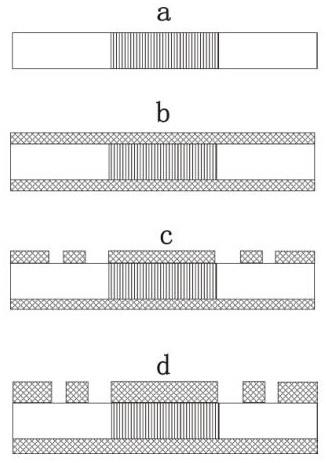
1.本发明涉及微波元器件领域,尤其涉及一种一种提高陶瓷嵌套铁氧体基片表面金属电路附着力的方法。
背景技术:
2.环行器/隔离器是微波工程中一类重要的基础性器件,其广泛应用于民用通讯、微波测量、雷达、通信、电子对抗、航空航天等各种民用、军用设备中,在设备中主要用来实现天线收发共用,级间隔离等问题。
3.随着电子元器件小型化、集成化的发展,对微波磁性元器件也提出了同样的需求。传统的加工工艺已经不能满足微带环行器/隔离器的发展,因此出现了基于mems技术的硅基、陶瓷基微带环行器/隔离器以及基于陶瓷嵌套铁氧体技术的微带环行/隔离器。其中,基于陶瓷嵌套铁氧体基片技术的微带环行器/隔离器因为具有承载功率大、旋磁区域可控、介电常数高、加工精度高、尺寸小、一致性好、稳定性高、易于集成、便于调试等优点,在一些使用场景里逐渐开始替代铁氧体基微带环行器,在当代相控阵雷达、电子对抗等军事领域应用中具有十分重要的地位。
4.目前,典型的基于陶瓷嵌套铁氧体基片技术的微带环行器/隔离器的结构如图1所示,由陶瓷嵌套铁氧体基片(包括外周的陶瓷基片1和嵌套于陶瓷基片1中心的旋磁铁氧体基片2)、金属电路3、铁底板4、陶瓷片5和永磁体6组成,其中,金属电路3制作于陶瓷嵌套铁氧体基片上用于微波传输,铁底板4和陶瓷嵌套铁氧体基片通过焊接方式组合在一起,陶瓷片5和永磁体6通过粘结方式固定在金属电路3上方。
5.陶瓷嵌套铁氧体技术的微带环行器/隔离器由于可以使用高介电常数的陶瓷材料,对于一般意义上基于陶瓷嵌套铁氧体技术的微带环行/隔离器主要通过在陶瓷基片1中间嵌套一个旋磁铁氧体基片2,然后通过薄膜电路工艺方式制作而成,其中在陶瓷基片中间嵌套一个旋磁铁氧体基片主要是通过高温共烧、无机胶黏合烧结等方式实现,薄膜金属电路可通过常用的薄膜工艺方式实现。
6.上述陶瓷基片1以及旋磁铁氧体基片2都可以选择介电常数非常高的材料,能够有效减小器件的尺寸。而通过图1的结构可见,金属电路3的可靠性(即金属电路3在陶瓷嵌套铁氧体基片表面的附着力的大小)直接关系到整个器件的结构稳定性和可靠性。但是,由于陶瓷基片和铁氧体基片材质不同,一般用于陶瓷基片的镀膜工艺很难同时满足铁氧体基片的镀膜需求,要同时满足两种材质基片的高附着力薄膜制作很难实现,因此需要对薄膜制作工艺进行改进,以满足器件的可靠性要求,实现高质量基于陶瓷嵌套铁氧体技术的微带环行/隔离器的制作。现有工艺制作的金属电路附着力主要和应用场景有关,一般最基础的要求是通过胶带拉剥后没有出现脱落现象:比如:文献:王盼,潘应君等.沉积温度对磁控溅射金属钌薄膜微观结构和附着力的影响[j].武汉科技大学学报,2017,40(1):23-26;王德山,磁控溅射镀膜附着力的优化机制研究[j].大众科技,2013,15(171):66-68;王德苗,董树荣,任高潮,铁氧体磁芯的磁控溅
射金属化工艺的研究[j],真空科学与技术学报,2006,26:87-90等等,可见现有的铁氧体基片或陶瓷基片上制作金属电路工艺路线类似,但是这些工艺都没有退火工艺。另外,铁氧体工艺一般都是高温工艺(>400℃),陶瓷一般都使用ti作为打底层;即要保证薄膜质量,提高薄膜电路的附着力,则需要改进薄膜制作工艺以同时满足陶瓷和旋磁铁氧体基片的高附着力薄膜沉积。
