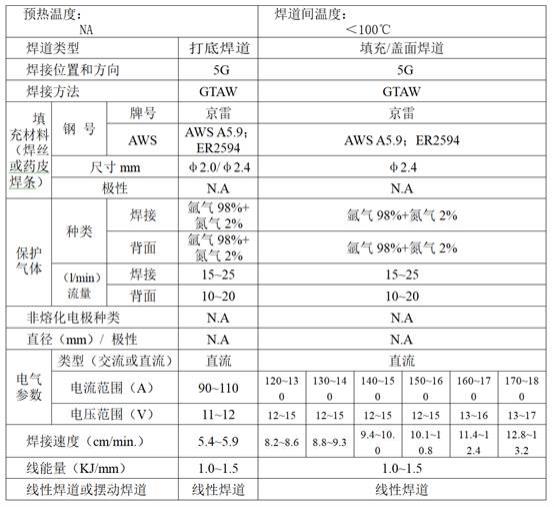
1.本发明属于焊接技术领域,尤其涉及一种超级双相钢工艺管道手工钨极氩弧焊接工艺方法。
背景技术:
2.超级双相钢asme sa-240m s32750的焊缝质量要求较高,对于焊缝焊接期间氢来源、道间/层间温度、焊接热输入控制要求严格。超级双相钢由于合金含量较高,焊缝热影响区及多层多道焊的焊缝金属容易析出σ相、x相、氧化物、氮化物以及金属间化合物,造成接头焊缝金属及热影响区耐腐蚀性能及塑韧性大幅度下降。
3.这种材质的焊缝目前采用手弧焊单面焊双面成型技术,虽然可以保证焊接质量,但是,由于手弧焊有飞溅,容易造成超级双相钢asme sa-240m s32750母材外表面以及坡口面形成熔合性飞溅,打磨飞溅后疤痕处铁素体含量偏低,耐腐蚀性能下降,适用范围受到限制。而钨极氩弧焊由于没有飞溅,且热量集中,熔深大,焊接质量稳定,因此成为超级双相钢asme sa-240m s32750接头焊缝打底层、填充及盖面层焊接的首选焊接工艺方法。
4.传统超级双相钢asme sa-240m s32750接头焊缝手工钨极氩弧焊工艺,焊缝组对间隙小,甚至无间隙,焊接操作要求焊工保持弧长稳定,直进式、走直线,实际焊接往往出现电弧在坡口两边停留时间不均匀,电弧长度不稳定,焊缝轴线不直,外观成型不良、未融合、气孔甚至根部未焊透等缺陷;熔敷顺序和方向不合理;焊接期间没有严格控制外界氢来源措施;也不重视控制道间温度及热输入的下限值和上限值,造成焊缝熔覆金属及热影响区母材铁素体含量值不均匀或不合格,耐腐蚀性能严重下降。
技术实现要素:
5.本发明所要解决的技术问题是:提供一种超级双相钢工艺管道手工钨极氩弧焊接工艺方法,利用该焊接工艺方法焊接超级双相钢asme sa-240m s32750焊缝时,焊缝成型美观,焊纹均匀,道间温度、焊接热输入量处于可控范围内,焊缝熔覆金属及热影响区母材铁素体含量值稳定,焊缝熔覆金属组织致密,焊接操作难度低。
6.为解决上述技术问题,本发明的技术方案是:一种超级双相钢工艺管道手工钨极氩弧焊接工艺方法,该焊接工艺方法用于两根牌号为asme sa-240m s32750的管材之间焊接或者两块牌号为asme sa-240m s32750的板材之间焊接,包括以下分步骤:a、焊前准备,包括以下分步骤:a1)确定焊接执行标准;a2)确定管材或板材的规格、牌号,焊材规格、牌号及保护气体的执行标准;a3)选择工具及配件;a4)管材或板材及工具和机器的验收检查;a5)对管材或板材进行划线并进行尺寸检查;a6)对管材或板材切割下料,切口端面与管材轴线或者切口与板材的板面的垂直
度符合标准规定要求;a7)对需焊接的管材或板材的切口端面冷加工坡口;其中管材或板材的壁厚小于等于21.95mm时,坡口角度为单边30
°‑
32
°
,钝边为0-1mm ;当管材或板材壁厚大于21.95mm时,坡口机加工成根部为r=8 mm的u型阶梯坡口,该u型阶梯坡口包括根部为r=8 mm的圆弧坡口面,圆弧坡口面的上方依次为第一坡口平面和第二坡口平面,所述第一坡口平面的坡口角度为20
°±2°
,第二坡口平面的坡口角度为10
°±2°
,所述第一坡口平面与第二坡口平面相连的位置与内表面之间的厚度范围为18-20mm,根部钝边为1-2mm;a8)将坡口面及内外表面20mm范围内杂物用丙酮清除干净,露出金属光泽;a9)检查管材内部或板材背面的保护气体装置运行是否符合工艺要求;b、将需要焊接的管材或者板材进行组对,包括以下分步骤:b1)确认组对用的工装卡具与母材材质相同或同组别,点固块材质与母材材质相同;b2)将管材或者板材进行组对并将保护气体室进行装配;b3)检查组对管材同轴度符合标准要求;b4)检查组对管材的内错边小于壁厚的10%,且小于等于1mm;检查组对板材的错边小于壁厚的10%,且小于等于1mm;c、将管材或板材的坡口焊缝进行点固焊:d、焊前对外界客观因素进行检查;e、坡口焊缝焊接:先焊接打底层焊缝两层,再焊接填充层及盖面层;e1)管材坡口打底层焊缝焊接方法包括以下分步骤:e11)确定打底焊的起弧点、施焊位置和施焊方向:采用手工钨极氩弧焊进行焊接,直流正接,左焊法,线性焊道,压道焊;具体的确定内容如下:e111)当管材采用水平固定焊接方式进行打底焊时,采用立向上焊接,对称焊,按照管道的圆周截面划分,将底部位置定义为六点位置,将顶部位置定义为十二点位置,并按照钟表刻度划分对称段,施焊方向为六点
