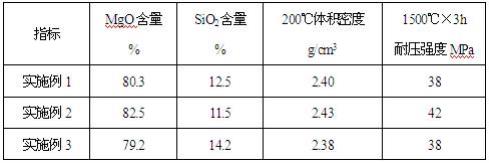
1.本发明涉及耐火材料应用领域,具体涉及一种满足品质钢冶炼用高性能中间包衬料及制备方法。
背景技术:
2.为满足高性能要求的品种钢的质量要求,对钢液中的微元素含量提出了更为苛刻的控制,对氢元素的控制成为重要的指标之一。过量的氢可在应力作用下形成白点,引起氢脆,恶化钢的物理特性如钢轨的机械性能、抗疲劳性能等,从而引发质量问题和安全隐患。
3.作为钢水凝固前的最后一个耐火材料容器,中间包工作衬料对最终钢的品质响很大。传统干式料多以镁砂为原料,以酚醛树脂为结合剂,含硼物质等为助烧剂,将镁砂骨料、镁砂粉料、结合剂、添加剂等一起直接干混即获得成品;通过酚醛树脂的低温结合、材料高温自烧结以及添加剂的助烧作用可使干式料获得一定的高温性能,因其制作工艺简单、施工方便,具有合适的高温性能,成为当前中间包衬料的主流体系;但树脂结合镁质干式料存在一些缺点:一是树脂在烘烤过程中会释放甲醛、酚等刺激性气体产生,污染环境;二是使用过程中树脂会放出co2、co、ch4、h2、h2o以及其它含碳氢气体等,对钢水产生增碳/增氢效应,严重降低钢材的品质。随着国家环保政策和行业绿色冶炼的发展需求,新型干式料的研制开发成为热点研究,如以葡萄糖、木糖、半乳糖、果糖、食用糖、柠檬酸等有机高分子物质做临时结合剂替代传统树脂粉,虽有利于环境的改善,但大多存在抗侵蚀性差,使用寿命低,没有得到推广性应用;结合剂中含有的氢组分也会造成钢液增氢,不利于品质钢的冶炼;另干式料中的氧化镁原料尤其氧化镁细粉在存放或使用过程中会长时间直接暴露在空气中,吸收空气中的水分,更是加剧了钢液增氢的危害。
技术实现要素:
4.为解决上述技术问题,本发明的目的是提出一种品质钢用高性能中间包衬料及制备方法。
5.本发明为完成上述目的采用如下技术方案:一种品质钢冶炼用中间包衬料,其特征在于:所述品质钢冶炼用中间包衬料由镁砂、造粒镁砂、镁橄榄石和石墨组成;粒度和质量百分比为:粒度为0.5-5mm的镁砂45-60%;粒度大于0mm小于0.5mm的镁砂5-15%;粒度大于0mm小于0.5mm的造粒镁砂0.5-0mm10-30%;镁橄榄石粉10-20%,石墨,0-5%;上述原料总重为100%。
6.所述镁砂为高纯烧结镁砂或电熔镁砂的任何一种,其中mgo≥95%。
7.所述镁橄榄石粉为高品位原料,其中粒度d0.9≤74um,mgo≥45%;sio2≥30%;灼碱≤3%。
8.所述的石墨为天然石墨或人造石墨的任意一种,其粒度d0.9≤0.15mm,固定碳≥90%。
9.一种品质钢冶炼用中间包衬料的制备工艺,其特征在于:包括以下步骤:
步骤1):先制备造粒镁砂;1.1)将镁砂粉、硅微粉、活性碱式磷酸盐、聚甲基纤维素按照质量配比10-15:1:1-3:0-0.05进行球磨预混2-6h,得到混合粉料;1.2)将混合粉料和硅溶胶按照100:5-10的质量比在高速混练机内混合进行裹覆造粒,硅溶胶在混炼时一次性加入;1.3)造粒结束后进行自然晾干;1.4)之后进行烘烤(80~150℃,不少于6h),烘烤后自然冷却;1.5)过筛,获得粒径小于0.5mm的造粒镁砂;步骤2):将镁砂、造粒镁砂、镁橄榄石和石墨按比例称量待用;步骤3):将粒度小于0.5mm的所有料先在搅拌机内进行5-10min的预混;步骤4):将其余颗粒料加入搅拌机内继续干混5-10min,得到中间包衬料成品。
