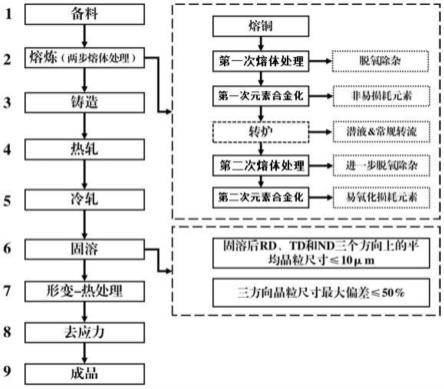
0.02%-0.1%、mg 0.05%-0.2%、fe 0.05%-0.2%、p 0.02%-0.06%、ti 0.02%-0.1%、余量为cu及不可避免的杂质元素。优选的,铜合金带材的组分及其质量百分含量为:cr 0.3%-0.6%、zr 0.04%-0.08%、mg 0.08%-0.15%、fe 0.08%-0.15%、p 0.02%-0.06%、ti 0.02%-0.06%、余量为cu及不可避免的杂质元素。铜合金带材的组分还包括m,m的质量百分含量小于0.5%;其中,m为la、ce、sn、zn、ni、si中的一种或几种,la的质量百分含量为0.02%-0.04%、ce的质量百分含量为0.02%-0.04%、sn的质量百分含量为0.02%-0.2%、zn的质量百分含量为0.02%-0.2%、ni的质量百分含量为0.02%-0.2%、si的质量百分含量为0.02%-0.2%。铜合金带材的抗拉强度达到595mpa-640 mpa、延伸率达到2%-5%、电导率达到80%-85%iacs、软化温度达到550℃-565℃。
32.参见图1,本发明的高性能铜合金带材的制备方法,包括以下步骤:
33.(1)备料:铜合金带材的组分中的cr、zr、mg、fe、p、ti分别采用cu-cr、cu-zr、cu-mg、cu-fe、cu-p、cu-ti中间合金形式添加,添加前需进行干燥和去除异物处理。按照铜合金带材的组分及其质量百分含量准备原料cu、cu-cr、cu-zr、cu-mg、cu-fe、cu-p、cu-ti、m,m为la、ce、sn、zn、ni、si中的一种或几种,将原料进行干燥和去除异物处理;原料cu为工业纯铜。
34.(2)熔炼:将原料cu装入感应熔炼装置进行熔化后,再添加步骤(1)中的其他原料,得到铜合金熔体。熔炼装置为非真空感应熔炼装置。
35.铜合金熔体的制备过程包括两次熔体处理、两次合金化,具体步骤如下:将原料cu装入感应熔炼装置进行熔化后依次进行第一次熔体处理、脱氧除杂,得到除杂后的铜熔体;将cr、fe等非易损耗难熔金属元素通过原料cu-cr、cu-fe形式加入到除杂后的铜熔体中再进行第一次合金化,得到添加cr、fe的中间熔体;根据实际设备情况确定是否需要转炉,转炉方式一般有潜液转流和常规倾倒式转炉;转入保温炉后进行第二次熔体处理,通过添加mg、p等元素进一步降低熔体中的氧含量:当需要添加原料m时,将原料m、cu-mg、cu-p加入到添加cr、fe的中间熔体中进行第二次熔体处理,得到添加cr、fe、mg、p的中间熔体;最后进行易氧化损耗zr、ti元素的合金化:将原料cu-zr、cu-ti加入到添加cr、fe、mg、p的中间熔体中进行第二次合金化,得到铜合金熔体。添加原料m时,la、ce分别采用cu-la、cu-ce中间合金形式添加,sn、zn、ni、si采用纯金属形式添加。
36.将原料cu装入感应熔炼装置进行熔化后依次进行第一次熔体处理、脱氧除杂时,采用木炭、鳞片石墨、惰性气体中的一种或两种组合进行脱氧除杂,除杂后的铜熔体中氧含量降低至50ppm以下;通过添加mg、p、稀土(la、ce)等元素进一步降低熔体中的氧含量,将添加cr、fe、mg、p的中间熔体中氧含量降低至30ppm以下。
37.(3)铸造:将铜合金熔体进行铸造,获得铜合金铸坯;铸造温度为1150℃-1280℃。
38.(4)热轧:将铜合金铸坯进行加热热轧和在线淬火,得到铜合金热轧带坯;加热热轧的温度为900℃-960℃、保温时间为2h-5h,在线淬火的温度为700℃-800℃。
