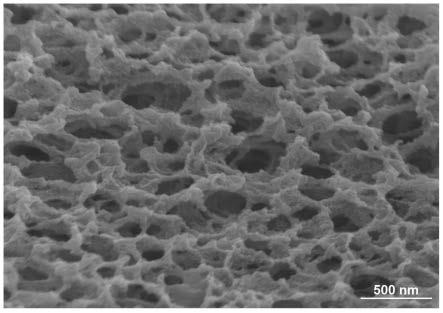
1.本发明涉及分离膜领域,具体地说,是涉及一种具有高贯通多孔结构支撑层的复合纳滤膜及其制备方法和该纳滤膜在水处理过程中的应用。
背景技术:
2.纳滤是一种介于反渗透和超滤之间的压力驱动膜分离过程,纳滤膜的孔径范围在几纳米左右,对单价离子和分子量小于200的有机物脱除较差,而对二价或多价离子及分子量介于200~500之间的有机物有较高的脱除率。可广泛地用于淡水软化、海水软化、饮用水净化、水质改善、油水分离、废水处理及回收利用,以及染料、抗生素、多肽和多糖等化工制品的分级、纯化及浓缩等领域。
3.复合膜是近年来开发的一种新型分离膜,商业纳滤膜目前大多为复合膜,它是由很薄且致密的功能分离层与微孔支撑层复合而成。通常是先制备多孔支撑膜,然后再在其表面形成一层非常薄的致密分离层。复合膜的综合性能受到分离层和支撑层的影响,分离表层对分离起主导作用,而支撑层则有利于降低流体阻力并且增加膜支撑强度,在整个复合膜中起到了至关重要的作用,其形貌结构与渗透性能直接决定了整个复合膜的渗透性能。现有的高分子材质复合膜支撑层多为采用溶液相转化法制得的不对称多孔膜,由该方法所制备的支撑层一般厚度较大,孔隙率较小并且所形成的微孔之间多是闭孔结构,这将直接导致复合膜过滤时水通量较低。为了增加支撑层的孔隙率,近年来,采用高孔隙率、高贯通多孔结构的基膜为支撑层制备的复合膜通量得到了显著的提高。文献《environmental science&technology,2005(39):7 684-7 691》中报道:与传统的商用复合纳滤膜相比较,由静电纺丝纳米纤维多孔膜和功能涂层组成的超薄纳米纤维基复合滤膜在保证高截留率的前提下,水渗透通量可提高10倍之多。中国专利(cn106582297a)以表面涂覆有多孔载体层的长方体状钢丝网作为制备纳滤膜,制备得到的纳滤膜拥有良好的渗透性和截留性,膜层间过滤更加高效。然而,纳米纤维及金属骨架多孔基膜(cn110280222a)的高孔隙率和相互贯通的大孔结构,在显著改善流通性的同时,容易造成在制备复合膜的过程中存在界面聚合单体溶液下渗或涂覆涂层厚度控制困难等技术问题,不能形成完整的分离层结构,难以实现规模化的工业应用。此外,纳米纤维基支撑层的制备仍然面临许多需要解决的问题,包括制膜成本及制膜效率,高质量纳米纤维和纳米纤维基复合材料的规模化制备,适合静电纺丝材料的选取,功能化所需的物理化学手段以及精细的制备方法的完善和改进等。
4.因此,开发简单高效的方法制备出具有高孔隙率、高贯通结构支撑层的纳滤复合膜具有十分重要的现实意义和商业价值。
技术实现要素:
5.本发明的目的是为了克服现有技术的存在的上述问题,而提供一种具有高贯通多孔结构支撑层的复合纳滤膜及其制备方法,以及该复合纳滤膜在水处理领域中的应用。
6.本发明目的之一在于提供一种复合纳滤膜,依次包括底层、多孔支撑层和活性分
离层,所述活性分离层为聚酰胺层,其中,所述多孔支撑层分为子层和表层,所述表层为窄孔径分布的小孔结构,所述子层与底层贴合、且为高度贯通的三维网络多孔结构。
