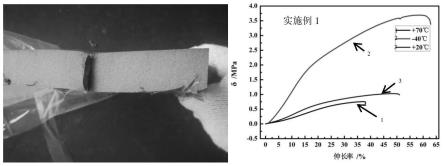
1.本发明涉及固体推进剂工艺领域,特别涉及一种声共振快速混合固体推进剂的工艺方法。
背景技术:
2.固体推进剂是战略导弹、战术导弹、空间飞行器各类固体发动机及动能拦截弹武器的动力源,其性能直接关系到导弹武器的作战性能和可靠性。固体推进剂的组分包括氧化剂、金属燃料、粘结剂、催化剂等,这些组分通过混合、浇注、固化等工艺制备成具有一定燃烧、力学性能的推进剂产品。混合工艺是推进剂制备的一个关键工序,直接关系到推进剂的力学试件的内部质量。目前,国内外普遍采用真空立式捏合机进行药浆混合,这种混合方式具有混合效率低、混合时间长等问题,而且,由于桨叶与锅壁的间距小,容易发生安全事故。同时,传统的立式混合器,推进剂混合工艺较为繁琐,具体过程包括:(1)粘合剂、增塑剂、键合剂和固化催化剂在高温下进行预混反应直至混合混匀;(2)加入固化剂,并混合均匀;(3)加入燃速催化剂,并混合均匀;(4)加入其他添加剂,并混合均匀;(5)加入金属燃烧剂,并混合均匀;(6)分步加入氧化剂,并混合均匀;(7)混合设定时间出料。整个混合工艺过程一般需要120-240min,甚至更多。
3.声共振混合是基于振动宏观混合和声流微观混合耦合作用的混合新工艺。无桨叶等混合元件、低频声流混合、可一次性加料、遥控操作人机隔离、在线混合时间短等混合工艺过程保证了混合的安全性;混合加速度高、混合无死角、全场混合保证了混合的高效性,此外,声共振还具有节能、易清洗、兼容多种材料体系等优势。因此,声共振混合技术已逐渐被应用到医药、食品、生物、化妆品、含能材料等化工领域。特别地,声共振技术已被证明可适用于超细材料、高固体含量、高粘态材料等的分散混合。cn108043305b公开了一种固体推进剂药浆的无桨混合制备方法及系统,说明声共振混合技术混合推进剂药浆的可行性。cn104492328公开了一种高固含量粘合剂体系的共振混合方法,说明声共振适用于高固含量粘合剂体系的混合,在火炸药等含能材料混合方面有一定的应用前景。cn106000198a公开了一种基于三自由度共振系统的声波混合装置,说明了声共振混合设备产生的声波能够在混合物料内部产生涡流从而使物料快速高效混合,同时混合容器内无桨叶,混合过程安全,对于各类混合体系有广泛的适用性,特别适合用来混合危险物料。
4.声共振混合具有安全高效的优点且混合均匀性受物料加入的先后顺序的影响较小,但推进剂是有着复杂化学反应的多组分体系,不当的混合工艺会导致样品产生反应气孔、强度低、断裂伸长率低等性能问题。
技术实现要素:
5.本发明的目的在于提供一种声共振快速混合固体推进剂的工艺方法,以解决推进剂混合工艺步骤冗长、耗时较长的问题,在快速的混合工艺下制备出性能优良的推进剂产品。
6.为了解决上述技术问题,本发明的技术方案是:
7.提供一种声共振快速混合固体推进剂的工艺方法,所述固体推进剂包括:粘合剂、氧化剂、增塑剂、键合剂、固化剂和其他组分;包括如下步骤:
8.将粘合剂、键合剂、氧化剂和增塑剂加入声共振混合容器中,预混反应得到初混物,增塑剂为增塑剂总量的0-100%但不包括0%;在初混物中加入固化剂,进行再混合得到再混物;在再混物中加入剩余的增塑剂、其他组分,进行终混合,得到快速混合的推进剂物料。
9.所述预混加入增塑剂比例为40-100%。
10.所述粘合剂为丁羟、聚醚或叠氮粘合剂中的任意一种或多种。
11.所述预混反应条件为:0-40g进行0-3min、40-70g进行0-7min、70-100g进行0-10min。
12.所述再混合温度为50-100℃。
13.所述再混合温度为60℃。
14.所述再混合条件为40-70g,0-10min。
