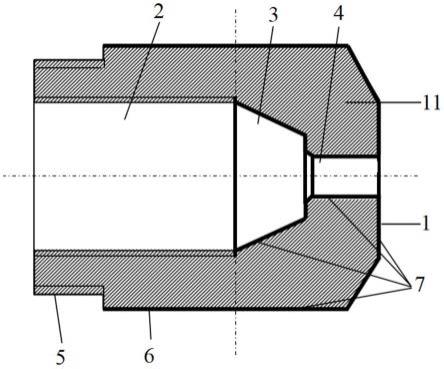
1.本发明属于高温喷嘴技术领域,涉及一种耐冲蚀耐腐蚀高温雾化喷嘴及其制备方法。
背景技术:
2.雾化喷嘴是一种能通过自身独特的结构设计和对流体加压,将流体雾化成微小的颗粒的设备。随着工业的发展,雾化喷嘴的应用范围越来越广泛,同时,特殊的高温、高压和腐蚀环境中需要雾化喷嘴具有耐高温、耐冲蚀、耐腐蚀等性能,因此就有了高温雾化喷嘴的需求。由于喷嘴运行时的苛刻工况,对喷嘴的制造材质就提出了极高的要求,不仅需要耐高温,而且需要优异的耐冲蚀和耐腐蚀性能。普通高温雾化喷嘴的只制造材质主要有310和316l不锈钢,但是不锈钢材质的喷嘴虽然具有较好的抗腐蚀性能,但在像化工类的高温脱硫塔中,温度时常能达到上千摄氏度。在此工况下,不锈钢喷嘴将发生软化,导致喷嘴耐冲蚀性大大降低,导致喷嘴结构发现变化,引发雾化效果变差,甚至发生喷嘴部件快速失效,导致生产中断,造成巨大的直接经济损失和间接损失。而陶瓷类的高温喷嘴具有优异的耐冲蚀、耐腐蚀和耐高温性能,可以满足高温苛刻工况的要求。但陶瓷材质脆性大,加工难度高,成本较高,而且其对喷射过程中的震动比较敏感,易发生震动性脆断。因此需寻求更为优异的材质制造耐冲蚀、耐腐蚀、耐高温喷嘴。
技术实现要素:
3.本发明的一个目的是提供一种耐冲蚀耐腐蚀高温雾化喷嘴,解决了现有高温雾化喷嘴不能同时兼顾耐高温性、耐冲蚀性和良好韧性的问题。
4.本发明的另一个目的是提供一种耐冲蚀耐腐蚀高温雾化喷嘴的制备方法。
5.本发明所采用的第一技术方案是,耐冲蚀耐腐蚀高温雾化喷嘴,包括喷嘴本体,喷嘴本体内部从左到右依次设置有相连通的内管道接口、锥形流体通道和柱形喷孔,喷嘴本体外表面从左到右依次为外管道螺纹连接面和外工作面,喷嘴本体采用tinb高温合金制造而成,外工作面、柱形喷孔外端面、锥形流体通道和柱形喷孔的内表面具有原位生成的层状(tinb)c强化层。
6.层状(tinb)c强化层包括内层、中间层和外层,内层由亚微米级的(tinb)c颗粒组成,中间层由微米级的(tinb)c颗粒组成,外层由准纳米级的(tinb)c颗粒组成。
7.层状(tinb)c强化层中(tinb)c相的体积分数大于97%,其余为fe、si和sic相。
8.本发明所采用的第二技术方案是,耐冲蚀耐腐蚀高温雾化喷嘴的制备方法,包括以下步骤:
9.步骤1,按照质量百分比分别称取以下组分:果壳木炭80~85%,高纯石墨粉1~5%,高纯na2co32~5%,高纯baco310~15%,以上各组分的质量百分比之和为100%;
10.步骤2,将步骤1称取的各组分粉末装入混料机中,混料10min~30min,制备混合粉剂;
11.步骤3,将tinb高温合金块依据雾化喷嘴既定尺寸加工成喷嘴毛坯件,然后对毛坯件内外表面进行精加工和抛光处理,使毛坯件内外表面粗糙度ra不大于3μm,获得喷嘴工件;
12.步骤4,在喷嘴工件的内管道接口内表面和外管道螺纹连接面上均匀涂覆防渗碳涂料,形成防渗碳层;
13.步骤5,将步骤2中所得混合粉剂均匀铺设在模具内底部,再用步骤2中所得混合粉剂灌满喷嘴工件内部空腔,然后将喷嘴工件放置在铺设有混合粉剂的模具内,在喷嘴工件外围填充步骤2所得混合粉剂;
14.步骤6,将填充好的模具装入高温炉内,进行1000~1250℃高温渗碳处理,即获得耐冲蚀耐腐蚀高温雾化喷嘴坯;