7.所述复合纳滤膜包含底层、多孔支撑层和活性分离层三层结构,其中多孔支撑层位于底层和活性分离层之间,主要提供机械强度和流体传输通道;活性分离层主要起分离筛分作用。
8.所述底层的材料可以包括但不限于:无纺布、有纺布、聚酯筛网、静电纺丝膜等多孔支撑材料。
9.所述活性分离层是由含有两个或两个以上氨基的胺类化合物和含有两个或两个以上酰氯基的酰氯化合物在多孔支撑层上通过界面聚合反应形成的。
10.优选地,所述活性分离层通过将脂肪族多官能胺化合物与芳香族多官能酰氯化合物进行界面聚合反应制备得到,其中所述脂肪族多官能胺化合物优选为聚乙烯亚胺、乙二胺、哌嗪、4-氨基甲基哌嗪中的至少一种,所述芳香族多官能酰氯化合物优选为对苯二甲酰氯、间苯二甲酰氯、邻苯二甲酰氯、联苯二甲酰氯、苯二磺酰氯、均苯三甲酰氯中的至少一种。
11.所述多孔支撑层采用雾化预处理辅助非溶剂诱导相分离法制备得到,特点在于诱导相分离制备支撑层的过程分为两步,雾化预处理工艺结合非溶剂诱导相分离,即成膜首先在雾化液滴浴中停留进行部分诱导相分离,接着进入非溶剂凝固浴进行完全相分离。
12.制备所述多孔支撑层的聚合物选自聚氯乙烯、聚砜、聚醚砜、磺化聚醚砜、聚丙烯腈、醋酸纤维素、聚偏氟乙烯、聚酰亚胺、聚丙烯酸、聚乳酸、聚酰胺、壳聚糖、聚醚酰亚胺、聚苯乙烯、聚烯烃、聚酯、聚三氟氯乙烯、有机硅树脂、丙烯腈-苯乙烯共聚物以及它们的改性聚合物中的至少一种。
13.所述多孔支撑层为不对称结构,其具有一层薄的表层,以及与底层贴合的子层,所述子层具有双连续高度贯通的三维网络多孔结构,可以减少水传递阻力,增加水通量;所述表层与活性分离层贴合。
14.所述支撑层的表层平均孔径为10~50nm。
15.所述支撑层的子层为互相贯通的三维网络多孔结构,其孔结构高度贯通并具有较大的孔隙率。所述支撑层的子层的断面为沿膜厚度方向上形貌基本保持一致的聚合物纤维骨架和孔洞的结构,即所述子层断面为沿膜厚度方向上分布着聚合物纤维骨架和同一类型孔洞的结构。例如传统的非溶剂相分离法得到的超滤膜就经常会有不同类型孔洞结构同时出现在子层断面上,通常包括海绵状孔结构和大的指状孔结构。
16.所述多孔支撑层的孔隙率为40~90%,优选为60~90%,更优选为70~80%。
17.本发明所述复合纳滤膜中,所述底层的厚度为50~300μm,所述多孔支撑层子层的厚度为10~60μm,所述多孔支撑层表层的厚度为0.5~5μm,所述活性分离层的厚度为5~100nm。
18.本发明的目的之二在于提供所述复合纳滤膜的制备方法,包括以下步骤:
19.1)将包含多孔支撑层的聚合物在内的组分溶解于溶剂中配制铸膜液;
20.2)将铸膜液在底层上刮铸;
21.3)进行雾化预处理,雾化预处理为在雾化的液滴浴中停留,其中将底层面朝向雾化液滴,并保护膜涂覆有铸膜液的一面不接触雾化液滴;
22.4)浸入凝固浴,得到所述多孔支撑层;
23.5)将所述多孔支撑层依次与含有脂肪族多官能胺化合物的水相溶液、以及含有芳香族多官能酰氯化合物的有机相溶液接触;
24.6)干燥、热处理制得所述复合纳滤膜。
25.步骤1)中,所述聚合物可选自本领域通常的过滤膜用聚合物材料,可使用的聚合物材料可以包括但不限于:聚氯乙烯、聚砜、聚醚砜、磺化聚醚砜、聚丙烯腈、醋酸纤维素、聚偏氟乙烯、聚酰亚胺、聚丙烯酸、聚乳酸、聚酰胺、壳聚糖、聚醚酰亚胺、聚苯乙烯、聚烯烃、聚酯、聚三氟氯乙烯、有机硅树脂、丙烯腈-苯乙烯共聚物类等,以及它们改性后的聚合物中的至少一种。