→
三点
→
十二点;六点
→
九点
→
十二点,并将焊接时行进方向定义为前;起弧点为六点位置,起始施焊位置取在距离起弧点后侧5-30mm的位置,对称焊;e112)当管材采用水平转动焊接方式进行打底焊时,按照管道的圆周截面划分,将底部位置定义为六点位置,将顶部位置定义为十二点位置;将焊接时行进方向定义为前;采用逆时针方向左焊法施焊,起弧点为一点三十的位置,起始施焊位置取在距离起弧点后侧5-30mm的位置;e113)当管材采用横焊位置方式进行打底横焊时,将焊接时行进方向定义为前,采用逆时针方向左焊法施焊,在起弧点起弧,起始施焊位置取在起弧点后侧5-30mm位置,对称焊;e114)当板材采用平焊方式进行打底焊时,将焊接时行进方向定义为前,采用从中间向两边分段对称跳焊;e115)当板材采用横焊方式进行打底焊时,将焊接时行进方向定义为前,采用从中间向两边分段对称跳焊;e12)对坡口进行打底层焊缝焊接,打底焊共焊2层,每层一道,线性焊道,道间接头
错开大于20mm;e2)坡口的填充层和盖面层焊接;e21)填充层和盖面层的每道焊缝熔覆金属按照打底焊的施焊方向施焊;线性焊道,压道焊,多层多道焊;熔池在坡口面两边停留时间比在焊缝中间停留时间长,每道焊缝宽度不超过焊材钢芯直径的3倍,后一道的熔覆金属接头与前一层和前一道熔覆金属的接头错开大于20mm,收弧填满弧坑,收弧处缺陷和道间的成型不良缺陷及时清理;e22)确定焊接工艺参数满足以下要求:焊接期间每道焊缝电弧起弧前,待道间温度≤100℃时再进行起弧焊接;当焊接电流120-130a,焊接电压12-15v时,焊接速度8.2-8.6cm/min;当焊接电流130-140a,焊接电压12-15v时,焊接速度8.8-9.3cm/min;当焊接电流140-150a,焊接电压12-15v时,焊接速度9.4-10cm/min;当焊接电流150-160a,焊接电压12-15v时,焊接速度8.2-8.6cm/min;当焊接电流160-170a,焊接电压13-16v时,焊接速度11.4-12.4cm/min;当焊接电流170-180a,焊接电压13-17v时,焊接速度12.8-13.2cm/min;正面保护气体流量15-25l/min;背面保护气体流量10-20l/min;每道焊缝热输出控制在1000j/mm至1500j/mm之间;e3)整个焊接过程中,起初焊枪磁嘴下部支撑在根部两边坡口面上,以此为支点,握紧焊把,手腕做均匀圆弧运动,带动焊把钨丝压帽轴向与支点的切线之间在70
°
~85
°
范围内,以磁嘴支点为顶点,钨极圧帽及氩弧弧柱做圆锥摆动和前进;随着焊缝的成形,磁嘴下部转而以红热的焊缝表面为支撑平稳的前移,焊缝根部的内凸高度控制在0-2mm范围内,仰焊部位焊丝端头送到坡口的根部,水平固定焊口从立上坡到平焊位置焊丝端头只给进到熔池边缘;e4)焊缝接头时的焊接方式为:从接头位置前10-20mm左右的坡口内起弧,然后向后移到接头缓坡位置上部,电弧在坡口两边停留时间比焊缝中间长以保证两边熔合,待熔池形成后,控制熔池大小逐渐给丝,铁水填满熔池两边熔合线边缘,然后向前移动使熔池前移,收弧电流衰减前填满弧坑;焊接完成完整的每道焊缝或者每层焊缝后,在熔覆金属表面随机选取三个位置测量铁素体值,铁素体值要求控制在40%-60%范围内;f、焊接过程中对焊接的各客观因素进行检查;g、焊后检查。
7.其中优选的,所述步骤b2将管材或者板材进行组对,包括以下分步骤:b21)背面保护气体室的装配:b211)管材的保护气体室的装配:在管材焊缝两边距离焊缝300-400mm的管内壁分别安装一块进气堵板和一块出气堵板,进气堵板的中心和出气堵板的中心之间由钢丝和拉簧连接,进气堵板上还连接有钢丝和进气管,进气管设置在进气堵板六点附近的低点位置,出气堵板上设置有出气管,该出气管设置在出气堵板十二点附近的高点位置;b212)板材的背面保护气体室的装配:在板材的焊缝背面安装固定一个保护气体储槽,保护气体储槽的材质与母材相同,该保护气体储槽的一端为进气端板且低处设进气管,另一端为出气端板且高处设出气管,该进气管贯穿进气端板且一端伸入到保护气体槽内并用封板焊接密封,进气管与进气端板角焊缝密封焊,处于保护气体槽内的进气管上均匀布置φ1-φ2mm的出气孔,进气管上方覆盖厚度大于30mm的蓬松状金属丝,蓬松状金属丝表面覆盖有20-30目的金属网,该金属网固定在保护气体储槽内壁上,金属网距离母材焊缝