15.步骤7,清除雾化喷嘴坯内外表面的防渗碳层,对内外表面进行抛光处理,然后对内管道接口内表面和外管道螺纹连接面进行螺纹加工,即制得耐冲蚀耐腐蚀高温雾化喷嘴。
16.步骤1中,果壳木炭和高纯石墨粉的质量百分比总和不大于86%。
17.步骤1中,果壳木炭的粒径为0.2mm~1mm,高纯石墨粉的纯度大于99.0%,高纯na2co3的纯度大于99.8%,高纯baco3的纯度大于99.0%。
18.步骤4中,防渗碳层厚度为0.5mm~1.2mm,此处防渗碳层厚度若太小,会影响喷嘴工件内管道接口内表面和外管道螺纹连接面的防渗碳效果,若太大,容易剥落。
19.步骤5中,在喷嘴工件外围填充步骤2所得混合粉剂,喷嘴工件与模具内壁的间距不小于5mm,喷嘴工件顶部混合粉剂厚度不小于5mm。
20.步骤6具体包括将填充好的模具装入高温炉内,密封高温炉,先将炉温升至400~600℃保温10min~20min进行预脱气、脱水,然后升温至1000~1250℃保温1h~24h进行渗碳处理,再将炉温降温至400-500℃,随后随炉冷却至室温,即获得耐冲蚀耐腐蚀高温雾化喷嘴坯。
21.步骤6中,炉温的升温速率和降温速率都不高于10℃/min,高温渗碳处理过程中,炉内气压不小于0.3mpa。
22.本发明的有益效果是,利用固体渗碳工艺,在tinb高温合金制备的喷嘴工件既定工作面上原位生成高致密的层状(tinb)c强化层,该强化层耐高温,具有良好的耐腐蚀性,强化层硬度不小于hv2000,大幅提高了雾化喷嘴表面的耐冲蚀性;层状(tinb)c强化层由不同粒径的三层(tinb)c颗粒组成,具有改善表面强化层硬而脆性的问题,其次,原位生成的层状(tinb)c强化层具有优异的异质界面结合强度,改善了强化层易于剥落的问题,可满足耐冲蚀、耐腐蚀耐高温雾化喷嘴的苛刻工况需求,同时tinb合金易加工,其材料成本与加工成本总和不高于陶瓷类喷嘴,经济成本相对较低。
附图说明
23.图1是本发明耐冲蚀耐腐蚀高温雾化喷嘴的结构示意图及强化层位置示意图;
24.图2是本发明耐冲蚀耐腐蚀高温雾化喷嘴工作面强化层的结构示意图;
25.图中,1.喷嘴本体,2.内管道接口,3.锥形流体通道,4.柱形喷孔,5.外管道螺纹连接面,6.外工作面,7.层状(tinb)c强化层,8.内层,9.中间层,10.外层,11.tinb高温合金。
具体实施方式
26.下面结合附图和具体实施方式对本发明进行详细说明。
27.本发明一种耐冲蚀耐腐蚀高温雾化喷嘴,参照图1,包括喷嘴本体1,喷嘴本体1内部从左到右依次设置有相连通的内管道接口2、锥形流体通道3和柱形喷孔4,喷嘴本体1外表面从左到右依次为外管道螺纹连接面5和外工作面6,喷嘴本体1采用tinb高温合金11制造而成,外工作面6、柱形喷孔4外端面、锥形流体通道3和柱形喷孔4的内表面具有原位生成的层状(tinb)c强化层7。tinb高温合金具有优异的高温力性和抗蠕变性能,表面层状(tinb)c强化层具有优异的耐冲蚀、耐腐蚀和耐高温性能。
28.参照图2,层状(tinb)c强化层7包括内层8、中间层9和外层10,内层8由亚微米级的(tinb)c颗粒组成,中间层9由微米级的(tinb)c颗粒组成,外层10由准纳米级的(tinb)c颗粒组成。层状(tinb)c强化层7中(tinb)c相的体积分数大于97%,其余为fe、si和sic相。特殊的层状结构大幅改善了金属碳化物类材料的高脆性,同时(tinb)c的高硬度(大于hv 2000)大幅提高了喷嘴表面的耐冲蚀性,而且金属碳化物本身具有优异的抗腐蚀和耐高温性能。