26.步骤1)中,所述铸膜液中聚合物的固含量为6wt%~20wt%,优选为8wt%~18wt%。
27.所述铸膜液中还可以包含常用的添加剂等组分。
28.所述制膜添加剂为可以为在制膜聚合物良溶剂中互溶且具有亲水性的高分子材料,可以包括但不限于:壳聚糖、聚乙烯吡咯烷酮、聚乙二醇、聚乙烯醇、丙三醇、丙二醇、丙酮、聚氧乙烯聚氧丙烯醚嵌段共聚物等中的至少一种。所述制膜添加剂也可以包括通常过滤膜制备过程中所需的常用无机盐致孔剂、不良溶剂和/或者各种无机纳米粒子如纳米级的无机填料,包括但不限于:氯化锌、氯化锂、氯化镁、溴化锂、水、各种小分子醇等;无机填料有二氧化锰、二氧化硅、氧化锌等。
29.制膜添加剂的用量是常规用量,本发明中可优选:所述高分子添加剂的浓度为1~200g/l;所述小分子添加剂的浓度为0.5~50g/l。
30.步骤1)中,所述溶剂为可以溶解所述制膜聚合物和制膜添加剂的良溶剂,其包括但不限于n,n-二甲基甲酰胺、n,n-二甲基乙酰胺、丙酮、n-甲基-2-吡咯烷酮、二甲基亚砜、四甲基亚砜、四氢呋喃、二氧六环、乙腈、氯仿、polarclean溶剂、磷酸三乙酯、磷酸三甲酯、六甲基磷酸铵、四甲基脲、乙腈、甲苯、己烷、辛烷等中的至少一种,铸膜液配制时间和温度可依铸膜材料决定。
31.步骤2)中,涂覆铸膜液所需的底层材料可采用现有技术中作为涂覆高分子溶液的支撑层材料或基底材料,可以包括但不限于:无纺布、有纺布、聚酯筛网和静电纺丝膜等多孔支撑材料。
32.步骤2)中,将铸膜液均匀涂覆在底层上进行刮膜。
33.步骤2)中,用所述铸膜液涂覆湿膜,厚度没有特别限定,优选刮膜厚度为50~500μm,更优选为75~300μm。
34.本发明中用到的多孔支撑层采用雾化预处理辅助非溶剂诱导相分离法制备。即首先在雾化液滴浴中停留进行部分诱导相分离,接着进入非溶剂凝固浴进行完全相分离。
35.本发明的雾化预处理方法与通常意义上的蒸汽诱导相分离(vips)有很大的区别,后者是指在一定的高湿度(或者饱和湿度)条件下发生相分离,不会涉及雾化的液滴浴。
36.步骤3)中,所述雾化预处理,即是将铸膜液涂覆后,将膜的底层面朝向雾化液滴,在雾化的液滴浴中停留接触一定时间,并保护膜涂覆有铸膜液的一面不接触雾化液滴。其中获得雾化液滴浴的方法没有特别限定,可采用常规的各种液体雾化的方法,例如压力雾化、转盘雾化、高压气流雾化、超声波雾化等方法。
37.雾化预处理时间优选为1s~60s,更优选为2s~40s。
38.所述液滴浴中液滴的尺寸优选为1~50μm,更优选为5~20μm。
39.单位膜面积所需的雾化量为2~50l/m2·
h,优选为10~20l/m2·
h。
40.雾化预处理中液滴为所述铸膜聚合物的不良溶剂,可以为水、乙醇、乙二醇等单一组份的,也可以是水与极性非质子溶剂、表面活性剂或其它溶剂组成的,还也可是盐、酸、碱的溶液。
41.所保护膜涂覆有铸膜液的一面不接触雾化液滴的方式可采用遮蔽保护、吹气保护等常规方法。