坡口根部的距离大于30mm,该保护气体储槽边缘与焊缝母材之间固定后的缝隙,用无卤素污染的粘胶带封堵;b22)坡口焊缝的组对,包括以下步骤:b221)针对母材为管材的情况:当选择水平固定焊接方式进行焊接时,坡口焊缝组对的方式如下:管径d≤φ168.3mm时,管材钟点位置六点处的组对间隙为2.4-3.2mm,十二点处的组对间隙大于3.2-4.0mm;当d>φ168.3mm时,管材钟点位置六点处的组对间隙为3.2-4.0mm,十二点处的组对间隙大于3.2-4.0mm;当选择水平转动焊接方式或者横焊方式时,坡口焊缝组对间隙均匀且为3.2-4.0mm;b222)针对母材为板材的情况,当选择平焊方式进行焊接时,坡口焊缝组对间隙大于3.2-4.0mm; 当选择横焊方式进行焊接时,坡口焊缝组对间隙均匀且为3.2-4.0mm。
8.其中优选的,所述步骤c包括以下分步骤:c1)确定组对固定方式,选用点固块组对固定;c2)对于管材选用点固块组对固定时,点固块避开管材钟点位置的三、六、九、十二点位置,当管径d≤φ168.3mm时,点固块的数目为1-3个,且均布于避开点以外的管材圆周坡口面上;当管径d>φ168.3mm时,将焊缝圆周分为对称的2(n 2)段,其中n>1,点固块的数目2(n 2)-4个,其中n>1,且均布于避开点以外的管材圆周坡口面上;对于板材选用点固块组对固定时,点固块从焊缝长度的中点向两边均布,两点固块之间距离300-500mm;c3)检查点固焊缝质量:点固块两边点固焊缝厚度2-8mm,长度5-45mm,点固焊缝落在坡口面与点固块之间;c4)点固焊接完成后,用无卤素污染的粘胶带封堵坡口间隙,保护气体室焊前充气至排尽杂气。
9.其中优选的,所述步骤e12对坡口进行打底层焊缝焊接的具体步骤为:e121)焊钳手把线跨过手臂后右手握住,从起弧点起弧,向后移动到起始施焊位置开始施焊;e122)以水平固定焊接方式对管材坡口打底层焊缝焊接:e1221)对于管径d≤φ168.3mm,打底层焊缝仅需要分为对称的两段圆弧,一段以六点
→
三点
→
十二点,另一段以六点
→
九点
→
十二点所示的移动方向进行对称施焊;起弧前从起弧点将粘胶带撕掉一个小口;当以六点
→
三点
→
十二点的移动方向施焊时,在六点后面10-20mm的位置,用电弧从间隙的中间位置打穿钝边形成熔孔,熔化的铁水充盈在熔孔下部,熔孔上移,铁水冷却形成单面焊双面成型的打底焊缝,打底焊缝向前延伸遇到点固块前收弧,打磨清除点固块将焊缝端头打磨成缓坡形,在焊缝端头前10-20mm位置起弧,然后电弧移动到端头的缓坡接头,焊缝熔覆金属继续向三点和十二点方向延伸,在十二点附近收弧,形成第一段打底焊熔敷金属焊道;再以同样的焊接方式以六点
→
九点
→
十二点的移动方向施焊,在第一段打底焊熔敷金属焊道起焊端头前10-20mm位置起弧,再把电弧移到起焊端头的缓坡进行接头,然后向九点和十二点方向焊接,与第一段打底焊熔敷金属焊道收弧点进行接头,形成第二段打底
焊熔敷金属焊道;e1222)对于管径d>φ168.3mm,采用分段对称焊接方法;其中,将焊缝圆周分为对称的2(n 2)段,其中n>1,从而形成了若干对中心对称的焊缝段;先从六点位置起弧后向九点方向移动,电弧后移10-20mm位置开始施焊,采用立向上焊接形成第一段打底焊熔敷金属焊道,在焊接的过程中若遇到点固块则在点固块前10mm收弧,打磨清除点固块,将第一段打底焊熔敷金属焊道的两个端头打磨成缓坡形;相对称的,以六点
→
三点
→
