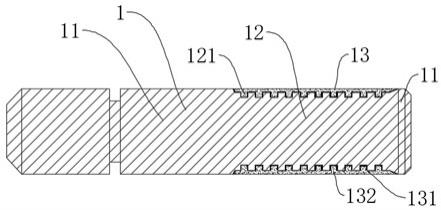
1.本发明涉及高压泵柱塞领域,具体涉及一种具有复合涂层的抗摩擦应力结构的高压泵柱塞及其制作方法。
背景技术:
2.高压柱塞泵是借助于柱塞在液缸工作腔内的往复运动来使工作腔容积产生周期性变化,来达到输送液体的目的,一般工作压力会达到5-25mpa。在柱塞泵中,液体介质的吸入和排出过程是交替进行的,而且活塞在位移过程中,其速度又在不断地变化之中。柱塞表面需要承受强烈的摩擦力及交变压力,很容易产生磨损和咬死。在柱塞表面通过热喷涂陶瓷涂层工艺制作高强度耐磨涂层,解决了柱塞在工作情况下的耐磨密封的问题,涂层具有高耐磨、耐腐蚀、低摩擦系数等特点。但是在高压超过25mpa时,由于陶瓷涂层本身的脆性和抗剪切性能比较弱,涂层往往容易因剪切应力而产生微裂纹,裂纹慢慢长大和导致涂层块状剥落而失效,因此需要提出一种具有复合涂层的抗摩擦应力结构的高压泵柱塞及其制作方法。
技术实现要素:
3.本发明的目的,是为了解决背景技术中的问题,提供一种具有复合涂层的抗摩擦应力结构的高压泵柱塞及其制作方法。
4.本发明的上述技术目的是通过以下技术方案得以实现的:一种具有复合涂层的抗摩擦应力结构的高压泵柱塞,包括有柱塞基体,所述柱塞基体由两个大直径部段和一个小直径部段组成,所述小直径部段位于两个所述大直径部段之间,所述小直径部段为涂层区,所述小直径部段的外表面沿着长度方向阵列开设有环形凹槽,所述小直径部段的表面涂覆有复合涂层,所述复合涂层的外表面与所述大直径部段的外表面齐平,所述复合涂层自内向外包括有镍铬底层和复合陶瓷涂层。
5.通过环形凹槽的设计,使得涂覆在小直径部段的复合涂层沿着小直径部段轴向方向上的厚度不同,这种涂层基底的基材处理方式,改变了常规的直线基底处理方式,使得涂层在受剪切力和压力较大的时候,不同厚度的涂层产生的应力方向不一致,导致破坏性的应力被有效分散,不容易集中在某一薄弱位置而诱发涂层微裂纹的产生。
6.优选地,所述小直径部段的直径小于所述第一直径部段的直径0.15mm-0.2mm, 从而能够预留出0.15
ꢀ‑
0.2mm涂层厚度。
7.优选地,所述凹槽的深度为0.1mm,边缘处倒角过渡,从而保证复合涂层具有不同厚度的同时,防止凹槽过深,影响高压泵柱塞的整体强度。
8.一种具有复合涂层的抗摩擦应力结构的高压泵柱塞的制作方法,包括以下步骤:s1,切削,确定柱塞基体的涂层区,将确定为涂层区的部分进行切削,使得柱塞基体涂层区的部分切割成小直径部段,将小直径部段继续通过车床加工开设出环形凹槽;
s2,除油烘干处理,将经过步骤切削后的柱塞基体柱塞基体进行除油烘干处理;s3,喷砂处理,将除油烘干处理后的柱塞基体的涂层区进行喷砂处理,使得喷砂后的柱塞基体表面粗化均匀;s4,等离子喷涂处理,将经过喷砂处理后的柱塞基体的涂层区喷涂一层镍铬底层,起到增加结合力、防腐蚀的功能,在底层之上使用等离子喷涂at13复合陶瓷涂层,初步形成了高压泵柱塞;s5,涂层封孔,使用微晶石蜡封孔剂对高压泵柱塞的复合涂层进行封孔,使复合涂层具有可靠的耐蚀性和润滑性;s6,侧面磨加工,用无心磨床对经过涂层封孔后的高压泵柱塞的侧面进行磨加工,分粗磨、精磨和抛光三道工序,分别使用120目、800目、2500目金刚砂轮, 粗磨后粗糙度为ra1.0μm;精磨后为ra0.2μm;抛光后为ra0.05μm,表面达到镜面状态;s7,两端抛光处理,采用抛头机构对经过侧面磨加工的高压泵柱塞的两头进行抛光处理,去除两端在加工过程中产生的污染,达到镜面状态。
