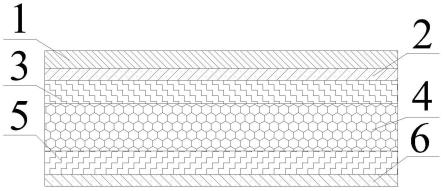
1.本发明属于车内装饰板材领域,具体涉及一种汉麻纤维增强有机复合材料车内饰板及其制备方法。
背景技术:
2.现有车内饰板大多采用聚丙烯(pp)丙烯腈-丁二烯-苯乙烯塑料(abs)和聚碳酸酯(pc)等作为原料,这类采用具有较好的抗菌性能和抗静电性能,但是制备过程污染大,且不易降解和回收困难,对生态环境产生的破坏愈加严重。寻求以可循环、可生物降解等符合可持续发展要求的天然纤维为增强体的复合材料引起人们的关注。汉麻韧皮纤维具有韧性强、拉伸强度高,纤维力学性能优良等优秀性能,作为新世纪人工合成纤维的替代产品,具有广阔的应用前景。全球约90%汉麻纤维产自中国,黑龙江省依靠独特的汉麻种植地域优势,成为我国汉麻天然纤维的主要产区。因此,加快汉麻纤维增强复合材料的研发,拓展汉麻纤维增强复合材料的适用领域,对发挥我国的独特优势,构建循环经济,加强材料领域的可持续、绿色健康发展具有重要意义。
3.我国种植的汉麻(hemp)属纤维型大麻,也称工业大麻(cannabis sativa l).,汉麻韧皮纤维作为增强体的复合材料具有良好透气、吸湿、隔热和吸音等优良性能,用汉麻纤维作增强体与不同种类聚合物基质,如可降解聚乳酸、聚己内酯等树脂,加入少量改性剂、添加剂,经混合、熔融或层叠等成型工艺制备轻质、高强、降噪等高性能天然纤维复合材料,有关的研发正在成为全球研究的热点,目前已经成为环境新材料研究领域的重要方向。
技术实现要素:
4.本发明的目的是要解决现有车内饰板存在制备过程污染大,且不易降解和回收困难的问题,而提供一种汉麻纤维增强有机复合材料车内饰板及其制备方法。
5.一种汉麻纤维增强有机复合材料车内饰板包括隔热层、吸音承接层、第一吸音芯层、吸音骨架层、第二吸音芯层和吸音面层,由所述吸音承接层、所述第一吸音芯层、所述吸音骨架层、所述第二吸音芯层和所述吸音面层组成吸音层,所述吸音承接层背离所述隔热层的另一侧面与所述第一吸音芯层的一侧面连接,所述第一吸音芯层背离所述吸音承接层方向的另一侧面与所述吸音骨架层的一侧面连接,所述吸音骨架层背离所述第一吸音芯层方向的另一侧面与所述第二吸音芯层的一侧面连接,所述第二吸音芯层背离所述吸音骨架层方向的另一侧面与所述吸音面层的一侧面连接,所述吸音层的总厚度不低于9mm;所述吸音承接层背离所述第一吸音芯层方向的一侧面与所述隔热层连接。
6.一种汉麻纤维增强有机复合材料车内饰板的制备方法,其特征在于它是按以下步骤完成的:
7.一、制备隔热纸层:
①
、按照重量份数称取35~65份汉麻纤维、1~5份玄武岩纤维、20~30份聚乳酸纤维和5份羧甲基纤维素;所述汉麻纤维的长度为3mm~12mm,所述玄武岩纤维的长度为3mm~12mm,所述聚乳酸纤维的长度为3mm~12mm;
②
、将步骤二
①
中称取的汉
麻纤维和聚乳酸纤维浸没于水中润胀,再加入水进行疏解使纤维均匀分布于水中,得到混合纤维浆料i;
③
、将步骤二
①
中称取的羧甲基纤维素放入水中溶解,得到羧甲基纤维素溶液;
④
、向混合纤维浆料i中加入羧甲基纤维素溶液和步骤二
①
中称取的玄武岩纤维,再加入水进行疏解使纤维均匀分布于水中,得到混合纤维浆料ⅱ;
⑤
、利用抄片器将混合纤维浆料ⅱ进行抄片,得到湿混合纤维层i;
⑥
、将湿混合纤维层i进行阴干,得到隔热纸层;所述隔热纸的厚度为0.1mm~0.5mm;
8.二、制备吸音层:
9.a、制备高麻双熔点复合纤维层:
①
、将汉麻纤维和聚乳酸纤维浸没于水中润胀,再加入水进行疏解使纤维均匀分布于水中,得到汉麻/聚乳酸混合纤维浆料i;