15.所述终混合条件为:0-40g进行0-3min、40-70g进行0-7min、70-100g进行0-10min。
16.所述预混反应和终混合的温度可以为常温,也可以为高温。所述高温为50-100℃。若预混反应的温度低于再混合温度,先将初混物升温至再混合温度,再进行再混合。
17.所述其他组分包括金属燃烧剂、固化催化剂、安定剂、防老剂、扩链剂、交联剂、其他助剂中的任意一种或多种。
18.以固体推进剂质量为100%计,所述固体推进剂包括:粘合剂5%-20%,氧化剂40%-80%,增塑剂1%-15%,键合剂0.1%-0.6%,固化剂0%-2%,其他组分2.01%-22.1%.。
19.具体的,以固体推进剂质量为100%计,所述固体推进剂包括:粘合剂5%-20%,氧化剂40%-80%,增塑剂1%-15%,键合剂0.1%-0.6%,固化剂0%-2%,金属燃烧剂2%-20%,固化催化剂0.01%-0.1%,其他组分0%-2%。
20.一种推进剂,通过上述任一所述的一种声共振快速混合固体推进剂的工艺方法制备得到。
21.综上所述,本技术至少包括以下有益技术效果:
22.(1)本发明可以安全快速的完成固体推进剂的均匀混合,通过本专利的混合工艺制备的推进剂样品致密无气孔裂纹,能够实现固体推进剂更加快速的成功制备。
23.(2)本工艺方法对丁羟、叠氮、聚醚推进剂体系均适用,且混合时间不超过20min。
24.(3)与常规制备方法的样品相比,本工艺制备样品性能相当或更优。
附图说明
25.图1示出了具体对比例1混合工艺下推进剂样品实物图;
26.图2示出了具体对比例2混合工艺下推进剂样品实物图;
27.图3示出了具体实施例1混合工艺下推进剂样品实物图和力学性能曲线图;
28.图4示出了具体对比例3混合工艺下推进剂样品实物图;
29.图5示出了具体实施例2混合工艺下推进剂样品实物图;
30.图6示出了具体对比例4混合工艺下推进剂样品实物图;
31.图7示出了具体实施例3混合工艺下推进剂样品实物图。
具体实施方式
32.为了使本技术的工艺技术方案及优点更加清楚明白,以下结合附图对本技术的示例性实施例进行进一步详细的说明,显然,所描述的实施例中推进剂配方仅作为本技术的实例配方,而不是所有推进剂配方的穷举。并且在不冲突的情况下,本说明中的实施例及实施例中的特征可以互相结合。
33.本发明的核心思想在于针对传统混合工艺的工序冗长、低效,并且不适用于声共振混合的问题,本发明提供一种声共振快速混合固体推进剂的工艺方法,以固体推进剂质量为100%计,固体推进剂包括组分:粘合剂(丁羟、聚醚或叠氮粘合剂均可,3%-30%),氧化剂(40%-80%),金属燃烧剂(10%-30%),燃速催化剂(0%-3%)、增塑剂(1%-10%),键合剂(0.1%-0.3%),固化剂(0%-2%),固化催化剂(0.01%-0.1%),其他组分(0%-2%);包括如下步骤:
34.s1、将所述粘合剂、键合剂、氧化剂和一定比例的增塑剂加入声共振混合容器中,预混反应得到初混物。声共振设置的预混程序具体包括:30g进行1min;
②
60g进行2min;
③
80g进行2min。
35.s2、在初混物中加入固化剂,50-100℃条件下进行再混合得到再混物,声共振设置的再混合程序为:60g进行5min。
36.s3、在再混物中加入金属燃烧剂、粘合剂、增塑剂、燃速催化剂、固化催化剂和其他组分,按声共振设置的终混合程序继续混合至设定时间后出料,得到快速混合的推进剂物料。声共振设置的终混合程序具体包括:30g进行1min;
②
60g进行4min;
③
80g进行5min。
37.其他组分可在其对应实施例或对比例的限定范围内任意选择,其他组分在其对应范围内任意选择对固体推进剂的力学性能和燃烧性能影响很小。
38.实施例1