29.实施例1
30.制备一种工作面强化层厚度为100μm的耐冲蚀耐腐蚀高温雾化喷嘴,包括以下步骤:
31.步骤1,按照质量百分比分别称取以下组分:颗粒等级为0.2mm的果壳木炭80%,高纯石墨粉5%,高纯na2co35%,高纯baco310%,以上各组分的质量百分比之和为100%;高纯石墨粉的纯度大于99.0%,高纯na2co3的纯度大于99.8%,高纯baco3的纯度大于99.0%;
32.步骤2,将步骤1称取的各组分粉末装入混料机中,混料10min,制备混合粉剂;
33.步骤3,将tinb高温合金块依据雾化喷嘴既定尺寸加工成喷嘴毛坯件,然后对毛坯件内外表面进行精加工和抛光处理,毛坯件内外表面粗糙度ra约为3μm,即得喷嘴工件;
34.步骤4,在喷嘴工件的内管道接口内表面和外管道螺纹连接面上均匀涂覆防渗碳涂料,形成防渗碳层,防渗碳层厚度为0.8mm,以防非工作面渗碳;
35.步骤5,将步骤2中所得混合粉剂均匀铺设在模具内底部,再用步骤2中所得混合粉剂灌满喷嘴工件内部空腔,然后将喷嘴工件放置在铺设有混合粉剂的模具内,喷嘴工件与模具内壁的间距为5mm,在喷嘴工件外围填充步骤2所得混合粉剂,喷嘴工件顶部混合粉剂厚度为5mm;
36.步骤6,将填充好的模具装入高温炉内,密封高温炉,先将炉温升至300℃保温20min进行预脱气、脱水,使炉内气压约为0.3mpa,然后以10℃/min升温至1000℃保温24h进行表面渗碳处理,再将炉温以10℃/min速率降温至400℃,随后随炉冷却至室温,即获得耐冲蚀耐腐蚀高温雾化喷嘴坯;
37.步骤7,清除雾化喷嘴坯内外表面的防渗碳层,对内外表面进行抛光处理,然后对内管道接口内表面和外管道螺纹连接面进行螺纹加工,即制得耐冲蚀耐腐蚀高温雾化喷嘴。
38.对实施例1制备的耐冲蚀耐腐蚀高温雾化喷嘴进行组织和性能检测,其中,该喷嘴的工作面(即外工作面、柱形喷孔外端面、锥形流体通道和柱形喷孔的内表面)形成有均匀致密的层状(tinb)c强化层,强化层中(tinb)c的体积百分比为98.6%,余量为fe、si和sic,
强化层厚度约为100μm,表面硬度平均值为hv
0.1 2514。
39.实施例2
40.制备一种工作面强化层厚度为500μm的耐冲蚀耐腐蚀高温雾化喷嘴,包括以下步骤:
41.步骤1,按照质量百分比分别称取以下组分:颗粒等级为1mm的果壳木炭85%,高纯石墨粉1%,高纯na2co32%,高纯baco312%,以上各组分的质量百分比之和为100%;
42.步骤2,将步骤1称取的各组分粉末装入混料机中,混料30min,制备混合粉剂;
43.步骤3,将tinb高温合金块依据雾化喷嘴既定尺寸加工成喷嘴毛坯件,然后对毛坯件内外表面进行精加工和抛光处理,毛坯件内外表面粗糙度ra约为2μm,即得喷嘴工件;
44.步骤4,在喷嘴工件的内管道接口内表面和外管道螺纹连接面上均匀涂覆防渗碳涂料,形成防渗碳层,防渗碳层厚度为1.0mm,以防非工作面渗碳;
45.步骤5,将步骤2中所得混合粉剂均匀铺设在模具内底部,再用步骤2中所得混合粉剂灌满喷嘴工件内部空腔,然后将喷嘴工件放置在铺设有混合粉剂的模具内,喷嘴工件与模具内壁的间距为6mm,在喷嘴工件外围填充步骤2所得混合粉剂,喷嘴工件顶部混合粉剂厚度为5mm;
46.步骤6,将填充好的模具装入高温炉内,密封高温炉,先将炉温升至600℃保温10min进行预脱气、脱水,使炉内气压约为0.4mpa,然后以10℃/min升温至1250℃保温6h进行表面渗碳处理,再以10℃/min速率降温至450℃,随后随炉冷却,降温至室温,即获得耐冲蚀耐腐蚀高温雾化喷嘴坯;
