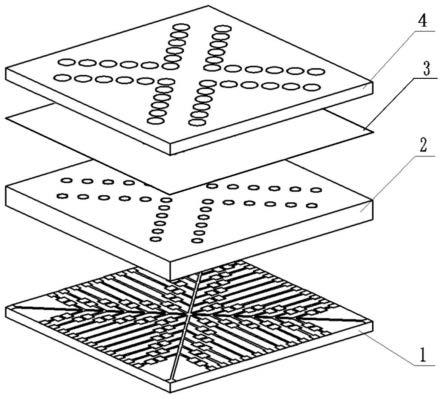
1.本发明涉及火工品技术领域,具体为一种火工阵列微推进器封装结构及封装方法。
背景技术:
2.火工阵列微推进器是随着微机电系统(mems)技术发展而出现的一种微型火工装置,具有体积微小、集成化程度高、可多次精确做功等特点,主要用于微纳卫星姿态调整、重力补偿、轨道变换等任务。阵列微推进器通常由点火电路层、装药室层、喷口层由下而上堆叠而成,层与层间的封装方案对推进器的结构强度和阵列之间工作独立性有显著影响,是阵列微推进器制作过程中的难点。
3.目前层间封装工艺包括直接键合和填料键合两种方案,直接键合直接键合方案首先需要待键合的两个表面达到原子级平整度,并且在高压或高温下实现范德华力或者原子间作用力实现封接,目前比较成熟的是硅-硅、硅-玻璃键合,键合材料受限且键合过程采用500℃以上温度,其优点在于封装后材料见的密封性好,封装结构强度高,在电子器件封装行业中有一定应用。微推进器表面存在点火电路层,做不到原子级平整,高温对点火电路层性能也有一定影响,因此不适用直接键合。填料键合指在键合层间添加粘接材料,依靠材料粘合力实现封装,粘合剂通常包括各种胶液、导电银浆等。填料键合的优点在于对封装表面平整度要求低,对封装材质几乎无限制,适用于大多数场景,目前国内的微推进器绝大大多采用填料键合进行封装。
[0004]“mems数字固体微推进器的制备与性能研究”(南京理工大学硕士论文,2016年)设计了一种底点火式结构的mems数字固体微推进器,采用绝热性能好的环氧树脂板作为装药室材料,采用硅基底表面镀覆多晶硅半导体桥膜作为发火基底材料,采用硅片等离子体刻蚀孔道作为喷口层材料,材料间采用h70e双组份环氧胶为材料进行填料键合,其键合实现过程为:(1)利用喷墨打印技术将h70e环氧胶打印在发火基底层上,喷墨打印机可以将胶液分散成极小液滴,并通过提前编程精准控制点胶位置和点胶量;(2)将装药室层定位安装在点火基底层上,装药孔道对准点火点位;(3)粘贴好的组件放入一定温度下固化24h,使其牢固粘接实现封装;(4)重复前序步骤实现装药室和喷口的封装。本方案采用粘合剂填料键合进行封装,粘合剂本身耐温性较差,易老化导致封装效果退化;在封装前需要试验确定点胶量,否则会出现点胶到发火区域导致产品无法点燃,或点胶量太少导致密封不足产品工作时高温燃气进入相邻单元引起的殉燃或解体等故障,而这些工艺缺陷通常难以检验;封装后,通常还需要外界温度或光照刺激一定时间使填料充分固化,影响制造效率。
[0005]
因此,填料键合的封装强度受填料影响大,封装工艺存在产品故障风险,封装固化耗时长等缺点,不能阵列微推进器推广发展需要,需要开发新型封装结构简化封装流程,提升封装可靠性与生产效率。
技术实现要素:
[0006]
本发明解决的技术问题是:克服现有技术的不足,提供一种火工阵列微推进器封装结构及封装方法,解决现有微推进器采用填料固化封装方案存在封装强度较低且易退化、封装工艺存在产品故障风险,封装固化耗时长等问题。
[0007]
本发明解决技术的方案是:一种火工阵列微推进器封装结构,该结构自上而下包括发火基底层、装药室层和密封薄膜层以及喷口层;其中,发火基底层包括陶瓷基底和点火电路,点火电路成型在点火陶瓷基底上,装药室层和喷口层采用阻燃热塑型高分子材料制成;发火基底层、装药室层、密封薄膜层以及喷口层采用熔融后浸润的方式粘接在一起。
[0008]
优选地,所述陶瓷基底材料为al2o3,点火电路层为ni-cr合金通过物理沉积和激光雕刻的方式成型到点火陶瓷基底上。
[0009]
优选地,所述装药室层和喷口层均为聚醚醚酮板材,通过机械加工形成上下平滑表面以及阵列孔道。