39.(5)冷轧:将铜合金热轧带坯进行铣面和冷轧,得到铜合金冷轧带坯;冷轧总变形量≥85%。
40.(6)固溶:将铜合金冷轧带坯进行在线固溶淬火处理,得到铜合金固溶带坯;在线固溶淬火处理的温度为800℃-980℃、时间为1min-5min;铜合金固溶带坯在轧向、横向和轧面法向三个方向上的平均晶粒尺寸≤10μm,并且轧向、横向和轧面法向三个维度晶粒尺寸
最大偏差≤50%。
41.(7)形变-热处理:将铜合金固溶带坯进行冷轧、时效处理,得到满足成品性能和厚度规格要求的铜合金带坯;冷轧、时效处理的具体步骤为:将铜合金固溶带坯进行一次冷轧,得到一次冷轧后的带坯,一次冷轧的变形量为50%-80%;将一次冷轧后的带坯进行一级时效处理,得到一级时效处理后的带材,一级时效处理的温度为400℃-550℃、时间为2h-8h;将一级时效处理后的带材依次进行二次冷轧、二级时效处理、三次冷轧,得到铜合金带坯,二次冷轧的变形量为30%-70%,三次冷轧的变形量为20%-60%,二级时效处理的温度为400℃-480℃、时间为2h-4h。
42.(8)去应力处理:去应力处理包含低温张力退火和拉弯矫直处理。将铜合金带坯进行张力退火和拉弯矫直处理,获得铜合金带材成品。将铜合金带坯进行张力退火的工艺条件为:将铜合金带坯在300℃-450℃下进行30-200秒的低温张力退火。
43.以下结合实施例对本发明具体实施方式进行详细的说明。
44.实施例1
45.(1)备料:根据铜合金带材的成分要求准备原料,采用的主原料为工业纯铜以及中间合金cu-10wt%cr、cu-15wt%zr、cu-10wt%mg、cu-10wt%fe、cu-15wt%ti和cu-14wt%p;采用的其他原料为cu-10wt%la和纯金属sn;并对所有原料进行相应的干燥和去除异物处理。
46.实施例1的铜合金带材的成分及其含量见表1。
47.(2)熔炼:将原料工业纯铜装入感应熔炼炉进行熔化,对熔体进行两步熔体处理,具体步骤为:将铜熔化后进行第一次熔体处理,采用木炭覆盖和熔体中通入惰性气体两种组合方式脱氧除气,将氧含量降低至47ppm;再进行第一次合金化,添加cu-10wt%cr、cu-10wt%fe和金属sn等非易损耗金属元素;将熔体潜液转炉至保温炉,进行第二次熔体处理,通过添加cu-10wt%mg、cu-14wt%p和cu-10wt%la进一步降低熔体中的氧含量至28ppm;最后进行第二次合金化,分散添加cu-15wt%zr和cu-15wt%ti,调整成分得到所需的铜合金熔体。
48.(3)铸造:对步骤(2)所得铜合金熔体进行铸造,铸造温度为1170℃,获得210
×
620mm规格的铜合金铸坯。
49.(4)热轧:对步骤(3)所得铜合金铸坯进行热轧和在线淬火,其中,热轧加热温度为900℃、保温时间为2h,在线淬火温度为705℃,获得厚度为15mm的铜合金热轧带坯。
50.(5)冷轧:对步骤(4)所得铜合金热轧带坯进行铣面和冷轧,冷轧总变形量为88%,获得厚度为1.7mm的铜合金冷轧带坯。
51.(6)固溶:对步骤(5)所得铜合金冷轧带坯,在800℃的加热温度下进行5分钟的在线固溶淬火处理,固溶处理后带坯在rd、td和nd三个方向上的平均晶粒尺寸分别为6.6μm、7.8μm和9.6μm,且三个维度晶粒尺寸最大偏差为45%。
52.(7)形变-热处理:对步骤(6)所得铜合金固溶带坯进行一次冷轧,冷轧变形量为80%,一次冷轧后的带坯进行一级时效处理,温度为400℃、时间为8h;将一级时效处理后的带材进行二次冷轧,变形量为30%,然后进行二级时效处理,温度为400℃、时间为2h;二级时效后的带坯进行三次冷轧,变形量为50%,获得厚度为0.127mm的铜合金带坯。