42.步骤4)中,所述凝固浴为所述铸膜聚合物的不良溶剂,可以为水、乙醇、乙二醇等单一组份的,也可以是水与极性非质子溶剂或其它溶剂混合而成,如氢氧化钠水溶液。
43.步骤5)中,将所述多孔支撑层依次与含有两个或两个以上氨基的化合物的水相溶液、以及含有两个或两个以上酰氯基酰氯化合物的有机相溶液接触而进行界面聚合。
44.所述含有两个或两个以上氨基的化合物为脂肪族多官能胺化合物中的一种或几种。所述脂肪族多官能胺化合物优选为聚乙烯亚胺、乙二胺、哌嗪、4-氨基甲基哌嗪中的至少一种。
45.所述多孔支撑层所述水相溶液中脂肪族多官能胺化合物的浓度为0.05~2.5w/v%。
46.与含有脂肪族多官能胺化合物的水相溶液的接触时间为5~150秒。
47.所述含有两个或两个以上酰氯基的酰氯化合物为芳香族多官能酰氯化合物中的一种或几种。所述芳香族多官能酰氯化合物优选为对苯二甲酰氯、间苯二甲酰氯、邻苯二甲酰氯、联苯二甲酰氯、苯二磺酰氯、均苯三甲酰氯中的至少一种。
48.所述有机相溶液的有机溶剂优选为正己烷、环己烷、三氟三氯乙烷、正庚烷、正辛烷、甲苯、乙苯、isopar溶剂油中的一种或几种。
49.所述有机相溶液中芳香族多官能酰氯化合物的浓度为0.02~0.15w/v%。
50.所述多孔支撑层与含有芳香族多官能酰氯化合物的有机相溶液的接触时间为5~150秒。
51.步骤6)中,所述热处理的温度为25~70℃,时间为1~5分钟。
52.本发明中制备所述活性分离层的过程可优选按以下步骤进行:
53.a)将多孔支撑层与含有两个或两个以上氨基的脂肪族化合物的水相溶液接触;
54.b)将经过水相溶液浸润后的多孔支撑层表面多余的水相溶液除去,除去多余溶液的方法可选为但不限于风淋法、辊压法等;
55.c)经过处理后的多孔支撑层与含有两个或两个以上酰氯基酰氯化合物的有机相溶液接触;
56.d)干燥、热处理、水洗。
57.本发明目的之三为提供所述制备方法得到的复合纳滤膜。
58.本发明目的之四为提供所述的复合纳滤膜或者所述制备方法得到的复合纳滤膜在水处理、生物、医药、能源等领域中的应用。
59.与现有技术相比,本发明的特点在于:
60.本发明公开的方法中制备的纳滤膜支撑层结构特殊,该多孔支撑层具有窄孔径分
布的小孔分离表层和双连续高度贯通孔结构的子层,并具有较大的孔隙率,可以有效降低纳滤膜的传质阻力,增加传质通道,大幅度提高膜的渗透通量。本发明仅需要在传统的非溶剂相转化法制备复合纳滤膜支撑层工艺基础上加上雾化预处理的工艺即可。兼具制备过程简单、原料易得、成本低廉等特点,可用于连续大规模制备纳滤膜材料,易于产业化应用。在水处理、生物、医药、能源等领域有广泛的应用空间,具有良好的应用前景。
61.本发明的其它特征和优点将在随后的具体实施方式部分予以详细说明。
附图说明
62.图1为实施例3所得纳滤膜的多孔支撑层的断面形貌图。
63.图2为实施例3所得纳滤膜的表面形貌图。
64.图3为对比例1所得纳滤膜的支撑层的断面形貌图。
具体实施方式
65.下面结合具体实施例对本发明进行具体的描述,有必要在此指出的是以下实施例只用于对本发明的进一步说明,不能理解为对本发明保护范围的限制,本领域技术人员根据本发明内容对本发明做出的一些非本质的改进和调整仍属本发明的保护范围。
