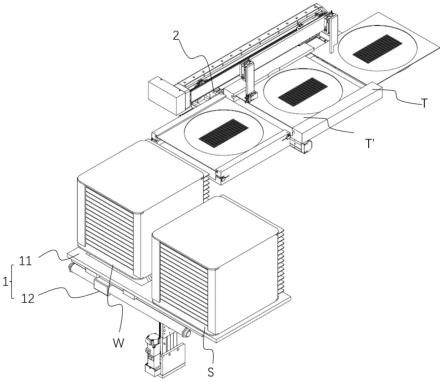
1.本发明属于半导体制造技术领域,尤其涉及一种铁环蓝膜自动上下料方法、装置及检测设备。
背景技术:
2.半导体制造中上料和下料是重要的工艺环节。以芯片自动检测全流程为例,一般要将整洁干净的晶圆粘贴在晶圆切割膜(蓝膜)上,用铁环来支撑蓝膜把晶圆固定住,让晶圆不被外界撞击到,周转存储晶圆的时候更加方便被切割开后的待测芯片不会散落下来。对于整个检测流程来说铁环蓝膜料片的上下料操作直接关系到整个检测流程的顺畅及检测效率。
3.晶圆以铁环蓝膜料片的形式通过料盒周转与放置在tray盘中周转是完全不同的,不能通过吸附搬运的方式进行上下料。料盒尺寸较大,为多层式储料形式,常规上下料方法无法适用。现有上下料方法中是在检测设备的上料位设置一个机械手从一个料盒中抓取出新料片流转至后续工序,在检测设备下料位再设置一个专门的机械手取走已经从铁环蓝膜料片上取完芯片的老料片放入另一个料盒进行回收。机械手运动幅度大,上下料路线长、装置结构庞大而且需要设定复杂的算法以精确地控制机械手,装置的开发成本很高且检测设备占用空间大,不能满足企业实际生产需求。
4.此外,现有上下料方法工作人员只能通过一个操作口在工作位更换料盒,一次只能装载一个料盒进行上料,只能一只料盒生产完成后,停机,人员更换一只新料盒再继续工作。而且有些还需要人员专门在下料位回收老料片。检测设备的正常运行需要人员及时取放料盒。需要补充待测芯片时若不能按时放置空料盒,会严重影响整个检测设备的检测效率。补充料片时间紧,需要安排工作人员保持在岗,人力资源利用率低、人工成本高。
5.可知,现有的铁环蓝膜上下料方法至少存在以下几个问题:1.上下料连贯性差、影响检测效率的提高;2.一次停机取放一个料盒,料盒更换周期过短,自动化程度低且频繁停机操作,失误率高容易引起整个检测流程运行故障;3.新料片输出和老料片回收的节拍时间没有得到统筹利用,整个上下料效率低且输出和回收沿一个方向进行,设备占用空间大和设计难度高。
技术实现要素:
6.本发明是为解决上述现有技术的全部或部分问题,本发明一方面提供了一种铁环蓝膜自动上下料方法。本发明还一方面提供了一种铁环蓝膜自动上下料装置,应用于自动检测流程。本发明另一方面提供了一种检测设备,用于进行自动检测。
7.本发明提供一种铁环蓝膜自动上下料方法,将用于进行上下料的料盒记为第一料盒,将完成上下料的料盒记为第二料盒;包括:在料盒周转区装载至少两个所述第一料盒,其中至少一个所述第一料盒存储有多层新料片,所述料盒周转区分为工作位和至少两个切换位;将所述第一料盒置于所述工作位,取完新料片和/或装满老料片后,将所述第一料盒
移动至所述切换位并将之前位于所述切换位的所述第一料盒移动至所述工作位继续取出新料片和/或回收老料片;上下料工作过程中和/或上下料工作停止时,取下位于所述切换位的所述第二料盒和/或补充所述第一料盒至所述切换位。
8.至少两个所述第一料盒中有装满新料片的,也可以有空的料盒。根据实际上下料工作情况切换位于所述工作位的所述第一料盒。例如有的实施情况中将装满新料片的所述第一料盒置于所述工作位取出新料片进行上料,取完新料片后成为空料盒后移动到所述切换位,待需要进行下料时将空的所述第一料盒从所述切换位移动至所述工作位进行下料,并不限定。
9.通过在所述料盒周转区装载至少两个所述第一料盒,能够切换料盒进行上下料工作,避免了现有铁环蓝膜料片上下料做法中一个料盒的周转能力用尽时(新料片被取完或回收满老料片),需要中止工作立即更换料盒的缺陷。更换位于所述切换位的料盒的操作,不受限于位于所述工作位的所述第一料盒的工作状态,可以根据具体工艺流程要求在对一个所述第一料盒进行上下料工作时,取走移动到所述切换位的第二料盒或者向所述切换位补充新的所述第一料盒,不间断地向所述工作位提供所述第一料盒;也可以在上下料工作停止时,取走所述第二料盒和/或补充所述第一料盒;还可以在不同的所述切换位同步取走所述第二料盒并补充所述第一料盒,也可以穿插进行;更换料盒操作时间宽裕、便于人员操作、料片周转连贯性强,在一个检测流程中持续供应更多的铁环蓝膜料片,能够进一步统筹利用待测芯片流转及芯片检测的节拍时间,缩短检测流程的整体工时、提高检测效率。
