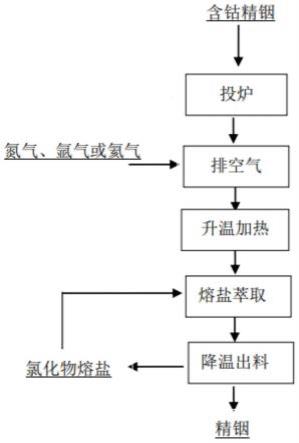
1.本发明涉及精铟生产技术领域,尤其是一种精铟中钴的去除方法。
背景技术:
2.铟是电子工业中非常重要的一种金属,例如由铟为原料制备的氧化铟锡(indium tin oxide,ito)被广泛用作电视、手机、电脑显示器的液晶屏等产品中。应用于制备铟化合物时,对铟的纯度要求很高,须采用4.5n以上纯度的高纯精铟。然而在地壳中铟是极为分散,没有单独矿床的,均是副产于其它主要金属,工业上通过回收烟灰中浓缩的铟来生产,例如锌冶炼和铅冶炼的副产品。因此,铟回收原料中含有大量的zn、fe、cu、al、ga、as、cd、等金属杂质,除这些金属成分外,还含有ni、co等微量成分。这些杂质往往对铟的性能影响很大,因此为去除这些金属杂质和回收高纯度铟需要复杂的过程。
3.现有的铟的回收方法主要有:(a)通过调节ph值以氢氧化物的形式沉淀的方法;(b)通过添加硫化剂以硫化物形式沉淀的方法;(c)通过添加金属al、zn、cd、zn-cd合金等进行置换沉淀的方法;(d)通过溶剂萃取、离子交换法回收铟的方法;(e)化学提纯和电解熔炼结合回收的方法。
4.传统的铟精炼方法中,湿法精炼相结合的方法工艺复杂,周期长,过程中产生的铟损失大,产生大量废水和废气,因此存在精炼成本高的问题。特别是在铟的生产过程中,钴含量的偏高会给进一步的电解精炼纯化造成较大的困难,当钴含量过高时导致烧板。并且精铟锭中要求钴的含量小于5ppm,为达到这个标准,不得不进行二次电解,而导致交货时间长并且增加成本。因此通过简单、快速、高效的工序严格控制杂质钴的含量显得尤为重要。
技术实现要素:
5.本发明的目的在于,克服现有的精铟的制备过程复杂、成本高的缺陷,提供一种精铟中钴的去除方法。本发明通过使用氯化物对铟中的钴进行熔融萃取,可以实现铟中杂质钴的高效脱除。
6.为实现上述目的,本发明采用如下技术方案:
7.一种精铟中钴的去除方法,包括如下步骤:
8.s1.在惰性氛围中,将铟原料与氯化物混合均匀并加热熔融进行反应;
9.s2.反应结束后,经静置、降温后,分离即可得到精铟。
10.本发明通过投入固态氯化物作为熔盐萃取剂,在较低的温度(300~500℃)下就能够使铟中的杂质钴萃取进入到熔盐中,形成氯化钴类的熔盐,从而实现钴的去除,且不会引入其它杂质元素。本发明充分利用熔盐的密度小于铟的密度,熔盐的熔点高于铟的熔点,能够实现铟与熔盐分离完全的目的,使得铟的回收率高,且使用后的熔盐,仍可以进行返回使用。
11.优选地,所述氯化物为氯化铵、氯化亚铟或三氯化铟中的至少一种。氯化铵与钴反应生成的气体可以排出,不会引入杂质;氯化亚铟和三氯化铟也不会引入新的杂质。所述氯
化物与铟的反应式及萃取原理如下:
[0012][0013][0014][0015]
优选地,所述氯化物为氯化亚铟和三氯化铟的混合物,所述氯化亚铟:三氯化铟的重量比为1:(0.5~2)。选用该复合氯化物,可以进一步提高铟中钴的去除效率。
[0016]
所述铟原料中,钴含量为20~55ppm/100kg铟。
[0017]
优选地,所述铟原料与氯化物的重量比为铟原料:氯化物=100:(1~10)。萃取剂氯化物的添加量过少,无法完全去除钴;萃取剂氯化物添加量过多,易造成原料浪费。合适的添加量可以快速、高效的去除铟中的杂质钴。本发明可以在少量萃取剂的添加量下,即可精准去除铟中的杂质钴,大大缩短了除杂工艺以及降低了成本。进一步优选地,重量比铟原料:氯化物=100:5。
