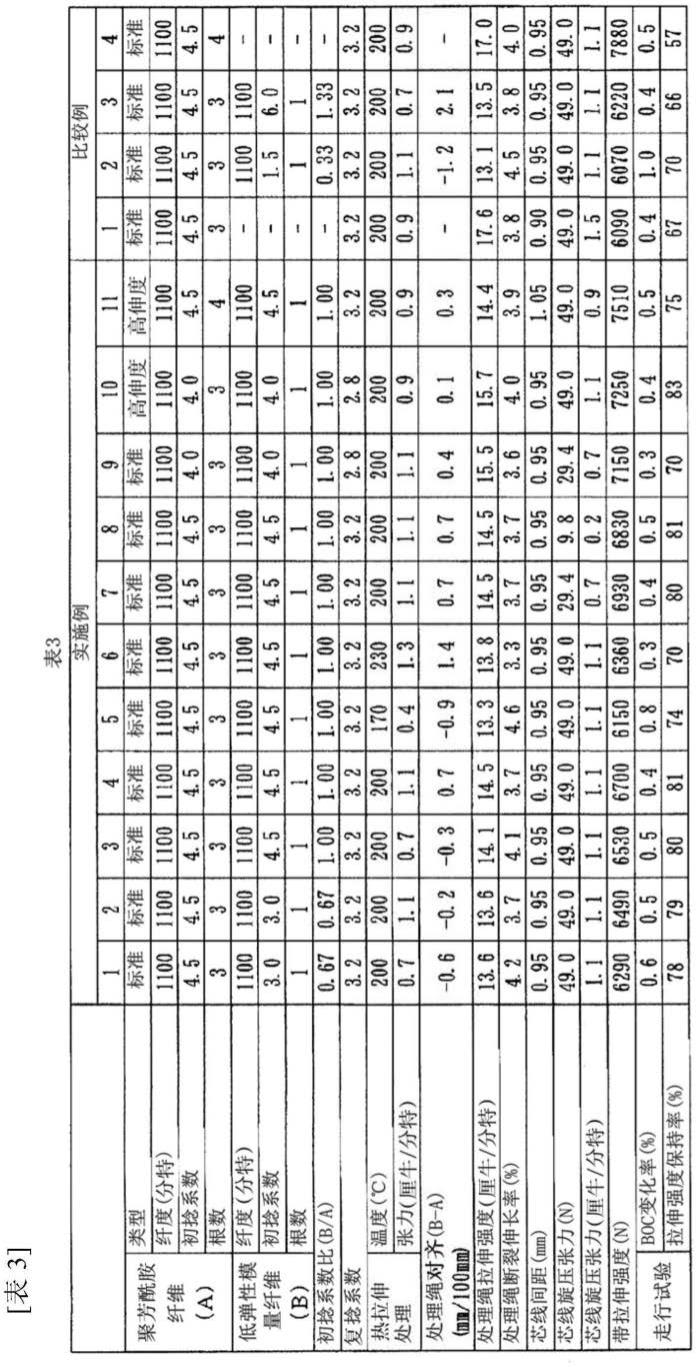
1.本发明涉及用于传动带的芯线和传动带以及它们的制造方法。
背景技术:
2.作为动力传递的机构,使用平带、v带、多楔带、齿形带等传动带的带传动被广泛使用。作为传动带所要求的性能之一,可以列举伸长率小。当传动带的伸长率大时,带的张力降低,容易发生滑动、跳动。如果发生滑动、跳动,则不仅不能正常地进行动力传递,而且传动带的耐久性降低。在汽车辅机驱动用多楔带中,有时使用具有吸收带的伸长而使张力保持恒定的功能的自动张紧器,但是,即使在这种情况下,当带的伸长率过大时,自动张紧器也不能完全吸收带的伸长,带的张力降低。因此,为了减小传动带的伸长,提出了各种含有拉伸强度、拉伸弹性模量高的聚芳酰胺纤维的加捻绳。
3.例如,在专利文献1中公开了一种总纤度4000~5000分特(dtex)的合股捻绳,其是使四根将纤度1000~1250分特的对位系聚芳酰胺纤维以1200~1350的捻系数进行初捻而成的初捻纱以900~1100的捻系数沿着与初捻相反的方向进行复捻而成的。另外,在专利文献2中公开了一种合股捻绳,其是使三根将平均纤度为1000~1250分特、拉伸弹性模量为55~70gpa以及拉伸强度为2800~3500mpa的对位系聚芳酰胺纤维以33~40次/10cm的初捻数进行初捻而成的初捻纱以初捻系数的0.25~1倍的捻系数沿着与初捻相反的方向进行复捻而成的。
4.另一方面,对将聚芳酰胺纤维与其他纤维组合混捻的技术也进行了一些研究。例如,在专利文献3中公开了一种加捻绳,其是将拉伸弹性模量为50~100gpa的高伸度聚芳酰胺纤维与低模量纤维混捻而成的。在该文献中,作为发明效果,记载了在用模压施工法制造时能够抑制芯线的间距的紊乱、损伤,并且即使用于动态张力高的用途也能够维持抗噪声产生性、耐久性。另外,在专利文献4中公开了一种载荷与伸长率的关系为特定范围的橡胶增强用绳,其是将高弹性模量纤维和低弹性模量纤维以65∶35~95∶5的重量比例进行混捻而成的。记载了如此将高弹性模量的纤维与低弹性模量的纤维以特定的比率进行捻纱,由此可以得到在低伸长区域示出低弹性模量、在高伸长区域示出高弹性模量的复合绳,以及能够同时满足成型加工时的延伸带来的橡胶组合物成形性和之后的橡胶成形物使用时的刚性。
5.现有技术文献
6.专利文献
7.专利文献1:国际公开第2015/193934号
8.专利文献2:日本特开2018-71035号公报
9.专利文献3:日本特开2019-7618号公报
10.专利文献4:日本特开2019-157298号公报
技术实现要素:
11.发明所要解决的问题
12.但是,专利文献1和专利文献2中公开的合股捻绳通过初捻和复捻的平衡的最优化、应用高伸度型聚芳酰胺纤维等来兼顾拉伸强度和耐弯曲疲劳性,但近年来一直增加的搭载有isg(一体式起动发电机,integrated starter generator)的发动机用途中的耐久可靠性仍不充分。特别是在仅由聚芳酰胺纤维构成加捻绳的情况下,即使能够抑制传动带的伸长,也难以充分提高耐弯曲疲劳性。
13.另一方面,专利文献3和专利文献4中公开的复合绳最适合于像轮胎、利用模压施工法制造的传动带那样在成型加工时需要绳的伸长的用途。即,通过在聚芳酰胺纤维中混合低弹性模量纤维从而增大轮胎、传动带的成型加工时的绳的伸长成为技术思想。因此,不适合于通过在成型加工时没有使绳伸长的工序的研磨法制造的传动带。这是因为,在成型加工时没有进行伸长的绳在使用传动带时的伸长率变大,使张力降低增大。
14.因此,本发明的目的在于提供拉伸强度高、可兼顾伸长率小和耐弯曲疲劳性高的传动带用芯线和传动带以及它们的制造方法。
15.用于解决问题的方法
16.本发明人为了解决上述问题进行了深入研究,结果发现,利用将含有纤度1500分特以下的聚芳酰胺纤维的两根以上硬质初捻纱(a)与含有低弹性模量纤维的一根软质初捻纱(b)并纱并进行复捻而成的合股捻绳形成传动带用芯线,将上述软质初捻纱(b)的初捻系数相对于上述硬质初捻纱(a)的初捻系数的平均值的比(b/a)调整为0.5~1.2,由此能够提供拉伸强度高、可兼顾伸长率小和耐弯曲疲劳性高的传动带用芯线和传动带,从而完成了本发明。
17.即,本发明的传动带用芯线是包含将两根以上初捻纱并纱并进行复捻而成的合股捻绳的传动带用芯线,其中,上述初捻纱包含两根以上硬质初捻纱(a)和一根软质初捻纱(b),上述硬质初捻纱(a)含有聚芳酰胺纤维,并且各硬质初捻纱(a)的纤度为1500分特以下,上述软质初捻纱(b)含有低弹性模量纤维,并且上述软质初捻纱(b)的初捻系数相对于上述硬质初捻纱(a)的初捻系数的平均值的比(b/a)为0.5~1.2。
18.上述硬质初捻纱(a)的纤度可以为1000~1250分特。上述硬质初捻纱(a)的根数可以为3~4根。上述软质初捻纱(b)的初捻系数可以为2.5~5。上述软质初捻纱(b)可以含有聚酯纤维。上述软质初捻纱(b)的纤度可以为900~1250分特。上述聚芳酰胺纤维可以为高伸度聚芳酰胺纤维。将上述合股捻绳解捻100mm并将初捻纱对齐时,软质初捻纱(b)的长度与硬质初捻纱(a)的平均长度之差(b-a)可以为软质初捻纱(b)的长度-硬质初捻纱(a)的平均长度=-1~2mm。