53.(8)去应力处理:对步骤(7)所得铜合金带坯进行低温张力退火和拉弯矫直等处
理,将铜合金带坯在300℃的加热温度下进行180秒的低温张力退火,退火后的带材进行拉弯矫直,得到高性能铜合金带材成品。实施例1采用的主要制备工艺参数件表2,实施例1得到的高性能铜合金带材成品的性能见表3。
54.实施例2
55.(1)备料:根据铜合金带材的成分要求准备原料,采用的主原料为工业纯铜以及中间合金cu-10wt%cr、cu-15wt%zr、cu-10wt%mg、cu-10wt%fe、cu-15wt%ti和cu-14wt%p;采用的其他原料为cu-10wt%ce和纯金属si;并对所有原料进行相应的干燥和去除异物处理。实施例2的铜合金带材的成分及其含量见表1。
56.(2)熔炼:将原料工业纯铜装入感应熔炼炉进行熔化,对熔体进行两步熔体处理,具体步骤为:将铜熔化后进行第一次熔体处理,采用鳞片石墨覆盖和熔体中通入惰性气体两种方式组合脱氧除气,将氧含量降低至40ppm;再进行第一次合金化1,添加cu-10wt%cr、cu-10wt%fe和金属si等非易损耗难熔金属元素;将熔体倾翻转炉至保温炉,进行第二次熔体处理,通过添加cu-10wt%mg、cu-14wt%p和cu-10wt%ce进一步降低熔体中的氧含量至22ppm;最后进行第二次合金化,分散添加cu-15wt%zr和cu-15wt%ti,调整成分得到所需的铜合金熔体。
57.(3)铸造:对步骤(2)所得铜合金熔体进行铸造,铸造温度为1210℃,获得210
×
620mm规格的铜合金铸坯。
58.(4)热轧:对步骤(3)所得铜合金铸坯进行热轧和在线淬火,其中,热轧加热温度为920℃、保温时间为3h,在线淬火温度为708℃,获得厚度为15mm的铜合金热轧带坯。
59.(5)冷轧:对步骤(4)所得铜合金热轧带坯进行铣面和冷轧,冷轧总变形量为90%,获得厚度为1.4mm的铜合金冷轧带坯。
60.(6)固溶:对步骤(5)所得铜合金冷轧带坯,在850℃的加热温度下进行4分钟的在线固溶淬火处理,固溶处理后带坯在rd、td和nd三个方向上的平均晶粒尺寸分别为6.7μm、7.5μm和8.9μm,且三个维度晶粒尺寸最大偏差为33%。
61.(7)形变-热处理:对步骤(6)所得铜合金固溶带坯进行一次冷轧,冷轧变形量为70%,一次冷轧后的带坯进行一级时效处理,温度为450℃、时间为6h;将一级时效处理后的带材进行二次冷轧,变形量为50%,然后进行二级时效处理,温度为420℃、时间为4h;二级时效后的带坯进行三次冷轧,变形量为37%,获得厚度为0.127mm的铜合金带坯。
62.(8)去应力处理:对步骤(7)所得铜合金带坯进行低温张力退火和拉弯矫直等处理,将铜合金带坯在350℃的加热温度下进行120秒的低温张力退火,退火后的带材进行拉弯矫直,得到高性能铜合金带材成品。实施例2采用的主要制备工艺参数件表2,实施例2得到的高性能铜合金带材成品的性能见表3。
63.实施例3
64.(1)备料:根据铜合金带材的成分要求准备原料,采用的主原料为工业纯铜以及中间合金cu-10wt%cr、cu-15wt%zr、cu-10wt%mg、cu-10wt%fe、cu-15wt%ti和cu-14wt%p;采用的其他原料为纯金属ni和si;并对所有原料进行相应的干燥和去除异物处理。实施例3的铜合金带材的成分及其含量见表1。