②
、利用抄片器将汉麻/聚乳酸混合纤维浆料i进行抄片,得到湿汉麻/聚乳酸混合纤维层i;
③
、将湿汉麻/聚乳酸混合纤维层i进行阴干,得到单层汉麻/聚乳酸混合纤维层i;
④
、按照需求厚度将单层汉麻/聚乳酸混合纤维层i交替铺设,得到高麻双熔点复合纤维层;所述高麻双熔点复合纤维层中汉麻纤维的质量分数为70%~80%,聚乳酸纤维的质量分数为20%~30%;
10.b、制备低麻双熔点复合纤维层:
①
、将汉麻纤维和聚乳酸纤维浸没于水中润胀,再加入水进行疏解使纤维均匀分布于水中,得到汉麻/聚乳酸混合纤维浆料ii;
②
、利用抄片器将汉麻/聚乳酸混合纤维浆料ii进行抄片,得到湿汉麻/聚乳酸混合纤维层ii;
③
、将湿混合纤维层ii进行阴干,得到单层汉麻/聚乳酸混合纤维层ii;
④
、按照需求厚度将单层汉麻/聚乳酸混合纤维层ii交替铺设,得到低麻双熔点复合纤维层;所述低麻双熔点复合纤维层中汉麻纤维的质量分数为30%~60%,聚乳酸纤维的质量分数为40%~70%;
11.c、针刺:先将一层高麻双熔点复合纤维层和一层低麻双熔点复合纤维层叠放,然后采用针刺机进行垂直针刺,得到低麻-高麻复合纤维毡;
12.d、成型:
①
、以多孔芯层骨架层作为吸音骨架层,以低麻双熔点复合纤维层作为吸音承接层和吸音面层,以高麻双熔点复合纤维层作为第一吸音芯层和第二吸音芯层的材料,依次按照低麻双熔点复合纤维层、高麻双熔点复合纤维层、多孔芯层骨架层、高麻双熔点复合纤维层和的低麻双熔点复合纤维层形式将低麻-高麻复合纤维毡、多孔芯层骨架和低麻-高麻复合纤维毡依次叠放,且多孔芯层骨架的相对两侧分别与低麻-高麻复合纤维毡的高麻双熔点复合纤维层一侧刷胶连接,得到纤维坯料;
②
、将纤维坯料置于烘箱中进行热固成型,得到汉麻纤维增强有机复合型材;
③
、按照需求厚度调整两个热辊的间距,然后利用热辊对汉麻纤维增强有机复合型材进行表面整饰,得到吸音层;
13.三、组装:以隔热纸层作为隔热层,将隔热层与吸音层的吸音承接层背离第一吸音芯层方向的一侧通过刷胶连接,得到汉麻纤维增强有机复合材料车内饰板。
14.本发明优点:一、本发明汉麻纤维增强有机复合材料车内饰板以隔热层作为表层,利用隔热层将吸音层与外界隔离,起到良好的隔热保温效果。二、本发明汉麻纤维增强有机复合材料车内饰板的吸音承接层、第一吸音芯层、第二吸音芯层和吸音面层以汉麻纤维和聚乳酸纤维为原料,并采用针刺方法将吸音承接层和第一吸音芯层之间或吸音承接层和第一吸音芯层之间进行预连接,多孔芯层骨架的相对两侧分别与第一吸音芯层和第二吸音芯层刷胶连接,再热固成型和表面整饰得到吸音层,汉麻纤维的吸声性能与气流阻力有关,气流阻力反映空气通过单元材料的阻力,而针刺可以改善中低频区域的吸声性能。本发明采用针刺方法使吸音层具有良好的吸音性能。三、本发明汉麻纤维增强有机复合材料车内饰
板采用的原料大部分都能够降解,或者回收再利用,不会给环境造成破坏。
附图说明
15.图1是本发明一种汉麻纤维增强有机复合材料车内饰板的结构示意图。
16.图2是蜂窝层芯层骨架的结构示意图。
17.图3是多层瓦楞增强型芯层骨架的结构示意图。
18.附图中:1-隔热层、2-吸音承接层、3-第一吸音芯层、4-吸音骨架层、5-第二吸音芯层、6-吸音面层。
具体实施方式