十二点移动方向施焊,在与第一段打底焊熔覆金属焊道收弧端头缓坡中心对称的位置附近撕开粘胶带小口起弧,待电弧稳定燃烧之后,再向后移动5-10mm开始焊接,熔池再向十二点位置移动,在与第一段打底焊熔覆金属焊道起弧端中心对称位置附近收弧,形成第二段打底焊熔敷金属焊道,打磨清除起弧点后面的点固块,将第二段打底焊熔敷金属焊道两个端头打磨成缓坡形;第一段打底焊熔敷金属焊道与第二段打底焊熔敷金属焊道对称;再以同样的焊接方式从第一段打底焊熔敷金属焊道起弧点端头前10-15mm位置起弧,向后移动与第一段打底焊熔敷金属焊道起弧点端头缓坡接头后,电弧再向三点位置移动立向上焊接形成第三段打底焊熔敷金属焊道,若遇到点固块则在点固块前10mm收弧;打磨清除点固块,将第三段打底焊熔敷金属焊道的收弧处打磨成缓坡形;相对称的,以六点
→
九点
→
十二点移动方向施焊,在与第三段打底焊熔覆金属焊道收弧端头缓坡中心对称的位置附近撕开粘胶带小口起弧,待电弧稳定燃烧之后,再向后移动5-10mm开始焊接,熔池再向十二点位置移动,在与第二段打底焊熔覆金属焊道收弧端缓坡上接头收弧,形成第四段打底焊熔敷金属焊道,打磨清除起弧点后面的点固块,将第四段打底焊熔敷金属焊道起弧端头打磨成缓坡形;第三段打底焊熔敷金属焊道与第四段打底焊熔敷金属焊道对称;以此类推,完成第一层打底焊熔敷金属焊道焊接;e1223)第二层打底焊的焊接方式与第一层打底焊相同,层间接头错开大于20mm,层间温度<100℃;e123)以水平转动焊接方式对管材坡口打底层焊缝焊接:采用逆时针方向左焊法施焊,线性焊道,压道焊,起始施焊位置取起弧点一点三十后侧10-20mm位置,撕开粘胶带小口后起弧,电弧稳定后开始焊接,遇到点固块时打磨清除,同时将现有焊道起弧端头和收弧端头打磨成缓坡形;转动一圈后,电弧与打底焊缝起焊端点缓坡接头,形成整条打底焊熔敷金属焊道,打磨清理接头余高,清除低熔点杂质缺陷;e124)以横焊方式对管材坡口打底层焊缝焊接:采用逆时针方向左焊法施焊,线性焊道,压道焊,在施焊位置撕开粘胶带小口起弧,电弧后移10-20mm,然后再前移10mm开始焊接,遇到点固块时,打磨清除,同时将现有焊道起弧及收弧端头打磨成缓坡形;以同样的方法依次焊接,对称焊;电弧最后与打底焊缝起焊端点端头缓坡接头,形成整条打底焊熔敷金属焊道,打磨清理接头余高,清除低熔点杂质缺陷;e125)当板材采用平焊方式进行打底焊时;点固块从焊缝长度的中点向两边均布,两点固块之间距离300-500mm;将焊缝的前进方向定义为前,采用从中间向两边分段对称跳焊;
第一层第一轮跳焊:在点固块之间的区域向两边对称跳焊;打磨清除全部点固块,将每条焊段两端头打磨成缓坡形;第一层第二轮跳焊:在第一轮焊段的间隔区域向两边进行对称跳焊,第二轮跳焊的每一焊段起弧点焊接端头与第一轮焊段收弧端头缓坡相接头;第二轮跳焊的每一焊段收弧弧点焊接端头与第一轮焊段起弧端头缓坡相接头;以同样的对称跳焊的方式形成第二层打底焊;e126)当板材采用横焊方式进行打底焊时,焊接方法与步骤e125相同;e127)焊接时若环境温度为-20℃-0℃时对管材或者板材的坡口周围进行预热,预热温度10-15℃;每层的焊道用铁素体检测仪随机检测3个点,控制铁素体测量值在40%-60%范围内,不合格返修重焊至合格。
10.其中优选的,所述步骤a3选择工机具及配件具体为:a31)选用焊机型号为ws-400cel;a32)选用氩弧焊炬角度75
°‑
80
°
、手把导线直径为30-50mm
2 且长度为3-4m,铈钨极直径2.0mm 或2.4mm,铈钨极的尖端加工为锥度35
°‑
45
°
的圆锥台形,圆锥台形的小圆直径为0.8-1.0mm,铈钨极相对氩弧焊炬的瓷嘴的伸出长度为6-8mm。
11.采用了上述技术方案后,本发明的效果是:利用该焊接工艺方法焊接超级双相钢asme sa-240m s32750接头坡口焊缝时,焊缝成型美观,焊纹均匀,热输入量大小适当,严格控制热输入量的上限和下限,焊缝及热影响区机械性能合格,铁素体含量合格,耐腐蚀性能合格,焊缝质量稳定,焊接难度低。
附图说明
12.下面结合附图和实施例对本发明进一步说明。