65.(2)熔炼:将原料工业纯铜装入感应熔炼炉进行熔化,对熔体进行两步熔体处理,具体步骤为:将铜熔化后进行第一次熔体处理,采用木炭覆盖和熔体中通入惰性气体两种
组合方式脱氧除气,将氧含量降低至35ppm;再进行第一次合金化,添加cu-10wt%cr、cu-10wt%fe和金属ni、si等非易损耗难熔金属元素;将熔体潜液转炉至保温炉,进行第二次熔体处理,通过添加cu-10wt%mg和cu-14wt%p进一步降低熔体中的氧含量至18ppm;最后进行第二次合金化,分散添加cu-15wt%zr和cu-15wt%ti,调整成分得到所需的铜合金熔体。
66.(3)铸造:对步骤(2)所得铜合金熔体进行铸造,铸造温度为1230℃,获得210
×
620mm规格的铜合金铸坯。
67.(4)热轧:对步骤(3)所得铜合金铸坯进行热轧和在线淬火,其中,热轧加热温度为930℃、保温时间4h,在线淬火温度为712℃,获得厚度为15mm的铜合金热轧带坯。
68.(5)冷轧:对步骤(4)所得铜合金热轧带坯进行铣面和冷轧,冷轧总变形量为92%,获得厚度为1.1mm的铜合金冷轧带坯。
69.(6)固溶:对步骤(5)所得铜合金冷轧带坯,在900℃的加热温度下进行3分钟的在线固溶淬火处理,固溶处理后带坯在rd、td和nd三个方向上的平均晶粒尺寸分别为5.8μm、6.6μm和7.8μm,且三个维度晶粒尺寸最大偏差为34%。
70.(7)形变-热处理:对步骤(6)所得铜合金固溶带坯进行一次冷轧,冷轧变形量为60%,一次冷轧后的带坯进行一级时效处理,温度为480℃、时间为5h;将一级时效处理后的带材进行二次冷轧,变形量为40%,然后进行二级时效处理,温度为450℃、时间为3h;二级时效后的带坯进行三次冷轧,变形量为50%,获得厚度为0.127mm的铜合金带坯。
71.(8)去应力处理:对步骤(7)所得铜合金带坯进行低温张力退火和拉弯矫直等处理,将铜合金带坯在400℃的加热温度下进行80秒的低温张力退火,退火后的带材进行拉弯矫直,得到高性能铜合金带材成品。实施例3采用的主要制备工艺参数件表2,实施例3得到的高性能铜合金带材成品的性能见表3。
72.实施例4
73.(1)备料:根据铜合金带材的成分要求准备原料,采用的主原料为工业纯铜以及中间合金cu-10wt%cr、cu-15wt%zr、cu-10wt%mg、cu-10wt%fe、cu-15wt%ti和cu-14wt%p;采用其他原料为纯金属zn;并对所有原料进行相应的干燥和去除异物处理。实施例4的铜合金带材的成分及其含量见表1。
74.(2)熔炼:将原料工业纯铜装入感应熔炼炉进行熔化,对熔体进行两步熔体处理,具体步骤为:将铜熔化后进行第一次熔体处理,采用鳞片石墨覆盖和熔体中通入惰性气体两种组合方式脱氧除气,将氧含量降低至38ppm;再进行第一次合金化,添加cu-10wt%cr和cu-10wt%fe等非易损耗难熔金属元素;将熔体潜液转炉至保温炉,进行第二次熔体处理,通过添加cu-10wt%mg、cu-14wt%p和纯金属zn进一步降低熔体中的氧含量至19ppm;最后进行第二次合金化,分散添加cu-15wt%zr和cu-15wt%ti,调整成分得到所需的铜合金熔体。
75.(3)铸造:对步骤(2)所得铜合金熔体进行铸造,铸造温度为1250℃,获得210
×
620mm规格的铜合金铸坯。
76.(4)热轧:对步骤(3)所得铜合金铸坯进行热轧和在线淬火,其中,热轧加热温度为940℃、保温时间为4h,在线淬火温度为718℃,获得厚度为15mm的铜合金热轧带坯。
77.(5)冷轧:对步骤(4)所得铜合金热轧带坯进行铣面和冷轧,冷轧总变形量为92%,获得厚度为1.1mm的铜合金冷轧带坯。