10.所述镁砂粉为粒度d
0.9
≤74um的任意一种高纯烧结镁砂、电熔镁砂或其混合粉,其中mgo≥95%。
11.所述硅微粉为高活性二氧化硅微粉,其中sio2≥95%,粒度d
0.9
≤5um。
12.所述活性碱式磷酸盐为一种复合磷酸盐,其中k2o≥13%;na2o≥13%;p2o5≥58%,体积密度≤1000g/l,软化点200~250℃。
13.所述硅溶胶为弱碱性物质,其中sio2≥20%,ph≥8。
14.本发明提出了一种适合品质钢冶炼用中间包衬料及制备方法;以高耐火度的碱性耐火原料高纯镁砂和高纯镁橄榄石为主原料,保障材料具有较高的使用温度和抗渣侵蚀性能,同时采用高纯原料尽量减少耐火原料中的杂质成分降低衬料的使用性能。
15.以造粒方式在干式料中间接引入镁砂细粉,采用活性碱式磷酸盐取代传统酚醛树脂,低温下赋予衬料较高的结合强度,保障中间包衬料低温脱模后的结构稳定性;且不产生污染性气体。采用弱碱性硅溶胶为造粒料的临时粘结剂,一方面可保障干式料中不引入其它杂质,也能作为辅助结合剂在现场烘烤脱模过程中进一步形成胶凝相,增加组分间的结合性;另一方面可在高温下与氧化镁反应形成镁橄榄石,与其它物相相互交织,赋予材料更高的热态强度,提高中间包衬料的抗侵蚀性能和使用寿命;利用硅微粉的高活性和高比表面积充分包裹镁砂细粉与溶胶中的硅组分共同形成m-s-h凝胶产物,不仅有利于造粒团的结构稳定,也有利于减少干式料存放和使用过程中从环境中吸收水分,降低衬料对钢液的增氢影响;利用羧甲基纤维素的增黏性可进一步保持造粒团的结合性和结构稳定性。
16.加入石墨是利用石墨与熔渣的非润湿性进一步提高材料的高温抗渣侵蚀性能,从而提高衬料的使用寿命。
17.综上所述,本发明具有如下优点:(1)本发明采用高纯耐火原料,保障衬料具有较高的耐火度和使用温度。
18.(2)本发明采用活性碱式磷酸盐取代传统酚醛树脂作为低温结合剂制备了一种环保型干式衬料,不仅可提供烘烤结合强度;且符合环保要求,制备、存放和使用过程中均不会产生污染性气体,有利于周围环境的保护和作业人员的健康安全。更重要的是能够消除传统酚醛树脂释放的含氢有机气体小分子对钢液产生的增碳和增氢,保障钢液的高品质。
19.(3)本发明中以造粒镁砂方式在干式料中间接引入镁砂,避免了镁砂细粉与空气中的水分直接接触发生反应,降低镁砂水化反应对钢液的增氢,特别是多雨季节高湿度环
境下因干式料吸潮对钢液造成的增氢危害。
具体实施方式
20.给出本发明的实施例,但不构成对本发明的任何限制。首先制备造粒镁砂,之后将造粒镁砂、镁砂、镁橄榄石、石墨等干混15分钟后在三联模中捣打成型,并在200℃/24h烘烤脱模,之后进行1500℃热处理,其理化指标见表1,并附当前干式料与传统酚醛树脂干式料首炉增氢对比数据(见表2)。