13.图1是本发明实施例的管材组对保护气体室的轴向结构剖视图;图2是本发明实施例的管材组对后的坡口示意图;图3是本发明实施例的焊缝圆周分布示意图;图4是本发明实施例的点固焊后的示意图;图5是本发明实施例的管材焊接顺序示意图;图6是本发明实施例焊接期间道间温度及铁素体测量示意图;图7是本发明实施例焊缝铁素体测量示意图;图8是另一种坡口示意图;图9是本发明实施例的板材组对保护气体室的结构剖视图;附图中:1.管材;101.钝边;2.坡口;21.圆弧坡口面;22.第一坡口平面;23.第二坡口平面;3. 进气堵板;4.出气堵板;5. 进气管;6.出气管;7.钢丝;8.拉簧;9.进气软管;10.盖面层;11.点固块;12.点固焊缝;13.打底层;14. 保护气体储槽;15.板材;16.金属丝;17.金属网;t.测温仪;f.铁素体检测仪。
具体实施方式
14.下面通过具体实施例对本发明作进一步的详细描述。
15.如图1至图9所示,一种超级双相钢工艺管道手工钨极氩弧焊接工艺方法,该焊接
工艺方法用于两根牌号为asme sa-240m s32750的管材1之间焊接或者两块牌号为asme sa-240m s32750的板材15之间焊接,包括以下分步骤:a、焊前准备,包括以下分步骤:a1)确定焊接执行标准;本实施例中执行标准为:asme锅炉及压力容器规范《焊接和钎焊接工艺、焊工、钎焊工及焊接和钎接操作工评定标准》第ix卷 2019;asme锅炉及压力容器规范《压力容器建造规则》第viii-1卷 2019;asme压力管道规范《工艺管道》asme b31.3
‑ꢀ
2019;a2)确定管材1或板材15的规格、牌号,焊材规格、牌号及保护气体的执行标准;表1记录了本实施例超级双相钢asme sa-240m s32750焊缝两侧管材1及焊接用焊材标准参数;表1a3)选择工具及配件;本实施例中,所述步骤a3选择工机具及配件具体为:a31)选用焊机型号为ws-400cel;a32)选用氩弧焊炬角度75
°‑
80
°
、手把导线直径为30-50mm
2 且长度为3-4m,铈钨极直径2.0mm 或2.4mm,铈钨极的尖端加工为锥度35
°‑
45
°
的圆锥台形,圆锥台形的小圆直径为0.8-1.0mm,铈钨极相对氩弧焊炬的瓷嘴的伸出长度为6-8mm。
16.a4)管材1或板材15及工具和机器的验收检查;验收检查具体方式为:检查管材1的牌号、规格、坡口2尺寸、表面质量等是否符合标准要求;检查焊机ws-400cel电流表、电压表及保护气体(氩气98% 氮气2%)流量计的计量器是否已标定且在有效期内;检查保护气体(氩气98% 氮气2%)纯度是否符合工艺要求;检查数显测温仪t是否已标定且在有效期内;检查数显铁素体检测仪f是否已标定且在有效期内;检查数显测氧仪是否已标定且在有效期内;检查焊丝表面是否清洁;检查管材1、板材15、焊丝的材质证明书引用标准及理化参数是否合格;确定使用不锈钢磨片、不锈钢割片以及不锈钢钢丝刷仅用于不锈钢焊缝打磨清理。
17.a5)对管材1或板材15进行划线并进行尺寸检查;a6)对管材1或板材15切割下料,切口端面与管材1轴线或者切口与板材15的板面的垂直度符合标准规定要求;a7)对需焊接的管材1或板材15的切口端面冷加工坡口2;其中管材1或板材15的壁厚小于等于21.95mm时,坡口角度为单边30
°‑
32
°
,钝边101为0-1mm,如图2所示;当管材1或板材15壁厚大于21.95mm时,坡口2机加工成根部为r=8 mm的u型阶梯坡口2,如图8所示,该u
4.0mm,十二点处的组对间隙大于3.2-4.0mm;当选择水平转动焊接方式或者横焊方式时,坡口2焊缝组对间隙均匀且为3.2-4.0mm;b222)针对母材为板材15的情况,当选择平焊方式进行焊接时,坡口2焊缝组对间隙大于3.2-4.0mm;当选择横焊方式进行焊接时,坡口2焊缝组对间隙均匀且为3.2-4.0mm。