10.当所述料盒周转区的全部料盒中均为所述老料片时,上下料工作停止并发出信号通知更换料盒;更换此时位于所述切换位及所述工作位的料盒。更换完成后,再次启动下一轮的上下料工作。
11.当全部料盒均为所述第二料盒时才停止上下料工作并通知人员前来一次性更换全部料盒,一次上下料工作的周期更长,不必专人时刻在岗等候换料盒,自动化程度进一步提高、操作失误概率大幅降低,在一个上下料工作周期中操作人员可以利用这段时间进行其他工作,进一步释放了人工、利于提高整体产能及节约人力成本。
12.所有所述第一料盒中均存储有所述新料片;所述上下料工作过程中,对同一个所述第一料盒交替进行取出新料片和回收老料片;当所述第一料盒中一层的新料片被替换为老料片后,移动所述第一料盒对另一层继续进行上下料工作;直至所述第一料盒中的新料片全部替换为老料片后将该料盒作为所述第二料盒移动至所述切换位。
13.通过对同一个所述第一料盒逐层交替进行新料片的取出和老料片的回收,在同一个工作位既进行新料片的输出又能回收后段工序已经取完待测芯片的老料片,整个料片的上下料路线缩短一半,利于满足设备结构小型化设计、提高企业生产空间利用率,一个新料片输出和上一个周期被后段工序取完待芯片的老料片回收的动作交替进行,无须等待一个新料片被后段工序取完待测芯片后再回收该老料片,动作行程紧凑、节拍时间得到了统筹利用,进一步提高了自动上下料的工作效率。
14.本发明一方面提供的一种铁环蓝膜自动上下料装置,用于实施本发明的铁环蓝膜自动上下料方法;包括料盒模组、料片上下料模组;所述料盒模组包括料盒支撑部件和料盒切换部件;所述料盒支撑部件至少能承载两个料盒;所述料盒切换部件与所述料盒支撑部件传动连接,带动所述料盒支撑部件作经过所述料盒模组的工作位的往复移动;所述料片
上下料模组与所述工作位对接,包括x轴横移组件、取料夹爪组件;所述x轴横移组件的输出端与所述取料夹爪组件传动连接,带动所述取料夹爪组件沿x轴往复运动,在所述工作位与接料载台之间移载料片。所述料盒支撑部件承载的至少两个料盒,其中一个料盒置于工作位时,其他料盒置于切换位。通过所述料盒支撑部件与所述料盒切换部件相互配合可以切换处于所述工作位的料盒,更多的料盒可以被切换到工作位进行工作,大幅延长了对料盒模组中的料盒进行更换操作的周期,操作人员不用时刻保持在岗等待更换料盒,可以长时间离开,可以在所述料盒支撑部件承载的全部料盒都完成上下料后再来更换,有效提高了操作人员的机动性,利用生产资源的优化配置、降低人工成本、提高单人产出。此外,由于操作人员一次可以更换多个料盒,并且不需要频繁更换,减少了停机次数,多个料盒能够切换进行不间断的上下料工作也减少了人员上下料而造成停机等待时间。
15.所述铁环蓝膜自动上下料装置还包括顶料z轴模组;所述料盒支撑部件的底部开设有镂空区,所述顶料z轴模组的输出端通过所述镂空区与位于所述工作位的料盒底部传动连接,用于升降所述料盒。通过所述顶料z轴模组切换位于所述工作位料盒的料片层,将料盒顶起使每一层料片分别移到对应的上下料位置。
16.所述料盒模组外部设置有壳体,所述壳体开设有至少两个操作口;所述操作口对接所述料盒模组的切换位,用于取放料盒。在所述料盒模组外部设置壳体,更好地防尘、保护料盒避免料片损伤,在壳体上至少设置两个所述操作口便于操作人员从不同位置更加灵活的更换切换位的料盒,进一步减少停机等待时间、利于提高生产线的产能。
