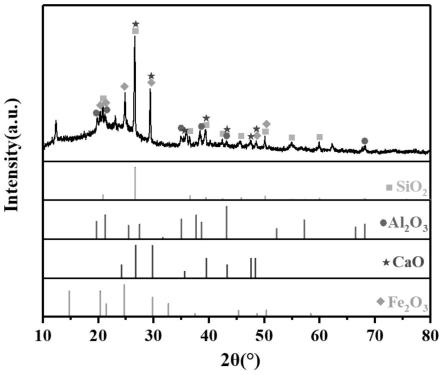
1.本发明属于膜分离技术领域,尤其涉及到一种具有自粘结性能炭膜的制备方法及所得炭膜。
背景技术:
2.水是生命的源泉,是生命存在与经济发展的必要条件,同样是构成人体组织的重要部分。工业生产和人类活动中产生的含有难降解有机污染物的废水已经造成了严重的全球环境污染,可能导致清洁水的短缺,对人类健康和生态环境造成破坏。为实现有机废水的深度和有效处理,研究人员已开展了大量的研究工作。
3.膜分离过程作为一门新型的高效分离、浓缩提纯及净化技术,被认为是一种有前景的水处理方法。膜分离技术的核心是膜材料。炭膜是一种性能优异的膜分离材料,它是由含碳物质经高温热解炭化制备而成,由无数炭微晶无序堆积而成的多孔炭基膜材料。炭膜融合了炭材料的结构特性及膜材料高效、节能的优势,具有稳定的化学性能、优异的导电性能和丰富均一的孔结构。区别于高分子膜和陶瓷膜材料,炭膜同时具有吸附、分离和电催化等多功能,在废水处理、水质净化等方面应用前景广阔。cn201110456881.4提出将含碳物质与粘结剂、造孔剂、导电剂混炼炭化制备炭膜,所制备的导电炭膜具有良好的导电性能和抗腐蚀能力,稳定性好,并且价格低廉,在电场强化膜分离技术等方面具有广泛的应用前景。但该发明采用的含碳物质主要为烟煤粉、活性炭、中间相炭微球、石油焦或酚醛树脂等,这些物质使用过程中存在预处理复杂、产生挥发性有机物(voc)。特别是,炭膜制备过程需要添加粘合剂,如苯并噁嗪树脂、煤焦油、馏塔釜底聚合副产物等,其高温炭化过程会产生更加多voc,污染环境,同时也致使炭膜抗折强度偏低、孔径大小不易难以控制。
4.兰炭是一种从煤或油页岩的中低温热解中获得的固体含碳物质,通常为低价值的废料处理,来源广泛,成本低。兰炭主要由碳和无机氧化物组成,中低温热解使其仍含有一定的焦油成分,赋予了一定的粘结性能,其目前也被认为是一种矿物生物炭,早期阶段被用作燃料和水泥厂的原料,也被用作污水中污染物的吸附剂。鉴于目前炭膜在制备过程及结构和性能存在一定的局限性,即很难同时具有孔隙可调控制备以及自粘结成膜、机械性能较好等特征,使其应用受到制约。因此,如果能够基于兰炭开发一种简单、高效的炭膜制备方法,无需添加其它粘结剂及额外工艺处理,则可在解决上述技术问题的同时,为焦化行业废弃物的资源化利用提供了一条新途径。
技术实现要素:
5.本发明提供了一种具有自粘结性能炭膜的制备方法及所得炭膜,所得炭膜能够同时具有孔隙可调控制备以及自粘结成膜、机械性能较好等特点,同时以兰炭为原料,也为焦化行业废弃物的资源化利用提供了一条新途径。
6.为了达到上述目的,本发明提供了一种具有自粘结性能炭膜的制备方法,包括以下步骤:
7.以兰炭为含碳物质,与造孔剂、增塑剂和溶剂混合,充分球磨混练后,经过干燥、研磨、加压成型,得到炭膜原膜(压制成型后未经炭化的炭膜);
8.将所得炭膜原膜经热处理炭化工艺处理,得到具有自粘结性能的炭膜;
9.其中,所述兰炭为煤制和/或油页岩制兰炭,其焦油含量为15-30%。
10.上述方案中对兰炭的焦油含量做了必要的限定,这是因为若焦油含量低于15%,则所得炭膜不能发生自粘接,而如果含量高于30%,则所得膜的孔隙率较低,后期无法使用。
11.在上述方案中,采用gb/t212-2008《煤的业分析方法》工业分析法,本方案中使用的兰炭的固定碳含量为65-80%、水分含量为3-6%、灰分含量为15-22%、挥发分含量为2-10%;采用gb/t476-2001《煤的元素分析方法》元素分析法,其元素碳(c)含量为65-85%,元素氢(h)含量为1-5%,元素氧(o)含量为5-20%,元素氮(n)含量为0.5-1%,元素硫(s)含量为0.2-1%;其比表面积为3-15m2/g,具体如下表1、表2所示。
