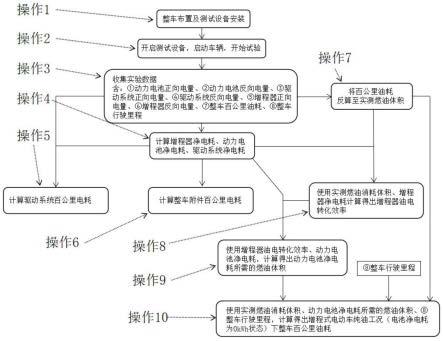
1.本发明属于增程式电动车测试技术领域,具体涉及一种增程式电动汽车能耗测试方法。
背景技术:
2.增程式电动车作为电动汽车的一种,因其具备纯电动汽车优良驾驶性、较低的使用成本、较好的驾驶体验感同时,具备了传统燃油汽车能源补给的便捷性,相对传统燃油车能耗也可一定程度下降。
3.针对增程式电动车油电转化效率分析工作,目前主要通过模拟计算,即利用发动机比油耗和电机系统效率计算增程器系统效率;台架测试使用油耗仪和功率分析仪对增程器进行单点、或多点测试,已实现增程器全部工作区域的效率测定,无论模拟计算还是台架测试均可以得出增程器系统效率。
4.增程器作为整车能量传递过程中的零部件之一,增程器的运行工况与整车策略及整车实际状态,如整车需求功率、动力电池可充电功率等有着直接的关系,均会影响增程器在整车行驶过程中的综合效率。
5.现今,多针对增程器单体进行测试或计算来获取增程器能耗数据,并以此为基础进行功率点选点和整车匹配工作。由于增程器工作区域内效率差距较大,整车能耗会受控制策略及其他系统影响,需要寻找一种方法对整车能耗进行测试。
技术实现要素:
6.目前现有研究中对于增程式电动车整车试验过程中油电转化效率的测定关注较少,本发明旨在设计一种增程式电动车能耗测试方法。
7.本发明所采取的技术方案是:增程式电动汽车能耗测试方法,包括以下步骤:
8.s1.整车布置及测试设备安装;
9.s2.开启测试设备,启动车辆,开始试验;
10.s3.收集试验数据;
11.s4.计算增程器净电耗、动力电池净电耗、驱动系统净电耗;
12.s5.计算驱动系统百公里电耗;
13.s6.计算整车附件百公里电耗;
14.s7.将百公里油耗反算至实测燃油体积;
15.s8.使用实测燃油消耗体积、增程器净电耗计算得出增程器油电转化效率;
16.s9.使用增程器油电转化效率、动力电池净电耗,计算得出动力电池净电耗所需的燃油体积;
17.s10.使用实测燃油消耗体积、动力电池净电耗所需的燃油体积、整车行驶里程,计算得出增程式电动车纯油工况下整车百公里油耗。
18.本发明与现有技术相比具有以下有益效果:
19.本发明通过对整车电耗、油耗数据进行测量,通过对数据进行计算,得出整车实际行驶期间增程器效率、整车附件百公里电耗、整车驱动系统百公里电耗、增程式电动车在纯油工况下的百公里油耗,实现增程式电动车效率细分计算,有利于整车能耗标定,降低碳排放。
附图说明
20.图1是本发明流程框图;
21.图2是本发明整车布置及测试设备安装图;
22.图3是增程器典型运行工况图;
23.其中:1、增程器;2、动力电池;3、驱动系统;4、其他附件;5、功率分析仪;6、转毂;7、尾气收集测量设备。
具体实施方式
24.为了更好地了解本发明的目的、结构及功能,下面结合附图,对本发明的做进一步详细的描述。
25.本发明的整车于排放试验室中进行,增程式电动车驱动轮位于转毂之上,记录行驶里程;通过布置功率分析仪5及其电压和电流测点对整车电能数据进行采集;通过尾气采集测量设备7通过对整车行驶过程中的油耗数据进行统计。通过发明所述方法统计试验数据,并经过一系列计算,可以精准得出增程式电动车在实际行驶过程中能耗数据,为增程式电动车控制策略的验证和及整车匹配提供直接有力的参考依据。