17.所述料盒切换部件为直线运动机构,所述直线运动机构的输出端与所述料盒支撑部件的底部传动连接,驱动所述料盒支撑部件以所述料盒在y轴方向上的宽度为步长沿y轴间歇式往复移动。所述料盒支撑部件由直线运动机构驱动沿直线以一个料盒的宽度为步长间歇式往复运动,能够将承载于所述料盒支撑部件不同区域的料盒移动到所述工作位后停止移动保持静止进行上下料,在完成上下料后继续移动已完成工作的料盒到所述切换位以等待操作人员取走,并更换新的料盒。切换行程占用空间小,结构简洁,采用直线运动机构运行稳定可靠且易于配置,利于节约制造成本。
18.一个具体实施例中所述直线运动机构采用气缸或电机驱动,配合丝杠实现按预设步长直线移动。所述直线运动机构也可以采用其他驱动机构实现驱动,并不限定。所述料盒切换部件也可以采用旋转机构实现弧线运动进行位置切换,可以根据具体结构和空间设计,切换运动路径避开结构干涉即可,并不限定。
19.所述取料夹爪组件包括第一升降部、第一推杆、设置在所述第一推杆下端的夹爪部;所述第一升降部的输出端与所述第一推杆的上端传动连接,以带动所述第一推杆升降。
20.所述取料夹爪组件还包括第二升降部、第二推杆;所述第二升降部的输出端与所述第二推杆传动连接,以带动所述第二推杆升降。
21.所述第一推杆与所述第二推杆在x轴方向的间距范围是350毫米至400毫米。
22.所述料片上下料模组还包括设置在所述工作位与所述接料载台之间的料片中转组件;所述料片中转组件包括中转位平台、第三升降部;所述第三升降部的输出端与所述中转位平台底部传动连接,以带动所述中转位平台升降;所述中转位平台包括层叠设置的第一料片层和第二料片层,分别用于承接来自料盒的新料片和来自所述接料载台的老料片。
23.所述第一料片层和/或第二料片层设置有卡位结构;所述卡位结构包括位置传感
器和限制感应块;所述位置传感器与限制感应块配合,控制料片移载至预设位置。
24.所述中转位平台在x轴方向的宽度等于所述第一推杆与所述第二推杆在x轴方向的间距。
25.所述料盒的层数范围是13层至25层。
26.本发明还有一方面提供一种检测设备,设置有本发明的铁环蓝膜自动上下料装置。
27.与现有技术相比,本发明的主要有益效果:1、本发明的一种铁环蓝膜自动上下料方法,一次能取放至少两个料盒,料盒切换工作,利于延长料盒更换周期、提高检测流程的流畅性、优化检测工艺,自动化程度高、连贯性好,料盒更换操作便捷高效、工时利用率高,能够优化生产资源配置,大幅节约生产成本。
28.2、本发明的一种铁环蓝膜自动上下料装置,构造简单,无须设置机械手、上下料运动行程合理、动作幅度小、运行稳定性高、结构占用空间小、易于维修保养且能够满足运行节拍时间短的生产线的自动上下料需求,适用于同本领域大部企业的实际应用,设置有切换位和工作位,能够方便快捷进上下料及料盒更换工作,能够增加人员更换料盒的工作周期、进一步减少人员上下料而造成停机等待时间并提高生产线的整体产能。
29.3、本发明的一种检测设备,因采用本发明的铁环蓝膜自动上下料装置,具有相应优势,能够连贯地获取铁环蓝膜料片以对待测芯片进行自动光学检测,上下料便捷、检测效率高。
附图说明
30.图1为本发明实施例一的铁环蓝膜自动上下料方法过程示意图。
31.图2为本发明实施例二的铁环蓝膜自动上下料装置的整体示意图。
32.图3为本发明实施例二的铁环蓝膜自动上下料装置的俯视示意图。
33.图4为本发明实施例二的料盒模组的侧视示意图。
34.图5为本发明实施例二的铁环蓝膜自动上下料装置的侧视示意图。
35.图6为本发明实施例二的卡位结构示意图。
36.图7为本发明实施例二的铁环蓝膜自动上下料流程示意图。
37.图8为本发明实施例二的检测设备示意图。
具体实施方式
38.下面将对本发明具体实施例中的技术方案进行清楚、完整地描述,显然,所描述的实施例仅是本发明的一部分实施例,而不是全部的实施例。基于本发明中的实施例,本领域普通技术人员在没有做出创造性劳动前提下所获得的所有其他实施例,都属于本发明保护的范围。