19.在本发明中还包括上述传动带用芯线的制造方法,其包含:通过将两根以上初捻纱并纱并进行复捻而制备合股捻绳的加捻工序和一边对加捻工序中得到的合股捻绳进行加热一边施加张力的热拉伸处理工序。在上述热拉伸处理工序中,加热温度可以为160~240℃。张力可以为0.3~1.5厘牛/分特(cn/dtex)。
20.在本发明中还包括一种传动带,其包含上述传动带用芯线。上述传动带可以是通过研磨法进行成形而得到的带。上述传动带可以为多楔带。
21.在本发明中还包括上述传动带的制造方法,其包含通过研磨法进行成形而制作传
动带的研磨工序。
22.发明效果
23.在本发明中,利用将含有聚芳酰胺纤维的两根以上硬质初捻纱(a)和含有低弹性模量纤维的一根软质初捻纱(b)并纱并进行复捻而成的合股捻绳形成传动带用芯线,上述软质初捻纱(b)的初捻系数相对于上述硬质初捻纱(a)的初捻系数的平均值的比(b/a)被调整为0.5~1.2,因此,能够提高传动带用芯线和传动带的拉伸强度,能够兼顾伸长率小和耐弯曲疲劳性高。例如,在用作多楔带等传动带的芯线的情况下,在正常地保持动力传递的同时,能够抑制滑动、肋错位(多楔带的肋部越过带轮的槽的现象)、弹出(芯线从传动带的侧面蹦出的现象),还能够提高耐弯曲疲劳性。
附图说明
24.图1a是用于说明本实施方式的加捻绳的热拉伸处理工序前的截面形态的示意图。
25.图1b是用于说明本实施方式的加捻绳的热拉伸处理工序后的截面形态的示意图。
26.图1c是用于说明在捻系数比、热拉伸处理条件等与本实施方式不同的条件下进行热拉伸处理的加捻绳的热拉伸处理工序后的截面形态的示意图。
27.图2是用于说明在热拉伸处理工序中使用的处理装置的示意图。
28.图3是示出本实施方式的多楔带的一例的示意性截面图。
29.图4是示出实施例的走行试验的布局的示意图。
具体实施方式
30.[传动带用芯线]
[0031]
本实施方式的芯线被用作传动带的芯线,包含将两根以上初捻纱并纱并进行复捻而成的合股捻绳。该合股捻绳包含含有纤度1500分特以下的聚芳酰胺纤维的两根以上硬质初捻纱(a)和含有低弹性模量纤维的一根软质初捻纱(b)。在上述初捻纱仅为聚芳酰胺纤维时,耐弯曲疲劳性不足,传动带的耐久性降低。另一方面,在上述初捻纱仅为低弹性模量纤维时,传动带的伸长率变大。
[0032]
(硬质初捻纱(a))
[0033]
硬质初捻纱(a)为含有两根以上聚芳酰胺纤维的聚芳酰胺复丝纱。聚芳酰胺复丝纱根据需要可以含有其他纤维(聚酯纤维等)。相对于复丝纱整体,聚芳酰胺纤维的比例可以为50质量%以上(特别是80~100质量%),通常,全部长丝由聚芳酰胺纤维构成。聚芳酰胺纤维的比例过小时,有可能伸长率变大。
[0034]
聚芳酰胺复丝纱包含两根以上聚芳酰胺长丝即可,可以包含例如约100根~约5000根、优选为约300根~约2000根、进一步优选为约600根~约1000根的长丝。聚芳酰胺长丝的平均纤度例如可以为约0.8分特~约10分特、优选为约0.8分特~约5分特、进一步优选为约1.1分特~约1.7分特。
[0035]
聚芳酰胺纤维可以是单一重复单元的对位系聚芳酰胺纤维(例如,作为聚对苯二甲酰对苯二胺纤维的帝人株式会社制造的“twaron(
トワロン
(注册商标))”、东丽杜邦株式会社制造的“kevlar(
ケブラー
)”等),也可以是包含两个以上重复单元的共聚对位系聚芳酰胺纤维(例如,作为聚对苯二甲酰对苯二胺与3,4
’‑
氧基二亚苯基对苯二甲酰胺的共聚聚
芳酰胺纤维的帝人株式会社制造的
“テクノーラ”
等)。
[0036]
聚芳酰胺纤维在4厘牛/分特载荷时的中间伸度为0.3%以上(例如为0.3~3%)即可,可以优选为0.5%以上(例如为0.5~2%)、进一步优选为0.6%以上(例如为0.6~1.5%)、更优选为0.8%以上(例如为0.8~1.3%)。聚芳酰胺纤维的上述中间伸度过低时,有可能耐弯曲疲劳性不足、耐久性降低。
[0037]
需要说明的是,在本技术中,中间伸度是指4厘牛/分特载荷时的中间伸度,可以通过依据jis l1017(2002)的方法进行测定。
[0038]
聚芳酰胺纤维的拉伸弹性模量可以从约50gpa~约100gpa的范围选择,例如为50~90gpa、优选为60~90gpa(例如为70~90gpa)、进一步优选为60~80gpa(特别是60~70gpa)。在要求高度的耐弯曲疲劳性的用途中,聚芳酰胺纤维可以是拉伸弹性模量为约50gpa~约70gpa的高伸度聚芳酰胺纤维。拉伸弹性模量过小时,有可能伸长率变大;相反过大时,有可能耐弯曲疲劳性降低。
[0039]
需要说明的是,在本技术中,拉伸弹性模量可以通过如下方法测定:通过jis l1013(2010)中记载的方法测定载荷-伸长率曲线并求出载荷1000mpa以下的区域的平均斜率。
[0040]
作为聚芳酰胺纤维的市售品,可以利用例如标准型(东丽杜邦株式会社制造的kevlar29、帝人株式会社制造的twaron1014)和高伸度型(东丽杜邦株式会社制造的kevlar119、帝人株式会社制造的twaron2100)中的任一种。在要求高耐弯曲疲劳性的情况下,优选使用高伸度型,在要求稳定的生产率的情况下,优选标准型。
[0041]
