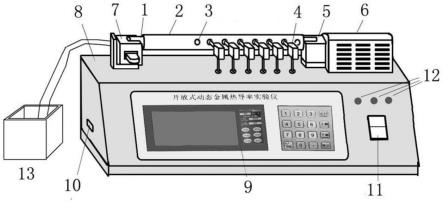
1.本发明涉及一种动态热导率测量方法,属于仪器测量领域。
背景技术:
2.导热是依靠材料中的电子、原子、分子和晶格热运动来传递热量,热导率k是材料本身的固有性能参数,用于描述材料的导热能力,又称为导热率(导热系数),单位为w/(m
·
k)。热导率的大小与物质的种类有关,材料性质不同,热导率不一样,一般来说,金属的热导率大于非金属,纯金属热导率大于合金。热导率的准确测量一直是个难题,一般来说,热导率越小的材料,热导率的准确测量越难。目前来说,即使对于热导率比较大金属(例如,在20℃时,铜的热导率是397w/(m
·
k)),热导率的准确测量也是个难题。根据傅里叶热传导定律,热传导宏观表达式可写为:
[0003][0004]
其中,δq为在δt时间内通过热传输界面的热量,s为导热的传输通道横截面积,为在热传输面附近的温度梯度,即沿热传导的方向x上单位长度温度t的改变量,而κ则是热导率,负号表示热量的流动指向温度减少的方向。因此,要通过宏观的测量求得热导率κ,在导热截面积s已知的情况下,只需要测出通过导体传输的热量δq所需的时间δt和导热面附近的温度梯度即可。
[0005]
目前在实验中,测量金属热导率的各种实验仪器的种类繁多,这些测量热导率的实验仪器虽在结构和测量方法上各不相同,但从测量方法上大体可以分为“稳态法”(或称为“稳流法”)与“动态法”两大类。所谓“稳态法”(或称为“稳流法”)的测量方法就是让热量从高温热源经被测金属导体往低温热源以稳定的形态流动。目前绝大部分的热导率测量仪都是采用这种方法,稳态法结构的一个共同特佂是:仪器的测温点是在被测物体的两端,在被测物的中部不设测温点。这类稳态法的热导率测量仪器所依据的物理理论都是傅里叶热传导定律。从测量的角度来看,操作比较简便,测量的可靠较高,但从实用的角度出发,难以在工业及生产实践中广泛应用。而另一类动态法的热导率测量仪,其实验的理论是依据波动理论,提供高温热源的温度按简谐形式变化而形成热波沿金属杆动态平衡传输,然后根据波动理论研究热波沿金属杆传输的流速,从而推算出金属的热导率。这种方法有也明显缺陷:需要实现动态恒定的热流传输,这就提高了仪器使用条件的门槛,不能应用在温度随时变化的实际应用场景中。
技术实现要素:
[0006]
针对目前热导率测量仪不能实现变温等不稳定场景条件下准确测量的问题,本发明提供了一种动态热导率测量方法。
[0007]
为达到上述目的,本发明采用的技术方案为一种动态热导率测量方法,其步骤包
括:
[0008]
a、将n个温度传感器沿等间距直线排列在待测金属材料上,间距为δx,n≥2;
[0009]
b、第1个温度传感器放置在高温区附近,第n个温度传感器放置在低温区附近;
[0010]
c、在高温区放置一个温度变化的热源δq,热源提供周期性稳定热源,其周期为2δt,在2δt周期内,热源工作时间为δt,间歇时间为δt;
[0011]
d、记录n个温度传感器的实时温度变化情况,得到第i个温度传感器的温度随时间变化函数ti(t),i=1,2,...,n;
[0012]
e、由周期2δt读出ti(t)函数曲线在温度为ki时对应的温度波动幅度δki;
[0013]
f、代入表达式可求出n-1个热导率κi(i=1,...,n-1)的测量值;
[0014]
h、求出n-1个热导率κi(i=1,...,n-1)的平均值作为最终的测量值k。
[0015]