66.另外需要说明的是,在以下具体实施方式中所描述的各个具体技术特征,在不矛盾的情况下,可以通过任何合适的方式进行组合。为了避免不必要的重复,本发明对各种可能的组合方式不再另行说明。
67.此外,本发明的各种不同的实施方式之间也可以进行任意组合,只要其不违背本发明的思想,由此而形成的技术方案属于本说明书原始公开内容的一部分,同时也落入本发明的保护范围。
68.根据本发明一个优选的实施方式,所述复合纳滤膜的制备方法可按以下步骤进行:
[0069]1’
)将包含聚合物的组分溶解于溶剂中配制铸膜液;
[0070]2’
)将铸膜液在支撑层上刮铸成膜;
[0071]3’
)进行雾化预处理,即在雾化的液滴浴中停留一定时间,其中将底层面朝向雾化液滴,并保护膜涂覆有铸膜液的一面不接触雾化液滴;
[0072]4’
)浸入凝固浴,得到所述聚合物支撑层;
[0073]5’
)将多孔支撑层与经稀释后含有两个或两个以上氨基的脂肪族化合物的水相溶液接触,接触时间为5~150秒;
[0074]6’
)经过水相溶液浸润后的多孔支撑层用橡胶辊辊压,除去多余的水相溶液;
[0075]7’
)将经过水相溶液浸润后的多孔支撑层与含有两个或两个以上酰氯基的酰氯化合物的有机相溶液接触5~150秒,通过界面聚合反应,在多孔支撑层表面生成一层致密功能层;
[0076]8’
)最后将上述经过有机相溶液浸润后的多孔支撑层在空气中自然干燥后,在一定温度下后处理1~5分钟,经过水洗后即得到本发明的纳滤复合膜。
[0077]
在以下实施例和对比例中:
[0078]
(1)复合纳滤膜的水通量通过以下方法测试得到:将复合纳滤透膜装入膜池中,在
0.5mpa下预压0.5小时后,在压力为0.5mpa、温度为25℃的条件下测得1h内所述复合纳滤膜的水透过量,并通过以下公式计算得到:
[0079]
j=q/a
·
t,
[0080]
其中,j为水通量,q为水透过量(l),a为复合纳滤膜的有效膜面积(m2),t为时间(h);
[0081]
(2)复合纳滤膜的脱盐率通过以下方法测试得到:将复合纳滤膜装入膜池中,在0.5mpa下预压0.5h后,在压力为0.5mpa、温度为25℃条件下测得1h内初始浓度为2g
·
l-1
mgso4原水溶液与透过液中mgso4的浓度变化,并通过以下公式计算得到:
[0082]
r=(c
p-cf)/c
p
×
100%,
[0083]
其中,r为脱盐率(%),c
p
为原液中mgso4的浓度(g/l或mol/l),cf为透过液中mgso4的浓度(g/l或mol/l);
[0084]
本发明实施例中,所用化学试剂均为市售产品,除非单独提出,都没有特殊提纯处理。
[0085]
喷雾设备:超声波加湿器选用浩奇hq-js130h。
[0086]
实施例1
[0087]
(1)多孔支撑层制备:将12g聚丙烯腈溶于88g dmf溶剂中,50℃下加热搅拌成均匀溶液,抽真空脱泡;接着采用连续刮膜机将其刮涂在无纺布上,涂布时塞尺厚度控制为200μm,然后将涂布后膜的背面朝向去离子水超声波雾化得到的液滴浴,在液滴浴中停留20s,并保护膜涂覆有铸膜液的一面不接触雾化液滴,单位膜面积的雾化量为6.2l/m2·
h;再将上述薄膜浸入去离子水凝固浴中完全相分离;经过水洗后得到多孔支撑层。