技术实现要素:
[0007]
本发明的目的就在于提供一种提高陶瓷嵌套铁氧体基片表面金属电路附着力的方法,以解决上述问题。为了实现上述目的,本发明采用的技术方案是这样的:一种提高陶瓷嵌套铁氧体基片表面金属电路附着力的方法,包括下述步骤:(1)陶瓷嵌套铁氧体基片准备:对陶瓷嵌套铁氧体基片进行清洗、烘干;(2)种子层制作:使用磁控溅射在所述陶瓷嵌套铁氧体基片上沉积膜层,得到双面沉积有膜层的基片,沉积膜层前采用rf等离子体反溅清洗分别处理陶瓷嵌套铁氧体基片上下表面,并在沉积膜层前将陶瓷嵌套铁氧体基片进行加热;(3)退火:将双面沉积完膜的基片放到真空退火炉中退火。
[0008]
由于旋磁铁氧体溅射和陶瓷溅射的沉积温度差距较大,本发明创新了一种低温溅射的方法制备种子层薄膜,其主要原理是基材的结构和性能对薄膜沉积的附着力有决定性影响,不同基材-薄膜之间的组合附着力差异极大,浸润性较差的物质之间不易形成较强的键合力,只有用表面能量小的薄膜材料覆盖在表面能量大的基片上,才会产生很好的浸润性。这也是为什么要选用合适种子层的原因。基底温度也是薄膜沉积另一个非常重要的关键因素,提高基片温度,有利于薄膜和基片间的原子扩散,并且还会加速其化学反应,从面有利于形成扩散附着和通过中间层的附着,所以附着力增大。但不同基材-薄膜之间附着力随温度的变化曲线是不同的,铁氧体基材在较高温度(比如400-600℃)时附着力最好,而陶瓷基材则是200℃左右。因此需要恰当的调节沉积温度以找到两种基材之间的平衡。;并且,本发明采用rf轰击/反溅清洗、低温沉积以及退火相结合的方法提升了薄膜在铁氧体和陶瓷基片上的附着力,这是本发明最重要的发明点;rf轰击/反溅清洗即采用高能粒子轰击基材表面以排除表面吸附的气体及有机物 , 提高表面的清洁度 , 改善形核和生长状态 , 提高界面的结合强度。等离子体活化处理可以促进吸附的气体和杂质解吸,有利于溅射粒子与基体的结合 , 同时还能在一定程度上增加表面的微观粗糙度。
[0009]
如前所述的,基片加热是非常有效的提高薄膜材料附着力的方法。另外过高温度会导致工艺时间过长,不利于生产。
[0010]
退火后处理可以促进膜层原子与基体原子间的相互扩散 , 使薄膜与基体的接触面积增加 , 从而增加附着性。采用本发明的方法后,通过拉力实验测试发现其附着力都超过250g/mm2,另外也通过了3m胶带以及刀片测试。
[0011]
作为优选的技术方案:步骤(2)中,所述膜层为cr/au、cr/cu、cr/tan/cr/cu膜或cr/tan/cr/au膜。在镀cu或au之前还可以沉积了一定厚度(100-200nm)的ni薄膜,这里ni的作用主要是作为缓冲层起阻挡作用:一方面是防止cu或者au往衬底扩散,以及au和cu之间
的扩散,影响器件性能,另一方面是可以防止在共晶焊接等工艺过程中出现的cu层返出后续电镀的au层。
[0012]
作为优选的技术方案,其特征在于:cr/au膜厚度分别为cr:20-50nm,au100-150nm ,cr/cu 中cu1500-2500nm。
[0013]