各硬质初捻纱(a)的纤度为1500分特以下、优选为500~1500分特、进一步优选为800~1300分特、更优选为1000~1250分特、最优选为1050~1200分特。纤度过小时,有可能伸长率变大,并且拉伸强度、拉伸弹性模量降低,经济性也降低;相反过大时,有可能耐弯曲疲劳性降低而容易发生芯线的弹出。
[0042]
硬质初捻纱(a)的根数可以为两根以上,优选为2~6根、进一步优选为2~4根、更优选为3~4根(特别是3根)。根数过多时,有可能耐弯曲疲劳性降低。
[0043]
硬质初捻纱(a)的初捻系数的平均值可以从约1~约8的范围选择,例如可以为2~6、优选为2.5~5.5、进一步优选为3~5、更优选为3.5~5(特别是4~5)。初捻系数的平均值过小时,有可能耐弯曲疲劳性降低;相反过大时,有可能拉伸强度、拉伸弹性模量降低。
[0044]
需要说明的是,在本技术中,初捻系数和复捻系数各捻系数可以基于下式算出。
[0045]
捻系数=[捻数(次/m)
×
√总纤度(tex)]/960
[0046]
(软质初捻纱(b))
[0047]
软质初捻纱(b)是含有两根以上低弹性模量纤维的低弹性模量复丝纱。低弹性模量复丝纱根据需要可以含有其他纤维(高弹性模量纤维等)。相对于复丝纱整体,低弹性模量纤维的比例可以为50质量%以上(特别是80~100质量%),通常,全部长丝由低弹性模量纤维构成。
[0048]
低弹性模量复丝纱含有两根以上低弹性模量长丝即可,例如可以含有约100根~约5000根、优选为约120根~约1000根、进一步优选为约300根~约400根低弹性模量长丝。低弹性模量长丝的平均纤度例如可以为约0.8分特~约10分特、优选为约1分特~约8分特、进一步优选为约2分特~约4分特。
[0049]
作为低弹性模量纤维,可以列举例如:天然纤维(棉、麻等)、再生纤维(人造丝、醋酸纤维等)、合成纤维(聚乙烯、聚丙烯等聚烯烃纤维、聚苯乙烯等苯乙烯类纤维、聚四氟乙烯等含氟类纤维、丙烯酸类纤维、聚氯乙烯纤维、聚偏二氯乙烯纤维、维纶纤维、聚乙烯醇等乙烯醇类纤维、聚酰胺纤维、聚酯纤维、聚氨酯纤维等)等。这些纤维可以单独使用或组合使用两种以上。
[0050]
这些纤维中,从经济性、机械特性、耐热性等观点出发,优选聚酯纤维、脂肪族聚酰胺纤维。其中,优选以对苯二甲酸乙二醇酯、2,6-萘二甲酸乙二醇酯等c
2-4
亚烷基芳酯作为主要结构单元的聚酯纤维[聚对苯二甲酸乙二醇酯类纤维(pet纤维)、聚萘二甲酸乙二醇酯类纤维(pen纤维)、聚对苯二甲酸丙二醇酯纤维(ptt纤维)等聚亚烷基芳酯类纤维]、脂肪族聚酰胺纤维(聚酰胺6纤维、聚酰胺46纤维、聚酰胺66纤维、聚酰胺612纤维、聚酰胺12纤维等),进一步优选聚亚烷基芳酯纤维、聚酰胺66纤维等脂肪族聚酰胺纤维,从能够兼顾带伸长率小和耐弯曲疲劳性的观点出发,最优选pet纤维等聚c
2-4
亚烷基-c
6-10
芳酯纤维。
[0051]
作为pet纤维,可以从市售的标准型、低收缩型、高模量低收缩型等中选择,其中,优选能够降低带伸长率、尺寸稳定性优良的高模量低收缩型。作为该市售品,可以列举东丽株式会社制造的
テトロン
(1100t-240-704m、1100t-240-705m、1100t-360-704m)等。
[0052]
低弹性模量纤维的拉伸弹性模量可以为20gpa以下,例如可以为2~18gpa、优选为4~15gpa、进一步优选为8~12gpa。拉伸弹性模量过小时,有可能伸长率变大;相反过大时,有可能耐弯曲疲劳性降低。
[0053]
软质初捻纱(b)的纤度可以为1500分特以下,可以优选为500~1500分特、进一步优选为800~1300分特、更优选为900~1250分特、最优选为1000~1200分特。特别是通过将由上述聚酯纤维形成的软质捻纱(b)的纤度调整为这些范围(特别是900~1250分特),能够在不使带伸长率过大的情况下提高拉伸强度和耐弯曲疲劳性。纤度过小时,有可能耐弯曲疲劳性不能充分提高;相反过大时,有可能传动带的伸长率变大。
[0054]
软质初捻纱(b)的初捻系数可以从约1~约7的范围选择,例如可以为2~6、优选为2.5~5、进一步优选为3~5、更优选为3.5~5(特别是4~5)。初捻系数过小时,有可能传动带的伸长率变大;相反过大时,有可能耐弯曲疲劳性降低。初捻系数小、加捻少的情况下伸长率变大的机理是利用现有的机理不能容易地预测的机理,如后所述,是通过与特定的硬质初捻纱(a)组合而表现出的意外的机理。
[0055]
(合股捻绳的特性)
[0056]
上述合股捻绳是将包含两根以上硬质初捻纱(a)和一根软质初捻纱(b)的初捻纱并纱,沿着与初捻的方向相反的方向施加复捻,得到合股捻纱(合股捻绳)。在初捻的方向与复捻的方向相同的顺捻绳的情况下,由于加捻绳本身的扭转性质(退捻转矩)大,因此容易形成环或扭结(变形),操作性差。另一方面,沿着与初捻的方向相反的方向施加复捻的合股捻绳的情况下,由于初捻和复捻抵消了退捻转矩,因此,环或扭结的形成被抑制,操作性优良。此外,通过使用退捻转矩小的合股捻绳作为传动带的芯线,传动带的直进稳定性提高,能够抑制肋错位、弹出的发生。
[0057]
上述合股捻绳除了上述硬质初捻纱(a)和上述软质初捻纱(b)以外还可以含有其他初捻纱。作为其他初捻纱,可以列举含有全芳香族聚酯纤维的硬质初捻纱、含有聚对苯撑苯并双唑(pbo)纤维的硬质初捻纱、含有碳纤维或玻璃纤维等无机纤维的硬质初捻纱、作