[0018]
优选地,步骤s1.中包括如下步骤:
[0019]
s11.先将铟原料加热到160~280℃下得到铟液;
[0020]
s12.向步骤s11.得到的铟液中加入氯化物,边搅拌边加热到300~500℃后,恒温搅拌反应30~120min。
[0021]
先将铟原料加热熔融成为铟液,有利于其与固态氯化物充分接触反应,提高杂质钴的去除率;进一步升温可以使得萃取剂氯化物变为熔融状态,在搅拌状态下与铟液充分反应,使铟液中的钴杂质进行充分的萃取脱除。本发明通过控制熔盐萃取的温度和时间,能够使铟与熔盐均为液态,形成液-液混合物,利于进行传质,加快萃取反应的进行,提高生产效率。
[0022]
优选地,所述惰性氛围为由氮气、氩气或氦气中的至少一种气体组成的氛围。在上述反应体系中通入氮气、氩气或氦气,使得坩埚内的空气排出,防止加热过程中铟金属的氧化,能够提高铟金属的回收率。
[0023]
优选地,步骤s2.中,静置的时间为30~60min。反应结束后静置的作用是排出反应产生的刺激性气体,保障操作人员安全;同时使铟液和氯化物熔盐(这里指反应后的氯化钴产物以及部分未反应的萃取剂)能够分层,便于降温后进行分离。
[0024]
优选地,步骤s2.中,所述降温为降温至200~250℃。在该温度下,铟仍然为液态,而氯化物已经变为固体状态,可以将铟与氯化物完全分离,且损失较小。
[0025]
上述工艺在坩埚中进行,所述坩埚的材质需要耐氯化物熔盐腐蚀,所述坩埚的材质为石墨、碳化硅、石英、玻璃、氧化铝、氧化镁或氧化锆中的至少一种。优选石墨和碳化硅。
[0026]
由上述方法除杂后得到的精铟的精度高,精度可达到4.5n甚至更高。
[0027]
与现有技术相比,本发明的有益效果是:
[0028]
本发明通过使用氯化物对铟中的钴进行熔融萃取,充分利用氯化物熔盐的密度小于铟的密度,氯化物熔盐的熔点高于铟的熔点,能够实现铟与氯化物熔盐分离完全的目的,使得铟的回收率高,且使用后的熔盐,仍可以进行返回使用。创造性的解决了精铟中杂质钴元素的处理问题,工艺简单,操作条件要求低,生产成本低,具有很高的经济效益。
附图说明
[0029]
图1为实施例1的工艺流程示意图。
具体实施方式
[0030]
为更好的说明本发明的目的、技术方案和优点,下面将结合具体实施例和附图来进一步说明本发明,但实施例并不对本发明做任何形式的限定。除非特别说明,本发明采用的试剂、方法和设备为本技术领域常规试剂、方法和设备。除非特别说明,本发明所用试剂和材料均为市购。
[0031]
实施例1
[0032]
本实施例提供一种精铟中钴的去除方法,包括如下步骤(工艺流程示意图如图1所示):
[0033]
s1.熔融萃取反应
[0034]
s11.称取100.12kg含钴量为21ppm的精铟(铟锭)置于熔炉反应器的石墨坩埚中,向石墨坩埚中,按照20l/min的流量通入氮气作为保护气,通气时间为5min,保证石墨坩埚中空气被完全排出;盖上反应炉盖后,对坩埚进行升温加热到160℃,待铟锭熔化成铟液;
[0035]
s12.按照原料铟:氯化物萃取剂的质量比为100:1的比例,称取1.0kg的萃取剂固态氯化铵,通过炉盖的加料孔投入到s11.得到的铟液中,开启石墨搅拌器,升温至300℃,然后保持温度继续进行搅拌反应30min;