39.实施例一实施例以micro led自动检测的应用为例进行介绍,为了便于本领域的专业技术人员全面的理解本发明,但不以任何形式限制本发明。本发明实施例一中,提供一种铁环蓝膜自动上下料方法,为了便于说明,将用于进行上下料的料盒记为第一料盒,将完成上下料的料盒记为第二料盒。示例的方法包括:在料盒周转区装载至少两个第一料盒,其中至少一
个第一料盒存储有多层新料片,料盒周转区分为工作位和至少两个切换位;将第一料盒置于工作位,取完新料片和/或装满老料片后,将第一料盒移动至切换位并将之前位于切换位的第一料盒移动至工作位继续取出新料片和/或回收老料片;上下料工作过程中和/或上下料工作停止时,取下位于切换位的第二料盒和/或补充第一料盒至切换位。如图1所示,一个具体的过程中,初始阶段先在料盒周转区装载两个第一料盒;启动第一次上下料工作,将一个第一料盒置于工作位,对该第一料盒交替进行取出新料片和回收老料片;该第一料盒中全部为回收的老料片后移动至切换位作为第二料盒并将之前位于切换位的另一个第一料盒移动至工作位;在上下料工作停止时,取走第二料盒同时补充新的第一料盒。人员在两次上下料工作之间更换料盒操作时间宽裕、便于人员操作。实际应用中可以装载更多的第一料盒并不限于两个。有些做法中是在对第二个第一料盒上下料工作中取下位于切换位的第二料盒更换为一个新的第一料盒。这个做法中能够不间断地向工作位提供第一料盒,料片周转连贯性强。还可以在不同的切换位由两个操作人员同步取走位于一个切换位的第二料盒并补充第一料盒到另一个切换位,也可以一个操作人员对不同的切换位穿插进行,并不限定。
40.一个具体的做法中当第一料盒中一层的新料片被替换为老料片后,移动第一料盒对另一层继续进行上下料工作;直至第一料盒中的新料片全部替换为老料片后将该料盒作为第二料盒移动至切换位。这个示例的做法中两个第一料盒中均预先装满有新料片,对同一个所述第一料盒逐层交替进行新料片的取出和老料片的回收,在同一个工作位既进行新料片的输出又能回收后段工序已经取完待测芯片的老料片,整个料片的上下料路线缩短一半,利于满足设备结构小型化设计、提高企业生产空间利用率,一个新料片输出和上一个周期被后段工序取完待芯片的老料片回收的动作交替进行,无须等待一个新料片被后段工序取完待测芯片后再回收该老料片,动作行程紧凑、节拍时间得到了统筹利用,进一步提高了自动上下料的工作效率。示例装载的两个第一料盒也可以一个第一料盒中装满新料片,另一个第一料盒是空的。在启动上下料工作后,交替从一个第一料盒中取新料片,往另一个第一料盒中放老料片。新料片被取空的第一料盒也可以用于下一轮工作时回收老料片,在此并不限定具体做法。
41.示例的做法中,一次上下料工作停止时,更换料盒周转区的料盒启动下一次上下料工作。示例的做法中当所述料盒周转区的全部料盒中均为所述老料片时,上下料工作停止并发出信号通知更换料盒;更换此时位于所述切换位及所述工作位的料盒。一次上下料工作的周期更长,不必专人时刻在岗等候换料盒,自动化程度进一步提高、操作失误概率大幅降低,在一个上下料工作周期中操作人员可以利用这段时间进行其他工作。
42.实施例二本发明实施例二中,如图2和图3所示,铁环蓝膜自动上下料装置可以用于实施上述实施例一的铁环蓝膜自动上下料方法,包括料盒模组1、料片上下料模组2。料片上下料模组2与料盒模组1的工作位w对接,包括x轴横移组件21、取料夹爪组件22。x轴横移组件21的输出端与取料夹爪组件22传动连接,带动取料夹爪组件22沿x轴往复运动,取料夹爪组件22在工作位w与接料载台t(接料位t’)之间移载料片。有些实施情况中,料片上下料模组2中也可以采用其他运动机构沿其他运动路径进行料片的上下,例如采用多轴机械手沿弧线往复运动在工作位w与接料载台t(接料位t’)之间移载料片,根据工作位w与接料位t’的相对位