26.本发明的一种增程式电动汽车能耗测试方法,包括以下步骤:
27.s1.整车布置及测试设备安装;
28.本发明的整车布置及测点安装如附图2所示,增程式电动车能耗试验主要涉及:增程器1、动力电池2、驱动系统3、其他附件4、功率分析仪5、转毂6、尾气收集测量设备7,其中增程器1、动力电池2、驱动系统3、其他附件4为增程式电动车固有组成部分,功率分析仪5、转毂6、尾气收集测量设备7设备为本能耗测试方法所需的测试设备;
29.在实际道路行驶中,转毂6可选用车辆里程表代替,尾气收集测量设备7可由车载油耗仪或其他油耗计量设备代替。
30.增程式电动车的后轮(驱动轮)位于转毂6之上,整车滑行阻力可按照整车滑行阻力试验数据进行设置;
31.增程式电动车排气管与尾气采集测量设备7连接,
32.分别在动力电池2直流母线正极( )、驱动系统3直流母线正极( )、增程器1直流母线正极( )位置安装电流传感器;
33.由于增程器1、动力电池2、驱动系统3均为并联关系,根据基尔霍夫电压定律,并联节点中电压幅值处处相等,在动力电池2直流母线正负极( 、-)位置安装电压测点,此点电压即可作为功率分析仪5的通道一、通道二、通道三的电压值;
34.将套在增程器1母线正极上的电流传感器接插件与功率分析仪5的通道一相连,将套在动力电池2母线正极上的电流传感器接插件与功率分析仪5的通道二相连,将套在驱动系统3母线正极上的电流传感器接插件与功率分析仪5的通道三相连。
35.将电压测点的正、负极分别与与功率分析仪5的通道一、通道二、通道三相应的电压接口相连。
36.s2.开启测试设备,启动车辆,开始试验;
37.分别开启功率分析仪5、尾气采集测量设备7、电流传感器等测量设备,开始测量车辆尾气及各个测点的电耗,启动车辆并开始行驶,开始试验;
38.在本发明的整车行驶轨迹或车速与时间的关系可选用三种不同的模式,分别为;
39.1、整车参照中国汽车行驶工况(cltc)、世界轻型汽车测试循环(wtlc)中车速-时间曲线进行行驶,测试条件按照gb1835中“电量保持模式sc”进行。
40.2、定速测试。根据按照固定车速0~150km/h内间隔10km/h为一个车速区间,如0km/h,此时测试增程式电动汽车在静止状态下整车能耗,进一步的进行10km/h、20km/h、
···
140km/h、150km/h、
···
至上限车速进行测试,每种车速对应的测试质量分别为:整备质量、最大设计质量。每种状态(车速-测试质量)的测试时间不小于2分钟。实际行驶工况可参考表1进行。
41.表1行驶工况及测试时间
[0042][0043]
3、基于用户驾驶习惯的预定工作循环试验。
[0044]
根据用户驾驶习惯统计增程器典型运行工况,并将此典型工况作为预先设定工作循环,在整车行驶期间增程器自动执行预先设定工作循环。增程器1发电功率随时间变化,驱动系统3用于平衡增程器发电功率与动力电池2可充电功率间的功率差值,避免增程器1因动力电池2可充电功率限制导致功率点偏移,保证增程器1按照预先设定工作循环正常工作。
[0045]