9.通过切削处理加工出环形凹槽,使得涂覆在小直径部段的复合涂层沿着小直径部段轴向方向上的厚度不同,得涂层在受剪切力和压力较大的时候,不同厚度的涂层产生的应力方向不一致,导致破坏性的应力被有效分散,不容易集中在某一薄弱位置而诱发涂层微裂纹的产生,有效的拓展了柱塞泵在高压区间的工作性能,使陶瓷涂层柱塞工作压力范围扩展到25-50mpa区间;通过除油烘干和喷砂处理,对涂层区进行预处理,喷砂后柱塞基体表面粗化均匀,粗糙度达到ra:0.4um以上,保证了后期涂层与基体能够有效结合;通过等离子喷涂处理,先喷涂一层镍铬底层,起到增加结合力、防腐蚀的功能,在底层之上使用等离子喷涂at13(13%氧化钛 87%氧化铝)复合陶瓷涂层,喷涂电流600a,电压75v,主气(氩气)流量45l/m,次气(氢气)流量7.5l/m,送粉速率50g/min,涂层孔隙率达到5%以下,显微硬度达到hv800-1000,喷涂工艺充分发挥at13陶瓷涂层高硬度高致密度的优点,耐磨性和机械强度十分适合柱塞的工作特点。
10.通过涂层封孔,封孔就是在涂层上再涂上一层封孔剂,封孔剂渗透到涂层里面,将涂层粉末的空隙封住,使涂层的耐磨效果更好。
11.通过侧面磨加工,使得表面达到镜面状态,有利于减小摩擦系数,减低摩擦热的产生;通过两端抛光处理,对经过侧面磨加工的高压泵柱塞的两头进行抛光处理,去除两端在加工过程中产生的污染,达到镜面状态,使得产品整体的光洁度保持一致。
12.优选地,抛头机构括有工作台、逆时针旋转的转盘、可旋转固定筒组、左侧抛光结构、左侧自动下料机构、右侧抛光结构、右侧自动下料机构,所述转盘设在所述工作台的上方,所述左侧抛光结构和右侧抛光结构相对设在所述转盘相对的两侧,所述可旋转固定筒组包括有第一固定筒、第二固定筒、第三固定筒、第四固定筒、第五固定筒、第六固定筒、第七固定筒、第八固定筒,未开始工作时,所述可旋转固定筒组呈圆周阵列分布在所述转盘的上表面且其第一固定筒位于所述左侧抛光结构的下方,第五固定筒位于所述右侧抛光结构的下方,所述右侧自动下料机构设在所述右侧抛光结构的侧边且位于第四固定筒的上方,所述左侧自动下料机构设在所述左侧抛光结构的侧边且位于第八固定筒的上方。
13.优选地,所述左侧抛光结构包括有水平滑台、竖直滑台、抛光电机、抛轮,所述水平滑台设在所述转盘的一侧且水平滑台与所述工作台的上表面固定连接,所述竖直滑台滑动设在所述水平滑台的上,所述抛光电机滑动设在所述竖直滑台的滑动方向上,所述抛轮设在所述抛光电机的输出端,通过水平滑台和竖直滑台,使得抛光电机能够进行水平方向和竖直方向的移动,从而调整抛光电机的位置。
14.右侧抛光结构的结构和左侧抛光结构的结构相同。
15.优选地,所述左侧自动下料机构包括有储料筒、上圆盘、下圆盘、旋转轴、驱动电机、第一支架,所述第一支架与所述工作台固定连接,所述储料筒设在所述第一支架上,所述储料筒的侧壁开设有挡料缺口,所述旋转轴位于所述储料筒的侧边,所述上圆盘与下圆盘至上而下固定在旋转轴的侧壁上,上圆盘与挡料缺口齐平,下圆盘与储料筒的底部齐平,所述上圆盘的边缘开设有第一下料缺口,所述下圆盘的边缘开设有第二下料缺口且朝向与第一下料缺口相反,所述挡料缺口至储料筒底部之间的距离和高压泵柱塞的长度相同,所述驱动电机设在所述旋转轴的底部且固定在第一支架上,所述高压泵柱塞的端面完成了倒角。
16.右侧自动下料机构的结构和左侧自动下料机构的结构相同。