78.(6)固溶:对步骤(5)所得铜合金冷轧带坯,在940℃的加热温度下进行3分钟的在线固溶淬火处理,固溶处理后带坯在rd、td和nd三个方向上的平均晶粒尺寸分别为6.0μm、7.3μm和8.1μm,且三个维度晶粒尺寸最大偏差为35%。
79.(7)形变-热处理:对步骤(6)所得铜合金固溶带坯进行一次冷轧,冷轧变形量为60%,一次冷轧后的带坯进行一级时效处理,温度为495℃、时间为5h;将一级时效处理后的带材进行二次冷轧,变形量为40%,然后进行二级时效处理,温度为450℃、时间为3h;二级时效后的带坯进行三次冷轧,变形量为50%,获得厚度为0.127mm的铜合金带坯。
80.(8)去应力处理:对步骤(7)所得铜合金带坯进行低温张力退火和拉弯矫直等处理,将铜带在400℃的加热温度下进行80秒的低温张力退火,退火后的带材进行拉弯矫直,得到高性能铜合金带材成品。实施例4采用的主要制备工艺参数件表2,实施例4得到的高性能铜合金带材成品的性能见表3。
81.实施例5
82.(1)备料:根据铜合金带材的成分要求准备原料,采用的主原料为工业纯铜以及中间合金cu-10wt%cr、cu-15wt%zr、cu-10wt%mg、cu-10wt%fe、cu-15wt%ti和cu-14wt%p;采用的其他原料为cu-10wt%la和纯金属zn;并对所有原料进行相应的干燥和去除异物处理。实施例5的铜合金带材的成分及其含量见表1。
83.(2)熔炼:将原料工业纯铜装入感应熔炼炉进行熔化,对熔体进行两步熔体处理,具体步骤为:将铜熔化后进行第一次熔体处理,采用木炭覆盖和熔体中通入惰性气体两种组合方式脱氧除气,将氧含量降低至42ppm;再进行第一次合金化,添加cu-10wt%cr和cu-10wt%fe等非易损耗金属元素;将熔体潜液转炉至保温炉,进行第二次熔体处理,通过添加cu-10wt%mg、cu-14wt%p、cu-10wt%la和纯金属zn进一步降低熔体中的氧含量至25ppm;最后进行第二次合金化,分散添加cu-15wt%zr和cu-15wt%ti,调整成分得到所需的铜合金熔体。
84.(3)铸造:对步骤(2)所得铜合金熔体进行铸造,铸造温度为1280℃,获得210
×
620mm规格的铜合金铸坯。
85.(4)热轧:对步骤(3)所得铜合金铸坯进行热轧和在线淬火,其中,热轧加热温度为960℃、保温时间为5h,在线淬火温度为722℃,获得厚度为15mm的铜合金热轧带坯。
86.(5)冷轧:对步骤(4)所得铜合金热轧带坯进行铣面和冷轧,冷轧总变形量为94%,获得厚度为0.8mm的铜合金冷轧带坯。
87.(6)固溶:对步骤(5)所得铜合金冷轧带坯,在980℃的加热温度下进行2分钟的在线固溶淬火处理,固溶处理后带坯在rd、td和nd三个方向上的平均晶粒尺寸分别为6.56μm、7.5μm和8.6μm,且三个维度晶粒尺寸最大偏差为32%。
88.(7)形变-热处理:对步骤(6)所得铜合金固溶带坯进行一次冷轧,冷轧变形量为50%,一次冷轧后的带坯进行一级时效处理,温度为530℃、时间为3h;将一级时效处理后的带材进行二次冷轧,变形量为60%,然后进行二级时效处理,温度为480℃、时间为2h;二级时效后的带坯进行三次冷轧,变形量为20%,获得厚度为0.127mm的铜合金带坯。
89.(8)去应力处理:对步骤(7)所得铜合金带坯进行低温张力退火和拉弯矫直等处理,将铜带在450℃的加热温度下进行40秒的低温张力退火,退火后的带材进行拉弯矫直,得到高性能铜合金带材成品。实施例5采用的主要制备工艺参数件表2,实施例5得到的高性