21.实施例1:造粒镁砂方案示例1:烧结镁砂粉、硅微粉、活性碱式磷酸盐按照10:1:2的质量比先通过球磨罐预混2h后,之后加入总混合料总重的6%硅溶胶(sio2=30wt%, ph=9.8)在高速混炼机进行造粒,混炼机的速度按照慢快慢快交替进行,每个速度共混5min,待自然晾干后在110℃烘烤12h,之后进行过筛,选取粒径小于0.5mm的造粒镁砂。
22.干式衬料配比示例1:烧结镁砂颗粒3mm<粒径≤5mm
ꢀꢀꢀꢀꢀꢀ
15%;烧结镁砂颗粒1mm<粒径≤3mm
ꢀꢀꢀꢀꢀꢀ
30%;烧结镁砂颗粒0.5mm<粒径≤1mm
ꢀꢀꢀꢀ
10%;烧结镁砂颗粒0.1um<粒径≤0.5mm
ꢀꢀ
10%;造粒镁砂粒径≤0.5mm
ꢀꢀꢀꢀꢀꢀꢀꢀꢀꢀꢀꢀꢀ
15%;镁橄榄石粉粒径≤74um
ꢀꢀꢀꢀꢀꢀꢀꢀꢀꢀꢀꢀ
17%;鳞片石墨
ꢀꢀꢀꢀꢀꢀꢀꢀꢀꢀꢀꢀꢀꢀꢀꢀꢀꢀꢀꢀꢀꢀꢀꢀ
3%上述原料的总重量为100%;实施例2:造粒镁砂方案示例2:烧结镁砂粉、硅微粉、活性碱式磷酸盐、聚甲基纤维素按照15:1:3:0.05的质量比先通过球磨罐预混4h后,之后加入总混合料总重的10%硅溶胶(sio2=30wt%, ph=9.8)在高速混炼机进行造粒,混炼机的速度按照慢快慢快交替进行,每个速度共混5min,待自然晾干后在150℃烘烤6h,之后进行过筛,选取粒径小于0.5mm的造粒镁砂。
23.干式衬料配比示例2:烧结镁砂颗粒3mm<粒径≤5mm
ꢀꢀꢀꢀꢀꢀ
10%;烧结镁砂颗粒1mm<粒径≤3mm
ꢀꢀꢀꢀꢀꢀ
28%;电熔镁砂颗粒0.5mm<粒径≤1mm
ꢀꢀꢀꢀ
7%;电熔镁砂颗粒0.1um<粒径≤0.5mm
ꢀꢀ
15%;造粒镁砂粒径≤0.5mm
ꢀꢀꢀꢀꢀꢀꢀꢀꢀꢀꢀꢀꢀ
30%;镁橄榄石粉粒径≤74um
ꢀꢀꢀꢀꢀꢀꢀꢀꢀꢀꢀꢀ
10%;上述原料的总重量为100%;实施例3:造粒镁砂方案示例3:烧结镁砂粉、硅微粉、活性碱式磷酸盐、聚甲基纤维素按照12:1:3:0.03的质量比
先通过球磨罐预混4h后,之后加入总混合料总重的8%硅溶胶(sio2=30wt%, ph=9.8)高速混炼机进行造粒,混炼机的速度按照慢快慢快交替进行,每个速度共混5min,待自然晾干后在80℃烘烤24h,之后进行过筛,选取粒径小于0.5mm的造粒镁砂。
24.干式衬料配比示例3:电熔镁砂颗粒3mm<粒径≤5mm
ꢀꢀꢀꢀꢀ
8%;电熔镁砂颗粒1mm<粒径≤3mm
ꢀꢀꢀꢀꢀ
27%;烧结镁砂颗粒0.5mm<粒径≤1mm
ꢀꢀꢀ
10%;烧结镁砂颗粒0.1um<粒径≤0.5mm 5%;造粒镁砂粒径≤0.5mm
ꢀꢀꢀꢀꢀꢀꢀꢀꢀꢀꢀꢀ
25%;镁橄榄石粉粒径≤74um
ꢀꢀꢀꢀꢀꢀꢀꢀꢀꢀꢀ
20%;鳞片石墨
ꢀꢀꢀꢀꢀꢀꢀꢀꢀꢀꢀꢀꢀꢀꢀꢀꢀꢀꢀꢀꢀꢀꢀ
5%;上述原料的总重量为100%;表1 实施例干式料的性能指标表2研制干式料对传统酚醛树脂干式料对40t中间包首炉增氢数据对比备注:增氢值为中间包首炉钢液氢含量与上一工序lf钢液中氢含量的差值。
再多了解一些
本文用于创业者技术爱好者查询,仅供学习研究,如用于商业用途,请联系技术所有人。