20.c、将管材1或板材15的坡口2焊缝进行点固焊:其中优选的,所述步骤c包括以下分步骤:c1)确定组对固定方式,选用点固块11组对固定;c2)对于管材1选用点固块11组对固定时,点固块11避开管材1钟点位置的三、六、九、十二点位置,当管径d≤φ168.3mm时,点固块11的数目为1-3个,且均布于避开点以外的管材1圆周坡口面上;当管径d>φ168.3mm时,将焊缝圆周分为对称的2(n 2)段(其中n为大于1的自然数),点固块11的数目2(n 2)-4个,其中n>1,且均布于避开点以外的管材1圆周坡口面上;如图3所示,图3中管材1按照钟点位置划分,并且取n=4,那么焊缝就一共有12段,点固块11为8个,由于8个点固块11要避开三、六、九、十二点位置,这样,就可以将点固块11设置在一、二、四、五、七、八、十、十一点位置;对于板材15选用点固块11组对固定时,点固块11从焊缝长度的中点向两边均布,两点固块11之间距离300-500mm;c3)检查点固焊缝12质量:点固块11两边点固焊缝12厚度2-8mm,长度5-45mm,点固焊缝12落在坡口面与点固块11之间;c4)点固焊接完成后,用无卤素污染的粘胶带封堵坡口2间隙,保护气体室焊前充气至排尽杂气。具体是否排尽杂气可以采用测氧仪测量:即在高点位置撕开粘胶带小口,测量排出的混合气体的含氧量,当含氧量低于标准要求即可。
21.d、焊前对外界客观因素进行检查;e、坡口2焊缝焊接:先焊接打底层焊缝两层,再焊接填充层及盖面层10;e1)管材1坡口2打底层焊缝焊接方法包括以下分步骤:e11)确定打底焊的起弧点、施焊位置和施焊方向:采用手工钨极氩弧焊进行焊接,直流正接,左焊法,线性焊道,压道焊;具体的确定内容如下:e111)当管材1采用水平固定焊接方式进行打底焊时,采用立向上焊接,对称焊,按照管道的圆周截面划分,将底部位置定义为六点位置,将顶部位置定义为十二点位置,并按照钟表刻度划分对称段,施焊方向为六点
→
三点
→
十二点;六点
→
九点
→
十二点,并将焊接时行进方向定义为前;起弧点为六点位置,起始施焊位置取在距离起弧点后侧5-30mm的位置,对称焊;如图5所示,本实施例中,焊缝一共12段,其中第一段和第二段为一对对称的焊缝;第三段和第四段为一对对称焊缝;第五段和第六段为一对对称焊缝;第七段和第八段为一对对称焊缝;第九段和第十段为一对对称焊缝,第十一段和第十二段为一对对称焊缝;e112)当管材1采用水平转动焊接方式进行打底焊时,按照管道的圆周截面划分,将底部位置定义为六点位置,将顶部位置定义为十二点位置;将焊接时行进方向定义为前;采用逆时针方向左焊法施焊,起弧点为一点三十的位置,起始施焊位置取在距离起弧点后侧5-30mm的位置;e113)当管材1采用横焊位置方式进行打底横焊时,将焊接时行进方向定义为前,
采用逆时针方向左焊法施焊,在起弧点起弧,起始施焊位置取在起弧点后侧5-30mm位置,对称焊;e114)当板材15采用平焊方式进行打底焊时,将焊接时行进方向定义为前,采用从中间向两边分段对称跳焊;e115)当板材15采用横焊方式进行打底焊时,将焊接时行进方向定义为前,采用从中间向两边分段对称跳焊;e12)对坡口2进行打底层焊缝焊接,打底焊共焊2层,每层一道,线性焊道,道间接头错开大于20mm;其中本实施例中优选的,所述步骤e12对坡口2进行打底层焊缝焊接的具体步骤为:e121)焊钳手把线跨过手臂后右手握住,从起弧点起弧,向后移动到起始施焊位置开始施焊;e122)以水平固定焊接方式对管材1坡口2打底层焊缝焊接:e1221)对于管径d≤φ168.3mm,打底层焊缝仅需要分为对称的两段圆弧,一段以六点
→
三点
→
十二点,另一段以六点
→
九点
→
十二点所示的移动方向进行对称施焊;起弧前从起弧点将粘胶带撕掉一个小口;当以六点
→
三点
→
十二点的移动方向施焊时,在六点后面10-20mm的位置,用电弧从间隙的中间位置打穿钝边101形成熔孔,熔化的铁水充盈在熔孔下部,熔孔上移,铁水冷却形成单面焊双面成型的打底焊缝,打底焊缝向前延伸遇到点固块11前收弧,打磨清除点固块11将焊缝端头打磨成缓坡形,在焊缝端头前10-20mm位置起弧,然后电弧移动到端头的缓坡接头,焊缝熔覆金属继续向三点和十二点方向延伸,在十二点附近收弧,形成第一段打底焊熔敷金属焊道;再以同样的焊接方式以六点
→
九点
→
十二点的移动方向施焊,在第一段打底焊熔敷金属焊道起焊端头前10-20mm位置起弧,再把电弧移到起焊端头的缓坡进行接头,然后向九点和十二点方向焊接,与第一段打底焊熔敷金属焊道收弧点进行接头,形成第二段打底焊熔敷金属焊道;e1222)对于管径d>φ168.3mm,采用分段对称焊接方法;其中,将焊缝圆周分为对称的2(n 2)段(其中n为大于1的自然数),从而形成了若干对中心对称的焊缝段;先从六点位置起弧后向九点方向移动,电弧后移10-20mm位置开始施焊,采用立向上焊接,若遇到点固块11则在点固块11前10mm收弧;若未遇到点固块11则焊接完形成第一段打底焊熔敷金属焊道,打磨清除点固块11,将第一段打底焊熔敷金属焊道的两个端头打磨成缓坡形;相对称的,以六点
