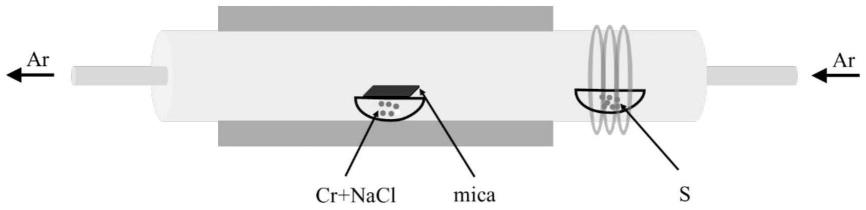
1.本发明属于纳米材料领域,具体涉及一种超小气流调控生长厘米级二维硫化铬薄膜的方法。
背景技术:
2.随着微电子及信息技术行业的快速发展,对电子器件的小型化、低维化、集成化提出了更高要求,实现微纳器件与硅基材料电路的集成化与兼容化成为当前发展的突破点。而传统的硅基半导体受到尺寸限制的影响,其器件性能很难获得提升。以类石墨烯材料为代表的二维材料,其具有合适的带隙、较高迁移率等特点,可抑制短沟道效应等,使其能够应用于高集成度的逻辑电路中,从而掀起了二维纳米半导体器件的研究热潮。二维材料凭借其自身独特的电子结构以及优异的物理性能,或将成为部分取代硅基材料或与其集成互补的材料体系,在微电子与光电子器件等领域有着很大的应用前景。
3.在二维半导体材料中,以石墨烯、二硫化钼为代表的范德瓦尔斯材料是目前研究比较广泛的一类。层状材料由于其层间弱的范德华力,很容易通过机械剥离或其它自下而上的生长方法来获得二维尺度下的材料。而对于非层状三维晶体而言,其三维方向上均以化学键相连,容易呈现三维方向上的生长,很难实现二维平面内的生长。然而,通过抑制各向同性生长的方法,非层状材料的二维平面内生长可以被实现,其最常用的方法就是范德华外延化学气相沉积法。范德华外延方法中,衬底与材料之间是依靠范德华力相连而非化学键力,因此二者之间的晶格失配容忍度较高。而采用化学气相沉积法合成二维非层状材料,需要着重考虑材料与衬底之间的晶格失配度大小及材料与衬底之间的相互作用力,进而抑制厚度方向上的过渡生长。因此,选用合适的外延衬底对实现非层状材料的平面内生长具有重要意义。常用衬底为石墨烯、氟金云母、六方氮化硼等。
4.新型二维薄膜材料能够表现出不同于块体材料的优异物理性质,其独特性能可应用于不同电子与光电子领域。例如,石墨烯薄膜、硒化铋薄膜具有高的透射率,有望取代氧化铟锡等传统的透明导电电极材料。具有高迁移率、合适的带隙mos2、bi2seo2及黑磷等薄膜体系是后摩尔时代电子器件的候选材料体系。目前,采用气相沉积法实现二维层状材料大面积薄膜的制备技术已相对成熟,但涉及非层状二维材料大面积连续薄膜的研究较为稀少。虽然,非层状材料的二维纳米结构制备已取得突飞猛进的突破,但大都集中在纳米片或纳米颗粒组成的薄膜,由二维非层状结构的纳米片扩展到具有一定均匀性的大面积的超薄薄膜存在较大的技术难度,目前少有报道。其中,非层状的二维纳米片难于形成薄膜的原因主要在于二维非层状材料生长方向的倾向性与晶畴间的非连续性较难统一,由于非层状材料在三维方向上均存在化学键,倾向于生长成几十至几百纳米厚度的分立纳米片,很难实现平面内畴区之间的拼接,限制了难以实现大面积连续薄膜的制备。因此,通过对二维非层状材料生长方法的调控实现非层状材料在二维平面内的外延、实现各个畴区的拼接并抑制厚度方向的生长,对生长大面积二维薄膜尤为重要。
技术实现要素:
5.本发明的目的在于,针对以上背景技术中存在的问题,提供了一种在柔性衬底上生长厘米级大面积二维非层状硫化铬薄膜的方法。
6.为了实现上述目的,本发明提供的技术方案为:
7.(1)将铬源置于石英管中心恒温区,将硫源置于石英管上游低温区,所述铬源为金属铬粉,所述硫源为硫粉;
8.(2)将氟金云母置于石英管中心恒温区铬源上方;
9.(3)反应之前通大流量惰性气体氩气10-20min排除石英管内空气;之后调节氩气流速至超小气流,同时打开管式炉加热装置以及硫源加热部,所述硫源加热部设置在石英管外侧与硫源区域对应的位置,当管式炉加热至中心恒温区温度780-850℃时,保温10-20min后停止管式炉加热装置和硫源加热部,之后快速冷却至室温,即可在氟金云母衬底上得到厘米级的连续大面积cr2s3薄膜。
