不引入新杂质。
7.本发明采用的技术解决方案是:
8.一种用于高温合金深度脱硫的冶炼方法,包括如下步骤:
9.(1)根据实际情况选择cao使用方式,并准备好cao吊装装置或预压制cao块, 作为脱硫剂;
10.(2)将原料放入真空感应炉内进行熔炼母合金,并进行高温精炼;
11.(3)高温精炼结束后停电至熔体边缘出现凝固现象后,恢复供电并提高熔体温度 至1550℃,将cao吊装装置浸入熔体,或加入预压制cao块,进行深度脱s处理;
12.(4)深度脱s处理工艺结束后,进行低温精炼处理;
13.(5)低温精炼结束后进行提温浇注,获得超低s含量高温合金。
14.所述的用于高温合金深度脱硫的冶炼方法,步骤(1)中,当冶炼质量不高于50kg, 或使用al质/高al质坩埚材质时,通过预制的cao陶瓷棒与吊装工装配合形成cao 吊装装置,通过上加料系统使cao陶瓷棒浸入熔体。
15.所述的用于高温合金深度脱硫的冶炼方法,为了提高cao陶瓷棒的强度,在cao 陶瓷棒中镶入2~3根φ0.18mm的mo丝或w丝形成复合材料。
16.所述的用于高温合金深度脱硫的冶炼方法,cao陶瓷棒的尺寸为10mm
×
5mm
×ꢀ
100mm,浸入熔体的陶瓷棒面积总和大于1.5倍坩埚横截面积。
17.所述的用于高温合金深度脱硫的冶炼方法,步骤(1)中,当冶炼质量高于50kg 时,采用mg质或高mg质坩埚,使用颗粒度为1mm~10mm的cao颗粒作为脱硫剂, 加入量为熔炼合金质量的0.05%~0.20%,使用时用al箔将cao颗粒进行包裹,并通 过预压制成cao块,通过上加料系统或侧加料系统加入熔体。
18.所述的用于高温合金深度脱硫的冶炼方法,步骤(2)中,熔炼期间炉内气压控制 在10pa以下,并在1500℃~1550℃下进行高温精炼,精炼时间与冶炼合金重量的关 系如下:冶炼合金重量≤10kg精炼时间7min,冶炼合金重量10~25kg精炼时间 10min,冶炼合金重量25~50kg精炼时间15min,冶炼合金重量50~100kg精炼时间 25min,冶炼合金重量100~200kg精炼时间30min,冶炼合金重量》200kg精炼时间 45min。
19.所述的用于高温合金深度脱硫的冶炼方法,步骤(3)中,将cao陶瓷棒通过cao 吊装装置浸入合金熔体,浸入深度为500~700mm,进行二次高温精炼7~15min,二 次精炼结束后将cao吊装装置取出;或者,将al箔包裹的cao颗粒预压制cao块, 通过顶加料或侧加料加入合金熔体,进行15min以上二次高温精炼处理,待cao颗粒 边缘无明显气泡产生时结束二次高温精炼。
20.所述的用于高温合金深度脱硫的冶炼方法,步骤(4)中,深度脱s处理工艺结束 后,降温至合金高于熔点10~30℃进行低温精炼,进一步促进加入cao后合金中形 成的脱s产物长大、上浮,低温精炼时间与冶炼合金重量的关系如下:冶炼合金重量 ≤10kg精炼时间5min,冶炼合金重量10~25kg精炼时间7min,冶炼合金重量25~ 50kg精炼时间10min,冶炼合金重量50~100kg精炼时间20min,冶炼合金重量100~ 200kg精炼时间25min,冶炼合
金重量》200kg精炼时间30min。
21.所述的用于高温合金深度脱硫的冶炼方法,步骤(5)中,低温精炼结束后,提温 至高于合金熔点80~100℃浇注。
22.所述的用于高温合金深度脱硫的冶炼方法,浇注系统设置具有挡渣过滤功能的过 滤网或挡渣墙结构,以过滤熔体表面的cao颗粒。
23.本发明的设计思想是:
24.基于cao脱硫机理,明确脱s速率的主要影响因素包括cao与熔体的接触面积 及其加入量;在保证s脱除效率而不增加残渣风险的前提下,将cao颗粒预制成形, 借助工装卡具将成形cao浸入熔体内部或投放于熔体上方,确保cao与合金熔体的 接触面积或覆盖面积,即提高了脱s效率,又避免了cao过小颗粒污染合金熔体;由 于反应熔渣密度小于合金熔体密度,熔渣浮于熔体表面,在浇注期间可通过挡滤渣装 置将其去除,获得洁净钢液。
25.本发明具有的优点和积极效果是:
26.1、与直接真空感应熔炼相比,能够大幅度提高合金熔炼期间的脱硫速率,有利于 提高合金的纯净度;与使用cao坩埚相比,能够避免cao坩埚热震性差、使用次数 少的缺点,提高生产效率,并且通过cao陶瓷棒浸入熔体,或直接加入预压制cao 块的方式,能够避免使用金属ca、金属mg或其他稀土元素作为脱硫剂时这类元素在 合金中残留量较高,或脱s产物尺寸极小无法过滤的缺点,有利于提高母合金纯净度 控制水平。
27.2、本发明适用于绝大多数高温合金母合金纯净化熔炼,并可根据需求或实际情况 自由选择cao使用形式,灵活多变,实用性强。
附图说明:
28.图1为cao吊装工装尺寸示意图。
29.图2为采用cao吊装装置进行深度脱s处理示意图。
30.图3为采用添加cao块进行深度脱s处理示意图。
具体实施方式:
31.在具体实施过程中,本发明用于高温合金深度脱硫的冶炼方法,包括以下步骤:
32.(1)根据实际情况选择cao使用方式,并准备好cao吊装装置或预压制cao块, 作为脱硫剂;
33.当冶炼质量不高于50kg,或使用al质/高al质坩埚材质时,可通过预制的cao 陶瓷棒(尺寸为10mm
×
5mm
×
100mm,尺寸设计依据为浸入熔体的陶瓷棒面积总和 应大于1.5倍坩埚横截面积)与吊装工装配合形成cao吊装装置,通过上加料系统使 cao陶瓷棒浸入熔体;为了提高cao陶瓷棒的强度,可在cao陶瓷棒中镶入2~3根 φ0.18mm的mo丝或w丝形成复合材料。
34.如图1所示,cao吊装工装为圆盘形本体中心开设吊孔a,在吊孔a外侧沿圆周 方向均匀开设安装孔b,其具体形状、尺寸以及嵌入cao陶瓷棒数量可根据现场实际 工况进行调整。吊孔a处可根据冶炼设备结构进行加装吊钩,cao陶瓷棒可插入安装 孔b处并通过螺纹连接固定,组成cao吊装装置。
35.当冶炼质量高于50kg时,可采用mg质或高mg质坩埚,使用颗粒度为1mm~ 10mm的
cao颗粒作为脱硫剂,加入量约为熔炼合金质量的0.05%~0.20%,使用时 可用al箔将cao颗粒进行包裹,并通过预压制成cao块,通过上加料系统或侧加料 系统加入熔体。
36.(2)将原料放入真空感应炉内进行熔炼母合金,熔炼期间炉内气压需控制在10pa 以下,并在1500℃~1550℃下进行高温精炼,精炼时间与冶炼合金重量的关系如表1 所示。
37.表1高温精炼时间与冶炼重量的关系
38.冶炼重量,kg高温精炼时间,min≤10710~251025~501550~10025100~20030》20045
39.(3)高温精炼结束后停电至熔体边缘出现凝固现象,恢复供电并提高熔体温度至 1550℃,进行深度脱s处理;将cao陶瓷棒通过cao吊装装置浸入合金熔体,浸入 深度约为500~700mm,进行二次高温精炼7~15min,二次精炼结束后将cao吊装 装置取出;或者,将al箔包裹的cao颗粒预压制cao块,通过顶加料或侧加料加入 合金熔体,进行15min以上二次高温精炼处理,待cao颗粒边缘无明显气泡产生时可 结束二次高温精炼。