为上述软质初捻纱(b)所例示的软质初捻纱等。其他初捻纱的根数例如可以为3根以下,优选为0~2根、进一步优选为0根或1根。
[0058]
相对于合股捻绳整体,硬质初捻纱(a)和软质初捻纱(b)的合计比例为50质量%以上即可,优选为80质量%以上、进一步优选为90质量%以上、更优选为100质量%。
[0059]
在本实施方式中,上述软质初捻纱(b)的初捻系数相对于上述硬质初捻纱(a)的初捻系数的平均值的比(b/a)为0.5~1.2。在本实施方式中,通过将初捻系数的比(b/a)调整为上述范围,能够提高合股捻绳(复捻纱)中的硬质初捻纱(a)与软质初捻纱(b)的平衡,能够兼顾伸长率小和耐弯曲疲劳性。在初捻系数的比(b/a)小于0.5时,合股捻绳中的软质初捻纱(b)的截面形状自由度变高(即,捻回松散,因此集束性降低,截面形状成为不均匀的形状),结果是传动带的伸长率变大。在初捻系数的比(b/a)超过1.2时,初捻纱(b)的伸长率变大,初捻纱(b)被赶到合股捻绳的周围(后述的图1c的状态),结果耐弯曲疲劳性没有充分提高。
[0060]
上述初捻系数的比(b/a)优选为0.6~1.2、进一步优选为0.7~1.15、更优选为0.8~1.1、最优选为0.9~1.05。
[0061]
上述合股捻绳的复捻系数优选为2~4。在复捻系数小于2时,有可能股线的集束性降低而耐弹出性、耐绽线性降低,复捻系数超过4时,有可能拉伸强度和拉伸弹性模量降低。
[0062]
上述合股捻绳通过后述的热拉伸处理(热定形处理)将解捻时的硬质初捻纱(a)和软质初捻纱(b)的长度调整为特定的范围。详细而言,将上述合股捻绳解捻100mm(将复捻纱解捻)并将初捻纱对齐时,软质初捻纱(b)的长度与硬质初捻纱(a)的平均长度(算术平均值)之差[处理绳对齐(b-a)])可以是软质初捻纱(b)的长度-硬质初捻纱(a)的平均长度=-1~2mm的范围,例如可以为-0.8~1.5mm、优选为-0.5~1mm、进一步优选为-0.3~0.7mm、更优选为-0.2~0.5mm、最优选为0~0.3mm。处理绳对齐(b-a)过小时,有可能带伸长率变大;相反过大时,有可能耐弯曲疲劳性降低。
[0063]
[传动带用芯线的制造方法]
[0064]
本实施方式的传动带用芯线经过通过将两根以上初捻纱并纱并进行复捻而制备合股捻绳的加捻工序和一边对由加捻工序得到的合股捻绳进行加热一边施加张力的热拉伸处理工序而得到。
[0065]
(加捻工序)
[0066]
在加捻工序中,将包含两根以上硬质初捻纱(a)和一根软质初捻纱(b)的初捻纱并纱,以达到上述复捻系数的方式通过惯用的方法沿着与初捻的方向相反的方向施加复捻。
[0067]
构成初捻纱的各初捻纱也是以达到上述初捻系数比的方式通过惯用的方法进行初捻而制作。包含上述硬质初捻纱(a)和软质初捻纱(b)的各初捻纱的加捻方向可以全部为同一方向,也可以根据目标芯线的方向选择沿s方向制作或者沿z方向制作。
[0068]
为了提高耐绽线性和与橡胶成分的粘接性,可以根据需要对复捻而成的加捻绳实施通用的粘接处理,将纤维间(长丝间)粘接,并且在绳表面形成粘接层。作为通用的粘接处理,可以列举:浸渍到含有环氧化合物或多异氰酸酯化合物的处理液中的方法、浸渍到含有间苯二酚(r)和甲醛(f)和胶乳(l)的rfl处理液中的方法、浸渍到橡胶糊中的方法等。这些处理可以单独应用,也可以组合两种以上应用。另外,除了进行浸渍以外,也可以为进行喷雾、涂布的方法,从容易使粘接成分渗透至绳的内部的观点、容易使粘接层的厚度均匀的观
点出发,优选浸渍。
[0069]
(热拉伸处理工序)
[0070]
为了拉伸强度高、能够兼顾伸长率小和耐弯曲疲劳性高,由上述加捻工序得到的加捻绳被供于热拉伸处理(热定形)工序。在热拉伸处理工序中,通过对加捻绳施加热和张力,能够使长丝彼此的融合良好(使长丝间的空隙减少),能够减小加捻绳、芯线、传动带的伸长率。即,对于传动带而言,能够在传动带的成形前除去加捻绳的伸长,能够减小传动带的伸长率。
[0071]
此外,在本实施方式中,通过将硬质初捻纱(a)和软质初捻纱(b)的捻系数比调整为特定范围,能够制备成可兼顾处于此消彼长的关系的伸长率小和耐弯曲疲劳性高的加捻绳的形态。图1a~图1c是用于说明热拉伸处理工序前后的加捻绳的截面形态的示意图。在图1a~图1c中,示出三根硬质初捻纱(a)(图1a~图1c中的a)和一根软质初捻纱(b)(图1a~图1c中的b)的截面形态,图1a示出本实施方式的加捻绳的热拉伸处理工序前的形态。在图1a中,捻纱后,软质初捻纱(b)为比硬质初捻纱(a)更向绳内周方向(图1a中的箭头方向)嵌入(凹陷)的形态。图1b示出本实施方式的加捻绳的热拉伸处理工序后的形态。热拉伸处理后,嵌入绳内部的软质初捻纱(b)向外周方向移动,制备了与硬质初捻纱(a)的平衡良好的捻纱绳。另一方面,图1c示出在捻系数比、热拉伸处理条件等与本实施方式不同的条件下进行热拉伸处理的加捻绳的热拉伸处理工序后的形态。在图1c中,软质初捻纱(b)为比硬质初捻纱(a)更向绳外周方向(图1c中的箭头方向)赶出(突出的)的平衡不良的形态,作为加捻绳整体,为软质初捻纱(b)卷绕于硬质初捻纱(a)的形状。
[0072]