17.通过储料筒将倒好角的高压泵柱塞至下而上依次储存,初始状态时,下圆盘将储料筒的底部进行遮挡,防止高压泵柱塞掉落,之后驱动电机带动旋转轴进行旋转,当下圆盘的第二下料缺口移动至储料筒的底部时,使得位于底部的高压泵柱塞失去阻挡,受到本身重力的作用,掉落至下方的可旋转固定筒组内,于此同时,上圆盘将上方的高压泵柱塞遮挡,之后缓慢旋转,当第一下料缺口到达挡料缺口时,高压泵柱塞掉落至下圆盘上,之后随着旋转,下圆盘的第二下料缺口移动至储料筒的下方,使得高压泵柱塞再次失去阻挡,受到本身重力的作用,掉落至下方的可旋转固定筒组内,于此同时上圆盘跟着旋转,使得上圆盘将上方的高压泵柱塞进行阻挡,之后一直这样进行重复下料,从而使得高压泵柱塞能够进行自动间隙下料,能够配合抛光机构进行自动下料,提高整体的工作效率。
18.优选地,所述第一固定筒包括有固定筒本体、被动齿轮、主动齿轮、旋转电机、固定轴承,所述旋转电机固定在所述转盘上,所述主动齿轮与所述旋转电机的输出轴固定连接,所述被动齿轮与所述主动齿轮啮合,所述被动齿轮套设固定在所述固定筒本体的外侧壁,所述固定轴承设在所述固定筒本体的底部,所述转盘上开设有便于固定轴承放置的凹槽,所述固定轴承设在凹槽内,所述固定轴承的内圈与固定筒本体的底部固定连接,所述固定轴承的外圈与凹槽固定连接。
19.第二固定筒、第三固定筒、第四固定筒、第五固定筒、第六固定筒、第七固定筒、第八固定筒的结构均与第一固定筒相同。
20.通过旋转电机的旋转,从而带动主动齿轮进行旋转,从而带动被动齿轮进行旋转,从而使得固定筒本体能够进行自传,从而完成高压泵柱塞端面的抛光。
21.优选地,所述固定筒本体相对的侧壁上设有两个夹持机构,所述夹持机构包括有电磁铁、拉簧,所述固定筒本体的侧壁上开设有限位槽,所述拉簧设在所述限位槽内,所述拉簧的一侧与限位槽的槽底固定连接,其另一侧连接所述电磁铁,所述电磁铁为弧形状,当需要抛光时,两个电磁铁通电进行吸合,从而将高压泵柱塞进行夹持,防止抛光时,出现晃动的情况,不需要抛光时,电磁铁失电,拉簧将电磁铁拉回至限位槽内,防止影响下一个物
料的掉落。
22.优选地,所述凹槽为通槽,所述转盘的底部设有挡料盘,所述挡料盘通过第二支架与工作台固定连接,所述挡料盘上开设有左出料口与右出料口,所述左出料口位于所述第二固定筒的下方,所述右出料口位于所述第六固定筒的下方,通过通槽的设计,使得高压泵柱塞的底部能够接触到挡料盘,当转盘带着已经抛光好的高压泵柱塞移动至左出料口与右出料口时,抛好光的高压泵柱塞能够从左出料口与右出料口出来,完成出料的目的,无需人工拿取,更加的便捷。
23.优选地,所述左出料口与右出料口的底部均设有集料槽,便于对抛光好的高压泵柱塞进行收集。
24.优选地,所述转盘的底部设有转盘旋转电机,所述转盘旋转电机的输出端贯穿所述挡料盘与所述转盘的底部固定连接,所述转盘旋转电机的电机端固定在所述工作台上,所述挡料盘与转盘旋转电机的输出轴通过轴承连接,通过转盘旋转电机带动转盘旋转,同时挡料盘与转盘旋转电机的输出轴通过轴承连接,能够使得转盘旋转的同时,挡料盘不发生旋转。
25.综上所述,本发明的有益效果:1.本发明通过环形凹槽的设计,使得涂覆在小直径部段的复合涂层沿着小直径部段轴向方向上的厚度不同,这种涂层基底的基材处理方式,改变了常规的直线基底处理方式,使得涂层在受剪切力和压力较大的时候,不同厚度的涂层产生的应力方向不一致,导致破坏性的应力被有效分散,不容易集中在某一薄弱位置而诱发涂层微裂纹的产生;2.本发明通过两端抛光处理,对经过侧面磨加工的高压泵柱塞的两头进行抛光处理,去除两端在加工过程中产生的污染,达到镜面状态,使得产品整体的光洁度保持一致;3.