40.(4)深度脱s处理工艺结束后,降温至合金高于熔点10~30℃进行低温精炼, 进一步促进加入cao后合金中形成的脱s产物长大、上浮。低温精炼时间与冶炼合金 重量的关系如表2所示。
41.表2低温精炼时间与冶炼重量的关系
42.冶炼重量,kg低温精炼时间,min≤10510~25725~501050~10020100~20025》20030
43.(5)低温精炼结束后,提温至高于合金熔点80~100℃浇注,即可获得超低s含 量高温合金。需要注意的是,浇注系统需设置过滤网或挡渣墙等具有挡渣过滤功能的 结构。
44.下面,通过实施例对本发明进一步详细阐述。
45.实施例1
46.本实施例中,熔炼10公斤k417g母合金,母合金s贡献主要元素及其贡献值如 表3所示,未列出元素为s贡献值小于0.05ppm,可忽略不计。
47.表3 k417g合金主要供s元素及s贡献值
[0048][0049]
首先将c、cr、co、mo、ni等原材料放入坩埚进行真空熔炼,化清后进行1500℃
ꢀ×
7min高温精炼,精炼结束后加入al、ti、ni-b、zr、v-al等元素,搅拌均匀后降温 至熔体表面出现凝固现象,随后送电加热至熔体达到1550℃,此时将安装配合好的 cao吊装装置由顶加料室送入炉内,并将cao陶瓷棒浸入熔体约600mm,如图2所 示,保持1550℃精炼10min后取出。
[0050]
随后降温至约1370℃进行5min低温精炼,结束后提温至1420℃浇注,冶炼过程 结束。
[0051]
对合金锭上、下部位进行取样,采用o/n仪分析o、n,采用gdms分析s、ca 含量,并与不使用cao脱硫剂制备的合金进行对比,分析检测结果如表4所示。
[0052]
表4采用不同方法制备的k417g合金锭o、n、s含量
[0053][0054]
可以看出,采用本发明制备的k417g合金锭s含量明显降低,且残留ca含量极 少。
[0055]
实施例2
[0056]
本实施例中,熔炼40公斤k444母合金熔炼,熔炼坩埚为mg质成型坩埚。母合 金s贡献主要元素及其贡献值如表5所示,未列出元素为s贡献值小于0.05ppm。
[0057]
表5 k444合金主要供s元素及s贡献值
[0058][0059]
首先将c、cr、co、mo、w、ni等原材料放入坩埚进行真空熔炼,化清后进行 1500℃
×
15min高温精炼,精炼结束后加入al、ti、ni-b、zr等元素,搅拌均匀后降 温至熔体表面出现凝固现象,随后送电加热至熔体达到1500℃,此时加入预压制cao 块,如图3所示,保持1500℃精炼15min,其中,加入预压制cao块约2min后,熔 体表面cao基本已烧结。
[0060]
随后降温至约1350℃进行10min低温精炼,结束后提温至1410℃浇注,冶炼过程 结束。需要注意的是,浇注系统中必须具备10ppi或孔隙率更小的过滤网,或相同功 能结构部件,以过滤熔体表面的cao颗粒。
[0061]
对合金锭上、下部位进行取样,采用o/n仪分析o、n,采用gdms分析s、ca 含量,并与不使用cao脱硫剂制备的合金进行对比,分析检测结果如表6所示。
[0062]
表6采用不同方法制备的k444合金锭o、n、s含量
[0063][0064]
由表6可以看出,采用本发明制备的k444合金锭s含量明显降低,且残留ca含 量小于10ppm。
[0065]
实施例结果表明,本发明适用于深度脱除大多数铸造高温合金母合金中的s元素, 操作简单,实施难度低,效果显著。
再多了解一些
本文用于创业者技术爱好者查询,仅供学习研究,如用于商业用途,请联系技术所有人。