能铜合金带材成品的性能见表3。
90.对比例1
91.(1)备料:根据铜合金带材的成分要求准备原料,采用的主原料为工业纯铜以及中间合金cu-10wt%cr、cu-15wt%zr;并对所有原料进行相应的干燥和去除异物处理。对比例1的铜合金带材的成分及其含量见表1。
92.(2)熔炼:将原料工业纯铜装入感应熔炼炉进行熔化,对熔体进行两步熔体处理,具体步骤为:将铜熔化后进行熔体处理,采用木炭覆盖和熔体中通入惰性气体两种组合方式脱氧除气,将氧含量降低至46ppm;再进行第一次合金化,添加cu-10wt%cr;将熔体潜液转炉至保温炉,因无金属脱氧,仅测试熔体中的氧含量78ppm;进行第二次合金化,分散添加cu-15wt%zr,调整成分得到所需的铜合金熔体。
93.(3)铸造:对步骤(2)所得铜合金熔体进行铸造,铸造温度为1250℃,获得210
×
620mm规格的铜合金铸坯。
94.(4)热轧:对步骤(3)所得铜合金铸坯进行加热热轧和在线淬火,其中,热轧加热温度为920℃、保温时间为3h,在线淬火温度为710℃,获得厚度为15mm的铜合金热轧带坯。
95.(5)冷轧:对步骤(4)所得铜合金热轧带坯进行铣面和冷轧,冷轧总变形量为90%,获得厚度为1.4mm的铜合金冷轧带坯。
96.(6)固溶:对步骤(5)所得铜合金冷轧带坯,在900℃的加热温度下进行3分钟的在线固溶淬火处理,固溶处理后带坯在rd、td和nd三个方向上的平均晶粒尺寸分别为12.7μm、15.3μm和26μm,平均晶粒尺寸>10μm,且三个维度晶粒尺寸最大偏差为105%,晶粒尺寸最大偏差>50%。
97.(7)形变-热处理:对步骤(6)所得铜合金固溶带坯进行一次冷轧,冷轧变形量为60%,一次冷轧后的带坯进行一级时效处理,温度为480℃、时间为5h;将一级时效处理后的带材进行二次冷轧,变形量为50%,然后进行二级时效处理,温度为450℃、时间为3h;二级时效后的带坯进行三次冷轧,变形量为40%,获得厚度为0.127mm的铜合金带坯。
98.(8)去应力处理:对步骤(7)所得铜合金带坯进行低温张力退火和拉弯矫直等处理,将铜带在400℃的加热温度下进行80秒的低温张力退火,退火后的带材进行拉弯矫直,得到高性能铜合金带材成品。对比例1采用的主要制备工艺参数件表2,对比例1得到的高性能铜合金带材成品的性能见表3。
99.对比例2
100.与对比例1相比,铜合金带材的中间合金元素增加了mg元素,对比例2的铜合金带材的成分及其含量见表1;第二次合金化前熔体中氧含量维持在49ppm;在900℃的加热温度下进行3分钟的在线固溶淬火处理,固溶处理后带坯在rd、td和nd三个方向上的平均晶粒尺寸分别为10.5μm、12.8μm和19μm,平均晶粒尺寸>10μm,且三个维度晶粒尺寸最大偏差为81%,晶粒尺寸最大偏差>50%。其余工艺与对比例1相同。对比例2采用的主要制备工艺参数件表2,对比例2得到的高性能铜合金带材成品的性能见表3。
101.表1实施例和对比例铜合金带材成分表
[0102][0103]
表2实施例和对比例采用的主要制备工艺参数
[0104][0105]
表3实施例及对比例的铜合金带材成品性能表
[0106][0107]
以上所述仅是本发明的较佳实施例,并不局限本发明。应当指出对于本领域的普通技术人员来说,在本发明所提供的技术启示下,还可以做出其它等同改进,均可以实现本发明的目的,都应视为本发明的保护范围。
再多了解一些
本文用于创业者技术爱好者查询,仅供学习研究,如用于商业用途,请联系技术所有人。