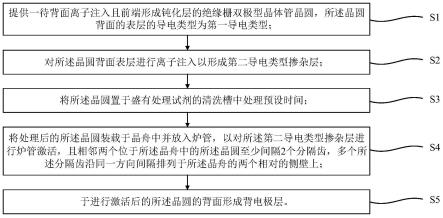
1.本发明属于半导体集成电路制造领域,涉及一种绝缘栅双极型晶体管及其制备方法。
背景技术:
2.功率半导体器件作为能源控制的一种核心元器件,是实现强电压向弱电压转换的桥梁,绝缘栅双极型晶体管(insulated gate bipolar transistor,简称igbt)作为一种栅控双极型器件,其具有导通损耗低、开关速度快、输入阻抗高和电流能力强等优点,在能源转换和能量控制市场中受到越来越多的重视。为了提高器件的耐压能力及降低器件的内阻,以获得更低的正向导通压降(v
dson
),目前,非穿通型绝缘栅双极型晶体管(npt planar igbt)通过调整其材料的电阻率来降低v
dson
,但器件耐压也会降低。同样通过调整背面p型注入浓度及激活温度,以降低背电极的接触电阻,继而降低v
dson
,但开关损耗亦会增加。
3.因此,急需寻找一种降低绝缘栅双极型晶体管的正向导通压降的绝缘栅双极型晶体管的制备方法。
技术实现要素:
4.鉴于以上所述现有技术的缺点,本发明的目的在于提供一种绝缘栅双极型晶体管及其制备方法,用于解决现有技术中器件的背电极层接触电阻大导致器件正向导通压降高的问题。
5.为实现上述目的及其他相关目的,本发明提供了一种绝缘栅双极型晶体管的制备方法,包括以下步骤:
6.提供一待背面离子注入且前端形成钝化层的绝缘栅双极型晶体管晶圆,所述晶圆背面的表层的导电类型为第一导电类型;
7.对所述晶圆背面表层进行离子注入以形成第二导电类型掺杂层;
8.将所述晶圆置于盛有处理试剂的清洗槽中处理预设时间;
9.将处理后的所述晶圆装载于晶舟中并放入炉管,以对所述第二导电类型掺杂层进行炉管激活,且相邻两个位于所述晶舟中的所述晶圆至少间隔2个分隔齿,多个所述分隔齿沿同一方向间隔排列于所述晶舟的两个相对的侧壁上;
10.于进行激活后的所述晶圆的背面形成背电极层。
11.可选地,对所述晶圆进行离子注入之前,还包括利用清洗试剂对所述晶圆进行清洗的步骤。
12.可选地,所述处理试剂包括稀氢氟酸溶液。
13.可选地,所述稀氢氟酸的浓度范围为0.5%~2%。
14.可选地,所述预设时间不少于1min。
15.可选地,在常温下,利用所述处理试剂对所述晶圆进行清洗处理。
16.可选地,在所述处理试剂处理之后,背面炉管激活之前,还包括对所述晶圆进行再
次清洗的步骤,以去除所述晶圆上残留的所述处理试剂。
17.可选地,进行背面炉管激活的过程中,所述晶圆的背面朝向同一方向放置。
18.可选地,对所述第二导电类型掺杂层进行背面炉管激活的时间范围为30min~50min,对所述第二导电类型掺杂层进行背面炉管激活的温度范围为300℃~400℃。
19.本发明还提供了一种绝缘栅双极型晶体管,所述绝缘栅双极型晶体管是采用上述所述的绝缘栅双极型晶体管的制备方法制备得到。
20.如上所述,本发明的绝缘栅双极型晶体管及其制备方法通过于形成所述第二导电类型掺杂层之后,采用所述处理试剂对所述晶圆进行处理预设时间,利用所述处理试剂将去除蓝膜过程中产生于所述晶圆背面的致密层去除,以减小致密层对所述背电极层与所述第二导电类型掺杂层之间的接触电阻的影响,降低所述背电极层与所述第二导电类型掺杂层的接触电阻,从工艺上降低器件的导通电阻,继而降低器件的导通压降;将处理后的所述晶圆放置于所述晶舟中,并将所述晶舟置于炉管中进行所述第二导电类型掺杂层的激活,且相邻两个所述晶圆之间间隔至少两个所述分隔齿,以增大相邻两个所述晶圆之间的距离,从激活工艺上减小汽化的所述钝化层对所述晶圆背面的影响,减少汽化的所述钝化层附着于所述晶圆背面的量,降低所述背电极层与所述第二导电类型掺杂层之间的接触电阻,进一步从工艺上降低器件的导通电阻,继而进一步地降低器件的导通压降,具有高度产业利用价值。