本发明通过右侧下料机构使得需要端面抛光的高压泵柱塞掉落至第四固定筒,通过左侧自动下料机构使得需要端面抛光的高压泵柱塞掉落至第八固定筒的上方,之后转盘逆时针旋转,使得第八固定筒位于左侧抛光结构的下方,第四固定筒位于右侧抛光结构的下方,同时第七固定筒移动至左侧自动下料机构的下方,第三固定筒移动至右侧自动下料机构的下方,之后左侧抛光结构和右侧抛光结构同时工作,第八固定筒和第四固定筒进行自转,从而同时完成对高压泵柱塞一面的端面进行抛光,在抛光的同时,下一个高压泵柱塞分别掉落至第七固定筒和第三固定筒,抛光结束后,转盘旋转,将第八固定筒和第四固定筒旋转至下一个固定筒进行收集,将第七固定筒与第三固定筒移动至左侧抛光结构和右侧抛光结构的下方重复第八固定筒和第四固定筒的抛光步骤,无需手工抛光,提高了抛光效率和精度,同时采用右侧抛光结构和左侧抛光结构同时运行,进一步的提高了抛光效率;4.本发明通过储料筒将倒好角的高压泵柱塞至下而上依次储存,初始状态时,下圆盘将储料筒的底部进行遮挡,防止高压泵柱塞掉落,之后驱动电机带动旋转轴进行旋转,当下圆盘的第二下料缺口移动至储料筒的底部时,使得位于底部的高压泵柱塞失去阻挡,受到本身重力的作用,掉落至下方的可旋转固定筒组内,于此同时,上圆盘将上方的高压泵柱塞遮挡,之后缓慢旋转,当第一下料缺口到达挡料缺口时,高压泵柱塞掉落至下圆盘上,之后随着旋转,下圆盘的第二下料缺口移动至储料筒的下方,使得高压泵柱塞再次失去阻挡,受到本身重力的作用,掉落至下方的可旋转固定筒组内,于此同时上圆盘跟着旋转,使得上圆盘将上方的高压泵柱塞进行阻挡,之后一直这样进行重复下料,从而使得高压泵柱
塞能够进行自动间隙下料,能够配合抛光机构进行自动下料,提高整体的工作效率。
附图说明
26.图1是本发明产品的剖视示意图;图2是本发明产品的立体示意图;图3是本发明制作方法的流程示意图;图4是本发明抛头机构的立体示意图;图5是本发明抛头机构的仰视示意图;图6是本发明抛头机构去掉工作台的俯视示意图;图7是本发明左侧自动下料机构的示意图;图8是本发明左侧自动下料机构的上圆盘阻挡住物料的示意图;图9是本发明左侧自动下料机构的下圆盘阻挡住物料的示意图;图10是本发明储料筒的示意图;图11是本发明储夹持机构夹住高压泵柱塞的剖视示意图;图12是本发明储夹持机构未夹住高压泵柱塞的剖视示意图;图13是本发明高压泵柱塞旋转到左侧出料口的剖视示意图。
具体实施方式
27.以下具体实施例仅仅是对本发明的解释,其并不是对本发明的限制,本领域技术人员在阅读完本说明书后可以根据需要对本实施例做出没有创造性贡献的修改,但只要在本发明的权利要求范围内都受到专利法的保护。
28.下面结合附图以实施例对本发明进行详细说明。
实施例
29.如图1-2所示,一种具有复合涂层的抗摩擦应力结构的高压泵柱塞,包括有柱塞基体1,所述柱塞基体1由两个大直径部段11和一个小直径部段12组成,所述小直径部段12位于两个所述大直径部段11之间,所述小直径部段12为涂层区,所述小直径部段12的外表面沿着长度方向阵列开设有环形凹槽121,所述小直径部段12的表面涂覆有复合涂层13,所述复合涂层13的外表面与所述大直径部段11的外表面齐平,所述复合涂层13自内向外包括有镍铬底层131和复合陶瓷涂层132,我们改进了陶瓷涂层的结构和制作工艺,有效的拓展了柱塞泵在高压区间的工作性能,使陶瓷涂层柱塞工作压力范围扩展到25-50mpa区间。
