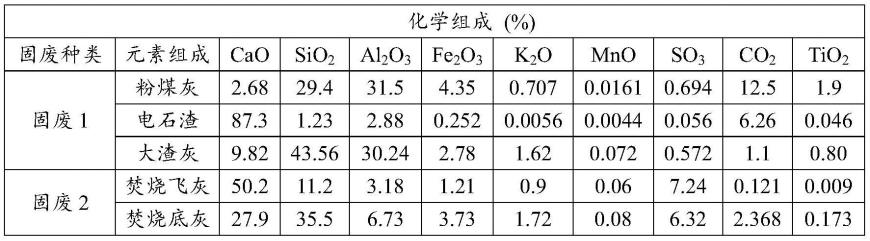
一种利用大宗固废协同矿化co2制备建筑材料的方法
技术领域
1.本发明涉及ipc分类的c04b28/00领域,尤其涉及一种利用大宗固废协同矿化co2制备建筑材料的方法。
背景技术:
2.随着经济的发展,人们生活环境的城镇化的加快,煤炭、电力和建筑等行业也随之快速发展,但是与此同时,相关领域所排放的大宗固体废弃物的质量也在逐年攀升。这些大宗固体废弃物的出现不仅占用了大量的土地资源进行储存,还因为其内部复杂的成分,对于环境、水体等都造成了严重的污染。
3.目前,固废的资源化手段主要集中于建材化利用,而现有的固废建材化利用手段多数都是高耗能的。例如现有技术(cn104072193b)中公开了一种基于含硅铝固废的发泡陶瓷材料及制备防火保温板的方法,以硅铝质固废为原材料,通过添加少量含钙矿石、助溶剂及发泡剂,制备发泡陶瓷材料和防火保温板,该方法虽然实现了硅铝质固废的资源化利用,但其生产过程中的能耗很高,产生了大量的co2。现有技术(cn106915938b)公开了一种利用工业固废制备硫铝酸盐超高水充填材料的系统和方法,主要利用煤矸石等硅铝铁基固废和脱硫石膏等硫酸钙基固废作为原材料,经过原料粉磨、均化、烧成、熟料粉磨等工艺,制得基体材料,而该方法中用到的粉磨、烧成等工艺均是高耗能。此外,现有技术在大宗固废以及二氧化碳的协同矿化,资源再利用方面的研究也较少,且通过矿化反应制得的建筑材料产品的强度也普遍较低,为保证使用性能都需额外添加水泥等辅助胶凝材料,而胶凝材料的生产过程又是高碳排的。
4.因此,亟需一种具有低能耗、低碳排的优点,且能够有效利用大宗固废与二氧化碳的协同作用,制备的建筑材料具有优异的力学强度的利用大宗固废协同矿化co2制备建筑材料的方法。
技术实现要素:
5.为了解决上述问题,本发明第一方面提供了一种利用大宗固废协同矿化co2制备建筑材料的方法,步骤包括制备固废混合料、矿化反应、水热反应和块化成型;所述矿化反应的顺序位于块化成型步骤之前或之后;所述固废混合料包括固废和水。
6.作为一种优选的方案,所述矿化反应的顺序位于块化成型步骤之前,所述制备建筑材料的方法依次包括以下步骤:(1)制备固废混合料;(2)矿化反应;(3)块化成型;(4)水热反应。
7.作为一种优选的方案,所述矿化反应步骤和块化成型步骤之间还包括调节固废混合料的固含量;所述调节固废混合料的固含量具体为:向固废混合料中补加固废或补加固废和石膏;
8.作为一种优选的方案,所述步骤(1)制备的固废混合料中水与固废的质量比为1:1~10:1。
9.作为一种优选的方案,所述矿化反应的顺序位于块化成型步骤之后,所述制备建筑材料的方法依次包括以下步骤:(1)制备固废混合料;(2)块化成型;(3)矿化反应;(4)水热反应。
10.作为一种优选的方案,所述块化成型为模具中浇筑振动成型,所述块化成型所用的固废混合料的固含量为50~85%;所述块化成型为压制成型,所述块化成型所用的固废混合料的固含量为65~95%。
11.本技术中,所述用于块化成型的固废混合料,根据矿化反应顺序的不同,可以是步骤(1)制备的固废混合料,也可以是调节固含量之后的固废混合料。
12.作为一种优选的方案,所述块化成型为模具中浇筑振动成型,所述块化成型所用的固废混合料中还包括石膏。
13.作为一种优选的方案,所述固废混合料中的元素组成满足:
14.n(cao)≥4n(al2o3) 1.5n(sio2)-n(caso4);