附图说明
21.图1显示为本发明的绝缘栅双极型晶体管的制备方法的工艺流程示意图。
22.图2显示为本发明的绝缘栅双极型晶体管的制备方法的晶圆的平面结构示意图。
23.图3显示为本发明的绝缘栅双极型晶体管的制备方法的晶舟的平面结构示意图。
24.图4显示为本发明的绝缘栅双极型晶体管在间隔不同分隔齿条件下,经过处理试剂处理及未处理的晶圆的导通压降统计图。
25.图5显示为本发明的绝缘栅双极型晶体管在间隔两个分隔齿条件下,经过处理试剂处理及未处理的晶圆的导通压降统计图。
26.附图标号说明
[0027]1ꢀꢀꢀꢀꢀꢀꢀꢀꢀꢀꢀꢀꢀꢀꢀꢀꢀꢀꢀ
晶圆
[0028]2ꢀꢀꢀꢀꢀꢀꢀꢀꢀꢀꢀꢀꢀꢀꢀꢀꢀꢀꢀ
晶舟
[0029]
21
ꢀꢀꢀꢀꢀꢀꢀꢀꢀꢀꢀꢀꢀꢀꢀꢀꢀꢀ
分隔齿
具体实施方式
[0030]
以下通过特定的具体实例说明本发明的实施方式,本领域技术人员可由本说明书所揭露的内容轻易地了解本发明的其他优点与功效。本发明还可以通过另外不同的具体实施方式加以实施或应用,本说明书中的各项细节也可以基于不同观点与应用,在没有背离本发明的精神下进行各种修饰或改变。
[0031]
请参阅图1至图5。需要说明的是,本实施例中所提供的图示仅以示意方式说明本发明的基本构想,遂图式中仅显示与本发明中有关的组件而非按照实际实施时的组件数目、形状及尺寸绘制,其实际实施时各组件的型态、数量及比例可为一种随意的改变,且其
组件布局型态也可能更为复杂。
[0032]
实施例一
[0033]
本实施例提供一种绝缘栅双极型晶体管的制备方法,如图1所示,为所述绝缘栅双极型晶体管的制备方法的工艺流程图,包括以下步骤:
[0034]
s1:提供一待背面离子注入且前端形成钝化层的绝缘栅双极型晶体管晶圆,所述晶圆背面的表层的导电类型为第一导电类型;
[0035]
s2:对所述晶圆背面表层进行离子注入以形成第二导电类型掺杂层;
[0036]
s3:将所述晶圆置于盛有处理试剂的清洗槽中处理预设时间;
[0037]
s4:将处理后的所述晶圆装载于晶舟中并放入炉管,以对所述第二导电类型掺杂层进行炉管激活,且相邻两个位于所述晶舟中的所述晶圆至少间隔2个分隔齿,多个所述分隔齿沿同一方向间隔排列于所述晶舟的两个相对的侧壁上;
[0038]
s5:于进行激活后的所述晶圆的背面形成背电极层。
[0039]
请参阅图2,执行所述步骤s1及所述步骤s2:提供一待背面离子注入且前端形成钝化层的绝缘栅双极型晶体管晶圆1,所述晶圆1背面的表层的导电类型为第一导电类型;对所述晶圆1背面表层进行离子注入以形成第二导电类型掺杂层。
[0040]
具体的,所述第一导电类型包括n型或者p型中的一种,所述第二导电类型包括n型或者p型中的一种,且所述第一导电类型与所述第二导电类型的导电类型相反。本实施例中,所述第一导电类型为n型,所述第二导电类型为p型。
[0041]
具体的,如图2所示,为所述晶圆1的平面结构示意图,所述晶圆1的材质包括硅、锗、碳化硅或者其他适合的半导体材料。本实施例中,采用硅作为所述晶圆1。
[0042]
具体的,在保证器件性能的情况下,所述晶圆1的厚度可以根据实际情况进行选择,这里不再限制;所述晶圆1背面表层的掺杂浓度可以根据实际情况进行选择,这里不再限制。
[0043]
具体的,所述钝化层的材质包括聚亚酰胺(polyimide)或者其他适合的材质。本实施例中,采用聚亚酰胺层作为器件正面的所述钝化层。
[0044]
具体的,在保证器件性能的情况下,所述钝化层的厚度可以根据实际情况进行选择,这里不再限制。
[0045]
作为示例,对所述晶圆1进行离子注入之前,还包括利用清洗试剂对所述晶圆1进行清洗的步骤。
[0046]