[0036]
s2.反应结束后,静置30min,再关闭加热,降温到200℃后,由坩埚底部阀门放出铟液,转到模具中浇筑成铟锭(97.86kg),并取样检测分析精铟中钴含量为1ppm,钴脱除率为95.24%,达到4.5n精铟的标准。铟的回收率为97.74%。
[0037]
实施例2
[0038]
本实施例提供一种精铟中钴的去除方法,包括如下步骤:
[0039]
s1.熔融萃取反应
[0040]
s11.称取100.25kg含钴量为30ppm的精铟(铟锭)置于熔炉反应器的石墨坩埚中,向石墨坩埚中,按照20l/min的流量通入氮气作为保护气,通气时间为5min,保证石墨坩埚中空气被完全排出;盖上反应炉盖后,对坩埚进行升温加热到200℃,待铟锭熔化成铟液;
[0041]
s12.按照原料铟:氯化物萃取剂的质量比为100:4的比例,称取4.0kg的萃取剂固态氯化亚铟,通过炉盖的加料孔投入到s11.得到的铟液中,开启石墨搅拌器,升温至400℃,然后保持温度继续进行搅拌反应60min;
[0042]
s2.反应结束后,静置30min,再关闭加热,降温到200℃后,由坩埚底部阀门放出铟液,转到模具中浇筑成铟锭(98.32kg),并取样检测分析精铟中钴含量为2ppm,钴脱除率为93.33%,达到4.5n精铟的标准。铟的回收率为99.07%。
[0043]
实施例3
[0044]
本实施例提供一种精铟中钴的去除方法,包括如下步骤:
[0045]
s1.熔融萃取反应
[0046]
s11.称取101.67kg含钴量为35ppm的精铟(铟锭)置于熔炉反应器的石墨坩埚中,向石墨坩埚中,按照20l/min的流量通入氮气作为保护气,通气时间为5min,保证石墨坩埚中空气被完全排出;盖上反应炉盖后,对坩埚进行升温加热到250℃,待铟锭熔化成铟液;
[0047]
s12.按照原料铟:氯化物萃取剂的质量比为100:7的比例,称取7.0kg的萃取剂固态三氯化铟,通过炉盖的加料孔投入到s11.得到的铟液中,开启石墨搅拌器,升温至450℃,然后保持温度继续进行搅拌反应90min;
[0048]
s2.反应结束后,静置30min,再关闭加热,降温到200℃后,由坩埚底部阀门放出铟液,转到模具中浇筑成铟锭(100.83kg),并取样检测分析精铟中钴含量为2ppm,钴脱除率为94.29%,达到4.5n精铟的标准。铟的回收率为99.17%。
[0049]
实施例4
[0050]
本实施例提供一种精铟中钴的去除方法,包括如下步骤:
[0051]
s1.熔融萃取反应
[0052]
s11.称取100.21kg含钴量为51ppm的精铟(铟锭)置于熔炉反应器的石墨坩埚中,向石墨坩埚中,按照20l/min的流量通入氮气作为保护气,通气时间为5min,保证石墨坩埚中空气被完全排出;盖上反应炉盖后,对坩埚进行升温加热到280℃,待铟锭熔化成铟液;
[0053]
s12.按照原料铟:氯化物萃取剂的质量比为100:10的比例,称取10.0kg的萃取剂固态三氯化铟,通过炉盖的加料孔投入到s11.得到的铟液中,开启石墨搅拌器,升温至500℃,然后保持温度继续进行搅拌反应120min;
[0054]
s2.反应结束后,静置30min,再关闭加热,降温到200℃后,由坩埚底部阀门放出铟液,转到模具中浇筑成铟锭(99.54kg),并取样检测分析精铟中钴含量为3ppm,钴脱除率为94.12%,达到4.5n精铟的标准。铟的回收率为99.33%。
