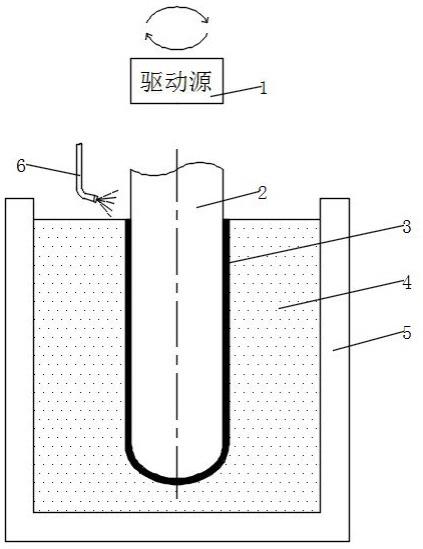
1.本发明涉及高压瓶制造技术领域,尤其是一种高压瓶内胆通过铸造成型的方法。
背景技术:
2.金属高压瓶内胆主流的制造方法有冲拔成型和旋压成型,通常采用圆柱型的钢坯、棒材经过切断、冲挤或旋转数铣得到带有内底的高压瓶内胆粗料,再经过齐口、收口等工艺得到完整的高压瓶内胆,再进一步通过热处理、表面处理、覆层处理、检验等工序得到高压气瓶。
技术实现要素:
3.针对现有高压瓶制造过程中,通过硬冲挤和旋铣加工高压瓶内胆存在设备吨位要求高、材料利用率低的问题,提出一种高压瓶直接铸造成型的方法,可以更简便的得到带有内底的高压瓶内胆粗料。
4.本发明采用的技术方案是:s1,将耐火材料涂覆在模具表面,将模具预加热至一定温度;s2,将模具置入熔融状态的金属液中,并使之匀速转动;s3,将模具取出,冷却至一定温度,使之与覆盖在耐火材料表面的高压瓶内胆粗料分离;s4,粗料经过旋压收口得到高压瓶内胆。
5.进一步地,铸造过程中向工作环境中通入保护气体或者保持真空环境,防止金属和铸件氧化。
6.再进一步地,模具浸入熔融状态的金属液之前对模具进行预热或预冷,可采取烘干和喷射的方式,以维持模具形状以及模具与熔融金属之间的温差。
7.再进一步地,模具从熔融状态的金属中取出后,继续使其匀速转动,控制壁厚的均匀性。
8.上述耐火材料可以使用石墨、滑石粉、硅藻土粉等耐火物质与粘结剂混合,涂覆在模具表面,起保护模具以及方便脱模的作用;上述熔融状态的金属包括高温下液态和固液混合状态的金属,金属包括合金以及微量非金属元素;上述保护气体可以采用氮气、氩气、氦气等惰性气体以及它们的混合气体。
9.高压瓶内胆的厚度由熔融状态金属的温度、模具的进入温度、以及模具在熔融金属中的停留时间控制,一般的,模具与金属的温差越大,熔融金属对模具的附着力越好,内胆的可制壁厚越大。上述温度和时间的确定应根据内胆的材料和所需厚度多次测试调整,以确定最佳温度、时间。
10.本发明相比于一般的高压瓶内胆制造方式,避免了冲压和机械加工材料损耗的问题。利用类似铸造的方法成型出高压瓶内胆粗料,将耐高温材料制成的模具置于熔融状态的金属中,使其被金属材料充分浸满,避免了传统铸造中金属材料过早冷却的问题,工艺简
单可靠,节约成本。
附图说明
11.图1为实施方式中所诉储氢瓶内胆粗料的加工示意图。图式是显示较佳实施例,仅为解说之用。
12.图中:1.驱动源,2.模具,3.成型铸件,4.熔融状态的金属,5.金属池,6.气体喷嘴。
具体实施方式
13.生产一种储氢瓶内胆:s1.制造模具,将砂型制成未收口储氢瓶内胆的形状,在砂型表面涂覆涂料以改善表面质量、便于脱模,并烘干至200℃;s2.在金属池中将cr10ni9ti不锈钢加热至1500℃以上的熔融状态,利用布置在桁架上的驱动源抓取吊挂模具,将砂型模具浸于熔融金属中,使用驱动源使其匀速旋转6~8秒,期间利用气体喷嘴向工作面喷射氮气,隔绝氧气;s3.将砂型模具从金属池中吊出,转移至后续加工区域,按每分钟10转的速度继续保持匀速旋转,使用喷嘴环绕模具喷射冷却气流,直至模具表面温度冷却至1300℃以下,分离砂型和铸件,继续冷却至室温,得到储氢瓶内胆粗料;s4.粗料经过数控旋压机旋压收口得到储氢瓶内胆。
14.砂型为一次性模具,每次加工后需要重新制作砂型。
15.在另一个实施例中采取金属型表面涂覆耐火材料的方式制造重复使用模具,先将金属型一端通过数控机床加工成内胆表面的形状,加热至170~200℃时在金属型工作表面均匀地涂覆主要有效成分为石墨的耐火材料,在重复试验过程中,通过控制金属型初始温度和冷却速度,得到不同壁厚的内胆粗料,每次加工完成后清理模具并重新涂抹耐火材料,金属型可多次使用。
16.在实际操作过程中对不同材料的熔融金属应使用不同的保护气体或保持不同等级的真空环境,这取决于金属还原性的强弱,还需要综合考虑成本因素,在一些实施例中保护气体氮气和氩气能同时起冷却气体的作用。
17.最后应该说明的是,以上所诉,仅为本发明专利较佳的具体实施方式,并不用于限制本发明专利,对于本领域的技术人员来讲,依然可以对前述各实施例所记载的技术方案进行多种变化、修改、替换和变型,本发明的保护范围由所附权利要求及其等同物限定。
技术特征:
1.一种高压瓶直接铸造成型法,包括以下步骤:s1,将耐火材料涂覆在模具表面,将模具预加热至一定温度;s2,将模具置入熔融状态的金属中,并使之匀速转动;s3,将模具取出,冷却至一定温度,使之与覆盖在模具表面的粗料分离;s4,粗料经过旋压收口得到高压瓶内胆。2.根据权利要求书1所诉的高压瓶直接铸造成型法,其特征是该方法还可进一步增加两个步骤:(1)向工作环境中通入保护气体或者保持真空环境,防止熔融金属和铸件氧化;(2)模具从熔融金属中取出后,继续匀速转动,控制壁厚均匀性。
技术总结
高压瓶直接铸造成型法,至少包括四个步骤S1,将耐火材料涂覆在模具表面,将模具预加热至一定温度;S2,将模具置入熔融状态的金属中,并使之匀速转动;S3,将模具取出,冷却至一定温度,使之与覆盖在模具表面的粗料分离;S4,粗料经过旋压收口得到高压瓶内胆。还可以进一步增加两个步骤:(1)向工作环境中通入保护气体或者保持真空环境,防止熔融金属和铸件氧化。(2)模具从熔融金属中取出后,继续匀速转动,控制壁厚均匀性。通过该方法制造高压瓶,可以避免冲拔成型和旋压成型需要的高吨位设备,提高了材料利用率,节约成本,且能规避常规铸造成型中金属冷却不均匀的问题。中金属冷却不均匀的问题。中金属冷却不均匀的问题。
技术研发人员:廖强
受保护的技术使用者:安徽强龙工业有限公司
技术研发日:2022.07.07
技术公布日:2022/8/26
再多了解一些
本文用于企业家、创业者技术爱好者查询,结果仅供参考。