39.以固体推进剂质量为100%计,叠氮固体推进剂配方包括:粘合剂端羟基3,3-双叠氮甲基氧杂环丁烷/四氢呋喃共聚醚9.95%,氧化剂高氯酸铵55%,金属燃烧剂al粉20%,增塑剂双(2,2-二硝基丙醇)缩丙醛3%,某磷酸键合剂0.15%,固化剂甲苯二异氰酸酯0.95%,防老剂n,n
’‑
二苯基对苯二胺、交联剂三羟甲基丙烷、扩链剂二乙二醇、固化催化剂三苯基铋等其他组分10.95%。
40.一种声共振快速混合固体推进剂的工艺方法,包括:
41.s1、将所述叠氮粘合剂、键合剂、氧化剂和40%的增塑剂加入声共振混合容器中,预混反应直至混合混匀。声共振设置的预混程序具体包括:30g 1min;
②
60g 2min;
③
80g 2min。混合温度为60℃。
42.s2、加入固化剂,60℃下混合均匀。声共振设置的预混程序为:60g 5min。
43.s3、按照配方要求加入金属燃烧剂、粘合剂、增塑剂、燃速催化剂、固化催化剂和其他剩余组分,按声共振设置的混合程序继续混合至设定时间后出料,得到快速混合的推进剂物料。声共振设置的混合程序具体包括:30g 1min;
②
60g 4min;
③
80g 5min。
44.混合完毕后出料,经浇注固化成型,得到图1的推进剂样品。浇注固化成型操作步
骤包括:将推进剂药浆在60℃下缓慢真空浇注至预先准备好的成型方坯中,保压10min后取出至60℃烘箱固化168h。
45.本实施例制备的推进剂样品致密无气孔,力学性能、燃烧性能与传统工艺相当甚至更优,推进剂样品实物如图3,性能数据见表1。
46.实施例2
47.与实施例1的不同之处在于:
48.步骤s1中,叠氮粘合剂、键合剂、氧化剂和100%的增塑剂加入声共振混合容器中,进行预混反应。
49.本实施例制备的推进剂样品致密无气孔,力学性能、燃烧性能与传统工艺相当甚至更优,推进剂试样实物如图5,性能数据见表1。
50.实施例3
51.与实施例1的不同之处在于:
52.以固体推进剂质量为100%计,丁羟固体推进剂配方包括:粘合剂端羟基聚丁二烯9%,氧化剂高氯酸铵75%,金属燃烧剂al 12%,增塑剂癸二酸二辛酯3%,某磷酸键合剂0.05%,固化剂甲苯二异氰酸酯0.55%,防老剂n,n
’‑
二苯基对苯二胺、交联剂三-1-(2-甲基氮丙啶)氧化膦、燃速催化剂三苯基铋等其他组分0.4%。
53.s1、将所述丁羟粘合剂端羟基聚丁二烯、某磷酸键合剂、氧化剂高氯酸铵和40%的增塑剂癸二酸二辛酯加入声共振混合容器中,进行预混反应到预混物。声共振设置的预混程序具体包括:30g 1min;
②
60g 2min;
③
80g 2min。混合温度为60℃。
54.s2、在预混物中加入固化剂,60℃下进行再混合得到再混物。声共振设置的再混合程序为:60g 5min。
55.s3、想再混物中加入金属燃烧剂al、剩余增塑剂癸二酸二辛酯、固化催化剂甲苯二异氰酸酯、交联剂三-1-(2-甲基氮丙啶)氧化膦、防老剂n,n
’‑
二苯基对苯二胺、燃速催化剂三苯基铋等其他组分,按声共振设置的终混合程序继续混合至设定时间后出料,得到快速混合的推进剂物料。声共振设置的混合程序具体包括:30g 1min;
②
60g 4min;
③
80g 5min。
56.本实施例采用丁羟粘合剂,经浇注固化成型,制备的推进剂试样实物图如图7,推进剂样品致密无气孔,性能数据见表1。
57.对比例1
58.与实施例1的不同之处在于:
59.混合固体推进剂的方法包括:所有组分一起加入声共振混合容器。
60.设置混合工艺程序:30g进行2min;
②
60g进行8min;
③
80g进行8min;
④
30g进行2min。混合温度为60℃。
61.本实施例采取“一锅式”加料方式,经浇注固化成型,制备的推进剂样品实物图如图1,样品内部存在大量裂纹气孔,不满足应用要求。