下面以金属长杆为测量对象,具体描述本发明的具体测量原理。在沿金属杆长度方向靠近高温热源的某一位置开始,等间距地设置多个测温孔,插入微形热电偶测量各测温孔点的实时温度,并通过信号线把测量所得的各测温孔点的温度变化信息传输到仪器机箱上的液晶屏幕或外接的电脑屏幕上,从而显示出各测温点温度的变化曲线。当从高温热源间断性的热流传来时,测量金属杆上任一测温点在一个升温期间内温度的上升量δti与该测温点到高温热源间被测金属杆的质量和比热容的乘积就可推算出传入的热量值δq,再从屏幕曲线上测量出这段升温过程的时间δt,就可推算出单位时间传输的热量另外,根据该测温点与相邻测温点间的温升峰值差与测温点间距的比值,还可推算出金属杆内在热传导时的温度梯度
[0016]
本发明的有益效果:首先是不需要构建复杂的恒温或者稳态热平衡的测量条件,可以测量温度非热平衡状态下的物体的热导率;其次,只要额外提供一温度变化的热源与放置n个温度传感器,就可以实现热导率的测量,适合用在测量对象不可移动或不方便拆卸等工业生产实践中。
附图说明
[0017]
图1为本发明的测量装置示意图。附图标记说明:1、待测金属棒;2、隔热套管;3、测温孔;4、微型热电偶;5、高温热源卡座;6、高温热源;7、低温热源卡座;8、主机箱;9、液晶显示控制屏;10、通讯口;11、主机电源开关;12、、工作和报警指示灯;13、冷却水箱。
[0018]
图2为本发明的温度测量变化曲线。
[0019]
图3为本发明的一个变化周期内的温度测量变化曲线。
[0020]
图4为本发明的动态t-x变化示意图。
[0021]
图5为本发明的动态温度变化幅度示意图。
[0022]
图6为本发明的热量传输示意图。
[0023]
图7为本发明的实验测量结果表1。
[0024]
下面结合附图对本发明的实施方式做进一步说明。
具体实施方式
[0025]
实施例1
[0026]
下面以金属铜杆为测量对象,具体描述如何应用本发明的测量方法,实现金属铜的热导率测量,其方法步骤包括:
[0027]
a、将n个温度传感器沿等间距直线排列,间距为δx,n≥2;这里δx取0.02m或0.04m,具体参见表1。
[0028]
b、第1个温度传感器放置在高温区附近,第n个温度传感器放置在低温区附近;这里n=4,具体参见图1。
[0029]
c、在高温区放置一个温度变化的热源δq,热源提供周期性稳定热源,其周期为2δt,在2δt周期内,热源工作时间为δt,间歇时间为δt;这里δt分别为90秒、120秒、180秒和240秒,具体结构参见表1。
[0030]
d、记录n个温度传感器的实时温度变化情况,得到第i个温度传感器的温度随时间变化函数ti(t),i=1,2,...,n;具体参见图2。
[0031]
e、由周期2δt读出ti(t)函数曲线在温度为ki时对应的温度波动幅度δki;具体参见图3。
[0032]
f、代入表达式可求出n-1个热导率κi(i=1,...,n-1)的测量值。
[0033]
求出n-1个热导率κi(i=1,...,n-1)的平均值作为最终的测量值k,具体参见表1。
[0034]
图1将被测金属杆(1)两端被加工成矩形或梯形,卡在高温热源的卡槽(5)和低温热源的弹性卡槽(7)之间,低温热源的弹性卡槽(7)设计为弹性的,是为了使被测金属杆与两端的卡槽间既能紧密接触又便于随时从卡槽中拆卸下来替换成其它金属杆。在高温热源的卡槽(5)右边是高温热源的罩壳(6),目的是防止实验操作时误碰烫伤。在被测金属杆(1)的侧面包裹有隔热套管(2),目的是为减少热量的散失。在被测金属杆(1)上从靠近高温热源一侧的某一位置开始,沿金属杆长度方向设置有多个测温孔(3),其数量可略多于热电偶1~2个。测温小孔间距要求适当靠拢,但须偏向高温热温一边,测温孔的分布范围不超过金属杆长度的2/3。