[0088]
(2)复合膜制备:称取一定量的水相单体哌嗪(pip)于容量瓶中,用去离子水定容到刻度,超声溶解成含0.5w/v%pip的均一水相溶液。称取一定量的有机相单体均苯三甲酰氯(tmc)于容量瓶中,用isopar溶剂油定容到刻度,超声溶解成含0.1w/v%tmc的均一有机相溶液。使用步骤(1)中制备的聚丙烯腈多孔支撑膜,与上述水相溶液浸润接触30秒。之后倒掉多余水相溶液,用干净橡胶辊将膜表面辊干,然后将膜与均苯三甲酰氯有机相溶液浸润接触30秒。之后倒掉多余有机相溶液,然后将形成的聚酰胺层在空气中晾干,在常温下后处理4min,得到复合纳滤膜。制备好的复合纳滤膜保存在去离子水中,测试备用。
[0089]
实施例1所得复合纳滤膜中,所述底层的厚度为85μm,所述多孔支撑层子层的厚度为44μm,所述多孔支撑层表层的厚度为2.1μm,所述活性分离层的厚度为46nm。所述支撑层表层的平均孔径为17nm。
[0090]
实施例2
[0091]
按照实施例1的方法制备纳滤膜,不同的是,在步骤(1)纳滤膜支撑层制备过程中,在雾化预处理阶段采用雾化液滴的雾化量为10l/m2·
h。
[0092]
实施例2所得复合纳滤膜中,所述底层的厚度为85μm,所述多孔支撑层子层的厚度为45μm,所述多孔支撑层表层的厚度为2.0μm,所述活性分离层的厚度为43nm。所述支撑层表层的平均孔径为18nm。
[0093]
实施例3
[0094]
按照实施例1的方法制备纳滤膜,不同的是,在步骤(1)纳滤膜支撑层制备过程中,在雾化预处理阶段采用雾化液滴的雾化量为17l/m2·
h。纳滤膜的多孔支撑层的断面形貌
见图1,纳滤膜的表面形貌见图2。
[0095]
实施例3所得复合纳滤膜中,所述底层的厚度为85μm,所述多孔支撑层子层的厚度为43μm,所述多孔支撑层表层的厚度为1.9μm,所述活性分离层的厚度为43nm。所述支撑层表层的平均孔径为19nm。
[0096]
实施例4
[0097]
按照实施例3的方法制备纳滤膜,不同的是,在步骤(1)纳滤膜支撑层制备过程中,在雾化预处理阶段将涂布后膜的背面朝向去离子水超声波雾化得到的液滴浴,在液滴浴中停留10s。
[0098]
实施例4所得复合纳滤膜中,所述底层的厚度为85μm,所述多孔支撑层子层的厚度为44μm,所述多孔支撑层表层的厚度为2.2μm,所述活性分离层的厚度为45nm。所述支撑层表层的平均孔径为17nm。
[0099]
实施例5
[0100]
按照实施例3的方法制备纳滤膜,不同的是,在步骤(1)纳滤膜支撑层制备过程中,在雾化预处理阶段将涂布后膜的背面朝向去离子水超声波雾化得到的液滴浴,在液滴浴中停留30s。
[0101]
实施例5所得复合纳滤膜中,所述底层的厚度为85μm,所述多孔支撑层子层的厚度为48μm,所述多孔支撑层表层的厚度为1.7μm,所述活性分离层的厚度为41nm。所述支撑层表层的平均孔径为23nm。
[0102]
实施例6
[0103]
按照实施例3的方法制备纳滤膜,不同的是,在步骤(1)纳滤膜支撑层制备过程中,在雾化预处理阶段将涂布后膜的背面朝向去离子水超声波雾化得到的液滴浴,在液滴浴中停留40s。
[0104]