19.具体实施方式一:如图1所示,本实施方式是一种汉麻纤维增强有机复合材料车内饰板,它包括隔热层1、吸音承接层2、第一吸音芯层3、吸音骨架层4、第二吸音芯层5和吸音面层6,由所述吸音承接层2、所述第一吸音芯层3、所述吸音骨架层4、所述第二吸音芯层5和所述吸音面层6组成吸音层,所述吸音承接层2背离所述隔热层1的另一侧面与所述第一吸音芯层3的一侧面连接,所述第一吸音芯层3背离所述吸音承接层2方向的另一侧面与所述吸音骨架层4的一侧面连接,所述吸音骨架层4背离所述第一吸音芯层3方向的另一侧面与所述第二吸音芯层5的一侧面连接,所述第二吸音芯层5背离所述吸音骨架层4方向的另一侧面与所述吸音面层6的一侧面连接,所述吸音层2的总厚度不低于9mm;所述吸音承接层2背离所述第一吸音芯层3方向的一侧面与所述隔热层1连接。
20.具体实施方式二:本实施方式与具体实施方式一不同点是:所述隔热层1的厚度为0.1mm~0.5mm。其他与具体实施方式一相同。
21.隔热层1不能太薄,不然无法起到隔热效果。
22.具体实施方式三:本实施方式与具体实施方式一或二之一不同点是:所述吸音承接层2和所述吸音面层6的厚度相同,所述第一吸音芯层3和第二吸音芯层5的厚度相同,且所述第一面层1与所述吸音骨架层3的厚度比为(0.5~1.5):3,所述第一芯层2与所述吸音骨架层3的厚度比为(1~2):3。其他与具体实施方式一或二相同。
23.具体实施方式四:本实施方式与具体实施方式一至三之一不同点是:所述隔热层1为隔热纸层;所述第一吸音芯层3和所述第二吸音芯层5均为高麻双熔点复合纤维层;所述吸音承接层2和所述吸音面层6均为低麻双熔点复合纤维层;所述吸音骨架层4为多孔芯层骨架层。其他与具体实施方式一至三相同。
24.具体实施方式五:结合图2和图3,本实施方式与具体实施方式一至四之一不同点是:所述多孔芯层骨架层为蜂窝层芯层骨架或多层瓦楞增强型芯层骨架。其他与具体实施方式一至四相同。
25.本实施方式中蜂窝层芯层骨架或多层瓦楞增强型芯层骨架选自中国已公开文章《sio2气凝胶/纤维复合隔热包装材料的制备及隔热机理研究》(哈尔滨工程大学,2014,博士论文,赵红,11-12页)。
26.多层瓦楞增强型芯层骨架的过程方法:将纤维定向铺设,制成瓦楞板,将瓦楞板沿厚度方向切割,得到瓦楞条,再将瓦楞条以瓦楞的孔道朝向厚度方向进行平铺,制成多层瓦楞增强型芯层骨架;一方面以瓦楞的孔道作为吸音结构,使多层瓦楞增强型芯层骨架具有
吸引性能,另一方面,多层瓦楞增强型芯层骨架中部分纤维沿厚度方向设置,纤维微观孔道能够进一步使多层瓦楞增强型芯层骨架的吸音性能增强。
27.具体实施方式六:本实施方式与具体实施方式一至五之一不同点是:所述隔热纸层按重量份数由35~65份汉麻纤维、1~5份玄武岩纤维、20~30份聚乳酸纤维和5份羧甲基纤维素复合而成。其他与具体实施方式一至五相同。
28.具体实施方式七:本实施方式与具体实施方式一至六之一不同点是:所述低麻双熔点复合纤维层由汉麻纤维和聚乳酸纤维复合而成,且所述低麻双熔点复合纤维中汉麻纤维的质量分数为30%~50%,聚乳酸纤维的质量分数为50%~70%;所述高麻双熔点复合纤维层由汉麻纤维和聚乳酸纤维复合而成,且所述高麻双熔点复合纤维中汉麻纤维的质量分数为70%~80%,聚乳酸纤维的质量分数为20%~30%。其他与具体实施方式一至六相同。
29.具体实施方式八:结合图1,本实施方式是一种汉麻纤维增强有机复合材料车内饰板的制备方法,具体是按以下步骤完成的:
30.一、制备隔热纸层:
①
、按照重量份数称取35~65份汉麻纤维、1~5份玄武岩纤维、20~30份聚乳酸纤维和5份羧甲基纤维素;所述汉麻纤维的长度为3mm~12mm,所述玄武岩纤维的长度为3mm~12mm,所述聚乳酸纤维的长度为3mm~12mm;
②
、将步骤二
①