置相应设置,并不限定。料盒模组1包括料盒支撑部件11和料盒切换部件12。料盒支撑部件11至少能承载两个料盒。料盒切换部件12与料盒支撑部件11传动连接,带动料盒支撑部件11作经过工作位w的往复移动,切换位于工作位w的料盒。示例的情况中料盒支撑部件11为一个支撑架,支撑架上部并排承载两个料盒,其中一个料盒在工作位w时,另一个料盒在切换位s,如图3所示例的情况中切换位s可以是工作位w的两侧,一个工作位的料盒完成后移动至一侧的切换位s,原来在工作位w另一侧切换位s等待工作的料盒同步被移动到工作位w投入工作。示例的料盒模组1外部设置有壳体(未图示),壳体开设有两个操作口;操作口对接料盒模组1的切换位,用于工作人员取放料盒。
43.本实施例中,如图4所示,铁环蓝膜自动上下料装置还包括顶料z轴模组3,料盒支撑部件11的底部开设有镂空区,顶料z轴模组3的输出端通过镂空区与位于工作位w的料盒底部传动连接,用于升降所述料盒,以切换料盒的料片层。示例的支撑架的承载面呈框状,对应工作位w的区域中开设有镂空区,顶料z轴模组3的输出端设置有承托面,镂空区的大小足够承托面通过,承托面与工作位w的料盒底部传动连接,可以将在工作位w的料盒从料盒支撑部件11上托起。顶料z轴模组3可以采用气缸驱动或者伺服电机驱动。有些实施情况中顶料z轴模组3也可以结合具体设备设计采用其他驱动机构实现z轴运动,并不限定。在有些具体实施中也可以没有顶料z轴模组3,料盒支撑部件11设置层架结构,一层承载一个料盒,通过料盒切换部件12带动料盒支撑部件11上下移动,可以垂直切换不同的料盒至工作位w,也可以切换工作位w的料盒的具体料片层进行上下料。通过设定外接控制模块控制具体动作,可以结合企业实际应用场所的空间布局相应设计切换料盒的运动是上下运动还是水平运动,在此并不限定。
44.在本实施例中,料盒切换部件12为直线运动机构,直线运动机构的输出端与料盒支撑部件11的底部传动连接,驱动料盒支撑部件11以料盒在y轴方向上的宽度为步长沿y轴间歇式往复移动。直线运动机构采样气缸驱动配合丝杠实现宽度为步长沿y轴间歇式往复移动,每移动一个料盒的宽度,停止移动,工作位w的料盒到位进行工作,工作完成后再移动一个料盒的宽度,更换工作位w的料盒同时将完成工作的料盒移动到切换位s等待人员取走,运行稳定、没有额外行程,工作位w的料盒和切换位s的料盒通过一个步长的一个移动动作同步到位,成本低、结构简单、操控方便、节约功耗。在有些实施例中料盒切换部件12也可以采用旋转机构带动料盒支撑部件11间隙式旋转切换工作位w的料盒,或者采用升降机构上下运动实现料盒切换,具体切换运动路径可以根据实际空间布局相应设置,并不限定。
45.如图5所示,在本实施例中,取料夹爪组件22包括第一升降部221、第一推杆222、设置在第一推杆222下端的夹爪部223。第一升降部221的输出端与第一推杆222的上端传动连接,以带动第一推杆222升降。
46.在一个具体的做法中,取料夹爪组件22还包括第二升降部224、第二推杆225。第二升降部224的输出端与第二推杆225传动连接,以带动第二推杆225升降。x轴横移组件21可以采用气缸,取料夹爪组件22设置两个推杆及相应两个升降部,可以采用气缸驱动升降,夹爪部223可以用一个朝向料盒的夹爪缸来实现,利于灵活的结合料片在流转中的位置配合完成抓取和推的动作,简化运动步骤、减少运动行程,利于提高搬运效率。
47.在本实施例中,料片上下料模组2还包括设置在工作位w与接料载台t的接料位t’之间的料片中转组件23。料片中转组件23包括中转位平台231、第三升降部232。第三升降部