图2中示出在热拉伸处理工序中使用的处理装置的示意图。上述处理装置如图2所示通常具备驱动辊12、加热炉13、折返辊14、驱动辊16。在该处理装置中,加捻绳11卷绕在各辊上,利用从驱动辊12和驱动辊16受到的驱动力在加热炉13中通过。如果将加捻绳11的行进方向设为后方、将与加捻绳11的行进方向相反的方向设为前方,则驱动辊12设置在加热炉13的前方,驱动辊16设置在加热炉13的后方。折返辊14设置在驱动辊12与驱动辊16之间。在热拉伸处理工序中,通过使驱动辊16的旋转速度大于驱动辊12的旋转速度,对加捻绳11赋予张力。加捻绳11的张力可以利用设置在驱动辊12与驱动辊16之间的适当位置的张力计15进行测定,也可以由施加于折返辊14的轴载荷来计算。通过反馈加捻绳11的张力来控制各驱动辊的旋转速度,能够调节施加于加捻绳11的张力。即,在该处理装置中,一边对加捻绳11施加规定的张力,一边在设定为规定温度的加热炉中通过,由此对加捻绳11进行热拉伸处理(热定形处理)。
[0073]
在热拉伸处理工序中,对加捻绳施加的张力可以根据加捻绳的捻系数等从约0.1厘牛/分特~约2厘牛/分特的范围适当选择,例如为0.3~1.5厘牛/分特、优选为0.4~1.2厘牛/分特、进一步优选为0.5~1厘牛/分特(特别是0.6~0.8厘牛/分特)。张力过小时,有可能热拉伸不充分,传动带的伸长率变大。另一方面,张力过大时,有可能热拉伸过量,耐弯曲疲劳性降低。热拉伸过量时,例如,软质初捻纱(b)被赶到合股捻绳的外周方向,变为图1c所示的形态。
[0074]
热拉伸处理工序中的加热温度可以根据形成加捻绳的纤维的材质、捻系数等从约150℃~约250℃的范围适当选择,例如为160~240℃、优选为170~230℃、进一步优选为180~220℃(特别是190~210℃)。加热温度过低时,有可能热拉伸不充分,传动带的伸长率
变大。另一方面,加热温度过高时,有可能加捻绳(特别是软质初捻纱(b))发生熔融或软化。
[0075]
为了提高与橡胶成分的粘接性,可以根据需要对在热拉伸处理工序中热拉伸处理后的加捻绳进一步实施利用橡胶糊的被覆(外涂)处理。
[0076]
[传动带]
[0077]
作为本实施方式的传动带,为芯线由上述芯线形成的传动带,可以列举例如包布v带、切边v带等v带、多楔带、平带、齿形带等。其中,优选通过研磨法进行成形而得到的多楔带。
[0078]
本实施方式的传动带(多楔带)的形态只要具有沿着带长度方向相互平行延伸的两个以上v形肋部就没有特别限制,例如可以例示图3所示的形态。图3是示出本实施方式的多楔带的一例的示意性截面图。图3所示的多楔带具有如下形态:从带下表面(内周面)朝向带上表面(背面)依次层叠有压缩橡胶层(第一橡胶层)2、沿着带长度方向埋设有芯线1的粘接橡胶层(第二橡胶层)4、由包覆布(机织物、针织物、无纺布等)或橡胶组合物构成的延伸层5。在压缩橡胶层2中,形成在带长度方向上延伸的两个以上截面v字形的槽,在该槽之间形成截面v字形(倒梯形)的两个以上v形肋部3(在图3所示的例子中为4个),该各v形肋部3的两个倾斜面(表面)形成摩擦传动面,与带轮接触而传递(摩擦传动)动力。
[0079]
本实施方式的多楔带不限于该形态,只要具备具有至少一部分能够与带轮的v形肋槽部(v形槽部)接触的传动面的压缩橡胶层即可,典型地,具备延伸层、压缩橡胶层和在延伸层与压缩橡胶层之间沿着带长度方向埋设的芯线即可。在本实施方式的多楔带中,例如,可以在不设置粘接橡胶层4的情况下在延伸层5与压缩橡胶层2之间埋设芯线1。此外,也可以为如下形态:将粘接橡胶层4设置在压缩橡胶层2或延伸层5中的任意一者上,将芯线1埋设于粘接橡胶层4(压缩橡胶层2侧)与延伸层5之间、或者粘接橡胶层4(延伸层5侧)与压缩橡胶层2之间。
[0080]
需要说明的是,至少上述压缩橡胶层2可以由以下详细说明的橡胶组合物形成,上述粘接橡胶层4可以由用作粘接橡胶层的惯用的橡胶组合物形成,上述延伸层5可以由用作延伸层的惯用的包覆布或橡胶组合物形成,可以并非由与上述压缩橡胶层2相同的橡胶组合物形成。
[0081]
(芯线)
[0082]
芯线通常是在带宽度方向上以规定的间隔排列的加捻绳。芯线埋设在传动带的橡胶层内即可,在上述例子中,在粘接橡胶层内在带的长度方向上延伸配设,可以在长度方向上配设平行的两根以上芯线,从生产率的观点出发,通常在带的长度方向上近似平行地以规定的间距并列延伸地配设成螺旋状。在配设成螺旋状的情况下,芯线相对于带长度方向的角度例如可以为5
°
以下,从带的直进稳定性的观点出发,越接近0
°
越优选。
[0083]
芯线的平均间距(相邻的芯线的中心间的平均距离)可以根据芯线直径、目标带拉伸强度适当选择,例如为约0.6mm~约2mm、优选为约0.8mm~约1.5mm、进一步优选为约0.9mm~约1.05mm。芯线的平均间距过小时,有可能在带制造工序中发生芯线彼此的缠结;相反过大时,有可能带的拉伸强度和拉伸弹性模量降低。芯线的平均间距是在多楔带的宽度方向的截面中测定10处相邻的芯线的中心间的距离并将它们平均而得到的值。需要说明的是,芯线的中心间的距离可以使用扫描型电子显微镜(sem)、投影仪等公知的装置进行测定。
[0084]
芯线可以为s捻、z捻中的任意一种,为了提高带的直进稳定性,优选交替地配设s捻和z捻。
[0085]
(橡胶组合物)
[0086]