中称取的汉麻纤维和聚乳酸纤维浸没于水中润胀,再加入水进行疏解使纤维均匀分布于水中,得到混合纤维浆料i;
③
、将步骤二
①
中称取的羧甲基纤维素放入水中溶解,得到羧甲基纤维素溶液;
④
、向混合纤维浆料i中加入羧甲基纤维素溶液和步骤二
①
中称取的玄武岩纤维,再加入水进行疏解使纤维均匀分布于水中,得到混合纤维浆料ⅱ;
⑤
、利用抄片器将混合纤维浆料ⅱ进行抄片,得到湿混合纤维层i;
⑥
、将湿混合纤维层i进行阴干,得到隔热纸层;所述隔热纸的厚度为0.1mm~0.5mm;
31.二、制备吸音层:
32.a、制备高麻双熔点复合纤维层:
①
、将汉麻纤维和聚乳酸纤维浸没于水中润胀,再加入水进行疏解使纤维均匀分布于水中,得到汉麻/聚乳酸混合纤维浆料i;
②
、利用抄片器将汉麻/聚乳酸混合纤维浆料i进行抄片,得到湿汉麻/聚乳酸混合纤维层i;
③
、将湿汉麻/聚乳酸混合纤维层i进行阴干,得到单层汉麻/聚乳酸混合纤维层i;
④
、按照需求厚度将单层汉麻/聚乳酸混合纤维层i交替铺设,得到高麻双熔点复合纤维层;所述高麻双熔点复合纤维层中汉麻纤维的质量分数为70%~80%,聚乳酸纤维的质量分数为20%~30%;
33.b、制备低麻双熔点复合纤维层:
①
、将汉麻纤维和聚乳酸纤维浸没于水中润胀,再加入水进行疏解使纤维均匀分布于水中,得到汉麻/聚乳酸混合纤维浆料ii;
②
、利用抄片器将汉麻/聚乳酸混合纤维浆料ii进行抄片,得到湿汉麻/聚乳酸混合纤维层ii;
③
、将湿混合纤维层ii进行阴干,得到单层汉麻/聚乳酸混合纤维层ii;
④
、按照需求厚度将单层汉麻/聚乳酸混合纤维层ii交替铺设,得到低麻双熔点复合纤维层;所述低麻双熔点复合纤维层中汉麻纤维的质量分数为30%~60%,聚乳酸纤维的质量分数为40%~70%;
34.c、针刺:先将一层高麻双熔点复合纤维层和一层低麻双熔点复合纤维层叠放,然后采用针刺机进行垂直针刺,得到低麻-高麻复合纤维毡;
35.d、成型:
①
、以多孔芯层骨架层作为吸音骨架层4,以低麻双熔点复合纤维层作为吸音承接层2和吸音面层6,以高麻双熔点复合纤维层作为第一吸音芯层3和第二吸音芯层5
的材料,依次按照低麻双熔点复合纤维层、高麻双熔点复合纤维层、多孔芯层骨架层、高麻双熔点复合纤维层和的低麻双熔点复合纤维层形式将低麻-高麻复合纤维毡、多孔芯层骨架和低麻-高麻复合纤维毡依次叠放,且多孔芯层骨架的相对两侧分别与低麻-高麻复合纤维毡的高麻双熔点复合纤维层一侧刷胶连接,得到纤维坯料;
②
、将纤维坯料置于烘箱中进行热固成型,得到汉麻纤维增强有机复合型材;
③
、按照需求厚度调整两个热辊的间距,然后利用热辊对汉麻纤维增强有机复合型材进行表面整饰,得到吸音层;
36.三、组装:以隔热纸层作为隔热层1,将隔热层1与吸音层的吸音承接层2背离第一吸音芯层3方向的一侧通过刷胶连接,得到汉麻纤维增强有机复合材料车内饰板。
37.具体实施方式九:本实施方式与具体实施方式八的不同点是:步骤二c中采用针刺机利用细针在针刺力为5n~20n下进行垂直针刺,按照间距为1mm~10mm均匀垂直针刺,单面均匀垂直针刺1遍后翻面继续垂直针刺,单面共垂直针刺2~5遍,得到纤维毡。其他与具体实施方式八相同。
38.具体实施方式十:本实施方式与具体实施方式八或九之一不同点是:步骤二d
②
中所述热固成型具体操作如下:在温度为100~220℃下热固10min~30min;步骤二d
③
中所述热辊的温度为100~220℃。其他与具体实施方式八或九相同。
39.本发明内容不仅限于上述各实施方式的内容,其中一个或几个具体实施方式的组合同样也可以实现发明的目的。