具体的,在进行器件前端工艺的过程中,需要对所述晶圆1的背面设置一层蓝膜,以防止形成器件正面结构的刻蚀工艺损伤所述晶圆1的背面,在完成器件的前端工艺后,进行器件的背面工艺时,需要去除所述晶圆1背面的蓝膜,由于在去除蓝膜后,所述晶圆1的背面容易残留蓝膜,因此,在去除蓝膜后需要利用所述清洗试剂对所述晶圆1进行清洗,以去除所述晶圆1背面的蓝膜残留。
[0047]
具体的,利用所述清洗试剂对所述晶圆1进行去蓝膜残留清洗的过程中,需要在40℃~60℃的温度环境下进行,去除蓝膜残留的同时所述晶圆1在该段温度下容易与所述清洗试剂发生反应,导致所述晶圆1的背部表面形成一层致密层。
[0048]
具体的,在保证器件性能的情况下,所述第二导电类型掺杂层的厚度可以根据实际情况进行设置,这里不再限制;所述第二导电类型掺杂层的掺杂浓度可以根据实际情况
进行选择,这里不再限制。
[0049]
再请参阅图3,执行所述步骤s3、所述步骤s4及所述步骤s5:将所述晶圆1置于盛有处理试剂的清洗槽中处理预设时间;将处理后的所述晶圆1装载于晶舟2中并放入炉管,以对所述第二导电类型掺杂层进行炉管激活,且相邻两个位于所述晶舟2中的所述晶圆1至少间隔2个分隔齿21,多个所述分隔齿21沿同一方向间隔排列于所述晶舟2的两个相对的侧壁上;于进行激活后的所述晶圆1的背面形成背电极层。
[0050]
作为示例,所述处理试剂包括稀氢氟酸溶液,也可以是其他适合的试剂。
[0051]
具体的,所述处理试剂用于去除所述晶圆1背面的蓝膜残留时产生的致密层,以消除致密层对所述背电极层与所述第二导电类型掺杂层之间的接触电阻的影响。
[0052]
作为示例,所述稀氢氟酸溶液的浓度范围为0.5%~2%,本实施例中,采用浓度为1%的氢氟酸作为所述处理试剂。
[0053]
具体的,由于稀氢氟酸溶液很难和所述晶圆1反应,使用稀氢氟酸溶液作为所述处理试剂去除所述致密层,便于去除所述晶圆背面的致密层的同时避免所述处理试剂腐蚀对所述晶圆1背面的腐蚀,保证了器件的性能。
[0054]
作为示例,所述预设时间不少于1min,即将所述晶圆1置于所述处理试剂中不少于1min的时间。
[0055]
具体的,所述处理试剂为稀氢氟酸溶液,将所述晶圆1置于所述处理试剂中不少于1min的时间,以便于所述晶圆1背面的致密层与所述处理试剂充分反应,完全去除所述晶圆1背面的致密层,以避免致密层影响所述背电极层与所述第二导电类型掺杂层之间的接触电阻,继而从工艺上降低绝缘栅双极型晶体管的导通电阻。
[0056]
作为示例,在常温下,利用所述处理试剂对所述晶圆1进行清洗处理,这里的常温是指20℃~30℃的室温。本实施例中,由于所述晶圆1背面的致密层在常温下可以直接与氢氟酸反应,且在常温下稀氢氟酸和所述晶圆1几乎不反应(反应速率很小,对所述晶圆1的影响可以忽略),因此选用稀氢氟酸溶液作为所述处理试剂可以避免处理过程中的升温过程,降低了成本。
[0057]
具体的,在不影响器件性能的情况下,在完全去除所述晶圆1背面的致密层的情况下,当所述处理试剂的浓度较高时,也可以适当缩短处理时间,例如利用浓度为3%的所述处理试剂对所述晶圆1的背面进行处理的情况下,可以将处理时间调整为45秒。
[0058]
作为示例,在所述处理试剂处理之后,背面炉管激活之前,还包括对所述晶圆1进行再次清洗的步骤,以去除所述晶圆1上残留的所述处理试剂。
[0059]
具体的,对所述晶圆1进行再次清洗的试剂可以是蒸馏水,也可以是其他适合的试剂。
[0060]
具体的,对所述第二导电类型掺杂层进行激活包括以下步骤:将再次清洗后的所述晶圆1装载至所述晶舟2中,且装载于所述晶舟2中相邻的两个所述晶圆1之间至少间隔两个所述分隔齿21;将装载完成的所述晶舟2放置到激活炉管的指定位置,设置炉管的加热参数,并启动炉管进行所述第二导电类型掺杂层的激活。
[0061]
具体的,如图3所示,为所述晶舟2的结构示意图,装载所述晶圆1的所述晶舟2中所述分隔齿21的尺寸、间隔距离及数量可以根据实际情况进行设置,这里不再限制。