在测温孔(3)上可根据实验的需要灵活地插入带信号线的微形热电偶(4)。在图1典型的实施例中,测温孔(3)有8个,带信号线的微形热电偶(4)有6个,通过信号线把各测温点的温度变化信息传输到仪器机箱(8)内部。在仪器机箱(8)上设置有彩色液晶屏(9),该屏用以显示各测温点的实时温度变化曲线。在仪器附近有一个小型冷却水箱(11)通过低温冷却循环水的输水管(10)给低温热源的弹性卡槽(7)持续降温。在图1中待测金属杆被安置在仪器顶部的卡槽中。在金属杆的右边是高温热源,在金属杆左边是低温热源(用循环水冷却)。高温热源间歇性地发热产生的热量沿待测金属杆以热波的形式传向低温热源。在待测金属杆靠近高温热源端开始依次有多个相互间距为2.00cm的测温孔。用于测温的热电偶插入这些测温孔中以实时测量金属杆上各个部位的温度。在做实验时可根据实验的不同要求任意选择若干个的微形热电偶,并选择不同的测温孔插入进行自主测量研究。在仪器的面板上设置有彩色液晶触摸屏,通过人机互动的模式可以选择不同的高温热源加热时间和屏幕的坐标及调出二级计算界面等。在机箱侧面还有一个与电脑联接的通讯口,可以把液晶屏显示的测量曲线图同步地传输到电脑屏幕上,便于在电脑屏幕上抓图和精确测量
及计算等。
[0035]
以下是本仪器用动态法测量铜材料的一个实测曲线,见图2。在图2中显示共有4个测温点的测温曲线。横坐标为时间轴,单位为秒;纵坐标为热电偶测量的温度经转换放大后的电压值。因热电偶测温后显示的电压与温度近似成正比,故用“数格子”的方法来代表温度的改变量在计算时更为方便。根据图中曲线的高度可知,最上面的那条曲线代表的测温点离热源最近温度也最高,随着测温点离热端的距离增大,各测温点曲线的高度依次降低。为了便于分析图2中的曲线,我们从图2中截取一部分升温曲线并稍作整理后得到图3。在图3中从上到下依次有4根曲线。为便于下面研究,对这4条曲线的读数作如下定义:t1:第1条曲线峰值的绝对高度,代表第1测温点相对于室温达到的最高温度;t2、t3、t4:第2、3、4条曲线的绝对高度,代表这些测温点相对于室温达到的最高温度;δt1:第1条曲线峰谷值之差,代表第1测温点温度波动的高低落差;δt2、δt3、δt4:第2、3、4条曲线峰谷值之差,代表这些测温点温度的波动落差;δt:某一条曲线温度上升的时段。
[0036]
m1、m2、m3、m4:分别为4条曲线上升段的中点位置,由于各升温曲线近似为正弦曲线,故通过简单的积分计算可知这些中点位置的温度就是各相应曲线在δt时段的平均温度
[0037]
从图3中曲线的几何关系可知:
[0038][0039][0040]
根据图3中的m1和m2两点,我们可得第1和第2测温点间的平均温度差,以此差与δx的比值来近似代替第1测温附近的温度梯度:
[0041][0042]
其它点的平均温度和平均温度梯度只须在式(2)、(3)、(4)的基础上依此类推改变相应的下标即可。式中δx为相邻两测温点间距离。
[0043]
以上参数的读取可参见图3中所示。
[0044]
有了以上的规定后,我们就可进行进一步地分析。
[0045]
考虑到图3中第1个测温点的温度因受它前面金属杆中的温度的改变而产生了图中δt1、的温升,那么,此测温点的温度和温升情况就影响和决定着它之后金属杆中其它测温点的温度和温升状态。从分子热运动的理论可知,金属体内温度的传输其本质上就是这种金属体内部分子热运动动量和能量传递的结果。只有当分子热运动的动量和能量从高温处传入低温处,才可能使原来低温处的温度升高。所以,高温处金属测温点的温升是导致后面低温处测温点温升的原因。这种热量传输时前后温度影响的关系可用图4表示。
[0046]