实施例6所得复合纳滤膜中,所述底层的厚度为85μm,所述多孔支撑层子层的厚度为51μm,所述多孔支撑层表层的厚度为1.7μm,所述活性分离层的厚度为38nm。所述支撑层表层的平均孔径为57nm。
[0105]
实施例7
[0106]
按照实施例3的方法制备纳滤膜,不同的是,在步骤(1)纳滤膜支撑层制备过程中,在雾化预处理阶段将涂布后膜的背面朝向去离子水超声波雾化得到的液滴浴,在液滴浴中停留50s。
[0107]
实施例7所得复合纳滤膜中,所述底层的厚度为85μm,所述多孔支撑层子层的厚度为54μm,所述多孔支撑层表层的厚度为1.5μm,所述活性分离层的厚度为36nm。所述支撑层表层的平均孔径为223nm。
[0108]
对比例1
[0109]
按照实施例3的方法制备纳滤膜,不同的是,在纳滤膜支撑层制备过程中,不经雾化预处理阶段,直接将超滤膜浸入溶剂凝固浴进行完全相分离,经过水洗后得到支撑层。支撑层的断面形貌见图3。
[0110]
对比例1所得复合纳滤膜中,所述活性分离层的厚度为46nm。所述支撑层的平均孔径为14nm。
[0111]
在操作压力为0.5mpa、温度为25℃的测试条件下,使用2g
·
l-1
mgso4水溶液测试上
述实施例1-7和对比例1制备的纳滤膜的水通量和截留率,测试的所得结果见表1。
[0112]
表1
[0113][0114]
从以上实施例3-5和对比例1的结果可以看出,通过采用雾化预处理后的支撑层制备的复合纳滤膜具有优异的水通量和截盐率,且在截盐率保持恒定的前提下,纳滤膜水通量随着雾化时间的增大而增大。从实施例6-7可以看出,随着雾化时间的进一步增加,支撑层的表面孔径变大,不利于形成完整的聚酰胺分离层,导致纳滤膜的截盐率下降明显。从实施例1-3可以看出,纳滤膜的渗透通量随着雾化量的增加而增加。
[0115]
实施例8
[0116]
(1)多孔支撑层制备:将12g聚砜、0.5g聚乙烯吡咯烷酮(pvp)溶于87.5g polarclean溶剂中,100℃下加热搅拌成均匀溶液,抽真空脱泡;接着采用连续刮膜机将其刮涂在无纺布上,涂布时塞尺厚度控制为200μm,然后将涂布后膜的背面(无纺布侧)朝向去离子水超声波雾化得到的液滴浴,在液滴浴中停留4s,并保护膜涂覆有铸膜液的一面不接触雾化液滴,单位膜面积的雾化量为17l/m2·
h;再将上述薄膜浸入去离子水凝固浴中完全相分离;经过水洗后得到多孔支撑层。
[0117]
(2)复合膜制备:称取一定量的水相单体哌嗪(pip)于容量瓶中,用去离子水定容到刻度,超声溶解成含0.5w/v%pip的均一水相溶液。称取一定量的有机相单体均苯三甲酰氯(tmc)于容量瓶中,用isopar溶剂油定容到刻度,超声溶解成含0.1w/v%tmc的均一有机相溶液。使用步骤(1)中制备的聚砜多孔支撑膜,与上述水相溶液浸润接触30秒。之后倒掉多余水相溶液,用干净橡胶辊将膜表面辊干,然后将膜与均苯三甲酰氯有机相溶液浸润接触30秒。之后倒掉多余有机相溶液,然后将形成的聚酰胺层在空气中晾干,在常温下后处理4min,得到复合纳滤膜。制备好的复合纳滤膜保存在去离子水中,测试备用。
[0118]