15.其中,n(cao)为固废中可发生碳化反应的以氧化物组成计的ca 元素摩尔量;n(al2o3)为固废中以氧化物组成计的al元素摩尔量; n(sio2)为固废中以氧化物组成计的si元素摩尔量;n(caso4)为石膏中caso4的摩尔量。
16.作为一种优选的方案,所述石膏的含量为固废混合料中固废总质量的0.1~5%。
17.本技术中,通过对石膏加入量的限定,不仅有效实现了大宗固废与废气的协同利用,还同时有效提高了所制得的建筑材料的力学性能,使其具有优异的抗氧强度和co2吸收效果。本技术人推测为:适宜含量的石膏的加入,能够在固废混合物的块化成型的过程中,加速混合物的成型以及脱模效率,加强了混合成型后的内容水泥与固废的连接强度,并且促进形成的微小孔隙能够有效地产生银纹和裂纹的转化作用,从而提高极限外作用力的作用下的建筑材料的压力承担上限。但是,石膏的加入量同时需要保持在一个合适的范围内,若石膏的加入量过多,若石膏加入量过多,不利于最终产物种类的优化,影响产品性能。
18.作为一种优选的方案,所述块化成型为压制成型,所述固废混合料中的元素组成满足:
19.n(cao)≥4n(al2o3) 1.5n(sio2);
20.其中,n(cao)为固废中可发生碳化反应的以氧化物组成计的ca 元素摩尔量;n(al2o3)为固废中以氧化物组成计的al元素摩尔量; n(sio2)为固废中以氧化物组成计的si元素摩尔量。
21.作为一种优选的方案,所述的固废为电石渣、镁渣、磷矿渣、钢铁炉渣、炉灰、铁渣、气化渣、粉煤灰、大渣灰、底灰、飞灰、红泥、建筑垃圾、废旧水泥、尾矿、矿石原料中至少一种。
22.作为一种优选的方案,所述矿化反应采用含有co2的气体进行,所述含有co2的气体中co2的体积分数为8~100%,矿化反应时间为 30~240min,矿化反应温度为20~120℃。
23.作为一种优选的方案,含有co2的气体为燃煤电厂烟气、石灰窑烟气、钢铁厂烟气、化工厂烟气、水泥厂烟气、碳捕集解析后的气体中的至少一种。
24.作为一种优选的方案,所述水热反应的具体操作为:将需要进行水热反应的坯体置入反应釜,抽至真空,通入高温水蒸气进行水热反应,反应温度为120~240℃,反应时间为4~12h。
25.作为一种优选的方案,所述矿化反应过程中的矿化压力为 0.3~2mpa。
26.作为一种优选的方案,所述水热反应过程中的压力为1~3mpa。
27.本发明第二方面提供了一种上述利用大宗固废协同矿化co2制备建筑材料的方法的应用,包括该利用大宗固废协同矿化co2制备建筑材料的方法在建材的制备以及co2的回收利用工艺中的应用。
28.有益效果:
29.1、本技术中提供的一种建筑材料的制备方法,其通过多源大宗固废复配和材料设计,既能够充分利用固废中的活性钙元素捕集废气中的co2,又能够在热力学的角度充分的利用大宗固废中各元素的活性,获得具有极高性价比的建筑材料。
30.2、本技术中提供的一种建筑材料的制备方法,其能够通过极低碳排的手段同时解决大宗固废的处理处置问题和co2的捕集利用问题,降低能耗,且适用于已有建材制备产线,具有流程简单、设备通用型强制品外观丰富等优点。
31.3、本技术不特别限定co2气体来源和浓度,可节省co2捕集过程中的能耗和成本,且配方设计中几乎不外掺水泥、砂石等建材常用的高碳排原材料,从原料端降低了整体工艺的碳排。
32.4、本技术中提供的一种建筑材料的制备方法,其能够通过石膏加入量的限定以及水泥比例的控制,不仅有效实现了大宗固废与废气的协同利用,还同时有效提高了所制得的建筑材料的力学性能,使其具有优异的抗氧强度和co2吸收效果,进而可以应用于多种的工业场景,例如钢铁、电力、煤化工、水泥、玻璃、陶瓷等,具有广泛的适用性。