[0055]
实施例5
[0056]
本实施例提供一种精铟中钴的去除方法,其工艺步骤与实施例1的不同之处在于:步骤s12.中,将1.0kg氯化铵替换为0.5kg氯化亚铟和0.5kg三氯化铟。步骤s2.得到的铟锭中钴含量为0.5ppm,钴脱除率为97.62%,达到4.5n精铟的标准,表明氯化亚铟和三氯化铟组成的混合萃取剂对钴具有更好的去除效果。
[0057]
铟的回收率为98.66%,这可能是因为使用氯化铵作为萃取剂,氯化铵除了会与钴进行反应外,还避免不了会有部分氯化铵与铟进行卤化反应。
[0058]
实施例6
[0059]
本实施例提供一种精铟中钴的去除方法,包括如下步骤:
[0060]
s1.称取100.12kg含钴量为21ppm的精铟(铟锭)、1.0kg的萃取剂固态氯化铵置于熔炉反应器的石墨坩埚中,向石墨坩埚中,按照20l/min的流量通入氮气作为保护气,通气时间为5min,保证石墨坩埚中空气被完全排出;盖上反应炉盖后,开启石墨搅拌器,对坩埚进行升温加热到300℃,然后保持温度继续进行搅拌反应90min;
[0061]
s2.反应结束后,静置30min,再关闭加热,降温到200℃后,由坩埚底部阀门放出铟液,转到模具中浇筑成铟锭(97.81kg),并取样检测分析精铟中钴含量为3ppm,钴脱除率为85.71%,达到4.5n精铟的标准。
[0062]
即,本实施例与实施例1的不同之处在于,本实施例是直接将铟原料与萃取剂氯化物进行共混,直接共混导致萃取不充分,即使将反应时间延长,钴的去除率也较低。铟的回收率为97.69%。
[0063]
实施例7
[0064]
本实施例提供一种精铟中钴的去除方法,工艺与实施例1的不同之处在于,步骤
s2.中未进行静置,反应结束后直接关闭加热进行降温。步骤s2.得到的铟锭中钴含量为1ppm,钴脱除率为95.24%,达到4.5n精铟的标准。但铟的回收率仅为94.15%,与实施例1相比,回收率较低。
[0065]
对比例1
[0066]
本对比例提供一种精铟中钴的去除方法,工艺与实施例1的不同之处在于,步骤s12.中并未继续升温,而是直接在160℃下进行搅拌反应。
[0067]
骤s2.得到的铟锭中钴含量为18ppm,钴脱除率为14.29%,铟中钴含量超标。铟的回收率为99.21%。
[0068]
对比例2
[0069]
本对比例提供一种精铟中钴的去除方法,工艺与实施例2的不同之处在于,步骤s12.中并未继续升温,而是直接在200℃下进行搅拌反应。
[0070]
骤s2.得到的铟锭中钴含量为25ppm,钴脱除率为16.67%,铟中钴含量超标。铟的回收率为99.04%。
[0071]
对比例3
[0072]
本对比例提供一种精铟中钴的去除方法,工艺与实施例1的不同之处在于,反应体系中并未通入保护气体,而是在空气气氛中进行反应。
[0073]
骤s2.得到的铟锭中钴含量为2ppm,钴脱除率为90.48%,但铟的回收率仅为91.15%,显著降低。
[0074]
最后所应当说明的是,以上实施例仅用以说明本发明的技术方案而非对本发明保护范围的限制,尽管参照较佳实施例对本发明作了详细说明,本领域的普通技术人员应当理解,可以对本发明的技术方案进行修改或者等同替换,而不脱离本发明技术方案的实质和范围。
再多了解一些
本文用于创业者技术爱好者查询,仅供学习研究,如用于商业用途,请联系技术所有人。