232的输出端与中转位平台231底部传动连接,以带动中转位平台231升降。中转位平台231包括层叠设置的第一料片层231a和第二料片层231b,分别用于承接来自料盒的新料片和来自接料载台t的老料片。本实施例中设置料片中转组件23可以使得来自接料载台t的老料片和来自料盒的新料片进行交替周转,进一步减少运行的节拍时间和缩短运动行程,能够加快上下料速度,用一个料盒实现新料片的输出和老料片的回收,极大的缩短了生产线整体运行周期,并能实现生产线的连续运行,无须进行一次新料片的逐一接收运行后、再进行一次老料片的逐一装载,整个生产线能够连续的同步上新料片和下老料片,工作效率大幅提高、能够进一步减少停机的次数。第一推杆222与第二推杆225由x轴横移组件21带动,两者在x轴方向同步移动时间距不变。示例的第一推杆222与第二推杆225在x轴方向的间距范围是350毫米至400毫米,其中一个优选的示例值是360毫米。这个间距范围的第一推杆222与第二推杆225对于当前常规料片宽度,能够同时到达一个料片的两侧;示例的中转位平台231在x轴方向的宽度等于第一推杆222与第二推杆225在x轴方向的间距,也能够同时到达中转平台231的两侧。取料夹爪组件22一次往返行程能够移动至少两个料片,进一步提高行程有效性、利于提高运行效率和生产线运行流畅性,减少无效动作而导致的功耗和工时损失。
48.示例的做法中,如图6所示,第一料片层231a和第二料片层231b设置有卡位结构。卡位结构包括位置传感器2311和限制感应块2312。位置传感器2311与限制感应块2312配合,控制料片移载至预设位置。示例的卡位结构分别设置在第一料片层231a右侧在y轴方向上的两边、第二料片层231b左侧在y轴方向上的两边。限制感应块2312通过复位扭簧与料片层边缘连接,当料片移动中出现过冲,触及限制感应块2312则通过复位扭簧使其回到料片层内部区域,并同步触发位置传感器2311,位置传感器2311发送信号给外接控制模块,控制取料夹爪组件22停止运动或适当进行返回动作将料片置于料片层上的预设位置。
49.下面的对采用本实施例的铁环蓝膜自动上下装置进行上下料的过程进行具体示例,可以使本领域的专业技术人员更全面地理解本发明的铁环蓝膜自动上下料方法,但不以任何方式限制本发明。
50.结合参考图2至图6,本实施例中采用铁环蓝膜自动上下料装置进行铁环蓝膜料片的上下料过程,如图7所示,步骤s1.将至少两个分别存储有多层新料片的料盒承载于料盒支撑部件11。步骤s2.将位于工作位w的当前料盒中的新料片移载至接料载台t,将接料载台t上完成的老料片移载至当前料盒中。步骤s3.料盒切换部件12运动带动料盒支撑部件11将当前料盒移动到切换位s,同时将原先在切换位s等待工作的料盒移动到工作位w。直至承载于料盒支撑部件11的全部料盒中均没有新料片,发出信号通知更换料盒。信号可以通过设置的信号灯或者是蜂鸣器发出声音等形式为企业生产空间的人员感知,收到信号后人员可以马上过来更换若干个料盒,也可以等下一批料盒到位后一次性运输至上下料工作区域进行料盒更换。根据生产实际安排相应实施,并不限制。更换料盒周期长,且一次更换过程可以更换多个料盒,便于实际实施和灵活操作,提高了人员的机动性、有利于实现工作的统筹安排和协调实施。通过一次至少承载两个料盒,进行切换工作,大幅减少了更换料盒的工作量,且充分延长了更换料盒的周期,解决了现有上下料做法中需要人员在岗关注的局限性,进一步释放了单人的产出能力,降低人工成本的同时还能提高整体生产线的工作效率。
51.示例的做法中,步骤s2的过程包括:步骤s21.取料夹爪组件22将当前料盒中的新
料片夹取至第一料片层231a。步骤s22.取料夹爪组件22运动将接料载台t上的老料片推到第二料片层231b。步骤s23.取料夹爪组件22将新料片推至接料载台t的接料位t’,将老料片推回当前料盒的空位。重复步骤s21至s23,直至当前料盒的新料片全部替换为老料片。