12.表1兰炭粉末的工业分析
[0013][0014]
表2兰炭粉末灰分的xrf分析
[0015][0016]
在上述方案中,在将兰炭作为含碳物质,与造孔剂、增塑剂和溶剂混合之前,需要对其进行预处理,具体为:
[0017]
将兰炭块、兰炭末放入蒸馏水内清洗去除表面灰尘,在恒温鼓风干燥箱内100℃干燥4-8h,取出冷却至室温后放入粉碎机内粉碎,将粉碎后的兰炭粉末放入震荡筛分仪内,得到平均粒径为75-250μm兰炭粉末。
[0018]
作为优选,球磨混练具体为:
[0019]
将50-90%兰炭、5-35%造孔剂、3-15%增塑剂按质量百分比混合得混合物料ⅰ,将质量百分浓度75-99.5%的溶剂与混合物料ⅰ放入球磨机中进行混合3-8h,得混合浆料ⅱ。
[0020]
在上述方案中,所用溶剂可以为乙醇、正丙醇、异丙醇、正丁醇。
[0021]
作为优选,所述兰炭的平均粒径为75-250μm,溶剂的加入量为混合物料ⅰ质量的270-400%。在本方案中,对兰炭的粒径做了必要的限定,原料的粒径对炭膜孔结构特性的影响十分显著,随着颗粒度的减小,炭膜的平均孔径变小,孔隙率增加。原料粒径过大时,因较大的原料颗粒之间的空隙较大,所制备炭膜机械强度差或无法自粘结成膜;而较小的原料粒径,所制备的炭膜平均孔径过小,纯水通量低,不利于后期水处理应用。
[0022]
作为优选,干燥、研磨具体为:
[0023]
将球磨机混合好的混合浆料ⅱ于恒温鼓风干燥箱内50-120℃、干燥8-15h,得混合物料ⅲ;
[0024]
将混合物料ⅲ放入转速为300-500r/min的行星球磨机中进行研磨粉碎3-8h,得混合物料ⅳ,所得混合物料ⅳ的平均粒径在75μm以下。在本方案中,球磨时长对原料粒径影响
显著,随着球磨时间的增长,原料的粒径逐渐减小,原料粒度更加均一。球磨的时间越长得到的原料颗粒度越均一越有利于制得具有均一孔隙结构的炭膜。烘干后的物料易结块,球磨时间过短,原料粒度大,不利于自粘结成膜,而球磨时间过长,原料粒径太小,所制备炭膜不利于后期使用。
[0025]
作为优选,液压成型具体为:
[0026]
将研磨后的混合物料ⅳ放入液压成型机,于10-15mpa下挤压12-18min,得到平板状原膜;或
[0027]
将在得到上述平板状原膜后,继续将其经真空塑封后放入等静压机中,于75-150mpa下进行8-12min的二次挤压成型。
[0028]
在上述方案中,一次挤压为液压成形,使原膜具有初始形状;二次挤压使粉料成形时更加紧实,增强炭膜的机械强度。
[0029]
作为优选,所述热处理炭化工艺具体为:
[0030]
将成型的炭膜原膜放入炭化炉中,在惰性气体保护下,进行炭化制备出自粘结炭膜;
[0031]
其中,炭化条件为:升温速率为3-10℃/min,炭化温度为700-1400℃,恒温时间为30-150min,惰性气体为氩气或氮气,载气流率为5-30m3/h。在本方案中,炭化过程需要用惰性气体进行充分的吹扫,以去除挥发性气体,并防止炭膜意外烧损和化学损害。低的气体流速不足以快速去除基体中产生的气体,挥发性气体如碳氢化合物可能会进一步分解并沉积在炭膜的表面或堵塞在孔隙中,导致炭膜孔径变小。
[0032]