具体实施方式
33.下述实施例以及对比例所述的试块的性能测试包括二氧化碳吸收率和抗压强度,其中二氧化碳的吸收率为固废吸收二氧化碳质量占试块质量的百分比例,其中固体废弃物吸收二氧化碳的含量是通过测试矿化产物的tg/dtg曲线所得,固体废弃物吸收二氧化碳的含量为550~850℃的重量减少量,试块的质量为矿化产物在105℃的质量;抗压强度按照gbt4111-2013《混凝土砌块和砖试验方法》测得。
34.实施例和对比例中的固废信息:固废1来自于合肥某盐煤化工厂,是气化渣、电石渣和大渣灰的混合物;固废2来自于苏州某生活垃圾焚烧厂,是垃圾焚烧底灰和飞灰的混合物。
[0035][0036]
实施例和对比例中的含有co2的气体的组成信息(体积分数):气体 a来自于合肥某盐煤化工厂的尾气;气体b来自于苏州某生活垃圾焚烧厂的烟气经过除尘、脱硫脱硝和有机胺法碳铺集装置后的co2气体。
[0037]
气体组成co2n2so
x
no
x
vocs气体a76.5%18.9%2.3%2%0.3%气体b98.6%1.4%0%0%0%
[0038]
实施例1
[0039]
实施例1第一方面提供了一种利用大宗固废协同矿化co2制备建筑材料的方法,具体步骤包括:(1)制备固废混合料;(2)矿化反应;(3)调节固废混合料的固含量;(4)块化成型;(5)水热反应。
[0040]
实施方式s1-1:
[0041]
(1)将固废1中以质量比粉煤灰:电石渣:大渣灰=4:5:1混合,记作sw1,称取10份sw1和10份水,输送至带有搅拌的反应器内均匀混合,得到混合料1;(2)在60℃下,向混合料1中通入气体a,矿化反应时间为120min;(3)矿化反应结束后,往反应器内补充40 份sw1,并快速搅拌,得到混合料2,混合料2的含固率为81.9%; (4)将混合料2输送至模具中,在15mpa的压力下压制成型,并脱模得到生坯;(5)将脱模后的生坯放入水热反应釜中反应,反应温度为180℃,反应时间为8h。
[0042]
实施方式c1-1:
[0043]
(1)将固废1中以质量比粉煤灰:电石渣:大渣灰=6:3:1混合,记作sw2,称取10份sw2和10份水,输送至带有搅拌的反应器内均匀混合,得到混合料3;(2)在60℃下,向混合料3中通入气体a,矿化反应时间为120min;(3)矿化反应结束后,往反应器内补充40 份sw2,并快速搅拌,得到混合料4,混合料4的含固率为81.9%; (4)将混合料4输送至模具中,在15mpa的压力下压制成型,并脱模得到生坯;(5)将脱模后的生坯放入水热反应釜中反应,反应温度为180℃,反应时间为8h。
[0044]
实施方式s1-2:
[0045]
(1)将固废1以质量比粉煤灰:电石渣:大渣灰=4:5:1混合,记作sw1,称取10份sw1和10份水,输送至带有搅拌的反应器内均匀混合,得到混合料5;(2)在100℃下,向混合料5中通入气体 a,矿化反应时间为40min;(3)矿化反应结束后,往反应器内补充 20份sw1和0.4份石膏,并快速搅拌,得到混合料6,混合料6的含固率为76.9%;(4)将混合料6输送至模具中,浇筑振动成型,待生坯具备可脱模强度时完成脱模得到生坯;(5)将脱模后的生坯放入水热反应釜中反应,反应温度为200℃,反应时间为6h。
[0046]
实施方式c1-2:
[0047]