10.本发明中的二维cr2s3薄膜是一种非层状材料,其结构是“abc”堆垛的菱方相。本发明中所制备的cr2s3薄膜材料具有不同厚度且晶体质量较高的二维硫化铬连续薄膜,薄膜的横向尺寸在15
×
15mm衬底上可以达到10-13mm。
11.本发明的反应装置中,使用固定尺寸的石英舟承载铬源,衬底放入石英舟内,将石英舟放置在石英管中心恒温区段,硫源放置在石英管上游低温区段。采用化学气相沉积的生长方法,调节石英管中心温度,在调控载气的辅助下进行反应,最终在特定衬底上生长出厚度均匀、可控的厘米级二维硫化铬连续薄膜。
12.上述反应中,铬源与硫源在加热作用下达到挥发温度,硫蒸气依靠载气运输到中心恒温反应区,由于硫源蒸发温度低,在外置加热带的辅助加热下,硫源先到达气化温度随着载气填充在石英管中,并有部分硫附着在衬底上,该操作可进一步排除反应装置中的杂质气体,提高产物纯度,另外提前附着在衬底上的硫源也是硫化铬成核的优先位点。待铬源到达一定挥发温度时,二者发生化学反应,沉积到云母衬底上。
13.材料与衬底之间是依靠范德华作用力相连,在平面内依靠范德华外延生长,晶畴尺寸不断扩大、拼接,最终完全连接,形成连续薄膜。通过控制反应温度、调节载气流量大小、控制反应物质的量并严格控制铬源与衬底之间的距离,达到控制反应速率的目的。在整个生长过程中为了维持二维非层状结构以及较好的大面积成膜,需要调控该化学反应以一个较低的反应速率进行,实现充分反应,特别是在畴区拼接阶段,稳定的供给是对连续薄膜生长至关重要的,进而得到高质量的二维大面积硫化铬薄膜。
14.在上述反应过程中,气流量大小的调控非常重要。经过大量的实验,我们创造性地发现使用超小气流载气可实现二维非层状材料的均匀成膜,而非常见的纳米片形式。我们认为该机理可能是在化学气相沉积生长过程中,载气只起到输运前驱体的作用。在此,氩气输运的前驱体为硫蒸气与铬,气流量的大小影响了反应区前驱体的蒸气浓度大小,进而会对成核速率及成核密度造成影响。当采用大气流生长硫化铬时,会迅速在衬底表面形成分立且密集的纳米颗粒及垂直生长纳米片,倾向于三维方向上生长而无法完成面内的薄膜拼接。这主要是由于载气携带的前驱体充足造成前驱体浓度偏高,沉积和反应速率过快。而随着气流的减小,前驱体的蒸汽浓度会降低,从而降低了其沉积在衬底上的反应速率,使得材料能够实现平面内外延生长,继而形成连续薄膜。更重要的是当气体流量较小时,能够提供
厚度较大的平稳边界层,对成核及薄膜拼接过程中物料的稳定供给有较大的促进作用,也利于硫化铬薄膜的生长。在本发明中,衬底直接设置在铬粉正上方,两者距离为1-10mm,铬源的传输距离短,避免了超小气流带来的前驱体供给不足问题。此外,硫源是采用了外置加热部加热,且在管式炉升温时便对硫源加热,因此保证了石英管内硫源供给充足,设定超小气流不会导致硫源不足。作为优选,氩气气流的范围大小在10-40sccm,进一步优选为15sccm,此时生长的薄膜质量最高,而当载气气流持续降低时,原料供给速度较慢,无法得到组成稳定的硫化铬。
15.在上述生长过程中,前驱体铬粉的量尤为重要,要想成功生长出连续薄膜,需要控制铬粉的质量在20-50mg。若铬粉质量偏高,即前驱体供给速率过快,会导致沉积反应过快,从而使得材料在三维方向上生长速度过快,在衬底上会形成尺寸小且厚度过高的硫化铬纳米片,无法继续实现平面内范德华外延生长。若铬粉质量不足,会导致前驱体供给不足,因而在衬底上会表现为生长分立的纳米片,一般为单层或少层无法完成拼接的晶畴,无法获得大面积连续薄膜。