在图4中x1点的温度从虚线位置上升到t1的高度时,由于x1点有δt1的温升,才会导致后方x2点处温度获得了δt2的温升。同理,x2点处的温升δt2又是引起后面x3点处的温升δt3的原因。后面测温点的温升与前面测温点的温升有密不可分的因果关系,没有前面点的温度波动起伏就不会有后面点的温度波动起伏。在实际的测量中如图4中所示,δt1对δt2、δt3等的影响关系是非线性的,因这种影响的函数关系不太容易给出,所以在误差允许的情况下,根据误差匹配的原则,忽略影响不大的误差,我们可以近似地将这些温度波
动的影响关系用图5来表示。在图5中将δt1和δt2之间温升的关系近似用三角形的线性关系来处理,粗略得出δt1向后方的影响距离l1;而把δt2向后方的影响距离l2用δt2与δt3之间的三角形来求得。这样可把复杂的问题简单化。
[0047]
在图5中根据相似三角形的成比例线段关系可得:
[0048][0049]
(5)式中l1表示δt1温度波动对后方温度波动的影响距离,δx为相邻两测温点之间的距离。从图5中可看出,l1的影响距离仅须考虑δt1与δt2的几何关系即可,而不必顾及和其它测温点温升的几何关系。
[0050]
由(5)式得:
[0051][0052]
同理,从图5中可推出δt2、δt3等对后方温升的影响距离l2、l3分别为:
[0053][0054]
下面我们再讨论一下通过金属杆某一个x1点界面在δt时间内向后方传输的热量计算问题。
[0055]
假设该金属材料的密度和比热容分别为ρ、c,金属杆的横截面积为s,而x1点温升对后方的影响距离实际上就是在此温升时段热量的传输距离l1。那么可认为是在此温升时段由x1点处界面向后方传输的热量为:
[0056][0057]
(8)式的物理意义可用图6形象地表示:在δt时间内通过x1点界面向后方一维传输l1距离内的热量可用图6中的圆柱体体积表示。
[0058]
把(2)式中的和(6)式中的l1代入(8)式,得:
[0059][0060]
至于x2、x3点界面在δt时间内向后方传输的热量,只须把(6)式中字符下标的“1”换成“2”、“2”换成“3”即可。依此类推。(9)式的意义在于:我们通过用动态的温升分析方法可求得在一个温升时段内热量的传输距离,由此可推算出在此温升时段通过x1点界面传输的热量。为了使温度的起伏变化曲线明显,以减少测量的相对误差,通常我们选择的加热时间都应大于90秒。
[0061]
最后,我们把上面的(4)式和(9)式代入原始的傅里叶热传导定律式(1),整理后就得到由x1点处的相关参数求得的热导率表达式:
[0062][0063]
若将其余测温点的测量参数代入(10)式,依次改换下标后就可得到各相应点的热导率计算值,最后再取平均汇总。
[0064]
为了验证本实验理论的正确性,我们选择了纯铜材料做成待测金属杆,目的是借助纯铜材料已知的密度、比热容和热导率的标准值来作参照对比。并可对比与纯铜热导率
的相对误差er。我们选择了加热时间δt分别为90秒、120秒、180秒和240秒、以及δx分别为0.02m和0.04m的情况测量曲线并用图3的办法从屏幕图上读出各条曲线的ti和δti的测量参数,并将公式(12)代入excel软件的计算表格中,算出由各不同加热时间、不同测量点间距和不同的测温点参数得到的热导率κi。最后进行汇总取平均。处理结果见表1。表中除温度单位采用“格”外,其余单位均采用国际单位制。从表1中可看出,对不同的测量情况下算出的纯铜热导率的总评与理论的标准值吻合度较好,总体偏差均小于10%。
再多了解一些
本文用于创业者技术爱好者查询,仅供学习研究,如用于商业用途,请联系技术所有人。