压缩橡胶层、粘接橡胶层和延伸层可以由含有橡胶成分的橡胶组合物形成。作为橡胶成分,可以使用能够硫化或交联的橡胶,可以列举例如:二烯类橡胶[天然橡胶、异戊二烯橡胶、丁二烯橡胶、氯丁二烯橡胶、丁苯橡胶(sbr)、丙烯腈丁二烯橡胶(丁腈橡胶)、氢化丁腈橡胶等]、乙烯-α-烯烃弹性体、氯磺化聚乙烯橡胶、烷基化氯磺化聚乙烯橡胶、环氧氯丙烷橡胶、丙烯酸类橡胶、硅橡胶、聚氨酯橡胶、氟橡胶等。这些橡胶成分可以单独或组合两种以上使用。
[0087]
优选的橡胶成分为乙烯-α-烯烃弹性体[乙烯-丙烯共聚物(epm)、乙烯-丙烯-二烯三元共聚物(epdm)等]和氯丁二烯橡胶。此外,从具有耐臭氧性、耐热性、耐寒性、耐候性、能够减轻带重量的观点出发,特别优选乙烯-α-烯烃弹性体[乙烯-丙烯共聚物(epm)、乙烯-丙烯-二烯三元共聚物(epdm)等]。在橡胶成分含有乙烯-α-烯烃弹性体的情况下,橡胶成分中的乙烯-α-烯烃弹性体的比例可以为50质量%以上(特别是约80质量%~约100质量%),特别优选为100质量%(只有乙烯-α-烯烃弹性体)。
[0088]
橡胶组合物可以还含有短纤维。作为短纤维,可以列举例如作为形成上述芯线的加捻绳的初捻纱中所含的纤维所例示的全部纤维等。由上述纤维形成的短纤维可以单独使用或组合使用两种以上。为了提高橡胶组合物中的分散性、粘接性,可以与芯线同样地对短纤维实施惯用的粘接处理(或表面处理)。短纤维的平均长度例如可以为约0.1mm~约20mm、优选为约0.5mm~约15mm(例如为约1mm~约10mm)、进一步优选为约1.5mm~约5mm(特别是约2mm~约4mm)。通过使短纤维在受到较大的来自带轮的侧压和摩擦力的压缩橡胶层中在带宽度方向上取向,能够确保多楔带的耐侧压性。短纤维的平均纤维直径例如为约1μm~约100μm、优选为约3μm~约50μm、进一步优选为约5μm~约40μm(特别是约10μm~约30μm)。
[0089]
橡胶组合物可以还含有惯用的添加剂。作为惯用的添加剂,可以列举例如:硫化剂或交联剂(或交联剂类)(含硫型硫化剂等)、共交联剂(双马来酰亚胺类等)、硫化助剂或硫化促进剂(秋兰姆类促进剂等)、硫化延迟剂、金属氧化物(氧化锌、氧化镁、氧化钙、氧化钡、氧化铁、氧化铜、氧化钛、氧化铝等)、增强剂(例如,炭黑、含水二氧化硅等氧化硅)、填充剂(粘土、碳酸钙、滑石、云母等)、软化剂(例如,石蜡油、环烷烃类油等油类等)、加工剂或加工助剂(硬脂酸、硬脂酸金属盐、蜡、石蜡、脂肪酸酰胺等)、抗老化剂(抗氧化剂、抗热老化剂、抗弯曲开裂剂、抗臭氧劣化剂等)、着色剂、增粘剂、增塑剂、偶联剂(硅烷偶联剂等)、稳定剂(紫外线吸收剂、热稳定剂等)、阻燃剂、抗静电剂等。这些添加剂可以单独使用或组合使用两种以上。需要说明的是,金属氧化物可以作为交联剂发挥作用。另外,特别地,构成粘接橡胶层的橡胶组合物可以含有粘接性改善剂(间苯二酚-甲醛共缩聚物、氨基树脂等)。
[0090]
构成压缩橡胶层、粘接橡胶层和延伸层的橡胶组合物可以相互相同,也可以相互不同。同样,压缩橡胶层、粘接橡胶层和延伸层中所含的短纤维也可以相互相同,也可以相互不同。
[0091]
(包覆布)
[0092]
延伸层可以由包覆布形成。包覆布例如可以由机织布、广角帆布、针织布、无纺布等布材(优选为机织布)等形成,根据需要可以进行粘接处理、例如利用rfl处理液进行处理
[0109]
硬脂酸:日油株式会社制造的
“ビーズステアリン
酸
つばき”
[0110]
抗老化剂:精工化学株式会社制造的
“ノンフレツクス
od3”[0111]
炭黑haf:东海碳素株式会社制造的
“シースト
3”[0112]
含水二氧化硅:東
ンー
·
シリ
力株式会社制造的“nipsilvn3”[0113]
硫:美源化学公司制造
[0114]
尼龙短纤维:旭化成株式会社制造的
“レオナ”
、平均纤维直径27μm、平均纤维长度3mm
[0115]
石蜡基油:出光兴产株式会社制造的
“ダイアナプロセスオイル”
[0116]
有机过氧化物:化藥
ヌーリオン
株式会社制造的
“パーカドツクス
14”[0117]
[表1]
[0118]
表1:粘接橡胶层用组合物
[0119]
构成成分质量份epdm100氧化锌5硬脂酸1抗老化剂1炭黑haf40含水二氧化硅20硫1二硫化二苯并噻唑2六甲氧基羟甲基三聚氰胺2合计172
[0120]
[表2]
[0121]
表2:压缩橡胶层用组合物
[0122]
构成成分质量份epdm100尼龙短纤维40氧化锌5硬脂酸1炭黑haf60石蜡基油10有机过氧化物2间苯撑双马来酰亚胺22-巯基苯并咪唑2合计222
[0123]
[包覆布]
[0124]
将聚酯纤维与棉的混纺丝(聚酯纤维/棉=50/50质量比)的机织布(120
°
广角编织、纤度为20支的经纱和20支的纬纱、经纱和纬纱的纱密度为75根/50mm、单位面积重量280g/m2)浸渍在下述rfl处理液中后,使其干燥,从而制作包覆布。
[0125]
[rfl处理液]
[0126]
含有间苯二酚2.6质量份、37质量%甲醛1.4质量份、乙烯基吡啶-苯乙烯-丁二烯共聚物胶乳17.2质量份和水78.8质量份的溶液。
[0127]
实施例1
[0128]
[加捻绳的制作]
[0129]