40.采用下述实验验证本发明效果:
41.实施例1:如图1和图3所示,一种汉麻纤维增强有机复合材料车内饰板的制备方法,所述汉麻纤维增强有机复合材料车内饰板包括隔热层1、吸音承接层2、第一吸音芯层3、吸音骨架层4、第二吸音芯层5和吸音面层6,由所述吸音承接层2、所述第一吸音芯层3、所述吸音骨架层4、所述第二吸音芯层5和所述吸音面层6组成吸音层,所述吸音承接层2背离所述隔热层1的另一侧面与所述第一吸音芯层3的一侧面连接,所述第一吸音芯层3背离所述吸音承接层2方向的另一侧面与所述吸音骨架层4的一侧面连接,所述吸音骨架层4背离所述第一吸音芯层3方向的另一侧面与所述第二吸音芯层5的一侧面连接,所述第二吸音芯层5背离所述吸音骨架层4方向的另一侧面与所述吸音面层6的一侧面连接,所述吸音层的总厚度为15mm;所述吸音承接层2背离所述第一吸音芯层3方向的一侧面与所述隔热层1连接;所述隔热层1的厚度为0.3mm;所述吸音承接层2和所述吸音面层6的厚度相同,所述第一吸音芯层3和第二吸音芯层5的厚度相同,且所述第一面层1与所述吸音骨架层3的厚度比为1:3,所述第一芯层2与所述吸音骨架层3的厚度比为2.5:3;所述隔热层1为隔热纸层;所述第一吸音芯层3和所述第二吸音芯层5均为高麻双熔点复合纤维层;所述吸音承接层2和所述吸音面层6均为低麻双熔点复合纤维层;所述吸音骨架层4为多孔芯层骨架层;所述多孔芯层骨架层为多层瓦楞增强型芯层骨架;
42.具体是按以下步骤完成的:
43.一、制备隔热纸层:
①
、按照重量份数称取50份汉麻纤维、3份玄武岩纤维、25份聚乳酸纤维和5份羧甲基纤维素;所述汉麻纤维的长度为8mm,所述玄武岩纤维的长度为8mm,所述聚乳酸纤维的长度为8mm;
②
、将步骤二
①
中称取的汉麻纤维和聚乳酸纤维浸没于水中润胀,再加入水进行疏解使纤维均匀分布于水中,得到混合纤维浆料i;
③
、将步骤二
①
中称取的羧甲基纤维素放入水中溶解,得到羧甲基纤维素溶液;
④
、向混合纤维浆料i中加入羧
甲基纤维素溶液和步骤二
①
中称取的玄武岩纤维,再加入水进行疏解使纤维均匀分布于水中,得到混合纤维浆料ⅱ;
⑤
、利用抄片器将混合纤维浆料ⅱ进行抄片,得到湿混合纤维层i;
⑥
、将湿混合纤维层i进行阴干,得到隔热纸层;
44.二、制备吸音层:
45.a、制备高麻双熔点复合纤维层:
①
、将汉麻纤维和聚乳酸纤维浸没于水中润胀,再加入水进行疏解使纤维均匀分布于水中,得到汉麻/聚乳酸混合纤维浆料i;
②
、利用抄片器将汉麻/聚乳酸混合纤维浆料i进行抄片,得到湿汉麻/聚乳酸混合纤维层i;
③
、将湿汉麻/聚乳酸混合纤维层i进行阴干,得到单层汉麻/聚乳酸混合纤维层i;
④
、按照需求厚度将单层汉麻/聚乳酸混合纤维层i交替铺设,得到高麻双熔点复合纤维层;所述高麻双熔点复合纤维层中汉麻纤维的质量分数为75%,聚乳酸纤维的质量分数为25%;
46.b、制备低麻双熔点复合纤维层:
①
、将汉麻纤维和聚乳酸纤维浸没于水中润胀,再加入水进行疏解使纤维均匀分布于水中,得到汉麻/聚乳酸混合纤维浆料ii;
②
、利用抄片器将汉麻/聚乳酸混合纤维浆料ii进行抄片,得到湿汉麻/聚乳酸混合纤维层ii;
③
、将湿混合纤维层ii进行阴干,得到单层汉麻/聚乳酸混合纤维层ii;
④
、按照需求厚度将单层汉麻/聚乳酸混合纤维层ii交替铺设,得到低麻双熔点复合纤维层;所述低麻双熔点复合纤维层中汉麻纤维的质量分数为45%,聚乳酸纤维的质量分数为55%;
47.c、针刺:先将一层高麻双熔点复合纤维层和一层低麻双熔点复合纤维层叠放,然后采用针刺机进行垂直针刺,得到低麻-高麻复合纤维毡;
