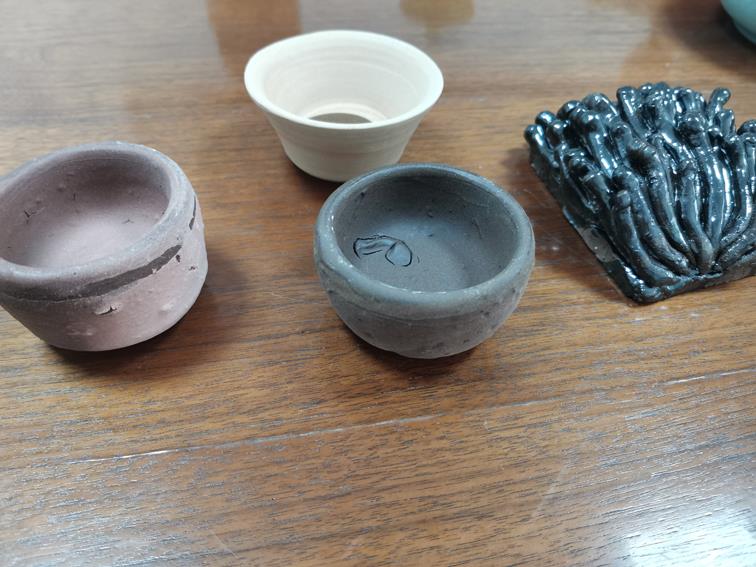
1.本发明涉及一种陶瓷技术领域,特别是涉及一种以机制砂淤泥为原料制备的陶瓷及制造方法。
背景技术:
2.国内地区数家机制砂石厂在洗砂过程中排放大力的淤泥,占用大量的土地、山林、耕地等进行填埋或倒掉,且淤泥中含有化工沉淀剂等化学成分对环境造成不利影响。
3.从机制砂淤泥化学组成看,淤泥中主要含有大量的sio2、al2o3等成分;从组成来看,机制砂淤泥可替代陶瓷原料作为配料引入。目前,在我国关于利用机制砂厂淤泥生产陶瓷的研究甚少。将废弃的机制砂淤泥作为制造陶瓷的原料,降低了原料成本,减轻了环境危害,具有显著的社会效益和经济效益。为此,一种以机制砂淤泥为原料制备泥坯及陶瓷的制造方法亟待研发。
技术实现要素:
4.本发明要解决的技术问题是提供一种以机制砂淤泥为原料制备陶瓷及制造方法,提高机制砂淤泥的利用率。
5.为解决以上技术问题,本发明的技术方案是:一种以机制砂淤泥为原料制备泥坯及陶瓷的制造方法。其所用原料主要是机制砂淤泥(含水率20%~35%)、水、外加原料和添加剂,重量百分比为55~95:5~8:8~35:1~5。
6.进一步的,所述原料由如下重量份的组份包括:机制砂淤泥35~85份,石英25~55份,氧化铝10~45份,高岭土15~45份,膨润土30~55份,长石0~20份,滑石0~10份;以陶瓷坯料计,所述添加剂的组成为粘结剂0~10份,増塑剂0~10份,润滑剂0~25份,分散剂0~8份。
7.进一步的,所述机制砂淤泥化学组成含有sio
2 45~75%,al2o
3 20~55%,cao0.5~1.5%,mgo 0.5~1.8%,k2o 1.5~2.5%,na2o 0.2~1.0%,cao 0.1~0.3%,mgo 0.1~1.0%,tio
2 0.5~1.0%,so
3 0.05~1.0%,i.l 3.0~7.0%,其他微量元素(铜、镍、铬、铅、总砷、总汞、氯甲烷、氯乙烯。1,1-二氯乙烯等)0.01~1%。
8.进一步的,粘结剂为羧甲基纤维素、聚乙烯醇、淀粉、甘油中一种或多种;增塑剂为乙酸三甘醇、硬脂酸丁酯、甘油、松香酸甲酯中的一种或多种;润滑剂为醋酸纤维素、石蜡、硬脂酸、煤油、油酸中的一种或多种;分散剂为聚甲基丙稀酰胺(pmaa-nh4) 、蓖麻油(cto)、氯化铵(nh4cl)、聚乙二醇(平均分子量为20000)、三油酸甘油酯(gto) 中的一种或多种。上述添加剂可提高球磨混合物中固含量,保证陶瓷坯料料浆的分散性和稳定性。上述添加剂使原料料浆效果佳,且添加剂不易挥发,对人体和环境都较安全。
9.进一步的,所述陶瓷的坯用原料为机制砂淤泥、石英、氧化铝、高岭土、膨润土、长石、滑石;所述陶瓷坯用原料的粒度为80或100目筛以下。所述陶瓷坯用原料中选用的瓷土为膨润土、黑泥和龙泉土中一种或多种;所述陶瓷的坯用原料添加剂为粘结剂、増塑剂、润
滑剂和分散剂。所述陶瓷的坯用瓷土原料为黑泥、膨润土和瓷土中的一种或多种;进一步的,一种以机制砂淤泥为原料制备的陶瓷制造方法,包括以下步s1 将坯用原料和水按混合细磨至全部通过万孔筛,并在混料机中搅拌混合1~2h;按重量比例称取坯用原料、水、添加剂为50~85:0.5~1.0:0.05~0.85进行化浆搅拌混合1~3h,过筛除铁后形成料浆;s2 经多次真空练泥后,进行陈腐工艺,后期再进行加工成型;s3 将成型的坯体进行干燥,经微波或热风干燥后,在500~600℃温度下进行素烧,保温0.5~1h;s4 待冷却后,再施釉水1~2mm,在氧化或还原气氛下热处理温度900~1200℃下烧成,热处理升温速度为2~5℃/min,保温1~2h,获得一种以机制砂淤泥为原料的陶瓷制品。