如表3所示,使三根将1100分特的聚芳酰胺纤维束以4.5的捻系数沿z方向初捻而成的初捻纱和一根将1100分特的低弹性模量纤维束以3.0的捻系数沿z方向初捻而成的初捻纱合并,沿s方向以3.2的捻系数进行复捻,制作s捻的合股捻绳。同样地,将初捻的方向设为s方向,将复捻的方向设为z方向,制作z捻的合股捻绳。
[0130]
[纤维间粘接处理~热拉伸处理]
[0131]
将s捻的合股捻绳和z捻的合股捻绳在上述rfl处理液(25℃)中浸渍5秒钟后,进行热拉伸处理,得到s捻的处理绳和z捻的处理绳。热拉伸处理的条件如下:温度为200℃(加热炉的温度)、张力(对加捻绳施加的张力)为0.7厘牛/分特、处理时间为(加捻绳的某一点在加热炉的入口通过直至到达加热炉的出口的时间)为约1分钟。
[0132]
[处理绳对齐(b-a)]
[0133]
1)将检捻机的卡盘间距离设定为25cm,卡盘固定处理绳。
[0134]
2)将复捻进行解捻,测定最短的初捻纱(施加张力而以直线状延伸的纱)的长度。此时,最短的初捻纱以外的初捻纱为松弛的状态。
[0135]
3)切断最短的初捻纱(施加张力而以直线状延伸的纱),测定第二短的初捻纱(通过切断最短的初捻纱,施加张力而以直线状延伸的纱)的长度。
[0136]
4)之后,同样地进行,测定全部初捻纱的长度。
[0137]
5)从软质初捻纱(b)的长度减去硬质初捻纱(a)的平均长度(3或4根的算术平均值),将其差换算为每100mm的长度的差。
[0138]
[多楔带的制作]
[0139]
首先,在表面平滑的圆筒状的成形模具的外周,卷绕一层(重叠一张)包覆布,在该包覆布的外侧卷绕由表1所示的橡胶组合物形成的未硫化的粘接橡胶层用片。接着,将s捻的处理绳和z捻的处理绳从粘接橡胶层用片上平行排列并以0.95mm的芯线间距(相邻的芯线的中心间的距离)以49.0n(1.1厘牛/分特)的张力(张力)以螺旋状旋压卷绕。进而,在其上依次卷绕由表1所示的橡胶组合物形成的未硫化的粘接橡胶层用片和由表2所示的橡胶组合物形成的未硫化的压缩橡胶层用片。然后,在压缩橡胶层用片的外侧配置有硫化用护套的状态下,将成形模具放入硫化罐中进行硫化。将硫化得到的筒状的硫化橡胶套筒从成形模具中取出,利用研磨机对硫化橡胶套筒的压缩橡胶层进行磨削,同时形成两个以上v字形槽。然后,利用切割器将圆筒状硫化橡胶套筒在周向上切成圆片而切断,由此得到具有3个v形肋部的周长1200mm(3pk1200、平均宽度10.7mm)的多楔带。所得到的带在图3所示的方向的截面图中s捻的处理绳和z捻的处理绳交替排列。另外,埋设在压缩橡胶中的短纤维从摩擦传动面(v形肋部的v字形侧面)突出。
[0140]
实施例2~11和比较例1~4
[0141]
将加捻绳的构成、热拉伸处理的条件、芯线间距、芯线旋压张力变为如表3所示,除此以外与实施例1同样地制造多楔带。比较例1和4中,将聚芳酰胺纤维的初捻纱3根(或4根)
合并复捻,不含低弹性模量纤维。
[0142]
[试验条件]
[0143]
[处理绳拉伸强度和处理绳断裂伸长率]
[0144]
依据jis l1017(2002)进行测定。详细而言,将芯线单体(实施了纤维间粘接处理和热拉伸处理的处理绳)以绳不松弛而笔直的方式设置在自动绘图仪的一对夹具上。将此时的夹持间隔设为l0(约250mm)。接着,使一个夹具以300mm/分钟的速度移动而对绳施加拉伸载荷,记录拉伸载荷和夹持间隔。处理绳拉伸强度通过用芯线断裂时的拉伸载荷除以芯线的纤度而求出。将芯线断裂时的夹持间隔设为l1(mm),处理绳断裂伸长率由下式求出。
[0145]
处理绳断裂伸长率(%)=((l
1-l0)/l0)
×
100
[0146]
[带拉伸强度]
[0147]
将3pk1200的多楔带在长度方向上三等分,制作三根肋数3、长度400mm的测定用试样。将该试样以试样不松弛而笔直的方式设置在amsler万能拉伸试验机的一对夹具上。接着,使一个夹具以50mm/分钟的速度移动而对试样施加拉伸载荷,记录试样断裂时的拉伸载荷。求出3根试样的拉伸载荷测定值的算术平均,作为带拉伸强度(n)。
[0148]
[走行试验]
[0149]
利用图4中示出布局的试验机使3pk1200的多楔带走行,对耐久性(boc变化率和拉伸强度保持率)进行评价。试验机具备直径120mm的驱动带轮(dr.)、直径45mm的张紧带轮(ten.)、直径120mm的从动带轮(dn.)、直径80mm的背面惰轮(idl.)。调节成带在张紧带轮上的卷绕角度为90
°
、带在背面惰轮上的卷绕角度为120
°
。驱动带轮的转速设为4900rpm。从动带轮的负荷设为8.8kw。通过对张紧带轮施加810n的轴载荷,对带施加张力。试验温度(气氛温度)设为120℃,走行100小时。
[0150]
[boc变化率]
[0151]
在将多楔带安装在走行试验机上的状态下,利用卷尺测定走行100小时前的带外周长(走行前boc(mm))和走行100小时后的带外周长(走行后boc(mm)),通过下式求出boc变化率。boc变化率越小,意味着多楔带的伸长率越小。
[0152]
boc变化率(%)=((走行后boc-走行前boc)/走行前boc)
×
100
[0153]
[拉伸强度保持率]
[0154]
与上述方法同样地求出走行100小时后的多楔带的带拉伸强度(走行后带拉伸强度(n))。然后,以走行前带拉伸强度(n)为基准,通过下式求出拉伸强度保持率。拉伸强度保持率越高,意味着多楔带的耐弯曲疲劳性越高。