16.在上述生长过程中,由于金属铬的熔点较高(~1857℃),因此采用了碱金属盐辅助降低其挥发温度。本发明中所使用的助熔剂为氯化钠,在氯化钠辅助下,优选的铬源放置的恒温区温度为780-850℃。作为优选,氯化钠的量要控制在1-3mg。若氯化钠的量过多,会在衬底以及材料上产生二维氯化钠杂质,导致材料表面有氯化钠的过沉积。若氯化钠的量过少,则会使得铬源供给不足,无法获得连续薄膜。这是由于氯化钠的熔点在800℃左右,而材料的生长所需温度较高,会造成部分氯化钠在高温下被载气输运到反应装置外而无法继续起到助熔剂作用。
17.本发明中,优选的,衬底与铬源之间的距离为5mm。通过严格选择云母和石英舟的尺寸来实现对二者之间距离的控制。选用外径为20
×
20mm的半圆石英舟盛放15
×
15mm的氟金云母,铬源与衬底之间的距离为1-10mm,优选为5mm。在这种生长距离下,结合其它合适的条件,可以获得高质量的连续二维硫化铬薄膜。若二者之间的距离太近,会导致铬源的过沉积,在衬底上得到的是分立且厚度过高的纳米片以及纳米棒和其它沉积物;若二者之间的距离过远,在衬底上会得到少量较薄的分立硫化铬纳米片。
18.作为优选,选用的衬底均为尺寸为15
×
15mm新鲜剥离的氟金云母。
19.作为优选,铬源采用微米级金属铬粉,硫源选用升华硫粉。现有研究中,大多生长硫化铬的方法大多用三氯化铬、二氯化铬,以及采用蒸镀金属铬作为前驱体的方法,以上前驱体尤其是氯化物前驱体,饱和蒸汽压较低且极易潮解,前驱体供给强烈且供给不稳定,导致反应过程的可控性差。与其它的铬基前驱体相比,金属铬粉的饱和蒸汽压较小,不会轻易产生由于前驱体供给强烈而出现的垂直生长的现象。虽然金属铬粉的分子平均自由程相对其它铬源来讲较短,但通过调节源与衬底间的距离可有效克服这一短板。
20.作为优选,盛放铬源、硫源的器皿均为半圆石英舟。
21.作为优选,硫源的温度设定为180-200℃,由于所使用的管式炉为单温区,石英管上游低温区处不存在恒温区间,为了保证硫源各部分温度恒定,本发明采用硫源加热部对硫源进行加热,硫源加热部包括加热带、热电偶和控制部,当热电偶识别硫源区域温度达到180-220℃时,控制部控制加热带停止硫源加热部加热;当热电偶识别硫源区域温度低于180℃时,控制部控制加热带继续加热。
22.硫源加热带也可以替换为硫源加热线圈。
23.本发明的有益技术效果如下:
24.1、该方法使用超小气流的氩气作为载气,利用超小流量的载气调控化学气相沉积时的气流边界层,使得反应原料在衬底附近反应的蒸汽浓度降低,从而降低了其沉积在衬底上的反应速率,使得材料能够实现平面内外延生长,形成连续薄膜。
25.2、同时载气流量较小,能够提供厚度较大的平稳边界层,对成核及薄膜拼接过程中物料供给的稳定作用大,采用该简单方法可获得连续性好、尺寸可控、晶体质量高、厚度较为均匀的二维非层状硫化铬薄膜。
附图说明
26.图1为本发明生长二维硫化铬薄膜所用实验装置图。
27.图2为本发明所制备硫化铬的晶体结构图。
28.图3为实施例1所制备cr2s3薄膜的光学显微图。
29.图4为实施例1所制备cr2s3薄膜的宏观形貌图。
30.图5为实施例1所制备cr2s3薄膜的扫描电子显微图。
31.图6为实施例1所制备cr2s3薄膜的拉曼光谱图。
32.图7为实施例1所制备cr2s3薄膜的x射线光电子能谱图。
33.图8为实施例2所制备cr2s3薄膜的光学显微图。
34.图9为实施例3所制备cr2s3薄膜的光学显微图。
35.图10为实施例4所制备cr2s3薄膜的光学显微图。
36.图11为实施例5所制备cr2s3薄膜的光学显微图。
37.图12为实施例6所制备cr2s3薄膜的光学显微图。
38.图13为对比例1所制备cr2s3纳米片的光学显微图。
39.图14为对比例2所制备cr2s3纳米片的光学显微图。
40.图15为对比例3所制备cr2s3纳米片的光学显微图。
具体实施方式