10.进一步的,所述步骤s1中:机制砂淤泥的加入量为陶瓷坯料的1~3倍;添加剂的加入量为陶瓷坯料的0.5~1.5倍。
11.进一步的,所述步骤s1中:d10>0.06μm,d50为0.75
±
0.05μm,d100<5μm,并使用孔径≤1μm的筛网进行过筛除杂,从而得到了陶瓷坯料料浆。陶瓷坯料料浆达到该微纳米级细度后,陶瓷坯体成瓷强度更佳,致密性更佳。
12.进一步的,所述步骤s2中:料浆陈腐中的料浆细度80或100目;料浆陈腐中的料浆细度80或100目;筛余0.1~0.6%;料浆含水率20~35%;料浆比重1.35~1.65%;料浆流速8~15秒。
13.进一步的,所述步骤s4中:所述陶瓷釉浆着色用原料为紫金土、fe2o3、feo、cuo、mno2中的一种或多种,或其他陶瓷色料、色剂。
14.本发明采用机制砂淤泥代替或替换部分现有技术中一般采用的普通石英粉和长石,配合优化的陶瓷坯用原料粉体改性处理,主要是利用机制砂淤泥中游离石英和由长石风化的高岭石,能够与陶瓷坯用原料充分反应的特性,使固相反应进行更为完全,有助于提高陶瓷成瓷强度。
15.本发明以机制砂淤泥为原料制备陶瓷,其坯用料浆具有良好的悬浮性和分散性,化学稳定性高、流变性能良好,环保无污染。而且,素烧过的坯体施釉后再经还原热处理,坯釉的结合性好、成瓷强度高、立体感强,色调细腻无色差。
16.本发明制造陶瓷工艺简单,并且能大幅降低生产成本,充分提高机制砂淤泥资源利用率。
附图说明
17.图1为本发明实施例1的产品效果图;图2为本发明实施例3的产品效果图;图3为本发明实施例4的产品效果图;图4为本发明实施例6的产品效果图。
具体实施方式
18.实施例1
s1按原料由如下重量份的组份组成:以陶瓷坯料计,所述添加剂的组成为粘结剂3份,増塑剂2份,润滑剂15份,分散剂5份。机制砂淤泥35份,石英15份,氧化铝10份,高岭土25份,膨润土1份,长石4份,滑石10份。其中机制砂淤泥化学组分含量为:sio
2 55%,al2o
3 38%,cao0.3%,mgo 1.5%,k2o 1.5%,na2o 0.2%,tio
2 0.4%,so
3 0.05%,i.l 3.0%,其他微量元素(铜、镍、铬、铅、总砷、总汞、氯甲烷、氯乙烯。1,1-二氯乙烯等)0.05%。
19.s2按重量百分比,机制砂淤泥、水、外加原料和添加剂,重量百分比为84:5:6:5。其中,以坯体坯料配方计,所述粘结剂羧甲基纤维素为8%,增塑剂甘油为2%,润滑剂醋酸纤维素为1%,分散剂pmaa-nh4为0.05%。将坯用原料、水和添加剂混合均匀后,置于球磨机中球磨至d10>0.06μm,d90为0.35
±
0.05μm,d100<3μm的细度后,使用孔径325目的筛网进行过筛除杂、陈腐,形成高性能陶瓷坯用料浆。
20.s3将料浆压滤形成泥状,经真空练泥陈腐后脱泡,然后重复进行真空练泥,再将成型的陶瓷坯体进行干燥,经微波干燥和热风干燥后,在750℃温度下进行素烧,保温1.5 h。