炭膜的孔结构是在炭化过程中从基体内的气体逸出而形成和发展的,升热速率明显影响炭膜的结构性能。低的升热速率有利于挥发性化合物从基体中缓慢释放,使碳膜形成均匀的孔隙结构,孔径较小;而高的升热速率则导致气体爆炸性地释放,产生一些不规则的孔隙,也可能形成针孔和微观裂缝。
[0033]
几乎所有的煤炭本身都不导电,只有将原膜经高温炭化处理后,才能得到具有优异导电性和电化学性能的炭膜。在本方案中对炭化温度做了必要的限定,这是因为当炭化温度低于700℃时,所制得炭膜不导电或电导率极低;当炭化温度高于700℃时,所制得炭膜导电性能和电化学活性不断提升;当炭化温度大于1400℃时,炭化温度对所制的炭膜性能提升极小。
[0034]
作为优选,所述增塑剂选自甲基纤维素、羧甲基纤维素、羟乙基纤维素、羟丙基甲基纤维素中的至少一种;所述造孔剂选自聚乙烯醇缩丁醛、聚苯乙烯、聚氨酯中的至少一种;所述溶剂选自乙醇、正丙醇、异丙醇、正丁醇中的至少一种。
[0035]
本发明还提供了一种根据上述任一项技术方案所述的制备方法制备得到的具有自粘结性能的炭膜。
[0036]
作为优选,炭膜孔径的分布为0.5-150nm,平均孔径为25-85nm,孔隙率为35-55%。
[0037]
作为优选,炭膜的电导率为10-5500s/m,抗折强度为5-20mpa,纯水渗透率为50-250l/m2·h·
bar。
[0038]
与现有技术相比,本发明的优点和积极效果在于:
[0039]
本发明以兰炭为炭源,利用兰炭中自含的未交联和交联程度低的焦油芳香组分为粘合剂,在高温炭化过程将兰炭中无定形炭和石墨炭紧密的粘结起来,实现材料的自粘结。
该制备方法操作简单、绿色环保,无需添加其它粘结剂及额外工艺处理。此外,兰炭中富含大量无机矿物质(15-22%),大大提高了炭膜的抗折强度(5-20mpa,显著优于现有炭膜的抗折强度)。本发明所制备的炭膜兼顾具有孔径更小、孔径分布可调,截留分离性能更加优异、成膜力学性能等特性。尤其是,本发明减少了粘结剂添加造成的环境污染,也为焦化行业废弃资源高值化利用提供了一条新途径。
附图说明
[0040]
图1为具有自粘结性炭膜制备工艺流程图;
[0041]
图2为实施例1-10中使用的兰炭粉末的sem照片;
[0042]
图3为实施例1-10中兰炭粉末的tg-dtg图像和焦油含量(22.39wt.%);第一个失重区间温度为室温至200℃,失重量约为1.98%,该阶段是兰炭中游离水与化合水的析出过程;第二个失重区间温度为300℃-630℃,失重量约为20.41%,该阶段主要挥发分的析出及挥发性有机物(vocs)释放;第三个失重区间温度为630℃-1000℃,失重量约为6.13%,这是由于兰炭中含有少量的碳酸盐在700℃以上的高温状态下发生热解及兰炭本身炭结构的重排所致;
[0043]
图4为实施例1-10中兰炭粉末的xrd图像;在25-30
°
处有一个石墨(002)晶面的特征峰,归因于芳香环碳网层片在空间排列的定向程度;此外,在兰炭中还观察到几个尖锐的矿物衍射峰,这主要归因于兰炭制备原煤中的矿物物质。
[0044]
图5为对比例x(图左)和实施例x(图左)所制得炭膜的数码照片。
具体实施方式
[0045]
下面将对本发明实施例中的技术方案进行清楚、完整地描述,显然,所描述的实施例仅仅是本发明一部分实施例,而不是全部的实施例。基于本发明中的实施例,本领域普通技术人员在没有做出创造性劳动前提下所获得的所有其他实施例,都属于本发明保护的范围。
[0046]
实施例1
[0047]