62.对比例2
63.与实施例1的不同之处在于:
64.s1、将除了固化剂和氧化剂外其余组分(其他组分中包括金属燃烧剂铝粉)加入声共振混合容器中,预混反应直至混合混匀。声共振设置的预混程序具体包括:30g进行1min;
②
60g进行2min;
③
80g进行2min。混合温度为60℃。
65.s2、加入固化剂,60℃下混合均匀。声共振设置的预混程序为:60g进行5min。
66.s3、加入氧化剂,按声共振设置的混合程序继续混合至设定时间后出料,得到快速混合的推进剂物料。声共振设置的混合程序具体包括:30g进行1min;
②
60g进行4min;
③
80g进行5min。
67.本实施例采取传统的加料方式,经浇注固化成型,制备的推进剂样品实物图如图2,样品内部存在裂纹气孔,不满足应用要求。
68.对比例3
69.与实施例1的不同之处在于:
70.步骤s1中,将叠氮粘合剂、键合剂、氧化剂加入声共振混合容器中(不加入增塑剂),进行预混反应。
71.本实施例制备的推进剂样品致密无气孔,内部能看见白色细小的氧化剂颗粒,推进剂试样实物如图4,性能数据见表1。
72.对比例4
73.与实施例1的不同之处在于:
74.步骤s2中,加入固化剂后,常温下混合均匀。
75.本实施例在室温条件下混合,经浇注固化成型,制备的推进剂试样实物图如图6,试样内部存在裂纹气孔,不满足应用要求。
76.对比例5-传统混合-叠氮配方
77.与实施例1的不同之处在于:
78.(1)叠氮粘合剂、增塑剂、键合剂和固化催化剂加入立式混合器内,在60℃高温下进行预混反应直至混合混匀;(2)加入固化剂,并混合均匀;(3)加入燃速催化剂,并混合均匀;(4)加入其他添加剂,并混合均匀;(5)加入金属燃烧剂,并混合均匀;(6)分步加入氧化剂,并混合均匀;(7)出料。
79.整个过程的时间为120min。
80.对比例6-传统混合-丁羟配方
81.与实施例4的不同之处在于:
82.(1)粘合剂、增塑剂、键合剂和固化催化剂加入立式混合器内,在60℃高温下进行预混反应直至混合混匀;(2)加入固化剂,并混合均匀;(3)加入燃速催化剂,并混合均匀;(4)加入其他添加剂,并混合均匀;(5)加入金属燃烧剂,并混合均匀;(6)分步加入氧化剂,并混合均匀;(7)出料。
83.整个过程的时间为108min。
84.性能检测
85.燃烧性能测试:将固化成型的固体推进剂药块切成5
×5×
100mm的药条,测试温度为20℃。按照gjb 770b-2005方法706.2《然速水下声发射法》规定测试药条的燃速。
86.力学性能测试:按gjb 770b-2005方法413.1《最大拉伸强度、断裂强度、最大伸长率和断裂伸长率单向拉伸法》切成哑铃状型试件,测试温度分别为70℃、20℃和-40℃;高温拉伸速度为2mm/min;常、低温拉伸速度为100mm/min。
87.检测结果见表1。
88.表1性能检测结果
[0089][0090][0091]
抗拉强度与伸长率为衡量推进剂力学性能的两个指标,对于同一配方,一般抗拉强度升高,伸长率降低,反之亦然。传统立式混合(对比例5),叠氮推进剂常、高、低温的拉伸强度和断裂伸长率分别为1065kpa、59.6%;571kpa、38.8%;2949kpa、61%。在加入40%增塑剂的制备工艺下(实施例1),试样常、高、低温的拉伸强度和断裂伸长率分别为1028kpa、484%;756kpa、37.2%;2309kpa、60.9%,常温抗拉强度和伸长率低于立式混合高温抗拉强度提高、伸长率降低,低温伸长率相当,但低温抗拉强度降低。传统立式混合制备的叠氮推进剂7mpa燃速为10.19mm/s,实施例1燃速为10.22mm/s。比较对比例5、实施例1力学性能可知,加入部分增塑剂可制备力学性能良好的推进剂试样,其中常温力学性能低于立式混合,高温、低温力学性能与之相当;与对比例5相比,实施例1制备的试样燃速高出0.03mm/s,与立式混合样品燃速处于同一水平。