41.下面结合一些具体实施案例对本发明进行更进一步的详细说明。本发明所采用的方法是常压化学气相沉积法。首先在石英管中心恒温区放置铬源与氯化钠,石英管上游低温区放置硫源。作为优选,在材料制备前先排尽石英管内空气,调节生长温度在780-850℃,载气流量在10-40sccm之间,生长时间为10-20min。生长完成后,打开管式炉快速冷却至室温,从而在绝缘柔性衬底上制备出连续二维硫化铬薄膜。
42.实施例1
43.取20-25mg金属铬粉与2-3mg氯化钠均匀混合,放置在外径为20
×
20mm的半圆石英舟中。新鲜剥离15
×
15mm氟金云母,厚度约为0.05mm,将其放置在铬源正上方。将该石英舟放入石英管中心恒温区,设定中心温区温度为850℃。将硫源放入外径20
×
20mm的半圆石英舟,置于石英管上游低温区,石英管外套有硫源加热部的加热带,设定温度为200℃。在程序升温之前,首先用流量为500sccm的氩气清洗石英管10min,排尽石英管内的空气。调节氩气到超小气流,超小气流的流速为15sccm,同时打开管式炉加热装置以及硫源加热部,使得管
式炉加热装置以30℃/min相同速度升温,硫源加热部先达到200℃,此时硫蒸发出来并输运到氟金云母片上,当管式炉加热至中心恒温区温度850℃时,保温15min后停止管式炉加热装置和硫源加热部,之后打开管式炉,使石英管快速冷却至室温后关闭气流,并取出样品,即可在氟金云母衬底上得到厘米级的连续大面积cr2s3薄膜。其光学显微图如图3所示,宏观形貌如图4所示,扫描电子显微图如图5所示,可以看出薄膜均匀连续、质量较高。图6所示为本实例制备薄膜的拉曼光谱图,其在174.1、246.9、281.2、355.1cm-1
处明显的特征峰表征了该材料为菱方相三硫化二铬。
44.实施例2
45.与实例1相比,区别在于载气流量为氩气100sccm。
46.取20-25mg金属铬粉与2-3mg氯化钠均匀混合,放置在外径为20
×
20mm的半圆石英舟中。新鲜剥离15
×
15mm氟金云母,厚度约为0.05mm,将其放置在铬源正上方。将该石英舟放入石英管中心恒温区,设定中心温区温度为850℃。将硫源放入外径20
×
20mm的半圆石英舟,置于石英管上游低温区,石英管外套有硫源加热部的加热带,设定温度为200℃。在程序升温之前,首先用流量为500sccm的氩气清洗石英管10min,排尽石英管内的空气。调节氩气到流速为100sccm,同时打开管式炉加热装置以及硫源加热部,使得管式炉加热装置以30℃/min升温,硫源加热部先达到200℃,此时硫蒸发出来并输运到氟金云母片上,当管式炉加热至中心恒温区温度850℃时,保温15min后停止管式炉加热装置和硫源加热部,之后打开管式炉,使石英管快速冷却至室温后关闭气流,并取出样品。其光学形貌如图8所示,云母表面为密集的纳米颗粒。
47.实施例3
48.与实例1相比,区别在于载气流量为氩气45sccm。
49.取20-25mg金属铬粉与2-3mg氯化钠均匀混合,放置在外径为20
×
20mm的半圆石英舟中。新鲜剥离15
×
15mm氟金云母,厚度约为0.05mm,将其放置在铬源正上方。将该石英舟放入石英管中心恒温区,设定中心温区温度为850℃。将硫源放入外径20
×
20mm的半圆石英舟,置于石英管上游低温区,石英管外套有硫源加热部的加热带,设定温度为200℃。在程序升温之前,首先用流量为500sccm的氩气清洗石英管10min,排尽石英管内的空气。调节氩气到流速为45sccm,同时打开管式炉加热装置以及硫源加热部,使得管式炉加热装置以30℃/min升温,硫源加热部先达到200℃,此时硫蒸发出来并输运到氟金云母片上,当管式炉加热至中心恒温区温度850℃时,保温15min后停止管式炉加热装置和硫源加热部,之后打开管式炉,使石英管快速冷却至室温后关闭气流,并取出样品。其光学形貌如图9所示,云母表面大部分区域均是纳米颗粒,且生长出没有固定形貌的纳米薄片。