30.如图3所示,一种具有复合涂层的抗摩擦应力结构的高压泵柱塞的制作方法,包括以下步骤:s1,切削,确定柱塞基体1的涂层区,将确定为涂层区的部分进行切削,使得柱塞基体涂层区的部分切割成小直径部段12,将小直径部段12继续通过车床加工开设出环形凹槽121;s2,除油烘干处理,将经过步骤切削后的柱塞基体柱塞基体1进行除油烘干处理;s3,喷砂处理,将除油烘干处理后的柱塞基体1的涂层区进行喷砂处理,使得喷砂后的柱塞基体1表面粗化均匀;
s4,等离子喷涂处理,将经过喷砂处理后的柱塞基体1的涂层区喷涂一层镍铬底层131,起到增加结合力、防腐蚀的功能,在底层之上使用等离子喷涂at13复合陶瓷涂层132,初步形成了高压泵柱塞;s5,涂层封孔,使用微晶石蜡封孔剂对高压泵柱塞的复合涂层13进行封孔,使复合涂层13具有可靠的耐蚀性和润滑性;s6,侧面磨加工,用无心磨床对经过涂层封孔后的高压泵柱塞的侧面进行磨加工,分粗磨、精磨和抛光三道工序,分别使用120目、800目、2500目金刚砂轮, 粗磨后粗糙度为ra1.0μm;精磨后为ra0.2μm;抛光后为ra0.05μm,表面达到镜面状态;s7,两端抛光处理,采用抛头机构2对经过侧面磨加工的高压泵柱塞的两头进行抛光处理,去除两端在加工过程中产生的污染,达到镜面状态。
31.如图4-13所示,抛头机构2括有工作台3、逆时针旋转的转盘4、可旋转固定筒组5、左侧抛光结构6、左侧自动下料机构7、右侧抛光结构8、右侧自动下料机构9,所述转盘4设在所述工作台3的上方,所述左侧抛光结构6和右侧抛光结构8相对设在所述转盘4相对的两侧,所述可旋转固定筒组5包括有第一固定筒501、第二固定筒502、第三固定筒503、第四固定筒504、第五固定筒505、第六固定筒506、第七固定筒507、第八固定筒508,所述可旋转固定筒组5呈圆周阵列分布在所述转盘4的上表面且其第一固定筒501位于所述左侧抛光结构6的下方,第五固定筒505位于所述右侧抛光结构8的下方,所述右侧自动下料机构9设在所述右侧抛光结构6的侧边且位于第四固定筒504的上方,所述左侧自动下料机构7设在所述左侧抛光结构6的侧边且位于第八固定筒508的上方,所述左侧抛光结构6包括有水平滑台61、竖直滑台62、抛光电机63、抛轮64,所述水平滑台61设在所述转盘4的一侧且水平滑台61与所述工作台3的上表面固定连接,所述竖直滑台62滑动设在所述水平滑台61的上,所述抛光电机63滑动设在所述竖直滑台62的滑动方向上,所述抛轮64设在所述抛光电机63的输出端,所述左侧自动下料机构7包括有储料筒71、上圆盘72、下圆盘73、旋转轴74、驱动电机75、第一支架76,所述第一支架76与所述工作台3固定连接,所述储料筒71设在所述第一支架76上,所述储料筒71的侧壁开设有挡料缺口711,所述旋转轴74位于所述储料筒71的侧边,所述上圆盘72与下圆盘73至上而下固定在旋转轴74的侧壁上,上圆盘72与挡料缺口711齐平,下圆盘73与储料筒71的底部齐平,所述上圆盘72的边缘开设有第一下料缺口721,所述下圆盘73的边缘开设有第二下料缺口731且朝向与第一下料缺口721相反,所述驱动电机75设在所述旋转轴74的底部且固定在第一支架76上,所述第一固定筒501包括有固定筒本体51、被动齿轮52、主动齿轮53、旋转电机54、固定轴承55,所述旋转电机54固定在所述转盘4上,所述主动齿轮53与所述旋转电机54的输出轴固定连接,所述被动齿轮52与所述主动齿轮53啮合,所述被动齿轮52套设固定在所述固定筒本体51的外侧壁,所述固定轴承55设在所述固定筒本体51的底部,所述转盘4