21.s4待冷却后,再施传统陶瓷粉青釉,在还原气氛1150℃温度下烧成,保温1.5h,热处理的升温速率为3℃/min,获得成瓷强度高、抗折抗压强度佳、色彩鲜艳、纹理自然、质感柔和、立体感强、具有天然粉青纹理和色彩,表面较平整和光滑的陶瓷制品。
22.实施例2s1按原料由如下重量份的组份包括:以陶瓷坯料计,所述添加剂的组成为粘结剂5份,増塑剂4份,润滑剂21份,分散剂7份。按原料由如下重量份的组份组成:机制砂淤泥50份,石英50份,煅烧氧化铝粉20份,煅烧高岭土25份,高岭土15份,钾长石4份,黑泥8份,膨润土0.5份。其中机制砂淤泥化学组分含量为:sio
2 64.42%,al2o
3 26.54%,cao0.25%,mgo 0.6%,k2o 2.5%,na2o 0.2%,tio
2 0.4%,so
3 0.08%,i.l 5.0%,其他微量元素(铜、镍、铬、铅、总砷、总汞、氯甲烷、氯乙烯。1,1-二氯乙烯等)0.06%。
23.s2按重量百分比,机制砂淤泥、水、外加原料和添加剂,重量百分比为75:8:12:5。其中,以坯体坯料配方计,所述添加剂的组成粘结剂聚乙烯醇为10%,增塑剂乙酸三甘醇为13%,润滑剂醋酸纤维素为21%,分散剂聚乙二醇为1%。将坯用原料、水和添加剂混合均匀后,置于球磨机中球磨至d10>0.06μm,d50为0.35
±
0.05μm,d100<3μm的细度后,使用孔径325目的筛网进行过筛除杂、陈腐,形成高性能陶瓷坯用料浆。
24.s3将料浆压滤形成泥状,经真空练泥陈腐后脱泡,然后重复进行真空练泥,再将成型的陶瓷坯体进行干燥,经微波干燥和热风干燥后,在600℃温度下进行素烧,保温1.5h。
25.s4待冷却后,再施传统陶瓷豆青釉,在还原气氛1200℃温度下烧成,保温2.5h,热处理的升温速率为2℃/min,获得成瓷强度高、抗折抗压强度佳、纹理自然、质感柔和、立体感强、具有天然豆青般纹理,表面较平整、光滑的陶瓷制品。
26.实施例3s1按原料由如下重量份的组份包括:以陶瓷坯料计,所述添加剂的组成为粘结剂5份,増塑剂7份,润滑剂6份,分散剂3份。按原料由如下重量份的组份组成:机制砂淤泥52份,石英56份,煅烧氧化铝粉25份,煅烧高岭土34份,黑泥16份,钾长石5份,膨润土0.7份。其中机制砂淤泥化学组分含量为:sio
2 44.38%,al2o
3 55.74%,cao1.5%,mgo 1.8%,k2o 2.5%,na2o 1.0%,tio
2 1.0%,so
3 0.08%,i.l 7.0%,其他微量元素(铜、镍、铬、铅、总砷、总汞、氯甲烷、氯乙烯。1,1-二氯乙烯等)0.06%。
27.s2按重量百分比,机制砂淤泥、水、外加原料和添加剂,重量百分比为81:3:11:5。其中,以坯体坯料配方计,所述添加剂的组成粘结剂淀粉为6.5%,增塑剂甘油为11%,润滑剂醋酸纤维素为23%,分散剂gto为2%。将坯用原料、水和添加剂混合均匀后,置于球磨机中球磨至d10>0.06μm,d50为0.35
±
0.05μm,d100<3μm的细度后,使用孔径325目的筛网进行过筛除杂、陈腐,形成高性能陶瓷坯用料浆。
28.s3将料浆压滤形成泥状,经真空练泥陈腐后脱泡,然后重复进行真空练泥,再将成型的陶瓷坯体进行干燥,经微波干燥和热风干燥后,在750℃温度下进行素烧,保温2h。