称取9g粒径为75μm的兰炭粉末(其sem照片如图2所示)、0.8g羧甲基纤维素、0.9g聚乙烯醇缩丁醛、60ml质量百分浓度99.5%的乙醇溶液加入到转速为500r/min的行星球磨机内充分混合3h得混合泥料,取出放入恒温鼓风干燥箱内80℃恒温干燥10h,直至泥料中溶剂及水分完全挥发。将干燥好的混合物料再次放入转速为500r/min的行星球磨机内研磨粉碎4h,粉碎后的混合物料称取9g采用液压成型机15mpa下15min制成平板式原膜,随后将原膜真空塑封放入等静压机内二次成型,在110mp下保压600s。将原膜取出放入炭化炉中,在氮气保护下,以3℃/min的升温速率升至950℃并恒温120min,待其冷却至室温取出即得兰炭基炭膜或自粘结性能的炭膜,其主要性能如表3所示,整个工艺流程图如图1所示,所采用的兰炭粉末的tg-dtg图像如图3所示,xrd图像如图4所示。
[0048]
实施例2~5
[0049]
按照实施例1的步骤,造孔剂为不同质量的聚乙烯醇缩丁醛(1.35g、1.80g、2.25g和2.70g),由此制备出实施例2~5的兰炭基炭膜或自粘结性能的炭膜,其主要性能如表3所示。
[0050]
实施例6
[0051]
称取9g粒径为75μm的兰炭粉末、0.8g甲基纤维素、1.8g聚乙烯醇缩丁醛、60ml质量百分浓度99.5%的丙醇溶液加入到转速为400r/min的行星球磨机内充分混合6h得混合泥料,取出放入恒温鼓风干燥箱内100℃恒温干燥8h,直至泥料中溶剂及水分完全挥发。将干燥好的混合物料再次放入转速为400r/min的行星球磨机内研磨粉碎8h,粉碎后的混合物料称取9g采用液压成型机10mpa下15min制成平板式原膜,随后将原膜真空塑封放入等静压机内二次成型,在110mp下保压600s。将原模取出放入炭化炉中,在氩气保护下,以6℃/min的升温速率升至750℃并恒温120min,待其冷却至室温取出即得兰炭基炭膜或自粘结性能的炭膜,其主要性能如表4所示。
[0052]
实施例7~10
[0053]
按照实施例6的步骤,其中改变炭化温度和恒温时间(依次为850℃和140min、950℃和130min、1150℃和100min、1350℃和80min),由此获得实施例7~10的兰炭基炭膜或具有自粘结的炭膜,其导电性能如表4所示。
[0054]
对比例1
[0055]
整体方法与实施例1相同,区别之处在于兰炭粉末的粒径为45μm。
[0056]
对比例2
[0057]
整体方法与实施例5相同,区别之处在于兰炭粉末的粒径为320μm。
[0058]
对比例3
[0059]
整体方法与实施例6相同,区别之处在于炭化温度为650℃。
[0060]
对比例4
[0061]
整体方法与实施例6相同,区别之处在于炭化温度为1450℃。
[0062]
表3实施例1-10及对比例1-4所得炭膜基本性能
[0063][0064]
表4实施例1-10及对比例1-4所得炭膜导电性能
[0065][0066][0067]
由上表3、表4数据可知,兰炭粉末的粒径的大小对于所得炭膜的平均孔径、孔隙率、抗折强度、纯水渗透率具有显著影响,如对比例1-2,当兰炭粉末的粒径过大或过小时,
炭膜的各项性能指标均未能满足本技术对于炭膜的要求,不仅如此,还体现在如图5左所示的表观上,即炭化过程中收缩过快或自粘结性能不足所产生裂缝。此外,炭化温度的变化虽对炭膜的基础物理性能影响小,但对电导率影响却很大,如对比例3-4,所得炭膜的电导率也均不能满足本技术对于炭膜的要求,这使得所得炭膜在电催化较差,其后续应用受到制约。
再多了解一些
本文用于企业家、创业者技术爱好者查询,结果仅供参考。