本发明的增程器典型运行工况如附图3所示,某型增程器额定功率为40kw,峰值功率为50kw。设定增程器一个工作循环周期为250s,包含最小发电功率、功率跟随功率、额定发电功率、峰值发电功率,其中最小发电功率在2-6kw之间,功率跟随功率在10-30kw,额定发电功率40kw、峰值发电功率50kw,在整车行驶期间,增程器根据预设工作循环程序运行。此方法也适用于更高功率增程器。
[0046]
s3.收集试验数据;
[0047]
在本发明中定义电流参考方向为:电流流出动力电池系统(动力电池输出电能)为电流或功率的正向流动,电流流出增程器(增程器发电)为电流或功率的正向流动,电流流进驱动系统(驱动系统耗电)为电流的正向流动。排放试验室含尾气采集及测量设备。
[0048]
根据功率分析仪5采集的数据由以下部分组成:
①
动力电池正向电量,简称为w
池
、
②
动力电池反向电量,简称为w
池-;
③
驱动系统正向电量,简称为w
驱
、
④
驱动系统反向电量,
简称为w
驱-;
⑤
增程器正向电量,简称为w
增
、
⑥
增程器反向电量,简称为w
增-;排放试验室输出
⑦
整车百公里油耗,简称为m
测_100km
、
⑧
整车行驶里程,简称为d。
[0049]
s4.计算增程器净电耗、动力电池净电耗、驱动系统净电耗;
[0050]
从功率分析仪(5)中可获取
⑤
增程器正向电量w
增
,根据电流参考方向,此值为增程器发电电量;
⑥
增程器反向电量w增-,根据电流参考方向,此值为增程器启动耗电电量;增程器在整车行驶过程中的增程器净电耗w增_净电耗,使用公式(1)计算,即:
[0051]w增_净电耗
=w
增 -w
增-ꢀꢀꢀꢀꢀꢀꢀꢀꢀꢀꢀꢀꢀꢀꢀꢀꢀꢀ
(1)
[0052]
从功率分析仪(5)中可获取
③
驱动系统正向电量w
驱
,根据电流参考方向,此值为驱动系统驱动车轮耗电电量;
④
驱动系统反向电量w
驱-,根据电流参考方向,此值为驱动系统动能回收电量,驱动系统在整车行驶过程中的驱动系统净电耗w
驱_净电耗
使用公式(2)计算,即:
[0053]w驱_净电耗
=w
驱 -w
驱-ꢀꢀꢀꢀꢀꢀꢀꢀꢀꢀꢀꢀꢀꢀꢀꢀꢀꢀꢀ
(2)
[0054]
从功率分析仪(5)中可获取
①
动力电池正向电量w
池
,根据电流参考方向,此值为动力电池输出电量;
②
动力电池反向电量w
池-,根据电流参考方向,此值为动力电池充电电量,动力电池在整车行驶过程中的动力电池净电耗w
池_净电耗
使用公式(3)计算,当w
池_净电耗
大于零时,证明动力电池输出电量大于充电电量;
[0055]w池_净电耗
=w
池 -w
池-ꢀꢀꢀꢀꢀꢀꢀꢀꢀꢀꢀꢀꢀꢀꢀꢀꢀꢀꢀꢀꢀꢀꢀꢀ
(3)
[0056]
s5.计算驱动系统百公里电耗;
[0057]
根据s4中得出的驱动系统净电耗w
驱_净电耗
、整车行驶里程d使用公式(4)计算得出驱动系统百公里电耗为m
100km
;
[0058]m100km
=w
驱_净电耗
÷
d*100
ꢀꢀꢀꢀꢀꢀꢀꢀꢀꢀꢀꢀꢀꢀꢀꢀꢀꢀꢀꢀ
(4)
[0059]
s6.计算整车附件百公里电耗;
[0060]
使用增程器净电耗、动力电池净电耗、驱动系统净电耗计算得出的整车附件净电耗、整车行驶里程计算得出整车附件百公里电耗;
[0061]
增程式电动车其他附件损耗统一归算为整车附件净电耗w
附_净电耗
,
[0062]
根据功率守恒原则,增程器净电耗w
增_净电耗
、动力电池净电耗w
池_净电耗
、驱动系统净电耗w
驱_净电耗