[0062]
具体的,所述分隔齿21沿排列方向的厚度可以根据是实际情况进行选择,这路不
再限制。
[0063]
作为示例,进行背面炉管激活的过程中,所述晶圆1的背面朝向同一方向放置,即相邻两个所述晶圆1的正面与背面相对放置,以便于机械化装载所述晶圆1至所述晶舟2中。
[0064]
具体的,将所述晶圆置于所述晶舟2的方法可以是机械装载,也可以是手动装载,且在进行机械装载时,需要设置控制参数,以使转载所述晶圆1时,相邻两个所述晶圆1之间间隔至少两个所述分隔齿21。
[0065]
作为示例,对所述第二导电类型掺杂层进行背面炉管激活的时间范围为30min~50min,对所述第二导电类型掺杂层进行背面炉管激活的温度范围为300℃~400℃。
[0066]
具体的,由于所述第二导电类型掺杂层进行背面炉管激活的过程中的激活温度较高,且进行激活的时间较长,在该温度下少量的所述晶圆1正面的所述钝化层会发生汽化,汽化后的所述钝化层扩散至所述晶圆1的背面,并附着于所述晶圆1的背面,导致所述第二导电类型掺杂层与所述背电极层之间的接触电阻的离散性差,继而导致器件的正向导通压降的升高。
[0067]
具体的,通过加大所述晶舟2中相邻两个所述晶圆1之间的距离,减小汽化的所述钝化层扩散至所述晶圆1背面的几率,继而降低对所述第二导电类型掺杂层激活的过程中,所述钝化层对所述晶圆背面与所述背电极层之间的接触电阻的影响,避免器件的正向导通压降的上升。
[0068]
具体的,当手动将所述晶圆1中装载所述晶圆1至所述晶舟2中时,也可以将相邻两个所述晶圆1的相同面相对,由于所述晶圆1的阻挡,减小了所述钝化层扩散至所述晶圆1背面的几率,继而减小对所述第二导电类型掺杂层激活的过程中,所述晶圆1的正面覆盖所述钝化层对所述晶圆1背面的影响。
[0069]
具体的,形成所述背电极层的方法包括溅射法、蒸发法、化学气相沉积法(cvd)、等离子体增强化学气相沉积法(pecvd)、低压化学气相沉积法(lpcvd)、金属化合物气相沉积法(mocvd)、分子束外延法(mbe)、原子气相沉积法(avd)或原子层沉积法(ald)中的一种,也可以是其他适合的方法。
[0070]
具体的,所述背电极层的材质包括ti(钛)、tin(氮化钛)、ag(银)、au(金)、cu(铜)、al(铝)及w(钨)中的至一种,也可以是其他适合的导电材料。
[0071]
具体的,在保证器件性能的情况下,所述背电极层的厚度可以根据实际情况进行选择,这里不再限制。
[0072]
具体的,形成所述背电极层之后,还包括于所述背电极层的背面形成背电极钝化层的步骤。
[0073]
具体的,形成所述背电极钝化层之后,还包括对所述晶圆1进行划片以得到单个的所述绝缘栅双极型晶体管芯片。
[0074]
本实施例的绝缘栅双极型晶体管的制备方法通过于所述晶圆1的背面的表层形成第二导电类型掺杂之后,将所述晶圆1在常温下置于所述处理试剂中处理预设时间,以保证所述处理试剂去除所述晶圆1背面的致密层,所述晶圆1背面的致密层是由去除蓝膜残留的过程中生成,所述处理试剂在常温下对所述晶圆1无影响,保证了器件的性能,避免了致密层导致的所述第二导电类型掺杂层与所述背电极层之间的接触电阻的增加,消除由前端工艺造成的器件的正向导通电阻的增加,从工艺上降低了器件的导通电阻;在对所述第二导
电类型掺杂层激活的过程中,将所述晶圆1间隔至少两个所述分隔齿21装载至所述晶舟2中,再进行所述第二导电类型掺杂层的激活,以降低对所述第二导电类型掺杂层进行激活的过程中,所述晶圆1正面的所述钝化层汽化影响并扩散至所述晶圆1的背面,影响所述第二导电类型掺杂层与所述背电极层之间的接触电阻,继而进一步从工艺上降低了器件的导通压降。
[0075]
实施例二
[0076]
本实施例提供一种绝缘栅双极型晶体管,所述绝缘栅双极型晶体管是采用实施例一中所述的绝缘栅双极型晶体管的制备方法制备得到。