29.s4待冷却后,再施传统陶瓷青釉,在还原气氛1250℃温度下烧成,保温1.5h,热处理的升温速率为2℃/min,获得成瓷强度高、抗折抗压强度佳、纹理自然、质感柔和、立体感强,具有天然梅子青纹理,表面较平整、光滑的陶瓷产品。
30.实施例4s1按原料由如下重量份的组份包括:以陶瓷坯料计,所述添加剂的组成为粘结剂4份,増塑剂9份,润滑剂8份,分散剂2份。按原料由如下重量份的组份组成:机制砂淤泥51份,石英54份,煅烧氧化铝粉27份,煅烧高岭土32份,膨润土14份,钾长石6份,龙泉瓷土10份,膨润土1.0份。其中机制砂淤泥化学组分含量为:sio
2 70.35%,al2o
3 22.74%,cao1.3%,mgo 0.5%,k2o 2.0%,na2o 0.8%,tio
2 0.7%,so
3 0.61%,i.l 6.0%,其他微量元素(铜、镍、铬、铅、总砷、总汞、氯甲烷、氯乙烯。1,1-二氯乙烯等)1.0%。
31.s2按重量百分比,机制砂淤泥、水、外加原料和添加剂,重量百分比为75:8:12:5。其中,以坯体坯料配方计,所述添加剂的组成粘结剂聚乙烯醇为5%,增塑剂乙酸三甘醇为8%,润滑剂硬脂酸为22%,分散剂pmaa-nh4为3.5%。将坯用原料、水和添加剂混合均匀后,置于球磨机中球磨至d10>0.06μm,d50为0.35
±
0.05μm,d100<3μm的细度后,使用孔径325目的筛网,并进行过筛除杂、陈腐,形成高性能陶瓷坯用料浆。
32.s3将料浆压滤形成泥状,经真空练泥陈腐后脱泡,然后重复进行真空练泥,再将成型的陶瓷坯体进行干燥,经微波干燥和热风干燥后,在550℃温度下进行素烧,保温1h。
33.s4 待冷却后,再施传统陶瓷豆青釉,在氧化气氛1200℃温度下烧成,保温1.5h,热处理的升温速率为2℃/min,获得成瓷强度高、抗折抗压强度佳,且纹理自然、质感柔和、立体感强、具有天然豆青纹理,表面较平整、光滑的陶瓷制品。
34.实施例5s1按原料由如下重量份的组份包括:以陶瓷坯料计,所述添加剂的组成为粘结剂9份,増塑剂10份,润滑剂25份,分散剂8份。按原料由如下重量份的组份组成:机制砂淤泥56份,石英58份,煅烧氧化铝粉24份,煅烧高岭土32份,高岭土18份,钾长石6份,膨润土0.9份,黑泥10份。其中机制砂淤泥化学组分含量为:sio
2 46.30%,al2o
3 43.74%,cao1.0%,mgo 1.5%,k2o 2.48%,na2o 0.3%,tio
2 0.6%,so
3 0.83%,i.l 3%,其他微量元素(铜、镍、铬、铅、总砷、总汞、氯甲烷、氯乙烯。1,1-二氯乙烯等)0.7%。
35.s2按重量百分比,机制砂淤泥、水、外加原料和添加剂,重量百分比为56:6:35:3。其中,以坯体坯料配方计,所述添加剂的组成粘结剂淀粉为6%,增塑剂硬脂酸丁酯为15%,润滑剂醋酸纤维素为12%,分散剂聚乙二醇为1.5%。将坯用原料、水和添加剂混合均匀后,置于球磨机中球磨至d10>0.06μm,d90为0.35
±
0.05μm,d100<3μm的细度后,使用孔径325目的筛网,并进行过筛除杂、陈腐,形成高性能陶瓷坯用料浆。
36.s3将料浆压滤形成泥状,经真空练泥陈腐后脱泡,然后重复进行真空练泥,再将成型的陶瓷坯体进行干燥,经微波干燥和热风干燥后,在850℃温度下进行素烧,保温2h。