→
三点
→
十二点移动方向施焊,在与第一段打底焊熔覆金属焊道收弧端头缓坡中心对称的位置附近撕开粘胶带小口起弧,待电弧稳定燃烧之后,再向后移动5-10mm开始焊接,熔池再向十二点位置移动,在与第一段打底焊熔覆金属焊道起弧端中心对称位置附近收弧,形成第二段打底焊熔敷金属焊道,打磨清除起弧点后面的点固块11,将第二段打底焊熔敷金属焊道两个端头打磨成缓坡形;第一段打底焊熔敷金属焊道与第二段打底焊熔敷金属焊道对称;再以同样的焊接方式从第一段打底焊熔敷金属焊道起弧点端头前10-15mm位置起弧,向后移动与第一段打底焊熔敷金属焊道起弧点端头缓坡接头后,电弧再向三点位置移
动立向上焊接,若遇到点固块11则在点固块11前10mm收弧;若未遇到点固块11则焊接完形成第三段打底焊熔敷金属焊道,打磨清除点固块11,将第三段打底焊熔敷金属焊道的收弧处打磨成缓坡形;相对称的,以六点
→
九点
→
十二点移动方向施焊,在与第三段打底焊熔覆金属焊道收弧端头缓坡中心对称的位置附近撕开粘胶带小口起弧,待电弧稳定燃烧之后,再向后移动5-10mm开始焊接,熔池再向十二点位置移动,在与第二段打底焊熔覆金属焊道收弧端缓坡上接头收弧,形成第四段打底焊熔敷金属焊道,打磨清除起弧点后面的点固块11,将第四段打底焊熔敷金属焊道起弧端头打磨成缓坡形;第三段打底焊熔敷金属焊道与第四段打底焊熔敷金属焊道对称;以此类推,完成第一层打底焊熔敷金属焊道焊接;如图5所示,图中记载了焊缝的焊接顺序和焊接方向,依次完成了第一段至第十二段的焊接。
22.e1223)第二层打底焊的焊接方式与第一层打底焊相同,层间接头错开大于20mm,层间温度<100℃;e123)以水平转动焊接方式对管材1坡口2打底层焊缝焊接:采用逆时针方向左焊法施焊,线性焊道,压道焊,起始施焊位置取起弧点一点三十后侧10-20mm位置,撕开粘胶带小口后起弧,电弧稳定后开始焊接,遇到点固块11时打磨清除,同时将现有焊道起弧端头和收弧端头打磨成缓坡形;转动一圈后,电弧与打底焊缝起焊端点缓坡接头,形成整条打底焊熔敷金属焊道,打磨清理接头余高,清除低熔点杂质缺陷;e124)以横焊方式对管材1坡口2打底层焊缝焊接:采用逆时针方向左焊法施焊,线性焊道,压道焊,在施焊位置撕开粘胶带小口起弧,电弧后移10-20mm,然后再前移10mm开始焊接,遇到点固块11时,打磨清除,同时将现有焊道起弧及收弧端头打磨成缓坡形;以同样的方法依次焊接,对称焊;电弧最后与打底焊缝起焊端点端头缓坡接头,形成整条打底焊熔敷金属焊道,打磨清理接头余高,清除低熔点杂质缺陷;e125)当板材15采用平焊方式进行打底焊时;点固块11从焊缝长度的中点向两边均布,两点固块11之间距离300-500mm;第一层第一轮跳焊:在点固块11之间的区域从中间向两边对称跳焊;打磨清除全部点固块11,将每条焊段两端头打磨成缓坡形;第一层第二轮跳焊:在第一轮焊段的间隔区域向两边进行对称跳焊,第二轮跳焊的每一焊段起弧点焊接端头与第一轮焊段收弧端头缓坡相接头;第二轮跳焊的每一焊段收弧弧点焊接端头与第一轮焊段起弧端头缓坡相接头;以同样的对称跳焊的方式形成第二层打底焊;在左焊法焊接情况下,保护气体室封堵间隙的粘胶带,起弧前撕小口,起弧后,粘胶带在电弧气氛外围,受到传导热和电弧光辐射热的作用下而逐步气化、碳化最后灰化后,再受到焊缝背面喷出的保护气体流和焊把头口喷出的正面保护气体流的联合冲刷,向远离电弧气氛外围的区域飘散,所以,粘胶带释放的气体及其灰化残留物不会对焊缝熔覆金属理化性能造成影响。这样,采用了上述的焊接方式,粘胶带只需要撕开一个小口即可完成焊接,操作更简便。
23.e126)当板材15采用横焊方式进行打底焊时,焊接方法与步骤e125相同;
e127)焊接时若环境温度为-20℃-0℃时对管材1或者板材15的坡口2周围进行预热,预热温度10-15℃;每层的焊道用铁素体检测仪f随机检测3个点,控制铁素体测量值在40%-60%范围内,不合格返修重焊至合格。