[0010]
优选地,所述密封薄膜层为聚酰亚胺薄膜。
[0011]
本发明的另一个技术方案是:一种火工阵列微推进器封装方法,该方法包括如下步骤:
[0012]
s1、将已布置好点火电路的发火基底层放置在加热台上,点火电路朝上,加热温度高于装药室熔点后,进行保温,保证阵列各处温度均匀;
[0013]
s2、在第一定位装置辅助下,将装药室安装在加热的发火基底上,装药室微孔道对准点火电路的阵列发火点,施加第一预设压强,使装药室底部表层熔融软化,浸润到发火基底层上,并自动填补结合缝隙;
[0014]
s3、从加热台取出装配装药室后的组件,充分自然冷却后,向装药室微孔道内装填推进剂;
[0015]
s4、将聚酰亚胺薄膜和喷口层依次放置在加热台上,加热温度高于喷口层熔点,施加第二预设压强,使喷口层底部表层熔融软化,并浸润聚酰亚胺薄膜,使聚酰亚胺薄膜和喷口层完全贴合;
[0016]
s5、夹取贴合聚酰亚胺膜后的喷口层,以聚酰亚胺膜朝下,在第二定位装置辅助下迅速压在装药后的装药室层上,加压并保压;
[0017]
s6、装药室上部表层受热熔融,并浸润聚酰亚胺膜,使聚酰亚胺膜和装药室完全贴合,完成阵列微推进器封装。
[0018]
优选地,所述步骤s1的保温时间为不少于10min。
[0019]
优选地,所述步骤s2中的第一预设压强为0~15kpa。
[0020]
优选地,所述步骤s4中的第二预设压强为10~15kpa。
[0021]
优选地,所述第一定位装置为环形框架结构,中间带有台阶孔,台阶孔的大孔用于套在发火基底层上,大孔的高度与发火基底层的高度相同,小孔设置在发火基底层的顶部。
[0022]
优选地,所述第二定位装置为环形框架结构,中间带有台阶孔,台阶孔的大孔用于套在发火基底层上,大孔的高度与发火基底层的高度相同,小孔套在装药层和喷口层外,用于将装药层和喷口层限位。
[0023]
本发明与现有技术相比的有益效果是:
[0024]
(1)、本发明发火基底层、装药室层、密封薄膜层以及喷口层采用熔融后浸润的方
式粘接在一起,属于直接键合,同时相对传统直接键合方案对材料表面平整度要求低,且可选材料更广泛;
[0025]
(2)、本发明不采用胶粘剂、封装效果不随贮存年限的增加导致材料老化而下降,也不存在胶粘剂用量不精准导致产品故障的风险。
[0026]
(3)、本发明装药室层和喷口层采用阻燃热塑型高分子材料制成,封装过程中受压自动填补材料表面缝隙,封装后无需固化等待直接得到成品,封装效率高。
附图说明
[0027]
图1为本发明实施例的封装结构整体示意图;
[0028]
图2为本发明中的封装结构各层爆炸示意图;
[0029]
图3为本发明中的封装结构实现过程示意图。
具体实施方式
[0030]
下面结合实施例对本发明作进一步阐述。
[0031]
如图1、2所示,本发明提供了一种火工阵列微推进器封装结构,该结构自上而下包括发火基底层1、装药室层2和密封薄膜层3以及喷口层4;其中,发火基底层1包括陶瓷基底和点火电路,点火电路成型在点火陶瓷基底上,装药室层2和喷口层4采用阻燃热塑型高分子材料制成;发火基底层1、装药室层2和密封薄膜层3以及喷口层4采用熔融后浸润的方式粘接在一起。
[0032]
优选地,所述陶瓷基底材料为al2o3,点火电路层为ni-cr合金通过物理沉积和激光雕刻的方式成型到点火陶瓷基底上。
[0033]
优选地,所述装药室层和喷口层均为聚醚醚酮板材,通过机械加工形成上下平滑表面以及阵列孔道,装药室层和喷口层最好耐高温280℃以上,也可以是其他耐高温阻燃的热塑型高分子材料。
[0034]
优选地,所述密封薄膜层为聚酰亚胺薄膜,也可以是其他耐高温且易被装药室层和喷口层浸润的薄层材料。