、整车附件电耗w
附_净电耗
之间的代数和必然为“0”。由此整车附件电耗w
附_净电耗
可由公式(5)计算得出,
[0063]w附_净电耗
=w
增_净电耗
w
池_净电耗-w
驱_净电耗
ꢀꢀꢀꢀꢀꢀ
(5)
[0064]
此时整车附件百公里电耗w
附_100km
可由公式(6)计算得出,
[0065]w附_100km
=w
附_净电耗
÷
d*100
ꢀꢀꢀꢀꢀꢀꢀꢀꢀꢀꢀꢀꢀꢀꢀꢀꢀ
(6)。
[0066]
s7.将百公里油耗反算至实测燃油体积;
[0067]
试验室输出油耗的数据型式为整车百公里油耗m
测_100km
,单位:l/100km,使用公式(7)可将百公里油耗转化为实际燃油消耗体积v
实
,
[0068]v实
=m
测_100km
÷
100*d
ꢀꢀꢀꢀꢀꢀꢀꢀꢀꢀꢀꢀꢀꢀꢀꢀꢀꢀꢀꢀꢀꢀ
(7)
[0069]
在实际整车试验中,实际燃油消耗体积v
实
也可通过车载燃油消耗仪统计。也可使用油枪二次加油方式获取,即:试验前加满油箱,试验后再次将油箱加满,则第二次加油的体积可视为试验过程中实际燃油消耗体积。
[0070]
s8.使用实测燃油消耗体积、增程器净电耗计算得出增程器油电转化效率;
[0071]
根据s7获取的实际燃油消耗体积v
实
、s3获取的增程器净电耗w
增_净电耗
,可计算得出增程器在整车行驶过程中的增程器油电转化效率s,计算过程如公式(8)所示:
[0072]
s=w
增_净电耗
÷v实
ꢀꢀꢀꢀꢀꢀꢀꢀꢀꢀꢀꢀꢀꢀꢀꢀꢀꢀꢀꢀꢀꢀꢀ
(8)
[0073]
通过s8计算得出的增程器油电转化效率s,可以准确评估增程器在整车行驶过程中的综合效率,为增程式电动车控制策略制定提供直接有效参考。
[0074]
s9.使用增程器油电转化效率、动力电池净电耗,计算得出动力电池净电耗所需的燃油体积;
[0075]
使用增程器油电转化效率、动力电池净电耗及公式(9),计算得出动力电池净电耗所需的燃油体积v
池_净
,
[0076]v池_净
=w
池_净电耗
÷sꢀꢀꢀꢀꢀꢀꢀꢀꢀꢀꢀꢀꢀꢀꢀꢀꢀꢀꢀꢀ
(9)。
[0077]
s10.使用实测燃油消耗体积、动力电池净电耗所需的燃油体积、
⑧
整车行驶里程,计算得出增程式电动车纯油工况(电池净电耗为0kwh状态)下整车百公里油耗。
[0078]
本发明所述纯油工况即为电池净电耗为0kwh状态下整车运行工况。
[0079]
使用实测燃油消耗体积、动力电池净电耗所需的燃油体积,使用公式(10)计算得出增程式电动车纯油工况(动力电池正向输出电量与充电电量相等,即净电耗w
池_净电耗
为0kwh状态)下整车百公里油耗m
纯油_100km
,
[0080]m纯油_100km
=(v
实-w
池_净电耗
÷
s)
÷
100*d
ꢀꢀꢀꢀ
(10)。
[0081]
可以理解,本发明是通过一些实施例进行描述的,本领域技术人员知悉的,在不脱离本发明的精神和范围的情况下,可以对这些特征和实施例进行各种改变或等效替换。另外,在本发明的教导下,可以对这些特征和实施例进行修改以适应具体的情况及材料而不会脱离本发明的精神和范围。因此,本发明不受此处所公开的具体实施例的限制,所有落入本技术的权利要求范围内的实施例都属于本发明所保护的范围内。
再多了解一些
本文用于企业家、创业者技术爱好者查询,结果仅供参考。