[0077]
具体的,位于所述绝缘栅双极型晶体管的半导体结构背面表层的所述第二导电类型掺杂层与所述背电极层电接触,且由于形成所述背电极层之前,利用所述处理试剂对所述半导体层的背面进行处理,降低了所述半导体层的背面与所述背电极层之间的接触电阻,继而降低了器件的导通压降,这里的半导体结构是指实施例一中的所述晶圆1经过划片后的部分,且不包括所述背电极层。
[0078]
具体的,由于所述钝化层在所述第二导电类型掺杂层激活的温度下汽化的量少,且扩散的慢,随着距离所述钝化层的距离的增加,汽化的所述钝化层的浓度逐渐降低,在对所述第二导电类型掺杂层激活的过程中,增大了所述半导体结构背面与所述半导体结构正面之间的距离,可以减小了所述钝化层附着至所述半导体结构背面的量,继而减小对所述半导体结构背面的接触电阻影响,进一步降低器件的所述背电极层与所述半导体层的背面之间的接触电阻,从工艺上降低器件的导通压降。
[0079]
具体的,当相邻两个所述晶圆1之间的距离较大时,由于距离所述晶圆1较远处的所述钝化层的浓度较低,附着于所述晶圆1背面的所述钝化层的量变化不大,因此,当逐渐增大相邻两个所述晶圆1之间的距离后,所述绝缘栅双极型晶体管的正向导通压降的变化不大。
[0080]
具体的,如图4及图5所示,分别为几种不同工艺下多批次的所述绝缘栅双极型晶体管的导通压降统计图及本发明的相邻两个所述晶圆1间隔两个所述分隔齿21的各批次的所述绝缘栅双极型晶体管的导通压降统计图,其中,本次试验使用的所述晶舟2中所述分隔齿21的尺寸及厚度均相同,即本次试验的所述晶舟2的规格相同,所试验的所述晶圆1的尺寸也相同,通过线上的试验可以看出,在背炉管激活之前未进行所述处理试剂多的处理,进行背炉管激活时,相邻两个所述晶圆1之间间隔一个所述分隔齿21的距离,所述绝缘栅双极型晶体管的正向导通压降较低明显较高,相邻两个所述晶圆1之间距离不小于两个所述分隔齿21,所述绝缘栅双极型晶体管的正向导通压降较低且变化不大,且相邻两个所述晶圆1之间间隔两个所述分隔齿21并进行所述处理试剂处理,所述绝缘栅双极型晶体管的正向导通压降在1.9v附近上下波动(图中每批次图的上下两端之间的标记线为本批次的导通压降的平均值)。
[0081]
本实施例的绝缘栅双极型晶体管通过采用实施例一中所述的绝缘栅双极型晶体管的制备方法制备得到,从工艺上消除了所述钝化层及所述晶圆1背面的致密层的影响,降低了所述背电极层与所述半导体结构的背面之间的接触电阻,使所述平面绝缘栅双极型晶体的导通电阻得以降低,继而降低了器件的导通压降。
[0082]
综上所述,本发明的绝缘栅双极型晶体管及其制备方法通过于晶圆的背面形成第
二导电类型掺杂层之后,采用处理试剂处理预设时间,以去除晶圆背面去除蓝膜过程中产生的致密层,防止致密层影响器件的背电极层与第二导电类型掺杂层之间的接触电阻,从工艺上减小了器件的导通电阻,降低了器件的导通压降;再进行第二导电类型掺杂层的炉管激活,通过适当增大晶舟中相邻两个晶圆之间的距离,以减小在第二导电类型掺杂层炉管激活多的过程中汽化的钝化层附着于晶圆背面的量,降低钝化层对晶圆背面的影响,进一步从工艺上减小背电极层与第二导电类型掺杂层之间的接触电阻,降低了器件的导通电阻,减小了器件的导通压降。所以,本发明有效克服了现有技术中的种种缺点而具有高度产业利用价值。
[0083]
上述实施例仅例示性说明本发明的原理及其功效,而非用于限制本发明。任何熟悉此技术的人士皆可在不违背本发明的精神及范畴下,对上述实施例进行修饰或改变。因此,举凡所属技术领域中具有通常知识者在未脱离本发明所揭示的精神与技术思想下所完成的一切等效修饰或改变,仍应由本发明的权利要求所涵盖。
再多了解一些
本文用于创业者技术爱好者查询,仅供学习研究,如用于商业用途,请联系技术所有人。