作为优选的技术方案:所述膜层为cr/au时,先将所述陶瓷嵌套铁氧体基片加热到180℃,然后再沉积打底cr层;在沉积au薄膜之前将所述陶瓷嵌套铁氧体基片加热到250℃,然后沉积au层。
[0014]
作为优选的技术方案:所述膜层cr/tan/cr/au膜时,其中cr沉积前先将所述陶瓷嵌套铁氧体基片加热到150-220℃,进一步优选180℃。
[0015]
作为优选的技术方案:步骤(3)中,退火方法为:本底真空<1e10-3pa,升温速率为6℃/min,升温到300℃,保温时间3小时,自然冷却降温。
[0016]
需要说明的是:采用本发明的方法可以制备大带宽微带环行隔离器(包括8-12ghz、7-13ghz、5-13ghz、6-18ghz、8-15ghz、2-18ghz等),器件性能和设计结果匹配;本发明的方法可以满足单结环行隔离器的制作,也可以满足双结、三结器件的制作;本发明的工艺方法不但可以用于微带环行隔离器的制作,还可以用于片上电感、片上隔离器变压器、mems磁通门等片上器件的制作。
[0017]
与现有技术相比,本发明的优点在于:本发明的制作方法具有工艺成熟,速度快、成本低、效率高且一致性好等优点,适合大批量生产,同时可以有效增强器件的膜层结构强度,增强器件的可靠性,减小铁氧体和器件的尺寸等优点,为了更小体积的基于高介陶瓷的微带环行器/隔离器打下了工艺基础。
附图说明
[0018]
图1为典型的基于陶瓷嵌套铁氧体基片技术的微带环行器结构图;图2为本发明的工艺流程图;图3为本发明所制得的器件的三维图;图4为实施例1的设计仿真结果图;图5为实施例1的实际测试结果图。
[0019]
图中:1、陶瓷基片;2、旋磁铁氧体基片;3、金属电路;4、铁底板;5、陶瓷片;6、永磁体。
具体实施方式
[0020]
下面将结合附图对本发明作进一步说明。
[0021]
一种提高陶瓷嵌套铁氧体基片表面金属电路附着力的方法,其工艺流程参见图2,包括:a、基片准备清洗;b、沉积膜层、退火;c、图案化(光刻、刻蚀)和d、电镀、膜层加厚。
[0022]
下面以制作微带环行器/隔离器为例,详细说明具体的方法。
[0023]
实施例1:一种基于陶瓷嵌套铁氧体基片的微带环行器/隔离的制作方法,包括下述步骤:(1)使用双面抛光的陶瓷嵌套铁氧体基片作为加工材料主体,尺寸为4寸(其他尺
寸也可以),陶瓷嵌套铁氧体基片的嵌套方法包括现有的共烧、无机胶黏合等,以实现两种材质的无缝黏合,其中,陶瓷基片1根据设计需要优选采用高介陶瓷,比如介电常数大于等于15的钛酸盐陶瓷,高介电常数陶瓷可以明显减小器件的尺寸,旋磁铁氧体材料可以选择高介电常数旋磁铁氧体,以进一步减小器件尺寸,使用打标机在基片上打标以区分正反面,一次使用山梨糖溶液、去离子水、丙酮、无水乙醇对嵌套基片进行超声清洗,然后烘干;(2)种子层制作:如果是制备环行器,则使用磁控溅射在嵌套基片上沉积cr/cu双层膜,镀膜前采用rf等离子体反溅清洗分别处理基片上下表面,厚度分别为cr:30nm,cu1500nm,这时候硅晶圆表面和通孔内都镀满了cr/au;如果是制作隔离器,则需要在基片正面沉积cr/tan/cr/cu结构的薄膜;为了提高薄膜和基片的结合力,在镀膜前将基片加热到180℃,然后再沉积打底cr层,在制备cu薄膜之前将基片加热到250