实施例8所得复合纳滤膜中,所述底层的厚度为85μm,所述多孔支撑层子层的厚度为47μm,所述多孔支撑层表层的厚度为1.5μm,所述活性分离层的厚度为46nm。所述支撑层表层的平均孔径为21nm。
[0119]
实施例9
[0120]
按照实施例8的方法制备纳滤膜,不同的是,在步骤(1)纳滤膜支撑层制备过程中,在雾化预处理阶段将涂布后膜的背面朝向去离子水超声波雾化得到的液滴浴,在液滴浴中停留6s。
[0121]
实施例9所得复合纳滤膜中,所述底层的厚度为85μm,所述多孔支撑层子层的厚度为51μm,所述多孔支撑层表层的厚度为1.4μm,所述活性分离层的厚度为42nm。所述支撑层表层的平均孔径为24nm。
[0122]
实施例10
[0123]
按照实施例8的方法制备纳滤膜,不同的是,在步骤(1)纳滤膜支撑层制备过程中,在雾化预处理阶段将涂布后膜的背面朝向去离子水超声波雾化得到的液滴浴,在液滴浴中停留8s。
[0124]
实施例10所得复合纳滤膜中,所述底层的厚度为85μm,所述多孔支撑层子层的厚度为53μm,所述多孔支撑层表层的厚度为1.3μm,所述活性分离层的厚度为39nm。所述支撑层表层的平均孔径为167nm。
[0125]
实施例11
[0126]
按照实施例8的方法制备纳滤膜,不同的是,在步骤(1)纳滤膜支撑层制备过程中,在雾化预处理阶段将涂布后膜的背面朝向去离子水超声波雾化得到的液滴浴,在液滴浴中停留12s。
[0127]
实施例11所得复合纳滤膜中,所述底层的厚度为85μm,所述多孔支撑层子层的厚度为55μm,所述多孔支撑层表层的厚度为1.1μm,所述活性分离层的厚度为35nm。所述支撑层表层的平均孔径为289nm。
[0128]
实施例12
[0129]
按照实施例8的方法制备纳滤膜,不同的是,在步骤(1)纳滤膜支撑层制备过程中,在雾化预处理阶段将涂布后膜的背面朝向去离子水超声波雾化得到的液滴浴,在液滴浴中停留24s。
[0130]
实施例12所得复合纳滤膜中,所述底层的厚度为85μm,所述多孔支撑层子层的厚度为57μm,所述多孔支撑层表层的厚度为1.0μm,所述活性分离层的厚度为34nm。所述支撑层表层的平均孔径为402nm。
[0131]
对比例2
[0132]
按照实施例8的方法制备纳滤膜,不同的是,在纳滤膜支撑层制备过程中,不经雾化预处理阶段,直接将超滤膜浸入溶剂凝固浴进行完全相分离,经过水洗后得到支撑层。
[0133]
对比例2所得复合纳滤膜中,所述活性分离层的厚度为49nm。所述支撑层的平均孔径为16nm。
[0134]
在操作压力为0.5mpa、温度为25℃的测试条件下,使用2g
·
l-1
mgso4水溶液测试上述实施例8-12和对比例2制备的纳滤膜的水通量和截留率,测试的所得结果见表2。
[0135]
表2
[0136][0137]
从以上实施例和对比例的结果可以看出,通过采用雾化预处理后的支撑层制备的纳滤膜具有优异的水通量和截盐率。其中,雾化时间对纳滤膜的渗透性能影响较大,当雾化预处理时间在一定范围内,支撑层的表层孔径较小,易于在界面聚合过程中生成完整的聚酰胺活性层,膜的分离渗透性能提高,随着雾化预处理时间的继续增加,纳滤膜的水通量和截盐率下降明显。
再多了解一些
本文用于创业者技术爱好者查询,仅供学习研究,如用于商业用途,请联系技术所有人。