50.实施例4
51.与实例1相比,区别在于金属铬粉的质量略低。
52.取15-19mg金属铬粉与2-3mg氯化钠均匀混合,放置在外径为20
×
20mm的半圆石英舟中。新鲜剥离15
×
15mm氟金云母,厚度约为0.05mm,将其放置在铬源正上方。将该石英舟放入石英管中心恒温区,设定中心温区温度为850℃。将硫源放入外径20
×
20mm的半圆石英舟,置于石英管上游低温区,石英管外套有硫源加热部的加热带,设定温度为200℃。在程序升温之前,首先用流量为500sccm的氩气清洗石英管10min,排尽石英管内的空气。调节氩气到超小气流,流速为15sccm,同时打开管式炉加热装置以及硫源加热部,使得管式炉加热装
置以30℃/min升温,硫源加热部先达到200℃,此时硫蒸发出来并输运到氟金云母片上,当管式炉加热至中心恒温区温度850℃时,保温15min后停止管式炉加热装置和硫源加热部,之后打开管式炉,使石英管快速冷却至室温后关闭气流,并取出样品。其光学显微图如图10所示,在云母表面生长的硫化铬厚度较薄,在10nm以内,且无法形成连续薄膜。
53.实施例5
54.与实例1相比,区别在于金属铬粉的质量较高。
55.取52-65mg金属铬粉与5-6mg氯化钠均匀混合,后续参数与实施例1一致,其光学显微图像如图11所示,由于铬源供给速率过快,其成核密度极高,在云母表面形成密集且较厚的硫化铬纳米片,从而无法形成连续的薄膜。
56.实施例6
57.与实例1相比,区别在于使用的石英舟尺寸为外径15
×
15mm,氟金云母尺寸为10
×
10mm。此时源与衬底的距离约为0.5mm。其光学形貌如图12所示,云母表面生成的硫化铬纳米片密度较高且厚,导致材料无法形成连续的膜。
58.下面给出对比案例,进一步验证本发明的可行性。对比例与实施例的区别主要在于使用铬源、生长温度的不同,对比例所用铬源为三氯化铬。在对比例中,铬源温度为750-800℃,硫源温度为200℃左右,氩气流量在10-80sccm之间,氢气流量在0-70sccm之间,生长时间为10-30min。
59.对比例1
60.取一定量的三氯化铬放入舟中,新鲜剥离10
×
10mm氟金云母,厚度约为0.05mm,放置在铬源正上方。将舟放入石英管中心恒温区,设定中心温度为800℃。将硫源放入外径15
×
15mm的半圆石英舟,置于石英管上游低温区,石英管外套有硫源加热部的加热带,设定温度为200℃。在程序升温之前,首先用流量为500sccm的氩气清洗石英管10min,排尽石英管内的空气。然后,将氩气流量调至50sccm,氢气调至20sccm,同时以30℃/min的升温速率将管内中心温度升至800℃,保温15min。在程序启动时打开加热圈温控系统,使其在短时间内升至200℃。生长结束后打开管式炉,使石英管快速冷却至室温后关闭气流,并取出样品。得到的样品光学形貌如图13所示,均为分立的三角形纳米片,无法形成连续薄膜。
61.对比例2
62.取一定量的三氯化铬放入舟中,新鲜剥离10
×
10mm氟金云母,厚度约为0.05mm,放置在铬源正上方。将舟放入石英管中心恒温区,设定中心温度为750℃。将硫源放入外径15
×
15mm的半圆石英舟,置于石英管上游低温区,石英管外套有硫源加热部的加热带,设定温度为200℃。在程序升温之前,首先用流量为500sccm的氩气清洗石英管10min,排尽石英管内的空气。然后,将氩气流量调至40sccm,氢气调至40sccm,同时以30℃/min的升温速率将管内中心温度升至750℃,保温15min。在程序启动时打开硫源加热部,并调节其控制部,使其加热带在短时间内升至200℃。生长结束后打开管式炉,使石英管快速冷却至室温后关闭气流,并取出样品。得到的大部分样品为沿面外生长的垂直纳米片,样品光学形貌如图14所示,黑色倾斜的样品为垂直纳米片,无法实现材料的平面内晶畴拼接、长大,因而无法生长为连续薄膜。