52.以中转位平台231有上下两层,上层是第一料片层231a,下层第二料片层231b为例说明中转搬运的流程。在步骤s21之前,顶料z轴模组3将当前料盒自上而下的第一层移动至与第一料片层231a等高,且第一料片层231a与接料载台t的接料位t’等高。步骤s23之后顶料z轴模组3将当前料盒向上移动一层后开始对第二层重复操作。
53.步骤s21中,夹爪部223将当前料盒中的新料片夹出料盒并移动到第一料片层231a的指定位置后,第一升降部221驱动第一推杆222上升脱离工作范围。第三升降部232驱动中转位平台231升降使得第二料片层231b与接料位t’等高,此时第一推杆222和第二推杆225运动至接料位t’在x轴方向上的两侧。步骤s22中,第二推杆225到达接料位t’远离中转位平台231的一侧后由第二升降部224驱动下降至工作范围,推动接料载台t上流转至接料位t’的老料片至第二料片层231b。此时第一推杆222和第二推杆225运动至中转位平台231在x轴方向上的两侧。步骤s23中,第三升降部232先驱动中转位平台231下降使得第一料片层231a与接料位t’等高,第二升降部224驱动第二推杆225上升脱离工作范围,第一升降部221驱动第一推杆222下降至中转位平台231远离接料载台t的一侧回到工作范围,推动新料片从第一料片层231a至接料位t’。此时第一推杆222和第二推杆225又运动至接料位t’在x轴方向上的两侧,且第一推杆222在工作范围,第二推杆225不在工作范围。第三升降部232再驱动中转位平台231回升使得第二料片层231b与当前料盒的空位等高,由第一推杆222再反向运动将老料片推至当前料盒的空位。取料夹爪组件22由x轴横移组件驱动往复于中转位平台和接料载台,并与第三升降部232配合切换第一料片层231a与第二料片层231b,并根据取料夹爪组件22所处的位置,通过交替穿插升降第一推222和第二推杆225灵活地进行夹取和推的动作,节约功耗且配合顺畅,没有多余往复及升降行程,避免了运输时间的浪费、进一步缩短了节拍时间。
54.参考图6,示例的步骤s2中,新料片或老料片作用于限制感应块2312时,触发位置传感器2311,传递信号至外接控制模块,控制x轴横移组件21使得取料夹爪组件22停止运动。
55.通过本实施例可以了解采用本发明的铁环蓝膜自动上下料方法进行上下料,步骤简洁、节拍时间短,还能够不需要人员保持关注、不依赖于人工切换料盒,避免了频繁停机更换料盒,进一步释放了产能,生产效率高且利于设备稳定运行。需要说明的是,本发明的铁环蓝膜自动上下料方法也可以结合企业具体的自动化生产设备采用其他设计的上下料机构实施,并不限定。
56.如图8所示,本实施例中还提供一种检测设备沿待测芯片流转方向依次设置有本实施例的铁环蓝膜自动上下料装置a及自动光学检测模组b。自动光学检测模组b用于对铁环蓝膜料片上的待测芯片进行自动光学检测。图8示例的情况中,检测设备的上下料位m对应工作位w和切换位s开设,能够在上下料工作停止时对工作位w和切换位s进行料盒的取放。图8示例的情况中铁环蓝膜自动上下料装置a与自动光学检测模组b之间还设置有取芯片机构,能够从铁环蓝膜料片上取下待测芯片向自动光学检测模组b输送进行检测。检测设备可以根据企业具体检测流程需要及生产空间相应设计,在此并不限定具体情况。
57.需要说明的是,在本文中,诸如“第一”和“第二”等之类的关系术语仅仅用来将一个实体或者操作与另一个实体或操作区分开来,而不一定要求或者暗示这些实体或操作之间存在任何这种实际的关系或者顺序。
58.以上对本发明进行了详细介绍,对于本技术领域的普通技术人员来说,在不脱离本发明原理的前提下,还可以对本发明进行若干改进和修饰,这些改进和修饰也落入本发明权利要求保护的范围内。
再多了解一些
本文用于企业家、创业者技术爱好者查询,结果仅供参考。