[0092]
实施例1和对比例2中,对比例1在步骤s1中先将其他组分(包括金属燃烧剂铝粉)与粘合剂、键合剂进行了混合,之后再与氧化剂和固化剂混合,而实施例1中,将氧化剂与粘合剂、键合剂一起进行混合,之后再与固化剂和其他组分(包括金属燃烧剂铝粉)混合,最终实施例1制得的试样各项力学性能和燃烧性能良好,而对比例2得到的试样存在明显裂纹气孔。是因为通过本技术的混合顺序,键合剂能够更均匀的包覆在氧化剂表面,键合反应进行更加充分。
[0093]
提高预混时加入增塑剂的配比(实施例2),常温抗拉强度明显提高,提高了502kpa,比立式混合试样提高了465kpa,伸长率略有降低;高温抗拉强度增大,伸长率降低;低温抗拉强度、伸长率均增大。试验表明,增加预混时增塑剂的加入配比,能够显著提高推进剂常温、低温环境下的抗拉强度和伸长率,实施例2低温力学性能比对比例5制备试样更优,燃速为10.21mm/s,与实施例10.22mm/s基本相当,且和传统立式混合测试结果(10.19mm/s)处于同一水平,燃烧性能相当。
[0094]
实施例1-2、对比例3中,步骤s1中,粘合剂、键合剂、氧化剂之间进行键合反应,而粘合剂、键合剂、氧化剂形成的体系粘度较大,增塑剂在不受s1中的加入降低了体系的粘度,提高步骤s1中加入组分混合的均匀性和混合效率;当增塑剂不加入或者加入较少时,键合剂在预混合过程中分散不均匀,常温、高温力学性能没有明显降低,但是在低温测试条件下最大伸长率为52.1%,断裂伸长率为27.7%,出现严重的低温“脱湿”现象,不满足应用要求。当加入增塑剂配比较少(加入增塑剂40%,实施例1)常温力学性能低于传统立式混合(对比例5),高温、低温力学性能与之相当,综合力学性能良好,满足应用要求;与对比例5相
比,实施例1制备的试样燃速高出0.03mm/s,与立式混合样品燃速处于同一水平。当加入足量增塑剂(加入增塑剂100%,实施例2)推进剂常温、低温环境下的抗拉强度和伸长率显著提高,实施例2低温力学性能比对比例5制备试样更优,燃速为10.21mm/s,与实施例10.22mm/s基本相当,且和传统立式混合测试结果(10.19mm/s)处于同一水平,燃烧性能相当,满足应用要求。
[0095]
实施例1、对比例4中,温度低于本技术限定的范围,对反应速度有影响,固化反应难以在有限的时间内达到推进剂所需程度,从而试样内部出现图6中的裂纹气孔,不满足应用要求;而温度过高,对于有着复杂化学反应的多组分体系的推进剂来说,安全性降低。但是在本技术限定的再混合温度范围内,固化反应进行迅速,且固化反应能够在较短的有限时间内进行到推进剂可以用的程度。先加入固化剂、后加入其他组分的混合顺序,有利于固化反应进行更加充分。
[0096]
由实施例1、对比例5、实施例3、对比例6可知,本技术的方法在粘合剂为丁羟粘合剂或者叠氮粘合剂时均适用;相对于传统混合方法,本技术的方法获得的推进剂产品综合力学性能与传统混合方法基本相当,其中低温力学性能明显优于传统立式混合制备试样,且对于叠氮、丁羟推进剂,声共振混合工艺制备试样的燃速均有所提高,燃烧性能稳定性更好。
[0097]
显然,本领域的技术人员可以对本发明进行各种改动和变形而不脱离本发明的精神和范围。这样,倘若本发明的这些修改和变型属于本发明权利要求及其等同技术的范围之内,则本发明也意图包含这些改动和变型在内。
再多了解一些
本文用于创业者技术爱好者查询,仅供学习研究,如用于商业用途,请联系技术所有人。