[0035]
本发明还提供了一种火工阵列微推进器封装结构的制备方法,该方法如下步骤:
[0036]
s1、将已布置好点火电路的发火基底层放置在加热台上,点火电路朝上,加热温度高于装药室熔点后,进行保温保证阵列各处温度均匀;
[0037]
s2、在第一定位装置辅助下,将装药室安装在加热的点火电路上,装药室微孔道对准点火电路的阵列发火点,施加第一预设压强,使装药室底部表层熔融软化,浸润到发火基底层上,并自动填补结合缝隙;
[0038]
s3、从加热台取出装配装药室后的组件,充分自然冷却后,向装药室微孔道内装填推进剂;
[0039]
s4、将聚酰亚胺薄膜和喷口层依次放置在加热台上,加热温度高于喷口层熔点,施加第二预设压强,使喷口层底部表层熔融软化,并浸润聚酰亚胺薄膜,使聚酰亚胺薄膜和喷口层完全贴合;
[0040]
s5、夹取贴合聚酰亚胺膜后的喷口层,以聚酰亚胺膜朝下,在第二定位装置辅助下迅速压在装药后的装药室层上,加压并保压;
[0041]
s6、装药室上部表层受热熔融,并浸润聚酰亚胺膜,使聚酰亚胺膜和装药室完全贴合,完成阵列微推进器封装。
[0042]
优选地,所述步骤s1的保温时间为不少于10min。
[0043]
优选地,所述步骤s2的第一预设压强10~15kpa。
[0044]
优选地,所述步骤s4的第二预设压强为10~15kpa。
[0045]
优选地,所述步骤s5保压时间不低于30s。
[0046]
优选地,所述第一定位装置环形框架结构,中间带有台阶孔,台阶孔的大孔用于套在发火基底层上,大孔的高度与发火基底层的高度相同,小孔用于压的发火基底层的顶部。
[0047]
优选地,所述第二定位装置环形框架结构,中间带有台阶孔,台阶孔的大孔用于套在发火基底层上,大孔的高度与发火基底层的高度相同,小孔套在装药层和喷口层外,用于将装药层和喷口层限位。
[0048]
本发明某一具体实施例中封装结构的制作方法为:
[0049]
第一步,如图3(a)所示,将发火基底层1电路朝上放置在恒温加热台5上,以高于装药室材料熔点(5
±
1)℃,静置10min以上保证阵列各处温度均匀;
[0050]
第二步,如图3(b)所示,将装药室层2放在发火基底层1上,在第一定位装置6的约束下保证装药孔道对其发火基底层1的点火点位,施加压力并保压保压(30
±
1)s,装药室层2底部表层熔融,浸润到点火电路层的陶瓷基底和ni-cr电路上并自动填补装药室层2和点火电路层之间的缝隙,实现密封粘接;
[0051]
第三步,取出装配装药室后的组件充分冷却,并装入推进剂;
[0052]
第四步,如图3(c)所示,将密封薄膜层3放置在恒温加热台5上,再将喷口层4放置在密封薄膜层3上,施加压力并保压(30
±
1)s,喷口层4底部表层轻微熔融,浸润到密封薄膜层3上表面,实现密封粘接;
[0053]
第五步,如图3(d)所示,将加热台上已粘接密封薄膜层3的喷口层4移出加热台,迅速放置在已装有推进剂9的装药室上表面,在第二定位装置8的约束下保证装药室层2和喷口层4的孔道正对,施加一定压力,装药室层2上表面受热后轻微熔化,浸润到密封薄膜层3下表面,实现密封粘接,得到所述阵列微推进器封装结构。
[0054]
本发明虽然已以较佳实施例公开如上,但其并不是用来限定本发明,任何本领域技术人员在不脱离本发明的精神和范围内,都可以利用上述揭示的方法和技术内容对本发明技术方案做出可能的变动和修改,因此,凡是未脱离本发明技术方案的内容,依据本发明的技术实质对以上实施例所作的任何简单修改、等同变化及修饰,均属于本发明技术方案的保护范围。
再多了解一些
本文用于创业者技术爱好者查询,仅供学习研究,如用于商业用途,请联系技术所有人。