[0155]
拉伸强度保持率(%)=(走行后带拉伸强度/走行前带拉伸强度)
×
100
[0156]
将实施例和比较例的评价结果示于表3中。
[0157][0158]
不含低弹性模量纤维的初捻纱(b)、将三根聚芳酰胺纤维的初捻纱(a)合并进行复捻而成的比较例1和将四根聚芳酰胺纤维的初捻纱(a)合并进行复捻而成的比较例4的耐弯
曲疲劳性不足,拉伸强度保持率低。
[0159]
另一方面,含有聚芳酰胺纤维的初捻纱(a)和低弹性模量纤维的初捻纱(b)、低弹性模量纤维的初捻纱(b)的初捻系数相对于聚芳酰胺纤维的初捻纱(a)的初捻系数的比(b/a)处于一定范围内的实施例1~11能够兼顾拉伸强度保持率高和传动带的伸长率小。
[0160]
通过实施例1~4与比较例2~3的比较可知:低弹性模量纤维的初捻纱(b)的初捻系数相对于聚芳酰胺纤维的初捻纱(a)的初捻系数的比(b/a)在约0.5~约1.2的范围内可以得到良好的结果。同样,认为低弹性模量纤维的初捻纱(b)的初捻系数优选为2.5~5的范围。在比较例2中,由于低弹性模量纤维的初捻纱(b)的初捻系数相对于聚芳酰胺纤维的初捻纱(a)的初捻系数的比(b/a)小至0.33,因此,带伸长率变大。认为这是合股捻绳中的初捻纱(b)的截面形状自由度变高的结果。另外,在比较例3中,低弹性模量纤维的初捻纱(b)的初捻系数相对于聚芳酰胺纤维的初捻纱(a)的初捻系数的比(b/a)大至1.33,因此,拉伸强度保持率低。认为这是因为,初捻纱(b)的伸长率变大,初捻纱(b)被赶到合股捻绳的周围,结果耐弯曲疲劳性降低。
[0161]
通过实施例3~4和10的比较,如果使用高伸度型聚芳酰胺纤维,则与使用标准型聚芳酰胺纤维的情况相比,拉伸强度保持率较高。但是,在实施例3和4中,也能够以足够的水平兼顾拉伸强度保持率高和传动带的伸长率小,可以说,可以优先考虑传动带的性能而使用高伸度型聚芳酰胺纤维,也可以优先考虑价格、获得性等而使用标准型聚芳酰胺纤维。
[0162]
实施例7~8是从实施例4降低了芯线旋压张力的例子,但提高了带拉伸强度。推测其原因是因为,将硫化橡胶套筒从成形模具中取出后的带收缩被抑制,容易保持热定形时最优化的聚芳酰胺纤维的初捻纱与低弹性模量纤维的初捻纱的平衡。但是可以推测,张力过低时,难以稳定地排列芯线。
[0163]
实施例9是与实施例7相比减小了初捻系数的例子。虽然处理绳的拉伸强度提高,但拉伸强度保持率降低。
[0164]
通过实施例10与实施例11的比较,认为对于聚芳酰胺纤维的初捻纱(a)的根数,与4根相比更优选3根。认为在聚芳酰胺纤维的初捻纱(a)为4根的情况下,由于耐弯曲疲劳性降低,拉伸强度保持率降低。
[0165]
在本实施例中,使用聚对苯二甲酸乙二醇酯纤维作为低弹性模量纤维,但也可以使用其他聚酯纤维(例如,聚萘二甲酸乙二醇酯)、脂肪族聚酰胺纤维(例如,尼龙66)等。但是,在使用这些其他纤维的情况下,有可能不能充分地提高传动带的拉伸强度和耐弯曲疲劳性,认为优选聚对苯二甲酸乙二醇酯纤维。
[0166]
将实施例3~6进行比较,在热拉伸处理的加热温度低的实施例5中,带伸长率大。认为这是因为,加热温度低时,加捻绳中的长丝彼此没有充分融合(长丝间的空隙没有充分减少),加捻绳容易伸长。另外,在热拉伸处理的加热温度高的实施例6中,拉伸强度保持率低。认为这是因为,热拉伸变得过量,低弹性模量纤维的初捻纱(b)被赶到加捻绳的周围,因此没有充分地得到提高耐弯曲疲劳性的效果。因此,认为热拉伸处理的加热温度优选为160~240℃,张力(对加捻绳施加的张力)优选为0.3~1.5厘牛/分特。
[0167]
通过实施例1~11与比较例2~3的比较还能够确认到,当处理绳对齐(b-a)处于-1~2mm/100mm的范围时,能够兼顾拉伸强度保持率高和传动带的伸长率小。
[0168]
如上所述,本发明的传动带用芯线通过混捻聚芳酰胺纤维和低弹性模量纤维,能
够在保持高的拉伸强度的同时,减小传动带的伸长率,能够提高耐弯曲疲劳性。因此,能够适合用于通过研磨法制造的多楔带(特别是通过研磨法制造的埋设于压缩橡胶中的短纤维从摩擦传动面突出的多楔带)。
[0169]
详细且参考特定的实施方式对本发明进行了说明,但对于本领域技术人员明显可知的是,在不脱离本发明的精神和范围内能够加以各种变更、修正。
[0170]
本技术基于2020年1月16日提出的日本专利申请2020-005388和2020年12月14日提出的日本专利申请2020-206743,将其内容作为参考并入本文中。
[0171]
产业上的可利用性
[0172]
本发明的传动带用芯线能够用作各种传动带、例如平带、包布v带、切边v带、切边齿形v带、多楔带等摩擦传动带;齿形带、双面齿形带等啮合传动带等的芯线。其中,由于拉伸强度高、耐久性也优良,因此,适合作为用于汽车发动机的辅机驱动的多楔带的芯线,能够特别适合用作用于驱动产生高动态张力的搭载有isg的发动机的多楔带的芯线。
[0173]
符号说明
[0174]1…
传动带用芯线
[0175]2…
压缩橡胶层
[0176]3…
v形肋部
[0177]4…
粘接橡胶层
[0178]5…
延伸层
再多了解一些
本文用于企业家、创业者技术爱好者查询,结果仅供参考。