63.对比例3
64.取一定量的三氯化铬放入舟中,新鲜剥离10
×
10mm氟金云母,厚度约为0.05mm,放
置在铬源正上方。将舟放入石英管中心恒温区,设定中心温度为750℃。将硫源放入外径15
×
15mm的半圆石英舟,置于石英管上游低温区,石英管外套有硫源加热部的加热带,设定温度为200℃。在程序升温之前,首先用流量为500sccm的氩气清洗石英管10min,排尽石英管内的空气。然后,将氩气流量调至15sccm,同时以30℃/min的升温速率将管内中心温度升至750℃,保温15min。在程序启动时打开硫源加热部,并调节其控制部,使其加热带在短时间内升至200℃。生长结束后打开管式炉,使石英管快速冷却至室温后关闭气流,并取出样品,其光学形貌如图15所示。衬底表面无法生长形状规则的纳米片,而是纳米线、纳米带等,且表面会沉积有大量的氯化铬,反应前驱体的过沉积较严重,很难提供稳定的前驱体供给氛围,无法实现材料的平面内外延生长。
65.此外发明人围绕制备方法中的升温速度、铬源设定加热温度、硫源设定加热温度、化学反应时间、衬底与铬源距离、载气流速等参数设置了大量实验,对其结果分析发现当铬粉的质量在20-50mg,如21mg、22mg、25mg、30mg、35mg、36mg、38mg、40mg、42mg、44mg、46mg、47mg、48mg或50mg时,氯化钠质量为1-3mg时,如1mg、1.5mg、2mg、2.5mg或3mg时,氟金云母片距铬源距离为1-10mm,如1mm、1.5mm、2mm、2.5mm、3mm、3.5mm、4mm、4.5mm、5mm、5.5mm、6mm、6.5mm、7mm、7.5mm、8mm、8.5mm、9mm或10mm时,以硫粉为硫源进行化学气相沉积制备硫化铬时,以5-80℃/min的速度,如5℃/min、6℃/min、8℃/min、10℃/min、15℃/min、20℃/min、25℃/min、30℃/min、35℃/min、40℃/min、50℃/min、60℃/min、70℃/min、75℃/min或80℃/min升温速度下将硫源升温到180-220℃,如180℃、185℃、190℃、195℃、200℃、205℃、210℃、215℃或220℃,超小流速载气氩气的流速为10-40sccm,如10sccm、15sccm、20sccm、25sccm、30sccm、35sccm或40sccm,且当铬粉所在恒温区域到780-850℃时,如780℃、785℃、788℃、790℃、795℃、800℃、810℃、820℃、830℃、840℃、850℃时,保温10-20min,如10min、11min、12min、13min、14min、15min、16min、17min、18min、19min或20min,之后快速冷却至室温,均可获得厘米级的连续大面积cr2s3薄膜。而当某一项参数不在该范围之内时,均无法获得具有较好质量的非层状二维连续大面积cr2s3薄膜,所得到的或为cr2s3纳米颗粒组成的薄膜或为分离的纳米片阵列或纳米片。
66.以上内容仅仅是对本发明结构所作的举例和说明,所属本技术领域的技术人员对所描述的具体实施例做各种各样的修改或补充或采用类似的方式替代,只要不偏离本发明的结构或者超越本权利要求书所定义的范围,均应属于本发明的保护范围。
再多了解一些
本文用于创业者技术爱好者查询,仅供学习研究,如用于商业用途,请联系技术所有人。