47.步骤7,清除雾化喷嘴坯内外表面的防渗碳层,对内外表面进行抛光处理,然后对内管道接口内表面和外管道螺纹连接面进行螺纹加工,即制得耐冲蚀耐腐蚀高温雾化喷嘴。
48.对实施例2制备的耐冲蚀耐腐蚀高温雾化喷嘴进行组织和性能检测,其中,该喷嘴工作面(即外工作面、柱形喷孔外端面、锥形流体通道和柱形喷孔的内表面)表面形成有致密的层状(tinb)c强化层,强化层中(tinb)c的体积百分比为99.1%,余量为fe、si和sic,强化层厚度约为500μm,表面硬度平均值为hv
0.1 2363。
49.实施例3
50.制备一种工作面强化层厚度为40μm的耐冲蚀耐腐蚀高温雾化喷嘴,包括以下步骤:
51.步骤1,按照质量百分比分别称取以下组分:颗粒等级为0.5mm的果壳木炭82%,高纯石墨粉1%,高纯na2co3为2%,高纯baco3为15%,以上各组分的质量百分比之和为100%;
52.步骤2,将步骤1称取的各组分粉末装入混料机中,混料30min,制备混合粉剂;
53.步骤3,将tinb高温合金块依据雾化喷嘴既定尺寸加工成喷嘴毛坯件,然后对毛坯件内外表面进行精加工和抛光处理,毛坯件内外表面粗糙度ra约为2μm,即得喷嘴工件;
54.步骤4,在喷嘴工件的内管道接口内表面和外管道螺纹连接面上均匀涂覆防渗碳涂料,形成防渗碳层,防渗碳层厚度为0.5mm,以防非工作面渗碳;
55.步骤5,将步骤2中所得混合粉剂均匀铺设在模具内底部,再用步骤2中所得混合粉剂灌满喷嘴工件内部空腔,然后将喷嘴工件放置在铺设有混合粉剂的模具内,喷嘴工件与模具内壁的间距为6mm,在喷嘴工件外围填充步骤2所得混合粉剂,喷嘴工件顶部混合粉剂
厚度为6mm;
56.步骤6,将填充好的模具装入高温炉内,密封高温炉,先将炉温升至500℃保温10min进行预脱气、脱水,使炉内气压约为0.4mpa,然后10℃/min升温至1250℃保温1h进行表面渗碳处理,再以10℃/min速率降温至400℃,随后随炉冷却,降温至室温,即获得耐冲蚀耐腐蚀高温雾化喷嘴坯;
57.步骤7,清除雾化喷嘴坯内外表面的防渗碳层,对内外表面进行抛光处理,然后对内管道接口内表面和外管道螺纹连接面进行螺纹加工,即制得耐冲蚀耐腐蚀高温雾化喷嘴。
58.对实施例3制备的耐冲蚀耐腐蚀高温雾化喷嘴进行组织和性能检测,其中,该喷嘴工作面(即外工作面、柱形喷孔外端面、锥形流体通道和柱形喷孔的内表面)形成有致密的层状(tinb)c强化层,强化层中(tinb)c的体积百分比为98.9%,余量为fe、si和sic,强化层厚度约40μm,表面硬度平均值为hv
0.1 2482。
59.实施例4
60.制备一种工作面强化层厚度为110μm的耐冲蚀耐腐蚀高温雾化喷嘴,包括以下步骤:
61.步骤1,按照质量百分比分别称取以下组分:颗粒等级为0.8mm的果壳木炭80%,高纯石墨粉3%,高纯na2co3为4%,高纯baco3为13%,以上各组分的质量百分比之和为100%;
62.步骤2,将步骤1称取的各组分粉末装入混料机中,混料15min,制备混合粉剂;
63.步骤3,将tinb高温合金块依据雾化喷嘴既定尺寸加工成喷嘴毛坯件,然后对毛坯件内外表面进行精加工和抛光处理,毛坯件内外表面粗糙度ra约为1.8μm,即得喷嘴工件;