(1)将固废1以质量比粉煤灰:电石渣:大渣灰=6:3:1混合,记作sw2,称取10份sw2和10份水,输送至带有搅拌的反应器内均匀混合,得到混合料7;(2)在100℃下,向混合料1中通入气体 a,矿化反应时间为40min;(3)矿化反应结束后,往反应器内补充 20份sw1和0.4份石膏,并快速搅拌,得到混合料8,混合料8的含固率为76.9%;(4)将混合料8输送至模具中,浇筑振动成型,待生坯具备可脱模强度时完成脱模得到生坯;(5)将脱模后的生坯放入水热反应釜中反应,反应温度为200℃,反应时间为6h。
[0048]
实施例1中各具体实施方式的性能测试结果如下表:
[0049]
试块名称二氧化碳吸收率(%)平均抗压强度(mpa)s1-118.3318.2c1-116.719.23
s1-219.4721.3c1-216.2410.32
[0050]
上表可以发现,对矿化后浆料压制成块或者浇筑成块进行水热实验的试块,其组成物质氧化钙、二氧化硅和氧化铝的比例对试块的二氧化碳吸收率及抗压强度影响较大。分别对比s1-1和c1-1以及s1-2 和c1-2,当混合原料的氧化钙、二氧化硅和氧化铝的比例满足n(cao) ≥4n(al2o3) 1.5n(sio2)条件时,最终产品的强度和吸收率都要较高,这是由于当氧化钙、二氧化硅和氧化铝的比例不满足上述式子时,一方面原料中的氧化钙含量降低,在矿化反应阶段二氧化碳与其接触几率降低,使得试样对二氧化碳的吸收率较低;另一方面,氧化钙在矿化阶段被反应,剩余的氧化钙无法与硅铝质充分反应生成强度增强相 (csh/aft/afm),进而使得试样的抗压强度大大降低。
[0051]
实施例2
[0052]
实施例2第一方面提供了一种利用大宗固废协同矿化co2制备建筑材料的方法,具体步骤包括:(1)制备固废混合料;(2)块化成型;(3)矿化反应;(4)水热反应。
[0053]
实施方式s2-1:
[0054]
(1)将固废2以质量比焚烧飞灰:焚烧底灰=3:2混合,记作sw3,称取100份sw3和20份水,输送至带有搅拌的反应器内均匀混合,得到混合料9,混合料9的含固率为83.3%;(2)将混合料9输送至模具中块化成型,在15mpa的压力下压制成型得生坯,待生坯具备可脱模强度时完成脱模;(3)将脱模后的生坯放入反应釜中,抽真空,通入气体b,进行矿化反应,反应温度为40℃,反应时间为180min; (4)矿化反应完成后,排空反应釜内的气体,再次抽真空,而后通入高温水蒸气进行水热反应,反应温度为160℃,反应时间为10h。
[0055]
实施方式c2-1:
[0056]
(1)将固废2以质量比焚烧底灰:焚烧飞灰=2:3混合,记作sw4,称取100份sw4和20份水,输送至带有搅拌的反应器内均匀混合,得到混合料10,混合料10的含固率为83.3%;(2)将混合料10输送至模具中块化成型,在15mpa的压力下压制成型得生坯,待生坯具备可脱模强度时完成脱模;(3)将脱模后的生坯放入反应釜中,抽真空,通入气体b,进行矿化反应,反应温度为40℃,反应时间为180min; (4)矿化反应完成后,排空反应釜内的气体,再次抽真空,而后通入高温水蒸气进行水热反应,反应温度为160℃,反应时间为10h。
[0057]
实施方式s2-2:
[0058]
(1)将固废2以质量比焚烧底灰:焚烧飞灰=3:2混合,记作sw3,称取30份sw3、15份水,0.2份石膏,输送至带有搅拌的反应器内均匀混合,得到混合料11,混合料11的含固率为66.67%;(2)将混合料11输送至模具中,浇筑振动成型,待生坯具备可脱模强度时完成脱模,得到生坯;(3)将脱模后的生坯放入反应釜中,抽真空,通入气体b,进行矿化反应,反应温度为80℃,反应时间为80min;(4) 矿化反应完成后,排空反应釜内的气体,再次抽真空,而后通入高温水蒸气进行水热反应,反应温度为140℃,反应时间为12h。