48.d、成型:
①
、以多孔芯层骨架层作为吸音骨架层4,以低麻双熔点复合纤维层作为吸音承接层2和吸音面层6,以高麻双熔点复合纤维层作为第一吸音芯层3和第二吸音芯层5的材料,依次按照低麻双熔点复合纤维层、高麻双熔点复合纤维层、多孔芯层骨架层、高麻双熔点复合纤维层和的低麻双熔点复合纤维层形式将低麻-高麻复合纤维毡、多孔芯层骨架和低麻-高麻复合纤维毡依次叠放,且多孔芯层骨架的相对两侧分别与低麻-高麻复合纤维毡的高麻双熔点复合纤维层一侧刷胶连接,得到纤维坯料;
②
、将纤维坯料置于烘箱中进行热固成型,得到汉麻纤维增强有机复合型材;
③
、按照需求厚度调整两个热辊的间距,然后利用热辊对汉麻纤维增强有机复合型材进行表面整饰,得到吸音层;
49.三、组装:以隔热纸层作为隔热层1,将隔热层1与吸音层的吸音承接层2背离第一吸音芯层3方向的一侧通过刷胶连接,得到汉麻纤维增强有机复合材料车内饰板。
50.实施例1步骤二c中采用针刺机利用细针在针刺力为10n下进行垂直针刺,按照间距为5mm均匀垂直针刺,单面均匀垂直针刺1遍后翻面继续垂直针刺,单面共垂直针刺2遍,得到纤维毡。
51.实施例1步骤二d
②
中所述热固成型具体操作如下:在温度为160℃下热固10min;步骤二d
③
中所述热辊的温度为160℃。
52.实施例2:本实施例与实施例1的不同点是:步骤二d
②
中所述热固成型具体操作如下:在温度为160℃下热固20min。其他与实施例1相同。
53.实施例3:本实施例与实施例1的不同点是:步骤二d
②
中所述热固成型具体操作如下:在温度为160℃下热固30min;其他与实施例1相同。
54.实施例4:如图1和图2所示,本实施例与实施例1的不同点是:所述多孔芯层骨架层为蜂窝层芯层骨架。其他与实施例1相同。
55.实施例5:本实施例与实施例4的不同点是:步骤二d
②
中所述热固成型具体操作如下:在温度为160℃下热固20min。其他与实施例4相同。
56.实施例6:本实施例与实施例4的不同点是:步骤二d
②
中所述热固成型具体操作如下:在温度为160℃下热固30min;其他与实施例4相同。
57.检测实施例1至实施例6得到的汉麻纤维增强有机复合材料车内饰板的导热系数,检测结果如表1所示。
58.表1
[0059][0060]
根据表1可知本发明得到的汉麻纤维增强有机复合材料车内饰板具有良好的隔热保温性能。
[0061]
采用驻波管法检测不同频率下实施例3至实施例6得到汉麻纤维增强有机复合材料车内饰板的吸音系数及声压变化,检测结果如表2所示。
[0062]
表2
[0063][0064]
根据表2可知本发明得到的汉麻纤维增强有机复合材料车内饰板的吸音性能良好。
[0065]
对实施例1至实施例6步骤二b中得到低麻双熔点复合纤维层进行机械性能检测,检测结果如表3所示。
[0066]
表3
[0067] 伸长率(%)断裂长(km)抗张力(kn)抗张强度(kn/m)抗张指数(n*m/g)实施例15.91.1467.44.4911.1实施例26.11.0663.24.2110.4实施例36.81.1668.94.5911.4实施例46.51.1368.74.5811.5实施例56.51.1568.94.5911.3实施例65.51.1668.64.5711.3
[0068]
根据表3可知本发明得到的汉麻纤维增强有机复合材料车内饰板的机械性能良好。
再多了解一些
本文用于创业者技术爱好者查询,仅供学习研究,如用于商业用途,请联系技术所有人。