℃,然后沉积cu层;如果是制作隔离器,则需要增加一步tan的沉积工艺以及cr的沉积工艺,其中cr沉积前仍然需要加热到180℃;(3)退火:将双面镀完膜的基片放到真空退火炉中,其中本底真空优于(即小于)1e10-3pa,将升温速率为6℃/min,升温到300℃,保温时间3小时,自然冷却降温;(4)光刻:将嵌套基片放入hmds烘箱做预处理,处理温度为120℃,然后在在基片正面涂正胶,光刻胶厚度为3.5μm,接着使用接触式曝光机曝光,然后显影,热板烘烤即可完成;(5)刻蚀:在基片背面贴uv膜以保护背面金属,接着把基片放入湿法腐蚀cu腐蚀槽中,腐蚀完cu之后并用去离子水清洗180s,然后放入湿法腐蚀cr腐蚀槽中,腐蚀时间30s,接着用去离子水冲洗180s,然后甩干烘干。(如果是隔离器,在腐蚀完上面的cr/cu之后,去胶清洗然后甩干烘干基片,随后重复步骤4和5,把基片放入tan腐蚀液中,然后用去离子水清洗180s,再放入湿法腐蚀cr腐蚀槽中,腐蚀时间30s,接着用去离子水冲洗180s,然后甩干烘干;需要说明的是,薄膜刻蚀也可以使用干法刻蚀的方法或干法湿法结合的方法完成,比如离子束刻蚀ibe方法;(6)去胶:使用uv照射机照射晶圆背面120s,然后撕掉uv膜,将制作好图案的基片放入去胶设备中,去胶,然后清洗甩干烘干;(7)电镀:将晶圆放入电镀槽,分别在晶圆正面和背面依次电镀cu和au;这里分为两种工艺:一是有cu的工艺,则需要在晶圆两边分别电镀cu和au,正面和背面厚度有差异;二是没有cu也就是纯au的工艺,这个时候只需要在晶圆两边电镀au,正面背面厚度依然有差异,cu层厚度为>3μm,au层厚度为>1μm(有cu的工艺),纯au工艺厚度分别是正面>4μm,背面>2μm。然后用去离子水冲洗300s,放入甩干机中甩干烘干;需要说明的是,在电镀过程中背面图案时还可以在电镀cu和au之间增加ni层电镀,以提高器件的可焊性;(8)划片,然后在背面焊接铁底板,正面粘接陶瓷基片和永磁体,完成微带环行器的制作。
[0024]
上述加工过程中的光刻、去胶、清洗等方法都为已知的常用的薄膜或mems工艺加工方法。
[0025]
所得的器件三维图如图3所示,所制得的微带环行器/隔离器,其设计仿真结果与
实际测试结果分别如图4和5所示,可见与设计结果匹配。
[0026]
采用上述方法,所得的陶瓷嵌套铁氧体基片表面金属电路拉力实验测试, 拉力实验测试方法是本领域常用的检测手段,具体参考前述的文献。结果,其附着力都超过250g/mm2(250g/mm2等效于2.5mpa,250n的抗拉强度);另外也通过了3m胶带以及刀片测试。
[0027]
表1 不同工艺条件的所得的陶瓷嵌套铁氧体基片表面金属电路的拉力试验结果从表1可以看到,不同条件下处理附着力有较为明显的变化,而最终的好的结果需要各种因素共同作用(都需要优化)。这里主要是找到一个平衡点,可以满足同时沉积陶瓷基片和铁氧体基片。
[0028]
以上所述仅为本发明的较佳实施例而已,并不用以限制本发明,凡在本发明的精神和原则之内所作的任何修改、等同替换和改进等,均应包含在本发明的保护范围之内。
再多了解一些
本文用于创业者技术爱好者查询,仅供学习研究,如用于商业用途,请联系技术所有人。