[0059]
实施方式c2-2:
[0060]
(1)将固废2以质量比焚烧底灰:焚烧飞灰=2:3混合,记作sw4,称取30份sw1,15份水,0.2份石膏,输送至带有搅拌的反应器内均匀混合,得到混合料12,混合料12的含固率为66.67%;(2)将混合料12输送至模具中,浇筑振动成型,待生坯具备可脱模强度时完成脱模,得到生坯;(3)将脱模后的生坯放入反应釜中,抽真空,通入气体b,进行矿化反应,反应
温度为80℃,反应时间为80min;(4) 矿化反应完成后,排空反应釜内的气体,再次抽真空,而后通入高温水蒸气进行水热反应,反应温度为140℃,反应时间为12h。
[0061]
实施例2中各具体实施方式的性能测试结果如下表:
[0062]
试块名称二氧化碳吸收率(%)平均抗压强度(mpa)s2-115.4318.47c2-111.017.23s2-216.0117.94c2-212.559.71
[0063]
通过上表可以发现,虽然固体废弃物原料发生了改变,但氧化钙、二氧化硅和氧化铝的比例对试块抗压强度和二氧化碳吸收率的影响效果是一样的。只要混合原料中的氧化钙、二氧化硅和氧化铝的比例满足n(cao)≥4n(al2o3) 1.5n(sio2)-n(caso4)条件时(固废混合料中未添加石膏时,n(caso4)=0),最终产品的强度和吸收率都会较高,这也证明所述规律适用于各种场景。
[0064]
对比例1
[0065]
对比例1第一方面提供了一种利用大宗固废协同矿化co2制备建筑材料的方法,具体步骤包括:
[0066]
(1)将固废以质量比焚烧飞灰:焚烧底灰=6:4混合,记作sw2-1,称取100份sw1和20份水,输送至带有搅拌的反应器内均匀混合,得到混合料13;(2)将混合料13输送至模具中块化成型,在15mpa 的压力下压制成型得生坯,待生坯具备可脱模强度时完成脱模;(3) 将脱模后的生坯放入反应釜中,抽真空,通入气体b,进行矿化反应,反应温度为40℃,反应时间为180min。
[0067]
对比例2
[0068]
(1)将固废2以质量比焚烧飞灰:焚烧底灰=6:4混合,记作 sw2-1,称取100份sw1和20份水,输送至带有搅拌的反应器内均匀混合,得到混合料14;(2)将混合料14输送至模具中块化成型,在15mpa的压力下压制成型得生坯,待生坯具备可脱模强度时完成脱模;(3)将脱模后的生坯放入反应釜中,抽真空,而后通入高温水蒸气进行水热反应,反应温度为160℃,反应时间为10h。
[0069]
试块名称二氧化碳吸收率(%)平均抗压强度(mpa)实施例2-s2-115.4318.47对比例114.895.23对比例2-16.31
[0070]
对比实施例和对比例可知,仅经过矿化反应的试块虽然固碳率有保证,但是反应后的试块强度较低,这是由于矿化后的产物主要为板状方解石,虽然填充了一部分孔隙,但晶体之间印染存在少量的孔隙,容易产生微裂纹,导致矿化后试块强度较低。仅水热后产品对二氧化碳的抗压强度高于仅矿化的,这是由于水热生成csh,其呈凝胶状,可作为粘结剂填充在晶相间,使得产品的强度大大提高;但仅水热的试块强度低于实施例的,这是由于矿化生成的板状碳酸钙水热反应阶段作为杂质相,降低了水热反应的晶格能,促使水热反应更充分。
再多了解一些
本文用于企业家、创业者技术爱好者查询,结果仅供参考。