24.e2)坡口2的填充层和盖面层10焊接;e21)填充层和盖面层10的每道焊缝熔覆金属按照打底焊的施焊方向施焊;线性焊道,压道焊,多层多道焊;熔池在坡口面两边停留时间比在焊缝中间停留时间长,每道焊缝宽度不超过焊材钢芯直径的3倍,后一道的熔覆金属接头与前一层和前一道熔覆金属的接头错开大于20mm,收弧填满弧坑,收弧处缺陷和道间的成型不良缺陷及时清理;e22)确定焊接工艺参数满足以下要求:焊接期间每道焊缝电弧起弧前,待道间温度≤100℃时再进行起弧焊接;当焊接电流120-130a,焊接电压12-15v时,焊接速度8.2-8.6cm/min;当焊接电流130-140a,焊接电压12-15v时,焊接速度8.8-9.3cm/min;当焊接电流140-150a,焊接电压12-15v时,焊接速度9.4-10cm/min;当焊接电流150-160a,焊接电压12-15v时,焊接速度8.2-8.6cm/min;当焊接电流160-170a,焊接电压13-16v时,焊接速度11.4-12.4cm/min;当焊接电流170-180a,焊接电压13-17v时,焊接速度12.8-13.2cm/min;正面保护气体流量15-25l/min;背面保护气体流量10-20l/min;其中,正面保护气体是从焊枪中流出,起到正面保护的作用,每道焊缝热输出控制在1000j/mm至1500j/mm之间;热输入量太大,焊缝热影响区及多层多道焊的焊缝金属容易析出σ相、x相、氧化物、氮化物以及金属间化合物,造成接头焊缝金属及热影响区耐腐蚀性能及塑韧性大幅度下降。而热输入值不能太小焊接接头冷却太快将抑制铁素体向奥氏体转变,造成单项铁素体化组织,因此通过控制热输入值及道间温度值在规定的范围内,就可以保证焊接的机械性能以及耐腐蚀性能,防止焊缝热影响区出现晶粒粗大的单项铁素体组织以及焊缝金属的脆化。
25.e3)整个焊接过程中,起初焊枪磁嘴下部支撑在根部两边坡口面上,以此为支点,握紧焊把,手腕做均匀圆弧运动,带动焊把钨丝压帽轴向与支点的切线之间在70
°
~85
°
范围内,以磁嘴支点为顶点,钨极圧帽及氩弧弧柱做圆锥摆动和前进;随着焊缝的成形,磁嘴下部转而以红热的焊缝表面为支撑平稳的前移,焊缝根部的内凸高度控制在0-2mm范围内,仰焊部位焊丝端头送到坡口2的根部,水平固定焊口从立上坡到平焊位置焊丝端头只给进到熔池边缘;e4)焊缝接头时的焊接方式为:从接头位置前10-20mm左右的坡口2内起弧,然后向后移到接头缓坡位置上部,电弧在坡口2两边停留时间比焊缝中间长以保证两边熔合,待熔池形成后,控制熔池大小逐渐给丝,铁水填满熔池两边熔合线边缘,然后向前移动使熔池前移,收弧电流衰减前填满弧坑;焊接完成完整的每道焊缝或者每层焊缝后,在熔覆金属表面随机选取三个位置测量铁素体值,铁素体值要求控制在40%-60%范围内;至此,超级双相钢asme sa-240m s32750坡口2焊缝打底层13及填充盖面层10的焊接工艺参数如下表:
表2f、焊接过程中对焊接的各客观因素进行检查,其主要包括:f1)检查清洁在规定的范围:坡口面及内外表面20mm范围内油、油漆等污垢物及附着的潮气用丙酮清除干净,露出金属光泽;f2)检查焊接电流值在焊接工艺评定规定的范围;f3)检查焊接电压值在焊接工艺评定规定的范围;f4)检查焊接速度值在焊接工艺评定规定的范围;f5)检查每道和每层焊缝熔覆金属铁素体含量值在规定的范围;f6)检查道间温度在焊接工艺评定规定的范围,如图6所示,温度检测通过测温仪t来检测;g、焊后检查,主要包括:g1)外观检查,焊缝完成后100%外观自检;g2)打磨清除局部咬边、熔合性飞溅及过高的余高,圆滑过渡到母材,进行铁素体值检测,消除不合格缺陷;g3)根据工艺管道的设计要求进行射线检测。
26.以上所述实施例仅是对本发明的优选实施方式的描述,不作为对本发明范围的限定,在不脱离本发明设计精神的基础上,对本发明技术方案作出的各种变形和改造,均应落
入本发明的权利要求书确定的保护范围内。
再多了解一些
本文用于创业者技术爱好者查询,仅供学习研究,如用于商业用途,请联系技术所有人。