上开设有便于固定轴承55放置的凹槽551,所述固定轴承55设在凹槽551内,所述固定轴承55的内圈与固定筒本体51的底部固定连接,所述固定轴承55的外圈与凹槽固定连接,所述固定筒本体51相对的侧壁上设有两个夹持机构56,所述夹持机构56包括有电磁铁561、拉簧562,所述固定筒本体51的侧壁上开设有限位槽511,所述拉簧562设在所述限位槽511内,所述拉簧562的一侧与限位槽511的槽底固定连接,其另一侧连接所述电磁铁561,所述凹槽551为通槽,所述转盘4的底部设有挡料盘41,所述挡料盘41通过第二支架42与工作台3固定连接,所述挡料盘41上开设有左出料口411与右出料口412,
所述左出料口411位于所述第二固定筒502的下方,所述右出料口412位于所述第六固定筒506的下方,本案的电机可采用步进电机,在进行旋转限位时,也可采用限位开关进行限位,对步进电机和限位开关的控制,均可通过控制器进行控制,控制器控制步进电机或者限位开关这是很成熟的技术,因此不在本案进行赘述。
32.如图5-6所示,所述左出料口411与右出料口412的底部均设有集料槽413,所述转盘4的底部设有转盘旋转电机43,所述转盘旋转电机43的输出端贯穿所述挡料盘41与所述转盘4的底部固定连接,所述转盘旋转电机43的电机端固定在所述工作台3上,所述挡料盘41与转盘旋转电机43的输出轴通过轴承连接。
33.工作原理:如图4-13所示,对高压泵柱塞两端的端面进行抛光时,将倒好角的高压泵柱塞放入左侧自动下料机构7和右侧自动下料机构9的储料筒71内,下圆盘73将高压泵柱塞进行阻挡,开始抛光时,驱动电机75带动旋转轴74进行旋转,第二下料缺口731旋转至储料筒71的底部,使得位于底部的高压泵柱塞失去阻挡,受到本身重力的作用,掉落至底部的第八固定筒508和第四固定筒504内,同时上圆盘72将上一个高压泵柱塞进行阻挡,之后上圆盘72和下圆盘73一直保持匀速的旋转,当下一个固定筒移动至储料筒71的下方时,第二下料缺口731正好旋转至储料筒71的下方,保证转盘旋转一下,就掉一个高压泵柱塞到固定筒内;之后第八固定筒508和第四固定筒504内的电磁铁561通电进行吸合,从而将高压泵柱塞进行夹持,之后转盘4开始,将第八固定筒508和第四固定筒504分别移动至左侧抛光结构6和右侧抛光结构8的下方,之后第八固定筒508和第四固定筒504的旋转电机54驱动固定筒本体51进行自转,之后抛光电机63驱动抛轮64对高压泵柱塞的一个端面进行抛光,于此同时第七固定筒507和第三固定筒503内已夹持有高压泵柱塞,准备抛光,第八固定筒508和第四固定筒504内的高压泵柱塞抛光结束后,电磁铁561失电,拉簧562带动电磁铁561恢复至限位槽511内,转盘逆时针旋转,将第八固定筒508和第四固定筒504分别移动至左出料口411与右出料口412的上方,高压泵柱塞通过左出料口411与右出料口412掉落至下方的收集槽413内,完成位于第八固定筒508和第四固定筒504内的高压泵柱塞一面的端面抛光,第七固定筒507和第三固定筒503移动至左侧抛光结构6和右侧抛光结构8的下方进行抛光,依次类推,对第六固定筒和第二固定筒,第五固定筒和第一固定筒内的高压泵柱塞一面的端面抛光,高压泵柱塞的一端全部抛光后,再对另一端也进行抛光,整个过程中,无需手工抛光,提高了抛光效率和精度,同时采用右侧抛光结构和左侧抛光结构同时运行,进一步的提高了抛光效率。
再多了解一些
本文用于创业者技术爱好者查询,仅供学习研究,如用于商业用途,请联系技术所有人。