37.s4待冷却后,再施传统陶瓷釉水,在氧化气氛1280℃温度下烧成,保温2.5h,热处理的升温速率为2℃/min,获得成瓷强度高、抗折抗压强度佳,且纹理自然、质感柔和、立体感强,具天然豆青纹理,表面较平整、光滑的陶瓷制品。
38.实施例6s1按原料由如下重量份的组份组成:以陶瓷坯料计,所述添加剂的组成为粘结剂10份,増塑剂5份,润滑剂18份,分散剂3份。按原料由如下重量份的组份组成:机制砂淤泥50份,石英46份,煅烧氧化铝18份,煅烧高岭土31份,高岭土12份,钾长石6份,膨润土0.8份。其中机制砂淤泥化学组分含量为:sio
2 64.12%,al2o
3 25.63%,cao1.2%,mgo 1.3%,k2o 2.5%,na2o 0.2%,cao 0.2%,mgo 0.7%,tio
2 0.65%,so
3 0.08%,i.l 3.34%,其他微量元素(铜、镍、铬、铅、总砷、总汞、氯甲烷、氯乙烯。1,1-二氯乙烯等)0.08%。
39.s2按重量百分比,机制砂淤泥、水、外加原料和添加剂,重量百分比为75:8:12:5。其中,所述添加剂的组成粘结剂淀粉为6%,增塑剂硬脂酸丁酯为14%,润滑剂油酸为20%,分散剂聚乙二醇为3%。将坯用原料、水和添加剂混合均匀后,置于球磨机中球磨到d10>0.06μm,d50为0.35
±
0.05μm,d100<3μm的细度后,使用孔径325目的筛网,并进行过筛除杂、陈腐,形成高性能陶瓷坯用料浆。
40.s3将料浆压滤形成泥状,经真空练泥陈腐后脱泡,然后重复进行真空练泥,再将成型的陶瓷坯体进行干燥,经微波干燥和热风干燥后,在900℃温度下进行素烧,保温1h。
41.s4待冷却后,再施传统陶瓷釉水,在氧化气氛1300℃温度下烧成,保温2.5h,热处理的升温速率为2℃/min,获得成瓷强度高、抗折抗压强度佳,且纹理自然、质感柔和、立体感强、具天然豆青纹理,表面较平整、光滑的陶瓷产品。
42.本发明技术优势:1、本发明以机制砂淤泥为原料制造陶瓷,不仅大大降低陶瓷的生产成本,且充分利用机制砂加工行业带来的淤泥,减少机制砂淤泥对环境的危害,具有重大的经济和社会效益。不仅符合我国资源再生利用的战略需求,而且符合未来我国建设能源集约化、绿色环保社会的发展要求。
43.2、本发明制备的陶瓷成瓷强度高、致密度高(抗冲击强度达到6.00 kj/ m2,抗折强度达到100 mpa以上,热稳定性可保证180~20 ℃水冷热交换一次不裂),可满足各种陶瓷材料性能要求。
44.3、本发明制造工艺简单,原料成本低(可节约45%以上),有利于节能减排和产业化的生产。
45.对于本领域技术人员而言,显然本发明不限于上述示范性实施例的细节,而且在不背离本发明的精神或基本特征的情况下,能够以其他的具体形式实现本发明。因此,无论从哪一点来看,均应将实施例看作是示范性的,而且是非限制性的,本发明的范围由所附权利要求而不是上述说明限定,因此旨在将权利要求等同要件含义和范围内的所有变化囊括在本发明内。
46.此外,应当理解,虽然本说明书按照实施方式加以描述,但并非每个实施方式仅包含一个独立的技术方案,说明书的这种叙述方式仅仅是为清楚起见,本领域技术人员应当
将说明书作为一个整体,各实施例中的技术方案也可以经适当组合,形成本领域技术人员可以理解的其他实施方式。
再多了解一些
本文用于企业家、创业者技术爱好者查询,结果仅供参考。