64.步骤4,在喷嘴工件的内管道接口内表面和外管道螺纹连接面上均匀涂覆防渗碳涂料,形成防渗碳层,防渗碳层厚度为0.7mm,以防非工作面渗碳;
65.步骤5,将步骤2中所得混合粉剂均匀铺设在模具内底部,再用步骤2中所得混合粉剂灌满喷嘴工件内部空腔,然后将喷嘴工件放置在铺设有混合粉剂的模具内,喷嘴工件与模具内壁的间距为5mm,在喷嘴工件外围填充步骤2所得混合粉剂,喷嘴工件顶部混合粉剂厚度为5mm;
66.步骤6,将填充好的模具装入高温炉内,密封高温炉,先将炉温升至450℃保温15min进行预脱气、脱水,使炉内气压约为0.4mpa,然后10℃/min升温至1150℃保温8h进行表面渗碳处理,再以10℃/min速率降温至400℃,随后随炉冷却,降温至室温,即获得耐冲蚀耐腐蚀高温雾化喷嘴坯;
67.步骤7,清除雾化喷嘴坯内外表面的防渗碳层,对内外表面进行抛光处理,然后对内管道接口内表面和外管道螺纹连接面进行螺纹加工,即制得耐冲蚀耐腐蚀高温雾化喷嘴。
68.对实施例4制备的耐冲蚀耐腐蚀高温雾化喷嘴进行组织和性能检测,其中,该喷嘴工作面(即外工作面、柱形喷孔外端面、锥形流体通道和柱形喷孔的内表面)表面形成有致密的层状多尺度(tinb)c强化层,强化层中(tinb)c的体积百分比为99.2%,余量为fe、si和sic,强化层厚度约110μm,表面硬度平均值为hv
0.1 2531。
69.实施例5
70.制备一种工作面强化层厚度为820μm的耐冲蚀耐腐蚀高温雾化喷嘴,包括以下步
骤:
71.步骤1,按照质量百分比分别称取以下组分:颗粒等级为0.6mm的果壳木炭83%,高纯石墨粉5%,高纯na2co3为2%,高纯baco3为10%,以上各组分的质量百分比之和为100%;
72.步骤2,将步骤1称取的各组分粉末装入混料机中,混料30min,制备混合粉剂;
73.步骤3,将tinb高温合金块依据雾化喷嘴既定尺寸加工成喷嘴毛坯件,然后对毛坯件内外表面进行精加工和抛光处理,毛坯件内外表面粗糙度ra约为2μm,即得喷嘴工件;
74.步骤4,在喷嘴工件的内管道接口内表面和外管道螺纹连接面上均匀涂覆防渗碳涂料,形成防渗碳层,防渗碳层厚度为1.2mm,以防非工作面渗碳;
75.步骤5,将步骤2中所得混合粉剂均匀铺设在模具内底部,再用步骤2中所得混合粉剂灌满喷嘴工件内部空腔,然后将喷嘴工件放置在铺设有混合粉剂的模具内,喷嘴工件与模具内壁的间距为5mm,在喷嘴工件外围填充步骤2所得混合粉剂,喷嘴工件顶部混合粉剂厚度为5mm;
76.步骤6,将填充好的模具装入高温炉内,密封高温炉,先将炉温升至600℃保温10min进行预脱气、脱水,使炉内气压约为0.4mpa,然后10℃/min升温至1250℃保温12h进行表面渗碳处理,再以10℃/min速率降温至500℃,随后随炉冷却,降温至室温,即获得耐冲蚀耐腐蚀高温雾化喷嘴坯;
77.步骤7,清除雾化喷嘴坯内外表面的防渗碳层,对内外表面进行抛光处理,然后对内管道接口内表面和外管道螺纹连接面进行螺纹加工,即制得耐冲蚀耐腐蚀高温雾化喷嘴。
78.对实施例5制备的耐冲蚀耐腐蚀高温雾化喷嘴进行组织和性能检测,其中,该喷嘴工作面(即外工作面、柱形喷孔外端面、锥形流体通道和柱形喷孔的内表面)表面形成有致密的层状多尺度(tinb)c强化层,强化层中(tinb)c的体积百分比为99.3%,余量为fe、si和sic,强化层厚度约820μm,表面硬度平均值为hv
0.1 2548。
再多了解一些
本文用于企业家、创业者技术爱好者查询,结果仅供参考。